Pouryanoury Nr1.Ps
Total Page:16
File Type:pdf, Size:1020Kb
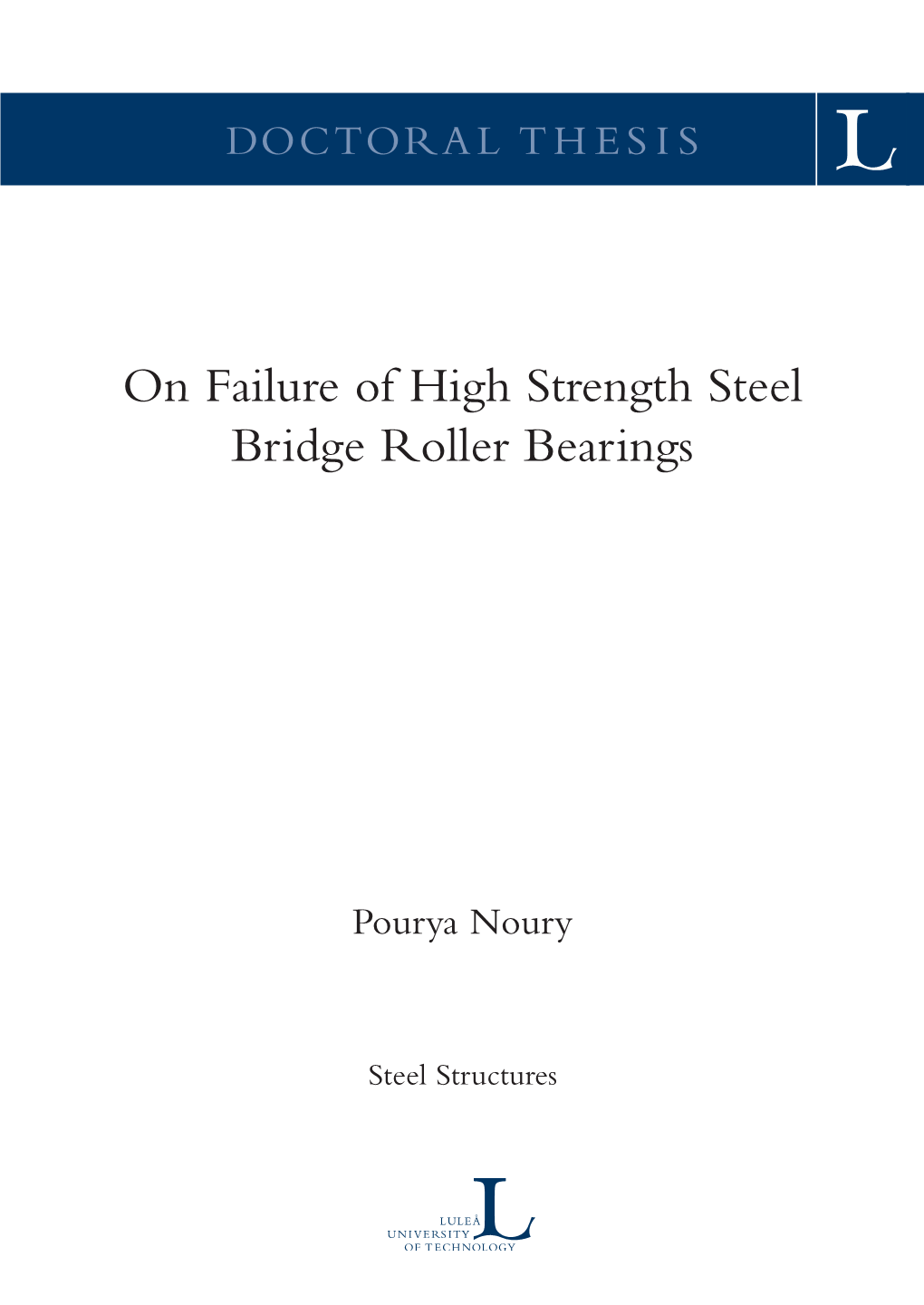
Load more
Recommended publications
-
Road Investment Strategy 2: 2020-2025
Road Investment Strategy 2: 2020–2025 March 2020 CORRECTION SLIP Title: Road Investment Strategy 2: 2020-25 Session: 2019-21 ISBN: 978-1-5286-1678-2 Date of laying: 11th March 2020 Correction: Removing duplicate text on the M62 Junctions 20-25 smart motorway Text currently reads: (Page 95) M62 Junctions 20-25 – upgrading the M62 to smart motorway between junction 20 (Rochdale) and junction 25 (Brighouse) across the Pennines. Together with other smart motorways in Lancashire and Yorkshire, this will provide a full smart motorway link between Manchester and Leeds, and between the M1 and the M6. This text should be removed, but the identical text on page 96 remains. Correction: Correcting a heading in the eastern region Heading currently reads: Under Construction Heading should read: Smart motorways subject to stocktake Date of correction: 11th March 2020 Road Investment Strategy 2: 2020 – 2025 Presented to Parliament pursuant to section 3 of the Infrastructure Act 2015 © Crown copyright 2020 This publication is licensed under the terms of the Open Government Licence v3.0 except where otherwise stated. To view this licence, visit nationalarchives.gov.uk/doc/ open-government-licence/version/3. Where we have identified any third party copyright information you will need to obtain permission from the copyright holders concerned. This publication is available at https://www.gov.uk/government/publications. Any enquiries regarding this publication should be sent to us at https://forms.dft.gov.uk/contact-dft-and-agencies/ ISBN 978-1-5286-1678-2 CCS0919077812 Printed on paper containing 75% recycled fibre content minimum. Printed in the UK by the APS Group on behalf of the Controller of Her Majesty’s Stationery Office. -
Dear Mr Carter, Freedom of Information Act Request: Planning Applications for Shale Or Coal Bed Methane Or Borehole Explorations
Professor Steven Broomhead Chief Executive Mr Carter – By Email Garry Legg Planning Policy & Programme Manager Environment and Regeneration Directorate New Town House Buttermarket Street Warrington WA1 2NH Our ref: 13 /1 4-276 th 6 January 201 4 Dear Mr Carter, Freedom of Information Act Request: Planning Applications for Shale or Coal Bed Methane or Borehole Explorations I am writing in response to your email of 16th December 2014 requesting information about planning applications submitted since 2007 for shale or coal bed methane or borehole explorations. In response to your enquiry I can advise that the following such planning applications were received by Warrington Borough Council for activities related to the extraction of unconventional gasses: • Doe Green, Farnworth Road, Penketh – Approved coal bed methane extraction development (planning application references. 99/40507 and 2010/16949) • Land at Woolston adjacent to the Thelwall Viaduct. Planning permission was granted for exploratory bore holes in 2010 (planning application reference. 2009/15700) • Land off Waterworks Lane, Winwick – Planning approval (2011/19226) granted for the 'Proposed drilling of exploratory borehole; erection of containerised units and associated plant and equipment; extraction of mine gas to generate electricity; sub-station; lighting post; fencing; gates and ancillary plant'. You can access further information on these applications by using the unique planning application reference number provided to search using the following web link: http://planning.warrington.gov.uk/swiftlg/apas/run/wphappcriteria.display ? If you experience any trouble doing so you can seek assistance from the Council’s Development Management Support Team who can be contacted on 01925 442819 or via email at [email protected] If you are not satisfied with my response to your request for information, you may ask the Council for an internal review of this decision. -
