OPERATION MANUAL 75' Aerialscope MM Platform
Total Page:16
File Type:pdf, Size:1020Kb
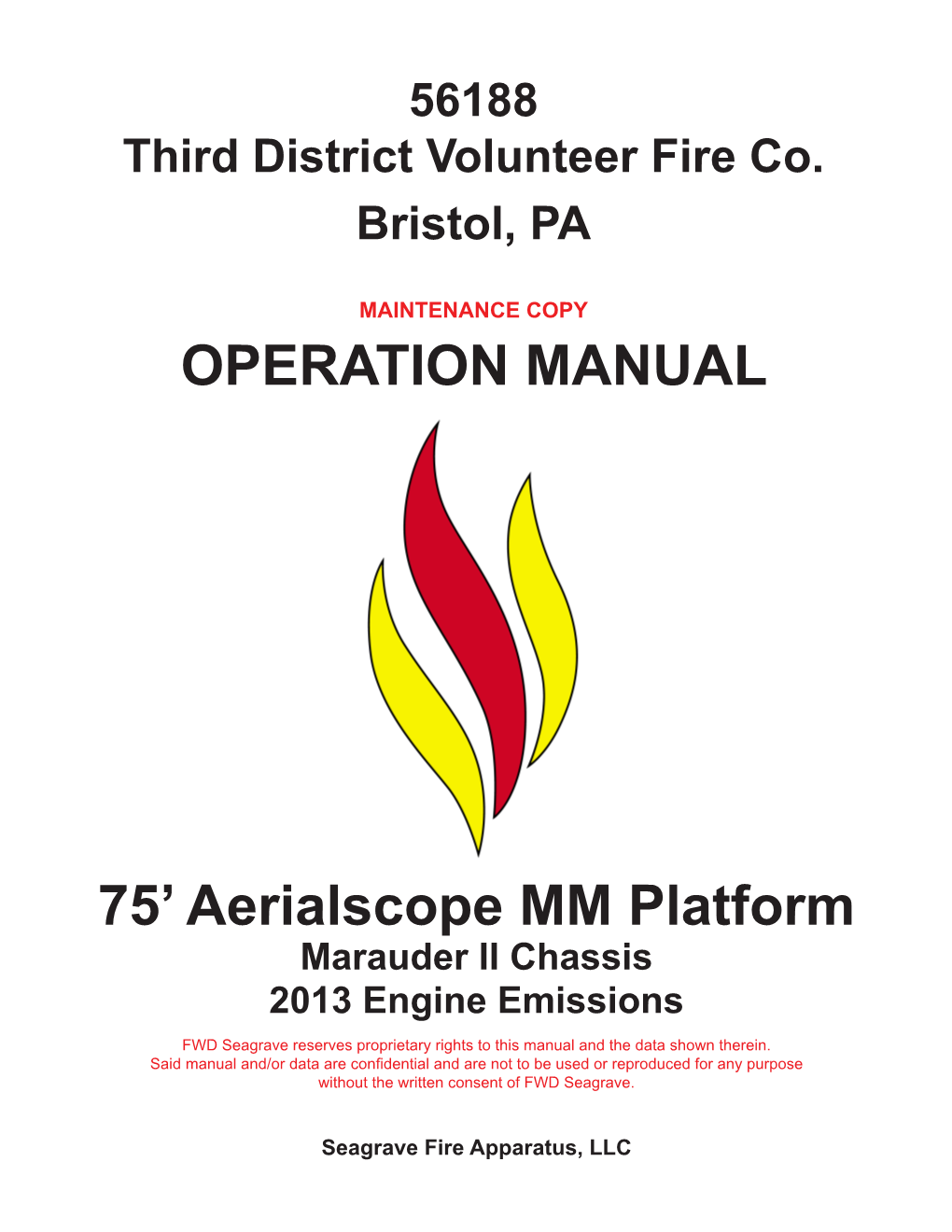
Load more
Recommended publications
-
EP / BP Compact Product Family
EP / BP Compact Product Family Foto Siemens AG“ APPLICATIONS High-Speed Trains | Locomotives | Metros | Regional and Commuter Trains 2 EP / BP COMPACT PRODUCT FAMILY IS A FLEXIBLE AND POWERFUL BRAKE CONTROL SYSTEM providing not only brake cylinder pressure control for central and decentralized systems but also for brake pipe pressure control. Its modular design of electronic and pneumatic modules makes it configurable for all types of high-speed trains, multiple units and metros. With its variety of modules, EP / BP CUSTOMER BENEFITS DIVERSIFICATION Compact can be used for a wide n Lightweight and compact EP Compact offers control of various range of different applications of all n Flexible system layout functions of the braking systems: car builders across different markets. n Maximum economy thanks to n Service brake (direct and indirect) Every electropneumatic module standardized modules n Emergency brake (direct and controls either brake pipe n Discrete, highly integrable indirect) applications, single bogies components n Magnetic track brake separately or several bogies with n Straightforward service and n Parking brake identical braking requirements. maintenance concept n Wheel slide control Different electronic modules allow n For central or decentralized control n Continuous load correction and the use of different communication n Multifunctional for numerous load limitation interfaces: wheel slide protection, system configurations pressure regulation and diagnosis n Innovative use of proven Electronic control functions: functions. Anti-skid valves as well as technology n Blending / brake management different auxiliary control functions n Integrated electronics for n Diagnostics and monitoring can be integrated into the module underfloor or separate electronics n Sanding and other auxiliary systems as an option. -
Real-World Exhaust Emissions of Diesel Locomotives and Motorized Railcars During Scheduled Passenger Train Runs on Czech Railroads
atmosphere Article Real-World Exhaust Emissions of Diesel Locomotives and Motorized Railcars during Scheduled Passenger Train Runs on Czech Railroads Michal Vojtisek-Lom 1,2,* , Jonáš Jirk ˚u 3 and Martin Pechout 4 1 Department of Automobile, Combustion Engine and Railway Engineering, Faculty of Mechanical Engineering, Czech Technical University of Prague, 160 00 Prague, Czech Republic 2 Department of Vehicles and Engines, Technical University of Liberec, 46117 Liberec, Czech Republic 3 Department of Vehicle Technology, Faculty of Transportation Sciences, Czech Technical University in Prague, 110 00 Prague, Czech Republic; [email protected] 4 Department of Vehicles and Ground Transport, Faculty of Engineering, Czech University of Life Sciences, 165 21 Prague, Czech Republic; [email protected] * Correspondence: [email protected] or [email protected]; Tel.: +420-774-262-854 Received: 17 April 2020; Accepted: 28 May 2020; Published: 2 June 2020 Abstract: The paper summarizes exhaust emissions measurements on two diesel-electric locomotives and one diesel-hydraulic railcar, each tested for several days during scheduled passenger service. While real driving emissions of buses decrease with fleet turnaround and have been assessed by many studies, there are virtually no realistic emissions data on diesel rail vehicles, many of which are decades old. The engines were fitted with low-power portable online monitoring instruments, including a portable Fourier Transform Infra Red (FTIR) spectrometer, online particle measurement, and in two cases with proportional particle sampling systems, all installed in engine compartments. Due to space constraints and overhead electric traction lines, exhaust flow was computed from engine operating data. Real-world operation was characterized by relatively fast power level transitions during accelerations and interleaved periods of high load and idle, and varied considerably among service type and routes. -
