Electrostatic Motors
Total Page:16
File Type:pdf, Size:1020Kb
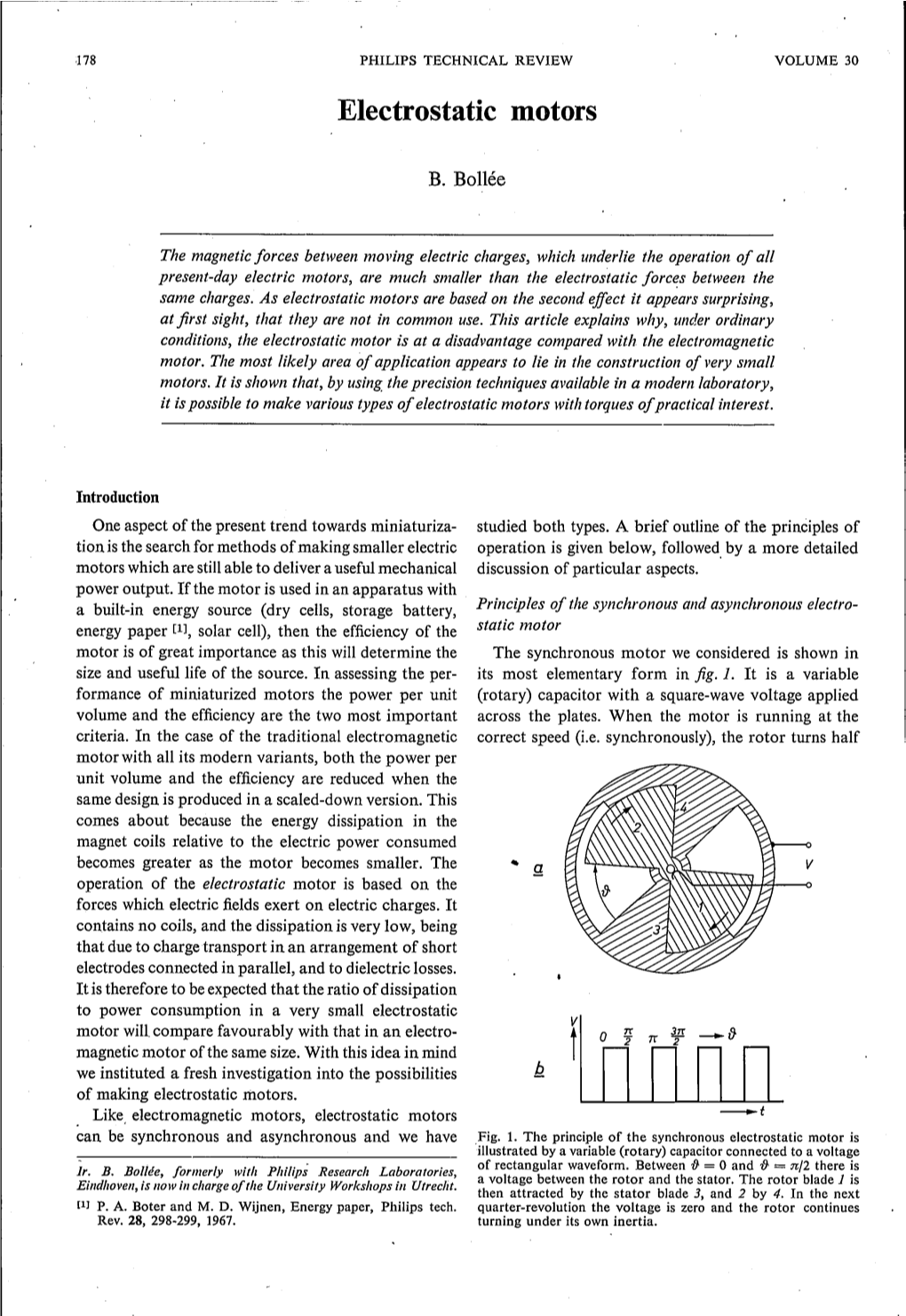
Load more
Recommended publications
-
Design and Fabrication of Moto Autor
A. John Joseph Clinton Int. Journal of Engineering Research and Applications www.ijera.com ISSN : 2248-9622, Vol. 5, Issue 1( Part 4), January 2015, pp.07-16 RESEARCH ARTICLE OPEN ACCESS Design and Fabrication of Moto Autor A. John Joseph Clinton*, P. Rajkumar** *(Department of Mechanical Engineering, Chandy College of Engineering, Affliated to Anna University- Chennai, Tuticorin-05) ** (Department of Mechanical Engineering, Chandy College of Engineering,Affliated to Anna University- Chennai, Tuticorin-05) ABSTRACT This project is based on the need for the unconventional motor. This work will be another addition in the unconventional revolution. Our project is mainly composed of design and fabrication of the ―MOTO AUTOR‖ which is a replacement of conventional motors in many applications of it. This motoautor can run on its own without any traditional input for fuelling it except for the initiation where permanent magnets has to be installed at first. It is a perpetual motion system that can energize itself by taking up the free energy present in the nature itself. This project enables to motorize systems with very minimal expenditure of energy. Keywords–Perpetual motion, Free energy conversion, Unconventional motor, Magnetic principles, Self- energizing I. INTRODUCTION Perhaps the first electric motors were In normal motoring mode, most electric motors simple electrostatic devices created by the Scottish operate through the interaction between an electric monk Andrew Gordon in the 1740s. The theoretical motor's magnetic field and winding currents to principle behind production of mechanical force by generate force within the motor. In certain the interactions of an electric current and a magnetic applications, such as in the transportation industry field, Ampère's force law, was discovered later with traction motors, electric motors can operate in by André-Marie Ampère in 1820. -
The Manual of Free Energy Devices and Systems
THE MANUAL OF FREE ENERGY DEVICES AND SYSTEMS THIS MANUAL FULLY DESCRIBES THE VARIOUS PIONEERING PROTOTYPE "FREE ENERGY" POWER PRO- JECTS BEING DEVELOPED AND EVOLVED IN THIS MAJOR NEW AREA OF APPLIED PHYSICS. THE MANUAL IS DIVIDED INTO FOURTEEN TYPES OF SPECIFIC PROJECTS IN BOTH ROTATING AND SOLID STATE UNITS, AND HYBRIDS, WITH SOME TYPES SUB- DIVIDED INTO OTHER SUBCLASSES, AS NOTED IN THE ENCLOSED TABLE OF CONTENT. CONTRARY TO THE OUTMODED OPINION OF MANY WELL ESTABLISHED PHYSICISTS, THESE VARIOUS UNITS AND SYSTEMS ARE HERE AND NOW EVENTS WHICH WILL CON- TINUE TO BE IMPROVED UPON UNTIL A "NEW WAVE" OF APPLIED ENERGY PHYSICS IS IN PLACE, AND THE OLD BELIEFS AND VIEWS FALL BY THE WAYSIDE! Copyright © 1986 General Content & Format, other Copyrights, as noted ISBN 0-932298-59-5 1st Printing 1986 ELECTRODYNE CORPORATION Clearwater, FL, 33516 2nd Printing 1987 3rd Printing 1991 - Published by CADAKE INDUSTRIES & TRI-STATE PRESS P.O. Box 1866 Clayton, Georgia 30525 THE SECRETS OF FREE ENERGY The subject of free energy and perpetual motion has received much undue criticism and misrepresentation over the past years. If we consider the entire picture, all motion is perpetual! Motion and energy may disperse or transform, but will always remain in a perpetually energized state within the complete system. Consider the "free energy" hydro-electric plants. Water from a lake powers generators and flows on down the river. The lake though is constantly replenished by springs, run-off, etc. Essentially, the sun is responsible for keeping this system "perpetual." The sun may burn out but the total energy-mass remains constant within the cycling univer- sal system. -
