Battery Technologies for Large-Scale Stationary Energy Storage
Total Page:16
File Type:pdf, Size:1020Kb
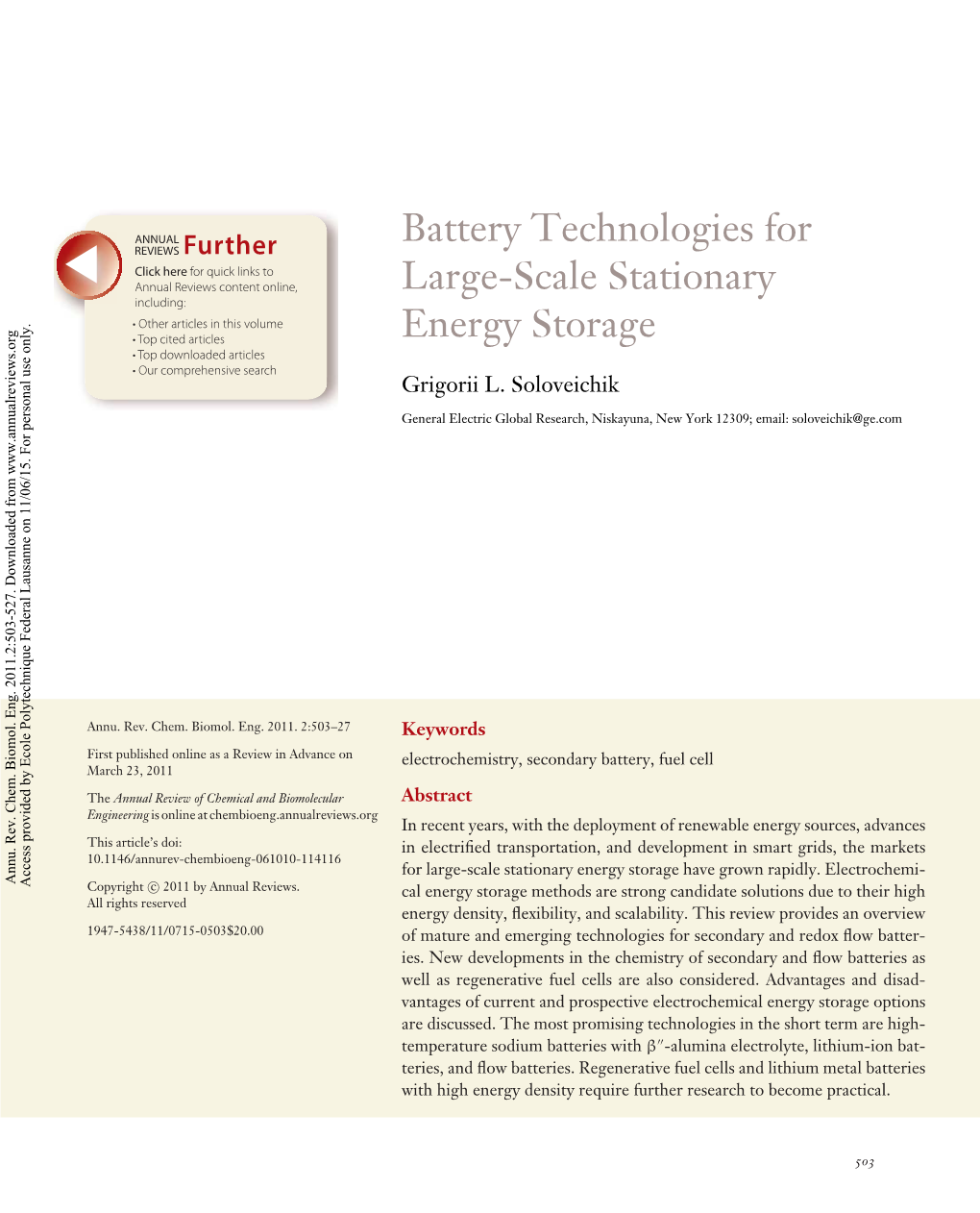
Load more
Recommended publications
-
In-Situ Tools Used in Vanadium Redox Flow Battery Research—Review
batteries Review In-Situ Tools Used in Vanadium Redox Flow Battery Research—Review Purna C. Ghimire 1,*, Arjun Bhattarai 1,*, Tuti M. Lim 2, Nyunt Wai 3 , Maria Skyllas-Kazacos 4 and Qingyu Yan 5,* 1 V-flow Tech Pte Ltd., Singapore, 1 Cleantech Loop, Singapore 637141, Singapore 2 School of Civil and Environmental Engineering, Nanyang Technological University, 50 Nanyang Avenue, Singapore 639798, Singapore; [email protected] 3 Energy Research Institute @Nanyang Technological University, 1 Cleantech Loop, Singapore 637141, Singapore; [email protected] 4 School of Chemical Engineering, The University of New South Wales, Sydney 2052, Australia; [email protected] 5 School of Material Science and Engineering, Nanyang Technological University, Singapore 637141, Singapore * Correspondence: purna.ghimire@vflowtech.com (P.C.G.); arjun.bhattarai@vflowtech.com (A.B.); [email protected] (Q.Y.); Tel.: +65-85153215 (P.C.G.) Abstract: Progress in renewable energy production has directed interest in advanced developments of energy storage systems. The all-vanadium redox flow battery (VRFB) is one of the attractive technologies for large scale energy storage due to its design versatility and scalability, longevity, good round-trip efficiencies, stable capacity and safety. Despite these advantages, the deployment of the vanadium battery has been limited due to vanadium and cell material costs, as well as supply issues. Improving stack power density can lower the cost per kW power output and therefore, intensive research and development is currently ongoing to improve cell performance by increasing electrode activity, reducing cell resistance, improving membrane selectivity and ionic conductivity, etc. In order Citation: Ghimire, P.C.; Bhattarai, A.; to evaluate the cell performance arising from this intensive R&D, numerous physical, electrochemical Lim, T.M.; Wai, N.; Skyllas-Kazacos, and chemical techniques are employed, which are mostly carried out ex situ, particularly on cell M.; Yan, Q. -
Battery Technologies for Small Scale Embeded Generation
Battery Technologies for Small Scale Embedded Generation. by Norman Jackson, South African Energy Storage Association (SAESA) Content Provider – Wikipedia et al Small Scale Embedded Generation - SSEG • SSEG is very much a local South African term for Distributed Generation under 10 Mega Watt. Internationally they refer to: Distributed generation, also distributed energy, on-site generation (OSG) or district/decentralized energy It is electrical generation and storage performed by a variety of small, grid- connected devices referred to as distributed energy resources (DER) Types of Energy storage: • Fossil fuel storage • Thermal • Electrochemical • Mechanical • Brick storage heater • Compressed air energy storage • Cryogenic energy storage (Battery Energy • Fireless locomotive • Liquid nitrogen engine Storage System, • Flywheel energy storage • Eutectic system BESS) • Gravitational potential energy • Ice storage air conditioning • Hydraulic accumulator • Molten salt storage • Flow battery • Pumped-storage • Phase-change material • Rechargeable hydroelectricity • Seasonal thermal energy battery • Electrical, electromagnetic storage • Capacitor • Solar pond • UltraBattery • Supercapacitor • Steam accumulator • Superconducting magnetic • Thermal energy energy storage (SMES, also storage (general) superconducting storage coil) • Chemical • Biological • Biofuels • Glycogen • Hydrated salts • Starch • Hydrogen storage • Hydrogen peroxide • Power to gas • Vanadium pentoxide History of the battery This was a stack of copper and zinc Italian plates, -
