1 High 2,3-Butanediol Production 1 From
Total Page:16
File Type:pdf, Size:1020Kb
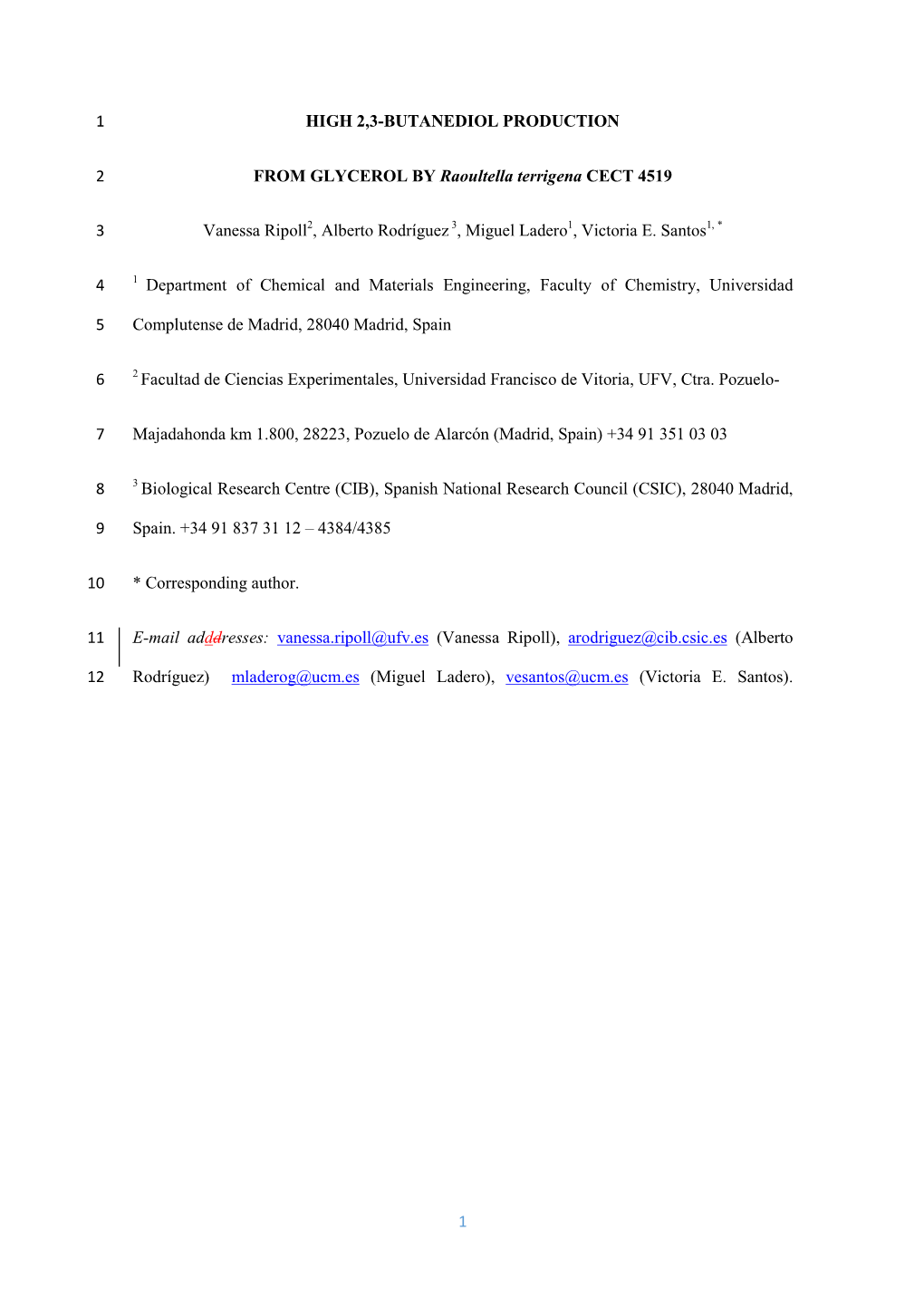
Load more
Recommended publications
-
Pseudomonas Spp. and Other Psychrotrophic
Pesq. Vet. Bras. 39(10):807-815, October 2019 DOI: 10.1590/1678-5150-PVB-6037 Original Article Livestock Diseases ISSN 0100-736X (Print) ISSN 1678-5150 (Online) PVB-6037 LD Pseudomonas spp. and other psychrotrophic microorganisms in inspected and non-inspected Brazilian Minas Frescal cheese: proteolytic, lipolytic and AprX production potential1 Pedro I. Teider Junior2, José C. Ribeiro Júnior3* , Eric H. Ossugui2, Ronaldo Tamanini2, Juliane Ribeiro2, Gislaine A. Santos2 2 and Vanerli Beloti2 , Amauri A. Alfieri ABSTRACT.- Teider Junior P.I., Ribeiro Júnior J.C., Ossugui E.H., Tamanini R., Ribeiro J., Santos G.A., Pseudomonas spp. and other psychrotrophic microorganisms Pseudomonas spp. and other psychrotrophic in inspected and non-inspected Brazilian Minas Frescal cheese: proteolytic, lipolytic andAlfieri AprX A.A. production& Beloti V. 2019. potential . Pesquisa Veterinária Brasileira 39(10):807-815. Instituto microorganisms in inspected and non- Nacional de Ciência e Tecnologia para a Cadeia Produtiva do Leite, Universidade Estadual de inspected Brazilian Minas Frescal cheese: Londrina, Rodovia Celso Garcia Cid PR-445 Km 380, Cx. Postal 10.011, Campus Universitário, proteolytic, lipolytic and AprX production Londrina, PR 86057-970, Brazil. E-mail: [email protected] The most consumed cheese in Brazil, Minas Frescal cheese (MFC) is highly susceptible to potential microbial contamination and clandestine production and commercialization can pose a risk to consumer health. The storage of this fresh product under refrigeration, although more appropriate, may favor the growth of spoilage psychrotrophic bacteria. The objective of this [Pseudomonas spp. e outros micro-organismos study was to quantify and compare Pseudomonas spp. and other psychrotrophic bacteria in inspected and non-inspected MFC samples, evaluate their lipolytic and proteolytic activities and e não inspecionados: potencial proteolítico, lipolítico e their metalloprotease production potentials. -
Neonatal Septicemia Caused by a Rare Pathogen: Raoultella Planticola
Chen et al. BMC Infectious Diseases (2020) 20:676 https://doi.org/10.1186/s12879-020-05409-5 CASE REPORT Open Access Neonatal septicemia caused by a rare pathogen: Raoultella planticola - a report of four cases Xianrui Chen1,2,3, Shaoqing Guo1,2,3* , Dengli Liu1,2,3 and Meizhen Zhong1,2,3 Abstract Background: Raoultella planticola(R.planticola) is a very rare opportunistic pathogen and sometimes even associated with fatal infection in pediatric cases. Recently,the emergence of carbapenem resistance strains are constantly being reported and a growing source of concern for pediatricians. Case presentation: We reported 4 cases of neonatal septicemia caused by Raoultella planticola. Their gestational age was 211 to 269 days, and their birth weight was 1490 to 3000 g.The R. planticola infections were detected on the 9th to 27th day after hospitalizationandoccuredbetweenMayandJune.They clinically manifested as poor mental response, recurrent cyanosis, apnea, decreased heart rate and blood oxygen, recurrent jaundice, fever or