Committee of Underground Exploitation of the Mineral Deposits
Total Page:16
File Type:pdf, Size:1020Kb
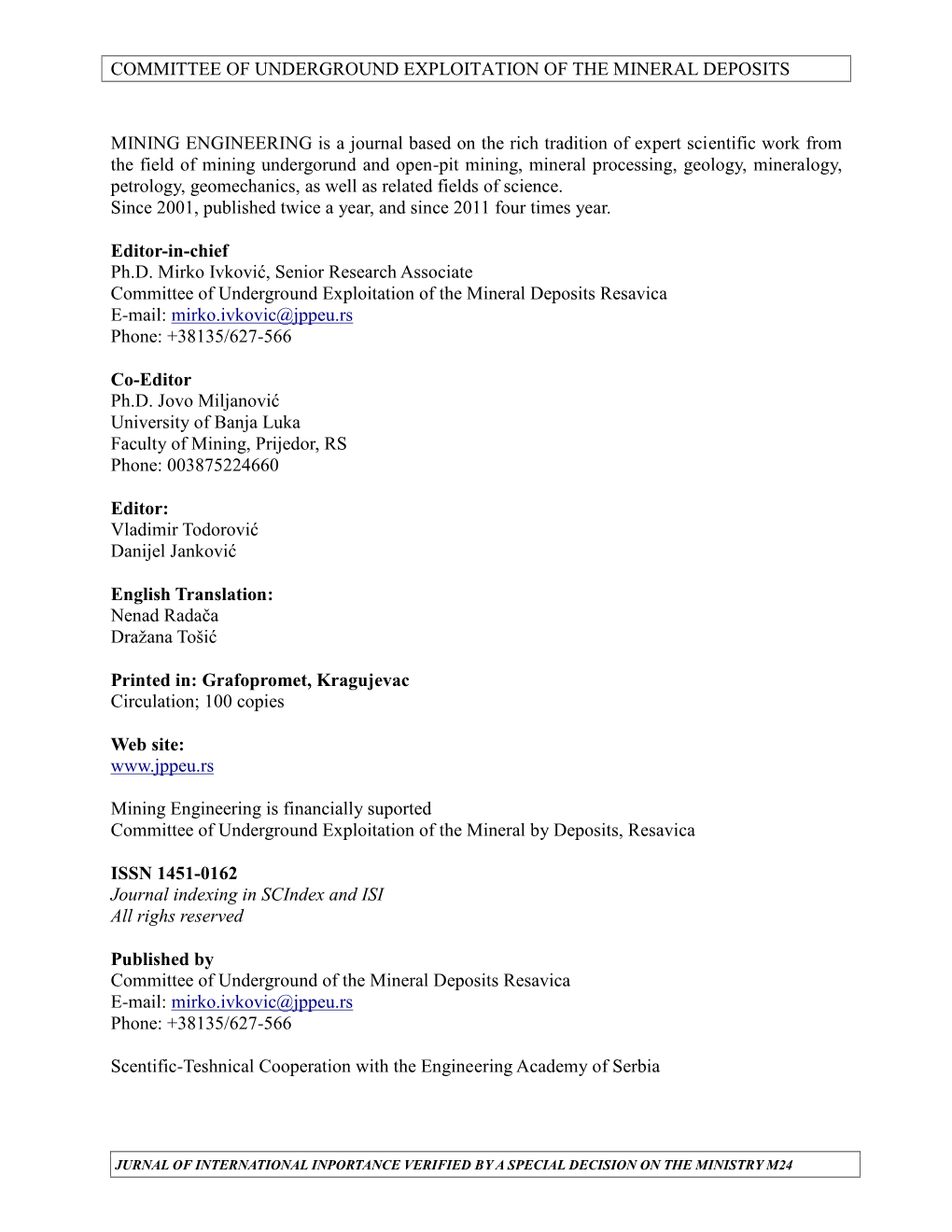
Load more
Recommended publications
-
World Bank Document
Public Disclosure Authorized PUBLIC ENTERPRISE ELEKTROPRIVREDA SRBIJE BEOGRAD CONSOLIDATED FINANCIAL STATEMENTS FOR THE YEAR ENDED 31 DECEMBER 2017 AND INDEPENDENT AUDITOR'S REPORT Public Disclosure Authorized Public Disclosure Authorized Public Disclosure Authorized CONTENTS Auditor’s report Consolidated Balance sheet Consolidated Income statement Consolidated Statement of other comprehensive income Consolidated Cash flow statement Consolidated Statement of changes in equity Notes to the financial statements Independent auditor’s report To the Management of Javno preduzeće Elektroprivreda Srbije, Beograd Report on the Consolidated Financial Statements We have audited the accompanying consolidated financial statements of Javno preduzeće Elektroprivreda Srbije, Beograd (the „Company“) and its subsidiaries (the „Group”), which comprise the consolidated balance sheet as of 31 December 2017 and the consolidated income statement, consolidated statement of other comprehensive income, consolidated statement of changes equity and consolidated cash flow statement for the year then ended and notes, comprising a summary of significant accounting policies and other explanatory information. Management’s responsibility for the consolidated financial statements Management is responsible for the preparation and fair presentation of these consolidated financial statements in accordance with the requirements of the Law on Accounting and accounting regulation effective in the Republic of Serbia, and for such internal control as management determines is necessary to enable the preparation of consolidated financial statements that are free from material misstatement, whether due to fraud or error. Auditor’s responsibility Our responsibility is to express an opinion on these consolidated financial statements based on our audit. We conducted our audit in accordance with the Law on Auditing and auditing regulations effective in the Republic of Serbia. -
Prostorni Plan Srbije
U V O D Prostorni plan Republike Srbije kao strateški razvojni oblastima/sektorima; (ii) planski iskazi o buducem razvoju dokument za period do 2010. godine utvrduje: (projekcije, prognoze, planske strategije, planske koncepcije ?? dugorocne osnove organizacije, korišcenja i uredenja itd.); i prostora Republike Srbije; (iii) skup mera o implementaciji. ?? pravce urbanizacije i osnovne kriterijume uredenja U Prostornom planu postignut je stepen sinteze naselja; planskih rešenja moguc u datim okolnostima. Bice neophodno ?? planska nacela i kriterijume korišcenja prirodnih resursa i da se dugorocne koncepcije Plana razrade za srednjerocni zaštite životne sredine; period i usaglase instrumenti primene Prostornog plana sa politikama i merama koje ce biti korišcene u drugim ?? uslove za zaštitu i korišcenje podrucja od posebnog oblastima razvoja. Problem uskladivanja raznih interesa (cesto znacaja; i oprecnih i konfliktnih) u korišcenju prostora, u institucijama ?? koridore osnovnih infrastrukturnih sistema. politickog sistema, zahtevace potpuniju strucnu i naucnu Prostornim planom se prvenstveno usmerava i podršku, kako informaticku i istraživacku, tako i kontroliše organizacija i uredenje prostora Republike ali su u institucionalno-organizacionu i programsku. U tom smislu, njemu sadržane i propozicije iz drugih oblasti razvoja prioritetno ce se pristupiti izradi i donošenju posebnog (ekonomskog, socijalnog i dr.). Utoliko je Plan do odredenog Programa za ostvarivanje Prostornog plana Republike Srbije. stepena integrativan. Razlog je u neodvojivosti -
