Numerical Investigation of Wing Morphing Capabilities Applied to a Horten Type Swept Wing Geometry
Total Page:16
File Type:pdf, Size:1020Kb
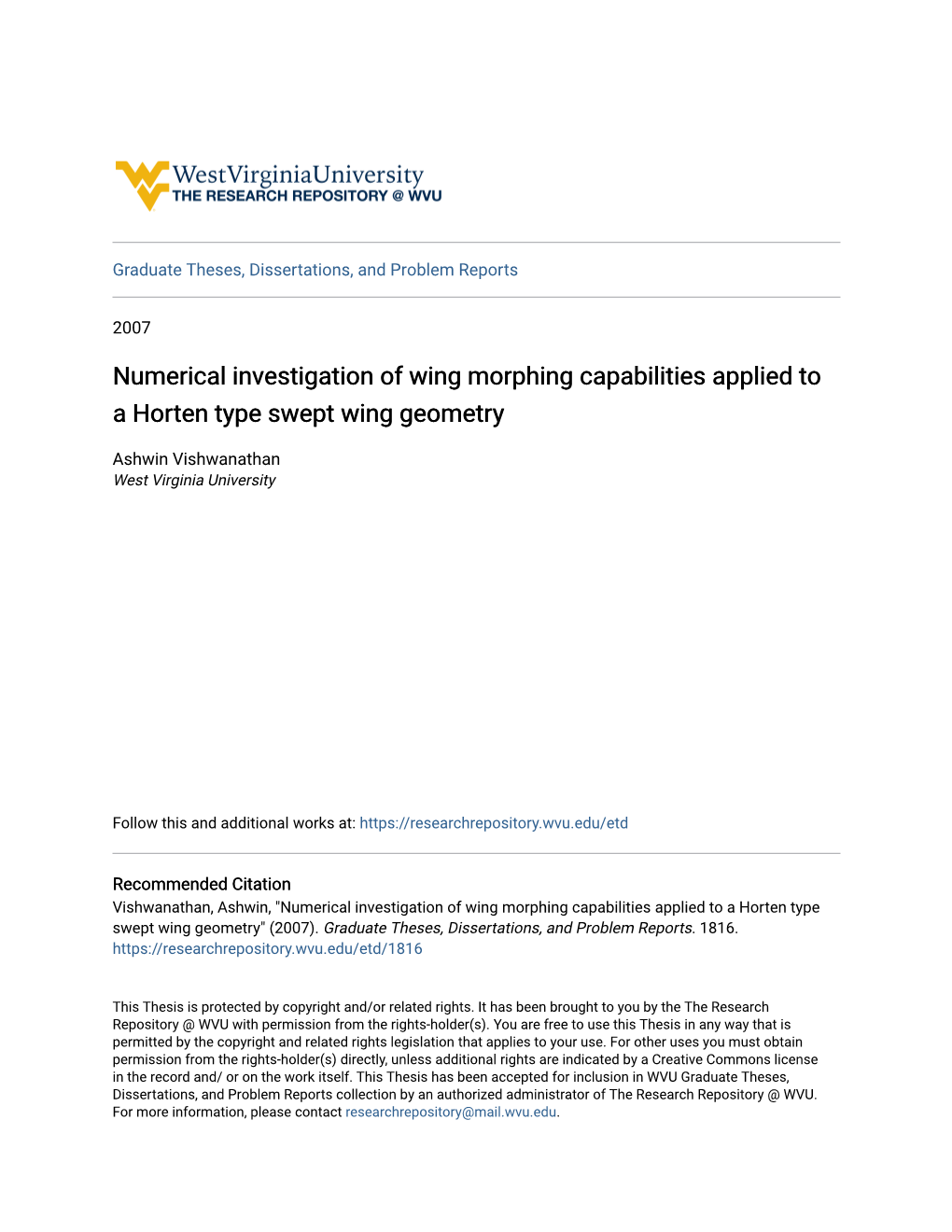
Load more
Recommended publications
-
Glider Accidents and Prevention
Glider Accidents – Statistics & Prevention Larry Suter / John Scott Northern California Soaring Association & Air Sailing Gliderport Glider Accident Summary Data from 2008 – 2013 172 accidents reported to NTSB SSF categorized into three Types 70% 60% 50% 40% Fatal 30% Non Fatal 20% 10% 0% Takeoff Free Flight Landing What fact is painfully obvious? Takeoff 70% 60% 50% 40% Fatal 30% Non Fatal 20% 10% 0% Takeoff Free Flight Landing Approximately 20% of all accidents occur during the takeoff phase Video of a canopy coming open on takeoff. According to the SSF opening canopies and deploying spoilers are more likely to cause a takeoff accident than a rope break or any other type PT3 event. (PT3 = Premature Termination of the Tow) Canopy and spoiler accidents are preventable! They occur because the pilot failed to properly complete their Pre-Takeoff checklist. Low altitude emergency training tends to focus on rope breaks. In reality rope breaks are a small fraction of Takeoff accidents. Deployed Spoilers There is no reason that deployed spoilers should cause an accident. Just close them! Rudder Waggle --- A potentially dangerous signal Two Landmark accidents; same scenario (2006 NV, 2011 MD) Pilots reacted too quickly w/o thinking and pulled release. (Panic? Misinterpretation?) Had insufficient altitude to return to airport. (120’, 200’) ASG Tow Pilot Manual discourages this signal below 1000’ AGL; Rudder deflections and AD coupling. Opening Canopy There is no reason that an opening canopy should cause an accident! Effects of an Opening -
09 Stability and Control
Aircraft Design Lecture 9: Stability and Control G. Dimitriadis Introduction to Aircraft Design Stability and Control H Aircraft stability deals with the ability to keep an aircraft in the air in the chosen flight attitude. H Aircraft control deals with the ability to change the flight direction and attitude of an aircraft. H Both these issues must be investigated during the preliminary design process. Introduction to Aircraft Design Design criteria? H Stability and control are not design criteria H In other words, civil aircraft are not designed specifically for stability and control H They are designed for performance. H Once a preliminary design that meets the performance criteria is created, then its stability is assessed and its control is designed. Introduction to Aircraft Design Flight Mechanics H Stability and control are collectively referred to as flight mechanics H The study of the mechanics and dynamics of flight is the means by which : – We can design an airplane to accomplish efficiently a specific task – We can make the task of the pilot easier by ensuring good handling qualities – We can avoid unwanted or unexpected phenomena that can be encountered in flight Introduction to Aircraft Design Aircraft description Flight Control Pilot System Airplane Response Task The pilot has direct control only of the Flight Control System. However, he can tailor his inputs to the FCS by observing the airplane’s response while always keeping an eye on the task at hand. Introduction to Aircraft Design Control Surfaces H Aircraft control -
Effects of Controls (Secondary)
Student Study Guide A Certificate EFFECTS OF CONTROLS (SECONDARY) Aim: To learn about any secondary effects of flight control inputs. We have seen the primary effect of controls… now lets explore any secondary effects… that is… does anything else happen when we pitch, roll or yaw… does one movement have more than the single effect we have seen so far? Secondary Effects: A secondary effect of control can be defined as any effect about one of the 3 main axis of motion which occurs as a result of an initial control input. If we pitch the glider, will it roll or yaw? No… so there is no secondary effect of pitch. How about if we apply aileron and