Switched Reluctance Generator
Wind Turbine Generator for Distributed Wind Systems Distributed Wind Energy Association— Electrical Systems Subgroup Meeting Eduard Muljadi March 25–26, 2015 NREL is a national laboratory of the U.S. Department of Energy, Office of Energy Efficiency and Renewable Energy, operated by the Alliance for Sustainable Energy, LLC. Types of WTGs Type 1—Fixed Speed Type 2—Variable Slip Type 3—Variable Speed Type 4—Full Power Conversion 2 Distributed Wind Turbine Progress Then (1980s) Now (2015) Technical Technical • Single-speed or dual-speed induction • Variable-speed operation (DFIG—Type 3 generator (fixed speed—Type 1) or PMSG—Type 4) • PM alternator with SCR base (harmonics, • IGBT Si-based (800 V–1 kV), currently slow operation, line commutated) SiC-based (10—15 kV) • Aerodynamic control was primitive, mostly • Aerodynamic control (yaw, electro- mechanical (furling/tilting—horizontal or mechanical servo-based), pitch control vertical), pitch control—relatively new, • Modern control allows optimization in mostly stall control design, control, and energy capture Cost Cost • PE had low power rating, slow switching, and • PE is relatively cheap—e.g., Siemens was very expensive chose exclusively Type 4 WTGs • PM was ferrite (B = 0.3 Tesla), large and • Rare earth PM (B = 1.4 Tesla), small, light heavy machines machines • Primitive control systems may lead to large • Modern control allows optimization of mechanical-based system size and dimension of the WTG • LCOE was heavily taxed by the CAPEX and • LCOE (CAPEX and OPEX) has dropped OPEX significantly -
High Power Electrostatic Motor with 95% Efficency
High Power Electrostatic Motor with 95% Efficency This small motor packs some punch at 100 watts and weights only 200 grams giving it a power to weight ration of 500 watts to the kilogram I took a liking to this motor on a recent review I was doing on new Electric motor technology. Although 100 watts and 200 grams weight may not sound impressive, it is when you need power for robotics and other specialist uses the power to weight ratio is important. This is also important for electric vehicle applications where weight is critical. Existing small motors are less than 200 watts per kilogram. According to SHINSEI CORPORATION, The High Power Electrostatic Motor ( ESM65-TR1) was made as an trial production model is very lightweight compared with the electromagnetic motor of the same power. Since there is almost neither a friction part nor an exothermic part, energy efficiency is more than 95%. Moreover, ESM65-TR1 can show high performance in a vacuum environment. Furthermore, ESM65-TR1 can also be used in a nonmagnetic environment. How Does it Work? With all the motor technologies being developed this one stood out to me on a recent review. The High Power Electrostatic Motor consists of a rotor, a stator and a shaft. Many electrodes are arranged on the rotor and the stator. An electric charge is electrified at this electrode and a shaft rotates by the attraction and repulsion of those electrodes. It is possible to control operation of a motor by controlling the timing which changes the electric charge impressed to an electrode.This is an image which shows the state of the electric charge of the electrode on a rotor and a stator. -
