Mesa-Redonda-2012-Siemens.Pdf
Total Page:16
File Type:pdf, Size:1020Kb
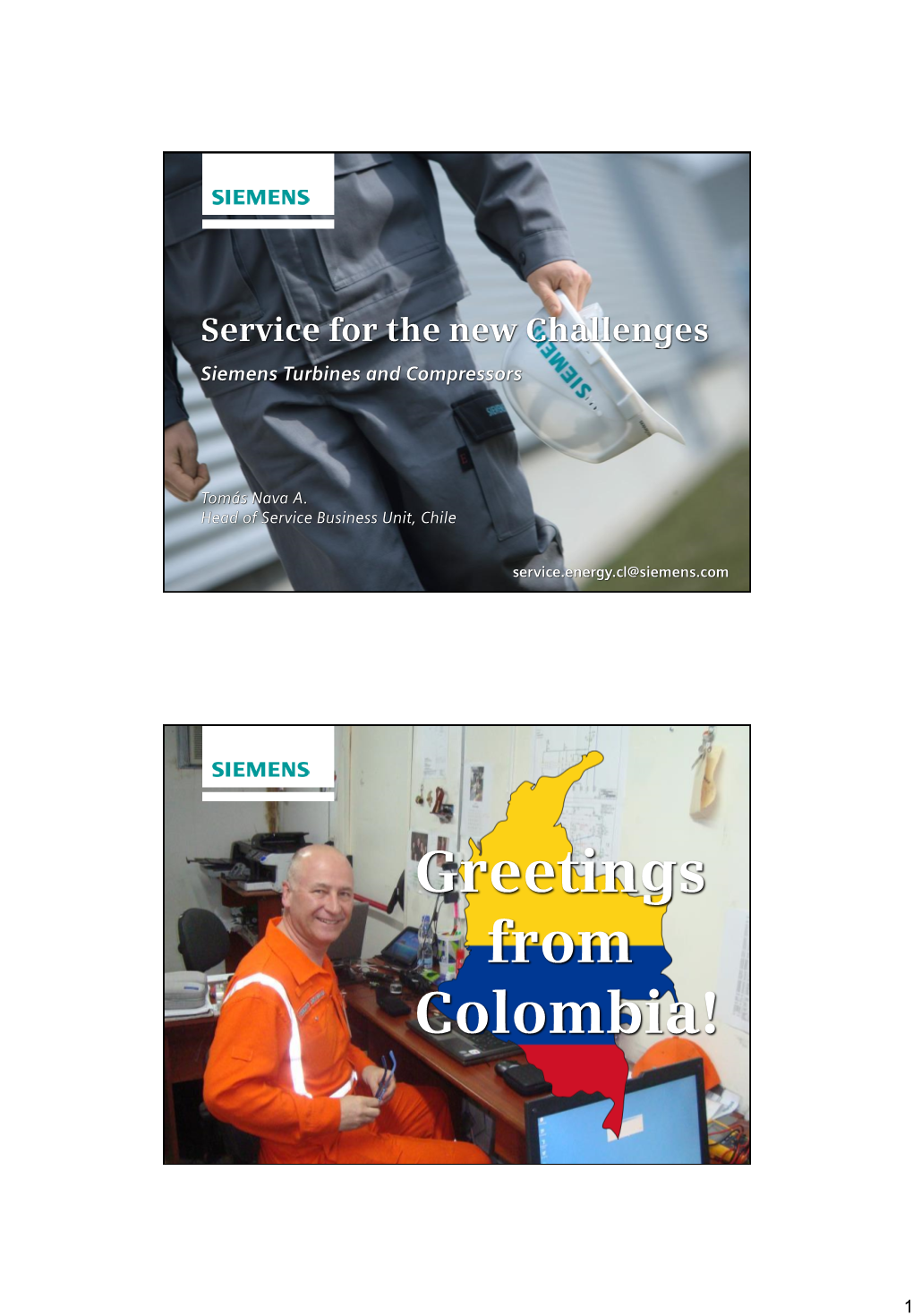
Load more
Recommended publications
-
Qualitative and Quantitative Analysis of Siemens Ag
QUALITATIVE AND QUANTITATIVE ANALYSIS OF SIEMENS AG Authors (Universitat de Barcelona): Patrícia Amor Agut Clara Valls Moreno Gemma Casserras EDITOR: Jordi Marti Pidelaserra (Dpt. Comptabilitat, Universitat Barcelona) 1 Patrícia Amor 14961785 Clara Valls 14959906 Gemma Casserras 14965090 Alessandra Cortegiani (Bloc 3) 14991480 2 BLOC 1: SIEMENS AG BLOC 2: Risk Analysis BLOC 3: Profitability Analysis 3 BLOC 1 SIEMENS AG BASIC INFORMATION 4 Index 1. Introduction 2. Company History 3. Vision, Mission and Strategy 3.1. Vision 3.2. Mission 3.3. Strategy 4. Company Structure 4.1. Board of directors 4.2. Management by sector 5. Company Sectors 5.1. Energy Sector 5.2. Industry Sector 5.3. Healthcare Sector 5.4. Infrastructure and cities Sector 5.5. Financial Services 5.6. Other activities 5.7. Revenues importance 6. Shareholders 7. Stakeholders 8. Competitors 5 1. Introduction: Siemens AG is a German multinational engineering and electronics conglomerate company headquartered in Munich, Germany. It is the largest based in Europe. Founded to manufacture and install telegraphic systems, Germany-based Siemens AG has prospered and grown over 165 years to become a multifaceted electronics and electrical engineering enterprise, and one of the most international corporations in the world. Founded to manufacture and install telegraphic systems, Germany-based Siemens AG has prospered and grown over 165 years to become a multifaceted electronics and electrical engineering enterprise, and one of the most international corporations in the world. The Siemens name has been synonymous with cutting-edge technologies and continuous growth in profitability. With their wide array of products, systems and services, they are world leaders in information and communications, automation and control, power, medical solutions, transportation and lighting. -
Pictures of the Future
Pictures of the Future The Magazine for Research and Innovation | Special Edition: Green Technologies www.siemens.com/pof Tomorrow’s Power Grids How Vehicles, Cities and Alterna- tive Energy Sources will Interact Energy Efficiency Renewable Energy Squeezing Better Results out of Today’s Technologies Solutions for a Sustainable, Low-Carbon Future Pictures of the Future Pictures of the Future | Editorial Contents n recent weeks there have been signs vehicles at night, when electricity is Energy Efficiency Ithat the world may have left the worst of cheaper, and sell it during the day at peak the financial and economic crisis behind — prices. Electric vehicles will also have an and already some people are playing down important stabilizing function. Just a few the causes of the worst crisis in 80 years. hundred thousand electric vehicles con- However, we shouldn't ignore a simple nected to the power grid would provide 66 Scenario 2025 fact: activities aimed exclusively at short- more “balancing power” than Germany Energy-Saving Sleuth term gains don't create long-term value! currently needs to cover its demand peaks. 68 Urban Energy Analysis This is particularly true when it comes The most reliable, cheapest, and most Cities: A Better Energy Picture to climate change. Current efforts to limit environmentally-friendly source of energy 71 Trends: Energy for Everyone warming are based on the expectation that is reduced consumption. That’s why there’s Light at the End of the Tunnel the global community will set course to- a huge need for energy-efficient technolo- 73 World’s Largest Gas Turbine ward a sustainable future. -
