Development of a Novel Oxide-Oxide Ceramic Matrix Composite for High
Total Page:16
File Type:pdf, Size:1020Kb
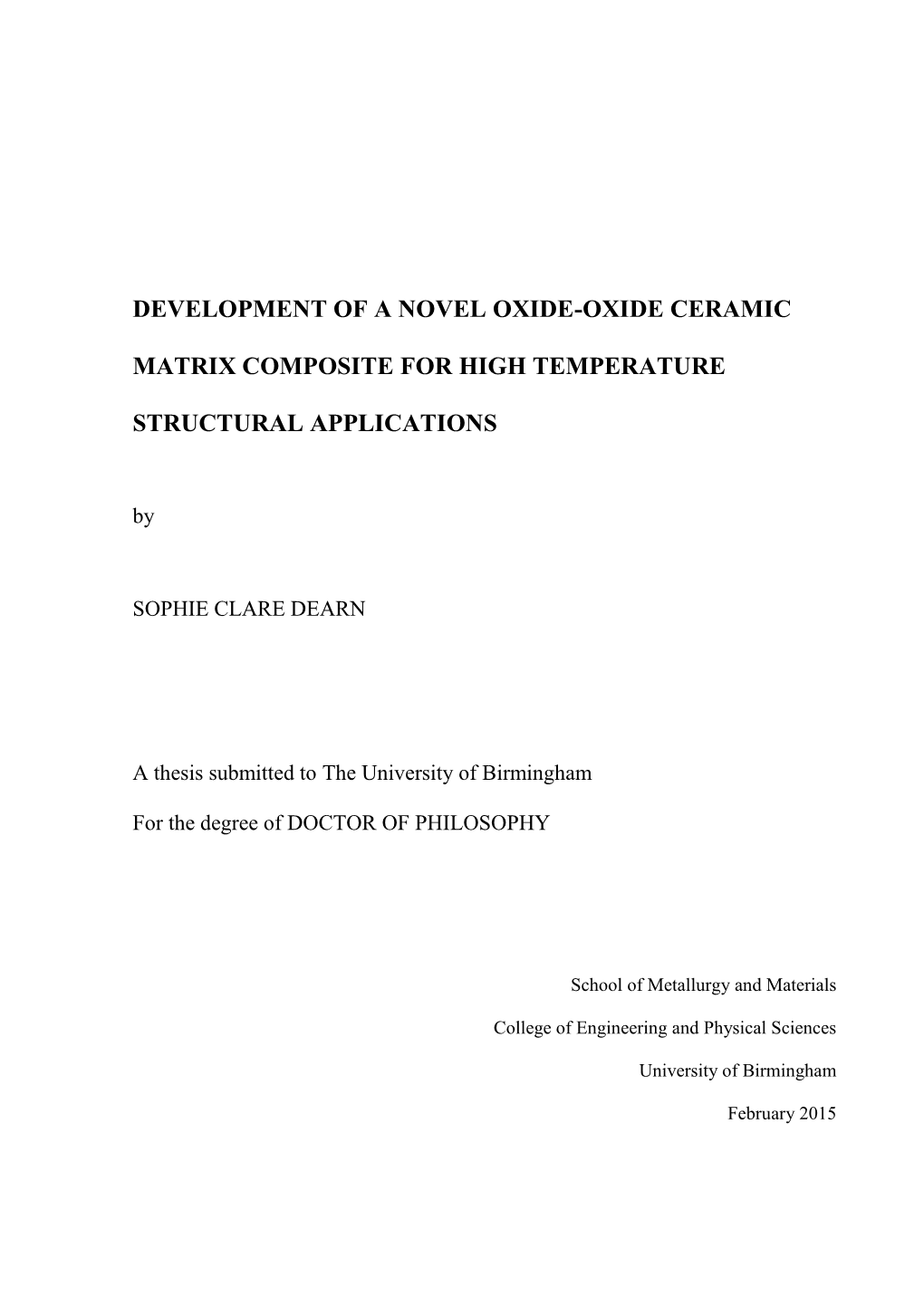
Load more
Recommended publications
-
Ceramic Matrix Composites Taking Flight at GE Aviation Featuring
AMERICAN CERAMIC SOCIETY bullemerginge ceramicstin & glass technology APRIL 2019 Ceramic matrix composites taking flight at GE Aviation Featuring: April 30 – May 1, 2019 Ceramic science in the skies: Electrification, EBCs, and PDCs | New Ohio partnership for technician training FIRING YOUR IMAGINATION FOR 100 YEARS Ads from the 1940’s and 1950’s www.harropusa.com ACerS Anniversary Ad 2.indd 1 2/13/19 3:44 PM contents April 2019 • Vol. 98 No.3 feature articles Ceramic matrix composites taking flight at 30 GE aviation The holy grail for jet engines is efficiency, and the improved high-temperature capability of CMC systems is giving General Electric a great advantage. department News & Trends . 4 by Jim Steibel Spotlight . 10 Ceramics in Energy . 19 cover story Research Briefs . 21 Nonoxide polymer-derived CMCs for 34 “super” turbines The melting point of single-crystal blades limits further columns advancement in operating temperature of gas turbines with metallic materials. Ceramics, which have much higher melt- All about aircraft . 29 ing points, hold the promise for future “super” turbines. Infographic by Lisa McDonald by Zhongkan Ren and Gurpreet Singh Deciphering the Discipline . 64 Ultra-high temperature oxidation of high entropy UHTCs Taking off: Advanced materials contribute by Lavina Backman 40 to the evolution of electrified aircraft Commercial electrified aircraft are expected to take off within the next decade—and advanced materials are play- ing an increasingly critical role in solving key technical challenges that will push the boundaries even higher. meetings 25th International Congress on by Ajay Misra Glass (ICG 2019) . 56 GFMAT-2/Bio-4 . -
Development of New Matrix and Interfacial Materials for Ceramic Matrix Composites Gavin C
University of Connecticut OpenCommons@UConn Doctoral Dissertations University of Connecticut Graduate School 8-26-2014 Development of New Matrix and Interfacial Materials for Ceramic Matrix Composites Gavin C. Richards University of Connecticut - Storrs, [email protected] Follow this and additional works at: https://opencommons.uconn.edu/dissertations Recommended Citation Richards, Gavin C., "Development of New Matrix and Interfacial Materials for Ceramic Matrix Composites" (2014). Doctoral Dissertations. 522. https://opencommons.uconn.edu/dissertations/522 Development of New Matrix and Interfacial Materials for Ceramic Matrix Composites Gavin C. Richards, PhD University of Connecticut, 2014 Pre-ceramic polymers are attractive, low cost materials for the manufacture of ceramic fibers and matrix materials in Ceramic Matrix Composites (CMCs). A new pre-ceramic polymer, an ethanol-modified polyvinylsilazane (PVSZ), was synthesized and characterized. The PVSZ polymer has been previously shown to be a viable precursor for silicon nitride and silicon carbide based ceramics, but lacked stability when exposed to air. The PVSZ polymer was synthesized via the ammonolysis of trichlorovinylsilazane in tetrahydrofuran (THF), and then reacted with ethanol to form the ethanol-modified PVSZ. The PVSZ polymer and ethanol- modified PVSZ resin were each characterized with Attenuated Total Reflectance spectroscopy (ATR), 1H Nuclear Magnetic Resonance ( 1H-NMR), and Gel Permeation Chromatography (GPC), Thermogravimetric Analysis (TGA), Residual Gas Analysis (RGA), and X-Ray Powder Diffraction (XRD) of the ceramic char after pyrolysis in various atmospheres. A second new modified PVSZ was also synthesized. Rather than use ethanol, a second silane monomer was added during synthesis, with the intent of stabilizing the polymer without incorporating oxygen. The new end cap modified PVSZ (EC-PVSZ) was characterized using the same methods outlined for the ethanol-modified PVSZ. -
