Veneer & Cabinetwork
Total Page:16
File Type:pdf, Size:1020Kb
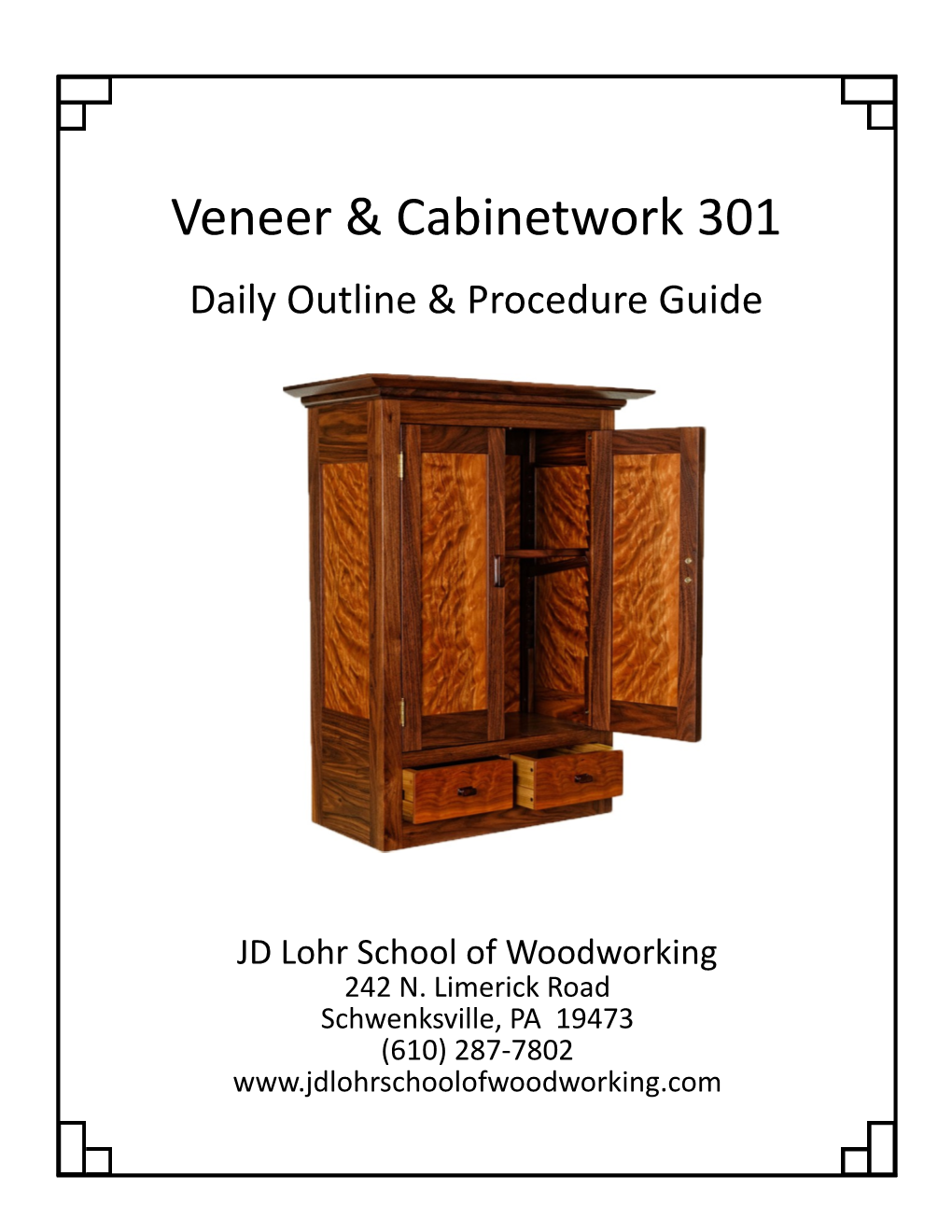
Load more
Recommended publications
-
Yamaha Guitar Information
Yamaha Strengths, Artist’s Advantage “Yamaha Guitars: Essential Knowledge” has been created to give you a behind-the-scenes view of the surprisingly vast and varied resources, facilities, skills, and people involved in making Yamaha guitars the special instruments that they are. Yamaha’s enviable position in musical instrument manufacturing is not only a result of more than 120 years of experience (the company was established in 1887), but also of the unique strengths that its expansive operations bring to bear. From research and development through design and manufacturing to sales and support, Yamaha goes to lengths that are simply beyond the capabilities of most guitar makers. But an underlying dedication to music and the creation of fine musical instruments is always there, forming a steadfast foundation that often results in profit taking a back seat to the pursuit of quality. Yamaha’s true strengths as a guitar maker are not apparent in product brochures or specifications, but they are clearly reflected in the sound, playability, dependability, and overall quality of every guitar that bears the Yamaha name. “Essential Knowledge” includes information that will hopefully provide a clearer picture of the prodigious resources and effort that give artists who choose Yamaha a significant musical advantage. Contents Research & Material Optimization......................p.4 Woods ...................................................................p.6 The Acoustic Guitar Elements of Sound and Playability ....................p.8 The Electric -
Metalwork & Woodwork Saws
HAMMERS - ANVILS - METALWORK & WOODWORK SAWS C HAMMERS BENCH PIN & ANVIL 77 CABLE TACKER GUN 76 DAVID USE PHOTO COPING SAWS 79 SD0010 FRETSAW BLADES 79 FRETSAW FRAMES 79 O HAMMER S & MALLETS 72 - 74 HACKSAWS 76 - 77 MINITURE ANVILS 74 MINITURE PINS 75 MALLET MITRE BOXES 82 PIERCING SAW BLADES 78 PIERCING SAW FRAMES 78 N DAVID USE PHOTO PIN PUSHERS 75 SD0010 RAZOR SAWS 81 SAW BLADE LUBRICANT 78 SAW KNIFE BLADES 81 STAPLE GUNS 75 - 76 V-BLOCK & CLAMPS 77 WEB STRETCHER 82 T ANVILS WOOD SAWS 80 - 81 X-ACTO RAZOR SAWS 81 DAVID USE PHOTO ZONA RAZOR SAWS 79 SD0010 E SAWS N DAVID USE PHOTO SD0010 T V BLOCK & CLAMP DAVID USE PHOTO SD0010 S Last Revised 04/07/2011 71 SQUIRES MODEL & CRAFT TOOLS HAMMERS & MALLETS MAGNETIC TACK HAMMER 6oz a specially designed hammer having one striking face magnetised for use when fitting small nails JEWELLERS MALLET a lightweight stainless steel mallet similar and upholstery tacks. The head features a claw for removing to those used by watchmakers and jewellers, with a solid head and tacks, the striking surface is a magnetic split pattern. The head is knurled shaft. hardened and pol- Length 145mm. ished. Fitted on a Weight 2½oz. hickory handle. Weight 6oz, length overall CODE TYPE PRICE 265mm. HA0025 Jewellers Mallet.................................................... £3.99 WATCHMAKERS MALLET a lightweight jewellers and watch- CODE TYPE PRICE makers mallet with a solid brass head. The handle is 260mm long 051-006 Magnetic Tack Hammer 6oz................................. £14.99 and has an increased diameter and is knurled for extra grip. -
