Steam-Engine." New York, J
Total Page:16
File Type:pdf, Size:1020Kb
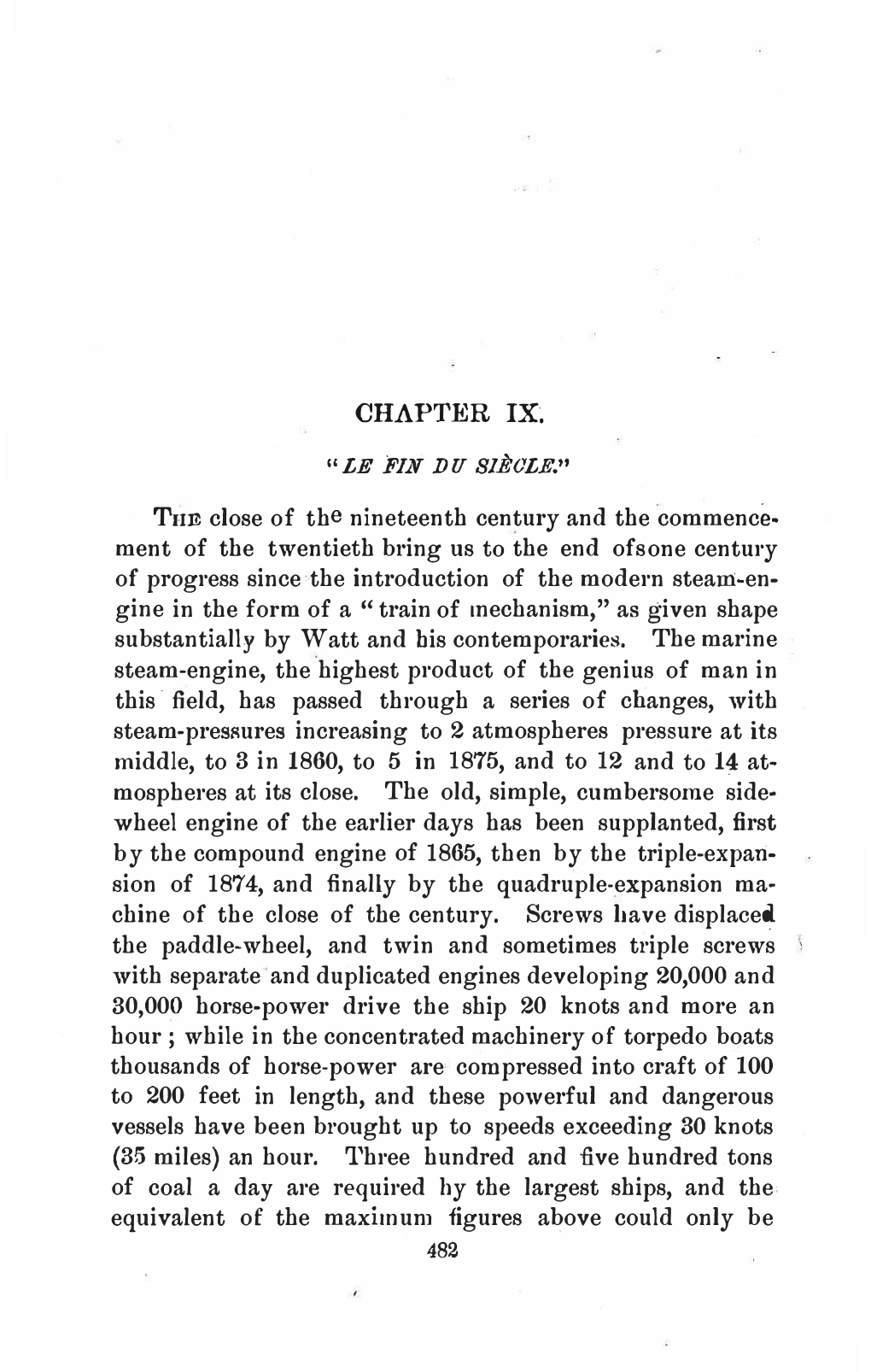
Load more
Recommended publications
-
THESIS WASTE HEAT RECOVERY from a HIGH TEMPERATURE DIESEL ENGINE Submitted by Jonas E. Adler Department of Mechanical Engineerin
THESIS WASTE HEAT RECOVERY FROM A HIGH TEMPERATURE DIESEL ENGINE Submitted by Jonas E. Adler Department of Mechanical Engineering In partial fulfillment of the requirements For the Degree of Master of Science Colorado State University Fort Collins, Colorado Fall 2017 Master’s Committee: Advisor: Todd M. Bandhauer Daniel B. Olsen Sybil E. Sharvelle Copyright by Jonas E. Adler 2017 All Rights Reserved ABSTRACT WASTE HEAT RECOVERY FROM A HIGH TEMPERATURE DIESEL ENGINE Government-mandated improvements in fuel economy and emissions from internal combustion engines (ICEs) are driving innovation in engine efficiency. Though incremental efficiency gains have been achieved, most combustion engines are still only 30-40% efficient at best, with most of the remaining fuel energy being rejected to the environment as waste heat through engine coolant and exhaust gases. Attempts have been made to harness this waste heat and use it to drive a Rankine cycle and produce additional work to improve efficiency. Research on waste heat recovery (WHR) demonstrates that it is possible to improve overall efficiency by converting wasted heat into usable work, but relative gains in overall efficiency are typically minimal (~5-8%) and often do not justify the cost and space requirements of a WHR system. The primary limitation of the current state-of-the-art in WHR is the low temperature of the engine coolant (~90°C), which minimizes the WHR from a heat source that represents between 20% and 30% of the fuel energy. The current research proposes increasing the engine coolant temperature to improve the utilization of coolant waste heat as one possible path to achieving greater WHR system effectiveness. -
WSA Engineering Branch Training 3
59 RECIPROCATING STEAM ENGINES Reciprocating type main engines have been used to propel This is accomplished by the guide and slipper shown in the ships, since Robert Fulton first installed one in the Clermont in drawing. 1810. The Clermont's engine was a small single cylinder affair which turned paddle wheels on the side of the ship. The boiler was only able to supply steam to the engine at a few pounds pressure. Since that time the reciprocating engine has been gradually developed into a much larger and more powerful engine of several cylinders, some having been built as large as 12,000 horsepower. Turbine type main engines being much smaller and more powerful were rapidly replacing reciprocating engines, when the present emergency made it necessary to return to the installation of reciprocating engines in a large portion of the new ships due to the great demand for turbines. It is one of the most durable and reliable type engines, providing it has proper care and lubrication. Its principle of operation consists essentially of a cylinder in which a close fitting piston is pushed back and forth or up and down according to the position of the cylinder. If steam is admitted to the top of the cylinder, it will expand and push the piston ahead of it to the bottom. Then if steam is admitted to the bottom of the cylinder it will push the piston back up. This continual back and forth movement of the piston is called reciprocating motion, hence the name, reciprocating engine. To turn the propeller the motion must be changed to a rotary one. -
Steam Consumption of Pumping Machinery