TRANSPORTATION NOTICE #2018-045 Effective 0001, Friday, December 14, 2018
THE BELT RAILWAY COMPANY OF CHICAGO TRANSPORTATION NOTICE #2018-045 Effective 0001, Friday, December 14, 2018 To: ALL CONCERNED Subject: Clearing Yard Transportation Work Instructions (Hump Notice) Transportation Notice 2018-034, effective August 21, 2018 is cancelled. The following changes are made to Clearing Yard Transportation Work Instructions (Hump) Addition: • CY 5.20 – Cars on Hump Needing Repairs (NEW) • CY 8.2.1 - Braking During Shove Over Movements (NEW) Transportation Notice 2018-045 Page 1 Clearing Yard Transportation Work Instructions (Hump) The instructions contained within this document are specifically intended for any Transportation Department employees working in Clearing Yard. These instructions provide specific instructions on the operation of the Clearing Yard. Where these instructions may differ from published rules, these instructions will govern operations as they relate to the operation of the Clearing Yard. Transportation Department Employees working in Train, Yard, and Engine Service; including Yardmasters (Humpmasters), Hump Conductors, and all crew members on BRC yard assignments, must have these instructions in their possession while on duty for reference while working in Clearing Yard. These instructions will be published quarterly, with additions made as needed using Transportation Notices, under the direction of the Superintendent-Transportation. CY 1 - Hump Operations: Hump Operations are under the direct control of the Trainmaster-Operations. Reporting to the Trainmaster- Operations are Yardmasters, Hump Conductors, Train Crews, and Transportation-Clerks. CY 2 - Hump Speeds: The Hump Conductor is responsible for regulating hump speeds and communicating this information to Hump Crews. Speed Settings: SPEED SETTING SPEED (MPH) HUMP SLOW 1.4 MPH HUMP 1.7 MPH HUMP FAST 2.2 MPH The default speed for hump operations is Hump. -
ABS 6 Standard Anti-Lock Braking System
Systems for Commercial Vehicles Product Manual ABS 6 Standard Anti-lock Braking System • Basic Principles of Operation of the System • Component Descriptions • Troubleshooting and Fault-Finding • Service Guidance to ensure Safe and Efficient Operation Training Nutzfahrzeug Bremssysteme Contents Contents 3 Disclaimer 4 Safety Checks 5 1. General Information 6 1.1 Service Intervals 6 1.2 Principles of Anti-lock Braking System (ABS) Operation 7 1.2.1 Introduction 7 1.2.2 Operation 9 1.3 General Advice when working with ABS 14 1.3.1 Dos and Don’ts for Drivers / Operators 14 1.3.2 Dos and Don’ts for ABS electrical components and cabling 15 1.3.3 Dos and Don’ts for ABS pneumatic components and pipework 17 1.4 Troubleshooting and Fault-finding 18 1.4.1 Normal Operation 18 1.4.2 Start-up Check 18 1.4.3 Fault Detection 18 1.4.4 Using Blink Codes 18 1.4.5 Configuration Blink Codes 19 1.4.6 Fault Blink Codes 21 1.4.7 Erasing Fault Codes from the ECU memory 26 1.4.8 PC Diagnostics 27 2. System Components 28 2.1 Electronic Control Unit (ECU) 28 2.2 ABS Warning Lamp 29 2.3 Sensing Ring 30 2.4 Wheel Speed Sensor 31 2.5 Sensor Extension Cable 34 2.6 Pressure Modulator Valves 35 2.7 VOSS plug connection system 230 (assembly instructions) 41 3. Wiring Diagrams 43 3 3 Disclaimer The information contained in this document is intended for the exclusive use of trained persons within the commercial vehicle industry, and must not be passed on to any third party. -
