2015 All.Pdf
Total Page:16
File Type:pdf, Size:1020Kb
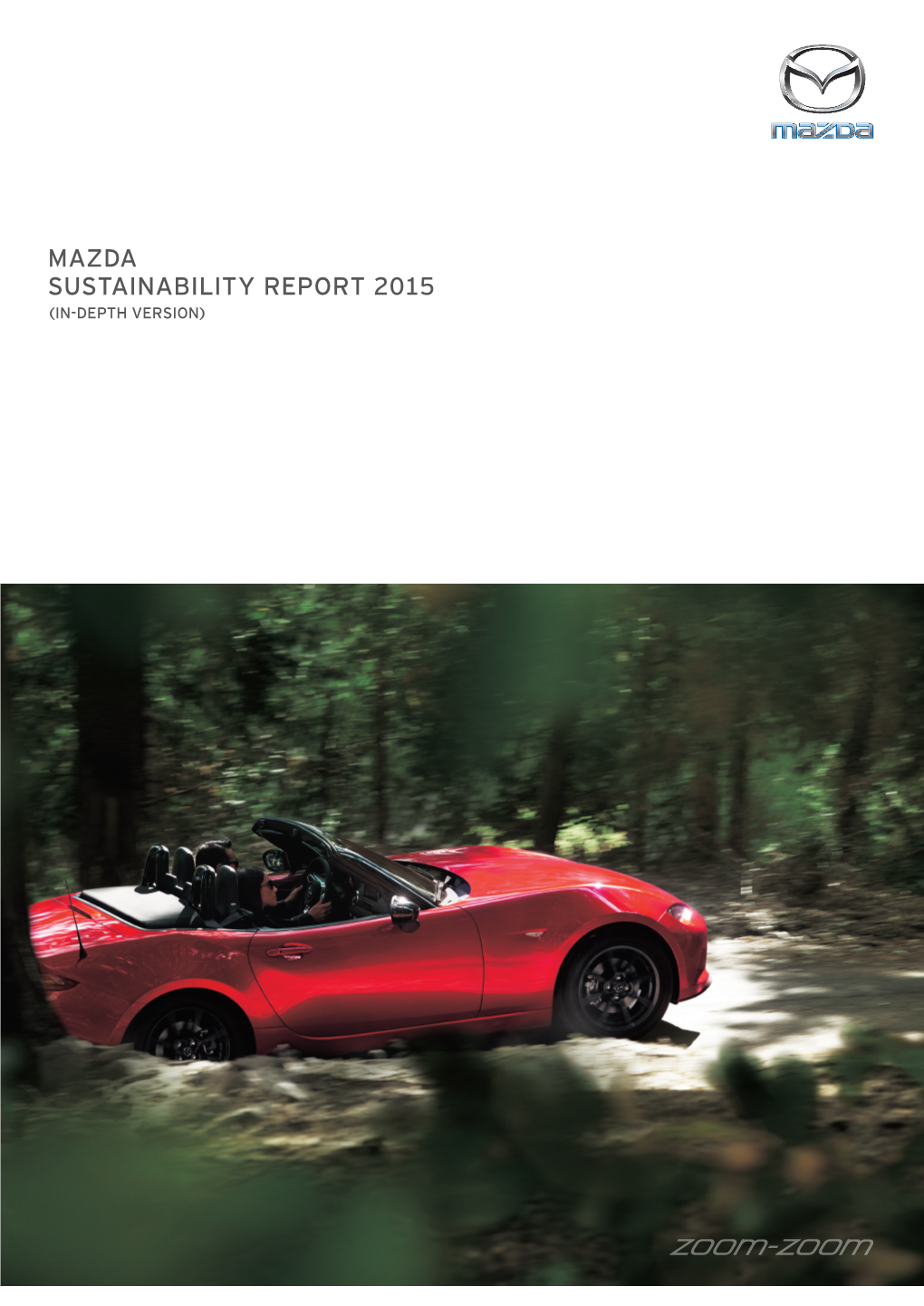
Load more
Recommended publications
-
Driving Growth Towards the Future
Head Office Jidosha Kaikan, Shiba Daimon 1-chome, Minato-ku Tokyo 105-0012 Japan Tel: +81-3-5405-6126 Fax: +81-3-5405-6136 DRIVING GROWTH http://www.jama.or.jp/ Singapore Branch North American Office 143 Cecil Street, 1050 17th Street, N.W., Suite 410 #09-03/04 GB Bldg. Washington, DC 20036-5518, USA TOWARDS THE FUTURE Singapore 069542 Tel: +1-202-296-8537 Tel: +65-6221-5057 Fax: +1-202-872-1212 Fax: +65-6221-5072 http://www.jama.org/ 2015 Beijing Representative European Office Office Avenue Louise 287 Unit 1001B, Level 10, 1050 Bruxelles, BELGIUM China World Office 2 Tel: +32-2-639-1430 No. 1 Fax: +32-2-647-5754 Jian Guo Men Wai Avenue Beijing, China 100004 Tel: +86-10-6505-0030 Fax: +86-10-6505-5856 KAWASAKI HEAVY INDUSTRIES, LTD. SUZUKI MOTOR CORPORATION DAIHATSU MOTOR CO., LTD. Kobe Head Office: Head Office: Head Office: Kobe Crystal Tower, 1-3, Higashi 300, Takatsuka-cho, Minami-ku, 1-1, Daihatsu-cho, Ikeda, Osaka 563-8651 Kawasaki-cho 1-chome Chuo-ku, Hamamatsu, Shizuoka 432-8611 Tel: +81(72)751-8811 Kobe, Hyogo 650-8680 Tel: +81(53)440-2061 Tokyo Office: Tel: +81(78)371-9530 Tokyo Branch: Shinwa Bldg, 2-10, Nihonbashi Hon-cho, Tokyo Head Office: Suzuki Bldg, Higashi-shimbashi 2F, 2-Chome, Chuo-ku, 2-2-8 Higashi-shinbashi, Tokyo 103-0023 1-14-5, Kaigan, Minato-ku, Tokyo 105-8315, Japan Minato-ku, Tokyo 105-0021 Tel: +81(3)4231-8856 Tel: +81(3)5425-2158 http://www.daihatsu.com/ Tel: +81(3)3435-2111 http://www.khi.co.jp/ http://www.globalsuzuki.com/ FUJI HEAVY INDUSTRIES LTD. -
Media Relations Activities As a Public Relation Strategy Implementation of Pt
49 MEDIA RELATIONS ACTIVITIES AS A PUBLIC RELATION STRATEGY IMPLEMENTATION OF PT. TOYOTA ASTRA MOTOR Galih Akbar Prabowo Institut Agama Islam Negeri Ponorogo Jl. Puspita Jaya, Jenangan, Ponorogo email: [email protected] Abstract: Public relations have an important role in a company. Not only in the effort to ensure good relations with the internal stakeholders, but also with its external stakeholders. In relation to external stakeholders, the media is one of the parties that have important roles in the formation of the company image. PT. Toyota Astra Motor as an international scale automotive company is an example of a company that owns a large commitment to building a good relation with media. Media relations activities conducted by the company have been proving that PT. Toyota Astra Motor not only placed the press as an instrument to build a positive image of the company but even more than that, the media is one of the important stakeholders and a partner for the PT. Toyota Astra Motor Itself. Keywords: Public Relations, Media, Toyota INTRODUCTION PT. Toyota Astra Motor is an example of a company that has a strong commitment to fostering good relations with the media as one of its external stakeholders. PT. Toyota Astra Motor shows that the media is not only a tool to create a positive image for the company. But more than that, PT. Toyota Astra Motor positions the media as partners. This can be seen from the various media relations activities carried out routinely as part of the efforts of PT. Toyota Astra Motor is creating and maintaining a harmonious relationship with the media as well as an effort to manage the positive image of PT. -
