Design Criteria for the Floating Walkways and Pontoons Considering the Extreme Climatic Conditions
Total Page:16
File Type:pdf, Size:1020Kb
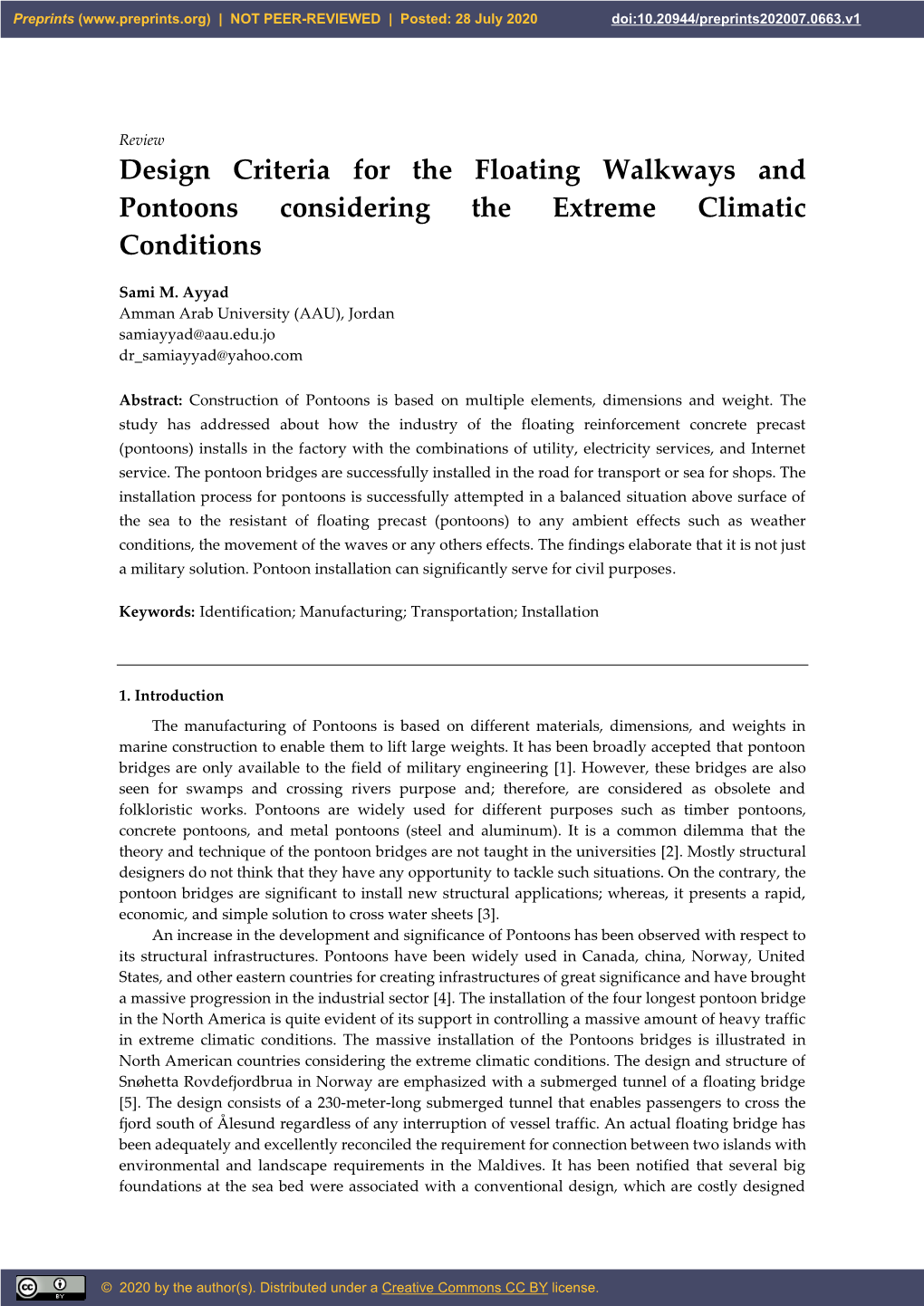
Load more
Recommended publications
-
Drawbridge Committee Notes from December 2, 2005 1 of 1
Lagoon Pond Drawbridge Committee Notes from Decemer 2, 2005 Present: Melinda Loberg and Mark London (Lagoon Pond Committee) and Steve McLaughlin (MassHighway) Location: MassHighway Offices, Boston Existing Bridge - As District 5 indicated, the Bridge Section is reviewing the Lichtenstein report so they can determine which preventative repairs are warranted, if any. Temporary Bridge - They are still awaiting the Coast Guard permit as well as the third, and hopefully final, review of the 100% design plans by the bridge and highway sections. He expects to advertise for construction in January or February, assuming the permit and approvals are forthcoming. - If it were advertised, say, on February 15, they would open bids about April 1, would award the contract about June 1, and would probably start construction in mid-June. - The completion date for the bridge is very dependent upon the ability to award the contract per the time-line above. Any delay could cause construction to be delayed up to one year. With the construction start in mid-June, the completion could take between one year and 18 months depending upon whether we get an accelerated schedule approved. - The cost estimate is now $6,026,130 not including the cost of securing the right of way from the owners of the house, but including about 10% for demolition of the existing bridge. Most of this will be for construction of foundations, transportation of materials, and labor. - The temporary bridge will likely be mostly or all newly built. MassHighway will own the structure and can reuse it elsewhere. - They believe that the present proposal for bikes and pedestrians are safe. -
Numerical Modelling and Dynamic Response Analysis of Curved Floating Bridges with a Small Rise-Span Ratio
Journal of Marine Science and Engineering Article Numerical Modelling and Dynamic Response Analysis of Curved Floating Bridges with a Small Rise-Span Ratio Ling Wan 1,2,3, Dongqi Jiang 4,* and Jian Dai 5 1 The State Key Laboratory of Hydraulic Engineering Simulation and Safety, School of Civil Engineering, Tianjin University, Tianjin 300072, China 2 Faculty of Science Agriculture and Engineering, Newcastle University, Singapore 599493, Singapore; [email protected] 3 Newcastle Research & Innovation Institute Pte Ltd. (NewRIIS), Singapore 609607, Singapore 4 Department of Civil Engineering, School of Science, Nanjing University of Science and Technology, Nanjing 210094, China 5 Department of Marine Technology, Norwegian University of Science and Technology, 7491 Trondheim, Norway; [email protected] * Correspondence: [email protected] Received: 9 May 2020; Accepted: 17 June 2020; Published: 24 June 2020 Abstract: As a potential option for transportation applications in coastal areas, curved floating bridges with a same small specified rise to span ratio of 0.134, supported by multiple pontoons, are investigated in this paper. Two conceptual curved bridges are proposed following a circular arc shape with different span lengths (500 and 1000 m). Both bridges are end-connected to the shoreline without any underwater mooring system, while the end-connections can be either all six degrees of freedom (D.O.F) fixed or two rotational D.O.F released. Eigen value analysis is carried out to identify the modal parameters of the floating bridge system. Static and dynamic analysis under extreme environmental conditions are performed to study the pontoon motions as well as structural responses of the bridge deck. -