Faculty of Engineering
University of Rajshahi DEPARTMENT OF ELECTRICAL & ELECTRONIC ENGINEERING Faculty of Engineering Bachelor of Science in Electrical and Electronic Engineering Degree Part-I Examination : 2018 Part-II Examination : 2019 Part-III Examination : 2020 Part-IV Examination : 2021 Syllabus For B.Sc. Engineering (EEE) Degree Session: 2017-2018 Published by Department of Electrical & Electronic Engineering University of Rajshahi Rajshahi – 6205, Bangladesh. Cover Concept: Md. Shariful Islam Cover Design: Printing Press Contact for Correspondence: Chairman Department of Electrical and Electronic Engineering University of Rajshahi Rajshahi – 6205, Bangladesh. Telephone: +88-0721-711309 Email: [email protected] Web: www.ru.ac.bd/eee Disclaimer Information contained in this booklet is intended to provide guidance to those who are concerned with undergraduate studies in the Department of Electrical and Electronic Engineering. No responsibility will be borne neither by the Department of Electrical and Electronic Engineering nor by University of Rajshahi if any inconvenience or expenditure is caused to any person because of the information provided in this booklet. Also, the information contained in it is subject to change at any time without any prior notification. ii PREFACE Electrical and Electronic Engineering (EEE) is one of the most regarded discipline among the engineering community all over the globe. It encompasses a diverse subject knowledge and vivid understanding of the physical world. From the generation of electrical power to the multiple uses and applications of it falls under the category of EEE. However, engineering as a whole is a rapidly evolving arena throughout the world nowadays. To meet the demands of this highly regarded and promptly changing branch of science upgradation of course curricula, improvement of the laboratory facilities and revisiting the needs for quality teaching are regularly monitored and addressed by the department of EEE at Rajshahi University. -
Thermodynamics and Steady State of Quantum Motors and Pumps Far from Equilibrium
entropy Article Thermodynamics and Steady State of Quantum Motors and Pumps Far from Equilibrium Raúl A. Bustos-Marún 1,2,* and Hernán L. Calvo 1,3,* 1 Instituto de Física Enrique Gaviola (CONICET) and FaMAF, Universidad Nacional de Córdoba, Córdoba 5000, Argentina 2 Facultad de Ciencias Químicas, Universidad Nacional de Córdoba, Córdoba 5000, Argentina 3 Departamento de Física, Universidad Nacional de Río Cuarto, Ruta 36, Km 601, Río Cuarto 5800, Argentina * Correspondence: [email protected] (R.A.B.-M.); [email protected] (H.L.C.) Received: 27 June 2019; Accepted: 16 August 2019; Published: 23 August 2019 Abstract: In this article, we briefly review the dynamical and thermodynamical aspects of different forms of quantum motors and quantum pumps. We then extend previous results to provide new theoretical tools for a systematic study of those phenomena at far-from-equilibrium conditions. We mainly focus on two key topics: (1) The steady-state regime of quantum motors and pumps, paying particular attention to the role of higher order terms in the nonadiabatic expansion of the current-induced forces. (2) The thermodynamical properties of such systems, emphasizing systematic ways of studying the relationship between different energy fluxes (charge and heat currents and mechanical power) passing through the system when beyond-first-order expansions are required. We derive a general order-by-order scheme based on energy conservation to rationalize how every order of the expansion of one form of energy flux is connected with the others. We use this approach to give a physical interpretation of the leading terms of the expansion. -