Global Network
18 CONTENTS Mazda Annual Report 2015 Foundations Underpinning Introduction Message from Management Growth Strategy Review of Operations Corporate Data Sustainable Growth Global Network 26 Changan Mazda Automobile 8 Hiroshima Plant 9 Hofu Plant Location : Nanjing, China Location : Aki-gun, Hiroshima, Japan Location : Hofu, Yamaguchi, Japan Production capacity : 220,000 units per year Production capacity : 515,000 units per year Production capacity : 481,000 units per year Models in production : Mazda2, Mazda3, CX-5 Main models in production : CX-3, CX-5, CX-9, Roadster, Models in production : Demio, Axela, Atenza Premacy, MPV, Biante, Verisa 22 17 20 21 19 18 6 25 28 15 7 26 27 29 12 14 4 10 23 24 9 32 39 5 13 16 33 3 30 31 35 34 11 42 1 2 8 40 36 30 AutoAlliance (Thailand) 13 Mazda de Mexico Vehicle Operation 41 43 37 38 Location : Salamanca, Mexico Production capacity : 250,000 units per year Location : Rayong, Thailand (March 2016 fiscal year) Production capacity : 141,000 units per year Models in production : Mazda2, Mazda3, Toyota- Models in production : Mazda2, Mazda3, BT-50 brand compact vehicles 19 CONTENTS Mazda Annual Report 2015 Foundations Underpinning Introduction Message from Management Growth Strategy Review of Operations Corporate Data Sustainable Growth Global Network Major Facilities Trends in Production Volume ■ Japan ■ Overseas (Thousands of units) Japan (Number of dealerships: 1,026) China (Number of dealerships: 455) 1,375 Headquarters 1 Headquarters Regional headquarters 23 Mazda Motor (China) (MCO) 1,277 1,269 1,185 -
Skripsi Analisis Strategi Segmentation, Targeting
SKRIPSI ANALISIS STRATEGI SEGMENTATION, TARGETING, POSITIONING (STP)PADAPT. KUMALA CELEBES MOTOR (MAZDA MAKASSAR) ROSNAINI 105720500914 JURUSAN MANAJEMEN FAKULTAS EKONOMI DAN BISNIS UNIVERSITAS MUHAMMADIYAH MAKASSAR MAKASSAR 2018 1 ANALISIS STRATEGI SEGMENTATION, TARGETING, POSITIONING (STP)PADAPT. KUMALA CELEBES MOTOR (MAZDA MAKASSAR) SKRIPSI ROSNAINI NIM 105720500914 Diajukan Guna Memenuhi Salah Satu Syarat Untuk Memperoleh Gelar Sarjana Ekonomi (S1) Fakultas Ekonomi Dan Bisnis Universitas Muhammadiyah Makassar JURUSAN MANAJEMEN FAKULTAS EKONOMI DAN BISNIS UNIVERSITAS MUHAMMADIYAH MAKASSAR MAKASSAR 2018 ii PERSEMBAHAN “Skripsi ini Kupersembahkan bagi kedua orang tua tercinta sebagai bentuk tanggung jawab, bakti, dan ungkapan terima kasih atas doa, motivasi, semangat, dan pengorbanan yang telah diberikan selama ini”. MOTTO HIDUP “Memulai dengan penuh keyakinan Menjalankan dengan penuh keikhlasan Menyelesaikan dengan penuh kebahagiaan” iii iv v vi KATA PENGANTAR Syukur Alhamdulillah penulis panjatkan ke hadirat Allah SWT atas