Brushless and Brush Generators
Total Page:16
File Type:pdf, Size:1020Kb
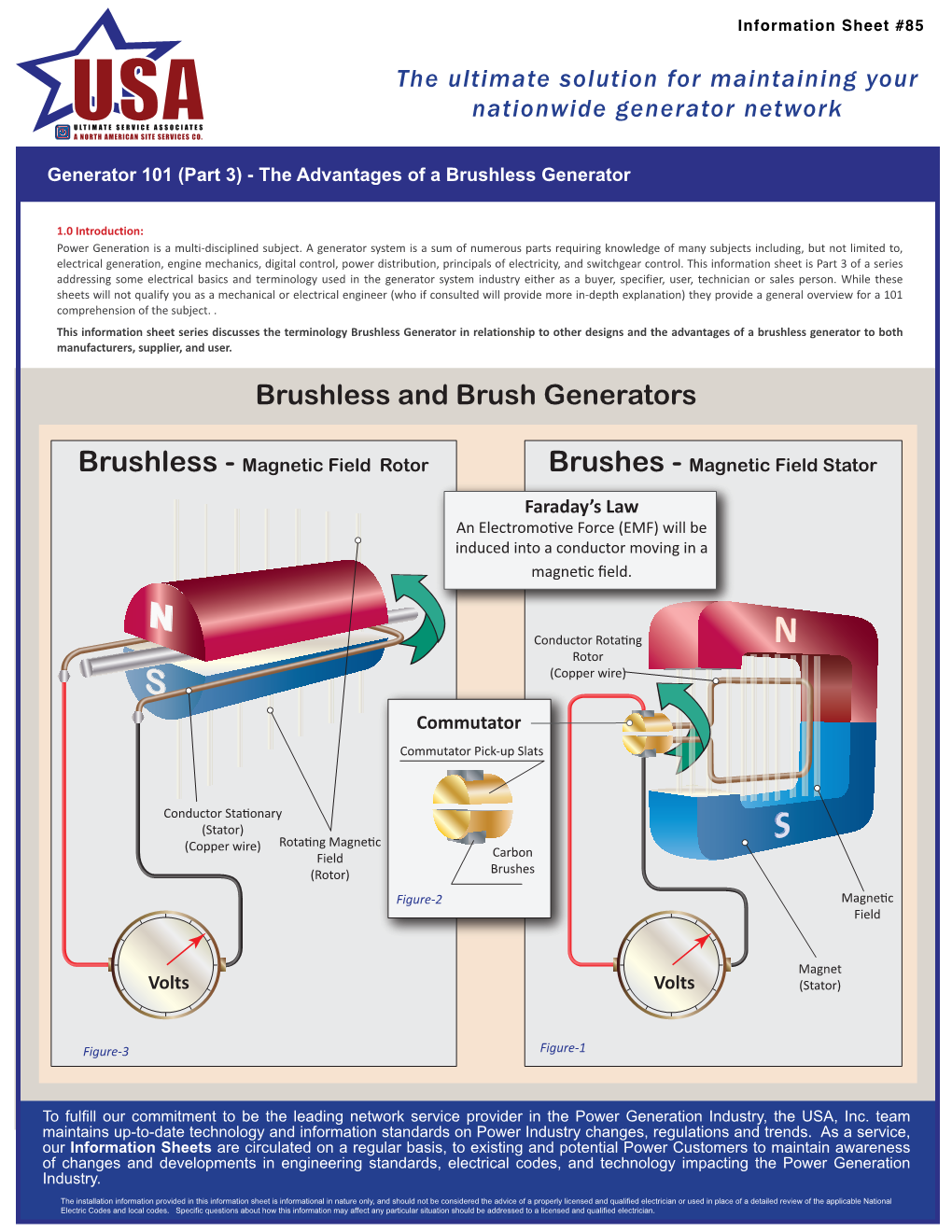
Load more
Recommended publications
-
Brushes for Aircraft Applications
Brushes for Aircraft Applications Bob Nuckolls AeroElectric Connection April 1993 Updated August 2003 Several times a year I receive a call or letter asking where one be 1000 hours or more of continuous motor operation! We obtains "aircraft" grade brushes for an alternator or generator. were hard pressed to demonstrate more than 600 hours from One of my readers called recently to say he had been verbally any grade of brush. This little motor runs at 22,000 rpm! There keel-hauled by an engineer with an alternator manufacturing were simply no brush products available that would last 1000 company. The reader had confessed to considering a plain hours at those commutator surface speeds. vanilla brush for use in the alternator on his RV-4. The program was nearly scuttled when project managers There's a lot of "hangar mythology" about what constitutes became fixated upon reaching the 1000-hour goal. We aircraft ratings in components. We all know that much of what researched our service records for the same motor supplied in is deemed "aircraft" today are the same products certified onto other forms for over 10 years. airplanes 30-50 years ago. Many developers and suppliers consider aviation a "dying" market; few are interested in Clutches and brakes turned out to be the #1 service problem. researching and qualifying new products. However, Brake problems occurred at 300 to 500 flight hours, not motor automotive markets continue to advance in every technology. operating hours. Given that trim operations might run a pitch It is sad to note that many products found on cars today far trim actuator perhaps 3 minutes total per flight cycle, 1000 exceed the capabilities and quality of similar hardware found hours of flight on a Lear might put less than 50 hours on certified airplanes. -
DRM105, PM Sinusoidal Motor Vector Control with Quadrature
PM Sinusoidal Motor Vector Control with Quadrature Encoder Designer Reference Manual Devices Supported: MCF51AC256 Document Number: DRM105 Rev. 0 09/2008 How to Reach Us: Home Page: www.freescale.com Web Support: http://www.freescale.com/support USA/Europe or Locations Not Listed: Freescale Semiconductor, Inc. Technical Information Center, EL516 2100 East Elliot Road Tempe, Arizona 85284 1-800-521-6274 or +1-480-768-2130 www.freescale.com/support Europe, Middle East, and Africa: Freescale Halbleiter Deutschland GmbH Technical Information Center Information in this document is provided solely to enable system and Schatzbogen 7 software implementers to use Freescale Semiconductor products. There are 81829 Muenchen, Germany no express or implied copyright licenses granted hereunder to design or +44 1296 380 456 (English) fabricate any integrated circuits or integrated circuits based on the +46 8 52200080 (English) information in this document. +49 89 92103 559 (German) +33 1 69 35 48 48 (French) www.freescale.com/support Freescale Semiconductor reserves the right to make changes without further notice to any products herein. Freescale Semiconductor makes no warranty, Japan: representation or guarantee regarding the suitability of its products for any Freescale Semiconductor Japan Ltd. particular purpose, nor does Freescale Semiconductor assume any liability Headquarters arising out of the application or use of any product or circuit, and specifically ARCO Tower 15F disclaims any and all liability, including without limitation consequential or 1-8-1, Shimo-Meguro, Meguro-ku, incidental damages. “Typical” parameters that may be provided in Freescale Tokyo 153-0064 Semiconductor data sheets and/or specifications can and do vary in different Japan applications and actual performance may vary over time. -
DC Motor Workshop
