Effect of the Miller Cycle on the Performance of Turbocharged Hydrogen Internal Combustion Engines ⇑ Qing-He Luo, Bai-Gang Sun
Total Page:16
File Type:pdf, Size:1020Kb
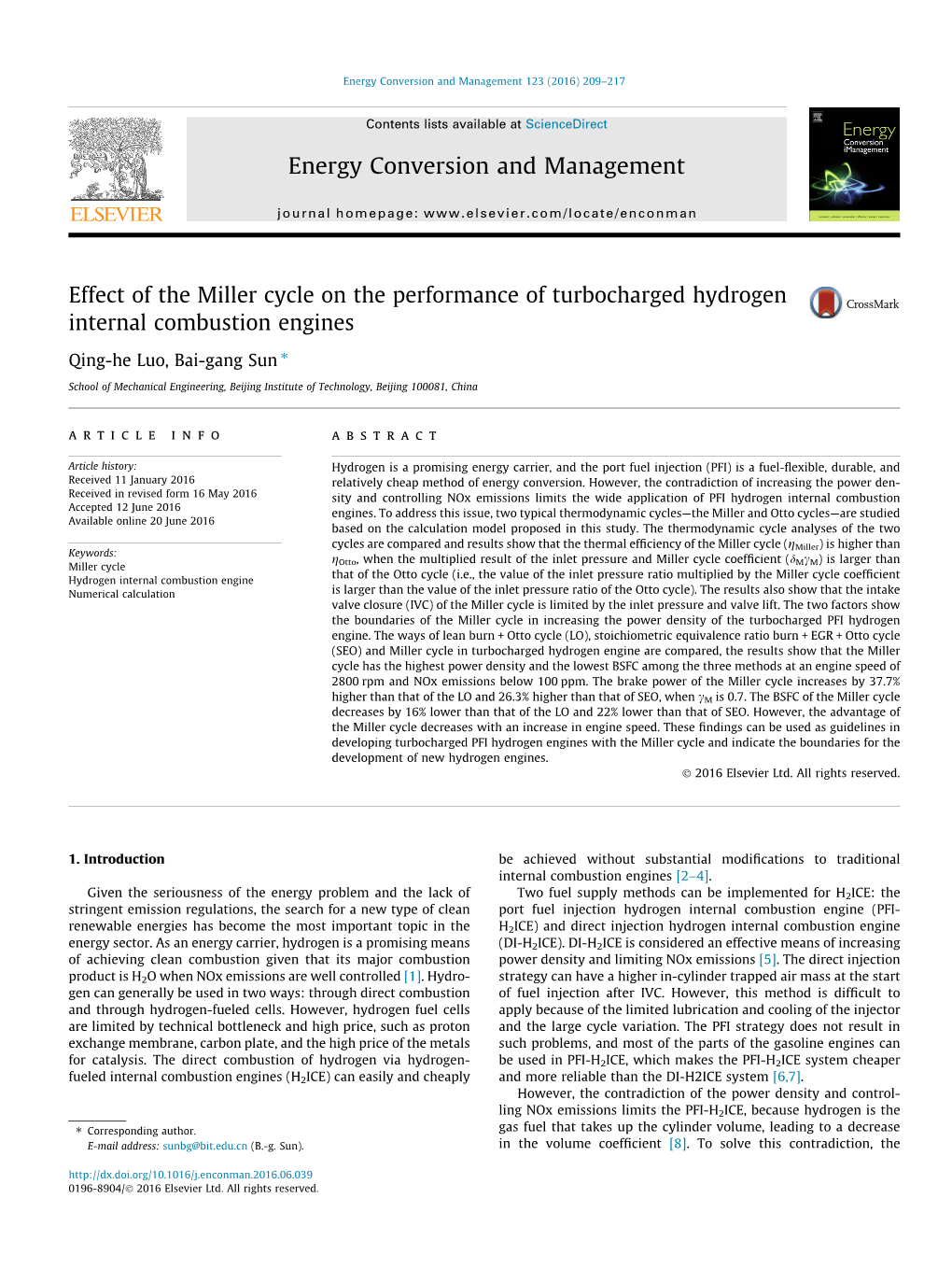
Load more
Recommended publications
-
Constant Volume Combustion Cycle for IC Engines
Constant Volume Combustion Cycle for IC Engines Jovan Dorić Assistant This paper presents an analysis of the internal combustion engine cycle in University of Novi Sad Faculty of Technical Sciences cases when the new unconventional piston motion law is used. The main goal of the presented unconventional piston motion law is to make a Ivan Klinar realization of combustion during constant volume in an engine’s cylinder. Full Professor The obtained results are shown in PV (pressure-volume) diagrams of University of Novi Sad Faculty of Technical Sciences standard and new engine cycles. The emphasis is placed on the shortcomings of the real cycle in IC engines as well as policies that would Marko Dorić contribute to reducing these disadvantages. For this paper, volumetric PhD student efficiency, pressure and temperature curves for standard and new piston University of Novi Sad Faculty of Agriculture motion law have been calculated. Also, the results of improved efficiency and power are presented. Keywords: constant volume combustion, IC engine, kinematics. 1. INTRODUCTION of an internal combustion engine, whose combustion is so rapid that the piston does not move during the Internal combustion engine simulation modelling has combustion process, and thus combustion is assumed to long been established as an effective tool for studying take place at constant volume [6]. Although in engine performance and contributing to evaluation and theoretical terms heat addition takes place at constant new developments. Thermodynamic models of the real volume, in real engine cycle heat addition at constant engine cycle have served as effective tools for complete volume can not be performed. -
Benchmarking a 2018 Toyota Camry 2.5L Atkinson Cycle Engine With
Downloaded from SAE International by John Kargul, Thursday, April 04, 2019 2019-01-0249 Published 02 Apr 2019 Benchmarking a 2018 Toyota Camry 2.5-Liter INTERNATIONAL. Atkinson Cycle Engine with Cooled-EGR John Kargul, Mark Stuhldreher, Daniel Barba, Charles Schenk, Stanislav Bohac, Joseph McDonald, and Paul Dekraker US Environmental Protection Agency Josh Alden Southwest Research Institute Citation: Kargul, J., Stuhldreher, M., Barba, D., Schenk, C. et al., “Benchmarking a 2018 Toyota Camry 2.5-Liter Atkinson Cycle Engine with Cooled-EGR,” SAE Technical Paper 2019-01-0249, 2019, doi:10.4271/2019-01-0249. Abstract idle, low, medium, and high load engine operation. Motoring s part of the U.S. Environmental Protection Agency’s torque, wide open throttle (WOT) torque and fuel consumption (EPA’s) continuing assessment of advanced light-duty are measured during transient operation using both EPA Tier Aautomotive technologies in support of regulatory and 2 and Tier 3 test fuels. Te design and performance of this 2018 compliance programs, a 2018 Toyota Camry A25A-FKS 2.5-liter engine is described and compared to Toyota’s published 4-cylinder, 2.5-liter, naturally aspirated, Atkinson Cycle engine data and to EPA’s previous projections of the efciency of an with cooled exhaust gas recirculation (cEGR) was bench- Atkinson Cycle engine with cEGR. The Brake Thermal marked. Te engine was tested on an engine dynamometer Efciency (BTE) map for the Toyota A25A-FKS engine shows with and without its 8-speed automatic transmission, and with a peak efciency near 40 percent, which is the highest value of the engine wiring harness tethered to a complete vehicle parked any publicly available map for a non-hybrid production gasoline outside of the test cell. -