Hand Saw Expert Fx
HAND SAW EXPERT FX Available with two types of double-ground toothings. Universal toothing (U7) for both cross-cutting and rip cutting. Ideal as an all-purpose saw. Alternatively with straight toothing (R7) for fast cross-cutting. L H Artikelkod T 319H22R7FX 22 550 mm 10x 7 t.p.i 0,52 7392746460280 HAND SAW PREMIUM ! TOOLBOX SAW 15 inch, R13 toothing for dry wood, medium cutting. Supplied with a 2-component plastic handle. L H Artikelkod T 275H15 15 380 mm 10x R13 0,47 7392746460303 HAND SAW PREMIUM ! PLASTIC Ideal for cutting pvc pipes and other plastic material. L H Artikelkod T 152H2011 20 500 mm 10x 11 t.p.i. 0,35 7392746453121 HAND SAW PREMIUM ! INSULATION SAW Insulation saw for sawing insulation material, mineral wool. Wave formed edge. Hardpoint finish L H Artikelkod T 255H22WA 22 550 mm 10x - 0,4 7392746460464 HAND SAW PREMIUM ! VENEER SAW Veneer saw for sawing of plywood, veneer etc. Extra thin and wide blade for accurate cut. Hardpoint blade with curved, toothed front-end. Straight toothing 13 teeth/inch L H Artikelkod T 158H 12,5 320 mm 10x 10 t.p.i 0,74 7392746420062 HAND SAW PREMIUM ! TENON SAW Tenon saw with very fine toothing for use in mitre boxes and for other precision jobs. Extra thin and wide blade for an accurate cut. Aluminium alloyed back and our comfortable plastic handle. Straight toothing 13 teeth/inch. Hardpoint finish. L H Artikelkod T 153H12 12 300 mm 10x 10 t.p.i 0,39 7392746453145 153H14 14 350 mm 10x 10 t.p.i 0,32 7392746458126 HAND SAW CONCRETE FX Special saw for cellular blocks and lightweight materials. -
Felder Competition Winners
Feature: Felder furniture making competition The Final Five in the Felder UK HQ FAR LEFT: Tony Wood showroom, behind the first prize of the with his wine table coveted A3-26 planer/thicknesser MIDDLE: Nathan Millar with his winning walnut Felder cabinet on stand LEFT: Patrick Walsh competition with his hall unit winners unveiling excellence After six long months, we finally unveil the five Felder competition finalists and Josh Milton kneels beside his ’Tilt Lounger’ Jamie Lake beside his ‘Wall of Heroes’ show you their fantastic pieces, before revealing the three overall winners for his wonderful wine table in American white multiplex; and for Nathan the nifty A3-26 oak; second place was given to Josh Milton for planer/thicknesser with Silent-Power spiral his ingenious ‘Tilt Lounger’; and finally, first place cutterblock. To say he looked pleased with his was awarded to the very well deserving Nathan prize was an understatement and it was great to s many of you will know, we task of having to choose our Final Five, each to receive so many excited emails in response, that this would be a worthwhile experience for Millar for his walnut and stone cabinet on stand, hear him say how he couldn’t wait to get it back have been running the Felder 60th of whom would be invited to a special judging and one of the finalists, Patrick Walsh, was even all. The next task was for myself, John and Peter which had people talking as soon as he brought to his workshop. He’s promised that he’ll keep anniversary competition in both ceremony held at Felder UK’s Milton Keynes HQ. -
