Cross-Connections and Backflow Prevention Manual
Total Page:16
File Type:pdf, Size:1020Kb
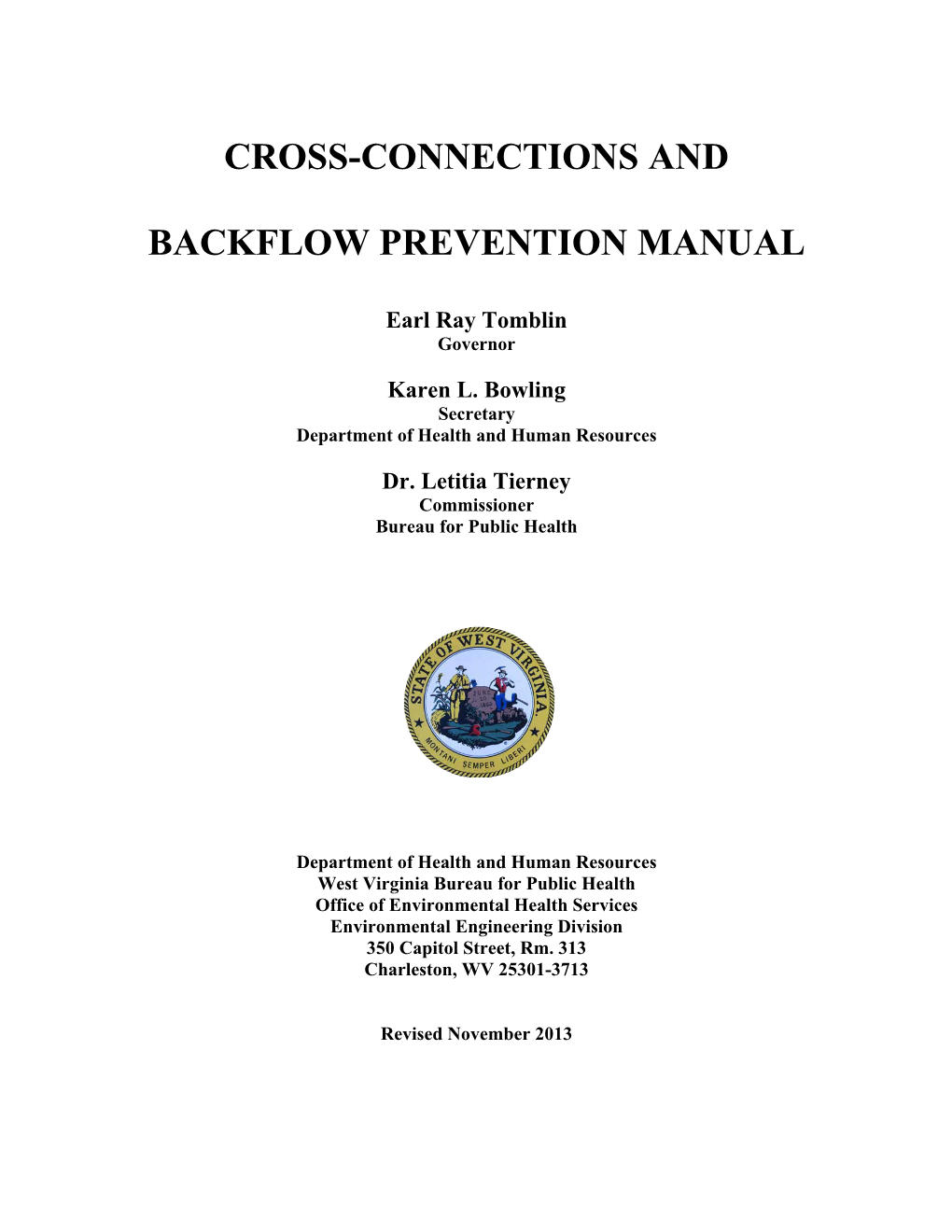
Load more
Recommended publications
-
Cross-Connection Control Manual and Design Criteria for Cross-Connection Control Plans, Ordinances, and Policies
CROSS-CONNECTION CONTROL MANUAL AND DESIGN CRITERIA FOR CROSS-CONNECTION CONTROL PLANS, ORDINANCES, AND POLICIES DIVISION OF WATER SUPPLY TENNESSEE DEPARTMENT OF ENVIRONMENT AND CONSERVATION 2008 1. TABLE OF CONTENTS Tennessee Department of Environment and Conservation Guidelines…………..…………….……................. p.1 Definition of Terms............................................................................................................................................p.3 CHAPTER I. Introduction to Backflow Prevention…………………………………………………………..…....…....…..p.6 1.1 Introduction 1.2 Objective 1.3 Causes of Backflow 1.3.1 Backsiphonage 1.3.2 Backpressure II. Responsibility and Authority for Cross-Connection Control…………………………………………….....p.9 2.1 Responsibility 2.1.1 The Water Purveyor 2.1.2 The Customer 2.1.3 Plumbing Inspection Agencies 2.1.4 Installers and Maintenance Personnel 2.1.5 Tennessee Department of Environment and Conservation 2.1.6 Legal Consideration 2.2 Authority 2.2.1 General Discussion 2.2.2 Local Authority 2.2.3 State Wide Authority 2.2.4 Federal Authority III. Developing and Implementing a Cross-Connection Control Program………………………………..….p.14 3.1 Introduction 3.2 Outline of Considerations in Preparing a Plan 3.3 Discussions of Local Cross-Connection Control Plan 3.4 Implementation of the Cross-Connection Control Plan 3.5 Establishing Priorities for Investigation IV. Recommended Practices……………………………………………………………………………………...p.19 4.1 Basic Consideration 4.2 Premises Isolation 4.3 Situations Requiring Maximum Protection 4.4 Establishments -
Backflow Prevention Assembly Installation Standards
Revised Oct. 06 BACKFLOW PREVENTION ASSEMBLY INSTALLATION STANDARDS All backflow prevention assembly installation shall be in accordance with the following Standards unless otherwise directed or approved by the San Antonio Water System (SAWS). These instructions are general guidelines and are subject to change without notice. Any Inquiries or requests should be directed to the San Antonio Water System’s Backflow Prevention Section, at (210) 233-2421. I. GENERAL INSTRUCTIONS 1. Assemblies will be installed in an accessible location to facilitate maintenance, testing and repair, and should be located no more than five feet above the floor or grade level. The backflow preventer must be installed between the meter and the owner’s first tap or tee (total containment) unless otherwise approved. Internal containment will be approved for car washes, schools, retail laundries, and multiple lease spaces by individual review. In no instances will the assembly be allowed in the same vault with the San Antonio Water System’s water meter. Containment assemblies on fire lines must be located within 100’ (pipe length) of the property line. 2. Vault lids will be constructed in such a manner as to permit easy accessibility at all times by an individual. Vaults deeper than five feet shall be provided with a ladder permanently attached to a side wall. It is the contractor’s and owner’s obligation and responsibility to ensure OSHA regulations are adhered to in the construction of all vaults. Additionally, confined space regulations are to be consulted and followed in the testing and maintenance of the backflow prevention assemblies. 3. Before installing the assembly, pipelines should be thoroughly flushed to remove foreign material. -
Methods and Devices for the Prevention of Backflow and Back
