Eastern Michigan
Total Page:16
File Type:pdf, Size:1020Kb
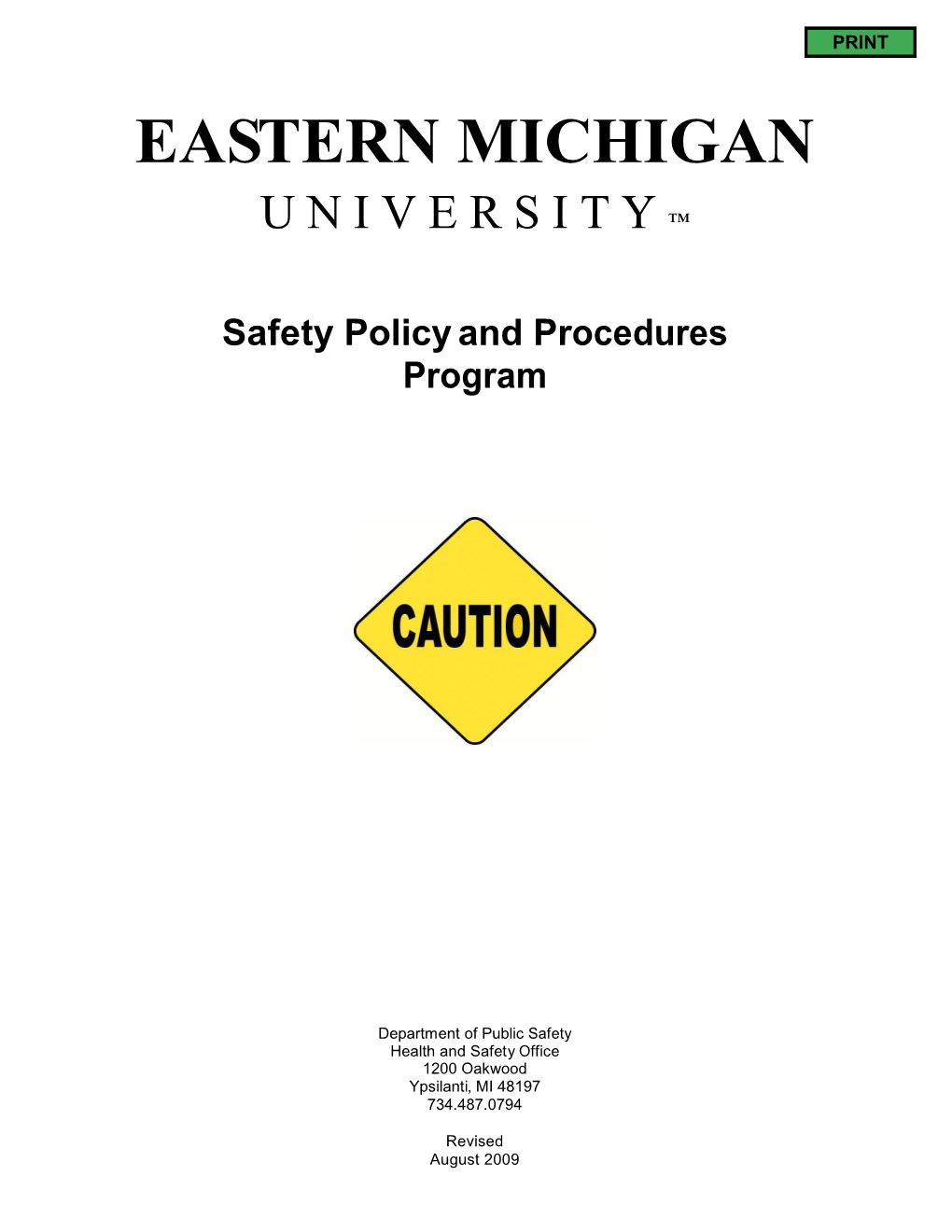
Load more
Recommended publications
-
Radio Stations in Michigan Radio Stations 301 W
1044 RADIO STATIONS IN MICHIGAN Station Frequency Address Phone Licensee/Group Owner President/Manager CHAPTE ADA WJNZ 1680 kHz 3777 44th St. S.E., Kentwood (49512) (616) 656-0586 Goodrich Radio Marketing, Inc. Mike St. Cyr, gen. mgr. & v.p. sales RX• ADRIAN WABJ(AM) 1490 kHz 121 W. Maumee St. (49221) (517) 265-1500 Licensee: Friends Communication Bob Elliot, chmn. & pres. GENERAL INFORMATION / STATISTICS of Michigan, Inc. Group owner: Friends Communications WQTE(FM) 95.3 MHz 121 W. Maumee St. (49221) (517) 265-9500 Co-owned with WABJ(AM) WLEN(FM) 103.9 MHz Box 687, 242 W. Maumee St. (49221) (517) 263-1039 Lenawee Broadcasting Co. Julie M. Koehn, pres. & gen. mgr. WVAC(FM)* 107.9 MHz Adrian College, 110 S. Madison St. (49221) (517) 265-5161, Adrian College Board of Trustees Steven Shehan, gen. mgr. ext. 4540; (517) 264-3141 ALBION WUFN(FM)* 96.7 MHz 13799 Donovan Rd. (49224) (517) 531-4478 Family Life Broadcasting System Randy Carlson, pres. WWKN(FM) 104.9 MHz 390 Golden Ave., Battle Creek (49015); (616) 963-5555 Licensee: Capstar TX L.P. Jack McDevitt, gen. mgr. 111 W. Michigan, Marshall (49068) ALLEGAN WZUU(FM) 92.3 MHz Box 80, 706 E. Allegan St., Otsego (49078) (616) 673-3131; Forum Communications, Inc. Robert Brink, pres. & gen. mgr. (616) 343-3200 ALLENDALE WGVU(FM)* 88.5 MHz Grand Valley State University, (616) 771-6666; Board of Control of Michael Walenta, gen. mgr. 301 W. Fulton, (800) 442-2771 Grand Valley State University Grand Rapids (49504-6492) ALMA WFYC(AM) 1280 kHz Box 669, 5310 N. -
Broadcasting Telecasting
YEAR 101RN NOSI1)6 COLLEIih 26TH LIBRARY énoux CITY IOWA BROADCASTING TELECASTING THE BUSINESSWEEKLY OF RADIO AND TELEVISION APRIL 1, 1957 350 PER COPY c < .$'- Ki Ti3dddSIA3N Military zeros in on vhf channels 2 -6 Page 31 e&ol 9 A3I3 It's time to talk money with ASCAP again Page 42 'mars :.IE.iC! I ri Government sues Loew's for block booking Page 46 a2aTioO aFiE$r:i:;ao3 NARTB previews: What's on tap in Chicago Page 79 P N PO NT POW E R GETS BEST R E SULTS Radio Station W -I -T -H "pin point power" is tailor -made to blanket Baltimore's 15 -mile radius at low, low rates -with no waste coverage. W -I -T -H reaches 74% * of all Baltimore homes every week -delivers more listeners per dollar than any competitor. That's why we have twice as many advertisers as any competitor. That's why we're sure to hit the sales "bull's -eye" for you, too. 'Cumulative Pulse Audience Survey Buy Tom Tinsley President R. C. Embry Vice Pres. C O I N I F I I D E I N I C E National Representatives: Select Station Representatives in New York, Philadelphia, Baltimore, Washington. Forloe & Co. in Chicago, Seattle, San Francisco, Los Angeles, Dallas, Atlanta. RELAX and PLAY on a Remleee4#01%,/ You fly to Bermuda In less than 4 hours! FACELIFT FOR STATION WHTN-TV rebuilding to keep pace with the increasing importance of Central Ohio Valley . expanding to serve the needs of America's fastest growing industrial area better! Draw on this Powerhouse When OPERATION 'FACELIFT is completed this Spring, Station WNTN -TV's 316,000 watts will pour out of an antenna of Facts for your Slogan: 1000 feet above the average terrain! This means . -
