Grain Boundary Engineering: Historical Perspective and Future Prospects
Total Page:16
File Type:pdf, Size:1020Kb
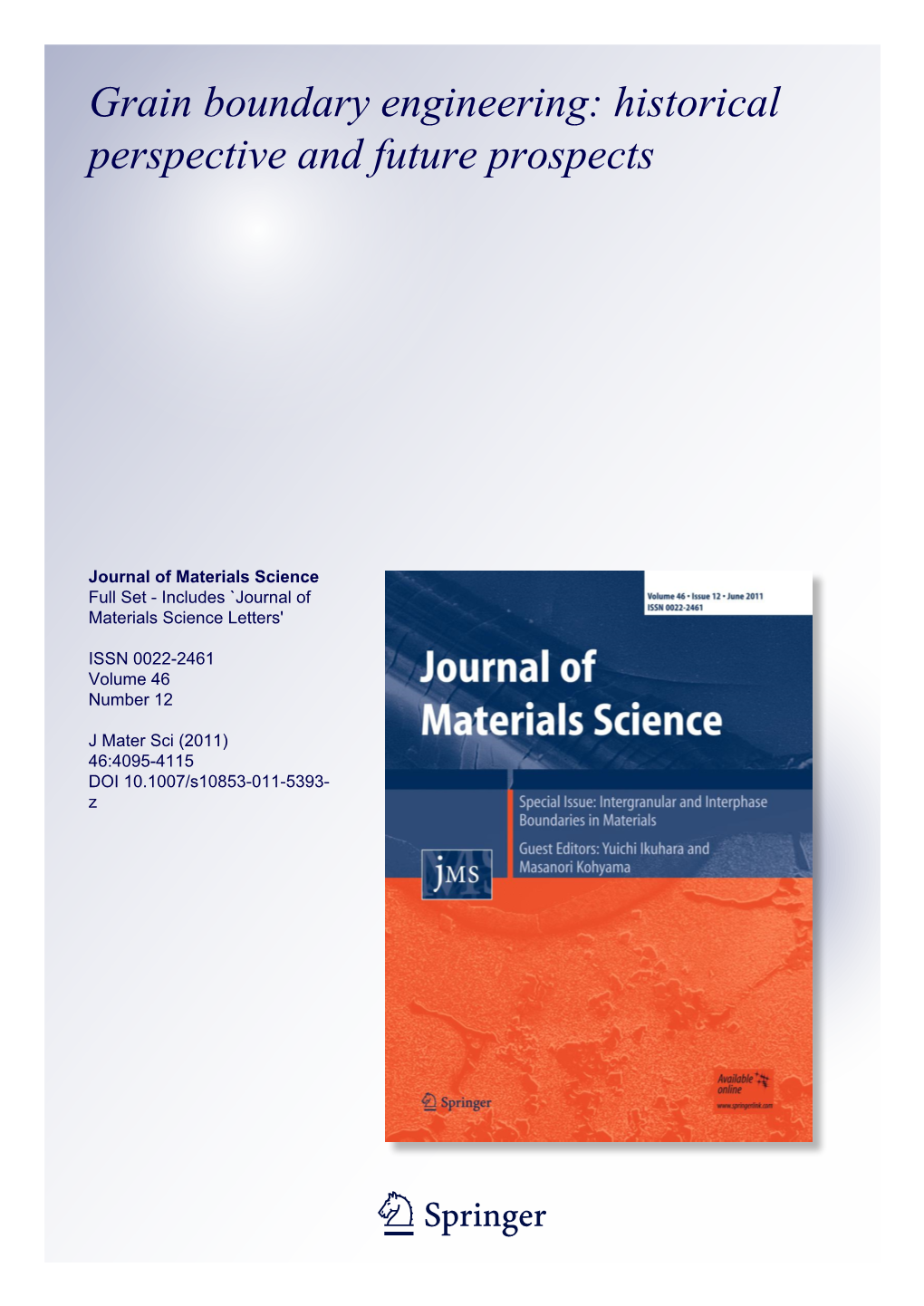
Load more
Recommended publications
-
Ceramics Overview: Classification by Microstructure and Processing Methods
Clinical Ceramics overview: classification by microstructure and processing methods Edward A. McLaren 1 and Russell Giordano 2 Abstract The plethora of ceramic systems available today for all types of indirect restorations can be confusing and overwhelming for the clinician. Having a better understanding of them is important. In this article, the authors use classification systems based on microstructural components of ceramics and the processing techniques to help illustrate the various properties. Introduction component atoms, and may exhibit ionic or covalent Many different types of ceramic systems have been bonding. Although ceramics can be very strong, they are also introduced in recent years for all types of indirect extremely brittle and will catastrophically fail after minor restorations, from very conservative nonpreparation veneers, flexure. Thus, these materials are strong in compression but to multi-unit posterior fixed partial dentures and everything weak in tension. in between. Understanding all the different nuances of Contrast that with metals: metals are non-brittle (display materials and material processing systems is overwhelming elastic behaviour) and ductile (display plastic behaviour). This and can be confusing. This article will cover what types of is because of the nature of the interatomic bonding, which is ceramics are available based on a classification of the called metallic bonds; a cloud of shared electrons that can microstructural components of the ceramic. A second, easily move when energy is applied defines these bonds. This simpler classification system based on how the ceramics are is what makes most metals excellent conductors. Ceramics can processed will give the main guidelines for their use. be very translucent to very opaque. -
Texture and Microstructure
Texture and Microstructure • Microstructure contains far more than qualitative descriptions (images) of cross-sections of materials. • Most properties are anisotropic •it is important to quantitatively characterize the microstructure including orientation information (texture). In latin, textor means weaver In materials science, texture way in which a material is woven. Polycrystalline material is constituted from a large number of small crystallites (limited volume of material in which periodicity of crystal lattice is present). Each of these crystallites has a specific orientation of the crystal lattice. A randomly texture sheet A strongly textured sheet The cube texture (001) ND (Sheet Normal Direction) [100] RD (Sheet Rolling Direction) Crystallographic texture is the orientation distribution of crystallites in a polycrystalline material Texture :Metallurgists and Materials Scientists Fabric :Geologists and Mineralogists Preferred Orientation :Everybody Why textures? Texture influences the following properties: •Elastic modulus •Yield strength •Tensile ductility and strength •Formability •Fatigue strength •Fracture toughness •Stress corrosion cracking •Electrical and Magnetic properties Major fields of application A. Conventional • Aluminium industry • Steel industry • LC steels • Electrical steels • Titanium alloys • Zirconium base nuclear grade alloys B. Modern • High Tc superconductors • Thin films for semiconducting and magnetic devices • Bulk magnetic materials • Structural Ceramics • Polymers Beverage Cans Aluminium beverage -
Introduction to Material Science and Engineering Presentation.(Pdf)