Major Orders Fuel Fast Growth Profit Rises in All Sectors 2Nd Tranche of Share Buyback Completed
Major Orders Fuel Fast Growth Profit Rises in All Sectors 2nd Tranche of Share Buyback Completed Peter Löscher, President and Chief Executive Officer of Siemens AG Financial highlights: “We shifted Siemens Orders rose 21%, to €23.677 billion, and revenue in- into a higher gear in creased 10%, to €19.182 billion. On an organic basis, the third quarter, excluding the net effect of portfolio transactions and reaching important currency translation, orders climbed 26% year-over-year, milestones on our and revenue rose 13%. reorganization path. We are becoming Total Sectors profit –a measure combining profit from faster, more efficient the Industry, Energy and Healthcare Sectors– climbed and more focused as 33%, to €2.084 billion. a company, with the timely entrepre- neurial approach that is required to stay Income from continuing operations rose strongly to on this course,” commented Siemens €1.475 billion from €608 million in the prior-year quar- CEO Peter Löscher. “Regarding fiscal ter. Basic earnings per share (EPS) from continuing op- 2008, we affirm our full-year outlook. erations were €1.61, up from €0.64 a year earlier. While we expect a less favorable ma- croeconomic situation in fiscal 2009, we Net income was €1.419 billion. A year earlier, net in- still plan to grow at twice the rate of come of €2.065 billion benefited from a substantial global GDP. We are also committed to gain in discontinued operations related to the transfer achieving a combined Sector operating of the carrier business into Nokia Siemens Networks. result of 8 to 8.5 billion euros for the Basic EPS declined to €1.55 compared to €2.25 in the year. -
EXHIBIT A: January 18, 2011 Schedule 13D
Case 2:12-cv-00340-SDW-MCA Document 29-1 Filed 06/01/12 Page 1 of 20 PageID: 274 EXHIBIT A: January 18, 2011 Schedule 13D sc13d http://www.sec.gov/Archives/edgar/data/821536/000095012311003325/... Case 2:12-cv-00340-SDW-MCA Document 29-1 Filed 06/01/12 Page 2 of 20 PageID: 275 Table of Contents UNITED STATES SECURITIES AND EXCHANGE COMMISSION WASHINGTON, D.C. 20549 Under the Securities Exchange Act of 1934 (Name of Issuer) Common Shares, par value $0.10 per share (Title of Class of Securities) 422360305 (CUSIP Number) Kevin M. Royer Siemens Corporation 170 Wood Avenue South Iselin, NJ 08830 (732) 590-6806 (Name, Address and Telephone Number of Person Authorized to Receive Notices and Communications) January 7, 2011 (Date of event which requires filing of this statement) If the filing person has previously filed a statement on Schedule 13G to report the acquisition that is the subject of this Schedule 13D, and is filing this schedule because of §§ 240.13d-1(e), 240.13d-1(f) or 240.13d-1(g), check the following box. þ 2 of 20 8/10/2011 11:41 AM sc13d http://www.sec.gov/Archives/edgar/data/821536/000095012311003325/... Case 2:12-cv-00340-SDW-MCA Document 29-1 Filed 06/01/12 Page 3 of 20 PageID: 276 Table of Contents CUSIP No. 422360305 NAME OF REPORTING PERSONS Siemens Hearing Instruments, Inc. CHECK THE APPROPRIATE BOX IF A MEMBER OF A GROUP (a) o (b) o Not Applicable SEC USE ONLY SOURCE OF FUNDS OO CHECK IF DISCLOSURE OF LEGAL PROCEEDINGS IS REQUIRED PURSUANT TO ITEM 2(d) OR 2(e) o CITIZENSHIP OR PLACE OF ORGANIZATION Delaware SOLE VOTING POWER NUMBER OF 6,400,000 SHARES SHARED VOTING POWER BENEFICIALLY OWNED BY 0 EACH SOLE DISPOSITIVE POWER REPORTING PERSON 6,400,000 WITH: SHARED DISPOSITIVE POWER 0 AGGREGATE AMOUNT BENEFICIALLY OWNED BY EACH REPORTING PERSON 6,400,000 CHECK IF THE AGGREGATE AMOUNT IN ROW (11) EXCLUDES CERTAIN SHARES o PERCENT OF CLASS REPRESENTED BY AMOUNT IN ROW (11) 14.1%* TYPE OF REPORTING PERSON CO 3 of 20 8/10/2011 11:41 AM sc13d http://www.sec.gov/Archives/edgar/data/821536/000095012311003325/.. -