Carbon Fiber /Reaction-Bonded Carbide Matrix For
Carbon fiber /reaction-bonded carbide matrix for composite materials -Manufacture and characterization Jérôme Magnant, Laurence Maillé, René Pailler, Jean-Christophe Ichard, Alain Guette, Francis Rebillat, Eric Philippe To cite this version: Jérôme Magnant, Laurence Maillé, René Pailler, Jean-Christophe Ichard, Alain Guette, et al.. Carbon fiber /reaction-bonded carbide matrix for composite materials -Manufacture and charac- terization. Journal of the European Ceramic Society, Elsevier, 2012, 32 (16), pp.4497 - 4505. 10.1016/j.jeurceramsoc.2012.06.009. hal-01845172 HAL Id: hal-01845172 https://hal.archives-ouvertes.fr/hal-01845172 Submitted on 20 Jul 2018 HAL is a multi-disciplinary open access L’archive ouverte pluridisciplinaire HAL, est archive for the deposit and dissemination of sci- destinée au dépôt et à la diffusion de documents entific research documents, whether they are pub- scientifiques de niveau recherche, publiés ou non, lished or not. The documents may come from émanant des établissements d’enseignement et de teaching and research institutions in France or recherche français ou étrangers, des laboratoires abroad, or from public or private research centers. publics ou privés. Carbon fiber /reaction-bonded carbide matrix for composite materials - Manufacture and characterization Jérôme Magnant1; Laurence Maillé1*; René Pailler1; Jean-Christophe Ichard1; Alain Guette1; Francis Rebillat1; Eric Philippe2 1 University of Bordeaux, Laboratory for Thermostructural Composites (LCTS), Pessac, France. 2 SAFRAN - Snecma Propulsion Solide, Le Haillan, France. ABSTRACT The processing of self-healing Ceramic Matrix Composites by a short time and low cost process was studied. This process is based on the deposition of fiber dual interphases by chemical vapor infiltration and on the densification of the matrix by reactive melt infiltration of silicon. -
Advanced Measurements of Silicon Carbide Ceramic Matrix Composites
INL/EXT-12-27032 Advanced Measurements of Silicon Carbide Ceramic Matrix Composites David Hurley Farhad Fazbod Zilong Hua Stephen Reese Marat Khafizov August 2012 The INL is a U.S. Department of Energy National Laboratory operated by Battelle Energy Alliance DISCLAIMER This information was prepared as an account of work sponsored by an agency of the U.S. Government. Neither the U.S. Government nor any agency thereof, nor any of their employees, makes any warranty, expressed or implied, or assumes any legal liability or responsibility for the accuracy, completeness, or usefulness, of any information, apparatus, product, or process disclosed, or represents that its use would not infringe privately owned rights. References herein to any specific commercial product, process, or service by trade name, trade mark, manufacturer, or otherwise, does not necessarily constitute or imply its endorsement, recommendation, or favoring by the U.S. Government or any agency thereof. The views and opinions of authors expressed herein do not necessarily state or reflect those of the U.S. Government or any agency thereof. INL/EXT-12-27032 Advanced Measurements of Silicon Carbide Ceramic Matrix Composites David Hurley Farhad Farzbod Zilong Hua Stephen Reese Marat Khafizov August, 2012 Idaho National Laboratory Materials Science and Engineering Department Idaho Falls, Idaho 83415 http://www.inl.gov Prepared for the U.S. Department of Energy Office of Nuclear Energy Under DOE Idaho Operations Office Contract DE-AC07-05ID14517 ii iii ABSTRACT Silicon carbide (SiC) is being considered as a fuel cladding material for accident tolerant fuel under the Light Water Reactor Sustainability (LWRS) Program sponsored by the Nuclear Energy Division of the Department of Energy. -