segala rahmat dan hidayah yang tiada henti diberikan kepada hamba-Nya. Shalawat dan salam tak lupa penulis kirimkan kepada Rasulullah SAW beserta para keluarga, sahabat, dan para pengikutnya. Merupakan nikmat yang tiada ternilai manakala penulisan skripsi yang berjudul “Analisis Strategi Segmentation, Targeting, Positioning Pada PT. Kumala Celebes Motor (Mazda Makassar)”. Skripsi yang penulis buat ini bertujuan untuk memenuhi syarat dalam menyelesaikan Program Sarjana (S1) pada Fakultas Ekonomi dan Bisnis Universitas -
Maruti Suzuki from Wikipedia, the Free Encyclopedia Jump To: Navigation, Search
Hide Wikipedia is getting a new look. Help us find bugs and complete user interface translations before August 25, 2010. Maruti Suzuki From Wikipedia, the free encyclopedia Jump to: navigation, search Maruti Suzuki India Limited Type Public (BSE MARUTI, NSE MARUTI) Industry Automotive Founded 1981 (as Maruti Udyog Limited) Headquarters Delhi, India Mr. Shinzo Nakanishi, Managing Director Key people and CEO Products Automobiles, Motorcycles Revenue ▲US$4.8 billion (2009) Employees 6,903 [1] Parent Suzuki Motor Corporation Website MarutiSuzuki.com Maruti Suzuki India Limited (Hindi: मारित सुजूकी इंिडया िलिमटेड) is a publicly listed automaker in India. It is the largest automobile manufacturer in South Asia. Suzuki Motor Corporation of Japan holds a majority stake in the company. It was the first company in India to mass-produce and sell more than a million cars. It is largely credited for having brought in an automobile revolution to India. It is the market leader in India and on 17 September 2007, Maruti Udyog Limited was renamed Maruti Suzuki India Limited. The company's headquarters are located in Delhi. Contents [hide] • 1 Profile • 2 Partner for the joint venture • 3 Joint venture related issues • 4 Industrial relations • 5 Services offered ○ 5.1 Current sales of automobiles 5.1.1 Manufactured locally 5.1.2 Imported ○ 5.2 Discontinued car models ○ 5.3 Manufacturing facilities 5.3.1 Gurgaon Manufacturing Facility 5.3.2 Manesar Manufacturing Facility ○ 5.4 Sales and service network ○ 5.5 Maruti Insurance ○ 5.6 Maruti Finance ○ 5.7 Maruti TrueValue ○ 5.8 N2N Fleet Management ○ 5.9 Accessories ○ 5.10 Maruti Driving School • 6 Issues and problems • 7 Exports • 8 See also • 9 References and notes • 10 External links [edit] Profile The old logo of Maruti Suzuki India Limited. -
BAB I PENDAHULUAN 1.1. Judul : Pusat DIKLAT Mobil Nasional
BAB I PENDAHULUAN 1.1. Judul : Pusat DIKLAT Mobil Nasional ESEMKA di Klaten 1.2. Pengertian Judul Pusat : pokok pangkal atau yang menjadi pumpunan (berbagai- bagai urusan, hal, dsb). (Kamus Besar Bahasa Indonesia). Diklat : Pendidikan dan pelatihan (Diklat) merupakan wahana strategis dalam rangka pengembangan sumber daya manusia yang berkualitas, memiliki ilmu pengetahuan, keterampilan dan kepribadian seutuhnya untuk dapat bekerja dengan baik dan mampu memecahkan berbagai masalah kehidupan dalam perubahan yang berlangsung begitu cepat. (Tigor Panusunan Siregar, 