Advanced Battery Storage Systems Testing at ACEP
Advanced Battery Storage Systems Testing at ACEP THE PRUDENT ENERGY VRB-ESS Characterization and Assessment of the Flow Battery Concept for Energy Storage and Ancillary Services in Isolated Wind-Diesel Power Networks in Alaska March 2012 Cover photo: The power conversion system of the 5 kw, 20 kWh Vanadium Redox Flow Battery courtesy of Prudent Energy. Any comments or suggestions may be directed to the authors at the respective addresses below. Billy Muhando Asst Research Prof Alaska Center for Energy and Power (ACEP) University of Alaska Fairbanks [email protected] 1 907 474 7082 Tom Johnson Research Engineer Alaska Center for Energy and Power (ACEP) University of Alaska Fairbanks [email protected] 1 907 474 5564 Further information may be obtained by contacting: Gwen Holdmann Director Alaska Center for Energy and Power (ACEP) University of Alaska [email protected] 1 907 474 5402 www.uaf.edu/acep Disclaimer This report was prepared by the Alaska Center for Energy and Power (ACEP) as an account of work sponsored by an agency of the United States Government – the Denali Commission – and is disseminated in the interest of information exchange and general guidance only. Neither the United States Government nor any agency thereof, nor the state of Alaska, nor any of their employees, makes any warranty, express or implied, or assumes any legal liability or responsibility for the accuracy, completeness, or usefulness of any information, apparatus, product, or process disclosed, or represents that its use would not infringe privately owned rights. Reference herein to any specific commercial product, process, or service by trade name, trademark, manufacturer, or otherwise does not necessarily constitute or imply its endorsement, recommendation, or favoring by the United States Government, the state of Alaska, or any agency thereof. -
Battery Storage Technology, Systems and Cost Trends
Energy Storage Technology Advancement Partnership (ESTAP) Webinar Energy Storage 101, Part 1: Battery Storage Technology, Systems and Cost Trends March 26, 2019 Housekeeping Join audio: • Choose Mic & Speakers to use VoIP • Choose Telephone and dial using the information provided Use the orange arrow to open and close your control panel Submit questions and comments via the Questions panel This webinar is being recorded. We will email you a webinar recording within 48 hours. This webinar will be posted on CESA’s website at www.cesa.org/webinars www.cesa.org Energy Storage Technology Advancement Partnership (ESTAP) (bit.ly/ESTAP) ESTAP is supported by the U.S. Department of Energy Office of Electricity and Sandia National Laboratories, and is managed by CESA. ESTAP Key Activities: ESTAP Project Locations: New Jersey: $10 1. Disseminate information to stakeholders New York: $40 Vermont: 4 MW Oregon: 500 kW million, 4-year Massachusetts: $40 Million Million energy storage Energy Storage energy storage Resilient Power/Microgrids Microgrids microgrid & Demonstration solicitation: 13 Solicitation: 11 projects • ESTAP listserv >5,000 members Initiative Airport Microgrid Project projects $10 Million energy storage • Webinars, conferences, information demo program updates, surveys. Connecticut: $50 Million, New Mexico: 3-year Microgrids Energy Storage 2. Facilitate public/private