Mersey Book 2 1/10/07 5:10 Pm Page 138 Mersey Book 2 1/10/07 5:10 Pm Page 139
mersey book 2 1/10/07 5:10 pm Page 138 mersey book 2 1/10/07 5:10 pm Page 139 Opposite The old Macclesfield to Buxton turnpike road near Derbyshire Bridge. ALONG THE BANKS Photograph Colin McPherson DAVID WARD n my end is my beginning. New Brighton is where the Mersey stops Sainsbury’s in Stockport. I used to do my shopping here but had no idea and the sea starts and the firm wide sands that wrap round this top that the Mersey begins nearby and I was only dimly aware that a shopping right-hand corner of the Wirral demand to be walked upon on a centre called Merseyway must have something to do with the river. I breezy, sun-filled day of late summer. So today I go in search of its source. Along Great Egerton Street, People amble, dogs run, oystercatchers dig. A black cat tip-toeing packed with cars looking for somewhere to park, and then left over a round the royal crest high on the sandstone walls of Fort Perch Rock eyes bridge, and left again to a kind of promontory marked by tired decorative me snootily as I clamber down towards the breakwater that I have iron work bearing a message whose meaning is clear despite the missing unilaterally decided marks the boundary between fresh and salt water letters: ‘Here ri ers Goyt & Tame becom Mersey flowing clear from lapping at my feet. Stockport to the sea.’ In cities, we usually look down on rivers from an embankment, a This is the confluence that makes the Mersey. -
Broomedge Farm Cottages, Broomedge Farm, Burford Lane, Lymm WA13 0SE Tel: 01925-752830 Website: Email: [email protected]
LOCATION AND DIRECTIONS Where we are Broomedge Farm Cottages are located between Lymm and Altrincham, to the west of Manchester. Distances to some key locations are below: • Lymm – 3 miles • Altrincham – 5 miles • Manchester Airport – 9 miles • Liverpool Airport – 26 miles • Lowry Centre, Salford – 17 miles • Trafford Centre, Manchester – 10 miles • Liverpool centre – 25 miles • Manchester centre – 16 miles Directions to Broomedge Farm Cottages Broomedge Farm Cottages are easily reached from the motorway. ! From the M6 motorway southbound (including from Liverpool John Lennon Airport) 1) After crossing the Thelwall Viaduct over the Manchester Ship Canal, leave the motorway at J20. This junction has 2 exits, and you need to leave at the first exit, signposted ‘A50, B5158 Lymm & Services’ 2) Take the A50 southbound (signposted ‘Knutsford’) [CHECK]. 3) Stay on the A50 for around 2! miles (4.0km). Once you reach High Legh village, take a left turn into West Lane, signposted Partington and Carrington. 4) Stay on West Lane for around 1! miles (2.4km), until you enter Broomedge village. 5) You will come to a crossroads under the control traffic lights. Go straight over this crossroads, obeying the light signals. Immediately after the crossroads, look for the sign for Broomedge Farm Cottages on your right-hand side (approx. 50 yds). 6) Turn into the driveway. The cottages are on your left-hand side after around 200 yards (200m). Broomedge Farm Cottages, Broomedge Farm, Burford Lane, Lymm WA13 0SE Tel: 01925-752830 Website: www.broomedgefarm.co.uk Email: [email protected] 2 / 3 ! From the M6 motorway northbound 1) Leave the motorway at J20. -