2011). Mobil Nasional : mobil yang rancangan hak kekayaan intelektual dan ownershipnya punya indonesia. (Dewa Yuniardi, 2012). Esemka : produk mobil nasional (Mobnas) hasil rakitan siswa- siswa SMK yang bekerja sama dengan institusi dalam negeri dan beberapa perusahaan lokal dan nasional. Kandungan komponen lokal berkisar antara 50-90%. (wikipedia, 2012). Klaten :*Sebuah kabupaten di Provinsi Jawa Tengah. Ibukotanya adalah Kota Klaten. Kabupaten ini berbatasan dengan Kabupaten Boyolali di utara, Kabupaten Sukoharjo di timur, serta Provinsi Daerah Istimewa Yogyakarta di selatan dan barat. (wikipedia, 2012). *Wilayah dimana akan dibuatnya Pusat DIKLAT Mobil Nasional ESEMKA. (Hasil Analisis Penulis, 2012). 1 | P a g e Pengertian Pusat DIKLAT Mobil Nasional ESEMKA di Klaten adalah sebuah pusat pendidikan dan pelatihan (perakitan, penjualan, promosi, informasi, modifikasi) mobil nasional bagi pelajar SMK. 1.3. Latar Belakang 1.3.1. Sejarah Industri Mobil Di Indonesia Perkembangan industri otomotif di Indonesia didorong oleh kebijakan Pemerintah yang mengatur sektor tersebut, kemajuan teknologi dan situasi ekonomi. Industri otomotif di Indonesia mulai berkembang pada tahun 1970, ketika itu Pemerintah Indonesia mengeluarkan beberapa kebijakan untuk mendukung industri otomotif di Indonesia seperti SK Menteri Perindustrian No.307/M/SK/8/76, SK Menteri Perindustrian No.231/M/SK/11/78 dan SK Menteri Perindustrian No.168/M/SK/9/79. -
Hand-In-Hand 2008
2008 Foreword Promoting the Sound Development of the ASEAN Automotive Industry The history of steadily expanding cooperative The past several years have seen the motor ties between member companies of the Japan industries in ASEAN neighboring countries Automobile Manufacturers Association (JAMA) increasing their competitive strength, which and their ASEAN partners is now close to half a underscores the urgency of greater global century old. competitiveness for ASEAN's automotive sector. With this goal in mind, there are high hopes that Those years were marked by some difficult ASEAN will further promote regional integration times―the Asian economic crisis of 1997, for at the earliest possible time. example―but throughout, JAMA members remained firmly committed to ASEAN, ASEAN is making bold moves to surmount the consistently striving, through automobile hurdles on the path to greater growth. Such production, sales, and exports, to advance moves include the abolition of regional tariffs, investment, create jobs, and transfer technology. harmonization of automotive technical This booklet outlines the more recent activities of regulations, mutual recognition of certification, JAMA and its member companies in the ASEAN the streamlining of customs procedures and region. distribution systems, the fostering of supporting industries and human resources, the promotion In 2007, new vehicle sales in the ASEAN market of safety, greater environmental protection, and (Indonesia, Malaysia, the Philippines, Singapore, other strategies aimed at promoting -
Automotive Electronics in North America