Ceramic Matrix Composites Containing Carbon Nanotubes
View metadata, citation and similar papers at core.ac.uk brought to you by CORE provided by Spiral - Imperial College Digital Repository Ceramic matrix composites containing carbon nanotubes Johann Cho1,2, Aldo R Boccaccini1*, Milo SP Shaffer2* 1 Department of Materials, Imperial College London, London SW7 2BP, U.K. 2 Department of Chemistry, Imperial College London, London SW7 2AZ, U.K. *Contact authors: A. R. Boccaccini ([email protected]), M. S. P. Shaffer ([email protected]) Abstract Due to the remarkable physical and mechanical properties of individual, perfect carbon nanotubes (CNTs), they are considered to be one of the most promising new reinforcements for structural composites. Their impressive electrical and thermal properties also suggest opportunities for multifunctional applications. In the context of inorganic matrix composites, researchers have particularly focussed on CNTs as toughening elements to overcome the intrinsic brittleness of the ceramic or glass material. Although there are now a number of studies published in the literature, these inorganic systems have received much less attention than CNT/polymer matrix composites. This paper reviews the current status of the research and development of CNT-loaded ceramic matrix composite materials. It includes a summary of the key issues related to the optimisation of CNT-based composites, with particular reference to brittle matrices and provides an overview of the processing techniques developed to 1 optimise dispersion quality, interfaces and density. The properties of the various composite systems are discussed, with an emphasis on toughness; a comprehensive comparative summary is provided, together with a discussion of the possible toughening mechanism that may operate. -
Design for Additive Manufacturing of Composite Materials and Potential Alloys: a Review
Manufacturing Rev. 2016, 3,11 Ó H.A. Hegab, Published by EDP Sciences, 2016 DOI: 10.1051/mfreview/2016010 Available online at: http://mfr.edp-open.org REVIEW OPEN ACCESS Design for additive manufacturing of composite materials and potential alloys: a review Hussien A. Hegab* Department of Mechanical Design and Production Engineering, Cairo University, 12613 Giza, Egypt Received 1 December 2015 / Accepted 23 May 2016 Abstract – As a first step of applying additive manufacturing (AM) technology, plastic prototypes have been pro- duced using various AM Process such as Fusion Deposition Modeling (FDM), Stereolithography (SLA) and other processes. After more research and development, AM has become capable of producing complex net shaped in mate- rials which can be used in applicable parts. These materials include metals, ceramics, and composites. Polymers and metals are considered as commercially available materials for AM processes; however, ceramics and composites are still considered under research and development. In this study, a literature review on design for AM of composite materials and potential alloys is discussed. It is investigated that polymer matrix, ceramic matrix, metal matrix, and fiber reinforced are most common composites through AM. Furthermore, Functionally Graded Materials (FGM) is considered as an effective application of AM because AM offers the ability to control the composition and optimize the properties of the built part. An example of FGM through using AM technology is the missile nose cone which includes an ultra-high temperature ceramic graded to a refractory metal from outside to inside and it used for sustaining extreme external temperatures. During this work, different applications of AM on different classifica- tions of composite materials are shown through studying of industrial objective, the importance of application, processing, results and future challenges. -