roll the glider… it banks, slips towards the lower wing then yaws towards that lower wing… so yes, there is a secondary effect of roll and it is yaw. And yawing…we apply some rudder…the glider yaws, skids sideways and rolls towards the direction of the yaw. Your instructor will set the glider up in a normal gliding attitude at 45kts and demonstrate these secondary effects so you can see them. To summarise then: Control Axis Primary Effect Secondary Effect Elevato Lateral Glider pitches nose up there is no roll or yaw r and down Aileron Longitudina glider rolls left the glider slips towards the lower wing, then yaws l / right towards the lower wing Rudder Vertical glider yaws left The glider skids then rolls towards the inner wing glider yaws right So What?! Applying elevator to pitch the nose up or down has no secondary effect to consider. -
Yaw and Roll Moment Equations and Estimation
Roll and Yaw Moments and Stability Yaw Moment Equation The yaw moment is the moment about the zbody axis and is positive if it moves the nose of the plane to the right. The big contributor to the yaw moment is the vertical tail. We can write the yaw moment equation in a similar manner to the way we wrote the pitch-moment equation by considering the contributions from the wing-body combination and from the vertical tail. If we take moments about the center of gravity we have: (1) where is the vertical tail length, the distance from the cg to the aerodynamic center of the vertical tail, are the lift and drag of the vertical tail, and is the angle of attack of the vertical tail measured positive so as to create a positive side force. If we make the usual assumptions such as that is a small angle, and that , we can reduce Eq. (1) to the form: (2) and (3) where is the vertical tail area. Dividing by we obtain the yaw-moment equation in coefficient form: (4) If we let the vertical tail lift coefficient depend on a vertical tail lift curve slope and a rudder deflection we can write it as: (5) where and are the vertical tail lift curve slope and rudder “lift curve slope” respectively. In addition we can write the vertical tail angle of attack in terms of the vehicle side slip angle, , and the side-wash angle, , as: (6) If we make the substitutions, the yawing moment equation takes the form: (7) We can put this equation in a more useful form by determining the stability and control derivatives and . -
United States Patent (19) 11 Patent Number: 6,079,672 Lam Et Al
USOO6079672A United States Patent (19) 11 Patent Number: 6,079,672 Lam et al. (45) Date of Patent: Jun. 27, 2000 54 AILERON FOR FIXED WING AIRCRAFT 2,665,084 1/1954 Feeney et al. .......................... 244/217 2,791,385 5/1957 Johnson. 76 Inventors: Lawrence Y. Lam, 27013 Woodbrook 3,041,014 6/1962 Gerin. Rd., Rancho Palos Verdes, Calif. 90275; 2. 1: E. et al Michael . s y Hermoso, 4,049,2192Y- - -2 9/1977 Deana C etC al.a ............................. 244/217 OSAILOS 11 IIS, UallI. 4,180.222 12/1979 Thornburg. 4,717,097 1/1988 Sepstrup .................................. 244/217 21 Appl. No.: 08/993,241 4,720,062 1/1988 Warrink et al. ... 244/90 R 5,655,737 8/1997 Williams et al. ................... 244/217 X 22 Filed: Dec. 18, 1997 7 Primary Examiner Robert P. Swiatek 51) Int. Cl.' ........................................................ Bisc 9/00 Attorney, Agent, or Firm-Burns, Doane, Swecker & 52 U.S. Cl. .......................................... 244/217; 244/90 R Mathis, LLP 58 Field of Search ................................ 244/90 R, 90 A, 244/110 D, 217 57 ABSTRACT 56) References Cited An aircraft aileron System unique in its construction, method of deployment and the functional results obtained, is com U.S. PATENT DOCUMENTS prised of two panels located at the rear portion of the wing, in a Spanwise direction and aligned with the wing's trailing E. to: With edge. The panels are independently hinged at their leading 1875S03 0f1932 Hall edges and rotate to make angular deflections with respect to 1992.157 2/1935 Hall. the wing. -