Chapter Four Air Gap (2) The air gap may be easily Methods and Devices defeated in the event that the Air gaps are non-mechanical “2D” requirement was purposely backflow preventers that are or inadvertently compromised. for the Prevention of very effective devices to be used Excessive splash may be encoun- where either backsiphonage or tered in the event that higher Backflow and backpressure conditions may than anticipated pressures or exist. Their use is as old as flows occur. The splash may be a Back-Siphonage piping and plumbing itself, but cosmetic or true potential only relatively recently have hazard—the simple solution standards been issued that being to reduce the “2D” wide choice of devices standardize their design. In dimension by thrusting the Aexists that can be used to general, the air gap must be supply pipe into the receiving prevent backsiphonage and twice the supply pipe diameter funnel. By so doing, the air gap backpressure from adding but never less than one inch. is defeated. contaminated fluids or gases See Figure 12. into a potable water supply (3) At an air gap, we expose the system. Generally, the selection water to the surrounding air FIGURE 12. with its inherent bacteria, dust of the proper device to use is Air gap. based upon the degree of hazard particles, and other airborne posed by the cross-connection. pollutants or contaminants. In addition, the aspiration effect of Additional considerations are Diameter based upon piping size, location, “D” the flowing water can drag down and the potential need to surrounding pollutants into the periodically test the devices to “2D” reservoir or holding tank. -
Evaluation of Backflow Prevention Devices: a State-Of-The-Art Report
NBSIR 76-1070 Evaluation of Backflow Prevention Devices: A State-of-the-Art Report Grover C. Sherlin Robert W. Beausoliel Center for Building Technology Institute for Applied Technology National Bureau of Standards Washington, D. C. 20234 June 1976 Final Report Prepared for Water Supply Division Environmental Protection Agency Washington, D. C. 20460 NBSIR 76-1070 EVALUATION OF BACKFLOW PREVENTION DEVICES: A STATE-OF-THE-ART REPORT Grover C. Sherlin Robert W. Beausoliel Center for Building Technology Institute for Applied Technology National Bureau of Standards Washington, D. C. 20234 June 1976 Final Report Prepared for Water Supply Division Environmental Protection Agency Washington, D. C. 20460 U.S. DEPARTMENT OF COMMERCE, Elliot L. Richardson, Secretary Edward O. Vetter, Under Secretary Dr. Betsy Ancker-Johnson. Assistant Secretary for Science and Technology NATIONAL BUREAU OF STANDARDS, Ernest Ambler, Acting Director CONTENTS Abstract 1 1. Introduction 2 1.1 Purpose and Scope 2 1.2 Fundamentals of Backflow 3 2. Background Information 7 2.1 Historical Background and Recorded Incidents of Backflow through Backflow Connection and Cross-Connections 7 2.2 Navy Study of FCCCR Certification Procedures 9 2.3 A.S.S.E. Concern for Backflow Problems 10 2.4 Backflow Prevention Devices and Piping Arrangements 12 3. Elements in the Evaluation of Backflow Prevention Devices... 18 3.1 The Product Standards 18 3.2 The Plumbing Codes 19 3.3 The Manufacturers of Backflow Prevention Devices 23 3.4 Testing Laboratories 23 3.5 A Conceptual Model Cross-Connection Control Program 36 / 4. Evaluation of Devices 39 4.1 Design Considerations that Affect Reliability 39 4.2 Methods that Test Appropriate Attributes 45 5. -
Hose Bibb Vacuum Backflow Preventer with Double Check Valve Breaker Atmospheric Vent (Continuous Pressure)
CROSS CONNECTION: A cross connection is any actual or potential physical connection between a potable water supply line and any pipe, vessel, or machine containing a non potable fluid or has the possibility of containing a non potable fluid, solid or gas, such that it is possible for the non potable fluid, solid or gas to enter the water system by backflow. A cross connection could be any physical arrangement whereby a potable water supply is connected, directly or indirectly, with any non potable or unapproved water supply system, sewer, drain, conduit, pool, storage reservoir, plumbing fixture, or any other device which contains, or may contain, contaminated water, liquid, gases, sewage, or other waste of unknown or unsafe quality which may be capable of imparting contamination to the potable water supply as a result of backflow. ** BACKFLOW: Backflow is a flow in reverse from the normal direction of flow in a piping system. It occurs due to a differential pressure existing between two different points within a continuous fluid system; fluids of higher pressure flowing to a