WORKSHOP 6 Bookcase Project II Routing Dadoes and Rabbets
WORKSHOP 6 Bookcase Project II Routing Dadoes and Rabbets, Curve Cutting, Sanding & Screwed and Plugged Joinery Date/Time: Saturday, Xtember tbd, 9 am to 12 noon Location: Mentor’s Shop Mentors: tbd Content: Follows FineWoodworking.com video “Getting Started in Woodworking” Season 2, Session 4, Rabbets and Dadoes with a Router; Session 5, Cutting Curves; Session 6, Sanding the Bookcase Parts; & Session 7, Joinery with Screws and Plugs. Description: Cutting Rabbets and Dadoes with a Router; Dadoes are square notches cut into the surface of a piece of lumber that hold the end of a joining board. They are perfect when building shelving or cabinetry as a way to join shelves and partitions. For this bookcase project, the dado joinery is reinforced with screws, although that added strength isn't essential to the joint. A simple but foolproof T-Square jig is built to assist in cutting the dadoes. This type of jig is designed to cut exactly 90 degrees to one edge, which is perfect for our shelf dadoes. You will also need a straight router bit. Ours is 3/4-in. diameter because our lumber measures that same thickness. Rabbets are similar to dodoes and groves in that they can go in the direction of the grain or across it. However, Rabbets are notches cut into the edge of a board. A rabbet is used to attach the back panel to the bookcase Laying Out, Cutting and Smoothing Curves; A changing radius curve isn't a section of a circle. This type of curve can be drawn with a variety of drawing tools, including french curves and battens. -
Using Veneering Tools
Using veneer hand tools Veneer Tape Dispenser A gum tape dispenser that will take 3/4”wide gum tape is excellent for securing veneer seams together. A manual pull and tear machine which has a brush or sponge that will moisten tape (25 gram weight). It is indispensable for any shop that works with veneer. A sponge in a cup works well for moistening short lengths of tape for smaller projects. Veneer Gum Tape 25 to 30 gram (non-perforated) veneer tape that has water activated hide or vegetable glue is ideal for veneering. It is cut to length, moistened with a sponge or with the tape dispenser wetting system, placed over the veneer seam or joint, and smoothed or burnished down with a brush or rag to secure it firmly onto the veneer. It is used for final assembly of veneer joints in decorative veneering, in order to create a single skin or sheet of veneer. Ideally, after the gum tape is applied over the joints, the assembled veneer skin gets placed between two plattens to insure that the moisture from the gum tape does not warp the veneer until it dries. This complete skin will then be glued onto a foundation or core of smooth plywood or MDF, with the gum tape side exposed. After the veneer is glued to the core with a mechanical or vacuum type veneer press, the tape is removed by moistening and peeling it off with a sharpened flexible putty knife, or sanded off the veneer with a belt, stroke or random orbital sander. -