An Educational Rudder Sizing Algorithm for Utilization in Aircraft Design Software
International Journal of Applied Engineering Research ISSN 0973-4562 Volume 13, Number 10 (2018) pp. 7889-7894 © Research India Publications. http://www.ripublication.com An Educational Rudder Sizing Algorithm for Utilization in Aircraft Design Software Omran Al-Shamma University of Information Technology and Communications, Baghdad, Iraq (Corresponding author) Rashid Ali Coventry University, Coventry, UK Haitham S. Hasan University of Information Technology and Communications, Baghdad, Iraq Abstract unfavorable center of gravity; (iv) landing gear retracted; (v) flaps in the approach position; and (vi) maximum landing The essential prerequisites of the rudder sizing process are the weight”. A similar regulation is founded in FAR part 23 [3] directional control and trim. The main roles of the rudder are: for general aviation and in MIL-STD [4] [5] for military turn coordinate, asymmetric thrust on conventional transport aircraft. aircraft, crosswind landing, adverse yaw, spin recovery, and glide slope adjustment. The asymmetric thrust and crosswind It should be noted that there are meddling between aileron and landing are the most crucial flight conditions that recognize rudder, and frequently employed concurrently. Therefore, the transport aircraft. This paper presents an educational directional and lateral dynamics are often coupled [6] [7]. rudder sizing algorithm of conventional aircraft, primarily, for Thus, it is a better rehearsal to size the aileron and rudder aeronautical engineering students and also for fresh engineers simultaneously. On the other hand, the aileron is a rate control to enhance their knowledge, understanding, and analysis. The device, while the rudder is similar to elevator as both are paper introduces the necessary equations to guide the designer displacement control device. -
Wind-Tunnel Investigation of the Flight Chasacteristics of a Canard
., , -. / ~ ,a ~ i t 1 1 / I -1 I' I , ,Wind-TunnelInvestigation of the Flight Chasacteristics of a Canard Genera1:Aviation Airplane Coniiguration - I Dale R. Satran j . iNA3A-22-2623 ) UIND- TUNKEL INVESTIGkTION OE 138 7 - 1 d 0 3 j IHZ ELIGHT Cii Ait ACiEiiI STILS C F A CANAtiD Fig32 AVI - G AL- A T iUN AIRP LANE CC NEPGUEATION I 60 [NASA) p csci 01A Ullcla s I H1/02 44247 , NASA NASA Technical Paper 2623 1986 Wind-Tunnel Investigation of the Flight Characteristics of a Canard General-Aviation Airplane Configuration Dale R. Satran Langley Research Center Hampton, Virginia National Aeronautics and Space Administration Scientific and Technical Information Branch Summary figuration. A 0.36-scale model was used in the free- flight investigation and was also used to obtain static A 0.36-scale model of a canard general-aviation and dynamic force data to aid in the interpretation airplane with a single pusher propeller and winglets of the free-flight test results. The free-flight tests was tested in the Langley 30- by 60-Foot Wind Tun- were conducted for angles of attack ranging from 7O nel to determine the static and dynamic stability and to 14O. The investigation included tests of the model control and free-flight behavior of the configuration. with high and low canard positions, three center-of- Model variables made testing of the model possible gravity locations, outboard wing leading-edge droop, with the canard in high and low positions, with in- winglets and a center vertical tail, and several roll- creased winglet area, with outboard wing leading- and yaw-control systems. -
II.E. Airplane Flight Controls