Free Energy Patents.Pdf
Free energy related patents Patentee Number Title Class Tesla, N. 512,340 Coil for Electromagnets Stubblef jeld,N. 600,457 Electrical Battery 2 Rodgers, J.H. 958,829 Apparatus for HF Currents 1 Tustin, E.B. 961,914 Wireless Lighting Tesla, N. 1,061,206 Turbine Rodgers, J.H. 1,220,005 Wireless Signaling 1 Bintliff, W.T. 1,237,862 Primer for Gas Engines 4 Rodgers, J.H. 1,303,729 Wireless Signaling 1 Rodgers, J.H. 1,303,730 Radiosignaling System 1 Rodgers, J.H. 1,315,862 Radiosignaling System 1 Rodgers, J.H. 1,316,188 Radiosignaling System 1 Martin, L.H. 1,319,718 Fuel Vaporizer 4 Rodgers, J.H. 1,322,622 Wireless Signaling 1 Rodgers, J.H. 1,349,103 Radiosignaling System 1 Rodgers, J.H. 1,349,104 Radiosignaling System 1 Rodgers, J.H. 1,387,736 Radiosignaling System 1 Rodgers, J.H. 1,395,454 Radiosignaling System 1 Rodgers, J.H. 1,510,799 Loop Aerial 1 Quisling, S. 1,743,978 Propulsion Mechanism Lilienfeld, J.E. 1,745,175 Current Control 5 Britten, C.J. 1,826,727 Radio Apparatus 2 Powell, A. 1,835,721 Magnetic Motor 6 Worthington, H.L. 1,859,643 Magnetic Motor 6 Bougon, G.H. 1,859,764 Magnetic Device 6 Lilienfeld, J.E. 1,877,140 Current Amplifier 5 Lilienfeld, J.E. 1,900,018 Current Controller 5 Lakhovsky, G. 1,962,565 Multiple Freq. Oscillator 1 Poysa, J.W. 1,963,213 Magnetic Motor 6 Brown, T.T. 1,974,483 Electrostatic Motor 7 Laskowitz, I.B. -
And Redox-Driven Artificial Molecular Motors
This is an open access article published under an ACS AuthorChoice License, which permits copying and redistribution of the article or any adaptations for non-commercial purposes. Review Cite This: Chem. Rev. 2020, 120, 200−268 pubs.acs.org/CR Photo- and Redox-Driven Artificial Molecular Motors Massimo Baroncini,*,†,‡ Serena Silvi,*,†,§ and Alberto Credi*,†,‡ † CLAN-Center for Light Activated Nanostructures, Istituto ISOF-CNR, via Gobetti 101, 40129 Bologna, Italy ‡ Dipartimento di Scienze e Tecnologie Agro-alimentari, Universitàdi Bologna, viale Fanin 44, 40127 Bologna, Italy § Dipartimento di Chimica “G. Ciamician”, Universitàdi Bologna, via Selmi 2, 40126 Bologna, Italy ABSTRACT: Directed motion at the nanoscale is a central attribute of life, and chemically driven motor proteins are nature’s choice to accomplish it. Motivated and inspired by such bionanodevices, in the past few decades chemists have developed artificial prototypes of molecular motors, namely, multicomponent synthetic species that exhibit directionally controlled, stimuli-induced movements of their parts. In this context, photonic and redox stimuli represent highly appealing modes of activation, particularly from a technological viewpoint. Here we describe the evolution of the field of photo- and redox-driven artificial molecular motors, and we provide a comprehensive review of the work published in the past 5 years. After an analysis of the general principles that govern controlled and directed movement at the molecular scale, we describe the fundamental photochemical and redox processes that can enable its realization. The main classes of light- and redox-driven molecular motors are illustrated, with a particular focus on recent designs, and a thorough description of the functions performed by these kinds of devices according to literature reports is presented. -