Stations Coverage Map Broadcasters
820 N. Capitol Ave., Lansing, MI 48906 PH: (517) 484-7444 | FAX: (517) 484-5810 Public Education Partnership (PEP) Program Station Lists/Coverage Maps Commercial TV I DMA Call Letters Channel DMA Call Letters Channel Alpena WBKB-DT2 11.2 GR-Kzoo-Battle Creek WOOD-TV 7 Alpena WBKB-DT3 11.3 GR-Kzoo-Battle Creek WOTV-TV 20 Alpena WBKB-TV 11 GR-Kzoo-Battle Creek WXSP-DT2 15.2 Detroit WKBD-TV 14 GR-Kzoo-Battle Creek WXSP-TV 15 Detroit WWJ-TV 44 GR-Kzoo-Battle Creek WXMI-TV 19 Detroit WMYD-TV 21 Lansing WLNS-TV 36 Detroit WXYZ-DT2 41.2 Lansing WLAJ-DT2 25.2 Detroit WXYZ-TV 41 Lansing WLAJ-TV 25 Flint-Saginaw-Bay City WJRT-DT2 12.2 Marquette WLUC-DT2 35.2 Flint-Saginaw-Bay City WJRT-DT3 12.3 Marquette WLUC-TV 35 Flint-Saginaw-Bay City WJRT-TV 12 Marquette WBUP-TV 10 Flint-Saginaw-Bay City WBSF-DT2 46.2 Marquette WBKP-TV 5 Flint-Saginaw-Bay City WEYI-TV 30 Traverse City-Cadillac WFQX-TV 32 GR-Kzoo-Battle Creek WOBC-CA 14 Traverse City-Cadillac WFUP-DT2 45.2 GR-Kzoo-Battle Creek WOGC-CA 25 Traverse City-Cadillac WFUP-TV 45 GR-Kzoo-Battle Creek WOHO-CA 33 Traverse City-Cadillac WWTV-DT2 9.2 GR-Kzoo-Battle Creek WOKZ-CA 50 Traverse City-Cadillac WWTV-TV 9 GR-Kzoo-Battle Creek WOLP-CA 41 Traverse City-Cadillac WWUP-DT2 10.2 GR-Kzoo-Battle Creek WOMS-CA 29 Traverse City-Cadillac WWUP-TV 10 GR-Kzoo-Battle Creek WOOD-DT2 7.2 Traverse City-Cadillac WMNN-LD 14 Commercial TV II DMA Call Letters Channel DMA Call Letters Channel Detroit WJBK-TV 7 Lansing WSYM-TV 38 Detroit WDIV-TV 45 Lansing WILX-TV 10 Detroit WADL-TV 39 Marquette WJMN-TV 48 Flint-Saginaw-Bay -
New Solar Research Yukon's CKRW Is 50 Uganda
December 2019 Volume 65 No. 7 . New solar research . Yukon’s CKRW is 50 . Uganda: African monitor . Cape Greco goes silent . Radio art sells for $52m . Overseas Russian radio . Oban, Sheigra DXpeditions Hon. President* Bernard Brown, 130 Ashland Road West, Sutton-in-Ashfield, Notts. NG17 2HS Secretary* Herman Boel, Papeveld 3, B-9320 Erembodegem (Aalst), Vlaanderen (Belgium) +32-476-524258 [email protected] Treasurer* Martin Hall, Glackin, 199 Clashmore, Lochinver, Lairg, Sutherland IV27 4JQ 01571-855360 [email protected] MWN General Steve Whitt, Landsvale, High Catton, Yorkshire YO41 1EH Editor* 01759-373704 [email protected] (editorial & stop press news) Membership Paul Crankshaw, 3 North Neuk, Troon, Ayrshire KA10 6TT Secretary 01292-316008 [email protected] (all changes of name or address) MWN Despatch Peter Wells, 9 Hadlow Way, Lancing, Sussex BN15 9DE 01903 851517 [email protected] (printing/ despatch enquiries) Publisher VACANCY [email protected] (all orders for club publications & CDs) MWN Contributing Editors (* = MWC Officer; all addresses are UK unless indicated) DX Loggings Martin Hall, Glackin, 199 Clashmore, Lochinver, Lairg, Sutherland IV27 4JQ 01571-855360 [email protected] Mailbag Herman Boel, Papeveld 3, B-9320 Erembodegem (Aalst), Vlaanderen (Belgium) +32-476-524258 [email protected] Home Front John Williams, 100 Gravel Lane, Hemel Hempstead, Herts HP1 1SB 01442-408567 [email protected] Eurolog John Williams, 100 Gravel Lane, Hemel Hempstead, Herts HP1 1SB World News Ton Timmerman, H. Heijermanspln 10, 2024 JJ Haarlem, The Netherlands [email protected] Beacons/Utility Desk VACANCY [email protected] Central American Tore Larsson, Frejagatan 14A, SE-521 43 Falköping, Sweden Desk +-46-515-13702 fax: 00-46-515-723519 [email protected] S. -
Moving & Relocation Directory
Moving & Relocation Directory Ninth Edition A Reference Guide for Moving and Relocation, With Profi les for 121 U.S. Cities, Featuring Mailing Addresses, Local and Toll-Free Telephone Numbers, Fax Numbers, and Web Site Addresses for: • Chambers of Commerce, Government Offi ces, Libraries, and Other Local Information Resources (including Online Resources) • Suburban and Other Area Communities • Major Employers • Educational Institutions and Hospitals • Transportation Services • Utility and Local Telecommunications Companies • Banks and Shopping Malls • Newspapers, Magazines, and Radio & TV Stations • Attractions, Sports & Recreation and also Including Statistical, Demographic, and Other Data on Location, Climate and Weather, History, Economy, Education, Population, and Quality and Cost of Living Business Directories Inc 155 W. Congress, Ste. 200 Detroit, MI 48226 800-234-1340 • www.omnigraphics.com 1 Contents Please see page 4 for a complete list of the cities featured in this directory, together with references to the page on which each city’s listing begins. A state-by-state list of the cities begins on page 5. Abbreviations Used in This Directory . Inside Front Cover Introduction. 7 United States Time Zones Map . 10 Special Features 1. Where to Get Help For Moving . 12 2. Chambers of Commerce—City . 14 3. Chambers of Commerce—State . 17 4. Employment Agencies . 18 5. National Moving Companies . 24 6. Corporate Housing . 26 7. Self-Storage Facilities . 26 8. National Real Estate Companies . 27 9. State Realtors Associations . 28 10. Mileage Table . 30 11. Area Codes in State Order . 31 12. Area Codes in Numerical Order . 34 Moving & Relocation Directory . 37 Index of Cities & Counties . .1417 Radio Formats & Television Network Abbreviations . -
530 CIAO BRAMPTON on ETHNIC AM 530 N43 35 20 W079 52 54 09-Feb