fluid of lower pressure. Backflow may occur due to either backsiphonage or backpressure. ** BACKSIPHONAGE: Backsiphonage is caused by negative pressure in the supply piping. Some common causes of backsiphonage are: (1) high velocity pipe lines; (2) line repair or break that is lower than a service point; (3) lowered main pressure due to high water withdrawal rate such as fire fighting or water main flushing; or (4) reduced supply pressure on the suction side of the booster pump. CONTINUOUS PRESSURE: An installation in which the pressure is being supplied continuously to a backflow prevention device for periods over 12 hours at a time. -
2015 International Plumbing Code (Amended) Backflow/Cross-Connection Control Requirements
2015 International Plumbing Code (amended) Backflow/Cross-Connection Control Requirements AMENDED SECTION NEW SECTION NOTE: Sections highlighted yellow are sections of the 2015 IPC that were amended. The wording in the yellow sections include the amended language (i.e., if you compare Section 312.10.1 below to that of the 2015 IPC, they will be different because the section below contains Louisiana amendments). Sections highlighted green are new sections added (i.e., there is no Section 312.10.3 in the 2015 IPC as there is in this document, it was added to the Louisiana code via Louisiana amendments). 312.10 Installation, inspection and testing of backflow prevention assemblies, barometric loops and air gaps. Installation, inspection and testing shall comply with Sections 312.10.1 through 312.10.3. 312.10.1 Inspections. Annual inspections shall be made of all backflow prevention assemblies, barometric loops and air gaps to determine whether they are operable, properly installed and maintained, and meet testing/code requirements. Inspections of backflow prevention devices including barometric loops and air gaps used to protect high degree of hazard cross connections shall be documented in writing and the report provided to the owner of the backflow prevention device. 312.10.2 Testing. Reduced pressure principle, double check, pressure vacuum breaker, reduced pressure detector fire protection, double check detector fire protection, and spill-resistant vacuum breaker backflow preventer assemblies shall be tested at the time of installation, immediately after repairs or relocation and at least annually. The testing procedure shall be performed in accordance with one of the following standards: ASSE 5013, ASSE 5015, ASSE 5020, ASSE 5047, ASSE 5048, ASSE 5052, ASSE 5056, CSA B64.10.1, USC’s FCCC & HR’s “Manual of Cross-Connection Control”, or UFL’s TREEO’s “Backflow Prevention – Theory and Practice”. -
Subchapter E : Complaint Process
Texas Commission on Environmental Quality Page 1 Chapter 344 - Landscape Irrigation SUBCHAPTER E: BACKFLOW PREVENTION AND CROSS CONNECTIONS §§344.50 - 344.52 Effective January 1, 2009 §344.50. Backflow Prevention Methods. (a) Any irrigation system that is connected to a public or private potable water supply must be connected through a commission-approved backflow prevention method. The backflow prevention device must be approved by the American Society of Sanitary Engineers; or the Foundation for Cross- Connection Control and Hydraulic Research, University of Southern California; or the Uniform Plumbing Code; or any other laboratory that has equivalent capabilities for both the laboratory and field evaluation of backflow prevention assemblies. The backflow prevention device must be installed in accordance with the laboratory approval standards or if the approval does not include specific installation information, the manufacturer's current published recommendations. (b) If conditions that present a health hazard exist, one of the following methods must be used to prevent backflow; (1) An air gap may be used if: (A) there is an unobstructed physical separation; and (B) the distance from the lowest point of the water supply outlet to the flood rim of the fixture or assembly into which the outlet discharges is at least one inch or twice the diameter of the water supply outlet, whichever is greater. (2) Reduced pressure principle backflow prevention assemblies may be used if: (A) the device is installed at a minimum of 12 inches above ground in a location that will ensure that the assembly will not be submerged; and (B) drainage is provided for any water that may be discharged through the assembly relief valve. -