DC Motor Annotated Handout American Physical Society A. What You Already Know Make a labeled drawing to show what you think is inside the motor. Write down how you think the motor works. Please do this independently. This important step forces students to create a preliminary mental model for the motor, which will be their starting point. Since they are writing it down, they can compare it with their answer to the same question at the end of the activity. B. Observing and Disassembling the Motor 1. Use the small screwdriver to take the motor apart by bending back the two metal tabs that hold the white plastic end-piece in place. Pull off this plastic end-piece, and then slide out the part that spins, which is called the armature. 2. Describe what you see. 3. How do you think the motor works? Discuss this question with the others in your group. C. Mounting the Armature 1. Use the diagram below to locate the commutator—the split ring around the motor shaft. This is the armature. Shaft Commutator Coil of wire (electromagnetic) 2. Look at the drawing on the next page and find the brushes—two short ends of bare wire that make a "V". The brushes will make electrical contact with the commutator, and gravity will hold them together. In addition the brushes will support one end of the armature and cradle it to prevent side- to-side movement. 1 3. Using the cup, the two rubber bands, the piece of bare wire, and the three pieces of insulated wire, mount the armature as in the diagram below. -
Electricity’ Contribute to the Second Industrial Revolution (I): the Power Engines
Delft University of Technology How did the General Purpose Technology ’Electricity’ contribute to the Second Industrial Revolution (I): The Power Engines. van der Kooij, Bauke Publication date 2016 Document Version Final published version Citation (APA) van der Kooij, B. (2016). How did the General Purpose Technology ’Electricity’ contribute to the Second Industrial Revolution (I): The Power Engines. Important note To cite this publication, please use the final published version (if applicable). Please check the document version above. Copyright Other than for strictly personal use, it is not permitted to download, forward or distribute the text or part of it, without the consent of the author(s) and/or copyright holder(s), unless the work is under an open content license such as Creative Commons. Takedown policy Please contact us and provide details if you believe this document breaches copyrights. We will remove access to the work immediately and investigate your claim. This work is downloaded from Delft University of Technology. For technical reasons the number of authors shown on this cover page is limited to a maximum of 10. How did the General Purpose Technology ’Electricity’ contribute to the Second Industrial Revolution (I): The Power Engines. B.J.G.van der Kooij Guest at the University of Technology, Delft, Netherlands Jaffalaan 5, 2628 BX, Delft, the Netherlands Abstract The concept of the General Purpose Technology (GPT) of the late 1990s is a culmination of many evolutionairy views in innovation-thinking. By definition the GPT considers the technical, social, and economic effects of meta-technologies like steam-technology and electric technology. -
Design Procedure of a Permanent Magnet D.C. Commutator Motor
International Journal of Engineering Research and Technology. ISSN 0974-3154 Volume 9, Number 1 (2016), pp. 53-60 © International Research Publication House http://www.irphouse.com Design Procedure of A Permanent Magnet D.C. Commutator Motor Ritunjoy Bhuyan HOD Electrical Engineering, HRH The Prince of Wales Institute of Engg & Technology (Govt.), Jorhat, Assam, India. Abstract Electrical machine with electro magnet as excitation system many problems out of which, less efficiency is a major one. Self excited dc machine has to sacrifice some power for excitation system as a result, power available for useful work become less. This problem can be solved to some extent whatever may be the amount , by using permanent magnet for the excitation system of dc machine and there by contributing towards the conservation of conventional energy sources which are alarmingly decrease day by day . Using of permanent magnet in the electrical machine helps in burning of less conventional fossil fuel and contributes indirectly in conservation of air- pollution free environment. With permanent magnet dc motor, the efficiency of the machine also rise up considerably. This paper is an effort to give a computer aided design procedure of permanent magnet dc motor. Keywords: permanent magnet dc motor, yoke, pole pitch, commutator, magnetic loading, electric loading, output coefficient. Introduction It can be stated without any dispute that for the ever developing modern civilization electric motor become an unavoidable part both in industrial product as well as domestic applications. But ever since the growing threat of running out of the conventional energy source used by the mankind by the middle of the next century, the scientists have very desperately engaged themselves for last few decades in molding suitable devices for conservation of different form of conventional energy. -
