Fluid Ow in a Rotating Low-Specific-Speed Centrifugal
Total Page:16
File Type:pdf, Size:1020Kb
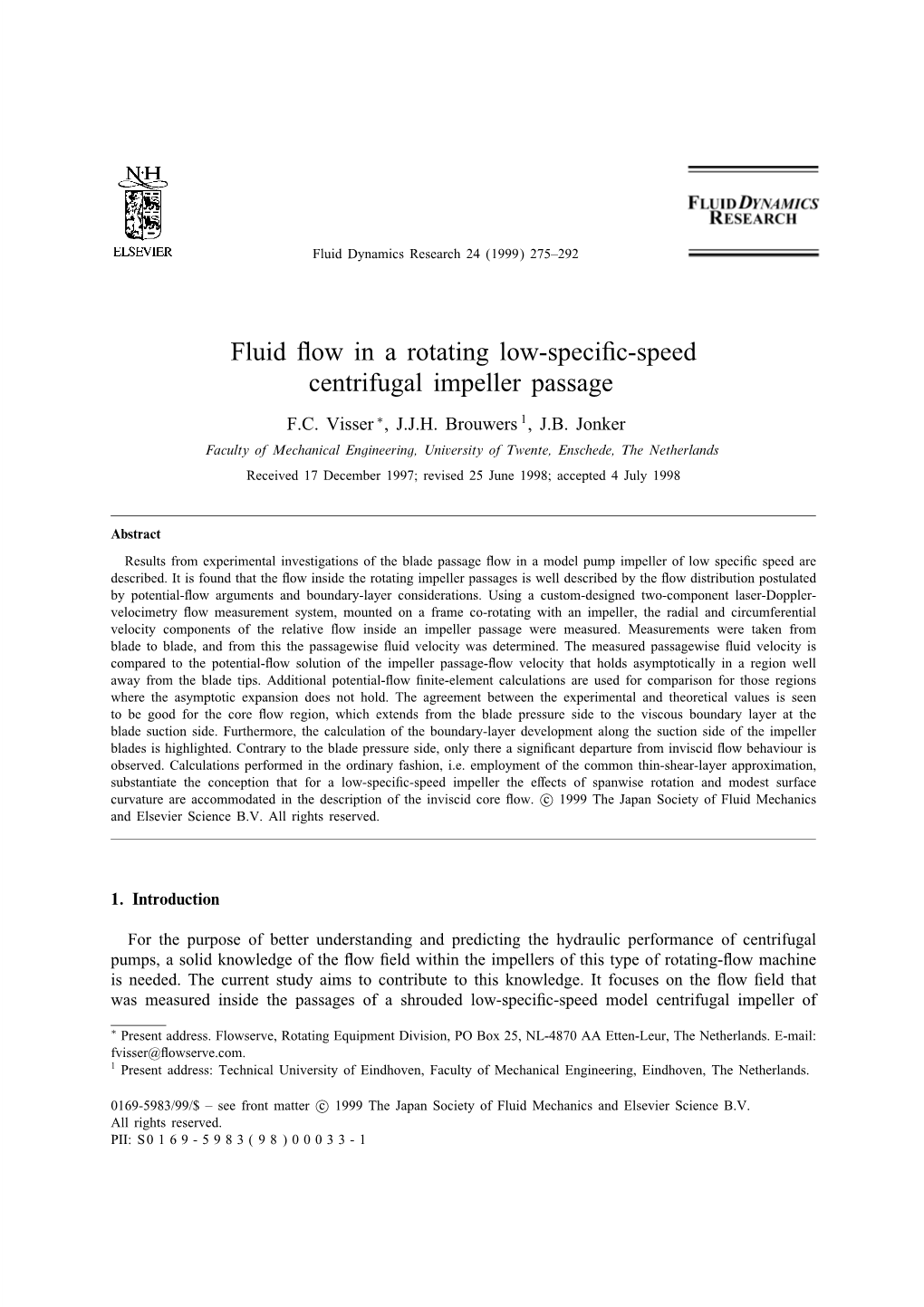
Load more
Recommended publications
-
Pump Product Catalog
Pump Division Pump Product Catalog Experience In Motion Pump Supplier to the World Flowserve is the driving force in the global Product Brands of Distinction industrial pump marketplace. No other pump ACEC™ Centrifugal Pumps company in the world has the depth or breadth of expertise in the successful application of Aldrich™ Pumps pre-engineered, engineered, and special purpose Byron Jackson ® Pumps pumps and systems. Calder™ Energy Recovery Devices Cameron™ Pumps Durco ® Process Pumps Flowserve ® Pumps IDP ® Pumps INNOMAG ® Sealless Pumps Lawrence Pumps ® Niigata Worthington™ Pumps Pacific ® Pumps Pleuger ® Pumps Scienco™ Pumps Sier-Bath ® Rotary Pumps TKL™ Pumps United Centrifugal ® Pumps Western Land Roller™ Irrigation Pumps Wilson-Snyder ® Pumps Worthington ® Pumps 2 Worthington Simpson™ Pumps flowserve.com Pump Designs Flowserve offers a wide range of complementary pump types, built to recognized global standards Committed to the Complete Pump and customer specification. These include: System Life Cycle • Single-stage process • Between bearings single-stage For more than two centuries, Flowserve has • Between bearings multistage served industries requiring solutions that add value and reduce costs throughout the life • Vertical cycle of a pumping system. • Submersible motor • Oil and gas • Positive displacement • Chemical • Nuclear • Power generation • Specialty • Water Available Configurations • General industry Flowserve partners • Sealed and sealless with customers to • Axially and radially split respond to the • Volute and diffuser dynamic business • Close coupled and spacer coupled conditions that • Single and double case affect them and to improve efficiency, maximize throughput and control process quality. Whether customer needs involve on-site technical assistance, equipment upgrades or broader project planning with full turnkey responsibility, Flowserve delivers professional, reliable results. -
Pumps for the Production of Renewable Energy
Technical Bulletin Pumps for the Production of Renewable Energy Experience In Motion Renewable Energy Table of Contents and Figures Pumps for the Production of Renewable Energy Table of Contents Page Figures Page Introduction Figure 1 Annual Energy Demand ................................................. 1 ................................................................................................. 1 Figure 2 Simplified Fossil Fuel Power Generation Flow Diagram ......... 2 Figure 3 Global Solar Power Map ................................................ 3 Concentrated Solar Power (CSP) Figure 4 Simplified Parabolic Trough Flow Diagram .................... 4 Figure 5 Simplified Power Tower Flow Design ............................. 5 The Technologies ...................................................................... 4 Figure 6 The Projects ............................................................................. 6 Parabolic Trough Solar Field, Storage and Steam Cycle .... 6 Figure 7 Power Tower Solar Field, Storage and Steam Cycle ...... 7 Figure 8 Typical Flashed-Steam Power Plant ............................... 8 Geothermal Figure 9 Dry-Steam Power Plant ............................................... 10 Types of Geothermal Power Plants ......................................... 10 Figure 10 Flashed-Steam Power Plant ......................................... 10 Figure 11 Binary-Cycle Power Plant ............................................ 11 Biomass Power Figure 12 Gasification Process Flow Diagram ............................ -