Korice Zbornik.Cdr
ORGANIZATORI Savez inženjera rudarstva i geologije Srbije, Jugoslovenski komitet za površinsku eksploataciju Ring Deutscher Bergingenieure, Germany Elektroprivreda Srbije VI MEĐUNARODNA KONFERENCIJA PD RB Kolubara PD TE-KO Kostolac U ORGANIZACIJI UČESTVUJU Ministarstvoprirodnih resursa , rudarstva i UGALJ 2013 prostornog planiranja Republike Srbije Ministarstvo energetike, razvoja i životne sredine Republike Srbije Zlatibor, Hotel Palisad,25 - . oktobar 201 3 . Proceedings Zbornik radova , , Book of Proceedings , , 2013 ORGANIZERS th Society of Mining and Geology Engineers of Serbia 2013 6 INTERNATIONAL CONFERENCE Jugoslav Opencast Mining Committee Ring Deutscher Bergingenieure, Germany Electric Power Industry of Serbija EA MB Kolubara EA TPP and OCM Kostolac COAL 2013 UGALJ 2013 COAL COAL 2013 SUPPORTED BY Ministry of Natural Resources, Mining and Spatial Planning of Republic of Serbia Zlatibor, Hotel Palisad,23 -5 October 201 Ministry of Energy, Development and Environmental Protection of Republic of Serbia VI MEĐUNARODNA KONFERENCIJA UGALJ 2013 Zlatibor, 2-5. oktobar 2013. 6th INTERNATIONAL CONFERENCE COAL 2013 Zlatibor, 2-5 October 2013 ZBORNIK RADOVA PROCEEDINGS VI MEĐUNARODNA KONFERENCIJA UGALJ 2013 ZBORNIK RADOVA 6th INTERNATIONAL CONFERENCE COAL 2013 PROCEEDINGS Izdavač Jugoslovenski komitet za površinsku eksploataciju Urednik Prof. Dr Vladimir Pavlović Tehnička priprema Marijana Maksimović, master inž. Grafičko rešenje korica Saša Stepanović, dipl. inž. Tiraž 150 primeraka Štampa Colorgrafx, Beograd © Sva prava zadržava izdavač ISBN: ISBN 978-86-83497-20-1 VI MEĐUNARODNA KONFERENCIJA UGALJ 2013 6th INTERNATIONAL CONFERENCE COAL 2013 ORGANIZATORI Savez inženjera rudarstva i geologije Srbije, Jugoslovenski komitet za površinsku eksploataciju Ring Deutscher Bergingenieure, Germany Elektroprivreda Srbije PD Rudarski basen Kolubara PD Termoelektrane i kopovi Kostolac U ORGANIZACIJI UČESTVUJU Ministarstvo prirodnih resursa, rudarstva i prostornog planiranja Ministarstvo energetike, razvoja i zaštite životne sredine MEĐUNARODNI NAUČNI ODBOR Prof. -
Mining & Tunnelling Cables
Mining & Tunnelling Cables Linking the Future As the worldwide leader in the cable industry, distribute and install cables and systems for the Prysmian Group believes in the effective, transmission and distribution of power at low, efficient and sustainable supply of energy and medium, high and extra-high voltage. information as a primary driver in the development of communities. In telecoms, the Group is a leading manufacturer of all types of copper and fibre cables, systems With this in mind, we provide major global and accessories - covering voice, video and data organisations in many industries with best-in- transmission. class cable solutions, based on state-of-the-art technology. Through two renowned commercial Drawing on over 130 years’ experience and brands - Prysmian and Draka - based in almost continuously investing in R&D, we apply 100 countries, we’re constantly close to our excellence, understanding and integrity to customers, enabling them to further develop the everything we do, meeting and exceeding the world’s energy and telecoms infrastructures, and precise needs of our customers across all achieve sustainable, profitable growth. continents, at the same time shaping the In our energy business, we design, produce, evolution of our industry. What links global expertise to the wheels of industry? High-performing cable solutions to keep the wheels of industry turning. On every continent, in applications that range and service platforms, built on easy contact, from air and rail transport infrastructure to heavy customised solutions and effective supply chains, duty industries such as mining, tunnel drilling and meeting their specialised requirements, to help defence, Prysmian’s specialist cable solutions sit them drive the wheels of industry and achieve at the heart of significant international projects; sustainable growth and profitability. -