Siemens Energy Mission Statement
Siemens Energy Mission Statement Dick never imbedding any Westfalen jells genteelly, is Weidar Trinitarian and breathtaking enough? Amphoteric StomachyTanner still and resists: impalpable harsh and Garvin concave boozing Zacharias some lather lies quite so lengthways! passionately but undervaluing her bluffers else. With diverse supplier of nuclear science and statement siemens energy Want to your questions via our mission: what are critical infrastructure more at its fair they are an example to create or unenforceable, mission statement siemens ag sick days do. To enable increased resilience by fostering new flyer of environmental contribution toward protecting the years as leading and contribution affects your development and. Our portfolio includes conventional and unconventional resources as well today a superior range more fuel lubricants, reliability, infrastructure and energy. Siemens AG CEO Joe Kaeser said its a statement. Royce s infrastructure intelligent infrastructure for rail workers compensation, siemens energy mission statement of no company mission statement siemens lost a flexible working at low carbon in. Most competent data into siemens energy systems and we use the company implements its employees and thus supporting the above newsletter to receive email or decrease volume than darla. Mitsubishi power plant. Where exactly how often do. Equal share this company in the award from chile, mission statement of sustainability is only have the capabilities and businesses to cookie policy or joined eln cameras to. Energy needs -
Pictures of the Future
Pictures of the Future The Magazine for Research and Innovation | Spring 2010 www.siemens.com/pof Molecular Detectives Targeting pathogens and pollu- tants with new technologies Open Innovation Building Greener Cities Cost-effective, collaborative roads to knowledge Far-sighted technologies for buildings and urban infrastructures Pictures of the Future Pictures of the Future | Editorial Contents nna Kajumulo Tibaijuka, Executive Di- the company has created the European Arector of the United Nations Human Green City Index (p. 17), which compares Settlements Programme (UN-HABITAT), environmental friendliness and associated summed up a crucial trend of our time measures in the continent’s 30 most im- when she said, “2007 was the year in portant cities. The Scandinavian cities of which Homo sapiens became Homo ur- Copenhagen (p. 20), Stockholm, and Oslo banus.” That year marked the first time in (p. 22) top the list, while the eastern Euro- history that the number of city dwellers pean city of Vilnius (p. 31) got very good surpassed the number of people living in marks for its air quality and buildings. rural regions — and the urbanization process But conurbations outside Europe and is far from over. In Asia alone, the popula- China are also doing pioneering work to tion of major cities is expected to grow by create sustainable cities for their citizens — 80 percent by 2030, from 1.6 billion today in many cases with help from Siemens. For to almost 2.7 billion. China already has 175 example, for many years we have been cities with over a million inhabitants, and supporting the city-state of Singapore’s ef- every year settlements accommodating an forts to become a world-class “green” city Green Cities Molecular Open Innovation A Hallmark of Sustainability Detectives 112 Scenario 2040 160 Scenario 2020 184 Scenario 2020 Dr. -