nonelevation of body temperature. The C-reactive protein and procalcitonin were elevated at significantly in the initial phase of the infection,and they had leukocytosis or leukopenia. Prior to R.planticola infection,all of them recevied at least one broad-spectrum antibiotic for 7- 27d.All the R.planticola strains detected were only sensitive to amikacin, but resistant to other groups of drugs: cephalosporins (such as cefazolin, ceftetan,etc) and penicillins (such as ampicillin-sulbactam,piperacillin, etc),and even developed resistance to carbapenem. All the infants were clinically cured and discharged with overall good prognosis. Conclusion: Neonatal septicemia caused by Raoultella planticola mostly occured in hot and humid summer, which lack specific clinical manifestations. -
Identification of Raoultella Terrigena As a Rare Causative Agent of Subungual Abscess Based on 16S Rrna and Housekeeping Gene Sequencing
Hindawi Publishing Corporation Canadian Journal of Infectious Diseases and Medical Microbiology Volume 2016, Article ID 3879635, 4 pages http://dx.doi.org/10.1155/2016/3879635 Case Report Identification of Raoultella terrigena as a Rare Causative Agent of Subungual Abscess Based on 16S rRNA and Housekeeping Gene Sequencing Yu Wang,1 Xiawei Jiang,1 Zemin Xu,2 Chaoqun Ying,1 Wei Yu,1 and Yonghong Xiao1 1 State Key Laboratory for Diagnosis and Treatment of Infectious Diseases, Collaborative Innovation Center for Diagnosis and Treatment of Infectious Diseases, The First Affiliated Hospital, School of Medicine, Zhejiang University, Hangzhou, China 2Ningbo Institute of Microcirculation and Henbane, Ningbo, China Correspondence should be addressed to Yonghong Xiao; [email protected] Received 8 October 2015; Revised 28 April 2016; Accepted 15 May 2016 Academic Editor: Maurizio Sanguinetti Copyright © 2016 Yu Wang et al. This is an open access article distributed under the Creative Commons Attribution License, which permits unrestricted use, distribution, and reproduction in any medium, provided the original work is properly cited. A 63-year-old-man was admitted to our hospital with severe subungual abscess. Bacteria were isolated from pus samples, and an inconsistent identification was shown by VITEK 2 system and MALDI-TOF mass spectrometry as Raoultella planticola and Raoultella terrigena, respectively. Molecular identification by 16S rRNA sequencing suggested that the isolate is R. terrigena,and this was further demonstrated by sequencing three housekeeping genes (rpoB, gyrA,andparC) with phylogenetic analysis. To our knowledge, this is the first report of subungual abscess caused by R. terrigena, a rare case of human infection due to soil bacterium. -
CTX-M-9 Group ESBL-Producing Raoultella Planticola Nosocomial
Tufa et al. Ann Clin Microbiol Antimicrob (2020) 19:36 https://doi.org/10.1186/s12941-020-00380-0 Annals of Clinical Microbiology and Antimicrobials CASE REPORT Open Access CTX-M-9 group ESBL-producing Raoultella planticola nosocomial infection: frst report from sub-Saharan Africa Tafese Beyene Tufa1,2,3*† , Andre Fuchs2,3†, Torsten Feldt2,3, Desalegn Tadesse Galata1, Colin R. Mackenzie4, Klaus Pfefer4 and Dieter Häussinger2,3 Abstract Background: Raoultella are Gram-negative rod-shaped aerobic bacteria which grow in