Steam Consumption of Pumping Machinery HENRY EZRA KEENEY THESIS FOR THE DEGREE OF BACHELOR OF SCIENCE IN MECHANICAL ENGINEERING IN THE COLLEGE OF ENGINEERING OF THE UNIVERSITY OF ILLINOIS PRESENTED JUNE, 19Q0 THIS IS TO CERTIFY THAT THE THESIS PREPARED UNDER MY SUPERVISION BY ____________ ______ Henry.Ezra.Keeney........_... entitled..s.ta.ara.C.an8mp.i.io.n.....Q.£ ...Bumping.. Machinery. IS APPROVED BY ME AS FULFILLING THIS PART OF THE REQUIREMENTS FOR THE DEGREE o f ....Bachelor.of.Science.in.Mechanical...Engineering.* h e a d o f d e p a r t m e n t o f ........Mechanical.Engineering, ' INTRODUCTION. Those who have not considered the subject of water distribu tion* may not believe that pumping machinery stands at the head of the various branches of Engineering. As to the truth of this state ment, we 'nave only to consider that coal could not be obtained with out the pumping engine; our water supply for boilers and our city water supply would be difficult of management if it were not for the pump. ”’ater is found in every mine, to a greater or less extent, and the first applications of steam were for pumping the water out of these mines. HISTORY AND DEVELOPMENT. Many forms of puraps were used for obtaining water, but not until the 17th century was steara used for pumping water. So man ifest was the economy of steam pumps over those driven by horses, (which were previously used to a great extent) even at the begin ning, that they were introduced as rapidly as they could be fur nished with the limited supply of tools at the command of the en gine and boiler builders of that day. -
For Steam Turbine
ISO 9001 www.dh.co.kr www. dh.co.kr Certificate Number 32533 We wish to communicate with our customers. OHSAS 18001 If you would like any further information about DongHwa Entec, Certificate Number C 0082 please visit our website (www.dh.co.kr). Gland Condenser DongHwa Entec cares for your concerns. ▶▶Engineering technology for the future Oil Cooler - HEAT EXCHANGER TO COOL THE LUBRICANT OIL FOR ROTATING MACHINERY Heat Exchanger Solution Partner for Steam Turbine Our company endeavor ceaselessly to develop new products and quality improvement Deaerator Deaerator is defined as a mechanical device for removal of dissolved gases, especially oxygen and carbon dioxide from water. And deaerator heat the feed water and maintain regular N.P.S.H of feed water pump. Spray & tray type is utilized for land-use deaerator, and stray • MAIN(SURFACE) CONDENSER & scrubber type is utilized for marine-use deaerator. • EJECTOR CONDENSER • GLAND CONDENSER WITH EJECTOR Donghwa Entec developed major part like spray valve, tray, Head Office and Factory and scrubber and still research for more high efficiency of 7, Noksansandan 261-ro, Gangseo-gu, Busan, Korea • GLAND CONDENSER WITH EXHAUST FAN deaerator. TEL : +82-51-970-1000 FAX : +82-51-970-1001 • OIL COOLER Donghwa Entec has ability of thermal design, strength Hwajeon Office and Factory • DEAERATOR calculation, purchase material, and manufacturing. 20, Hwajeonsandan 1-ro 63beon-gil, Gangseo-gu, Busan, Korea • H.P / L.P HEATER TEL : +82-51-970-1100 FAX : +82-51-970-0710 R&D Center 7, Gwahaksandan-ro 305beon-gil, Gangseo-gu, Busan, Korea H.P / L.P Feed Water Heater TEL : +82-51-970-0711 FAX : +82-51-970-0730 DongHwa Entec (Shanghai) Co., Ltd. -
ENGINES: an Engine Failure Is Always Bad News. Besides Taking Away
ENGINES: An engine failure is always bad news. Besides taking away your wheels, it forces you to make a painful financial decision. If the cost to repair, overhaul or replace the engine is more than the resale value of your car or truck, the investment may not be worth it. But if your vehicle is in good condition otherwise, repairing or replacing the engine may be less expense than trading for another used vehicle (always a gamble), or taking on payments for a new car or truck. Assuming you have gotten past the initial trauma and has decided in favor of fixing the engine, you have to figure out why the engine failed so the repaired engine (or replacement engine) won't suffer the same fate. A good place to start your postmortem is to review the circumstances