partnerships to support joint Initiative: 11 projects Task Force federal/state energy storage demonstration project deployment Pennsylvania Alaska: Kodiak Battery 3. Support state energy storage efforts with technical, policy Island Demonstration Wind/Hydro/ Project and program assistance Battery & Cordova hydro/battery Northeastern Maryland Game Changer Awards: projects States Post-Sandy Solar/EV/Battery Critical & Resiliency Through Microgrids Infrastructure Task Force Hawaii: 6MW Resiliency Project storage on Molokai Island and HECO projects 4 Webinar Speakers Dr. -
Vanadium Redox Flow Batteries: a Review Oriented to Fluid-Dynamic Optimization
energies Review Vanadium Redox Flow Batteries: A Review Oriented to Fluid-Dynamic Optimization Iñigo Aramendia 1,* , Unai Fernandez-Gamiz 1 , Adrian Martinez-San-Vicente 1, Ekaitz Zulueta 2 and Jose Manuel Lopez-Guede 2 1 Nuclear Engineering and Fluid Mechanics Department, University of the Basque Country UPV/EHU, Nieves Cano 12, 01006 Vitoria-Gasteiz, Spain; [email protected] (U.F.-G.); [email protected] (A.M.-S.-V.) 2 Automatic Control and System Engineering Department, University of the Basque Country UPV/EHU, Nieves Cano 12, 01006 Vitoria-Gasteiz, Spain; [email protected] (E.Z.); [email protected] (J.M.L.-G.) * Correspondence: [email protected]; Tel.: +34-945-014-066 Abstract: Large-scale energy storage systems (ESS) are nowadays growing in popularity due to the increase in the energy production by renewable energy sources, which in general have a random intermittent nature. Currently, several redox flow batteries have been presented as an alternative of the classical ESS; the scalability, design flexibility and long life cycle of the vanadium redox flow battery (VRFB) have made it to stand out. In a VRFB cell, which consists of two electrodes and an ion exchange membrane, the electrolyte flows through the electrodes where the electrochemical reactions take place. Computational Fluid Dynamics (CFD) simulations are a very powerful tool to develop feasible numerical models to enhance the performance and lifetime of VRFBs. This review aims to present and discuss the numerical models developed in this field and, particularly, to analyze different types of flow fields and patterns that can be found in the literature. -
Fundamental Flow Battery Studies
FUNDAMENTAL FLOW BATTERY STUDIES: ELECTRODES AND ELECTROLYTES By MALLORY A. MILLER Submitted in partial fulfillment of the requirements for the degree of Doctor of Philosophy Dissertation Advisor: Dr. Robert F. Savinell Department of Chemical and Biomolecular Engineering CASE WESTERN RESERVE UNIVERSITY May, 2017 CASE WESTERN RESERVE UNIVERSITY DISSERTATION APPROVAL We hereby approve the thesis/dissertation of ___________________Mallory A. Miller___________________ Candidate for the Doctor of Philosophy degree* _______________Professor Robert Savinell_______________ _______________Professor Jesse Wainright_______________ ________________Professor Burcu Gurkan________________ ________________Professor Mark DeGuire________________ Date _____December 13, 2016_____ *We also certify that written approval has been obtained for any proprietary material contained therein. II Dedication To my mother for always believing in me and for her encouragement and support. III Table of Contents Acknowledgements .................................................................................................................. VIII List of Tables ............................................................................................................................... IX List of Figures ............................................................................................................................ XII Abbreviations ........................................................................................................................ XXIV Abstract -