7Th ROMAN BRIDGES on the LOWER PART of the DANUBE
th 7 INTERNATIONAL CONFERENCE Contemporary achievements in civil engineering 23-24. April 2019. Subotica, SERBIA ROMAN BRIDGES ON THE LOWER PART OF THE DANUBE Isabella Floroni Andreia-Iulia Juravle UDK: 904:624.21"652" DOI: 10.14415/konferencijaGFS2019.015 Summary: The purpose of the paper is to present the Roman bridges built across the Romanian natural border, the Danube, during the Roman Empire expansion. Some of these are less known than the famous Traian’s bridge in Drobeta Turnu Severin. The construction of bridges on the lower part of the Danube showed the importance of conquering and administrating the ancient province of Dacia. The remaining evidences prove the technical solutions used by the Roman architects at a time when public works had developed. Keywords: Danube bridges, pontoon bridge, Bridge of Constantine the Great, Columna Traiana 1. INTRODUCTION The Danube1 was once a long-standing frontier of the Roman Empire, and today flows through 10 countries, more than any other river in the world. Originating in Germany, the Danube flows southeast for 2,850 km, passing through or bordering Austria, Slovakia, Hungary, Croatia, Serbia, Romania, Bulgaria, Moldova and Ukraine before draining into the Black Sea. Romania has the longest access to the river, around 1075 km, of which 225 km on Romanian territory exclusively. | CONFERENCE PROCEEDINGS INTERNATIONAL CONFERENCE (2019) | 189 7. МЕЂУНАРОДНА КОНФЕРЕНЦИЈА Савремена достигнућа у грађевинарству 23-24. април 2019. Суботица, СРБИЈА Fig. 1 Map of the main course of the Danube During the Roman Empire many wooden or masonry bridges were built, some of which lasted longer, other designed for ephemeral military expeditions. -
Static Behaviors of a Long-Span Cable-Stayed Bridge with a Floating Tower Under Dead Loads
Journal of Marine Science and Engineering Article Static Behaviors of a Long-Span Cable-Stayed Bridge with a Floating Tower under Dead Loads Minseo Jang 1, Yunwoo Lee 1, Deokhee Won 2 , Young-Jong Kang 1 and Seungjun Kim 1,* 1 School of Civil, Environmental and Architectural Engineering, Korea University, Seoul 02841, Korea; [email protected] (M.J.); [email protected] (Y.L.); [email protected] (Y.-J.K.) 2 Coastal and Ocean Engineering Division, Korea Institute of Ocean Science and Technology, Busan 49111, Korea; [email protected] * Correspondence: [email protected]; Tel.: +82-2-3290-4868 Received: 14 September 2020; Accepted: 15 October 2020; Published: 20 October 2020 Abstract: Owing to the structural characteristics of floating-type structures, they can be effectively applied to overcome the limitation of conventional long-span bridges in deep water. Unlike cable-supported bridges with fixed towers, floating cable-supported bridges show relatively large displacements and rotations under the same load because of floating towers; moreover, the difference in the support stiffness causes differences in the behavior of the superstructures. In addition, the risk of overturning is greater than in conventional floating offshore structures because the center of gravity of the tower is located above the buoyancy center of the floater. A floating cable-supported bridge in which the tether supports the floating main tower is directly influenced by the tether arrangement, which is very important for the stability of the entire structure. In this study, according to the inclined tether arrangement, the outer diameter of the floater, and the buoyancy vertical load ratio (BVR), the static behavioral characteristics of the long-span cable-stayed bridges with floating tower are evaluated through nonlinear finite-element analysis. -