Introduction to Material Science and Engineering Introduction What is material science? Definition 1: A branch of science that focuses on materials; interdisciplinary field composed of physics and chemistry. Definition 2: Relationship of material properties to its composition and structure. What is a material scientist? A person who uses his/her combined knowledge of physics, chemistry and metallurgy to exploit property-structure combinations for practical use. What are materials? What do we mean when we say “materials”? 1. Metals 2. Ceramics 3. Polymers 4. Composites - aluminum - clay - polyvinyl chloride (PVC) - wood - copper - silica glass - Teflon - carbon fiber resins - steel (iron alloy) - alumina - various plastics - concrete - nickel - quartz - glue (adhesives) - titanium - Kevlar semiconductors (computer chips, etc.) = ceramics, composites nanomaterials = ceramics, metals, polymers, composites Length Scales of Material Science • Atomic – < 10-10 m • Nano – 10-9 m • Micro – 10-6 m • Macro – > 10-3 m Atomic Structure – 10-10 m • Pertains to atom electron structure and atomic arrangement • Atom length scale – Includes electron structure – atomic bonding • ionic • covalent • metallic • London dispersion forces (Van der Waals) – Atomic ordering – long range (metals), short range (glass) • 7 lattices – cubic, hexagonal among most prevalent for engineering metals and ceramics • Different packed structures include: Gives total of 14 different crystalline arrangements (Bravais Lattices). – Primitive, body-centered, face-centered Nano Structure – 10-9 m • Length scale that pertains to clusters of atoms that make up small particles or material features • Show interesting properties because increase surface area to volume ratio – More atoms on surface compared to bulk atoms – Optical, magnetic, mechanical and electrical properties change Microstructure – 10-6 • Larger features composed of either nanostructured materials or periodic arrangements of atoms known as crystals • Features are visible with high magnification in light microscope. -
Correlation Between Crystal Structure, Surface/Interface Microstructure, and Electrical Properties of Nanocrystalline Niobium Thin Films
nanomaterials Article Correlation between Crystal Structure, Surface/Interface Microstructure, and Electrical Properties of Nanocrystalline Niobium Thin Films L. R. Nivedita 1, Avery Haubert 2, Anil K. Battu 1,3 and C. V. Ramana 1,3,* 1 Center for Advanced Materials Research, University of Texas at El Paso, 500 West University Avenue, El Paso, TX 79968, USA; [email protected] (L.R.N.); [email protected] (A.K.B.) 2 Department of Physics, University of California, Santa Barbara, Broida Hall, Santa Barbara, CA 93106, USA; [email protected] 3 Department of Mechanical Engineering, University of Texas at El Paso, 500 West University Avenue, El Paso, TX 79968, USA * Correspondence: [email protected]; Tel.: +1-915-747-8690 Received: 10 May 2020; Accepted: 26 June 2020; Published: 30 June 2020 Abstract: Niobium (Nb) thin films, which are potentially useful for integration into electronics and optoelectronics, were made by radio-frequency magnetron sputtering by varying the substrate temperature. The deposition temperature (Ts) effect was systematically studied using a wide range, 25–700 ◦C, using Si(100) substrates for Nb deposition. The direct correlation between deposition temperature (Ts) and electrical properties, surface/interface microstructure, crystal structure, and morphology of Nb films is reported. The Nb films deposited at higher temperature exhibit a higher degree of crystallinity and electrical conductivity. The Nb films’ crystallite size varied from 5 to 9 ( 1) nm and tensile strain occurs in Nb films as Ts increases. The surface/interface morphology of ± the deposited Nb films indicate the grain growth and dense, vertical columnar structure at elevated Ts. The surface roughness derived from measurements taken using atomic force microscopy reveal that all the Nb films are characteristically smooth with an average roughness <2 nm. -