Membranes and Electrodes for Vanadium Redox Flow Batteries
Membranes and Electrodes for Vanadium Redox Flow Batteries by Liuyue Cao M.E. in Material Science and Engineering A thesis submitted in fulfilment of the requirements for the degree of Doctor of Philosophy School of Chemical Engineering The University of New South Wales Sydney, Australia December 2018 PLEASE TYPE THE UNIVERSITY OF NEW SOUTH WALES Thesis/Dissertation Sheet Surname or Family name: Cao First name: Liuyue Other name/s: Abbreviation for degree as given in the University calendar: PhD School: School of Chemical Engineering Faculty: Engineering Title: Membrane and Electrode Materials for Vanadium Redox Flow Batteries Abstract 350 words maximum: (PLEASE TYPE) An Important Issue that has limited the more widespread deployment of the vanadium redox flowbattery (VRFB) technology to date Is the relatively high capital cost. Economic analysis reveals that a high current design with decreased stack size and low--0ost alternative membranes can dramatically reduce the cell cost. To address this, the thesis has (1) evaluated three alternative commercial ion exchange membranes by experimental measurement and mathematic simulation, (2) studied the vanadium redox reaction kinetics on various electrode surfaces to elucidate the effect of surface area and surface functional groups, and (3) developed two approaches to reduce the activation overpotential of the carbon paper electrodes in "zero-gap" cell architecture for high power densities operation. The main results Include: (1) The chemical and mechanical stability, vanadium penneation rates and cell perfonnance of Fumasep� FAP-450 (anion exchange membrane), Fumasep� F930-rfd (cation exchange membrane) and VB2 (cation exchange membrane) were evaluated in the VRFB. Simulations were conducted with experimental data to predict the capacity loss and thennal behaviour of the cells during long-tenn operation. -
Catalytic Production of Impurity-Free V3.5+ Electrolyte for Vanadium Redox flow Batteries
ARTICLE https://doi.org/10.1038/s41467-019-12363-7 OPEN Catalytic production of impurity-free V3.5+ electrolyte for vanadium redox flow batteries Jiyun Heo1, Jae-Yun Han2, Soohyun Kim1, Seongmin Yuk1, Chanyong Choi1, Riyul Kim1, Ju-Hyuk Lee1, Andy Klassen3, Shin-Kun Ryi2* & Hee-Tak Kim 1,4* The vanadium redox flow battery is considered one of the most promising candidates for use in large-scale energy storage systems. However, its commercialization has been hindered due 1234567890():,; to the high manufacturing cost of the vanadium electrolyte, which is currently prepared using a costly electrolysis method with limited productivity. In this work, we present a simpler method for chemical production of impurity-free V3.5+ electrolyte by utilizing formic acid as a reducing agent and Pt/C as a catalyst. With the catalytic reduction of V4+ electrolyte, a high quality V3.5+ electrolyte was successfully produced and excellent cell performance was achieved. Based on the result, a prototype catalytic reactor employing Pt/C-decorated carbon felt was designed, and high-speed, continuous production of V3.5+ electrolyte in this manner was demonstrated with the reactor. This invention offers a simple but practical strategy to reduce the production cost of V3.5+ electrolyte while retaining quality that is adequate for high-performance operations. 1 Department of Chemical and Biomolecular Engineering, Korea Advanced Institute of Science and Technology, 291, Daehak-ro, Yuseong-gu, Daejeon, Republic of Korea. 2 Advanced Materials and Devices Laboratory, Korea Institute of Energy Research (KIER), 152 Gajeong-ro, Yuseong-gu, Daejeon, Republic of Korea. 3 Avalon Battery, 3070 Osgood Ct Fremont, Fremont, CA 94539, USA. -