Cheshire Neighbourhood Watch Association Week Ending 6Th December 2020 Cheshire News & Appeals
Cheshire Neighbourhood Watch Association Week ending 6th December 2020 Cheshire News & Appeals Latest Cheshire News Commissioner praises Chief Constable as Cheshire’s top cop announces retirement Cheshire Constabulary Chief Constable Darren Martland has announced his intention to retire in the Spring of next year. PCC David Keane praises his dedication to policing in Cheshire and for more than three decades of service as a police officer. Darren started his policing career in 1990, having graduated from Sheffield University. The initial part of his career was spent in the Knowsley area where he completed a number of uniform and CID postings. In 1999 he joined Cheshire Constabulary where he worked in a number of areas, in mainly uniform operational roles in Halton and Macclesfield. He was later posted to the Eastern Area as the uniformed Chief Inspector. Following his spell in Cheshire, he has served in senior roles at both Merseyside and Cumbria. He successfully completed the Strategic Command Course in 2013 before finally returning to Cheshire in the start of 2017. CC Darren Martland said: “It has been an honour and privilege to serve the public, as a police officer, for more than 30 years, and I have made the very difficult decision to retire from policing in order to enable me to spend more time with my family and pursue other personal interests. I am immensely proud to have led such a wonderful organisation, and I have no doubt that, given the professionalism, care and commitment demonstrated by our staff and volunteers, Cheshire Constabulary will meet the current and future policing challenges, and will continue to ‘Make Cheshire Safer’.” Praising Darren for his work both as Chief Constable and across his policing career David Keane said: “I want to thank Darren personally for more than 30 years of service to the public as a police officer, and in particular for his commitment to making Cheshire safer during his tenure as our Chief Constable. -
Bridgewater Canal- Little Bollington to Keckwick
Bridgewater Canal- Little Bollington to Keckwick Hill Bridge Easy Trail: Please be aware that the grading of this trail was set according to normal water levels and conditions. Weather and water level/conditions can change the nature of trail within a short space of time so please ensure you check both of these before heading out. Route Distance: 11 miles Lymm Bridge Summary Approximate Time: 3-5 hours The time has been estimated based on you travelling 3 – Canoe through 5mph (a leisurely pace using a recreational type of boat). rural Cheshire Type of Trail: One Way along the first Waterways Travelled: Bridgewater Canal canal in England to Type of Water: Urban and Rural Canal be built under an Portages and Locks: None Act of Parliament. Nearest Town: Lymm, Cheshire The original Act Start: Ye Old No 3 Public House, Lymm Road, Little was dated 1759 but this section that joins the Trent and Mersey Bollington, Altrincham, Cheshire WA14 4TA Canal at Preston Brook was not completed until 1776. Finish: Keckwick Hill Bridge, Delph Lane, Daresbury, WA4 4AN