Bridges Connect…
BRIDGES CONNECT… GULIZAR OZYURT TCCE 49th ECCE General Meeting 22 – 23 May 2009 Ljubljana, Slovenia “the human being is the connecting creature who must always separate and can not connect without separating…first conceive intellectually of the merely indifferent existence of the two river banks as something separated in order to connect them by means of a bridge.” Georg Simmel • Death and Bridge • Building Bridges, Burning Bridges • Intercultural cooperation as a Bridge • Bridge connecting opposite political parties: coalition • In a dream: to make peace with others for mutual benefits • Soccer: a bridge that only men shall cross* Physically… • As a potent historical and cultural icon. • As visual proxies in popular culture and a variety of commercial media for their respective cities • Bridges inspire …paintings, songs and films and creative writings… BOSPHORUS BRIDGE First Pontoon Bridge • Constructed by architect Mandrocles from Greek island Samos by the order of Persian emperor Darius I around 500BC. • First pontoon Bridge of history over 1 km long with some 200 ships supporting roadway • Army of 70000 crossed over Europe when campaigning against Scythia. Leonardo’s Bridge • In 1502 Leonardo da Vinci did a simple drawing of a graceful bridge with a single span of approximately 240-meters. Da Vinci designed the Bridge as part of a civil engineering project for Sultan Bajazet II. The bridge was to span the Golden Horn, an inlet at the mouth of the Bosphorus River in what is now Turkey. The Bridge was never built. • A project suBmitted to Sultan Abdulhamit on NovemBer,1900. • The idea first come up Before the ottoman- Russian war in 1877- 1878 and gained significance after the concessions granted to Germany for the Baghdad railway. -
Historic Bridges Historic Bridges 397 Survey Report for Historic Highway Bridges
6 HISTORIC BRIDGES HISTORIC BRIDGES 397 SURVEY REPORT FOR HISTORIC HIGHWAY BRIDGES HIGHWAY FOR HISTORIC REPORT SURVEY 1901-1920 PERIOD By the turn of the century, bridge design, as a profession, had sufficiently advanced that builders ceased erecting several of the less efficient truss designs such as the Bowstring, Double Intersection Pratt, or Baltimore Petit trusses. Also, the formation of the American Bridge Company in 1901 eliminated many small bridge companies that had been scrambling for recognition through unique truss designs or patented features. Thus, after the turn of the century, builders most frequently erected the Warren truss and Pratt derivatives (Pratt, Parker, Camelback). In addition, builders began to erect concrete arch bridges in Tennessee. During this period, counties chose to build the traditional closed spandrel design that visually evoked the form of the masonry arch. Floods in 1902 and 1903 that destroyed many bridges in the state resulted in counties going into debt to undertake several bridge replacement projects. One of the most concentrated bridge building periods at a county level occurred shortly before World War I as a result of legislation the state passed in 1915 that allowed counties to pass bond issues for road and bridge construction. Consequently, several counties initiated large road construction projects, for example, Anderson County (#87, 01-A0088-03.53) and Unicoi County (#89, 86-A0068- 00.89). This would be the last period that the county governments were the most dominant force in road and bridge construction. This change in leadership occurred due to the creation of the Tennessee State Highway Department in 1915 and the passage of the Federal Aid Highway Act of 1916. -