A Profile of the Company That's Intelligently Automating the World's
Limitorque Actuation Systems A profile of the company that’s intelligently automating the world’s valves Making valve control eas for customers When the gates of a huge hydroelectric dam open and allow millions of gallons of water to around the surge through, there’s a hidden force that moves them. When oil pipelines stretch over hundreds of miles of frozen tundra or across furnace-like wor desert sands, there’s a control mechanism that automates the flow no matter how hostile the environment. When a nuclear-powered super carrier puts to sea, it becomes a floating city supported by a network of pipes and valves delivering everything from the steam that powers the propellers to water for the kitchen sink. The complex engineering behind each of these systems depends on the precise, reliable operation of a relatively simple mechanism: a valve. For well over half a century, valves in applications from the extraordinary to the everyday have depended on valve actuators from a company called Limitorque. 2 A heritage of innovation that spans more than seven decades. Limitorque is an operating unit of Limitorque’s original torque-limiting Flowserve, a $2.5+ billion-a-year innovation was devised, company strongly focused on then was adopted by essentially all automation. Limitorque has evolved electric valve actuator makers world- over 70 years since its strategic intro- wide. Limitorque has shipped more ier duction of a “torque-limiting” design than one million actuators—which that changed an industry. have logged more than one billion Limitorque’s commitment to hours of reliable service—an incom- extraordinary valve control solutions parable achievement, unmatched by emphasizes automation choices that any other actuator supplier. -
Flowserve Pump Product Portfolio
PUMP PRODUCT PORTFOLIO Experience In Motion TABLE OF CONTENTS Experience In Motion . 4 Vertical Pumps Solving the World’s Toughest Quick Reference Chart . 53 Pumping Challenges . 6 Wet-Pit . 55 Industries . 8 Double-Case . 57 Applications . .. 10 Deep-Well . 59 Services . 12 Mechanical Seals and Systems . 14 Slurry . 60 Other Flowserve Products . 16 Solids Handling . 61 When and Where You Need Us . 17 Sump . 62 Overhung Pumps Positive Displacement Pumps Quick Reference Chart . 21 Quick Reference Chart . 65 Chemical Process — ASME, ISO . 24 Diaphragm . 66 Industrial Process . 26 Gear . 66 Solids Handling . 30 Twin Screw . 67 Slurry . 32 Multiphase Twin Screw . 67 API Process . 33 Axial Flow . 36 Between Bearings Pumps Quick Reference Chart . 39 Single-Case — Axially Split . 42 Single-Case — Axially Split — API . 42 Single-Case — Axially Split — Multistage . 44 Single-Case — Radially Split . 44 Horizontal — Multistage — Single-Case . 46 Horizontal — Multistage — Double-Case . 49 2 Flowserve Corporation Side Channel Reference Sources . 92 Quick Reference Chart . 69 Index . 93 Side Channel . 71 Vacuum Pumps & Compressors Quick Reference Chart . 77 Dry Vacuum Pumps . 79 Liquid Ring Vacuum Pumps . 79 Liquid Ring Compressors . 80 Vacuum, Membrane and Compressor Systems . 81 Specialty Products Quick Reference Chart . 83 Nuclear Pumps and Seals . 85 Hydraulic Decoking Systems . 89 Energy Recovery Devices . 90 Thruster . 90 Concrete Volute . 91 Polyolefin Reactor . 91 flowserve.com 3 EXPERIENCE IN MOTION Every day, our customers are challenged to take their plant operations to the next level . To do that, they need partners who deliver much more than products . Flowserve is answering that call . We’re working with the world’s most important providers of oil and gas, power, chemicals, water and other essential products to solve the absolute toughest challenges in fluid motion and control . -