Rotary Friction Welding of Inconel 718 to Inconel 600
metals Article Rotary Friction Welding of Inconel 718 to Inconel 600 Ateekh Ur Rehman * , Yusuf Usmani, Ali M. Al-Samhan and Saqib Anwar Department of Industrial Engineering, College of Engineering, King Saud University, Riyadh 11451, Saudi Arabia; [email protected] (Y.U.); [email protected] (A.M.A.-S.); [email protected] (S.A.) * Correspondence: [email protected]; Tel.: +966-1-1469-7177 Abstract: Nickel-based superalloys exhibit excellent high temperature strength, high temperature corrosion and oxidation resistance and creep resistance. They are widely used in high temperature applications in aerospace, power and petrochemical industries. The need for economical and efficient usage of materials often necessitates the joining of dissimilar metals. In this study, dissimilar welding between two different nickel-based superalloys, Inconel 718 and Inconel 600, was attempted using rotary friction welding. Sound metallurgical joints were produced without any unwanted Laves or delta phases at the weld region, which invariably appear in fusion welds. The weld thermal cycle was found to result in significant grain coarsening in the heat effected zone (HAZ) on either side of the dissimilar weld interface due to the prevailing thermal cycles during the welding. However, fine equiaxed grains were observed at the weld interface due to dynamic recrystallization caused by severe plastic deformation at high temperatures. In room temperature tensile tests, the joints were found to fail in the HAZ of Inconel 718 exhibiting good ultimate tensile strength (759 MPa) without a significant loss of tensile ductility (21%). A scanning electron microscopic examination of the fracture surfaces revealed fine dimpled rupture features, suggesting a fracture in a ductile mode. -
Introduction to Microstructure
Materials and Minerals Science Practical 17 CP1 Course C: Microstructure Introduction to microstructure 1.1 What is microstructure? When describing the structure of a material, we make a clear distinction between its crystal structure and its microstructure. The term ‘crystal structure’ is used to describe the average positions of atoms within the unit cell, and is completely specified by the lattice type and the fractional coordinates of the atoms (as determined, for example, by X-ray diffraction). In other words, the crystal structure describes the appearance of the material on an atomic (or Å) length scale. The term ‘microstructure’ is used to describe the appearance of the material on the nm-cm length scale. A reasonable working definition of microstructure is: “The arrangement of phases and defects within a material.” Microstructure can be observed using a range of microscopy techniques. The microstructural features of a given material may vary greatly when observed at different length scales. For this reason, it is crucial to consider the length scale of the observations you are making when describing the microstructure of a material. In this course you will learn about how and why microstructures form, and how microstructures are observed experimentally. Most importantly, microstructures affect the physical properties and behaviour of a material, and we can tailor the microstructure of a material to give it specific properties (this is the subject of the next course). The microstructures of natural minerals provide information about their complex geological history. Microstructure is a fundamental part of all materials and minerals science, and these themes will be expanded on in subsequent courses. -