6.061 Class Notes, Chapter 11: DC (Commutator) and Permanent
Massachusetts Institute of Technology Department of Electrical Engineering and Computer Science 6.061 Introduction to Power Systems Class Notes Chapter 11 DC (Commutator) and Permanent Magnet Machines ∗ J.L. Kirtley Jr. 1 Introduction Virtually all electric machines, and all practical electric machines employ some form of rotating or alternating field/current system to produce torque. While it is possible to produce a “true DC” machine (e.g. the “Faraday Disk”), for practical reasons such machines have not reached application and are not likely to. In the machines we have examined so far the machine is operated from an alternating voltage source. Indeed, this is one of the principal reasons for employing AC in power systems. The first electric machines employed a mechanical switch, in the form of a carbon brush/commutator system, to produce this rotating field. While the widespread use of power electronics is making “brushless” motors (which are really just synchronous machines) more popular and common, com mutator machines are still economically very important. They are relatively cheap, particularly in small sizes, they tend to be rugged and simple. You will find commutator machines in a very wide range of applications. The starting motor on all automobiles is a series-connected commutator machine. Many of the other electric motors in automobiles, from the little motors that drive the outside rear-view mirrors to the motors that drive the windshield wipers are permanent magnet commutator machines. The large traction motors that drive subway trains and diesel/electric locomotives are DC commutator machines (although induction machines are making some inroads here). -
Electromagnetic Coil Gun Launcher System
ISSN(Online): 2319-8753 ISSN (Print) : 2347-6710 International Journal of Innovative Research in Science, Engineering and Technology (A High Impact Factor, Monthly, Peer Reviewed Journal) Visit: www.ijirset.com Vol. 8, Issue 3, March 2019 Electromagnetic Coil Gun Launcher System Prof. Yogesh Fatangde1 Swapnil Biradar2, Aniket Bahmne3, Suraj Yadav4, Ajay Yadav5 Department of Mechanical Engineering, RMD Sinhgad Technical Campus, Savitribai Phule Pune University, Pune, Maharashtra, India1 ABSTRACT: In our present time, a study was undertaken to determine if ground based electromagnetic acceleration system could provide a useful reduction in launching cost with current large chemical boosters, while increasing launch safety and reliability. An electromagnetic launcher (EML) system accelerates and launches a projectile by converting electric energy into kinetic energy. An EML system launches projectile by converting electric energy into kinetic energy. There are two types of EML system under development: rail gun and coil gun. A coil gun launches the projectile by magnetic force of electromagnetic coil. A higher velocity needs multiple stages of system, which make coil gun EML system longer. As a result installation cost is very high and it required large installation site for EML. So, we present coil gun EML system with new structure and arrangement for multiple electromagnetic coils to reduce the length of system KEYWORDS: EML, coil gun, Electromagnetic launcher, suck back effect I. INTRODUCTION In chemical launcher systems such as firearms and satellite launchers, chemical explosive energy is converted into mechanical dynamic energy. The system must be redesigned and remanufactured if the target velocity of the projectile is changed. In addition, such systems are not eco-friendly. -
Construction Set Curriculum