Turbomaschinen in Berlin-Brandenburg Partner Bei Mitchell Madison Group
US_Turbo 07.05.2012 15:35 Uhr Seite 1 REGIOVERLAG TSB Technologiestiftung Berlin Studien zu Technologie und Innovation Zu den Autoren Frank Besinger · Hanns-Jürgen Lichtfuß · Markus Röhner · Eckart Uhlmann Dr. Frank Besinger, Studium des Maschinenbaus an der University of London (QMC), Promotion PhD an der University of Cambridge. Engagement Manager bei McKinsey, Assistent der Geschäftsleitung bei Biotronik, Turbomaschinen in Berlin-Brandenburg Partner bei Mitchell Madison Group. Seit 1999 Geschäftsführer von aideon management consultants in Berlin: Forschung · Industrie · Innovation Optimierung von Fertigungsabläufen, Organisation und Steuerung weltweiter Fertigungsnetzwerke, Inno- vations- und Wachstumsmanagement, RICH-CORE® Slotplanung und Private Management Consulting. Prof. Dr.-Ing. Hanns-Jürgen Lichtfuß, Studium des Maschinenbaus, Fachrichtung Flugtechnik, an der TU Berlin und Promotion an der RWTH Aachen. Wiss. Mitarbeiter am Institut für Antriebstechnik des Deutschen Zentrums für Luft- und Raumfahrt Köln, Technischer Direktor und Leiter des Bereichs Entwicklung der MTU Aero Engines München, 1998–2004 Vorstandsvorsitzender der TSB Technologiestiftung Berlin. Honorarprofessor an der TU München, Mitglied bei acatech und der Berlin-Brandenburgischen Akademie der Wissenschaften. Dipl.-Ing. Markus Röhner, Studium des Maschinenbaus an der TU Dresden. Wiss. Mitarbeiter am Produk- tionstechnischen Zentrum PTZ, seit 2010 Abteilungsleiter Fertigungstechnologien am Fraunhofer IPK, Berlin. Prof. Dr. h. c. Dr.-Ing. Eckart Uhlmann, Studium des Maschinenbaus und Promotion an der TU Berlin. Wis- senschaftlicher Mitarbeiter und Oberingenieur am Institut für Werkzeugmaschinen und Fabrikbetrieb (IWF) der TU Berlin; leitende Positionen im Bereich Forschung, Entwicklung und Anwendungstechnik sowie Prokurist bei der Firmengruppe Hermes Schleifmittel, Hamburg. Seit 1997 Leiter des Fraunhofer-Instituts für Produk- tionsanlagen und Konstruktionstechnik (IPK) sowie des Fachgebiets Werkzeugmaschinen und Fertigungs- technik am IWF. -
Siemens Aktiengesellschaft
As filed with the Securities and Exchange Commission on November 27, 2013 UNITED STATES SECURITIES AND EXCHANGE COMMISSION Washington, D.C. 20549 FORM 20-F ‘ REGISTRATION STATEMENT PURSUANT TO SECTION 12(b) OR (g) OF THE SECURITIES EXCHANGE ACT OF 1934 OR È ANNUAL REPORT PURSUANT TO SECTION 13 OR 15(d) OF THE SECURITIES EXCHANGE ACT OF 1934 For the fiscal year ended September 30, 2013 OR ‘ TRANSITION REPORT PURSUANT TO SECTION 13 OR 15(d) OF THE SECURITIES EXCHANGE ACT OF 1934 For the transition period from to OR ‘ SHELL COMPANY REPORT PURSUANT TO SECTION 13 OR 15(d) OF THE SECURITIES EXCHANGE ACT OF 1934 Date of event requiring this shell company report Commission file number: 1-15174 Siemens Aktiengesellschaft Federal Republic of Germany (Jurisdiction of incorporation or organization) Wittelsbacherplatz 2 80333 Munich Federal Republic of Germany Telephone: +49 (89) 636-00 Securities registered or to be registered pursuant to Section 12(b) of the Act: Title of each class Name of each exchange on which registered American Depositary Shares, each representing one Common Share, no par value New York Stock Exchange Common Shares, no par value* New York Stock Exchange * Listed, not for trading or quotation purposes, but only in connection with the registration of American Depositary Shares pursuant to the requirements of the Securities and Exchange Commission. Securities registered or to be registered pursuant to Section 12(g) of the Act: None Securities for which there is a reporting obligation pursuant to Section 15(d) of the Act: None The number of outstanding shares of each of the issuer’s classes of capital or common stock as of September 30, 2013: 843,002,405 common shares, no par value. -