Nicoletta Fala Last modified: 04/20/19 II.E. Airplane Flight Controls Objectives The student should develop knowledge of the elements related to primary flight controls, trim control, and wing flaps. Key Elements Primary flight controls—airflow and pressure distribution Trim relieves control pressures Flaps increase lift and induced drag Elements Primary flight controls Trim controls Wing flaps Schedule 1. Discuss objectives 2. Review material 3. Development 4. Conclusion Equipment White board Markers References Instructor’s 1. Discuss lesson objectives Actions 2. Present lecture 3. Questions 4. Homework Student’s Participate in discussion Actions Take notes Completion The student can explain the primary flight controls, their function, and Standards how they do what they do. The student understands how trim works and can more effectively use it, and understands the different types of flaps and their differing characteristics. II-E-1 Nicoletta Fala Last modified: 04/20/19 References FAA-H-8083-25B, Pilot’s Handbook of Aeronautical Knowledge (Chapter 6) II-E-2 Nicoletta Fala Last modified: 04/20/19 Instructor Notes Introduction Overview—review objectives and key ideas. Why—airplane’s attitude controlled by deflection of primary flight controls. When deflected, the primary flight controls change the camber and angle of attack of the wing/stabilizer and change its lift and drag characteristics. Trim controls are used to relieve the control pressures. Flaps create a compromise between a high cruise speed and low landing speed. Primary flight Required to safely control the airplane during flight. controls Secondary control systems improve performance characteristics or relieve excessive control forces (wing flaps, trim systems). -
Gliding Turns by Ron Ridenour
Gliding Turns, anatomy of a simple maneuver By Ron Ridenour, SSF Trustee After a student learns how to adjust the glider’s pitch attitude to maintain the desired airspeed the next task is how to make turns. The Joy of Soaring, a book written by Carle Conway for the SSA, speaks about the 5 “undesired side effects of the turn”. The undesired side effects are present in every turn we make and all the training manuals I’ve read speaks to them to various degrees. The first side effect is called “adverse yaw”. Adverse yaw is caused by the use of the ailerons to bank into or out of the turn. The downward moving aileron creates more lift on that wing and this increase in lift also creates more drag on that wing. This creates a yaw opposite from the direction of the desired turn. The rudder must be used in a coordinated fashion to overcome this adverse yaw to streamline the fuselage while the ailerons are being used to change the bank angle. When rolling into or out of the bank, the greater the deflection of the ailerons (stick position) the greater the rate of roll (i.e. the rate of change of the bank angle). Correspondingly, a greater amount of rudder must also be used to counteract the increased adverse yaw. The yaw string is used to determine the amount of rudder needed to maintain ‘coordinated’ flight. The second side effect is called the “diving tendency”. The diving tendency is caused by the glider’s need for the wing to create more total lift as the bank angle is increased. -
FLYING LESSONS for March 31, 2016
FLYING LESSONS for March 31, 2016 Suggested by this week’s aircraft mishap reports FLYING LESSONS uses the past week’s mishap reports to consider what might have contributed to accidents, so you can make better decisions if you face similar circumstances. In almost all cases design characteristics of a specific make and model airplane have little direct bearing on the possible causes of aircraft accidents, so apply these FLYING LESSONS to any airplane you fly. Verify all technical information before applying it to your aircraft or operation, with manufacturers’ data and recommendations taking precedence. You are pilot in command, and are ultimately responsible for the decisions you make. FLYING LESSONS is an independent product of MASTERY FLIGHT TRAINING, INC. www.mastery-flight-training.com Pursue Mastery of Flight™ This week’s lessons: Everybody talks about crosswind practice, but few pilots do anything about it. Crosswinds are the number one factor in weather-related accidents, with even far more in-motion aviation insurance claims. The answer to handling crosswinds is usually to…practice crosswinds. But how can we develop the skills we need to employ during that practice, and in our day-to-day flying? There’s no question that practice makes (at least closer to) perfect. But like other maneuvers, landing in crosswinds requires the artful combination of a number of individual skills. There are several of ways to develop and improve these skills so you’ll be ready to combine them in a strong or gusty crosswind. Here are five exercises you (with and without your instructor) can use to help you make better crosswind landings. -