Optimal Charging of Vanadium Redox Flow Battery with Time-Varying Input Power
batteries Article Optimal Charging of Vanadium Redox Flow Battery with Time-Varying Input Power Md. Parvez Akter 1, Yifeng Li 1, Jie Bao 1,*, Maria Skyllas-Kazacos 1 and Muhammed Fazlur Rahman 2 1 School of Chemical Engineering, The University of New South Wales, Sydney, NSW 2052, Australia; [email protected] (M.P.A.); [email protected] (Y.L.); [email protected] (M.S.-K.) 2 School of Electrical Eng. and Telecom., The University of New South Wales, Sydney, NSW 2052, Australia; [email protected] * Correspondence: [email protected]; Tel.: +61-(2)-9385-6755 Received: 14 November 2018; Accepted: 31 January 2019; Published: 10 February 2019 Abstract: The battery energy storage system has become an indispensable part of the current electricity network due to the vast integration of renewable energy sources (RESs). This paper proposes an optimal charging method of a vanadium redox flow battery (VRB)-based energy storage system, which ensures the maximum harvesting of the free energy from RESs by maintaining safe operations of the battery. The VRB has a deep discharging capability, long cycle life, and high energy efficiency with no issues of cell-balancing, which make it suitable for large-scale energy storage systems. The proposed approach determines the appropriate charging current and the optimal electrolyte flow rate based on the available time-varying input power. Moreover, the charging current is bounded by the limiting current, which prevents the gassing side-reactions and protects the VRB from overcharging. The proposed optimal charging method is investigated by simulation studies using MATLAB/Simulink. -
Iron-Based Flow Batteries: Improving Lifetime and Performance
IRON-BASED FLOW BATTERIES: IMPROVING LIFETIME AND PERFORMANCE by STEVEN SELVERSTON Submitted in partial fulfillment of the requirements for the degree of Doctor of Philosophy Department of Chemical and Biomolecular Engineering CASE WESTERN RESERVE UNIVERSITY August, 2017 CASE WESTERN RESERVE UNIVERSITY SCHOOL OF GRADUATE STUDIES We hereby approve the dissertation of Steven Selverston candidate for the degree of Doctor of Philosophy*. Committee Chair Dr. Robert Savinell Committee Member Dr. Jesse Wainright Committee Member Dr. Rohan Akolkar Committee Member Dr. Gary Wnek Date of Defense May 18, 2017 *We also certify that written approval has been obtained for any proprietary material contained therein. Contents List of Tables iii List of Figures v Acknowledgments ix Abstract x 1 Introduction 1 2 Literature Review 5 2.1 Flow Batteries ............................... 6 2.2 All-Iron Hybrid Flow Batteries ..................... 8 2.3 Electrolytes ................................ 10 2.4 Iron Plating Electrodes .......................... 17 2.5 Rebalancing ................................ 20 2.6 System Modeling ............................. 21 2.7 Zinc-Iron Electroplating ......................... 24 2.8 Accelerated Lifetime Testing ....................... 28 3 Dissertation Research 30 3.1 Electrolyte Rebalancing ......................... 31 3.2 System Modeling ............................. 32 i CONTENTS 3.3 Zinc-Iron Chloride Flow Batteries .................... 32 4 Model for Sealed Flow Batteries 34 4.1 Introduction ............................... -