Automotive Electronics in North America Primary Report Volume I June 1990 "^^^^^ / Morris Kindig> Project Director Thomas Black Associate Editor/Senior Associate V ^J::^^_ "dJy-^^^^ Dennis D^r^ Database/Senior Associate Research/Senior Associate The content of this report represents our interpretation and analysis of information generally avail able to the public or released by knowledgeable individuals in'the subject industry, but is not guaranteed as to accuracy or completeness. It does not contain material provided to us in confidence by our clients. This information is not furnished in connection with a sale or offer to sell securities, or in connec tion with the solicitation of an offer to buy securities. This firm and its parent and/or their officers, stockholders, or members of their families may, from time to time, have a long or short position in the securities mentioned and may sell or buy such securities. Printed in the United States of America. All rights reserved. No part of this publication may be reproduced, stored in retrieval systems, or transmitted, in any form or by any means—mechanical, elec tronic, photocopying, duplicating, microfilming, videotape, or otherwise—without the prior written per mission of the publisher. © 1990 Dataquest Incorporated Dataquest - Automotive Electronics in North America (c) TABLE OF CONTENTS Introduction. Objective erf ^ Study 1 Scope of the Study 1 Geographic Coverage 1 Assumpfcns 1 Definition of Terms 2 Definition of Cfeitegories 3 Vefiide Categories 3 Bectronic !\/lodule/System Categories 3 Model Year/Calendar Year Conversion 5 Methodology. Database Definition 7 Database Structure 7 Datatase Information 8 Primary Research 9 Secondary Research 10 Market Analysis. -
Century Yuasa 57Mf 530 Calcium Battery
CENTURY YUASA 57MF 530 CALCIUM BATTERY MAJOR APPLICATIONS Manufacturer Model Service DAIHATSU Applause BATTERY DAIHATSU Applause BATTERY DAIHATSU Charade BATTERY DAIHATSU Charade BATTERY DAIHATSU Cuore BATTERY DAIHATSU Handivan BATTERY DAIHATSU Mira, Applause BATTERY DAIHATSU Move BATTERY DAIHATSU Pyzar BATTERY DAIHATSU Sirion BATTERY DAIHATSU Terios BATTERY DAIHATSU TRV BATTERY DAIHATSU YRV BATTERY FORD Econovan BATTERY FORD Laser BATTERY FORD Spectron BATTERY HOLDEN Cruze BATTERY HONDA Civic BATTERY HONDA Jazz BATTERY ISUZU Aska BATTERY ISUZU Big Horn BATTERY KIA Picanto BATTERY KIA Pride BATTERY MAZDA 2 BATTERY MAZDA 626 BATTERY MAZDA Astina BATTERY MAZDA Autozam BATTERY MAZDA Carol BATTERY MAZDA E2000 BATTERY MAZDA E2200 BATTERY MAZDA Eunos BATTERY MITSUBISHI Galant BATTERY MITSUBISHI Lancer BATTERY MITSUBISHI Minica BATTERY MITSUBISHI Minicab BATTERY MITSUBISHI Mirage BATTERY NISSAN Cube BATTERY NISSAN Escargot BATTERY NISSAN Micra BATTERY NISSAN NX Coupe BATTERY NISSAN Primera BATTERY NISSAN Primera BATTERY NISSAN Pulsar BATTERY NISSAN Pulsar BATTERY NISSAN Sentra BATTERY NISSAN Serena BATTERY NISSAN Silvia BATTERY NISSAN Stagea BATTERY NISSAN Wingroad BATTERY NISSAN Wingroad BATTERY SUBARU Impreza BATTERY SUBARU Liberty