Lean Miller Cycle System Development for Light-Duty Vehicles
Total Page:16
File Type:pdf, Size:1020Kb
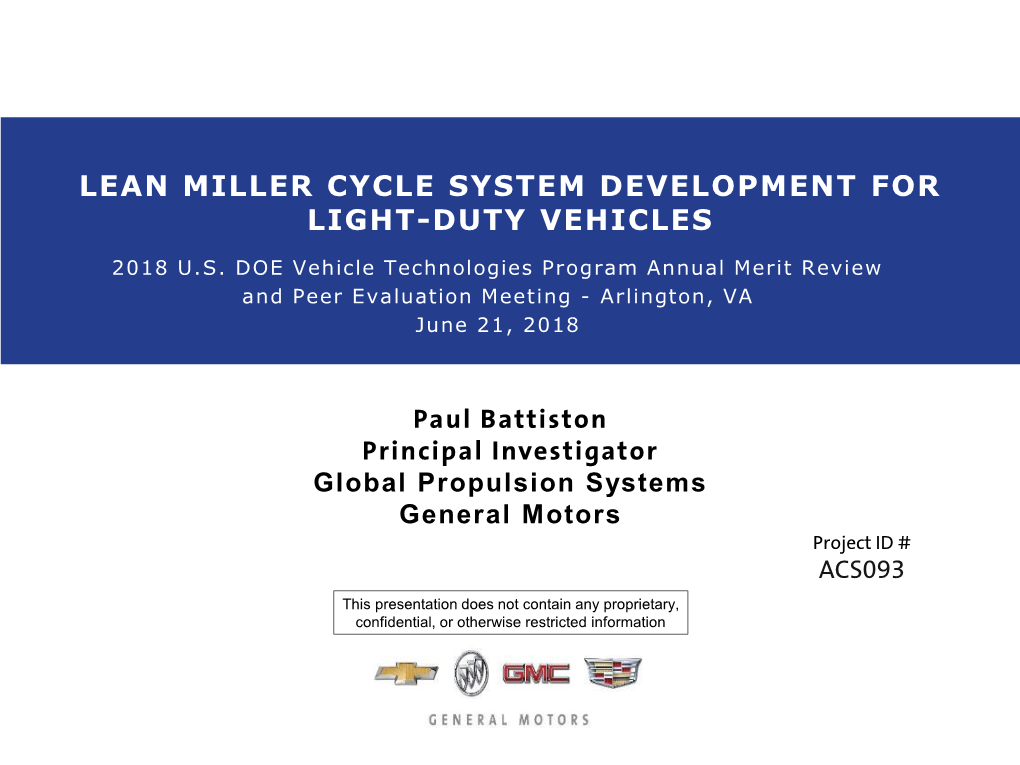
Load more
Recommended publications
-
Hybrid Electric Vehicles: a Review of Existing Configurations and Thermodynamic Cycles
Review Hybrid Electric Vehicles: A Review of Existing Configurations and Thermodynamic Cycles Rogelio León , Christian Montaleza , José Luis Maldonado , Marcos Tostado-Véliz * and Francisco Jurado Department of Electrical Engineering, University of Jaén, EPS Linares, 23700 Jaén, Spain; [email protected] (R.L.); [email protected] (C.M.); [email protected] (J.L.M.); [email protected] (F.J.) * Correspondence: [email protected]; Tel.: +34-953-648580 Abstract: The mobility industry has experienced a fast evolution towards electric-based transport in recent years. Recently, hybrid electric vehicles, which combine electric and conventional combustion systems, have become the most popular alternative by far. This is due to longer autonomy and more extended refueling networks in comparison with the recharging points system, which is still quite limited in some countries. This paper aims to conduct a literature review on thermodynamic models of heat engines used in hybrid electric vehicles and their respective configurations for series, parallel and mixed powertrain. It will discuss the most important models of thermal energy in combustion engines such as the Otto, Atkinson and Miller cycles which are widely used in commercial hybrid electric vehicle models. In short, this work aims at serving as an illustrative but descriptive document, which may be valuable for multiple research and academic purposes. Keywords: hybrid electric vehicle; ignition engines; thermodynamic models; autonomy; hybrid configuration series-parallel-mixed; hybridization; micro-hybrid; mild-hybrid; full-hybrid Citation: León, R.; Montaleza, C.; Maldonado, J.L.; Tostado-Véliz, M.; Jurado, F. Hybrid Electric Vehicles: A Review of Existing Configurations 1. Introduction and Thermodynamic Cycles. -
Development of Miller Cycle Gas Engine for Cogeneration
4. 9 & FR0105396 DEVELOPMENT OF MILLER CYCLE GAS ENGINE FOR COGENERATION DEVELOPPEMENT D UN MOTEUR A GAZ A CYCLE DE MILLER DESTINE A LA COGENERATION N. Tsukida , A.Sakakura, Y.Murata, and K. Okamoto Tokyo Gas CO.,LTD , Japan T.Abe and T. Takemoto Yanmar Diesel Engine CO.,LTD , Japan ABSTRACT We have developed a 300 kW gas engine cogeneration system for practical use that uses natural gas.Using a gas engine operated under conditions with an excess air ratio X =1 that is able to use a three way catalyst to purify the exhaust gases,we were able to achieve high efficiency through the application of the Miller Cycle, as well as a low NOx output. In terms of product specifications, we were able to achieve an electrical efficiency of 34.2% and a heat recovery efficiency of 49.3%, making an overall efficiency of 83.5% as a cogeneration system. RESUME Nous avons developpe un systeme de cogeneration de 300 kW avec moteur au gaz natural et tout a fait utilisable dans la pratique. Avec un moteur a gaz fonctionnant dans les conditions d ’un rapport d ’exces d ’air de X = 1 et capable d ’utiliser un catalyseur trois voies pour purifier les gaz d ’echappement, nous avons ete en mesure d ’obtenir un rendement eleve en appliquant le Cycle de Miller, et d ’obtenir egalement une faible emission d ’oxydes d ’azote. En termes de performances techniques du produit, nous avons obtenu un rendement electrique de 34,2 % et un rendement de recuperation thermique de 49,3 %, ce qui donne un rendement total de 83,5 % pour le systeme de cogeneration. -
Generation of Entropy in Spark Ignition Engines