water and soil. They mostly cause nosocomial infections associated with surgical procedures. This case study is the frst report of a Raoultella infec- tion in Africa. Case presentation We report a case of a surgical site infection (SSI) caused by Raoultella planticola which developed after caesarean sec- tion (CS) and surgery for secondary small bowel obstruction. The patient became febrile with neutrophilia (19,157/µL) 4 days after laparotomy and started to develop clinical signs of a SSI on the 8 th day after laparotomy. The patient con- tinued to be febrile and became critically ill despite empirical treatment with ceftriaxone and vancomycin. Raoultella species with extended antimicrobial resistance (AMR) carrying the CTX-M-9 β-lactamase was isolated from the wound discharge. Considering the antimicrobial susceptibility test, ceftriaxone was replaced by ceftazidime. The patient recovered and could be discharged on day 29 after CS. Conclusions: Raoultella planticola was isolated from an infected surgical site after repeated abdominal surgery. Due to the infection the patient’s stay in the hospital was prolonged for a total of 4 weeks. It is noted that patients under- going surgical and prolonged inpatient treatment are at risk for infections caused by Raoultella. -
Comparison Between Vitek MS, Bruker Biotyper, Vitek2, and API20E for Differentiation of Species of the Genus Raoultella
European Journal of Clinical Microbiology & Infectious Diseases (2019) 38:467–470 https://doi.org/10.1007/s10096-018-03444-4 ORIGINAL ARTICLE Comparison between Vitek MS, Bruker Biotyper, Vitek2, and API20E for differentiation of species of the genus Raoultella Carlos Ruiz de Alegría Puig1 & Marina Fernández Torres1 & Eduardo Marfil-Pérez2,3 & María Isabel Rodríguez Ferández1 & Manuel Causse Del Río2,3 & Jesús Agüero Balbín1,4 & Luis Martínez-Martínez2,3,5 Received: 11 September 2018 /Accepted: 29 November 2018 /Published online: 25 January 2019 # Springer-Verlag GmbH Germany, part of Springer Nature 2019 Abstract Rapid and reliable identification of microorganisms in the clinical laboratory is essential for an early and accurate diagnosis guiding timely therapy. However, conventional methods are sometimes unreliable and show controversial outcomes. Matrix- assisted laser desorption/ionization time-of-flight mass spectrometry (MALDI-TOF MS) has been reported as a rapid and reliable method for identification of bacteria and fungi isolated from clinical samples. Members of the genus Raoultella are increasingly recognized as clinically relevant. There are difficulties in their identification at the species level since sequencing the 16S rRNA or the rpoB genes does not show conclusive results. The aim of this study has been to compare two MALDI-TOF MS systems (Vitek MS and Bruker Biotyper) with Vitek2 and API20E systems for differentiation of Raoultella species. A collection of 97 clinical isolates of Raoultella species was identified with Vitek MS, in parallel with Vitek2 and API, and finally with Bruker Biotyper. Among the two most widely used MALDI-TOF MS platforms, results obtained with Vitek MS were slightly superior to those obtained with the Bruker Biotyper system, with sensitivities and specificities of 98.9/57.9% and 98.8/37.0%, respectively. -