frequency callsign city format identification slogan latitude longitude last change in listing kHz d m s d m s (yy-mmm) 530 CIAO BRAMPTON ON ETHNIC AM 530 N43 35 20 W079 52 54 09-Feb 540 CBKO COAL HARBOUR BC VARIETY CBC RADIO ONE N50 36 4 W127 34 23 09-May 540 CBXQ # UCLUELET BC VARIETY CBC RADIO ONE N48 56 44 W125 33 7 16-Oct 540 CBYW WELLS BC VARIETY CBC RADIO ONE N53 6 25 W121 32 46 09-May 540 CBT GRAND FALLS NL VARIETY CBC RADIO ONE N48 57 3 W055 37 34 00-Jul 540 CBMM # SENNETERRE QC VARIETY CBC RADIO ONE N48 22 42 W077 13 28 18-Feb 540 CBK REGINA SK VARIETY CBC RADIO ONE N51 40 48 W105 26 49 00-Jul 540 WASG DAPHNE AL BLK GSPL/RELIGION N30 44 44 W088 5 40 17-Sep 540 KRXA CARMEL VALLEY CA SPANISH RELIGION EL SEMBRADOR RADIO N36 39 36 W121 32 29 14-Aug 540 KVIP REDDING CA RELIGION SRN VERY INSPIRING N40 37 25 W122 16 49 09-Dec 540 WFLF PINE HILLS FL TALK FOX NEWSRADIO 93.1 N28 22 52 W081 47 31 18-Oct 540 WDAK COLUMBUS GA NEWS/TALK FOX NEWSRADIO 540 N32 25 58 W084 57 2 13-Dec 540 KWMT FORT DODGE IA C&W FOX TRUE COUNTRY N42 29 45 W094 12 27 13-Dec 540 KMLB MONROE LA NEWS/TALK/SPORTS ABC NEWSTALK 105.7&540 N32 32 36 W092 10 45 19-Jan 540 WGOP POCOMOKE CITY MD EZL/OLDIES N38 3 11 W075 34 11 18-Oct 540 WXYG SAUK RAPIDS MN CLASSIC ROCK THE GOAT N45 36 18 W094 8 21 17-May 540 KNMX LAS VEGAS NM SPANISH VARIETY NBC K NEW MEXICO N35 34 25 W105 10 17 13-Nov 540 WBWD ISLIP NY SOUTH ASIAN BOLLY 540 N40 45 4 W073 12 52 18-Dec 540 WRGC SYLVA NC VARIETY NBC THE RIVER N35 23 35 W083 11 38 18-Jun 540 WETC # WENDELL-ZEBULON NC RELIGION EWTN DEVINE MERCY R. -
“Where the Mix Is Perfect”: Voices
“WHERE THE MIX IS PERFECT”: VOICES FROM THE POST-MOTOWN SOUNDSCAPE by Carleton S. Gholz B.A., Macalester College, 1999 M.A., University of Pittsburgh, 2007 Submitted to the Graduate Faculty of The Arts and Sciences in partial fulfillment of the requirements for the degree of Doctor of Philosophy University of Pittsburgh 2011 UNIVERSITY OF PITTSBURGH SCHOOL OF ARTS AND SCIENCES This dissertation was presented by Carleton S. Gholz It was defended on April 11, 2011 and approved by Professor Brent Malin, Department of Communication Professor Andrew Weintraub, Department of Music Professor William Fusfield, Department of Communication Professor Shanara Reid-Brinkley, Department of Communication Dissertation Advisor: Professor Ronald J. Zboray, Department of Communication ii Copyright © by Carleton S. Gholz 2011 iii “WHERE THE MIX IS PERFECT”: VOICES FROM THE POST-MOTOWN SOUNDSCAPE Carleton S. Gholz, PhD University of Pittsburgh, 2011 In recent years, the city of Detroit’s economic struggles, including its cultural expressions, have become focal points for discussing the health of the American dream. However, this discussion has rarely strayed from the use of hackneyed factory metaphors, worn-out success-and-failure stories, and an ever-narrowing cast of characters. The result is that the common sense understanding of Detroit’s musical and cultural legacy tends to end in 1972 with the departure of Motown Records from the city to Los Angeles, if not even earlier in the aftermath of the riot / uprising of 1967. In “‘Where The Mix Is Perfect’: Voices From The Post-Motown Soundscape,” I provide an oral history of Detroit’s post-Motown aural history and in the process make available a new urban imaginary for judging the city’s wellbeing. -