Hybrid Electric Vehicles: a Review of Existing Configurations and Thermodynamic Cycles
Review Hybrid Electric Vehicles: A Review of Existing Configurations and Thermodynamic Cycles Rogelio León , Christian Montaleza , José Luis Maldonado , Marcos Tostado-Véliz * and Francisco Jurado Department of Electrical Engineering, University of Jaén, EPS Linares, 23700 Jaén, Spain; [email protected] (R.L.); [email protected] (C.M.); [email protected] (J.L.M.); [email protected] (F.J.) * Correspondence: [email protected]; Tel.: +34-953-648580 Abstract: The mobility industry has experienced a fast evolution towards electric-based transport in recent years. Recently, hybrid electric vehicles, which combine electric and conventional combustion systems, have become the most popular alternative by far. This is due to longer autonomy and more extended refueling networks in comparison with the recharging points system, which is still quite limited in some countries. This paper aims to conduct a literature review on thermodynamic models of heat engines used in hybrid electric vehicles and their respective configurations for series, parallel and mixed powertrain. It will discuss the most important models of thermal energy in combustion engines such as the Otto, Atkinson and Miller cycles which are widely used in commercial hybrid electric vehicle models. In short, this work aims at serving as an illustrative but descriptive document, which may be valuable for multiple research and academic purposes. Keywords: hybrid electric vehicle; ignition engines; thermodynamic models; autonomy; hybrid configuration series-parallel-mixed; hybridization; micro-hybrid; mild-hybrid; full-hybrid Citation: León, R.; Montaleza, C.; Maldonado, J.L.; Tostado-Véliz, M.; Jurado, F. Hybrid Electric Vehicles: A Review of Existing Configurations 1. Introduction and Thermodynamic Cycles. -
Development of Miller Cycle Gas Engine for Cogeneration
4. 9 & FR0105396 DEVELOPMENT OF MILLER CYCLE GAS ENGINE FOR COGENERATION DEVELOPPEMENT D UN MOTEUR A GAZ A CYCLE DE MILLER DESTINE A LA COGENERATION N. Tsukida , A.Sakakura, Y.Murata, and K. Okamoto Tokyo Gas CO.,LTD , Japan T.Abe and T. Takemoto Yanmar Diesel Engine CO.,LTD , Japan ABSTRACT We have developed a 300 kW gas engine cogeneration system for practical use that uses natural gas.Using a gas engine operated under conditions with an excess air ratio X =1 that is able to use a three way catalyst to purify the exhaust gases,we were able to achieve high efficiency through the application of the Miller Cycle, as well as a low NOx output. In terms of product specifications, we were able to achieve an electrical efficiency of 34.2% and a heat recovery efficiency of 49.3%, making an overall efficiency of 83.5% as a cogeneration system. RESUME Nous avons developpe un systeme de cogeneration de 300 kW avec moteur au gaz natural et tout a fait utilisable dans la pratique. Avec un moteur a gaz fonctionnant dans les conditions d ’un rapport d ’exces d ’air de X = 1 et capable d ’utiliser un catalyseur trois voies pour purifier les gaz d ’echappement, nous avons ete en mesure d ’obtenir un rendement eleve en appliquant le Cycle de Miller, et d ’obtenir egalement une faible emission d ’oxydes d ’azote. En termes de performances techniques du produit, nous avons obtenu un rendement electrique de 34,2 % et un rendement de recuperation thermique de 49,3 %, ce qui donne un rendement total de 83,5 % pour le systeme de cogeneration. -