Neonatal Enteral Feeding Tubes As Loci for Colonisation by Members of The
BMC Infectious Diseases BioMed Central Research article Open Access Neonatal enteral feeding tubes as loci for colonisation by members of the Enterobacteriaceae Edward Hurrell1, Eva Kucerova1, Michael Loughlin1, Juncal Caubilla-Barron1, Anthony Hilton2, Richard Armstrong2, Craig Smith3, Judith Grant4, Shiu Shoo4 and Stephen Forsythe*1 Address: 1School of Science and Technology, Nottingham Trent University, Clifton Lane, Nottingham, NG11 8NS, UK , 2Life and Health Sciences, Aston University, Aston Triangle, Birmingham, B4 7ET, UK , 3Nottingham City Hospital, Nottingham, NG5 1PB, UK and 4Queens Medical Centre, Nottingham, NG7 2UH, UK Email: Edward Hurrell - [email protected]; Eva Kucerova - [email protected]; Michael Loughlin - [email protected]; Juncal Caubilla-Barron - [email protected]; Anthony Hilton - [email protected]; Richard Armstrong - [email protected]; Craig Smith - [email protected]; Judith Grant - [email protected]; Shiu Shoo - [email protected]; Stephen Forsythe* - [email protected] * Corresponding author Published: 1 September 2009 Received: 9 February 2009 Accepted: 1 September 2009 BMC Infectious Diseases 2009, 9:146 doi:10.1186/1471-2334-9-146 This article is available from: http://www.biomedcentral.com/1471-2334/9/146 © 2009 Hurrell et al; licensee BioMed Central Ltd. This is an Open Access article distributed under the terms of the Creative Commons Attribution License (http://creativecommons.org/licenses/by/2.0), which permits unrestricted use, distribution, and reproduction in any medium, provided the original work is properly cited. Abstract Background: The objective of this study was to determine whether neonatal nasogastric enteral feeding tubes are colonised by the opportunistic pathogen Cronobacter spp. -
Assessing the Temporal Dynamics of the Lower Urinary Tract Microbiota and the Effects of Lifestyle
Loyola University Chicago Loyola eCommons Dissertations Theses and Dissertations 2019 Assessing the Temporal Dynamics of the Lower Urinary Tract Microbiota and the Effects of Lifestyle Travis Kyle Price Follow this and additional works at: https://ecommons.luc.edu/luc_diss Part of the Microbiology Commons Recommended Citation Price, Travis Kyle, "Assessing the Temporal Dynamics of the Lower Urinary Tract Microbiota and the Effects of Lifestyle" (2019). Dissertations. 3367. https://ecommons.luc.edu/luc_diss/3367 This Dissertation is brought to you for free and open access by the Theses and Dissertations at Loyola eCommons. It has been accepted for inclusion in Dissertations by an authorized administrator of Loyola eCommons. For more information, please contact [email protected]. This work is licensed under a Creative Commons Attribution-Noncommercial-No Derivative Works 3.0 License. Copyright © 2019 Travis Kyle Price LOYOLA UNIVERSITY CHICAGO ASSESSING THE TEMPORAL DYNAMICS OF THE LOWER URINARY TRACT MICROBIOTA AND THE EFFECTS OF LIFESTYLE A DISSERTATION SUBMITTED TO THE FACULTY OF THE GRADUATE SCHOOL IN CANDIDACY FOR THE DEGREE OF DOCTOR OF PHILOSOPHY PROGRAM IN MICROBIOLOGY AND IMMUNOLOGY BY TRAVIS KYLE PRICE CHICAGO, IL MAY 2019 i Copyright by Travis Kyle Price, 2019 All Rights Reserved ii ACKNOWLEDGMENTS I would like to thank everyone that made this thesis possible. First and foremost, I want to thank Dr. Alan Wolfe. I could not have asked for a better mentor. I don’t think there will ever be another period of my life where I grow as a scientist, as a professional, or as a person more than I did under your mentorship. -