Int. J. of Thermodynamics ISSN 1301-9724 Vol. 10 (No. 2), pp. 53-60, June 2007 Generation of Entropy in Spark Ignition Engines Bernardo Ribeiro, Jorge Martins*, António Nunes Universidade do Minho, Departamento de Engenharia Mecânica 4800-058 Guimarães PORTUGAL [email protected] Abstract Recent engine development has focused mainly on the improvement of engine efficiency and output emissions. The improvements in efficiency are being made by friction reduction, combustion improvement and thermodynamic cycle modification. New technologies such as Variable Valve Timing (VVT) or Variable Compression Ratio (VCR) are important for the latter. To assess the improvement capability of engine modifications, thermodynamic analysis of indicated cycles of the engines is made using the first and second laws of thermodynamics. The Entropy Generation Minimization (EGM) method proposes the identification of entropy generation sources and the reduction of the entropy generated by those sources as a method to improve the thermodynamic performance of heat engines and other devices. A computer model created and implemented in MATLAB Simulink was used to simulate the conventional Otto cycle and the various processes (combustion, free expansion during exhaust, heat transfer and fluid flow through valves and throttle) were evaluated in terms of the amount of the entropy generated. An Otto cycle, a Miller cycle (over-expanded cycle) and a Miller cycle with compression ratio adjustment are studied using the referred model in order to evaluate the amount of entropy generated in each cycle. All cycles are compared in terms of work produced per cycle. Keywords: IC engines, Miller cycle, entropy generation, over-expanded cycle 1. -
Thermodynamics of Power Generation
THERMAL MACHINES AND HEAT ENGINES Thermal machines ......................................................................................................................................... 1 The heat engine ......................................................................................................................................... 2 What it is ............................................................................................................................................... 2 What it is for ......................................................................................................................................... 2 Thermal aspects of heat engines ........................................................................................................... 3 Carnot cycle .............................................................................................................................................. 3 Gas power cycles ...................................................................................................................................... 4 Otto cycle .............................................................................................................................................. 5 Diesel cycle ........................................................................................................................................... 8 Brayton cycle ..................................................................................................................................... -
An Analytic Study of Applying Miller Cycle to Reduce Nox Emission from Petrol Engine Yaodong Wang, Lin Lin, Antony P
An analytic study of applying miller cycle to reduce nox emission from petrol engine Yaodong Wang, Lin Lin, Antony P. Roskilly, Shengchuo Zeng, Jincheng Huang, Yunxin He, Xiaodong Huang, Huilan Huang, Haiyan Wei, Shangping Li, et al. To cite this version: Yaodong Wang, Lin Lin, Antony P. Roskilly, Shengchuo Zeng, Jincheng Huang, et al.. An analytic study of applying miller cycle to reduce nox emission from petrol engine. Applied Thermal Engineering, Elsevier, 2007, 27 (11-12), pp.1779. 10.1016/j.applthermaleng.2007.01.013. hal-00498945 HAL Id: hal-00498945 https://hal.archives-ouvertes.fr/hal-00498945 Submitted on 9 Jul 2010 HAL is a multi-disciplinary open access L’archive ouverte pluridisciplinaire HAL, est archive for the deposit and dissemination of sci- destinée au dépôt et à la diffusion de documents entific research documents, whether they are pub- scientifiques de niveau recherche, publiés ou non, lished or not. The documents may come from émanant des établissements d’enseignement et de teaching and research institutions in France or recherche français ou étrangers, des laboratoires abroad, or from public or private research centers. publics ou privés. Accepted Manuscript An analytic study of applying miller cycle to reduce nox emission from petrol engine Yaodong Wang, Lin Lin, Antony P. Roskilly, Shengchuo Zeng, Jincheng Huang, Yunxin He, Xiaodong Huang, Huilan Huang, Haiyan Wei, Shangping Li, J Yang PII: S1359-4311(07)00031-2 DOI: 10.1016/j.applthermaleng.2007.01.013 Reference: ATE 2070 To appear in: Applied Thermal Engineering Received Date: 5 May 2006 Revised Date: 2 January 2007 Accepted Date: 14 January 2007 Please cite this article as: Y. -