RECIPROCATING ENGINES Franck Nicolleau
RECIPROCATING ENGINES Franck Nicolleau To cite this version: Franck Nicolleau. RECIPROCATING ENGINES. Master. RECIPROCATING ENGINES, Sheffield, United Kingdom. 2010, pp.189. cel-01548212 HAL Id: cel-01548212 https://hal.archives-ouvertes.fr/cel-01548212 Submitted on 27 Jun 2017 HAL is a multi-disciplinary open access L’archive ouverte pluridisciplinaire HAL, est archive for the deposit and dissemination of sci- destinée au dépôt et à la diffusion de documents entific research documents, whether they are pub- scientifiques de niveau recherche, publiés ou non, lished or not. The documents may come from émanant des établissements d’enseignement et de teaching and research institutions in France or recherche français ou étrangers, des laboratoires abroad, or from public or private research centers. publics ou privés. Distributed under a Creative Commons Attribution - NonCommercial| 4.0 International License Mechanical Engineering - 14 May 2010 -1- UNIVERSITY OF SHEFFIELD Department of Mechanical Engineering Mappin street, Sheffield, S1 3JD, England RECIPROCATING ENGINES Autumn Semester 2010 MEC403 - MEng, semester 7 - MEC6403 - MSc(Res) Dr. F. C. G. A. Nicolleau MD54 Telephone: +44 (0)114 22 27700. Direct Line: +44 (0)114 22 27867 Fax: +44 (0)114 22 27890 email: F.Nicolleau@sheffield.ac.uk http://www.shef.ac.uk/mecheng/mecheng cms/staff/fcgan/ MEng 4th year Course Tutor : Pr N. Qin European and Year Abroad Tutor : C. Pinna MSc(Res) and MPhil Course Director : F. C. G. A. Nicolleau c 2010 F C G A Nicolleau, The University of Sheffield -2- Combustion engines Table of content -3- Table of content Table of content 3 Nomenclature 9 Introduction 13 Acknowledgement 16 I - Introduction and Fundamentals of combustion 17 1 Introduction to combustion engines 19 1.1 Pistonengines.................................. -
Efficiency of Atkinson Engine at Maximum Power Density Using Temperature Dependent Specific Heats
Volume 2, Number 2, Jun. 2008 ISSN 1995-6665 JJMIE Pages 71 - 75 Jordan Journal of Mechanical and Industrial Engineering Efficiency of Atkinson Engine at Maximum Power Density using Temperature Dependent Specific Heats A. Al-Sarkhi, B. Akash *, E. Abu-Nada and I. Al-Hinti Department of Mechanical Engineering, Hashemite University, Zarqa, 13115, Jordan Abstract Thermodynamic analysis of an ideal air-standard Atkinson cycle with temperature dependant specific heat is presented in this paper. The paper outlines the effect of maximizing power density on the performance of the cycle efficiency. The power density is defined as the ratio of the power output to the maximum cycle specific volume. It showed significant effect on the performance of the cycle over the constant specific heat model. The results obtained from this work can be helpful in the thermodynamic modeling and in the evaluation of real Atkinson engines over other engines. © 2008 Jordan Journal of Mechanical and Industrial Engineering. All rights reserved Keywords: Atkinson engine; power density; temperature dependant specific heat; specific heats of air (the working fluid) were used. The maximization of the power density is defined as the ratio 1. Introduction of the maximum power to the maximum specific volume in the cycle. It takes into consideration the engine size The Atkinson cycle (the complete expansion cycle) is instead of just maximizing its power output. The inclusion named after its inventor James Atkinson in 1882 [1]. As of the engine size in the calculation of its performance is a shown in Fig. 1, the cycle involves isentropic compression very important factor from an economical point of view. -