map ref 572826. It is the small towns and villages bordering the canal where much of its beauty lies with Lymm and Grappenhall being particularly O.S. Sheets: OS Landranger Map 109 Manchester, and 108 Liverpool and surrounding attractive. After skirting the Stockton Heath area of Warrington areas. one heads off again into rural Cheshire, past the villages of Lower Licence Information: A licence is required to and Higher Walton a pretty late-Victorian estate and beyond paddle this waterway. See full details in Useful Moore where it passes the Daresbury Atomic energy tower. -
Plans for Lymm Fire Station and Safety Centre
Plans for Lymm Fire Station and Safety Centre: Public Consultation 14/7/14 Page 1 of 12 Summary Cheshire Fire and Rescue Service intends to submit planning permission in 2014 to build a new integrated fire station and safety centre on land off Cliff Lane, Lymm. The Service was keen to gauge public opinion about the plans in advance of the formal submission. To do this the Service organised a public exhibition in the area at Lymm Village Hall and invited people to comment about the plans online via the Service’s website. Key findings were: • 26 of 32 respondents supported the Service’s plans to build a fire station and safety centre in Lymm. • 26 respondents liked the proposed design of the fire station and safety centre. • 27 respondents supported the Service’s plans to target the safety centre towards school groups, new parents and carers. • 28 respondents supported the type of activities and programmes that the Service plans to undertake at the safety centre. • Main concerns raised relate to access and traffic concerns onto the A50 and concerns over the Green Belt status of the proposed site. Background In 2012-13 Cheshire Fire and Rescue Service (CFRS) carried out a detailed review into how its frontline emergency response services could be best provided in the future. The aim was to ensure the Service could continue to protect and improve the safety of local communities while taking into account risk and activity levels and the major cuts in its funding. Following a major public consultation programme, a wide-ranging Emergency Response Programme was agreed in principle which involves building some new fire stations, keeping the same number of fire engines, but making significant changes in how they are staffed. -
Flying in the Manchester Ctr
NATS Manchester has provided these plain text briefs for the assistance of pilots operating within and in the vicinity of the Manchester Control Zone. They have been provided for guidance purposes only. The authors have produced these purely for the assistance of other pilots in a voluntary capacity and cannot guarantee or give assurance as to their accuracy, reliability or omissions therein. The CAA, who will not be responsible for their adequacy, accuracy or for any omissions therein, has not validated their content. It is the responsibility of the pilot in command to carry out comprehensive pre-flight planning based on current data from an approved source including NOTAMS. FLYING IN THE MANCHESTER CTR So you’re planning to fly into Manchester International or Woodford and have started to think about planning the trip. The chances are that you’ll look at your 1:500,000 chart and flight guide and think, ‘this is going to be complex and probably beyond me’. Well, it isn’t if you remember what I’m sure your CFI told you. Remember the bit about good pre-planning? Well, that’s the answer here. Certainly Manchester is going to be much bigger and more complex airspace than the one you learned in but all the information you need to do a professional job is available at your fingertips. First stop can be the www.ais.org.uk website and a print-off of the pages relevant to Manchester from the AIP. I’m primarily concerned with the navigation element here so I’m not going to go into all the details here but you must … 1. -