Annual Report 2019 Contains a Full Overview of Its Corporate Stakeholder Expectations As Well As Long-Term Trends Governance Practices
Table of Contents Management report Company overview 4 Business overview 5 Disclosures about market risk 44 Group organizational structure 47 Key transactions and events in 2019 50 Recent developments 53 Research and development 54 Sustainable development 57 Corporate governance 67 Luxembourg takeover law disclosure 108 Additional information 110 Chief executive officer and chief financial officer’s responsibility statement 115 Financial statements of ArcelorMittal parent company for the year ended December 31, 2019 116 Statements of financial position 117 Statements of operations and statements of other comprehensive income 118 Statements of changes in equity 119 Statements of cash flows 120 Notes to the financial statements 121 Report of the réviseur d’entreprises agréé 170 4 Management report Company overview other countries, such as Kazakhstan, South Africa and Ukraine. In addition, ArcelorMittal’s sales of steel products History and development of the Company are spread over both developed and developing markets, which have different consumption characteristics. ArcelorMittal is the world’s leading integrated steel and ArcelorMittal’s mining operations, present in North and mining company. It results from the merger in 2007 of its South America, Africa, Europe and the CIS region, are predecessor companies Mittal Steel Company N.V. and integrated with its global steel-making facilities and are Arcelor, each of which had grown through acquisitions over important producers of iron ore and coal in their own right. many years. Since its creation ArcelorMittal has experienced periods of external growth as well consolidation Products: ArcelorMittal produces a broad range of high- and deleveraging (including through divestments), the latter quality finished and semi-finished steel products (“semis”). -
2020-Arcelormittal-Annual-Report.Pdf
Table of Contents Page Page Share capital 183 Management report Additional information Introduction Memorandum and Articles of Association 183 Company overview 3 Material contracts 192 History and development of the Company 3 Exchange controls and other limitations affecting 194 security holders Forward-looking statements 9 Taxation 195 Key transactions and events in 2020 10 Evaluation of disclosure controls and procedures 199 Risk Factors 14 Glossary - definitions, terminology and principal 201 subsidiaries Business overview Chief executive officer and chief financial officer’s 203 Business strategy 35 responsibility statement Research and development 36 Sustainable development 40 Consolidated financial statements 204 Products 54 Consolidated statements of operations 205 Sales and marketing 58 Consolidated statements of other comprehensive 206 Insurance 59 income Intellectual property 59 Consolidated statements of financial position 207 Government regulations 60 Consolidated statements of changes in equity 208 Organizational structure 67 Consolidated statements of cash flows 209 Notes to the consolidated financial statements 210 Properties and capital expenditures Property, plant and equipment 69 Report of the réviseur d’entreprises agréé - 322 consolidated financial statements Capital expenditures 91 Reserves and Resources (iron ore and coal) 93 Operating and financial review Economic conditions 99 Operating results 120 Liquidity and capital resources 132 Disclosures about market risk 137 Contractual obligations 139 Outlook 140 Management and employees Directors and senior management 141 Compensation 148 Corporate governance 164 Employees 173 Shareholders and markets Major shareholders 178 Related party transactions 180 Markets 181 New York Registry Shares 181 Purchases of equity securities by the issuer and 182 affiliated purchasers 3 Management report Introduction Company overview ArcelorMittal is one of the world’s leading integrated steel and mining companies. -