Understanding Materials Microstructure and Behavior at the Mesoscale A.D
Understanding materials microstructure and behavior at the mesoscale A.D. Rollett , G.S. Rohrer , and R.M. Suter Taking the mesoscale to mean length and time scales at which a material’s behavior is too complex to be understood by construction from the atomistic scale, we focus on three- dimensional characterization and modeling of mesoscale responses of polycrystals to thermal and mechanical loading. Both elastic and plastic internal structural responses are now accessible via high-energy x-ray probes. The combination of diffraction experiments and computed tomography, for example, is yielding new insights into how void formation correlates with microstructural features such as grain boundaries and higher-order junctions. The resulting large, combined data sets allow for validation of micromechanical and thermal simulations. As detectors improve in resolution, quantum effi ciency, and speed of readout, data rates and data volumes present computational challenges. Spatial resolutions approach one micrometer, while data sets span a cubic millimeter. Examples are given of applications to tensile deformation of copper, grain growth in nickel and titanium, and fatigue cracks in superalloys. Introduction Dislocations, in particular, are well understood as individual The mesoscale is a crucial realm in materials science, espe- defects where an example of a well-established method is cially for polycrystalline materials. Put as succinctly as pos- the calculation of the Peierls stress required to move them sible, a mesoscale property is an attribute of a material that through a lattice. 2 Plastic deformation presents challenges cannot be straightforwardly constructed from properties at the because it generates large dislocation densities on multiple slip atomic scale. -
Forensic Materials Scientist Or “Whodunit” Detective
S-E-A SEAlimited.com FALL 2019 FORENSIC MATERIALS SCIENTIST OR “WHODUNIT” DETECTIVE Being a forensic materials scientist is being a “whodunit” detective, tasked with determining why a product or process allegedly failed and who is responsible. Robert S. Carbonara, Ph.D. Forensic materials science is a broad devices (bolts, etc.), hoses and piping, Why the “so what” question matters technical discipline, that analyzes physical amusement rides, firearms, glassware, To illustrate the importance and practical evidence using the principles of physics and bicycles, CPVC piping, sprinkler systems, application of answering the “so what,” chemistry. Before the advent of modern storage tanks, and numerous others several complex case profiles are presented. engineering materials, most forensic • Material Production and Manufacturing These cases involved: (1) a serious injury materials scientists worked with metals and Processes — Recycling precious metal, where there was responsibility avoidance by were called metallurgists. Today, forensic aluminum and steel furnace operations, the parties involved, (2) a very complex metal materials scientists work with an metal casting operations, metal forging assortment of materials, including plastics, recovery process with a seven-figure loss and rolling production, pipe claim, (3) medical devices that fail and are ceramics, glass, composites, even wood and manufacturing leather and, of course, metals. Despite the complicated by issues of patient or doctor • Construction — Beams and support conduct, and (4) a pipeline failure that oc- broadening of the materials spectrum, the structures, welds, safety device material, same scientific principles that apply to metals curred many years after installation and with lifting cables, chains and straps, hoisting multiple possible technical failure scenarios. -