Electrostatic Micro Walkers Micro Electromechanics and Micro Tribology
Electrostatic Micro Walkers Micro Electromechanics and Micro Tribology Niels Tas Electrostatic Micro Walkers Micro Electromechanics and Micro Tribology Niels Tas The Micro Walker Project: The Research described in this thesis was carried out at the Micromechanical Transducers Group ('MicMec') of the MESA Research Institute, Faculty of Electrical Engineering, University of Twente. The Micro Walker project was a cooperative research with and was sponsored by Philips Research, Eindhoven, The Netherlands. De promotiecommissie: Voorzitter: Prof. dr. H. Wallinga Universiteit Twente Secretaris: Prof. dr. H. Wallinga Universiteit Twente Promotoren: Prof. dr. M.C. Elwenspoek Universiteit Twente Prof. dr. ir. M.P. Koster Universiteit Twente Leden: Prof. dr. ir. J.C. Compter Technische Universiteit Eindhoven Prof. dr. ir. P.J. French Technische Universiteit Delft Prof. dr. ir. P.P.L. Regtien Universiteit Twente Dr. D. Reynaerts Katholieke Universiteit Leuven Prof. dr. J.-Å Schweitz Universiteit Uppsala Prof. dr. ir. H.Tijdeman Universiteit Twente CIP-gegevens koninklijke bibliotheek, Den Haag: Tas, Niels R. Electrostatic Micro Walkers/ Niels R. Tas [S.I. : s.n.] Ph.D. Thesis University of Twente, Enschede, The Netherlands ISBN 90-36514355 Subject headings: electrostatic/ micromotors / tribology © 2000 by Niels Tas, Enschede, The Netherlands. ELECTROSTATIC MICRO WALKERS PROEFSCHRIFT ter verkrijging van de graad van doctor aan de Universiteit Twente op gezag van de rector magnificus prof. dr. F.A. van Vught volgens besluit van het College voor Promoties in het openbaar te verdedigen op donderdag 20 april 2000 te 16:45 uur. door Niels Roelof Tas geboren op 4 januari 1970 te Jutphaas Dit proefschrift is goedgekeurd door de promotoren: Prof. dr. -
Sudan University of Science &Technology College Of
SUDAN UNIVERSITY OF SCIENCE &TECHNOLOGY COLLEGE OF GRADUATE STUDIES MSc MECHATRONICS ENGINEERING GENERATING ENERGY FROM LOW ENVIROMENTAL VIBERATION BY USING ELECTROSTATIC ENERGY HARVESTER توليد الطاقة من اﻹهتزازات البيئية املنخفضة بإستخدام حاصـدة الطاقـة اﻹلكرتوستاتيكية A THESIS SUBMITTED IN PARTIAL FULFILMENT OF THE REQUIREMENTS FOR THE DEGREE OF MASTER OF SCIENCE IN MECHATRONICS ENGINEERING PREPARED BY: MOHAMMED RASHID MOHAMMED ELZOUBIER SUPERVISED BY: Dr. MUSSAB ZARROG NOV 2015 ACKNOWLEDGMENT First of all, I would like to thank Allah, The Almighty Allah, for giving me the strength courage to endlessly pursue what is so called knowledge. I would like to express my sincere gratitude and deepest appreciation to my supervisor Dr. Mousab Zarrog, for his support, kind assistance, important advices and encouragement during all stages of the research. Also I would like to express my special thanks and extremely grateful to my family beginning from my father Mr. Rashid Mohammed and my mother Mrs. Siham Awad who supported me throughout this research and my brother Mr. Mojahid and My sisters Miss. Asia Miss. Amal for their courage to finish this research and their deepest love. I also wish to thank my dear friends Eng. Nadir Ahmed Ali and Eng. Mouid Elfatih for their help through the research and listening to my complaints, and my extremely grateful to all of those friends who had supplied me with unlimited encouragement and friendship throughout my period of study I ABSTRACT This research focuses on vibration energy harvesting using electrostatic converters. It synthesizes the various works carried out on electrostatic devices, from concepts, models and up to prototypes; Integration of structures and functions has permitted to reduce electric consumptions of sensors, actuators and electronic devices. -