Environmental Product Portfolio 2 KNORR-BREMSE ENVIRONMENTAL PRODUCT PORTFOLIO
1 Environmental product portfolio 2 KNORR-BREMSE ENVIRONMENTAL PRODUCT PORTFOLIO Our contribution towards making mobility more environmentally friendly and energy-efficient In recent years, climate change and environmental Our product portfolio offers solutions that protection have taken on greater relevance for >> minimize energy consumption and enhance the commercial vehicle and rail vehicle sectors. In fuel efficiency, response, Knorr-Bremse has for many years been >> reduce atmospheric emissions, giving top priority to developing fuel-saving, >> minimize noise emissions, emission-reducing technologies with solutions >> protect the environment by using eco-friendly tailored to market needs. materials and manufacturing processes. ENERGY EFFICIENCY PROTECTING RESOURCES AND REDUCING EMISSIONS • CFCB bogie-mounted block brakes • Oil-free compressor with sound insulation • Compact brake calipers • Flexpad Silent brake pad • Lightweight HVAC units, doors, brake discs • LL composite brake block • iCOM Assist (LEADER) driver assistance system • Sanding systems with reduced sand use DIVISION • Driving and training simulators • iCOM Energy Metering • HVAC systems • IFE Generation 4 entrance system RAIL VEHICLE RAIL • Isobar brake pads • Aluminum brake discs • Pneumatic disc brakes • Electronic braking system (EBS) • Electronic air treatment • Engine retarder DIVISION • Aluminum compressor casing • Genuine remanufactured products • Compressor with clutch • Electric screw compressor • Compressor with energy-saving system • Mechatronic transmission -
Chapter 2. General Principle of Electromagnetic Brakes
Chapter 2. General Principle of Electromagnetic Brakes 2.1. Introduction Electromagnetic brakes have been used as supplementary retardation equipment in addition to the regular friction brakes on heavy vehicles. We outline the general principles of regular brakes and several alternative retardation techniques in this section. The working principle and characteristics of electromagnetic brakes are then highlighted. 2.2. General Principle of Brake System The principle of braking in road vehicles involves the conversion of kinetic energy into thermal energy (heat). When stepping on the brakes, the driver commands a stopping force several times as powerful as the force that puts the car in motion and dissipates the associated kinetic energy as heat. Brakes must be able to arrest the speed of a vehicle in a short periods of time regardless how fast the speed is. As a result, the brakes are required to have the ability to generating high torque and absorbing energy at extremely high rates for short periods of time. Brakes may be applied for a prolonged periods of time in some applications such as a heavy vehicle descending a long gradient at high speed. Brakes have to have the mechanism to keep the heat absorption capability for prolonged periods of time. 2.3. Conventional Friction Brake 4 The conventional friction brake system is composed of the following basic components: the “master cylinder” which is located under the hood is directly connected to the brake pedal, and converts the drivers’ foot pressure into hydraulic pressure. Steel “brake hoses” connect the master cylinder to the “slave cylinders” located at each wheel. -
“Road Vehicles — Endurance Braking Systems of Motor Vehicles and Towed Vehicles — Test Procedures”