Grappenhall +Thelwall Parish Walks
Mid-Cheshire Footpath Society (MCFS) Contents Page Walks in and around 1. Notes and general information (please read this section) 3 1. Maps 2. Safety Grappenhall & Thelwall Parish 3. Parking 4. Notes 5. Abbreviations 4 6. List of Grappenhall and Thelwall PRoWs 5 This booklet offers a selection of circular walks that residents and visitors can enjoy by 2. Grappenhall and Thelwall Civil Parish 6 walking from the parish. The walks are of various lengths and difficulty, albeit none are Local information 7 difficult. Some can be walked in stout shoes but others, particularly if it has rained, may Car parking 9 be easier in walking boots. Other publications and acknowledgements 9 3. Walks from the Walled Garden (P1) Enjoy the 50 miles of walks in this booklet. 1. Grappenhall Church 1.8 miles 11 2. Grappenhall Wood 2.9 13 3. Cliff Lane and the Bridgewater Canal 4.2 15 4. Lumb Brook Valley 5.5 17 5. Appleton Thorn via Canal Side 5.7 21 6. Pewterspear 7.9 23 4. Walks from Weaste Lane (P2) 7. Latchford Locks via the Penny Ferry 3.5 miles 27 8. Thelwall and the Penny Ferry 5.2 29 9. Lymm Sow Brook and the Penny Ferry 6.3 31 10. Lymm and The Bongs 8.5 35 5. Update information (Please read before walking) 38 Copyright All the maps included within this document use Open StreetMap as the base mapping and non- copyright material for the overlays. The overlays are © Peter Waite (The author). © Open StreetMap contributors. The data is available under the Open Database Licence which can be seen at www.openstreetmap.org/copyright. -
The London Gazette &Utf)Oriti>
Number 52460 3125 The London Gazette &utf)oriti> Registered as a Newspaper at The Post Office WEDNESDAY, 27TH FEBRUARY 1991 State Intelligence TREASURY SOLICITOR DEPARTMENT OF TRANSPORT Notice of Disclaimer Under s.656 of the Companies Act 1985 HIGHWAYS ACT 1980 THE SOLICITOR FOR THE AFFAIRS OF HER MAJESTY'S THE M6 MOTORWAY: WIDENING BETWEEN TREASURY in whom the assets of BENTLEY (PLYMOUTH) JUNCTIONS 20 AND 21A (THELWALL VIADUCT) AND LTD (No. 783973) vested pursuant to section 654 of the CONNECTING ROADS SCHEME 1990 Companies Act 198S on its dissolution under section 652 of the THE M6 MOTORWAY: WIDENING BETWEEN said Act on 27th October 1987 in pursuance of the power JUNCTIONS 20 AND 21A (THELWALL VIADUCT) granted by section 656 of the said Act HEREBY DISCLAIMS AND CONNECTING ROADS SCHEME (SIDE ROADS) the Crown's title (if any) in 73 Union Street, The Octagon, ORDER 1990 Plymouth, Devon (title number DN 30657). The vesting of the same having come to his notice on 14th December 1990. AND S. L. Sargant, Assistant Treasury Solicitor THE M6 MOTORWAY: WIDENING BETWEEN 15th February 1991. (7 SI) JUNCTIONS 20 AND 21A (THELWALL VIADUCT) AND CONNECTING ROADS SCHEME (SIDE ROADS) (NO 2) ORDER 1990 The Secretary of State for Transport hereby gives notice that he has made the following Scheme and Orders: 1. A Scheme under sections 16, 17, 19, 106 and 108 of the Highways Act 1980 authorising him: (a) to provide for the exclusive use of traffic of Classes I and II of the classes of traffic set out in Schedule 4 to the Highways Act 1980 DEPARTMENT OF THE -