Handbook on Battery Energy Storage System
HANDBOOK ON BATTERY ENERGY STORAGE SYSTEM DECEMBER 2018 ASIAN DEVELOPMENT BANK HANDBOOK ON BATTERY ENERGY STORAGE SYSTEM DECEMBER 2018 ASIANASIAN DEVELOPMENT DEVELOPMENT BANKBANK Creative Commons Attribution 3.0 IGO license (CC BY 3.0 IGO) © 2018 Asian Development Bank 6 ADB Avenue, Mandaluyong City, 1550 Metro Manila, Philippines Tel +63 2 632 4444; Fax +63 2 636 2444 www.adb.org Some rights reserved. Published in 2018. ISBN 978-92-9261-470-6 (print), 978-92-9261-471-3 (electronic) Publication Stock No. TCS189791-2 DOI: http://dx.doi.org/10.22617/TCS189791-2 The views expressed in this publication are those of the authors and do not necessarily reflect the views and policies of the Asian Development Bank (ADB) or its Board of Governors or the governments they represent. ADB does not guarantee the accuracy of the data included in this publication and accepts no responsibility for any consequence of their use. The mention of specific companies or products of manufacturers does not imply that they are endorsed or recommended by ADB in preference to others of a similar nature that are not mentioned. By making any designation of or reference to a particular territory or geographic area, or by using the term “country” in this document, ADB does not intend to make any judgments as to the legal or other status of any territory or area. This work is available under the Creative Commons Attribution 3.0 IGO license (CC BY 3.0 IGO) https://creativecommons.org/licenses/by/3.0/igo/. By using the content of this publication, you agree to be bound by the terms of this license. -
Vanadium Redox Flow Battery
VANADIUM REDOX FLOW BATTERY Sizing of VRB in electrified heavy construction equipment NATHAN ZIMMERMAN School of Business, Society and Engineering Supervisor: Javier Campillo, Bobbie Frank Course: Degree Project Date: 2014-07-13 Course code: ERA401 Email: [email protected] Subject: Energy Engineering HE credits: 30 Program: Master of Science Program in Sustainable Energy Systems ABSTRACT In an effort to reduce global emissions by electrifying vehicles and machines with internal combustion engines has led to the development of batteries that are more powerful and efficient than the common lead acid battery. One of the most popular batteries being used for such an installation is lithium ion, but due to its short effective usable lifetime, charging time, and costs has driven researcher to other technologies to replace it. Vanadium redox flow batteries have come into the spotlight recently as a means of replacing rechargeable batteries in electric vehicles and has previously be used mainly to store energy for load leveling. It possesses many qualities that would be beneficial to electrify vehicles. The battery has the ability for power and energy to be sized independently which is not dissimilar to internal combustion vehicles. It also has the potential for a tolerance to low discharges, fast response time, and can quickly be refueled by replacing the electrolyte; just like is done when a car refuels at the gas station. The purpose of the study is to determine the possibility of using vanadium redox flow batteries to power heavy construction equipment, a wheel loader, with a finite amount of space available for implementation. A model has been designed in MATLAB to determine how long the battery could last under typically applications for the wheel loader which needs a peak power of 200 kW.