Construction Set Curriculum Grades 8-12 Student Edition Center for Mathematics Science and Technology Center for Renewable Energy Illinois State University Normal, Illinois 1 Construction Set Curriculum Grades 8 - 12 Nearly everything done by humans re- quires some type of energy. Of course, manufacturing, transportation, and con- struction require energy, but also the “little things,” like heating your food and charging your cell phone. Energy allows things to be done. Imagine the changes necessary if gasoline was suddenly unavailable for your car, or electricity was shut off at your school. Modern society could not function without energy. Nearly all work was accomplished entirely by muscle power until relatively recent times. The domestication of animals helped to make work easier and more efficient, but both humans and animals have limited power and get tired easily. Inventors have always been looking for ways to produce power that is reliable and inexpensive. At the end of the Roman era, by about 200 B.C., Europeans were using waterwheels to crush grain, saw wood, and do many more tasks. 1200 years later in 1000 A.D., the Dutch had harnessed the power of wind to do many of the same tasks as well as pump water out of manmade basins to expose land. https://www.google.com/imgres?imgurl=https%3A%2F%2Fi.redd.it%2F7en51y8osrlz.jpg&imgrefurl=https%3A%2F%2Fwww.reddit.com%2Fr%2Fancientrome% 2Fcomments%2F6zzw4v%2Fthe_norias_of_hama_tech_referenced_in_painting% 2F&tbnid=cFD679meUV8DfM&vet=12ahUKEwjpnKP9r7vnAhVBYa0KHWLlCCAQMygJegQIARBR..i&docid=Yg5zCQjBvV2lmM&w=972&h=648&itg=1&q=roman% 20water%20wheel&hl=en&ved=2ahUKEwjpnKP9r7vnAhVBYa0KHWLlCCAQMygJegQIARBR 2 Your Horsepower When James Watt first invented the steam engine, he was naturally asked how much power it pro- duced. -
Vector Control of Three Phase Induction Motor
International Research Journal of Engineering and Technology (IRJET) e-ISSN: 2395-0056 Volume: 06 Issue: 07 | July 2019 www.irjet.net p-ISSN: 2395-0072 Vector Control of Three Phase Induction Motor Prof. Jisha Kuruvila1, Abhijith S2, John Joseph3, Ajmal U P4, J Jaya Sankar5 1Assistant Professor, Dept. of Electrical and Electronics Engineering, Mar Athanasius College of Engineering, Kothamangalam, Kerala, India 2,3,4,5Student, Dept. of Electrical and Electronics Engineering, Mar Athanasius College of Engineering, Kothamangalam, Kerala, India ---------------------------------------------------------------------***--------------------------------------------------------------------- Abstract - High dynamic performance, which is obtained separately excited DC motor, and achieve the same quality of from DC motors, became achievable from induction motors dynamic performance. As for DC machines, torque control in with the advances in power semiconductors, digital signal AC machines is achieved by controlling the motor currents. processors and development in control techniques. By using field oriented control, torque and flux of the induction motors However, in contrast to a DC machine, in AC machine, both can be controlled independently as in DC motors. The control the phase angle and the modulus of the current has to be performance of field oriented induction motor drive greatly controlled, or in other words, the current vector has to be depends on the stator flux estimation. Vector control, also controlled. This is the reason for the terminology vector called field-oriented control, is a variable-frequency drive control. control method in which the stator currents of a three-phase AC electric motor are identified as two orthogonal components 2. FIELD ORIENTATION CONTROL that can be visualized with a vector. One component defines the magnetic flux of the motor, the other the torque. -
Motor Actuators Basics
Motor Actuators Basics - 1 - Note: All specifications and other information are not guaranteed and are subject to change without notice. Prior to any new usage of JE motor actuators it is recommended to contact Johnson Electric. All information below and content of links are subject to the disclaimer of the Johnson Electric website - 2 - Contents Overview ....................................................................................................................................................................... 4 Classification ............................................................................................................................................................. 