Generation of Entropy in Spark Ignition Engines
Int. J. of Thermodynamics ISSN 1301-9724 Vol. 10 (No. 2), pp. 53-60, June 2007 Generation of Entropy in Spark Ignition Engines Bernardo Ribeiro, Jorge Martins*, António Nunes Universidade do Minho, Departamento de Engenharia Mecânica 4800-058 Guimarães PORTUGAL [email protected] Abstract Recent engine development has focused mainly on the improvement of engine efficiency and output emissions. The improvements in efficiency are being made by friction reduction, combustion improvement and thermodynamic cycle modification. New technologies such as Variable Valve Timing (VVT) or Variable Compression Ratio (VCR) are important for the latter. To assess the improvement capability of engine modifications, thermodynamic analysis of indicated cycles of the engines is made using the first and second laws of thermodynamics. The Entropy Generation Minimization (EGM) method proposes the identification of entropy generation sources and the reduction of the entropy generated by those sources as a method to improve the thermodynamic performance of heat engines and other devices. A computer model created and implemented in MATLAB Simulink was used to simulate the conventional Otto cycle and the various processes (combustion, free expansion during exhaust, heat transfer and fluid flow through valves and throttle) were evaluated in terms of the amount of the entropy generated. An Otto cycle, a Miller cycle (over-expanded cycle) and a Miller cycle with compression ratio adjustment are studied using the referred model in order to evaluate the amount of entropy generated in each cycle. All cycles are compared in terms of work produced per cycle. Keywords: IC engines, Miller cycle, entropy generation, over-expanded cycle 1. -
Performance Analysis of an Atkinson Cycle Engine Under Effective Power
Vol. 132 (2017) ACTA PHYSICA POLONICA A No. 4 Performance Analysis of an Atkinson Cycle Engine under Effective Power and Effective Power Density Conditions G. Gonca∗ Yildiz Technical University, Naval Arch. and Marine Eng. Depart., Besiktas, Istanbul, Turkey (Received November 16, 2016; in final form May 20, 2017) This study presents performance optimization of an Atkinson cycle engine using criteria named as effective power and effective power density conditions. The effects of design and operating parameters such as compression ratio, cycle pressure ratio, cycle temperature ratio, equivalence ratio, bore/stroke ratio, inlet temperature, inlet pressure, engine speed, friction coefficient, mean piston speed and stroke length, on the performance characteristics have been examined. Moreover, the energy losses have been determined as fuel energy and they have been classified as incomplete combustion losses, friction losses, heat transfer losses, and exhaust output losses. Realistic values of specific heats have been used depending on temperature of working fluid. The results of the study can be assessed as an engineering tool by the Atkinson cycle engine designers. DOI: 10.12693/APhysPolA.132.1306 PACS/topics: gasoline engine, Atkinson cycle, engine performance, power density, finite-time thermodynamics 1. Introduction on artificial neural network technique. Gahruei et al. [28] compared the performances of dual Diesel cycle and dual In the recent years, the researchers carried out several AC based on the FTT by considering irreversible energy studies [1–21] on the Miller cycle (MC) engine to dimin- losses. It was observed from the results that the perfor- ish NOx emissions by reducing the maximum combus- mance of dual AC are higher than that of dual Diesel tion temperatures of the engines. -