Hadiotv EXPERIMENTER AUGUST -SEPTEMBER 75C
DXer's DREAM THAT ALMOST WAS SHASILAND HadioTV EXPERIMENTER AUGUST -SEPTEMBER 75c BUILD COLD QuA BREE ... a 2-FET metal moocher to end the gold drain and De Gaulle! PIUS Socket -2 -Me CB Skyhook No -Parts Slave Flash Patrol PA System IC Big Voice www.americanradiohistory.com EICO Makes It Possible Uncompromising engineering-for value does it! You save up to 50% with Eico Kits and Wired Equipment. (%1 eft ale( 7.111 e, si. a er. ortinastereo Engineering excellence, 100% capability, striking esthetics, the industry's only TOTAL PERFORMANCE STEREO at lowest cost. A Silicon Solid -State 70 -Watt Stereo Amplifier for $99.95 kit, $139.95 wired, including cabinet. Cortina 3070. A Solid -State FM Stereo Tuner for $99.95 kit. $139.95 wired, including cabinet. Cortina 3200. A 70 -Watt Solid -State FM Stereo Receiver for $169.95 kit, $259.95 wired, including cabinet. Cortina 3570. The newest excitement in kits. 100% solid-state and professional. Fun to build and use. Expandable, interconnectable. Great as "jiffy" projects and as introductions to electronics. No technical experience needed. Finest parts, pre -drilled etched printed circuit boards, step-by-step instructions. EICOGRAFT.4- Electronic Siren $4.95, Burglar Alarm $6.95, Fire Alarm $6.95, Intercom $3.95, Audio Power Amplifier $4.95, Metronome $3.95, Tremolo $8.95, Light Flasher $3.95, Electronic "Mystifier" $4.95, Photo Cell Nite Lite $4.95, Power Supply $7.95, Code Oscillator $2.50, «6 FM Wireless Mike $9.95, AM Wireless Mike $9.95, Electronic VOX $7.95, FM Radio $9.95, - AM Radio $7.95, Electronic Bongos $7.95. -
Historic Trinity MUSIC in OUR WORSHIP TODAY Lutheran Church in Honor of Our American Labor Day Holiday Weekend, Rev
Historic Trinity MUSIC IN OUR WORSHIP TODAY Lutheran Church In honor of our American Labor Day holiday weekend, Rev. D. Lee Andrzejewski, Senior Pastor organ music in today’s services is by American composers. Dr. Kieth Gerberding ~ Rev. James Gruetzner Rev. Ronald Guettler ~ Rev. Gary Headapohl Response as Dr. John L. Heins ~ Dr. John Herzog the second in Three Compositions for Organ, 1890. Chadwick Seminarian ~ Jakob Andrzejewski wasGeorge from Whitfield Lowell, Chadwick Massachusetts. (1854-1931) He studiedwrote organ in Karl Osterland, Organist Boston with Eugene Thayer and at the New England Conservatory of 13th Sunday After Pentecost September 3, 2017 Music. However, 19th century American musicians needed to study in Europe to be taken seriously. So Chadwick studied at the Leipzig Historic Trinity Lutheran Church Conservatory and privately with Joseph Rheinberger for composition and Is a traditional Cathedral Ministry in downtown Detroit organ. He