Analysis of the Microstructure and Microhardness of Rotary Friction Welded Titanium (Ti‐6AL‐V4) Rods
Analysis of the Microstructure and Microhardness of Rotary Friction Welded Titanium (Ti‐6AL‐V4) Rods DM Mukhawanaa, PM Mashininib and DM Madyirac aUniversity of Johannesburg, Department of Mechanical and Industrial Engineering Technology, Doornfontein Campus, Cnr Siemert & Beit Streets, Doornfontein, 2094 bUniversity of Johannesburg, Department of Mechanical and Industrial Engineering Technology, Doornfontein Campus, Cnr Siemert & Beit Streets, Doornfontein, 2094 cUniversity of Johannesburg, Department of Mechanical Engineering Science, Auckland Park Campus, Cnr Kingsway and University Road, Auckland Park, 2092 email address :[email protected], [email protected], [email protected] Abstract This paper presents the evolution of mechanical properties in Ti6Al4V rods welded by rotary friction welding. This is evaluated by monitoring the microstructure and micro hardness changes resulting from the welding. 16 mm diameter Ti6Al4V rods were joined by rotary friction welding utilizing different process parameter settings, namely; axial force, rotational speed and upset distance. The microstructure and micro hardness analysis were observed on each of the weld zones/regions. The micro hardness results revealed higher hardness on the weld zone and low hardness on the heat‐affected zone when compared to the parent material. The higher axial force resulted in higher hardness in the weld zone because of more friction and hence higher heat input which led to refined microstructure. Microstructure characterization for the different weld zones due to varying process parameters is also discussed. Keywords: Rotary friction welding, Ti‐6Al‐4V, Process parameters, Microstructure, Microhardness 1. Introduction Rotary Friction Welding (RFW) is a solid state welding process which uses frictional heat combined with pressure to join two components. -
Microstructure and Mechanical Behaviuor of Rotary Friction Welded Titanium Alloys
World Academy of Science, Engineering and Technology International Journal of Materials and Metallurgical Engineering Vol:1, No:11, 2007 Microstructure and Mechanical Behaviuor of Rotary Friction Welded Titanium Alloys M. Avinash, G. V. K. Chaitanya, Dhananjay Kumar Giri, Sarala Upadhya, and B. K. Muralidhara rotated part by sliding action under predetermined friction Abstract—Ti-6Al-4V alloy has demonstrated a high strength to pressure. The friction pressure is applied for a certain length weight ratio as well as good properties at high temperature. The of time. Then the drive is released and the rotary component is successful application of the alloy in some important areas depends quickly stopped while the axial pressure is being increased to on suitable joining techniques. Friction welding has many a higher predetermined upset pressure, for a predetermined advantageous features to be chosen for joining Titanium alloys. The time. The parts burn off to a few mm after the joint is made. A present work investigates the feasibility of producing similar metal simple set up of a rotary friction welding machine are shown joints of this Titanium alloy by rotary friction welding method. The joints are produced at three different speeds and the performances of in Fig. 1. the welded joints are evaluated by conducting microstructure studies, Friction welding has been successfully carried out by many Vickers Hardness and tensile tests at the joints. It is found that the workers earlier for producing both similar and dissimilar weld joints produced are sound and the ductile fractures in the tensile metal joints [3] - [9]. weld specimens occur at locations away from the welded joints. -