Thermodynamics of Power Generation
THERMAL MACHINES AND HEAT ENGINES Thermal machines ......................................................................................................................................... 1 The heat engine ......................................................................................................................................... 2 What it is ............................................................................................................................................... 2 What it is for ......................................................................................................................................... 2 Thermal aspects of heat engines ........................................................................................................... 3 Carnot cycle .............................................................................................................................................. 3 Gas power cycles ...................................................................................................................................... 4 Otto cycle .............................................................................................................................................. 5 Diesel cycle ........................................................................................................................................... 8 Brayton cycle ..................................................................................................................................... -
An Analytic Study of Applying Miller Cycle to Reduce Nox Emission from Petrol Engine Yaodong Wang, Lin Lin, Antony P
An analytic study of applying miller cycle to reduce nox emission from petrol engine Yaodong Wang, Lin Lin, Antony P. Roskilly, Shengchuo Zeng, Jincheng Huang, Yunxin He, Xiaodong Huang, Huilan Huang, Haiyan Wei, Shangping Li, et al. To cite this version: Yaodong Wang, Lin Lin, Antony P. Roskilly, Shengchuo Zeng, Jincheng Huang, et al.. An analytic study of applying miller cycle to reduce nox emission from petrol engine. Applied Thermal Engineering, Elsevier, 2007, 27 (11-12), pp.1779. 10.1016/j.applthermaleng.2007.01.013. hal-00498945 HAL Id: hal-00498945 https://hal.archives-ouvertes.fr/hal-00498945 Submitted on 9 Jul 2010 HAL is a multi-disciplinary open access L’archive ouverte pluridisciplinaire HAL, est archive for the deposit and dissemination of sci- destinée au dépôt et à la diffusion de documents entific research documents, whether they are pub- scientifiques de niveau recherche, publiés ou non, lished or not. The documents may come from émanant des établissements d’enseignement et de teaching and research institutions in France or recherche français ou étrangers, des laboratoires abroad, or from public or private research centers. publics ou privés. Accepted Manuscript An analytic study of applying miller cycle to reduce nox emission from petrol engine Yaodong Wang, Lin Lin, Antony P. Roskilly, Shengchuo Zeng, Jincheng Huang, Yunxin He, Xiaodong Huang, Huilan Huang, Haiyan Wei, Shangping Li, J Yang PII: S1359-4311(07)00031-2 DOI: 10.1016/j.applthermaleng.2007.01.013 Reference: ATE 2070 To appear in: Applied Thermal Engineering Received Date: 5 May 2006 Revised Date: 2 January 2007 Accepted Date: 14 January 2007 Please cite this article as: Y. -