Miller-Cycle on a Heavy Duty Diesel Engine
Miller-cycle on a heavy duty diesel engine Henrik Dembinski Clive Lewis Master of Science Thesis MMK 2009:1 MFM124 KTH Industrial Engineering and Management Machine Design SE-100 44 STOCKHOLM Master of Science Thesis MMK2 2009:1 MFM124 Miller-cycle on a heavy duty diesel engine Clive Lewis Henrik Dembinski Approved Examiner Supervisor 090128 Prof. Hans-Erik Ångström Prof. Hans-Erik Ångström Commissioner Contact person Scania CV AB Stefan Olsson 1. Sammanfattning Denna report beskriver ett examensarbete inom ämnet förbränningsmotorteknik och är utfört på Scania CV AB i Södertälje i sammarbete med Kungliga Tekniska Högskolan i Stockholm. Fordonsindustrin står inför nya utmaningar när en större fokusering på koldioxid (CO2) utsläpp från väg-gående fordon efterfrågas, vilket är direkt kopplat till fordonets bränsleförbrukning. Detta skall klaras av med lägre övriga emissioner i form av kväveoxider (NOx) och rök som är de två stora problemområdena för en dieselmotor. Scania vill därför undersöka potentialen med Miller cykling och om detta koncept skulle kunna implementeras på en lågeffektsmotor. Idén är att byta hög effekt mot verkningsgrad på motorer i motorprogrammet som inte utnyttjar hela grundmotorns effektpotential. Med Miller cykling menas senare- eller tidigarelagd stängning av insugsventilen och på så sätt öka graden expansionsarbete i förhållande till kompressionsarbete, dvs. öka den indikerade verkningsgraden. Då detta medför en minskning i effektiv slagvolym då cylindern inte fylls med luft helt måste kompensering i laddtryck göras för att motorn skall få samma luftmängd. En del kompressionsarbete görs då alltså utanför cylindern som belastar turbosystemet och inte motorn. En ny turbomatchning måste således göras då förflyttningar i turbomappen görs på ett mindre fördelaktigt sätt. -
Turbocharging & Miller Cycle
DRIVING AUTOMOTIVE INNOVATION 2 Turbocharging & Miller Cycle • Turbocharging enables engine downsizing for significant fuel economy benefits without performance compromise. • More stringent regulation is demanding more efficiency from internal combustion engines. • One solution to increasing engine efficiency is by adopting a Miller Cycle strategy. • Technologies available today including, VNT (variable nozzle turbines) Turbochargers, Variable Valve Timing & Valve Lift, and Direct Injection, allow engines to use higher levels of Miller to meet future regulation. © 2015 by Honeywell International Inc. All rights reserved. 3 How a Turbocharger Works © 2015 by Honeywell International Inc. All rights reserved. Small Engine Fuel Economy, Big Engine Performance © 2015 by Honeywell International Inc. All rights reserved. 4 Modern Turbo Gasoline Engines No-Compromise Solution More Stringent Regulations 3L 6 Cylinders 2L 4 Cylinders Enacted Targets* Naturally Aspirated Turbocharged MPG Improvement By 2021 MPG Improvement By 2020 MPG Improvement By 2025 240 = 240 Horsepower Horsepower MPG Improvement By 2022 +30% +25% 20% Torque Fuel Efficiency MPG Improvement CO2 By 2017 * Source ICCT Fuel Economy Standards – August 2015 Light Vehicles Only. MPG Improvement vs 2014 Levels. † Equivalent Standards to Euro 5 (5mg/km PM, 60-180mg/km NOx) and Euro 6 (5mg/km PM, 60-80mg/km NOx) © 2015 by Honeywell International Inc. All rights reserved. Turbochargers are a Key Enabler to Current & Future Regulation © 2015 by Honeywell International Inc. All rights reserved. Increasing Gasoline Engine Efficiency Normal Combustion 70 65 Piston 60 Flame Propagation 55 Knock 50 Piston 45 ɣ = 1.4 Ideal conversion efficiency [%] Ideal conversion efficiency Increasing Compression Ratio 40 4 6 8 10 12 14 16 18 Geometric Compression Ratio => Ɛ [-] © 2015 by Honeywell International Inc. -
Machinery/Automation