Assessment of the Dynamic Response of a Floating Pontoon Bridge with A
Assessment of the dynamic response of a floating pontoon bridge with a fiber reinforced polymer superstructure C.E.M. Heuberger Assessment of the dynamic response of a floating pontoon bridge with a fiber reinforced polymer superstructure by C.E.M. Heuberger to obtain the degree of Master of Science in Civil Engineering - Hydraulic Engineering at the Delft University of Technology to be defended publicly on Thursday July 5, 2018 at 10:30 a.m. Student number: 4166272 Project duration: September 2017 - July 2018 Thesis committee: Prof. Dr. Ir. S.N. Jonkman Delft University of Technology Dr. Ir. D.J. Peters Delft University of Technology & Royal HaskoningDHV Dr. Ir. A. Jarquin Laguna Delft University of Technology Ir. E. Tromp Royal HaskoningDHV Ir. Y. Wang Royal HaskoningDHV Cover photo by S. Hansen, Bergsøysundbrua An electronic version of this thesis is available at http://repository.tudelft.nl/. Preface This thesis is the final part of my master program of Hydraulic Engineering at Delft University of Technology. My thesis is titled: ”Assessment of the dynamic response of a floating pontoon bridge with a fiber reinforced polymer superstructure”. Royal HaskoningDHV offered me the opportunity to work on this subject, for which I am very grateful. They provided me with the means and the motivation to complete this research. Many people assisted me during the process of writing this thesis. Without their help, this report would not be lying in front of you. First and foremost I would like to express my gratitude towards my graduation committee. I would like to thank Bas Jonkman for chairing the committee. -
Connecticut River Bridges, Rev
NEW HAMPSHIRE DIVISION OF HISTORICAL RESOURCES State of New Hampshire, Department of Cultural Resources 603-271-3483 19 Pillsbury Street, 2 nd floor, Concord NH 03301-3570 603-271-3558 Voice/ TDD ACCESS: RELAY NH 1-800-735-2964 FAX 603-271-3433 http://www.nh.gov/nhdhr [email protected] Garvin--Connecticut River Bridges, Rev. 7/2009 LIST OF HIGHWAY BRIDGES ON THE CONNECTICUT RIVER BETWEEN VERMONT AND NEW HAMPSHIRE BY 1906, WITH NOTES ON LATER SPANS The basic information in this list was obtained from Report of the Bridge Commissioners of the State of New Hampshire to the Legislature, Dec. 31, 1906 (Manchester, N.H.: John B. Clarke Company, 1906) Existing bridges are identified by New Hampshire Department of Transportation bridge coordinates, as “042/044.” [Bridges described in italics had disappeared by 1906.] 1. Hinsdale to Brattleboro, Vermont. The first bridge was built in 1804 by the Hinsdale Bridge and Sixth New Hampshire Turnpike Corporation, chartered in 1802. Frederick J. Wood in his The Turnpikes of New England (1919) says that this company “appears to have been primarily a toll-bridge corporation, although it had authority to build about ten miles of turnpike through Hinsdale and Winchester to connect with a branch of the Fifth Massachusetts [Turnpike] which was built to the state line prior to 1806.” The Hinsdale Bridge was apparently replaced several times. Hinsdale, New Hampshire (Hinsdale, N.H.: Bicentennial Committee [1976]) says that bridges here have “been carried away, by floods and ice, on the average of once in every ten years.” The corporate name was shortened to “Hinsdale Bridge Corporation” in 1853, probably reflecting the relinquishment of any turnpike road the corporation had built. -
