Electroactive Fibre Sensor Systems for Fluidics
Total Page:16
File Type:pdf, Size:1020Kb
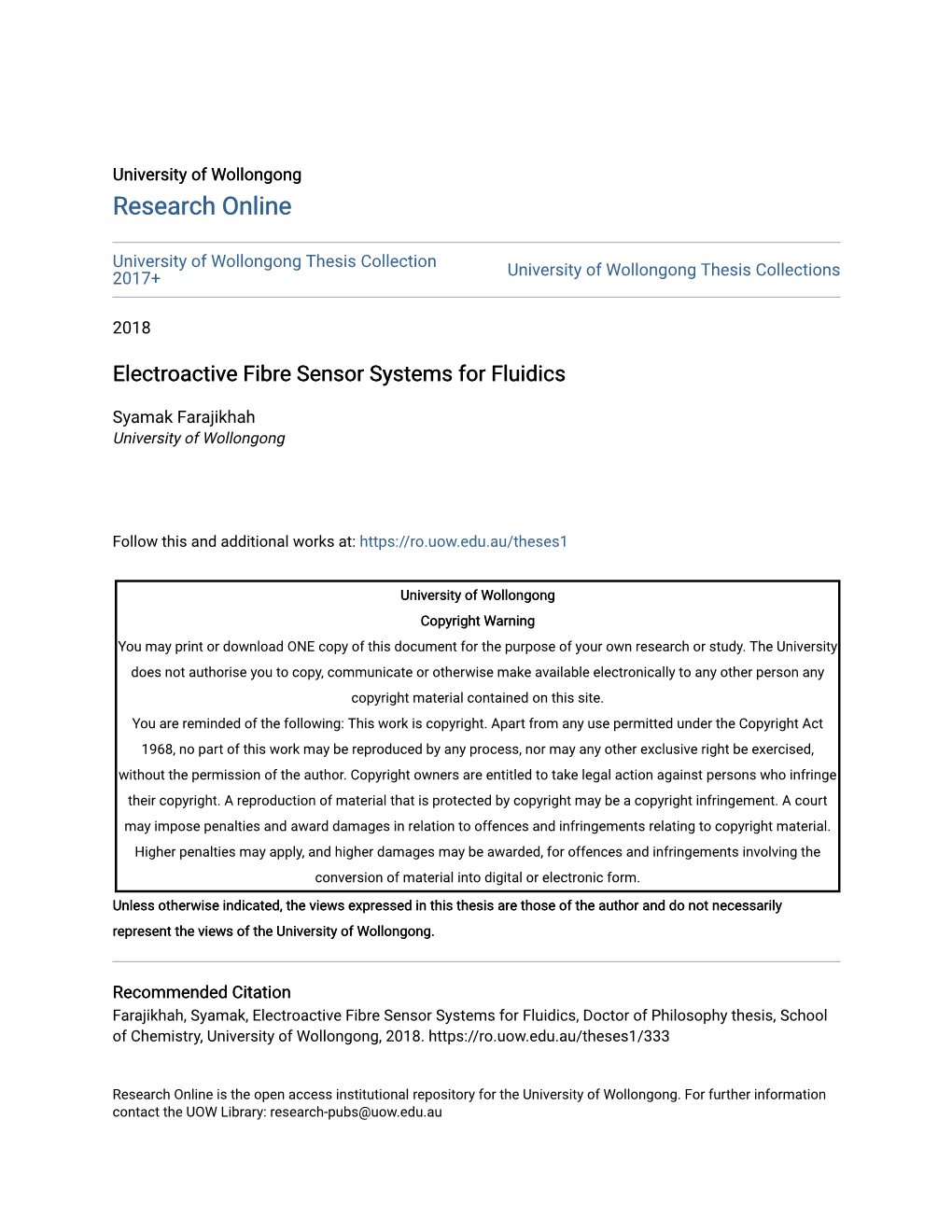
Load more
Recommended publications
-
Graphene.Vortex Fluidics.Final
Vortex fluidic exfoliation of graphite and boron nitride Author Chen, Xianjue, Dobson, John F, Raston, Colin L Published 2012 Journal Title Chemical Communications DOI https://doi.org/10.1039/C2CC17611D Copyright Statement © 2012 Royal Society of Chemistry. This is the author-manuscript version of this paper. Reproduced in accordance with the copyright policy of the publisher. Please refer to the journal website for access to the definitive, published version. Downloaded from http://hdl.handle.net/10072/47070 Griffith Research Online https://research-repository.griffith.edu.au Dynamic Article Links ► Journal Name Cite this: DOI: 10.1039/c0xx00000x www.rsc.org/xxxxxx ARTICLE TYPE Vortex fluidic exfoliation of graphite and boron nitride Xianjue Chen,a John F. Dobson,b and Colin L. Rastona,* Received (in XXX, XXX) Xth XXXXXXXXX 20XX, Accepted Xth XXXXXXXXX 20XX DOI: 10.1039/b000000x 5 Graphite is exfoliated into graphene sheets by the shearing in vortex fluidic films of N-methyl-pyrrolidone (NMP), as a (a) (c) (d) controlled process for preparing oxide free graphene with minimal defects, and for the exfoliation of the corresponding boron nitride sheets. (b) 10 Solution based methods have been widely used for the synthesis !"#$%&'()*+, of graphene from graphite or graphite oxide,1 using high energy '-%.", sonication for the exfoliation process in generating mono- or 2-8 multi-layer structures. However, the associated cavitation process can result in damage to the graphene,2 which can affect Figure 1. (a) Schematic of the vortex fluidic device (10 mm diameter 9,10 o 15 its properties. Developing facile methods for accessing viable tube, 16 cm long, inclined at 45 , operating at 7000 and 8000 rpm for quantities of graphene devoid of such defects, and also of graphite and BN respectively). -
DRAFT Nanotechnology Roadmap Technology Area 10
National Aeronautics and Space Administration DRAFT NANoTechNology RoADmAp Technology Area 10 Michael A. Meador, Chair Bradley Files Jing Li Harish Manohara Dan Powell Emilie J. Siochi November • 2010 DRAFT This page is intentionally left blank DRAFT Table of Contents Foreword Executive Summary TA10-1 1. General Overview TA10-6 1.1. Technical Approach TA10-6 1.2. Benefits TA10-6 1.3. Applicability/Traceability to NASA Strategic Goals, AMPM, DRMs, DRAs TA10-7 1.4. Top Technical Challenges TA10-7 2. Detailed Portfolio Discussion TA10-8 2.1. Summary Description TA10-8 2.2. WBS Description TA10-8 2.2.1. Engineered Materials TA10-8 2.2.1.1. Lightweight Materials and Structures. TA10-8 2.2.1.2. Damage Tolerant Systems TA10-9 2.2.1.3. Coatings TA10-10 2.2.1.4. Adhesives TA10-10 2.2.1.5. Thermal Protection and Control TA10-10 2.2.1.6. Key Capabilities TA10-11 2.2.2. Energy Generation and Storage TA10-12 2.2.2.1. Energy Generation TA10-13 2.2.2.2. Energy Storage TA10-13 2.2.2.3. Energy Distribution TA10-14 2.2.2.4. Key Capabilities TA10-14 2.2.3. Propulsion TA10-14 2.2.3.1. Nanopropellants TA10-14 2.2.3.2. Propulsion Systems TA10-15 2.2.3.3. In-Space Propulsion TA10-16 2.2.3.4. Key Capabilities TA10-17 2.2.4. Electronics, Devices and Sensors TA10-17 2.2.4.1. Sensors and Actuators TA10-17 2.2.4.2. Electronics TA10-17 2.2.4.3. -
Nanotechnology Publications: Leading Countries and Blocs