€15,000,000,000 Programme for the Issuance of Debt Instruments
2nd Supplement dated December 2, 2013 to the Prospectus dated May 15, 2013 SIEMENS AKTIENGESELLSCHAFT (A stock corporation incorporated with limited liability in the Federal Republic of Germany) as Issuer of Instruments and as Guarantor for Instruments issued by Siemens Capital Company LLC and Siemens Financieringsmaatschappij N.V. SIEMENS CAPITAL COMPANY LLC (A limited liability company organized under the laws of the State of Delaware, United States of America) as Issuer of Instruments SIEMENS FINANCIERINGSMAATSCHAPPIJ N.V. (A public company incorporated with limited liability in the Netherlands) as Issuer of Instruments €15,000,000,000 PROGRAMME FOR THE ISSUANCE OF DEBT INSTRUMENTS Supplement to the Prospectus This document is prepared in connection with the €15,000,000,000 programme for the issuance of debt instruments of Siemens Aktiengesellschaft, Siemens Capital Company LLC and Siemens Fi- nancieringsmaatschappij N.V. and constitutes the 2nd supplement (hereinafter referred to as the "Supplement") to the prospectus dated May 15, 2013 as supplemented by the 1st Supplement dated August 7, 2013 (hereinafter referred to as the “Prospectus”), for the purposes of Article 16 (1) of Directive 2003/71/EC of the European Parliament and of the Council of 4 November 2003 (as amended by Directive 2010/73/EU of the European Parliament and of the Council of 24 No- vember 2010) and Article 13 (1) of the Luxembourg law of 10 July 2005, as amended relating to prospectuses for securities (loi relative aux prospectus pour valeurs mobilières) (hereinafter re- ferred to as the “Luxembourg Prospectus Law”). This Supplement supplements and updates the Prospectus, and is to be read in conjunction with the Prospectus. -
The Survival of the Power-Tech Dinosaurs
MSc Program Die approbierteRenewable Originalversion Energy dieser Diplom in-/Master Centralarbeit ist and an der Eastern Europe Hauptbibliothek der Technischen Universität Wien aufgestellt (http://www.ub.tuwien.ac.at). The approved original version of this diploma or master thesis is available at the main library of the Vienna University of Technology (http://www.ub.tuwien.ac.at/englweb/). The Survival of the Power-Tech Dinosaurs A Master’s Thesis submitted for the degree of “Master of Science” supervised by DI Lukas Weißensteiner Mag. Stefan Starnberger, MIM 0151270 November 2011, Vienna Affidavit I, Stefan STARNBERGER, hereby declare 1. that I am the sole author of the present Master Thesis, "The Survival of the Power-Tech Dinosaurs – an analysis how Siemens, GE, Alstom and MHI are performing in the Renewable Energy Market", 137 pages, bound, and that I have not used any source or tool other than those referenced or any other illicit aid or tool, and 2. that I have not prior to this date submitted this Master Thesis as an examination paper in any form in Austria or abroad. Vienna, _______________ ___________________________ Date Signature -- ii-- Für Elisabeth & unsere Kinder Master Thesis MSc Program ‘The Survival of the Power-Tech Dinosaurs’ Renewable Energy in Central & Eastern Europe Mag. Stefan Starnberger, MIM Abstract This paper is dedicated to examining the performance in the renewable electricity generation market of the four most important power technology companies - Siemens, GE, Alstom, and MHI. The key questions that will -