returned to the New England Conservatory as a professor and Serving the metropolitan area eventually became its director. Providing an open and caring environment That encourages personal and spiritual growth Lord, Take My Hand and Lead Me So nimm denn meine Haende und fuehre mich ( family) isliving beloved in Latvia. among She Germans. was one It’s of sevena favorite sisters. confirmation Their mother hymn. died The in 1859.words Juliewere took by Julie care Hausmann of her sickly (c. father1825-1901), until he who died was in 1861.from aShe German lived with a younger sister in France from 1866 to 1877, eventually moving to St. Petersburg, Russia to join 3 other sisters working at pension house. -
February 2015 Focus
PRST STD U.S. Postage PAID February 2015 POSTAL CUSTOMER Permit No. 253 Volume 27 • Issue 2 Westland, MI www.canton-mi.org 1150 Canton Center South Canton, Michigan 48188 Canton’s Home Expo comes to the *Community Calendar and Village Theater schedule are subject to change. Check with sponsors to confirm date and information. Summit March 7 and 8 Tax Payment Reminder COMMUNITY VILLAGE THEATER Canton’s annual Home Improvement Expo Just a reminder to residents that will be held next month on Saturday, March 7 taxes are due by Tuesday, February 17. from 9 a.m. to 5 p.m. and Sunday, March 8 from The last day for 2014 taxes to be CALENDAR SCHEDULE 11 a.m. to 3 p.m. at the Summit on the Park. paid at the Canton Treasurer’s Office Highlights at this year’s Expo include: free is Friday, February 28. After that, taxes FEBRUARY FEBRUARY 1-8 parking and refreshments; live broadcasts form must be paid at the Wayne County special guest stars Murray Gula, Host of “Your Treasurer’s Office, and penalties and 2 Planning Commission Meeting. Forever After Productions interest will be applied (3% penalty 7 p.m. “Fiddler on the Roof.” Home with Murray Gula” on 1130 WDFN and Joe Gagnon “The Appliance Doctor” from 1600 applies to Winter; 6% interest applies 3 Board of Trustees--Study Session. Various times. Call 734/547-5156. to Summer plus the 3% penalty). 7 p.m. WAAM; live wood carving demonstrations; a hands-on children’s project center; and multiple Winter tax deferment for seniors 6 Butterfly Ball – Daddy/Daughter FEBRUARY 13 raffles throughout the weekend, including with household incomes of $40,000 Dance. -
Worldwide Christian Science Local Broadcast Listings
WORLDWIDE CHRISTIAN SCIENCE LOCAL BROADCAST LISTINGS ® ® Broadcasts of Christian Science Sentinel —Radio Edition, Christian Science Quarterly Weekly ® Bible Lessons, and The Herald of Christian Science can be heard and seen as listed below. LOCALITY PROGRAM | STATION DAY | TIME LOCALITY PROGRAM | STATION DAY | TIME AUSTRALIA UNITED STATES ACT Canberra S 1RPH 1125 AM WE 1:00PM AK Alaska Statewide S Telephone Line (907) 331-0238 24 HRS/DAY Kodiak S KVOK 560 AM SU 9:00AM NSW Newcastle S 2RPH 100.5 FM SU 8:00PM AL Birmingham S WAPI 1070 AM SU 