Design of Floating Bridge Cross Over
International Research Journal of Engineering and Technology (IRJET) e-ISSN: 2395-0056 Volume: 04 Issue: 12 | Dec-2017 www.irjet.net p-ISSN: 2395-0072 DESIGN OF FLOATING BRIDGE CROSS OVER M. Hari Sathish Kumar1, E. Saravanan2, S. Manikandan3, S. Akash Kumar 4 1Assistant Professor, Department of Civil Engineering, PERI Institute of Technology, Chennai 48. 2,3,4Student, Department of Civil Engineering, PERI Institute of Technology, Chennai 48 ----------------------------------------------------------------------------------------***---------------------------------------------------------------------------------------- Abstract - Economy in construction is the ultimate need impractical.As we propose to build a bridge across a for today, so we go for suitable structures to fit the natural drainage like rivers or some obstruction, we have purpose. The bridge uses floats (floating concrete) to to consider the height of piers constructed above the support a continuous or separate deck for vehicle and ground level as well as below the ground level as a part of pedestrian travel. It is used in the area where there is not foundation. When we lay piers for bridges crossing deeper feasible to suspend a bridge from anchored piers and also rivers then the height of piers would be very large. the area which has large deep sea bed. Pier-less bridge are not new to this world. During the Cholas period for their Even if the river bed is of soft bed rock then the depth invasion across rivers, they made use of trained elephants up to which the piers have to be laid under the ground that swim on the surface, over which they transported all level as foundation is also so high. -
SR 520 Pontoon Construction Project
WSDOT SR520 PROGRAM Pontoon Construction Project Expert Panel Report, Phase 2 Submitted to WSDOT by the Expert Panel February 18th 2013 . THE SR520 EXPERT REVIEW PANEL: Chair: John Reilly, Panel: Dr. Neil Hawkins, Dr. John Clark Mr. Tom Sherman, Mr. Mark Leonard Mr. Stephen Tatro Panel Members’ – Background (for details, See Appendix E) The Expert Panel members were selected for their expertise in the design and construction of complex concrete and pre-stressed/post-tensioned1 concrete structures. More than one member was required to have experience in floating bridges. An understanding of concrete materials and technologies was required. Current Expert Panel members are: Dr. Neil M. Hawkins, Ph.D., Dist. M. ASCE, Hon. M. ACI, Professor Emeritus, University of Illinois, and former chair of the Civil Engineering Department, University of Washington, specialist in reinforced and prestressed concrete. Dr. John H. Clark, P.E., Ph. D., a consultant for the design and construction of long-span bridges and heavy structures, including pre-stressed concrete. Mr. Tom Sherman, specialist in floating bridge design and construction, TES Enterprises Mr. Mark Leonard, FHWA Resource Center, former Bridge Engineer for the Colorado Department of Transportation. Mr. Stephen B. Tatro, consultant specializing in evaluation, testing, design, and construction of concrete structures and materials. The panel is chaired by Mr. John Reilly, P.E., C.P. Eng., with experience in major project management, contracting and delivery, risk assessment / mitigation and prestressed concrete design. Summary resumes of the Panel members can be found in Appendix E 1 Prestressing refers to beneficial stressing of the concrete structures before application of in-service loads. -