The Impact of Some Microcystins on the Growth of Heterotrophic Bacteria from Portuguese Freshwater Reservoirs
Limnetica, 29 (2): x-xx (2011) Limnetica, 34 (1): 215-226 (2015). DOI: 10.23818/limn.34.17 c Asociación Ibérica de Limnología, Madrid. Spain. ISSN: 0213-8409 The impact of some microcystins on the growth of heterotrophic bacteria from Portuguese freshwater reservoirs Diana Miguéns and Elisabete Valério∗ Laboratório de Biologia e Ecotoxicologia, Departamento de Saúde Ambiental, Instituto Nacional de Saúde Dr. Ricardo Jorge. Avenida Padre Cruz, 1649-016 Lisboa, Portugal. ∗ Corresponding author: [email protected] 2 Received: 16/12/2013 Accepted: 05/05/2014 ABSTRACT The impact of some microcystins on the growth of heterotrophic bacteria from Portuguese freshwater reservoirs Microcystins (MCs) are hepatotoxins that are abundantly produced by cyanobacteria. Studies have shown that these toxins affect many multicellular organisms that inhabit aquatic ecosystems; however, their impact on bacteria that co-occur with freshwater cyanobacteria is still unclear. In this study, the impact of the three most common variants of MCs (MCLR, MCRR, and MCYR) on the growth of heterotrophic bacteria isolated from four Portuguese reservoirs was evaluated. Some isolates were derived from freshwater sources where blooms of cyanobacteria that often contain microcystin-producing strains are frequently observed and from a reservoir where these phenomena do not occur. Morphological and molecular characterisation of the bacterial isolates was performed, and these bacteria were exposed to three different concentrations of each MC variant. The effect of MCs on bacterial growth was then evaluated. This study showed that MCLR, MCRR and MCYR can reduce the growth of some heterotrophic bacteria isolated from freshwater sources. To our knowledge, this is the first study in which the impact of several variants of MCs was evaluated in a diverse group of freshwater heterotrophic bacteria. -
The Quest for Novel Extracellular Polymers Produced by Soil-Borne Bacteria
Copyright is owned by the Author of the thesis. Permission is given for a copy to be downloaded by an individual for the purpose of research and private study only. The thesis may not be reproduced elsewhere without the permission of the Author. Bioprospecting: The quest for novel extracellular polymers produced by soil-borne bacteria A thesis presented in partial fulfilment of the requirements for the degree of Master of Science In Microbiology at Massey University, Palmerston North, New Zealand Jason Smith 2017 i Dedication This thesis is dedicated to my dad. Vaughan Peter Francis Smith 13 July 1955 – 27 April 2002 Though our time together was short you are never far from my mind nor my heart. ii Abstract Bacteria are ubiquitous in nature, and the surrounding environment. Bacterially produced extracellular polymers, and proteins are of particular value in the fields of medicine, food, science, and industry. Soil is an extremely