Image-Based Numerical Modeling of Self-Healing in a Ceramic-Matrix Minicomposite
ceramics Article Image-Based Numerical Modeling of Self-Healing in a Ceramic-Matrix Minicomposite Grégory Perrot 1,2,†, Guillaume Couégnat 2,† , Mario Ricchiuto 3,† and Gerard L. Vignoles 1,*,† 1 Laboratoire des Composites ThermoStructuraux (LCTS), University of Bordeaux, UMR 5801: CNRS-Safran-CEA-UBx, 3, Allée de La Boétie, 33600 Pessac, France; [email protected] 2 CNRS, Laboratoire des Composites ThermoStructuraux (LCTS), 33600 Pessac, France; [email protected] 3 Team CARDAMOM, Inria Bordeaux Sud-Ouest, 200 Avenue de la Vieille Tour, 33405 Talence CEDEX, France; [email protected] * Correspondence: [email protected]; Tel.: +33-5-5684-4700 † These authors contributed equally to this work. Received: 27 February 2019; Accepted: 29 April 2019; Published: 2 May 2019 Abstract: Self-healing, obtained by the oxidation of a glass-forming phase, is a crucial phenomenon to ensure the lifetime of new-generation refractory ceramic-matrix composites. The dynamics of oxygen diffusion, glass formation and flow are the basic ingredients of a self-healing model that has been developed here in 2D in a transverse crack of a mini-composite. The presented model can work on a realistic image of the material section and is able to simulate the healing process and to quantify the exposure of the material to oxygen: a prerequisite for its lifetime prediction. Crack reopening events are handled satisfactorily, and healing under cyclic loading can be simulated. This paper describes and discusses a typical case in order to show the model capabilities. Keywords: self-healing; ceramic-matrix composites; image-based modelling Highlights • The numerical model features oxidation kinetics and liquid oxide flow • The model works on material images or on virtual material meshes (incorporates realistic fiber arrangements and size distributions) • It describes self-healing restart after crack reopening 1. -
Performance Characterization of Ceramic Matrix Composites Through Uniaxial Monotonic Tensile Testing
Dissertations and Theses 12-2016 Performance Characterization of Ceramic Matrix Composites through Uniaxial Monotonic Tensile Testing Jóhannes Pétursson Follow this and additional works at: https://commons.erau.edu/edt Part of the Aerospace Engineering Commons Scholarly Commons Citation Pétursson, Jóhannes, "Performance Characterization of Ceramic Matrix Composites through Uniaxial Monotonic Tensile Testing" (2016). Dissertations and Theses. 310. https://commons.erau.edu/edt/310 This Thesis - Open Access is brought to you for free and open access by Scholarly Commons. It has been accepted for inclusion in Dissertations and Theses by an authorized administrator of Scholarly Commons. For more information, please contact [email protected]. PERFORMANCE CHARACTERIZATION OF CERAMIC MATRIX COMPOSITES THROUGH UNIAXIAL MONOTONIC TENSILE TESTING A Thesis Submitted to the Faculty of Embry-Riddle Aeronautical University by J´ohannesP´etursson In Partial Fulfillment of the Requirements for the Degree of Master of Science in Aerospace Engineering December 2016 Embry-Riddle Aeronautical University Daytona Beach, Florida iii ACKNOWLEDGMENTS I have always said that engineering is a team sport. Even in the process of com- pleting my individual thesis, there have been many people along the way on whom I have relied for moral, technical, and logistical support, and I give my thanks: Dr. Luis Gonzalez for his direction and patience as my thesis advisor, and for getting our technical paper accepted into the 2015 CMCEE ceramics conference in Vancouver, BC. Dr. Daewon Kim for allowing me use of his tensile machine and DAQ devices, and for serving on my advisory board. Dr. Virginie Rollin for teaching me the foundations of failure analysis, and for serving on my advisory board. -