Microstructure, Hardness, and Elastic Modulus of a Multibeam-Sputtered Nanocrystalline Co-Cr-Fe-Ni Compositional Complex Alloy Film
materials Article Microstructure, Hardness, and Elastic Modulus of a Multibeam-Sputtered Nanocrystalline Co-Cr-Fe-Ni Compositional Complex Alloy Film Péter Nagy 1,2, Nadia Rohbeck 2, Zoltán Heged ˝us 3 , Johann Michler 2,László Pethö 2,János L. Lábár 1,4 and Jen˝oGubicza 1,* 1 Department of Materials Physics, Eötvös Loránd University, P.O. Box 32, H-1518 Budapest, Hungary; [email protected] (P.N.); [email protected] (J.L.L.) 2 EMPA Swiss Federal Laboratories for Materials Science and Technology, Laboratory for Mechanics of Materials and Nanostructures, Feuerwerkerstrasse 39, CH-3602 Thun, Switzerland; [email protected] (N.R.); [email protected] (J.M.); [email protected] (L.P.) 3 Deutsche Elektronen-Synchrotron DESY, Notkestr. 85, 22603 Hamburg, Germany; [email protected] 4 Institute for Technical Physics and Materials Science, Centre for Energy Research, Konkoly Thege Miklós út 29-33, H-1121 Budapest, Hungary * Correspondence: [email protected]; Tel.: + 36-1-372-2876; Fax: +36-1-372-2811 Abstract: A nanocrystalline Co-Cr-Ni-Fe compositional complex alloy (CCA) film with a thickness of about 1 micron was produced by a multiple-beam-sputtering physical vapor deposition (PVD) technique. The main advantage of this novel method is that it does not require alloy targets, but rather uses commercially pure metal sources. Another benefit of the application of this technique is that it produces compositional gradient samples on a disk surface with a wide range of elemental Citation: Nagy, P.; Rohbeck, N.; concentrations, enabling combinatorial analysis of CCA films. In this study, the variation of the Heged˝us,Z.; Michler, J.; Pethö, L.; phase composition, the microstructure (crystallite size and defect density), and the mechanical Lábár, J.L.; Gubicza, J. -
Effect of Heterogeneous Microstructure on Refining Austenite Grain Size in Low Alloy Heavy-Gage Plate
metals Article Effect of Heterogeneous Microstructure on Refining Austenite Grain Size in Low Alloy Heavy-Gage Plate Shengfu Yuan 1, Zhenjia Xie 2 , Jingliang Wang 2, Longhao Zhu 3, Ling Yan 3, Chengjia Shang 2,3,* and R. D. K. Misra 4 1 School of Materials Science and Engineering, University of Science and Technology Beijing, Beijing 100083, China; [email protected] 2 Colarborative Innovation Center of Steel Technology, University of Science and Technology Beijing, Beijing 100083, China; [email protected] (Z.X.); [email protected] (J.W.) 3 State Key Laboratory of Steel for Marina Equipment and Application, Anshan Steel, Anshan 114021, China; [email protected] (L.Z.); [email protected] (L.Y.) 4 Laboratory for Excellence in Advanced Steel Research, Department of Metallurgical and Materials Engineering, University of Texas at El Paso, El Paso, TX 79912, USA; [email protected] * Correspondence: [email protected]; Fax: +8610-6233-2428 Received: 18 November 2019; Accepted: 13 January 2020; Published: 16 January 2020 Abstract: The present work introduces the role of heterogeneous microstructure in enhancing the nucleation density of reversed austenite. It was found that the novel pre-annealing produced a heterogeneous microstructure consisting of alloying elements-enriched martensite and alloying-depleted intercritical ferrite. The shape of the martensite at the prior austenite grain boundary was equiaxed and acicular at inter-laths. The equiaxed reversed austenite had a K-S orientation with adjacent prior austenite grain, and effectively refined the prior austenite grain that it grew into. The alloying elements-enriched martensite provided additional nucleation sites to form equiaxed reversed austenite at both prior austenite grain boundaries and intragranular inter-lath boundaries during re-austenitization.