Trafficmaster Congestion Study
Trafficmaster/ RAC Foundation Journey Time Index Summer 2008 In partnership with Contents Foreword PAGE 01 Summer sunshine, blue skies and balmy nights draw us out of our homes to visit attractions, attend Foreword by Tony Eales, Chief Executive, events, festivals or go on holiday, but all this activity has unforeseen consequences for the nation’s Trafficmaster Plc and Stephen Glaister, road network. Director, RAC Foundation This report assesses the impact summer sporting highlights. These include The Congestion remains a frustrating reality for PAGE 02 events have on our journeys, and which Glastonbury Festival, the Silverstone many motorists – hardly surprising when Report Highlights events have the worst effect on UK roads. Formula 1 Grand Prix, Cowes Week and the you consider that nearly 34 million We also provide an analysis of how road Epsom Derby. Unfortunately these produce UK-registered vehicles, 1.7 million foreign traffic speeds change on key holiday routes, heavy localised traffic on roads that are not heavy goods vehicles, and thousands of PAGE 03 when additional motorists take to the roads often suitable for high volumes. Theme other visiting vehicles are fighting for space Introduction at certain times of the day. parks and other places of local interest will on just 245,000 miles of roads. While the also entice crowds, causing bottlenecks and volume of traffic is a key factor in causing Principally this report analyses the change Index Methodology jams around these local honey-pots. congestion on Britain’s roads, driver in journey times across some of the UK’s behaviour, road works, incidents and major routes as well as providing information This report highlights the events that weather also play their part. -
Reshaping for Growth
_ AMEC plc 65 Carter Lane London EC4V 5HF United Kingdom Tel: +44 (0)20 7634 0000 Fax: +44 (0)20 7634 0001 www.amec.com AMEC plc annual report and accounts 2005 AMEC plc annual report and Contents accounts Financial highlights 1 Chairman’s statement 2 Reshaping for growth 4 A leader in project management Oil and Gas 6 2005 and services, we design, deliver Engineering and Technical Services 12 and support infrastructure – from local Project Solutions 18 Sustainability 24 technical services to international Our board of directors 28 landmark projects Chief executive’s review 30 Business and financial review 34 Report of the directors 56 Directors’ remuneration report 61 Across the world Consolidated income statement 67 Consolidated statement of recognised income Responsibly and expense 68 Consolidated balance sheet 69 For the long term Consolidated cash flow Reshaping statement 70 Notes to the consolidated accounts 71 for growth Company balance sheet 104 45,000 people Notes to the company balance sheet 105 700 locations Statement of directors’ responsibilities 112 Independent auditors’ report 40 countries to the members of AMEC plc 113 Principal group companies 114 Five year record 116 Shareholder information 117 Investor relations report 118 AMEC in 2005/6 119 _ AMEC plc 65 Carter Lane London EC4V 5HF United Kingdom Tel: +44 (0)20 7634 0000 Fax: +44 (0)20 7634 0001 www.amec.com AMEC plc annual report and accounts 2005 AMEC plc annual report and Contents accounts Financial highlights 1 Chairman’s statement 2 Reshaping for growth 4 A leader