that preceded the failure. Sometimes failures occur unexpectedly. One minute the engine is running fine and you're keeping up with traffic, and the next you're sitting along side the road with the hood up wondering what happened. In most instances, though, there is ample warning that something is amiss long before the engine actually fails. Unusual engine noises, low oil pressure, engine overheating, loss of power, misfiring, hard starting and similar drivability and performance complaints can all be indications of problems that need attention. The underlying cause may be something minor or major. There is no way to know unless somebody checks it out. If a motorist ignores such warnings long enough, it can be a very costly mistake because eventually the engine may succumb to whatever is causing the problem, which is a classic example of the famous preventive maintenance line, "You can pay me now or you can pay me later." ENGINE OVERHEATING Overheating can be caused by any number of things. -
Steam Power Plant Cycle Rankine Cycle
Cycle A cycle is a series of two or more processes in which the final state is the same as the initial state. Steam Power Cycle : A power generating cycle that uses steam or water vapor as the working substance. This cycle differ with an internal combustion engine cycle because the combustion occurs in the boiler, unlike that of an IC engine that combustion occurs inside the working cylinders. Steam Power Plant Cycle Rankine Cycle Components: a. Steam Turbine b. Condenser c. Pump d. Steam Generator or boiler Processes: 1 to 2 – Isentropic Expansion (S = C) 2 to 3 – constant pressure Heat Rejection (P = C) 3 to 4 – Isentropic pumping (S = C) 4 to 1 – Constant pressure Heat Addition (P = C) ms 1 kg 1 Steam Turbine Boiler or St ea m Ge ne r at or Wt 2 QA Co nd e ns er Feedwater Q R Pu mp 3 W P T 1 P1 4' 4 P2 = P 3 3 2 2' S 40 A. Turbine Work (W t) (considering S = C; Q = 0; ∆KE = 0; ∆PE = 0) Wt = m s(h 1 – h2) KW Where: ms – steam flow rate, kg/sec h – enthalpy, KJ/kg Wt – turbine power, KW B. Heat Rejected in the Condenser (Q R) QR = m(h 2 – h3) KW C. Pump Work (W P) WP = m(h 4 – h3) D. Heat added to Boiler (Q A) QA = m(h 1 – h4) KW E. Thermal efficiency Net Work e x 100% = Heat Added W e x 100% = Q A F. Net Work W = W t - Wp G. -
Steam Engines of Which We Have Any Knowledge Were
A T H OROUGH AND PR ACT I CAL PR ESENT AT I ON OF MODER N ST EAM ENGI NE PR ACT I CE LLEWELLY DY N . I U M . E . V i P O F S S O O F X P M L G G P U DU U V S Y R E R E ERI ENTA EN INEERIN , R E NI ER IT AM ERICAN S O CIETY O F M ECH ANI C A L EN G INEERS I LL US T RA T ED AM ER ICA N T ECH N ICA L SOCIET Y C H ICAGO 19 17 CO PY GH 19 12 19 17 B Y RI T , , , AM ER ICA N T ECH N ICAL SOCIET Y CO PY RIG H TE D IN G REAT B RITAI N A L L RIGH TS RE S ERV E D 4 8 1 8 9 6 "GI. A INT RO DUCT IO N n m n ne w e e b e the ma es o ss H E moder stea e gi , h th r it j tic C rli , which so silently o pe rates the m assive e le ctric generators in f r mun a owe an s o r the an o o mo e w one o ou icip l p r pl t , gi t l c tiv hich t m es an o u omman s our uns n e pulls the Limited a sixty il h r , c d ti t d n And t e e m o emen is so f ee and e fe in admiratio . -
Icone20-Power2012-55076
Proceedings of the 2012 20th International Conference on Nuclear Engineering collocated with the ASME 2012 Power Conference ICONE20-POWER2012 July 30 - August 3, 2012, Anaheim, California, USA ICONE20-POWER2012-55076 DESIGN AND CONTROL OF BYPASS CONDENSERS Michael Phipps, P.E. Ranga Nadig, Ph. D. Maarky Thermal Systems Maarky Thermal Systems Cherry Hill, New Jersey, USA Cherry Hill, New Jersey, USA ABSTRACT INTRODUCTION In waste to energy plants and certain genre of Waste to energy plants generate their revenues cogeneration plants, it is mandatory to condense the from the burning of waste and production of electricity. steam from the boiler or