Thermodynamic Modeling of an Atkinson Cycle with Respect to Relative AirFuel Ratio, Fuel Mass Flow Rate and Residual Gases R
Vol. 124 (2013) ACTA PHYSICA POLONICA A No. 1 Thermodynamic Modeling of an Atkinson Cycle with respect to Relative AirFuel Ratio, Fuel Mass Flow Rate and Residual Gases R. Ebrahimi∗ Department of Agriculture Machine Mechanics, Shahrekord University, P.O. Box 115, Shahrekord, Iran (Received March 26, 2013; in nal form April 17, 2013) The performance of an air standard Atkinson cycle is analyzed using nite-time thermodynamics. The results show that if the compression ratio is less than a certain value, the power output increases with increasing relative airfuel ratio, while if the compression ratio exceeds a certain value, the power output rst increases and then starts to decrease with increase of relative airfuel ratio. With a further increase in compression ratio, the increase in relative airfuel ratio results in decrease of the power output. Throughout the compression ratio range, the power output increases with increase of fuel mass ow rate. The results also show that if the compression ratio is less than a certain value, the power output increases with increase of residual gases, on the contrast, if the compression ratio exceeds a certain value, the power output decreases with increase of residual gases. The results obtained herein can provide guidance for the design of practical Atkinson engines. DOI: 10.12693/APhysPolA.124.29 PACS: 05.70.Ln, 82.60.Fa, 88.05.−b 1. Introduction formance of an air standard Atkinson cycle under the re- striction of the maximum cycle temperature. The results The Atkinson cycle is a type of internal combustion show that the power output as well as the eciency, for engine, which was designed and built by a British engi- which the maximum power-output occurs, will rise with neer James Atkinson in 1882. -
Atkinson Engine - Stop/Start Systems
A survey of state-of-the-art fuel efficiency ATKINSON CYCLE ENGINES & technologies and designs for passenger cars STOP-START SYSTEMS Driving Automotive Innovation Conference Washington DC, September 13th, 2016 V 1.13 Dr. Dean Tomazic, Executive VP & CTO, FEV North America, Inc. © by FEV – all rights reserved. Confidential – no passing on to third parties Agenda n Introduction n Development Trends - Atkinson Engine - Stop/Start Systems n Summary V 1.13 © by FEV – all rights reserved. Confidential – no passing on to third parties | 2 Development Trends Engines ATKINSON ENGINE & STOP-START TECHNOLOGY Atkinson Engine Technology n Current conventional engines exhibit efficiency losses due to incomplete in-cylinder expansion n Atkinson cycle increases efficiency at expense of power density n Changes to the engines’ valve timing and compression ratio mitigate these losses n Max. engine efficiency demonstrated in field: up to 40% (Toyota Prius) James Atkinson Patent (1882) Stop-Start Technology n Current conventional engines continue running while vehicle is not moving à waste of fuel n Mechanism to shut off engine when not used and turn it back on quickly is highly desired n Stop-start systems allow to only operate the engine when needed to propel the vehicle n System is directly attached to the engine and hence relatively simple n Impressive improvements in overall fuel consumption demonstrated in the field V 1.13 Source: FEV research © by FEV – all rights reserved. Confidential – no passing on to third parties | 3 Development Trends Engines