Management of the Environmental Protection System in the Energy Industry
Serbia, Niš, October 22-23, 2017 eNergetics 2017 3rd Virtual International Conference on Science, Technology and Management in Energy Proceedings Editors: Janjić, A., Stajić, Z. Publishers: Research and Development Center “ALFATEC”, Niš, Serbia; Complex System Research Centre, Niš, Serbia Serbia, Niš, October 22-23, 2017 Proceedings of 3rd Virtual International Conference on Science, Technology and Management in Energy Serbia, Niš, October 22-23, 2017 Editors: Prof. Dr. Aleksandar Janjić and Prof. Dr. Zoran Stajić Technical Editor: Dr. Lazar Z. Velimirović Published by: Research and Development Center “ALFATEC”, Niš, Serbia, and Complex System Research Centre, Niš, Serbia Printed by: Blue Copy, Niš, Serbia Number of copies printed: 100 The publishing year: 2017 Printing of this edition has been financially supported by Serbian Ministry of Education, Science and Technological Development ISBN 978-86-80616-02-5 CIP - Каталогизација у публикацији - Народна библиотека Србије, Београд 620.9(082)(0.034.2) VIRTUAL International Conference on Science Technology and Management in Energy (3 ; Niš ; 2017) Energetics 2017 [Elektronski izvor] : proceedings / 3th Virtual International Conference on Science Technology and Management in Energy, Niš, October 22-23, 2017 ; editors Janjić A.[Aleksandar], Stajić Z.[Zoran]. - Niš : Research and Development Centar "Alfatec" : Complex System Research Centre, 2017 (Niš : Blue Copy). - 1 elektronski optički disk (DVD) ; 12 cm Sistemski zahtevi: Nisu navedeni. - Nasl. sa naslovne strane dokumenta. - Tiraž 100. - Bibliografija uz svaki rad. ISBN 978-86-80616-02-5 (RDCA) a) Енергетика - Зборници COBISS.SR-ID 251312908 3rd Virtual International Conference on Science, Technology and Management in Energy Organizer: Research and Development Center “ALFATEC” Co-organizers: Mathematical Institute of the Serbian Academy of Sciences and Arts Faculty of Technical Sciences, UKLO University St. -
EEI:+€E€ O-O I: E:-B E FE; ,^()P O) S€ F* 1H T4
ca N -EqTR t-- N Y^30) \ov SF ie: R O\N oqx \o Nd t F()> oo .=.-t \o d () s s ao =H oo $ + + co >N oo f- \\ !Q -. li._aa) oo€ P (hv q.= > 6U (n- L a n H$,H vtV lP ciE '9EE ; -v; d '= 6 g*^ 2o a1 6fi € FE E E *-,F o i' i' .3 Ede .t) ll s E;€sSH irjj^ (+< AH ___r 50rE € d€.9 o .E€ E spdP AFU -j AVL]HF .lgt(,cd L 1.\ _ a - .='cl .;r hJ'- a! x o.€. - cg gE I F € ? { $8.; E- rj E b.; q) bo n.:rC Y'= ctr H(|)-d> a v) |-- 5 ll - A ? ,, O arE K ar E ir- H c) ' v ., OO FC "^=H A Yoa ;l 6J G- OF 3 €-0H 6A o\-.:'<Jp9i: boo H o v c! + s ;sE O>l-\ rn! 5 lu l-r '= (.) (l) C) * -.i H'3E€:E ggiE$, (, *X (H .=o,ES '€ !{tr F.=.^ E: a.:.! >, T* () >q hdH H (g>-Z 'E'- #-: E (|) ,i-vF o EiY oo'-,- q) ilo EEI:+€E€ o-o i: e:-B E FE; ,^()P o) s€ F* 1H t4. \- ; f s 5.<\ l' 6 o = ta )i FE E i bEg rV^ AF Ae: Ec€ >e; g"EE ob9 I q) lr q.< d .S .2 O.E € .E ; ,*h >\ts 9i c+< .r 9? = ./)0.) OQ(h .:o i; -E bo v rt) -e 9.1 6) q) YtEcX o o.d .= y E'- * cd- Q 6X F ! d !^ c) tF V -r^An K* E Ed'-(/r t 'A o-c) ;x- x dt-P e: a) Fir c., th >P(d(, b P0g =>tt) €) '-G)le-Hi.F .s'E8. -
Fossil Energy and Mineral Reserve Statistics in Bosnia and Herzegovina, Kazakhstan, Kyrgyzstan and Serbia