Karyn Ovelmen
Election of members of Board of Directors 8 June 2021 Karyn Ovelmen Karyn Ovelmen is a non-executive and independent Director of ArcelorMittal as well as the chairman of the Audit & Risk Committee. From January 2019 to December 31, 2019, Mrs. Ovelmen was the Gas Power Transformation Leader for the General Electric Company. Prior to that, she served as Executive Vice President and Chief Financial Officer of Flowserve, a position that she held from June 2015 to February 2017. Previously, she also served as Chief Financial Officer and Executive Vice President of LyondellBasell Industries NV from 2011 to May 2015, as Executive Vice President and Chief Financial Officer of Petroplus Holdings AG from May 2006 to September 2010 and as Executive Vice President and Chief Financial Officer of Argus Services Corporation from 2005 to 2006. Prior to that, she was Vice President of External Reporting and Investor Relations for Premcor Refining Group Inc. She also spent 12 years with PricewaterhouseCoopers, primarily serving energy industry accounts. Mrs. Ovelmen is a member of the Hess Corporation Board of Directors and a member of the Audit Committee as of November 4, 2020. Mrs. Ovelmen was a member of the Gates Industrial Corporation plc. Board of Directors as a non-executive director and was a member of their Audit Committee from December 2017 to March 2019. Mrs. Ovelmen holds a Bachelor of Arts degree from the University of Connecticut, USA, and is a Certified Public Accountant ("CPA"). Mrs. Ovelmen is a citizen of the United States of America. 1 Tye Burt Tye Burt, 63, is a non-executive and independent Director of ArcelorMittal and a member of the Appointments, Remuneration, Corporate Governance Committee and Sustainability Committee. -
Desalination
DECEMBER 2019 Application Solutions Guide DESALINATION Experience In Motion © 2017 Flowserve Corporation – November 2016 1 TABLE OF CONTENTS THE GLOBAL DESALINATION LANDSCAPE COMMUNICATING OUR VALUE Market Overview . 4 Flowserve Valve Proposition in Desalination . 38 A Closer Look at Desalination Technologies . 6 Innovative Ways Flowserve Addresses Customer – Membrane Desalination . 6 Challenges . 39 – Thermal Desalination . 8 Desalination Project Models . 10 APPENDIX A: Flowserve DWEER Operating Principles and Other Useful Information . 41 THE DESALINATION-FLOWSERVE INTERFACE Business Impact and Focus Areas . 12 B: Flowserve Energy Recovery Turbine Principles and Other Useful Information . 44 Products for Desalination — At-a-Glance . 14 – Pumps . 14 – Energy Recovery Devices . 14 Installations and Experience . 15 FLOWSERVE OPPORTUNITIES IN DESALINATION — PRODUCTS AND CAPABILITIES Overview . 17 Flowserve Products in Thermal Desalination — MSF and MED . 17 Flowserve Products and Capabilities in SWRO . 19 – RO Process Applications Overview . 19 – Pumps for SWRO . 22 – Energy Recovery Devices for SWRO . 28 – Mechanical Seals for SWRO . 32 – Valves for SWRO . 34 – Materials of Construction in SWRO . 35 – Aftermarket Opportunities . 36 2 Application Solutions Guide — Desalination THE GLOBAL DESALINATION LANDSCAPE © 2019© Flowserve2017 Flowserve Corporation Corporation – December – May 20192017 3 THE GLOBAL DESALINATION LANDSCAPE MARKET OVERVIEW The global demand for fresh water is continuously While there is plenty of optimism for growth in growing, but fresh water sources are limited and desalination, it does not come without a few not always available where population and industry significant cautions: need them. Only 2.5 percent of the world’s water • Political unrest is a risk. is fresh, and 70 percent of this remains frozen • Anticipated restructuring and/or privatization of in polar ice caps and snow. -