8:00AM QLD Brisbane L 4RPH 1296 AM SU 1:30PM Fairhope, Mobile S WABF 1220 AM SU 9:00AM Brisbane S 4RPH 1296 AM SU 5:30PM Gold Coast S Tweed Coast Comm Radio 101.3 FM SU 7:30AM & WE 10:00PM AR Hot Springs S KVRE 92.9 FM SU 9:30AM Mitchell S Music Radio 102.1 FM SU 7:30AM & WE 10:00PM Little Rock S KMTL 760 AM SA 11:30AM Rockhampton S 4YOU 98.5 FM SU 5:30PM North Little Rock S KMTL 760 AM SA 11:30AM Roma S Music Radio 95.9 FM SU 7:30AM & WE 10:00PM Northwest Arkansas S KURM 100.3 SU 8:00AM Wynnum S BAY 100.3 FM SU 7:00-9:00AM Sherwood S KMTL 760 AM SA 11:30AM SA Adelaide S 5RPH 1197 AM TU 7:00PM AZ Four Corners S KTNN 660 AM SU 8:30PM Green Valley S KGVY 1080 AM SU 7:30AM VIC Melbourne Inner East S 3WBC 94.1 FM SU 8:00AM Phoenix Metro L Telephone Line (602) 222-6220 24 HRS/DAY Statewide S 3RPH 1179 AM, FM Regionals SU 6:00AM & 5:00PM Phoenix Metro S www.csarizona.com SU 9:00AM WA Perth S Radio Fremantle 6CCR 107.9 FM TU 1:00PM Phoenix Metro S KFNX 1100 AM SU 9:00AM Perth L Radio Fremantle 6CCR 107.9 FM -
The Idea Is to Put Together a Communications
Community Talent Survey Key Messages: • Many people in the community are facing or are in career transitions • Partner organizations want to find out what types of resources and assistance people are looking for • We need to identify the best ways to communicate with people Survey Mechanics: • County will put into Survey Monkey • Partner organizations will be asked to link to survey (hopefully by March 2) Out reach (as soon as the survey is ready) • Marti (M3) working with Elizabeth will prepare a news release, sample e-mail and specifics • Work with AA News to develop article • Use Jesse Bernstein’s connection at WAAM • Contact Michigan Radio (WUOM and WEMU) • Ask IT Zone, Chambers to send out e-mail about the survey to their lists and in their news letters. • Ask UM, EMU and WCC to send out to their lists. • Ask UAW to send to their list • Ask MichBio to send to their list • Ask to send to Pfizer internal e-mail • Ask Michigan Works to send to their list March 6, 2007 1 Many people in the Ann Arbor region are exploring their options. Closings and downsizings at Pfizer, Ford, Visteon, ACH and other companies have many Washtenaw county residents looking at their choices for the future. Some people are looking for their next job and want to stay in the area. For others, this might be the right time to start a company; and for others still it is a time to launch a career in a new field. Our region has great talent and great resources, but to make them work effectively it is essential that we find out from you: • What options are you exploring? • What types of resources are you looking for? • What resources and services are you already aware of? and • What is the best way to communicate with you? A partnership of community organizations are working together to assist community residents as they explore their options, access resources and find new careers.