Backflow Prevention & Cross-Connection Control Manual
6606 Tussing Road – P.O. Box 4009 Reynoldsburg, Ohio 43068-9009 (614) 644-3153 FAX (614) 995-1146 Backflow Prevention & Cross-Connection Control Manual For the Education of Ohio Certified Backflow Prevention Technicians Administered by: The Ohio Department of Commerce, Industrial Compliance, Backflow Section. 1 Manual Development Sponsored By: Ohio Department of Commerce Ohio Department of Health Ohio Environmental Protection Agency Ohio Rural Water Association Operator Training Committee of Ohio, Incorporated Ohio Section, American Water Works Association Original Manual Development Committee: David Bornino, Ohio Environmental Protection Agency Frank Czako, APHC Backflow School Rick Eberle, Ohio Section, American Waterworks Association Ron Graves, Plumbers, Pipefitters and Service Technicians Local 189 JATC Jess Jones, Operator Training Committee of Ohio, Inc. Andy Provoznik, Ohio Rural Water association Ralph Reeb, Ohio Department of Commerce Terry Urbanek, Plumbers & Pipefitters Local 120 Jack Wormley, PHCC of Ohio ***IN MEMORY…a special appreciation and thanks to Jess Jones, Operator Training Committee of Ohio Inc., for a lifetime commitment to the Water Purveyor and Backflow Industries.*** ***IN MEMORY…of Ralph Reeb, Plumbing Chief, Ohio Department of Commerce, Division of Industrial Compliance.*** ***IN MEMORY…of Jack Wormley, PHCC of Ohio.*** 2 TABLE OF CONTENTS Table of Contents …………………………………………………..3 About This Course …………………………………………………..4 Introduction …………………………………………………..5 Authority in Ohio …………………………………………………..6 Responsibility -
Undersizing Backflow Preventers
Undersizing Backflow Preventers In the Fall 2004 issue of Cross Talk, the Undersized backflow preventer: issue of oversized backflow preventers 1-inch piping & 1/2-inch backflow preventer was discussed. It was determined that placing a backflow preventer on a water line of a size smaller than the backflow preventer would not be detrimental to the operation of the assembly. Another issue that arises periodically is the undersizing of an assembly. If the water line feeding a property were a 3-inch water line with a 3- inch water meter, one would expect a 3-inch assembly to be installed. But some have desired to install a 2- inch assembly instead. Perhaps this is due to the lower price of a 2-inch assembly. This is undersizing the backflow preventer assembly. A problem could occur if the assembly Contents Rotating Shutoff Valves p. 5 is undersized. The flow rate through the 2-inch assembly could exceed its Aesthetics of Assemblies p. 3 rated flow. The higher velocity of water through the assembly may damage the Double Checks on assembly. This is not likely to occur Irrigation Systems p. 4 continued on page 6 Foundation Membership The Foundation’s Membership Program provides many benefits to the Members of the Foundation. These include: a twenty-five percent discount on manuals, twenty percent dis- count on Foundation Training Courses for any employee of the Member company/organi- zation, the List of Approved Backflow Prevention Assemblies, printed quarterly, and access to the up-to-the-minute version of the List for those Members with Internet access. -
Backflow Prevention Cross-Connection Control Handbook
Backflow Prevention Cross-Connection Control Handbook Watts.com A Brief History of Cross-Connection Control Man has long recognized the need for pure drinking water, but only in the last 50 or 60 years has there been any real effort to prevent contamination caused by cross-connections. Although double check valves came into use around the turn of the century to isolate fire mains and industrial water lines Contents from the potable water supply, little interest was shown in the individual treatment of plumbing fixtures. Backflow — What is it? ................................................. 