View the Door Catalog
Roy’s Wood Products OVER 45 YEARS OF CUSTOM WOODWORKING A passion for quality and almost 50 years of custom woodworking drives Roy’s Wood Products, RWP, to manufacture some of the best wood products in the industry. Our grandfather Roy Brazell, Sr., after serving in WWII, started building cabinets and other products for local craftsmen and contractors. His son, Roy Brazell, Jr. continued to grow the business by focusing on what the customer needed and working hard for timely delivery. As a result of hard work, attention to quality, and the blessings of our Lord and Savior Jesus Christ, RWP has grown into what it is today. We are looking forward to providing you with the custom cabinet doors, custom mouldings, hardwood flooring or any other products you might find in the pages of this catalog. Thank you for your business. Cherry Roman Eyebrow Roman Arch Square Raised Panel DFT-01-202-110 011-01-202-110 005-01-202-110 003-01-202-110 401-00-000-110 402-00-000-110 Maple Double American American Arch Square Raised Panel DFT-03-203-113 015-03-203-113 010-03-203-113 003-03-203-113 401-00-000-113 403-00-000-113 Hickory PICTURED: Cathedral Eyebrow Cathedral Arch Square Raised Panel DFT-01-209-109 Square Raised Panel Door 003-01-202-110 008-01-209-109 004-01-209-109 003-01-209-109 401-00-000-109 Solid Raised Panel Drawer Front 502-00-000-110 509-00-000-109 In Cherry with stain 4 5 Birch DFT-01-FPL-110 Glass Four Lite Flat Roman Classic Flat 409-00-000-110 003-03-G04-111 905-01-FPL-110 903-01-FPL-110 401-00-000-110 Knotty Pine DFT-03-FPL-107 Flat -
Combination Frame and Panel Cabinet Doors
Cabinet Doors & Drawer Fronts Combination Frame & Panel B Section View of Top Rail for #1616 Door Raised Panel Style: 1616 Style: 4016 Section View of Top Rail for #1618 Door - ⅜" Dowels Face of Door SR100 ⅜" Diam. Dowels Section View of Stile for #1618 Door - ⅜" Dowels Face of Door SR100 ⅝" Diam. Dowels Section View of Top Rail for #1618 Door - ⅝" Dowels Raised Flat Face of Door Panel Panel SR100 Section View of Stile for #1618 Door - ⅝" Dowels Style: 1618 Style: 4018 Face of Door SR100 ** Please fax or e-mail your rough draft or CAD drawings to Customer Support for your manufacturing and quote needs. ** ► For PRICING ► See Section B13 in our Wholesale Pricing Catalog. ® ® B13-1 (Phone) 1-800-237-1326 6:00AM - 4:30PM CST (24 Hour Fax) 1-608-781-3667 V15.2 .com C Combination Frame & Panel Cabinet Doors & Drawer Fronts B ⅜" Thick Slats Section View of Top Rail for #1617 Door ¾" Thick Section View of Top Rail for #1617 Door Slats Raised Panel Style: 1617 Style: 4017 ** Please fax or e-mail your rough draft or CAD drawings to Customer Support for your manufacturing and quote needs. ** Combination Frame and Panel Door Notes 1) Pricing A price quote will be provided for your approval before beginning the manufacturing process. These doors can be ordered with raised or reversed center panels in solid wood & raw MDF or with 2) Center Panel flat center panels in ¼" wood veneer & ¼" raw MDF. Mullions or a Lite Pattern are optional in the Frame Only section. Any “Traditional”, “Old World” or “Mitered” stile and rail profile can be used, some profilesmay not be compatible for use with mullions or Lite Pattern options. -