PRODUCT CATALOG Pumps | Seals | Valves | Actuation
PRODUCT CATALOG Pumps | Seals | Valves | Actuation Experience In Motion flowserve.com 1 TABLE OF CONTENTS Introduction . 4 Valves . .140 Industries . 6 Ball . 142 Services . .8 Butterfly . 158 Rotary Control . .162 Pumps . 10 Linear Control . .168 Overhung . 12 Severe Service Control . 178 Between Bearings . .30 Gate . .186 Vertical . 44 Globe . 190 Positive Displacement . 56 Check . .198 Side Channel . .60 Plug . 206 Vacuum Pumps & Compressors . 68 Specialty Products . 74 Actuation & Instrumentation . 216 Electric Actuation . .218 Seals . .84 Gearboxes . 226 Standard Cartridge . 86 Fluid Power Actuation . .230 Pusher . 90 Positioners . 242 Metal Bellows . 98 Switch Boxes . 250 Mixer . 104 Software . 254 Compressor Seals and Systems . .108 Slurry . 114 Index . .258 Gas Barrier and Containment . 118 OEM and Special Duty . 122 Seal Support Systems . .128 Accessories . .134 2 Flowserve Corporation Pumping systems from Flowserve meet customer demands in the most arduous services . Our world-renowned brands of pre-engineered, engineered and special purpose pumps give customers access to the PUMPS 10 most impressive portfolio of proven hydraulic and mechanical know-how . Whether for pumps, compressors, mixers or steam turbines, Flowserve mechanical sealing solutions keep rotating equipment running safely and efficientl . You’ll find them in the toughest applications, such a SEALS 84 flashing hyd ocarbons, abrasive slurries and ultra-high pressure gases . Flowserve valves are found in the world’s toughest industries, where reliable performance is the only option . High temperatures, ultra-high pressures, erosion and corrosion are at the core of the dozens of VALVES 140 leading brands that comprise our broad valve portfolio . From positioners and switches to remotely controlled, fully automated electric, hydraulic and pneumatic actuators, customers depend on ACTUATION & 216 the full range of intelligent automation solutions from Flowserve to INSTRUMENTATION help their processes run smarter, safer and more efficientl . -
Mt- 31.12.2019
UNITED STATES SECURITIES AND EXCHANGE COMMISSION Washington, D.C. 20549 FORM 20-F ¨ REGISTRATION STATEMENT PURSUANT TO SECTION 12(b) OR (g) OF THE SECURITIES EXCHANGE ACT OF 1934 OR x ANNUAL REPORT PURSUANT TO SECTION 13 OR 15(d) OF THE SECURITIES EXCHANGE ACT OF 1934 For the fiscal year ended December 31, 2019 OR ¨ TRANSITION REPORT PURSUANT TO SECTION 13 OR 15(d) OF THE SECURITIES EXCHANGE ACT OF 1934 OR ¨ SHELL COMPANY REPORT PURSUANT TO SECTION 13 OR 15(d) OF THE SECURITIES EXCHANGE ACT OF 1934 Commission file number 001-35788 ARCELORMITTAL (Exact name of Registrant as specified in its charter) N/A (Translation of Registrant’s name into English) Grand Duchy of Luxembourg (Jurisdiction of incorporation or organization) 24-26, Boulevard d’Avranches, L-1160 Luxembourg, Grand Duchy of Luxembourg (Address of principal executive offices) Henk Scheffer, Company Secretary, 24-26, Boulevard d’Avranches, L-1160 Luxembourg, Grand Duchy of Luxembourg. Fax: +352 4792 2235 (Name, Telephone, E-mail and/or Facsimile number and Address of Company Contact Person) Securities registered or to be registered pursuant to Section 12(b) of the Act: Title of each class Trading Symbol(s) Name of each exchange on which registered Ordinary Shares MT New York Stock Exchange Securities registered or to be registered pursuant to Section 12(g) of the Act: None Securities for which there is reporting obligation pursuant to Section 15(d) of the Act: None Indicate the number of outstanding shares of the issuer’s classes of capital or common stock as of the close of the period covered by the annual report: Ordinary Shares 1,012,079,421 Indicate by check mark if the registrant is a well-known seasoned issuer, as defined in Rule 405 of the Securities Act. -