rich source of bacteria with over 100 million per gram of soil, many of which produce extracellular polymers. Approximately 90% of soil-borne bacteria are yet to be cultured and classified. Here we employed an exploratory approach and culture based method for the isolation of soil-borne bacteria, and assessed their capability for extracellular polymer production. Bacteria that produced mucoid (of a mucous nature) colonies were selected for identification, imaging, and polymer production. Here we characterised three bacterial isolates that produced extracellular polymers, with a focus on one isolate that formed potentially novel proteinaceous cell surface appendages. These appendages have an unknown function, however, I suggest they may be important for bacterial communication, signalling, and nutrient transfer. -
How Are Gene Sequence Analyses Modifying Bacterial Taxonomy? the Case of Klebsiella
View metadata, citation and similar papers at core.ac.uk brought to you by CORE provided by Hemeroteca Cientifica Catalana REVIEW ARTICLE INTERNATIONAL MICROBIOLOGY (2004) 7:261-268 www.im.microbios.org Julio Martínez1 How are gene sequence Lucía Martínez1,2 Mónica Rosenblueth1 analyses modifying Jesús Silva3 Esperanza Martínez-Romero1* bacterial taxonomy? The case of Klebsiella 1 Genomic Science Center, National University of México (UNAM), Cuernavaca, Mexico 2Research Center of Biological Summary. Bacterial names are continually being changed in order to and Medical Sciences, Faculty of Medicine more adequately describe natural groups (the units of microbial diversity) and Surgery, Autonomous University and their relationships. The problems in Klebsiella taxonomy are illustra- Benito Juárez, Oaxaca, Mexico tive and common to other bacterial genera. Like other bacteria, Klebsiella 3National Institute of Public Health, spp. were isolated long ago, when methods to identify and classify bacte- Cuernavaca, Mexico ria were limited. However, recently developed molecular approaches have led to taxonomical revisions in several cases or to sound proposals of novel species. [Int Microbiol 2004; 7(4):261-268] Received 30 September 2004 Accepted 20 October 2004 Key words: Klebsiella · Enterobacteria · pathogenic bacteria · species *Corresponding author: concept · bacterial taxonomy · phylogeny E. Martínez-Romero Centro de Ciencias Genómicas, UNAM Apdo. Postal 565-A Cuernavaca, Morelos, México Tel. 52-7773131697. Fax 52-7773135581 E-mail: [email protected] which ammonium is produced from gaseous dinitrogen. Introduction Klebsiella variicola may also serve as a model to define a bacterial species (see below). Although Klebsiella species are Historically, the classification of Klebsiella species, like that widely distributed in water, soil, and plants as well as in of many other bacteria, was based on their pathogenic fea- sewage water, it is the human pathogens that have rendered tures or origin. -
Bioresource Technology 100 (2009) 68–73