1. Hand Tools 3. Related Tools 4. Chisels 5. Hammer 6. Saw Terminology 7. Pliers Introduction
1 1. Hand Tools 2. Types 2.1 Hand tools 2.2 Hammer Drill 2.3 Rotary hammer drill 2.4 Cordless drills 2.5 Drill press 2.6 Geared head drill 2.7 Radial arm drill 2.8 Mill drill 3. Related tools 4. Chisels 4.1. Types 4.1.1 Woodworking chisels 4.1.1.1 Lathe tools 4.2 Metalworking chisels 4.2.1 Cold chisel 4.2.2 Hardy chisel 4.3 Stone chisels 4.4 Masonry chisels 4.4.1 Joint chisel 5. Hammer 5.1 Basic design and variations 5.2 The physics of hammering 5.2.1 Hammer as a force amplifier 5.2.2 Effect of the head's mass 5.2.3 Effect of the handle 5.3 War hammers 5.4 Symbolic hammers 6. Saw terminology 6.1 Types of saws 6.1.1 Hand saws 6.1.2. Back saws 6.1.3 Mechanically powered saws 6.1.4. Circular blade saws 6.1.5. Reciprocating blade saws 6.1.6..Continuous band 6.2. Types of saw blades and the cuts they make 6.3. Materials used for saws 7. Pliers Introduction 7.1. Design 7.2.Common types 7.2.1 Gripping pliers (used to improve grip) 7.2 2.Cutting pliers (used to sever or pinch off) 2 7.2.3 Crimping pliers 7.2.4 Rotational pliers 8. Common wrenches / spanners 8.1 Other general wrenches / spanners 8.2. Spe cialized wrenches / spanners 8.3. Spanners in popular culture 9. Hacksaw, surface plate, surface gauge, , vee-block, files 10. -
The Complete Illustrated Guide to Shaping Wood / Lonnie Bird
The COMPLETE ILLUSTRATED Guide to ShapingWood LONNIE BIRD ➤ Squares, Circles, and Ellipses ➤ Edge Treatments and Moldings ➤ Coves, Reeds, and Flutes ➤ Bent and Laminated Curves ➤ Turned and Carved Shapes The COMPLETE ILLUSTRATED Guide to ShapingWood TJ51-1-2008 IMUS 7/UOA0069-Shaping Wood W:9.25”xH:10.875” Wood TJ51-1-2008 IMUS 7/UOA0069-Shaping 175L EX 128White A M/A(D) The COMPLETE ILLUSTRATED Guide to ShapingWood LONNIE B IRD t TJ51-1-2008 IMUS 7/UOA0069-Shaping Wood W:9.25”xH:10.875” Wood TJ51-1-2008 IMUS 7/UOA0069-Shaping 175L EX 128White A M/A Magenta(D) Text © 2001 by Lonnie Bird Photographs © 2001 by Lonnie Bird Illustrations © 2001 by The Taunton Press, Inc. All rights reserved. Pp The Taunton Press, Inc., 63 South Main Street, PO Box 5506, Newtown, CT 06470-5506 e-mail: [email protected] DESIGN: Lori Wendin LAYOU T: Suzi Yannes ILLUSTRATOR: Mario Ferro PHOTOGRAPHER: Lonnie Bird LIBRARY OF CONGRESS CATALOGING-IN-PUBLICATION DATA: Bird, Lonnie. The complete illustrated guide to shaping wood / Lonnie Bird. p. cm. Includes index. ISBN-13: 978-1-56158-400-0 ISBN-10: 1-56158-400-2 1. Woodwork. I. Title. TT180 .B57 2001 TJ51-1-2008 IMUS 7/UOA0069-Shaping Wood W:9.25”xH:10.875” Wood TJ51-1-2008 IMUS 7/UOA0069-Shaping 175L EX 128White A M/A Magenta(D) 684’.08--dc21 2001027430 Printed in Thailand 1098765 About Your Safety: Working with wood is inherently dangerous. Using hand or power tools improperly or ignoring safety practices can lead to permanent injury or even death. -
Acoustic Guitar Buying Guide