Building Our Bridge to Fun Presentation
Building Our Bridge to Fun! Civil Engineering in the Classroom Main Goals of this Activity • Learn about how bridges are used and why we need them • Identify forces acting on a bridge • Hands-on activity: build two type of bridges (with two type of materials) • Measure deflection of a span using LEGO ultrasonic sensor • Gather data (load vs. deflection) Introduction What is a bridge? Why do we need build bridges? Water supply Crossing rivers Traffic or water bodies 2 Engineering for bridges Construction Materials: -Concrete -Steel -Wood -Stone -Brick Bridges are structures to provide passage over water, roadways, and more! 3 Engineering for bridges: History Primitive People: Roman Empire—First Great ▪ Logs Bridge Builders ▪ Slabs of Rocks ▪ Timber Truss Bridges ▪ Intertwined Vines or Ropes ▪ Masonry Arch Bridges Nineteenth Century Europeans ▪ Modern Long Bridges ▪ Followed Roman Empire style until ▪ Moveable Bridges iron and steel was used 4 Engineering for bridges: Primitive Bridges Rock Bridges Rope Bridges Log Bridges Engineering for bridges: Loads Primary Loads acting in a bridge Weight of the bridge DEAD LOAD Traffic: cars, trucks, people Wind, snow LIVE LOAD Dynamic: earthquake and vibrations 6 Engineering for bridges: Primary forces Tension: magnitude of the pulling force that acts to lengthen an object, usually by a string, cable, or chain. Compression: a pushing force that acts to shorten the thing that it is acting on. Opposite to tension. 7 Engineering for bridges: Primary forces Demo: Use a sponge to represent a beam. When loaded with weight, the divots (holes) on top _________close and the divots (holes) on bottom _________open Conclusion: compression tension The top of a beam experiences compression__________. -
Article: Types of Movable Bridges and Their Construction Details I
Article: Types of Movable Bridges and their Construction Details _____________________________________________________________ Introduction Movable bridges are designed and constructed to change its position and occasionally its shapes to permit the passage of vessels and boats in the waterway. This type of bridge is generally cost effective since the utilization of long approaches and high piers are not required. When the waterway is opened to vessels and ships, traffics over the bridge would be stopped and vice-versa. Moveable bridge is a bridge that can change position (and even shape in some cases) to allow for passage of boats below. This has a lower cost of building because it has no high piers and long approaches but its use stops the road traffic when the bridge is open for river traffic. The oldest know movable bridge was built in the 2nd millennium BC in the ancient Egypt. History also knows for one early movable bridge built in Chaldea in the Middle East in 6th century BC. Since then they were almost forgotten until Middle Ages when they again appeared in Europe. Leonardo da Vinci designed and built designed and built bascule bridges in 15th century. He also made designs and built models of swing and a retractable bridges. Industrial revolution allowed for new technologies like mass-produced steel and powerful machines and it is no surprise that new types of modern movable bridges appeared in 19th century. They are built even today but many movable bridges that are still in use in United States are built in early 20th century. In time, some of them are repaired with lighter materials and their gears are replaced with hydraulics.