Annual Report 2016 2 Management Report Management Report 3
Management report 1 Annual Report 2016 2 Management report Management report 3 Table of contents Management Report Company overview ____________________________________________________________________________________________ 4 Business overview _____________________________________________________________________________________________ 5 Disclosures about market risks ___________________________________________________________________________________ 28 Group operational structure _____________________________________________________________________________________ 30 Key transactions and events in 2016 _______________________________________________________________________________ 32 Recent developments __________________________________________________________________________________________ 33 Corporate governance _________________________________________________________________________________________ 33 > Luxembourg takeover law disclosure_____________________________________________________________________________ 59 Additional information __________________________________________________________________________________________ 60 Chief executive officer and chief financial officer’s responsibility statement _______________________________________________ 63 Consolidated financial statements for the year ended December 31, 2016 ________________________________________________ 64 Consolidated statements of operations ____________________________________________________________________________ 65 Consolidated statements of other -
Valve, Actuation and Instrumentation Portfolio
VALVE, ACTUATION AND INSTRUMENTATION PORTFOLIO Experience In Motion TABLE OF CONTENTS Experience In Motion . 4 Linear Control Valves Precision Control for the Toughest Flow Quick Reference Chart . 43 Management Challenges . 6 Linear Globe/Angle . 45 Industries . 8 Linear Tank Bottom . 51 Services . 10 Other Flowserve Products . 12 Severe Service Control Valves and Trim When and Where You Need Us . 13 Quick Reference Chart . 53 Valves Introduction . 15 Anti-Erosion . 55 Valves for Cavitation Elimination . 55 Ball Valves Noise Reduction . 56 Quick Reference Chart . 17 Cavitation Control . 57 Floating . 20 Trim for Cavitation Elimination . 58 Segmented . 22 Trunnion-Mounted . 22 Gate Valves Rising Stem . 25 Quick Reference Chart . 61 Lined . 26 Flexible Split Wedge . 62 Top-Entry . 29 Flexible Wedge . 62 Parallel Slide . 63 Butterfly Valves Split Wedge . 63 Quick Reference Chart . 33 Slab . 63 Double-Offset . .. 34 Triple-Offset . .. 34 Globe Valves Lined . 35 Quick Reference Chart . 65 Y-Pattern . 67 Rotary Control Valves T-Pattern . 69 Quick Reference Chart . 37 Eccentric Plug . 38 Check Valves Segmented Ball . 38 Quick Reference Chart . 73 High-Performance Butterfly . 39 Piston (Lift) . 75 Trunnion-Mounted Control Ball . 40 Swing . 77 Floating Control Ball . 41 Tilting Disk . 77 2 Flowserve Corporation Plug Valves Positioners Quick Reference Chart . 81 Quick Reference Chart . 117 Non-Lubricated . 83 Digital . 119 Lubricated . 84 Analog . 122 Lined . 89 Switch Boxes Actuation & Instrumentation Quick Reference Chart . .. 125 Introduction . 91 Switch Boxes . 126 Electric Actuation Software Quick Reference Chart . 93 Quick Reference Chart . .. 129 Intrusive Multi-Turn . 95 Software . 130 Non-Intrusive Quarter-Turn . 96 Non-Intrusive Multi-Turn . 96 Index .