Bioresource Technology 100 (2009) 68–73 Contents lists available at ScienceDirect Bioresource Technology journal homepage: www.elsevier.com/locate/biortech Proteolytic activity in stored aerobic granular sludge and structural integrity Sunil S. Adav a, Duu-Jong Lee a,*, Juin-Yih Lai b a Department of Chemical Engineering, National Taiwan University, Taipei 10617, Taiwan b Department of Chemical Engineering, R&D Center of Membrane Technology, Chung Yuan Christian University, Chungli 32023, Taiwan article info abstract Article history: Aerobic granules lose stability during storage. The goal of this work was to highlight the main cause of Received 13 April 2008 stability loss for stored granules as intracellular protein hydrolysis. The quantity of extracellular proteins Received in revised form 24 May 2008 was noted to be significantly lower during granule storage, and protease enzyme activities were corre- Accepted 27 May 2008 spondingly higher in the cores of stored granules. The proteolytic bacteria, which secrete highly active Available online 9 July 2008 protease enzymes, were for the first time isolated and characterized by analyzing 16S rDNA sequences. The proteolytic bacteria belonged to the genera Pseudomonas, Raoultella, Acinetobacter, Pandoraea, Klebsi- Keywords: ella, Bacillus and uncultured bacterium, and were grouped into Proteobacteria, Enterobacteria and Firmi- Aerobic granules cutes. The PB1 (Pseudomonas aeruginosa) strain, which exhibited very high proteolytic activity during the Protease Proteolytic bacteria skim milk agar test, was located at the core regime with active protease enzymes, and was close to the EPS obligate anaerobic strain Bacteroides sp. Hence, the extracellular proteins in stored granules were pro- posed to be hydrolyzed by enzymes secreted by proteolytic bacteria with the hydrolyzed products ulti- mately being used by nearby anaerobic strains. -
Identification and Metabolic Activities of Bacterial Species Belonging to the Enterobacteriaceae on Salted Cattle Hides and Sheep Skins by K
186 IDENTIFicATION And METABOLic ACTIVITIES OF BACTERIAL SPEciES BELONGinG TO THE ENTEROBACTERIACEAE ON SALTED CATTLE HidES And SHEEP SKins by K. ULUSOY1 AND M. BIrbIR*2 1Marmara University, Institute of Pure and Applied Science, GOZTEPE, ISTANBUL 34722, TURKEY 2Marmara University, Faculty of Science and Letters, Department of Biology, GOZTEPE, ISTANBUL 34722, TURKEY ABSTRACT and skin samples contain different species of Enterobacteriaceae which may cause deterioration of hides The detailed examination of the Enterobacteriaceae on salted and skins; therefore, effective antibacterial applications should hides and skins offers important information to assess faecal be applied to hides and skins to eradicate these microorganisms contamination of salted hides and skins, its roles in hide and prevent substantial economical losses in leather industry. spoilage, and efficiency of hide preservation. Hence, salted cattle hide and skin samples were obtained from different INTRODUCTION countries and examined. Total counts of Gram-negative bacteria on hide and skin samples, respectively, were 104-106 Cattle hides and sheep skins may be contaminated by and 105-106 CFU/g; of Enterobacteriaceae 104-105 and 105-106 members of the family Enterobacteriaceae. The family is CFU/g; of proteolytic Enterobacteriaceae 103-105 and 105-106 prevalent in nature, normally found in soil, human and animal CFU/g; of lipolytic Enterobacteriaceae 102-105 and 104-105 intestines, water, decaying vegetation, fruits, grains, insects CFU/g; and of each species belonging to