1 In 1929 the major breakthrough came when a device consist- Case Histories ......................................................... 2 - 3 ing of two check valves with a relief valve between them was Typical Cross-Connections .................................... 4 - 5 successfully tested in Danville, Illinois. However, this valve was not produced commercially and it was not until the late Backflow Prevention Devices ...................................... 6 1930’s that the real development of effective vacuum breakers and backflow preventers took place. How Backflow Prevention Devices Work ................... 7 It was in this period that ordinances for cross-connection Device Selection ........................................................... 8 control began to be enforced. The Safe Drinking Water Act, Installation ............................................................... 8 - 9 signed into law by President Ford, placed more emphasis on the -
Theory of Backflow and Backsiphonage
Chapter Three Pabsolute = Pgage + 14.7psi Water Pressure Theory of Backflow or For an understanding of the Pgage = Pabsolute – 14.7 psi nature of pressure and its and Backsiphonage In essence then, absolute relationship to water depth, pressure is the total pressure. consider the pressure exerted on Gage pressure is simply the the base of a cubic foot of water pressure read on a gage. If there at sea level. (See Fig. 1) The is no pressure on the gage other average weight of a cubic foot than atmospheric, the gage cross-connection1 is the of water is 62.4 pounds per would read zero. Then the link or channel connecting square foot gage. The base may A absolute pressure would be a source of pollution with a be subdivided into 144-square equal to 14.7 psi which is the potable water supply. The inches with each subdivision atmospheric pressure. polluting substance, in most being subjected to a pressure of The term vacuum indicates cases a liquid, tends to enter the 0.433 psig. that the absolute pressure is less potable supply if the net force Suppose another cubic foot than the atmospheric pressure acting upon the liquid acts in of water were placed directly and that the gage pressure is the direction of the potable on top of the first (See Fig. 2). negative. A complete or total supply. Two factors are therefore The pressure on the top surface vacuum would mean a pressure essential for backflow. First, of the first cube which was of 0 psia or -14.7 psig. -
Backflow Device
BACKFLOW DEVICE City of Newberg City Hall ~ P.O. Box 970 ~ 414 E First Street ~ Newberg, OR 97132 ~ Phone: (503) 537-1240 ~ Fax: (503) 537-1272 www.newbergoregon.gov K:\WP\COMMON\FormsCD\Bldg Div Forms\Backflow Device.doc8-24-11 Page 1 Submitting a Permit SUBMITTAL Permit Application Applications are available online at www.newbergoregon.gov and City Hall. Permits can also be obtained online at www.oregon-epermitting.info, through the State ePermitting program. Fees Fees are due at time of issuance. INSPECTIONS Call (503) 554-7714 for Inspections Installation All devices subject to freezing shall be protected from freezing DOUBLE CHECK BACKFLOW ASSEMBLY Installed where potential contamination would not be hazardous may be installed above or below ground. Should not be flooded continually. Protects against backpressure or back siphonage. Same installation requirements as “double check valve below grade”. ABOVE GROUND Freezing The double checks above ground need to be protected from freezing (i.e. insulation, heat tape or installed in a heated area). Installation When installed above the ground they are normally required to be installed in the horizontal position (unless the manufacturer approves them to be installed in the vertical position, check the installation instructions that came with the unit). Location Double check valves can be installed either above or below the ground. Shut off valve You are required to have a shutoff valve in front of the double check. Test ports The test ports (4ea) on top, have to be plugged with either brass or plastic plugs and protected from debris entry. Testing Required to be tested by a certified backflow tester when the unit is installed, replaced or repaired.