Presentation to GRRF, 55th Session, Geneva Febr. 3rd, 2004 ISO CD 12161 Doc TC22/SC2 N 597 “Road vehicles — Endurance braking systems of motor vehicles and towed vehicles — Test procedures” by ISO TC22/SC2/WG6 SWG 6 „Endurance braking systems“ Dr. Reinhold Pittius (VOITH TURBO) Pittius 2004-02-03 page 1 ISO 22/2/6/SWG 6 / Retarders / Test procedures for type approval / WD 12161 1. Structure of ISO Working Group Subworking group SWG 6 „Endurance braking systems“ Chairman Dr. Reinhold Pittius • reporting to ISO 22/2/WG6 „Braking Systems“ Chairman Prof. v. Glasner • Active members of SWG 6: DaimlerChrysler TELMA IVECO VOITH TURBO MAN ZF • Status - Working Draft agreed by TC22 Æ Committee Draft (CD) - Distribution as ISO DIS in Dec. 2003 - Balloting until May 2004 Pittius 2004-02-03 page 2 ISO 22/2/6/SWG 6 / Retarders / Test procedures for type approval / WD 12161 Contents 1. Structure of ISO Working Group 2. The Target 3. Basic legal requirements 4. Basic understanding of equivalent energy 5. Specific properties of different types of retarders 6. Test methods 7. Conclusion Pittius 2004-02-03 page 3 ISO 22/2/6/SWG 6 / Retarders / Test procedures for type approval / WD 12161 2. The Target Standardization • of testing procedures • of vehicles - equipped with endurance braking systems - to be type approved • according to existing legal requirements ¾ Detailed description of ¾ different test methods such that ¾ results are • objectiv, • realistic and • compatible Pittius 2004-02-03 page 4 ISO 22/2/6/SWG 6 / Retarders / Test procedures for type approval / WD 12161 3. Basic legal requirements (1) ECE-R 13, Annexe 4 para. -
Engineering Greatsolutions
Engineering GREAT Solutions Mobile Pneumatics Mobile Pneumatics Solutions for trailers, body builders, buses and specialist vehicles 02 Mobile Pneumatics Contents 03 Experience and Expertise in 16 – Buses & Coaches 26 Our market leading product brands Commercial Vehicles 20 – Specialist Vehicles - Agriculture 06 Solutions for Mobile Pneumatics 22 – Specialist Vehicles - 08 – Trailers Mining & Construction 12 – Body Builders 24 – Specialist Vehicles - Marine Engineering GREAT solutions through people, products, innovation and service IMI Precision Engineering is a world-leader in fluid and motion control. Building close, collaborative relationships with our customers, we gain a deep understanding of their engineering needs and then mobilise our resources and expertise to deliver distinctive products and solutions. Wherever precision, speed and engineering reliability are essential, our global footprint, problem-solving capability and portfolio of high performance products enables us to deliver GREAT solutions which help customers tackle the world’s most demanding engineering challenges. > Reliability We deliver and support our high quality products through our global service network. > High performance products Calling on a world-class portfolio of fluid and motion control products including IMI Norgren, IMI Buschjost, IMI FAS, IMI Herion and IMI Maxseal. We can supply these singlely, or combined in powerful customised solutions to improve performance and productivity. > Partnership & Problem Solving We get closer to our customers to understand their exact challenges. Mobile Pneumatics 03 Experience and Expertise in Commercial Vehicles With over 40 years experience working directly with global commercial vehicle manufacturers, IMI Precision Engineering offer a comprehensive range of pneumatic, hydraulic, electronic and vacuum solutions covering every major vehicle system, from the front bumper to the rear. -
Model 320 Operator's Manual