Ceramic Matrix Composite Environmental Protection Strategies Bradley Richards University of Virginia
Engineering Conferences International ECI Digital Archives Thermal Barrier Coatings IV Proceedings Summer 6-26-2014 Ceramic matrix composite environmental protection strategies Bradley Richards University of Virginia Hengbei Zhao University of Virginia Haydn Wadley University of Virginia Follow this and additional works at: http://dc.engconfintl.org/thermal_barrier_iv Part of the Materials Science and Engineering Commons Recommended Citation Bradley Richards, Hengbei Zhao, and Haydn Wadley, "Ceramic matrix composite environmental protection strategies" in "Thermal Barrier Coatings IV", U. Schulz, German Aerospace Center; M. Maloney, Pratt & Whitney; R. Darolia, GE Aviation (retired) Eds, ECI Symposium Series, (2015). http://dc.engconfintl.org/thermal_barrier_iv/41 This Conference Proceeding is brought to you for free and open access by the Proceedings at ECI Digital Archives. It has been accepted for inclusion in Thermal Barrier Coatings IV by an authorized administrator of ECI Digital Archives. For more information, please contact [email protected]. CERAMIC MATRIX COMPOSITE ENVIRONMENTAL PROTECTION STRATEGIES Bradley Richards, Hengbei Zhao and Haydn Wadley University of Virginia, USA Ceramic matrix composite components based upon SiC fibers and matrices are beginning to be used in aircraft engines. However, the formation of gaseous silicon hydroxides at the temperatures and pressures present within the hot section of the engine results in volatilization of their normally protective oxide scale leading to SiC recession rates significantly -
Rolls Royce Environmental Barrier Coatings For
Environmental Barrier Coatings for SiC Ceramic Matrix Composite Gas Turbine Blades Adithya Bhattachar, Mary Katherine O’Brien, Mitchell Rencheck, Gregory Scofield Faculty Advisors: Prof. Rodney Trice Industrial Sponsors: Dr. Kang Lee & Dr. Stephanie Gong Rolls-Royce has been developing silicon carbide (SiC) Ceramic Matrix Composites (CMCs) to be used in place of single crystal This work is super alloys for gas turbine blades due to their lower weights and higher operating temperature limits. However, SiC degrades in a sponsored by high-temperature combustion environment, creating a need for an environmental barrier coating (EBC) to protect the SiC. It has Rolls-Royce been hypothesized that an EBC containing mullite and barium strontium aluminosilicate (BSAS) can prevent the glassy phase from North America, forming, while also displaying limited cracking when thermally cycled. During experimentation, this hypothesis was not confirmed, Indianapolis, IN. as adding BSAS to mullite caused the coating to bubble during thermal cycling. Project Background Results Results Continued • CMCs have the potential to increase operating Coating Process Thermal Cycle Testing temperatures inside gas turbine aircraft engines and Effective slurries contain Coating SiC thereby increase fuel efficiency. • 1 wt. % Darvan-C • SiC/SiC CMCs are desirable due to their low weight, • 4 wt. % PVB low coefficient of thermal expansion (CTE), and high • 1:1 wt. % Ethanol:Powder melting temperature. Observations • SiC is problematic in high temperature environments • Coatings adhered to SiC due to interaction with water vapor, which causes substrate after sintering. 200 μm [1] 150 μm oxidation and the formation of a low-Tm glass phase . • When LiCO3 was used as • An EBC is needed to protect SiC from the water vapor a sintering aid, coating 30 μm Images of a 4:1 BSAS to mullite coating before thermal cycling (left) and after thermal cycling (right) present in a combustion environment. -