BATTERY SUBARU Outback BATTERY SUBARU Rex BATTERY SUBARU Sambar BATTERY SUBARU Vivio BATTERY SUZUKI Alto BATTERY SUZUKI Alto BATTERY SUZUKI Baleno BATTERY SUZUKI Cappuccino BATTERY SUZUKI Cappuccino BATTERY SUZUKI Cervo BATTERY SUZUKI Cultus BATTERY SUZUKI Ignis BATTERY SUZUKI Jimny BATTERY SUZUKI Jimny BATTERY SUZUKI Liana BATTERY SUZUKI Samurai BATTERY SUZUKI SUZUKI BATTERY SUZUKI Vitara BATTERY TOYOTA Alteza BATTERY TOYOTA Corolla Corsa Tercel BATTERY TOYOTA Corolla Levin Sprinter BATTERY TOYOTA Starlet BATTERY. -
Statistik Pencemaran Dan Kerusakan Lingkungan
Hasil Pengukuran Kualitas Udara Ambien Tepi Jalan Raya Rata-Rata Karbon Monoksida (CO) Tahun 2017–2019 Kualitas Udara Tepi Jalan Raya Baku Mutu (Roadside Monitoring) No Kota Kategori Kota Rata-Rata CO (BM 10.000) (μg/Nm3) 2017 2018 2019 1 2 3 8 9 10 11 1 BANDUNG Metropolitan - - - 10,000 2 BEKASI Metropolitan - 1,913 - 10,000 3 DEPOK Metropolitan - - 6,313 10,000 4 JAKARTA BARAT Metropolitan 6,223 - 5,468 10,000 5 JAKARTA PUSAT Metropolitan 496 1,402 4,707 10,000 6 JAKARTA SELATAN Metropolitan 1,402 1,595 4,533 10,000 7 JAKARTA TIMUR Metropolitan 8,509 1,277 629 10,000 8 JAKARTA UTARA Metropolitan 7,366 1,651 3,053 10,000 9 MAKASSAR Metropolitan 305 1,277 859 10,000 10 MEDAN Metropolitan - - - 10,000 11 PALEMBANG Metropolitan 4,303 3,940 - 10,000 12 SEMARANG Metropolitan - 2,338 3,970 10,000 13 SURABAYA Metropolitan - - - 10,000 14 TANGERANG Metropolitan - - 3,666 10,000 1 BALIKPAPAN Besar - 1,336 4,321 10,000 2 BANDAR LAMPUNG Besar - - - 10,000 3 BANJARMASIN Besar - 3,817 458 10,000 4 BOGOR Besar - - - 10,000 5 CIMAHI Besar - 1,915 - 10,000 6 DENPASAR Besar 4,230 3,964 4,642 10,000 7 KOTA BATAM Besar - - 3,473 10,000 8 MALANG Besar - - 1,214 10,000 9 MANADO Besar 1,309 - - 10,000 10 PADANG Besar - - - 10,000 11 PEKAN BARU Besar - - - 10,000 12 PONTIANAK Besar - - 2,978 10,000 13 SAMARINDA Besar - 2,497 1,270 10,000 14 SURAKARTA Besar - 1,654 4,711 10,000 15 TANGERANG SELATAN Besar - - 2,826 10,000 1 Evaluasi Kualitas Udara Perkotaan (EKUP) 16 YOGYAKARTA Besar 6,757 - 113 10,000 1 AMBON Sedang - - - 10,000 2 BANDA ACEH Sedang - - - 10,000 3 BENGKULU Sedang - - - 10,000 4 GORONTALO Sedang - 4,064 4,533 10,000 5 JAMBI Sedang - 941 6,072 10,000 6 JAYAPURA Sedang - - - 10,000 7 KENDARI Sedang - - - 10,000 8 KOTA TERNATE Sedang - - - 10,000 9 KUPANG Sedang - - - 10,000 10 MAMUJU Kecil - - - 10,000 11 MANOKWARI Kecil - - - 10,000 12 MATARAM Sedang - - - 10,000 13 PALANGKA RAYA Sedang - - - 10,000 14 PALU Sedang - - - 10,000 15 PANGKAL PINANG Sedang - - - 10,000 16 SERANG Sedang 4,513 - - 10,000 17 TANJUNG PINANG Sedang - - - 10,000 Sumber: Dit. -
Riding Southeast Asia's Automotive Highway