Machinery/Automation Miniature Blimps for Surveillance and Collection of Samples These robots could follow complex three-dimensional trajectories through buildings. NASA’s Jet Propulsion Laboratory, Pasadena, California Miniature blimps are under develop- structures on Earth. The widely per- 1.2 kg. It can be filled in 30 seconds ment as robots for use in exploring the ceived need for means to thwart attacks from the small bottle shown on the thick, cold, nitrogen atmosphere of Sat- on buildings and to mitigate the effects table in the figure. This blimp also op- urn’s moon, Titan. Similar blimps can of such attacks has prompted considera- erates under radio control and carries a also be used for surveillance and collec- tion of the use of robots. Relative to video camera. This blimp has been tion of biochemical samples in build- “rover”-type (wheeled) robots that have equipped with an ultralight (170 g) au- ings, caves, subways, and other, similar been considered for such uses, minia- tomatic pilot manufactured commer- ture blimps offer the advantage of abil- cially for radio-controlled small air- ity to move through the air in any direc- planes. This autopilot enables the tion and, hence, to perform tasks that control system of the blimp to utilize are difficult or impossible for wheeled the Global Positioning System in fol- robots, including climbing stairs and lowing a trajectory through as many as looking through windows. In addition, 60 different waypoints. This autopilot miniature blimps are expected to have also utilizes ultrasound for precise mea- greater range and to cost less, relative to surement and control of altitude when wheeled robots. -
Performance Study for Miller Cycle Natural Gas Engine Based on GT-Power
Journal of Clean Energy Technologies, Vol. 3, No. 5, September 2015 Performance Study for Miller Cycle Natural Gas Engine Based on GT-Power Songsong Song and Hongguang Zhang [4]. Abstract—In order to improve the thermal efficiency of However, few attentions have been paid to the working natural gas engine and reduce the NOx emission from engine, process of the natural gas engine. In this paper, GT-Power this paper presented the technical route which applied Miller software was used to simulate the turbocharged natural gas cycle to turbocharged lean-burn natural gas engine. GT-Power engine. BSFC and NO emission were analyzed for two software was used to model the turbocharged natural gas x engine, and simulation research based on Miller cycle was kinds of engine working processes based on Otto cycle and performed according to various engine loads in the engine Miller cycle respectively. speed range of 2000-5000rpm. The simulation results showed that, under part load (50% of the engine full load) operating conditions of the turbocharged lean-burn natural gas engine, II. METHODOLOGY compared with Otto cycle, Miller cycle can reduce the brake specific fuel consumption (BSFC) and NOx emission. Under In order to improve the thermal efficiency of the engine, high load and low speed as well as moderate load and high Ralph Miller proposed Miller cycle in 1947 [5], which is a speed operating conditions, Miller cycle can effectively reduce kind of over-expanded cycle, as shown in Fig. 1. the BSFC. Under high load and low speed or high speed operating conditions, the NOx emission can be reduced apparently. -
MARTINS-Generation of Entropy in S I Engines
Int. J. of Thermodynamics ISSN 1301-9724 Vol. 10 (No. 2), pp. 53-60, June 2007 Generation of Entropy in Spark Ignition Engines Bernardo Ribeiro, Jorge Martins*, António Nunes Universidade do Minho Departamento de Engenharia Mecânica 4800-058 – Guimarães – PORTUGAL [email protected] Abstract Recent engine development has focused mainly on the improvement of engine efficiency and output emissions. The improvements in efficiency are being made by friction reduction, combustion improvement and thermodynamic cycle modification. New technologies such as Variable Valve Timing (VVT) or Variable Compression Ratio (VCR) are important for the latter. To assess the improvement capability of engine modifications, thermodynamic analysis of indicated cycles of the engines is made using the first and