Submitted in Partial Fulfillment Of
11 FEB 193.5 LI r~ r4RI VACUUM ELECTROSTATIC ENGINEERING By John G. Trump E. E. Polytechnic Institute of Brooklyn, 1929. M. A. Columbia University, 1931. Submittedin partial fulfillment of the requirement for the degree of Doctor of Science from the Massachusetts Institute of Technology 1933 1t.11?7 fAt+o A0IIv,+ . VL AUG&-L *-J. A * -· · *· a · * · . * Certif'ication by Department ......................... , ;~i i ACKNOWLEDGIENT It is a pleasure to recall the stimulating and invaluable association during this research with Dr. RobertJ. Van de Graaff. It was his experimental work and vision which started vacuum electrostatic engineering, and during this investigation he has contributed unfailingly of research technique, ideas, and inspiration. P ' I ?2!3 1_,,2 11 ,, 1 1 I ii TABLE OF CONTENTS Page CHAPTER I - VACUUM ELECTROSTATIC ENGINEERING .................. 1 High Vacuum Insulation .......,.................... 1 VacuumElectrostatic Versus Electromagnetic Machinery ... 8 Electrical Engineering Applications of Vacuum Electrostatics ................,..,.........*** 11 CHAPTER II - VACUUMELECTROSTATIC MACHINE ANALYSIS .......... 15 A-C Synchronous Electrostatic Machine - Type I ... 15 A-C Electrostatic Machines - Type II ..................25 D-C Electrostatic Generator - Type III ... ..............32 D-C Electrostatic Generator - Type IV 38.................38 D-C ElectrostaticGenerator - Type V ........ ·......... 43 D-C Electrostatic Generator - Type VI ................ 46 D-C Electrostatic Motor - Type VII ...................... 48 D-C -
(12) Patent Application Publication (10) Pub. No.: US 2011/0175371 A1 Gray (43) Pub
US 2011 0175371 A1 (19) United States (12) Patent Application Publication (10) Pub. No.: US 2011/0175371 A1 Gray (43) Pub. Date: Jul. 21, 2011 (54) FLYWHEEL SYSTEM Publication Classification (51) Int. Cl. (75) Inventor: Bill Gray, San Francisco, CA (US) HO2NHO2K 7/18I/00 (2006.01) (52) U.S. Cl. .......................... 290/1 R; 318/116; 310/300 (73) Assignee: Yets INC., San Francisco, (57) ABSTRACT A flywheel system has an approximately toroidal flywheel rotor having an outer radius, the flywheel rotor positioned (21) Appl. No.: 13/008,292 around and bound to a hub by Stringers, the stringers each of a radius slightly smaller than the outer radius of the flywheel rotor. The hub is Suspended from a motor-generator by a (22) Filed: Jan. 18, 2011 flexible shaft or rigid shaft with flexible joint, the flywheel rotor having a mass, Substantially all of the mass of the fly wheel rotor comprising fibers, the fibers in large part movable Related U.S. Application Data relative to each other. The motor-generatoris Suspended from a damped gimbal, and the flywheel rotor and motor-generator (62) Division of application No. 11/995,539, filed on Mar. are within a chamber evacuatable to vacuum. An electrostatic 14, 2008, now abandoned, filed as application No. motor/generator can also be within the same vacuum as the PCT/US08/50670 on Jan. 9, 2008. flywheel. 21 Patent Application Publication Jul. 21, 2011 Sheet 1 of 26 US 2011/0175371 A1 Patent Application Pu blication Patent Application Publication Jul. 21, 2011 Sheet 3 of 26 US 2011/0175371 A1 Fig.