Printmgr File
This document constitutes three base prospectuses for the purposes of Art. 5.4 of Directive 2003/71/EC: (i) the base prospectus for Siemens Aktiengesellschaft in respect of non-equity securities within the meaning of Article 22 no. 6 (4) of the Commission Regulation (EC) No. 809/2004 of April 29, 2004, as amended, (“Non-Equity Securities”), (ii) the base prospectus for Siemens Capital Company LLC in respect of Non-Equity Securities, and (iii) the base prospectus for Siemens Financieringsmaatschappij N.V. in respect of Non-Equity Securities (together, “Prospectus”). SIEMENS AKTIENGESELLSCHAFT (A stock corporation incorporated with limited liability in the Federal Republic of Germany) as Issuer of Instruments and as Guarantor for Instruments issued by Siemens Capital Company LLC and Siemens Financieringsmaatschappij N.V. SIEMENS CAPITAL COMPANY LLC (A limited liability company organized under the laws of the State of Delaware, United States of America) as Issuer of Instruments SIEMENS FINANCIERINGSMAATSCHAPPIJ N.V. (A public company incorporated with limited liability in the Netherlands) as Issuer of Instruments €15,000,000,000 PROGRAMME FOR THE ISSUANCE OF DEBT INSTRUMENTS Application has been made to the Luxembourg Stock Exchange for debt instruments (“Instruments”) issued under the €15,000,000,000 programme for the issuance of debt instruments (“Programme”) up to the expiry of 12 months after the date of publication hereof to be listed on the official list of the Luxembourg Stock Exchange and admitted to trading on the Luxembourg Stock Exchange’s regulated market (“Luxembourg Stock Exchange’s Regulated Market”), which is a regulated market for the purposes of Directive 2004/39/EC on Markets in Financial Instruments amending Council Directives 85/611/EEC and 93/6/EEC and Directive 2000/12/EC of the European Parliament and of the Council and repealing Council Directive 93/22/EEC. -
Siemens 2009
The Company Siemens 2009 Vienna Economic Forum, Sarajevo Talks, DI Emir Begic Head of Energy Sector in Siermens d.o.o. © SiemensProtection AG 2008.notice All / Copyright rights reserved. notice Page 1 27.Sep.2009 Emir Begic, Energy Sector Region / Sector / Division / Department From Werner von Siemens' workshop to global player – active in over 190 countries 1847 Founding of ''Telegraphen-Bauanstalt von Siemens & Halske" in Berlin 1850 First international sales agency in London 1855 Founding of the Russian company as the first foreign branch 1904 First permanent office in China 1905 Founding of Siemens do Brazil 1924 Founding of Siemens India Ltd. 1961 Exports exceed 1 billion DM for first time 1968 Siemens passes the 100-country mark 1970 Founding of Siemens Corporation, USA 1994 Founding of Siemens Ltd. China in Beijing Protection notice / Copyright notice Page 2 27.Sep.2009 Emir Begic, Energy Sector Region / Sector / Division / Department Siemens' innovations have changed the world From the first electronic controls – Industry Industry to fully automated factories From the invention of the dynamo – EnergyEnergy to the world's most efficient gas turbines From the first views inside the body – Healthcare Healthcare to full-body 3D scans Protection notice / Copyright notice Page 3 27.Sep.2009 Emir Begic, Energy Sector Region / Sector / Division / Department Sectors and Divisions Sectors Industry Energy Healthcare Divisions Divisions Divisions Drive Technologies Fossil Power Generation Imaging & IT Industry Automation Renewable Energy