HRSG in a separate bypass Waste is incinerated on a continuous basis and heat from condenser when the steam turbine is out of service. The incineration converts water to steam in a boiler. The high steam from the boiler or HRSG is attemperated in a pressure steam from the boiler flows through a steam pressure reducing desuperheating valve and then turbine generator producing electricity. The low pressure condensed in a bypass condenser. To avoid flashing of steam emerging from the steam turbine is condensed in a condensate in downstream piping it is customary to steam surface condenser. Continuous incineration subcool the condensate in the bypass condenser. mandates that the steam from the boiler must be Circulating water from the steam surface condenser is condensed whether the steam turbine is operational or used to condense the steam in the bypass condenser. not. When the steam turbine is not in service, the steam from the boiler is condensed in a bypass condenser. -
Circular Surface Condenser
CIRCULAR SURFACE CONDENSER OVERVIEW FEATURES THERMAL ENGINEERING INTERNATIONAL (USA) INC. (TEi), a Babcock ■ Axial steam inlet / top steam inlet ® Power Inc. company, is a leading supplier of heat transfer technology products. Backed ■ Single pass / two pass by more than 165 years of experience, we offer fully integrated design, engineering, ■ Divided waterbox / non-divided waterbox manufacturing, construction and technical services for all power, oil and gas, chemical ■ Optimized tube layout geometrics and petrochemical industry applications. ■ Superior surface area design to promote TEi’s Circular Surface Condensers, manufactured using design methodologies perfected maximum heat transfer efficiency by decades of experience, provide customers with a proven optimal and economic ■ Optimal bundle arrangement to promote design that offers protection against destructive tube vibration eliminating the low steam velocities possibility of failure. ■ Protection against destructive tube vibration The TEi brand is globally recognized for its technical superiority when it comes to ■ Minimizing troubleshooting during operation performance. The TEi team understands that failures to these systems are costly and that reliability and efficiency are of utmost importance. TEi creates customized BENEFITS condensers designed to meet the plant layout requirement and space availability, and can ■ Reliable also enhance performance by design optimization. ■ Less down time The key features of Circular Surface Condensers include an optimized compact tube ■ Best -
Troubleshooting Surface Condenser Venting Systems
Troubleshooting Surface Condenser Venting Systems J.R. LINES, R.E. ATHEY AND L.L. FRENS GRAHAM MANUFACTURING COMPANY ABSTRACT tem related problems designed into the system, or caused by a venting system malfunction. Steam condenser venting equipment In an ideal situation, the condensing pressure achievable in a steam is sometimes misdesigned, improperly installed, or required to surface condenser is determined by the exiting cooling water tem- operate beyond its capabilities. The recent trend to part load perature. However the failure of the venting system to properly operation has accentuated the problem. remove noncondensible gases from the steam condenser will result in elevated condenser pressures. Information is presented in this If the venting system is unable to remove the noncondensible paper relative to the most common venting systems available, as gases at the pressure which is achievable by the condenser the well as providing procedures for troubleshooting each type of sys- condenser back pressure will rise. In this case the condenser does tem. A description is given of the various operating characteristics, not control the back pressure. Rather the venting system is the along with narrative discussions of field problems and