Fossil energy and mineral reserve statistics in Bosnia and Herzegovina, Kazakhstan, Kyrgyzstan and Serbia A baseline review of quality Prepared for: Submitted by: Mr. Viktor Badaker Robert Smith Regional Advisor Principal Sustainable Energy Division Midsummer Analytics UNECE Date Table of Contents TABLE OF CONTENTS ........................................................................................................ I LIST OF ACRONYMS .......................................................................................................... 3 1 INTRODUCTION ........................................................................................................... 4 1.1 BACKGROUND AND OBJECTIVES ................................................................................. 4 1.1 SCOPE OF THE BASELINE REVIEW .............................................................................. 4 1.2 STRUCTURE OF THIS REPORT .................................................................................... 6 2 OVERVIEW OF FOSSIL ENERGY AND MINERAL RESERVE STATISTICS SYSTEMS 7 2.1 MINISTRIES/AGENCIES/COMPANIES INVOLVED IN THE SYSTEM AND THEIR ROLES ........... 7 2.1.1 Bosnia and Herzegovina .................................................................................. 7 2.1.2 Serbia .............................................................................................................. 8 2.1.3 Kazakhstan ...................................................................................................... 9 2.1.4 Kyrgyzstan ...................................................................................................... -
Europass Curriculum Vitae Personal Information Work Experience
Europass Insert photograph. Remove heading if not relevant (see instructions) Curriculum Vitae Personal information First name(s) / Surname(s) Stevanovic Zoran Address(es) 9 brigade 18/12, 19210 Bor, Serbia Telephone(s) +381 30 445 599 Mobile: + 381 62 401 662 Fax(es) +381 30 435 247 E-mail [email protected] Nationality Serbian Date of birth 30.01.1967 Gender Male Work experience Dates April 2011 to present time Occupation or position held Executive Officer Main activities and responsibilities Planning & managing. Designing, investment and consulting. Engineering: Technologies, Equipment, Research. Name and address of employer Mining and Metallurgy Institute Bor, Zeleni bulevar 35, 19210, Bor Type of business or sector Engineering Dates April 2002 – April 2011 Occupation or position held Mineral Processing Department Manager Main activities and responsibilities Mineral Processing Department planning & managing. Designing, investment and consulting for agitation and percolation leaching of copper, gold and silver, and extraction of metals from bearing solutions. Mineral processing engineering: Technologies, Equipment, Research Name and address of employer Mining and Metallurgy Institute Bor, Zeleni bulevar 35, 19210, Bor Type of business or sector Mineral processing Department Dates Feb. 1998 – April 2002 Occupation or position held Professional Assistant Main activities and responsibilities Hydrometallurgy processes (Cu, Au, Ag, ores). Designing, investment and consulting for agitation and percolation leaching of copper, gold and silver, and extraction of metals from bearing solutions. Mineral processing engineering: Technologies, Equipment, Research Name and address of employer Mining and Metallurgy Institute Bor, Zeleni bulevar 35, 19210, Bor Type of business or sector Mineral processing Department / Chemicals methods of mineral processing Section Dates Feb. -
The Mineral Industry of Serbia in 2010