Strategies to steer through Southeast Asia’s promising automotive market November 2015 Riding Southeast Asia’s automotive highway In this paper 2 Southeast Asia’s motoring potential 3 An uneven road to growth 4 Dual carriageway – Regional manufacturing hub and local sales 7 Bumps in the road – Volatility and complexity 8 Navigating Growth Markets 9 Strategies to steer through complexity 15 Cambodia, Laos, Myanmar, Vietnam (CLMV) – The next automotive frontiers www.pwc.com/gmc Riding Southeast Asia’s automotive highway The region as a whole has low levels of car Following a few sluggish years, the global ownership and many first-time car buyers. It is automotive scene is starting to look up, most expected that many two-wheeler owners will notably marked by an increase in M&A activity eventually convert to four-wheeled vehicles, in 2014. According to PwC’s automotive analyst forming a large group of first-time buyers as group, Autofacts, global production is set to rise affluence grows. Many potential new drivers in the by 22.3m units between 2014 and 2021, at an region still own two-wheelers, with motorcycle annual compounded growth rate (CAGR) of 3.4%.1 penetration rates at over 80% in Indonesia, Whilst the BRIC markets have previously led global Thailand, Vietnam and Malaysia5. In a study growth, car sales have dipped 20% to date since conducted by the Pew Research Centre last year, December last year, due to slowing growth in China car owners accounted for less than 10% of the and declining sales in Russia and Brazil, while populations in Indonesia, the Philippines and newer growth markets take the lead. -
Edition 4 Edition 4 Edition
ABN 97 097 993 283 PO Box 339 OIL SEALS Hornsby NSW 1630 Australia Edition 4 Edition 4 Distributed by. TECHNICAL SUPPORT Wherever you are, Motospecs technical support is only a phone call away. The Technical Support Line can provide information on vehicle fitment, product range and latest application listings. If assistance is required, please call . 1800 245 748 (free call) Monday to Friday 8.00am-5.00pm (Eastern Standard Time) or fax: 02 9847 5757 or email: [email protected] www.motospecs.com.au To ensure you receive a quick response to your question, please have the following information at hand: • Make / Model / Year or build date, chassis number (if applicable). • Product name. • Product part number on pack and batch code / production date on label. Kelpro Oil Seals are sourced only from approved manufacturers globally, using guidelines set out in our QS9000 Certification. WARRANTY Motospecs recognises the importance of customer confidence and satisfaction in the quality of its products. Kelpro Oil Seals are warranted against faulty materials and workmanship when used for their designated purpose for a period of two years or 40,000 km from date of fitment, whichever occurs first. Kelpro Oil Seal warranty does not cover faulty fitment, damage caused by contamination or incorrect application. CLAIMS must be submitted through the distributor accompanied by the faulty product, proof of purchase and the reason for the failure. CREDIT for items supplied as ordered will be at the discretion of Motospecs. FREIGHT charges on returns will be borne by the customer. COPYRIGHT NOTICE 2007 Motospecs is the owner of Copyright in this production, including layout, drawings, photographs, text and part number systems.