experiences. controlling factor. It is worth noting that any time the back pres- Simple visual, audible and physical guides to the analysis of vent- sure is higher than necessary due to air retained in the condenser ing system problems are discussed. Power plant operating the plant heat rate will reflect this condition. personnel will be able to utilize this information when investigat- ing steam condenser performance problems. A checklist is Manufacturers that provide both condensers and vacuum equip- provided which can be used to isolate these performance prob- ment to the power industry are involved in the design, lems. -
STEAM OR VAPOUR CONDENSERS (Condensation of Vapours B01D5
F28B STEAM OR VAPOUR CONDENSERS (condensation of vapours B01D5/00; steam engine plants having condensers F01K; liquefaction of gases F25J; details of heat-exchange and heat-transfer arrangements of general application F28F) Definition statement This subclass/group covers: As specified in the head notes of the field F28, an apparatus using heat exchange for specific purposes is classified either in subclass F28B or in the appropriate subclasses of, for example, classes F22, F24, F25, F26, or F27; or in F28C, F28D. The subclass F28B covers heat exchangers for converting steam or vapour from its gaseous to its liquid state: typically, a steam condenser has a function to condense exhausted steam from a steam turbine for reuse in the cycle. Steam condensers are widely used in steam turbine power plants. Usually, steam condensers are operated at a pressure below atmospheric pressure, to increase the plant efficiency. However, F28B does not cover condensers used for separation, nor condensers for refrigeration systems. In this subclass, the condenser is not characterised by a mixture of vapours to be separated, nor by a separation process, nor by a specific cooperation with steam engine plants or refrigeration systems: • in the subclass B01D, condensers are involved in a process of separating chemical compounds of a mixture of at least 2 vapours, or a vaporised mixture or solution, e.g. vaporised sea water (the term "vapours" is in the plural); • in the subclass F25J, condensers are also involved in separating processes , but operates under pressure and cryogenic temperatures of liquified gaseous mixtures; • in the subclass F25B, condensers are used in cooling cycles and are characterised by features related to the refrigerant, e.g. -
REEVES Double Cylinder, Simple and Cross Compound Engines
DIRECTIONS FOR OPERATING REEVES Double Cylinder, Simple and Cross Compound Engines Emerson-Brantingham Implement Co., (Incorpo,.,.ted ) Rockford, Illinois REEVES WORKS, COLUMBUS, INDIANA • ~1J,lillII~lIiiOOlm in I J.lililll~~~IIII~lli~ lu l l . I J I I I WlII[)tW:tlJ: I JJJJlmn~~mLIJJ:I]l!lil~t~1il 1 LlI]nlill~il~ru:~I.ld .~.1. 1 1 1 ~Mi~llll[h~m[lm l mm[JIll 'I :J:r,l l , 1 , 1 , Lll .i~ 1.11:ll~m R~ • DIRECTIONS FOR OPERATING Reeves Double Cylinder, Simple and Cross Compound Engines EMERSON-BRANTINGHAM IMPLEMENT COMPANY, ( I ncorporatcd ) ROCKFORD, ILLINOIS REEVES WORKS, COLUMBUS, INDIANA Form A241-5m-5-14 Directions for Operating Reeves Double Cylinder, Simple and Cross Compound Engines The first thing that will be seen when the trimming box is opened is this book, the next thing that shou ld ~e done is to carefully read it. The mar ginal index will help to find the subject on which information is desired. Trimmings The small and deli cate trimmings, also a kit of tools are in the wooden box, other parts are in the smoke box and in the fire box of the boiler. Oil Hol es All the oi l holes, also holes in pipes and in the boi ler are filled with a And Holes wooden plug to keep the ci nders and dust out during transportation. If For Fillings by any means a plug is missing, great care should be taken to clean out the hole before the oil cap or fitting is attached.