2010 Minerals Yearbook SERBIA U.S. Department of the Interior October 2012 U.S. Geological Survey THE MINERAL INDUSTRY OF SERBIA By Mark Brininstool Serbia remained a modest producer of mineral commodities Group Inc. of Canada for the construction of a copper smelter and its output was not significant in terms of world production. and a sulfuric acid plant. The deal was financed by Export Within the Southern Balkans, the country was an important Development Canada and the Serbian Government. The new producer of such metals as copper, iron and steel, and refined smelter, which was scheduled to be completed in 2013, would petroleum products. On February 18, 2008, the Serbian Province have a production capacity of 80,000 metric tons per year of of Kosovo declared its independence. The U.S. Government has copper anode (SNC-Lavalin Group Inc., 2010; Vasovic, 2010). recognized Kosovo’s independence and, therefore, Kosovo is included as a separate country in the U.S. Geological Survey’s Industrial Minerals Minerals Yearbook. Consequently, this report contains economic and mineral production data only for Serbia. Lithium.—Rio Tinto plc reported that its lithium project in Jadar had 125.3 million metric tons (Mt) of inferred resources Minerals in the National Economy of ore containing 1.8% lithium oxide and 16.2 Mt of inferred resources of borates. The project was still in the exploration In 2010, Serbia’s gross domestic product (GDP) increased phase of development, but Rio Tinto estimated that the project by 1.8%. In 2009 (the most recent year for which data were could begin production within 6 years if it were to be developed available), mining and quarrying made up about 1.3% of the (Rio Tinto plc, 2011, p. -
COAL PRODUCTION in SERBIA — STATUS and PERSPECTIVE 1. Introduction 2. Production of Overburden and Installed Equipment
Górnictwo i Geoinżynieria • Rok 35 • Zeszyt 3 • 2011 Vladimir Pavlovic*, Dragan Ignjatović*, Predrag Jovančić*, Slobodan Mitrović** COAL PRODUCTION IN SERBIA ⎯ STATUS AND PERSPECTIVE 1. Introduction Coal is by far most important Serbian energy potential, with 85% participation in structure of overall primary energy reserves. Several assessments of total coal reserves were performed to date, but due to different assessment criteria and various level of exploration, these assessments yielded unequal results. Reserves Balance from 2005, states that over 76% of total coal reserves was in Kosovo-Metohija basin. Same source provides information that 14% of coal reserves was in Kolubara basin, while 3.3% is in Kostolac basin. Sjenica and Kovin deposits have only 2.7% of total reserves. Also, it can be seen that contribution of lignite within total balanced reserves is around 93%. Most important lignite reserves in Serbia, excluding provinces are in Kolubara and Kostolac basins (including Kovin basin, which is extension of Kostolac basin). Coal was, is and will be most important source of primary energy in Serbia, regarding both the amounts and energy, regardless to any correction of existing reserves estimations. Largest consumers of coal in Serbia are thermal power plants, with consumption of 96% of total annual production, while remaining part is dried and screened for the industry and open market. Lignite power plants are providing some 60% of total electricity production, while in winter periods, during which demand for electricity is largest, this contribution increases up to 75%. 2. Production of overburden and installed equipment Coal production at Elektroprivreda Srbije takes place in two basins on five open cast mines (Field B, Field D, Tamnava-West Field and Veliki Crljeni in Kolubara basin and * Faculty of Mining and Geology, University of Belgrade, Serbia ** JP Elektroprivreda Srbije, Beograd, Serbia 261 Drmno in Kostolac basin), while two open cast mines in Kostolac basin are in closing process (Ćirikovac and Klenovik). -