MODEL 320 OPERATOR’S MANUAL Quick Table of Contents •Introduction ............................................ 1 •Cab, Frame Access, & Cab Ladder........... 5 •Getting To Your Engine................................. 8 •Controls And Displays ................................... 12 •Seat And Restraint Systems............................. 49 •Driver’s Checklists................................................ 58 •Starting And Operating The Vehicle........................ 62 •Maintenance and Service........................................... 96 •Vehicle Identification .................................................... 166 •Consumer Information .................................................... 167 •Subject Index ............................................................ 169 California Proposition 65 Warning • Diesel engine exhaust and some of its constituents are known to the State of California to cause cancer, birth defects, and other reproductive harm. • Other chemicals in this vehicle are also known to the State of California to cause cancer, birth defects or other reproductive harm. • Battery posts, terminals, and related accessories con- tain lead and lead compounds, chemicals known to the State of California to cause cancer and reproductive harm. Wash hands after handling. PART 1: INTRODUCTION This manual contains useful information for the safe and efficient operation of your Model 320. It also provides information on main- taining your vehicle in the best condition, with an outline for perform- ing safety checks and basic preventive maintenance inspections. We have tried to present the information you’ll need to learn about your vehicle’s functions, controls, and operation - and to present it as clearly as possible. We hope you’ll find this manual easy to use. There will be times when you need to take this manual out of your Peterbilt. When you do, please be sure to return it to the cab when you are finished using it. That way it will be there when you need it the next time or when you pass the vehicle on to the next user. -
Retarders for Heavy Vehicles: Evaluation of Performance Characteristics and In-Service Costs
RETARDERS FOR HEAVY VEHICLES: EVALUATION OF PERFORMANCE CHARACTERISTICS AND IN-SERVICE COSTS Phase I - Technical Report Paul S. Fancher James 0' Day Howard Bunch Michael Sayers Christopher B. Winkler Contract No. DOT-HS-9-02239 Contract Amount: $201,594 Highway Safety Research Institute The University of Michigan Ann Arbor, Michigan 48109 February 1981 Prepared for the Department of Transportation, National Highway Traffic Safety Administration, under Contract No. : DOT-HS-9-02239. This document is disseminated under the sponsorship of the Department of Transportation in the interest of information exchange. The United States Government assumes no 1 iabil i ty for the contents or use thereof. Tnhrical Report Docummtation Page 1. Roport No. 2. Gowe-t Accession No. 3. Recipimt'r Catslo9 No. 1 4. Title d Subtitle 5. Rmport Date RETARDERS FOR HEAVY VEHICLES: EVALUATION OF PERFORMANCE CHAFACTERISTICS Aiin IN-SERVICE 6. Pwforring Orponization COA COSTS - Vol. I: Technical Report 01 7691 8. Pukrring Or9mixation Ropart No. h*drLP. Fancher, J. O'Day, H. Bunch, M. Sayers, UM-HSRI-81-8-1 C.- Winkler. - . I 9. Puforning Orgmirstion Wane md Address 1 10. Wo& Unit No. Highway Safety Research Institute The University of Michi an 11. Controcc or Gront No. Huron Parkway. & . Baxter W oad , DOT-HS-9-02239 13. TYPO O! Roport and Period Covered Ann Arbor, Mich~qan48109 I 12. $onsorino A~~~~ NH MI( Address Final (Phase I) National Highway Traffic Safety Administration I 9/79-9/80 ' I U. S. ~epartment-of ~ransportatjon 14. Sponsoring Agency Code Washington, D.C. 20590 IS. Supplmnntar Mows I*. Abstract The potential benefits to be derived from retarder use in heavy truck applications are evaluated in terms of (1) productivity gains due to de- creased trip time, (2) cost savings due to decreased brake wear and main- tenance, and (3) safety enhancement due to reduced probability of a runaway accident. -