Control of a Swept Wing Tailless Aircraft Through Wing Morphing
Graduate Theses, Dissertations, and Problem Reports 2007 Control of a swept wing tailless aircraft through wing morphing Richard W. Guiler West Virginia University Follow this and additional works at: https://researchrepository.wvu.edu/etd Recommended Citation Guiler, Richard W., "Control of a swept wing tailless aircraft through wing morphing" (2007). Graduate Theses, Dissertations, and Problem Reports. 2779. https://researchrepository.wvu.edu/etd/2779 This Dissertation is protected by copyright and/or related rights. It has been brought to you by the The Research Repository @ WVU with permission from the rights-holder(s). You are free to use this Dissertation in any way that is permitted by the copyright and related rights legislation that applies to your use. For other uses you must obtain permission from the rights-holder(s) directly, unless additional rights are indicated by a Creative Commons license in the record and/ or on the work itself. This Dissertation has been accepted for inclusion in WVU Graduate Theses, Dissertations, and Problem Reports collection by an authorized administrator of The Research Repository @ WVU. For more information, please contact [email protected]. CONTROL OF A SWEPT WING TAILLESS AIRCRAFT THROUGH WING MORPHING by Richard W. Guiler Dissertation submitted to the College of Engineering and Mineral Resources at West Virginia University in partial fulfillment of the requirements for the degree of Doctor of Philosophy in Aerospace Engineering Approved by Wade Huebsch, PhD., Committee Chairperson John Loth, PhD. Gary Morris, PhD. John Kuhlman, PhD. Jens Madsen, PhD. Department of Mechanical and Aerospace Engineering Morgantown, West Virginia 2007 Keywords: Morphing Aircraft Structures, Tailless Aircraft, Horten, Wing Twist, Blended Wing Body and Aircraft Controls Copyright 2007 Richard W. -
Aileron-Rudder Interconnect Control System in the I Landing Configuration G '
NASA Technical Memorandum 81972 lNASA-TM-81972 19820005275 Limited Evaluation of an _or z,o_. r_t_v _e.o_ _s ROo_ F-14A Airplane Utilizing an Aileron-Rudder Interconnect Control System in the i Landing Configuration _g_'_ ., _._-_ _ _,_, . _,_,G_._"_ _q, _ _.,_\l_ x,r,' _\?,,q_'"... q\_.-_" Wendell W. Kelley and Einar K. Enevoldson _'- _ _ _'_ DECEMBER 1981 E i NASA Technical Memorandum 81972 Limited Evaluation of an F-14A Airplane Utilizing an Aileron-Rudder Interconnect Control System in the Landing Configuration Wendell W. Kelley Langley Research Center Hampton, Virginia Einar K. Enevoldson Dryden Flight Research Center Edwards, California NILSA National Aeronautics and Space Administration Scientific and Technical Information Branch 1981 SUMMARY A flight test was conducted for preliminary evaluation of an aileron-rudder interconnect (ARI) control system for the F-14A airplane in the landing configura- tion. Two ARI configurations were tested in addition to the standard F-14 flight control system. Flight data and pilot comments were used to compare the effects of each control system on airplane lateral-directional handling qualities during a final-approach-course correction maneuver. Results of the flight test showed marked improvement in handling qualities when the ARI systems were used. Sideslip due to adverse yaw was considerably reduced, and airplane turn rate was more responsive to pilot lateral-control inputs. Pilot com- ments substantiated the flight data and indicated that the ARI systems were superior to the standard control system in terms of pilot capability to make lateral offset corrections and heading changes on final approach.