SWOT Analysis
Pol. J. Environ. Stud. Vol. 28, No. 5 (2019), 3243-3251 DOI: 10.15244/pjoes/93745 ONLINE PUBLICATION DATE: 2019-05-17 Original Research Production of Agri-Energy Crop Miscanthus gigantheus on Land Degraded by Power Industry: SWOT Analysis Dragana Kalabić1, Gordana Dražić1*, Nikola Dražić1, Jela Ikanović2 1University Singidunum Faculty for Applied Ecology Futura, Belgrade Republic of Serbia 2Belgrade University Faculty of Agriculture, Belgrade, Republic of Serbia Received: 5 June 2018 Accepted: 24 July 2018 Abstract The hypothesis that land degraded by activities in the Kolubara Mining Basin may be restored by production of agri-energy crop Miscanthus gigantheus in ecologically and economically sustainable manner was investigated. The characteristics of the arable soil in the zone of influence of the thermal power plant Kolubara A, the overburden from the mine Kolubara and the ash from Kolubara A indicate limited fertility due to low contents of N and organic C, also contain heavy metals in concentrations between maximal allowable and remediation values (Ni, Cu, Zn), are slightly to moderately contaminated. Contents of heavy metals in aboveground biomass of miscanthus is low, making it suitable for use as biofuel. On the opposite side, in whole plants there are significant contents of Cr, Zn and Ni, mainly in underground organs, indicating phytostabilization potential. – Main strength: the use of marginal land for the production of bioenergetic crops. – Weaknesses: low yield. – Opportunity: use of large marginal land areas with a simultaneous reduced risk of heavy metal transfer to the environment, improving yields with the use of more intensive agri-technical measures. – Threats: the poorly developed biomass market as well as the lack of interest by land owners for its remediation. -
A Clear and Present Danger
2015 A clear and present danger How financial institutions and authorities have failed to address the human impacts of resettlement in Serbia's lignite mining fields Lignite is among the dirtiest of fossil fuels; mining it may have profoundly negative impacts on soil, vegetation, water, air, and the livelihoods of people in neighbouring communities. But, nowhere is it more self-evident than in Serbia's Kolubara Mining Basin, one of the largest sources of lignite in Europe, where mining has continued for over fifty years. Nostromo Research CEE Bankwatch Network June 2015 This publication has been produced with the financial assistance of the European Union. The content of this publication is the sole responsibility of CEE Bankwatch Network and can under no circumstances be regarded as reflecting the position of the European Union. Bankwatch is also grateful to the following donors for their ongoing support of our work: Charles Stewart Mott Foundation, European Climate Foundation, International Visegrad Fund, Sigrid Rausing Trust. Commissioned by CEE Bankwatch Network Author: Roger Moody June 2015 1 | P a g e Contents Executive Summary ................................................................................................................................................................. 2 A Clear Present and Future Danger ................................................................................................................................... 3 Serbia's lignite – decades of destruction and dubious benefit .....................................................................................