5 DC Motors ................................................................................................................................................................. 6 Universal Motors ....................................................................................................................................................... 7 BLDC Motors ............................................................................................................................................................. 8 Synchronous Motors ................................................................................................................................................. 9 Stepper Motors ........................................................................................................................................................ 10 Shaded -
Brush DC Motors Turning More Advanced
Brush DC Motors wearing process by targeting brush assemblies, brush size, and brush materials. turning More Advanced The traditional method for mounting brushes in DC motor assem- blies has been to solder the brushes onto standard cantilever “Off-the-shelf” brush-commutated DC motors typically springs to enable the required constant contact with the commu- tend to serve as a “starting point,” because virtually every tator. The conventional spring design, however, exhibits inherent application for a motor carries particular design and drawbacks as force levels diminish over time, often resulting in performance criteria to be accommodated. premature motor failure. Motor manufacturers usually address these criteria by This problem can be overcome by housing brushes within a customizing products with components to satisfy the specially designed cartridge and utilizing torsion springs to ensure demands. An end-user thereby gains a motor designed to desired even force over the life of a motor. perform as required and, in the process, others ultimately may benefit if and when a custom component becomes The cartridge brush assembly fits into the motor base and “standard.” Many innovations in motor technology, in fact, consists of a two-piece, high-temperature plastic snap-together have originated as specific solutions to specific customer assembly in which each of two brushes is seated securely within its challenges. own specially constructed slot. This cartridge design restricts the brushes to traveling in a track in a desired linear motion. The design further can provide for an ideal Innovations have further been driven by overall marketplace needs. region of pressure for brushes to withstand the detrimental effects As examples, motor manufacturers have been obliged to offer more of mechanical wear. -
Basics of DC Motors
You’ve got a DC (direct current) motor down and you need it repaired, but you aren’t just responsible for keeping things running but keeping the repairs within budget. How can you tell if you are getting a reasonable repair quote if you don’t know what kind of repairs are common for DC motors? That’s the purpose of this article: to provide solid facts so you can make an informed decision about repairing that DC motor that has brought production to a grinding halt. Basics of DC Motors DC motors can be found in elevators, hoists, steel rolling mill drives, turntables, conveyor belts, mixers, printing presses, extruders, and more. These motors used direct current (DC) as opposed to alternating current (AC) and their speed can be adjusted by either adjusting the static field current or the voltage that is applied to the armature. Types of DC Motors The four types of DC motors are shunt wound motors, series wound motors, permanent magnet, and compound motors. Shunt motors are typically used for speed regulation made possible because the shunt field can be excited separately from the armature windings. Series motors generate excellent starting torque but don’t offer much in the way of speed regulation. Permanent magnetic motors are typically limited to low horsepower applications. Compound motors offer a good starting torque but don’t do well in variable speed applications. You also have other variations of DC motors that are unique variations and designs of these 4 types. Basic Components of a DC Motor DC motors will have a field frame that contains the field coils and an armature with windings wrapped around a core made of iron.