Fabrication of Ceramic and Metal Matrix Composites from Selective
Fabrication ofCeramic and Metal Matrix ComJX>sites From Selective Laser Sintered Ceramic Preforms Lucy Deckard and T. Dennis Oaar Lanxide Corporation Newark, Delaware Abstract This paper will discuss the tool~less fabrication offunctional advanced comJX>sites by infusion ofa ceramic or metal matrixinto Selective Laser Sintered(SLS) porous ceranU~preforms using Lanxide'spatentedmatrix infusionproc;esses. The fabri~ationofJX>rous preformS ofparticulate cerami~sby SLS atthe University ofTexas at Austin is described in a companion paper. The PRlME}(TI4 pressureless metal infi1trationp~ss was used to infiltrate<alUIninum matrices into both SiC and Al~03 particulate SLS prefonns to make metal matrix comJX>sites withoutthe use of tooling. Also, SiC I~03 ceramic matrix comJX>sites were fabricated using the DIMO}(TI4 Al 0 directed metal oxiJation process to grow an 2 3 matrix into porous SiC particulate SLS preforms. Measured properties and microstructures of the resulting composites will be presented and compared to similar comJX>sites made using conventionally fabricated preforms. The rapid prototyping of a SiCiAI MMC electronic power package to near~net shape from an SLS preform will also be describeQ. Introduction Lanxide's matrix infusion processes for fabricating ceramic and metal matrix ~omJX>sites are near~net shape processes in which a matrix is infused into a porous ceramic preform. The final comJX>site shape is dictated by the shape of the preform; therefore, a critical step in the process is the fabrication of a porous preform to near-net shape. Prefonns typically have been made using a variety ofstandard ceramic processing methods, including tape casting, injection molding, green machining, dry pressing, etc. -
Characterization of Ceramic Matrix Composite Materials Using Millimeter-Wave Techniques
Wright State University CORE Scholar Browse all Theses and Dissertations Theses and Dissertations 2012 Characterization of Ceramic Matrix Composite Materials using Millimeter-Wave Techniques Matthew Lee Bischoff Wright State University Follow this and additional works at: https://corescholar.libraries.wright.edu/etd_all Part of the Physics Commons Repository Citation Bischoff, Matthew Lee, "Characterization of Ceramic Matrix Composite Materials using Millimeter-Wave Techniques" (2012). Browse all Theses and Dissertations. 683. https://corescholar.libraries.wright.edu/etd_all/683 This Thesis is brought to you for free and open access by the Theses and Dissertations at CORE Scholar. It has been accepted for inclusion in Browse all Theses and Dissertations by an authorized administrator of CORE Scholar. For more information, please contact [email protected]. CHARACTERIZATION OF CERAMIC MATRIX COMPOSITE MATERIALS USING MILLIMETER-WAVE TECHNIQUES A thesis submitted in partial fulfillment of the requirements for the degree of Master of Science By MATTHEW LEE BISCHOFF B.S., The University of Maine, 2002 M.S., Purdue University, 2006 2012 Wright State University WRIGHT STATE UNIVERSITY GRADUATE SCHOOL November 19, 2012 I HEREBY RECOMMEND THAT THE THESIS PREPARED UNDER MY SUPERVISION BY Matthew Lee Bischoff ENTITLED Characterization of Ceramic Matrix Composite Materials Using Millimeter-Wave Techniques BE ACCEPTED IN PARTIAL FULFILLMENT OF THE REQUIREMENTS FOR THE DEGREE OF Master of Science. Committee on Final Examination Douglas T. Petkie, Ph.D. Thesis Director Douglas T. Petkie, Ph.D. Douglas T. Petkie, Ph. D. Chair, Department of Physics Jason A. Deibel, Ph.D. Gary Farlow Ph.D. Andrew Hsu, Ph.D. Dean, Graduate School COPYRIGHT BY MATTHEW L.