Acoustic Guitar Buying Guide A Starter’s Guide to Buying an Acoustic Guitar Shopping for an acoustic guitar can be an overwhelming experience. Because guitar makers use a wide range of woods, hardware, and design elements, there are many factors to consider. Specifically, there are four primary areas you will want to consider and/or know about before you start shopping. Table of Contents Purpose and Budget - How are you going to use your guitar, and how much will you spend? Construction and Design - Learn the basics before you shop. Styles and Sound - Understand how different features affect the sound of the guitar. Acoustic Guitar Variants - 12-string acoustics and alternate body shapes Don't Forget Personal Preference Glossary Purpose and Budget Before you think about brand names or body styles, consider what you are going to use the guitar for, and how much money you have to spend on one. Skill Level - Amateur or Advanced If you are a new player who is looking for an instrument to learn on, you may not want to spend too much on a high-end acoustic guitar just yet. Thanks to modern manufacturing techniques, there is a wide selection of good, low- to mid-range acoustic guitars to choose from. But maybe you are an experienced player who is ready to upgrade to a better guitar. In that case, it is important to know the difference between tonewoods, and how the soundboard effects resonance. Purpose - Acoustic-Electrics Expand Your Options Will you be playing with a band, or taking your guitar to public events such as open mic nights? If so, you may want to consider an acoustic-electric guitar. -
Tips & Tricks for Project Boards
Tips & Tricks for Project Boards What are project boards? Project boards are pre-finished, smaller, easy-to-transport, easy-to-store, easy-to-handle craft and hobby boards, available in a variety of styles and colors, excellent for a wide range of DIY home projects. Understanding project board finishes Charred – Our method of charring wood uses the Japanese technique of shou-sugi-ban to create artfully burned boards intended to create unique home décor projects, accent walls, crafts, hobbies and more. Rustic – These project boards are perfect for your next reclaimed-wood project. It's new lumber that has been distressed, primed and painted to have the authentic look and texture of vintage, rough-sawn, rustic barn wood. Getting a clean edge when sawing project boards Don’t own a saw? Ask a sales associate if complementary cutting is available. Most stores will cut as many pieces as you’d like to any dimensions you need. Feel free to bring your project instructions along so you’re ready to take advantage of this service when and where it’s offered. The professionals are there to help! All the cuts you need to make on your project boards can be made with a circular saw. A miter saw and table saw work too – and can save time on large jobs – but the circular saw is your Swiss army knife of cutting. Whichever saw you choose, make sure you’re using one with sharp carbide teeth. A high number of sharp teeth – at least 80 – will ensure clean cuts, while dull blades are more likely to chew up the edges of your wood.