Trail Sign: Potomac Yards Rail Hump
Certain rail classification yards depended on a simple landform called the "hump." Technological Advances In the late 1950s, the hump yards were once again updated when Potomac Yard had two humps: one for northbound trains and one for southbound trains. the VELAC system was installed at the southbound hump. VELAC, an Potomac Yard incorporated numerous technological advances automated classification yard system, replaced remote switches with Trains first entered a receiving yard where locomotives were detached from trains and cars over the years to improve efficiency. Classifying cars evolved from electronic switches controlled from a four-story concrete tower. Touted as weresentto aclassificationyardoverthehump: a hill built between the two yards.After being primarily manual labor to utilizing automated and digital systems. an "electronic brain," VELAC made car classification even more efficient pushed to the top ofthe hump by a yard locomotive, cars were uncoupled in specific groups and required fewer employees. Computers, installed at the Yard in the 1960s and 1970s, replaced and allowed to roll down one of several different tracks to become part of a new train. This mechanical relay systems with state-of-the-art digital systems. group of tracks formed the classification yard. This system used gravity-and a good deal of pre-planning by track managers-to make classifying ( or sorting) rail cars much easier. The first hump yards at Potomac '\.'¥~~~~;;__;_;_::.:_::.._ Southbound Receiving Yard Yard were operated manually I by car-cutters who uncoupled the cars when they reached the top of the hump. Switch tenders lined the switches and brakemen rode the cars down the hill and slowed their descent using hand operated brakes. -
(For Insertion in Lieu of the Paragraph
Memorandum U.S. Department of Transportation Federal Railroad Administration Date: MAR 2 4 2010 Reply to Attn of: 1\'IP&E 10-01 SUbject: Technical Bulletin MP&E 10-01, Enforcement Guidance Regarding Securement of Equipment with Title 49 Code of Federal Regulations Section 232.1 03(n) From: Edward vV. Pritchard, Director, Office of Safety Assurance and Compliance To: All Regional Administrators and Deputy Regional Administrators, Motive Power and Equipment (MP&E) and Operating Practices (OP) Specialists, Chief Inspectors, Railroad Safety Oversight Managers, State Program Managers, and all Federal and State MP&E and or Inspectors The purpose ofthis technical bulletin (TB) is to provide inspectors with guidance in the application ofTitle 49 Code of Federal Regulations (CFR) Section 232.103(n), Securement ofunattended equipment. A recent Railroad Safety Board mling reiterates that the application of no hand brakes on unattended equipment will not meet the securement requirements of49 CFR 232.103. However, the Federal Railroad Administration (FRA) recognizes that it is necessary to have unsecure equipment at times in the switching oftrains within classification yards. Therefore, this TB provides guidance in railroad usage ofalternate forms of securement including where they may be appropriate and what constitutes effective use of alternate forms of securement. It also provides guidance in the application of securement on repair tracks. Title 49 CFR 232.103(n) addresses the securement of unattended equipment by means of applying hand brakes, venting the brake pipe to zero and leaving the angle cock open on one end of a cut of cars, and requiring the railroad to develop and implement procedures to verify that the equipment is secure.