second laws of thermodynamics. The Entropy Generation Minimization (EGM) method proposes the identification of entropy generation sources and the reduction of the entropy generated by those sources as a method to improve the thermodynamic performance of heat engines and other devices. A computer model created and implemented in MATLAB Simulink was used to simulate the conventional Otto cycle and the various processes (combustion, free expansion during exhaust, heat transfer and fluid flow through valves and throttle) were evaluated in terms of the amount of the entropy generated. An Otto cycle, a Miller cycle (over-expanded cycle) and a Miller cycle with compression ratio adjustment are studied using the referred model in order to evaluate the amount of entropy generated in each cycle. All cycles are compared in terms of work produced per cycle. Keywords: IC engines, Miller cycle, entropy generation, over-expanded cycle 1. -
Thermal Efficiency and Emission Analysis of Advanced
Purdue University Purdue e-Pubs Open Access Dissertations Theses and Dissertations Fall 2014 Thermal efficiency and emission analysis of advanced thermodynamic strategies in a multi- cylinder diesel engine utilizing valve-train flexibility Chuan Ding Purdue University Follow this and additional works at: https://docs.lib.purdue.edu/open_access_dissertations Part of the Mechanical Engineering Commons Recommended Citation Ding, Chuan, "Thermal efficiency and emission analysis of advanced thermodynamic strategies in a multi-cylinder diesel engine utilizing valve-train flexibility" (2014). Open Access Dissertations. 257. https://docs.lib.purdue.edu/open_access_dissertations/257 This document has been made available through Purdue e-Pubs, a service of the Purdue University Libraries. Please contact [email protected] for additional information. *UDGXDWH6FKRRO(7')RUP 5HYLVHG 0114 PURDUE UNIVERSITY GRADUATE SCHOOL Thesis/Dissertation Acceptance 7KLVLVWRFHUWLI\WKDWWKHWKHVLVGLVVHUWDWLRQSUHSDUHG %\Chuan Ding (QWLWOHG Thermal Efficiency and Emission Analysis of Advanced Thermodynamic Strategies in a Multi-cylinder Diesel Engine Utilizing Valve-train Flexibility Doctor of Philosophy )RUWKHGHJUHHRI ,VDSSURYHGE\WKHILQDOH[DPLQLQJFRPPLWWHH GREGORY M. SHAVER JOHN H. LUMKES PETER H. MECKL ROBERT P. LUCHT 7RWKHEHVWRIP\NQRZOHGJHDQGDVXQGHUVWRRGE\WKHVWXGHQWLQWKHThesis/Dissertation Agreement. Publication Delay, and Certification/Disclaimer (Graduate School Form 32)WKLVWKHVLVGLVVHUWDWLRQ adheres to the provisions of 3XUGXH8QLYHUVLW\¶V³3ROLF\RQ,QWHJULW\LQ5HVHDUFK´DQGWKHXVHRI -
The Miller Cycle on Single-Cylinder and Serial Configurations of a Heavy-Duty Engine
The Miller Cycle on Single-Cylinder and Serial Configurations of a Heavy-Duty Engine VARUN VENKATARAMAN Master of Science Thesis Stockholm, Sweden 2017 The Miller Cycle on Single-Cylinder and Serial Configurations of a Heavy-Duty Engine Varun Venkataraman Master of Science Thesis TRITA-ITM-EX 2018:28 KTH Industrial Engineering and Management Machine Design, Division of Internal Combustion Engines SE-100 44 STOCKHOLM Examensarbete TRITA-ITM-EX 2018:28 Millercykeln i en Encylindrig och Flercylindrig Lastbilsmotor Varun Venkataraman Godkänt Examinator Handledare 2017-12-22 Anders Christiansen Anders Christiansen Erlandsson Erlandsson Uppdragsgivare Kontaktperson Anders Christiansen Erlandsson Sammanfattning I jämförelse med sina föregångare, har moderna lastbilsmotorer genomgått en betydande utveckling och har utvecklats till effektiva kraftmaskiner med låga utsläpp genom införandet av avancerade avgasbehandlingssystem. Trots att de framsteg som gjorts under utvecklingen av lastbilsmotorer har varit betydande, så framhäver de framtida förväntningarna vad gäller prestanda, bränsleförbrukning och emissioner behovet av snabba samt storskaliga förbättringar av dessa parametrar för att förbränningsmotorn ska fortsätta att vara konkurrenskraftig och hållbar. Utmaningen i att uppfylla dessa till synes enkla krav är den invecklade, ogynnsamma balansgång som måste göras mellan parametrarna. Förbränningsmotorns kärna är förbränningsprocessen, som i sin tur är kopplad till motorns luftbehandlings- och bränsleregleringssystem. I denna studie undersöks