Date: January 29, 2010 Author Note: I provide links and a copy of my working paper (that you may make freely available on your website) and a link to the published paper. Link to working paper: http://www.cherry.gatech.edu/PUBS/09/STIP_AN.pdf Link to published paper: http://www.springerlink.com/content/ag2m127l6615w023/ Page 1 of 1 Program on Nanotechnology Research and Innovation System Assessment Georgia Institute of Technology Active Nanotechnology: What Can We Expect? A Perspective for Policy from Bibliographical and Bibliometric Analysis Vrishali Subramanian Program in Science, Technology and Innovation Policy School of Public Policy and Enterprise Innovation Institute Georgia Institute of Technology Atlanta, GA 30332‐0345, USA March 2009 Acknowledgements: This research was undertaken at the Project on Emerging Nanotechnologies (PEN) and at Georgia Tech with support by the Project on Emerging Nanotechnologies (PEN) and Center for Nanotechnology in Society at Arizona State University ( sponsored by the National Science Foundation Award No. 0531194). The findings contained in this paper are those of the author and do not necessarily reflect the views of Project on Emerging Nanotechnologies (PEN) or the National Science Foundation. For additional details, see http://cns.asu.edu (CNS‐ASU) and http://www.nanopolicy.gatech.edu (Georgia Tech Program on Nanotechnology Research and Innovation Systems Assessment).The author wishes to thank Dave Rejeski, Andrew Maynard, Mihail Roco, Philip Shapira, Jan Youtie and Alan Porter. Executive Summary Over the past few years, policymakers have grappled with the challenge of regulating nanotechnology, whose novelty, complexity and rapid commercialization has highlighted the discrepancies of science and technology oversight. -
Science & Technology Trends 2020-2040
Science & Technology Trends 2020-2040 Exploring the S&T Edge NATO Science & Technology Organization DISCLAIMER The research and analysis underlying this report and its conclusions were conducted by the NATO S&T Organization (STO) drawing upon the support of the Alliance’s defence S&T community, NATO Allied Command Transformation (ACT) and the NATO Communications and Information Agency (NCIA). This report does not represent the official opinion or position of NATO or individual governments, but provides considered advice to NATO and Nations’ leadership on significant S&T issues. D.F. Reding J. Eaton NATO Science & Technology Organization Office of the Chief Scientist NATO Headquarters B-1110 Brussels Belgium http:\www.sto.nato.int Distributed free of charge for informational purposes; hard copies may be obtained on request, subject to availability from the NATO Office of the Chief Scientist. The sale and reproduction of this report for commercial purposes is prohibited. Extracts may be used for bona fide educational and informational purposes subject to attribution to the NATO S&T Organization. Unless otherwise credited all non-original graphics are used under Creative Commons licensing (for original sources see https://commons.wikimedia.org and https://www.pxfuel.com/). All icon-based graphics are derived from Microsoft® Office and are used royalty-free. Copyright © NATO Science & Technology Organization, 2020 First published, March 2020 Foreword As the world Science & Tech- changes, so does nology Trends: our Alliance. 2020-2040 pro- NATO adapts. vides an assess- We continue to ment of the im- work together as pact of S&T ad- a community of vances over the like-minded na- next 20 years tions, seeking to on the Alliance. -
Molecular Transport Properties Through Carbon Nanotube Membranes
University of Kentucky UKnowledge University of Kentucky Doctoral Dissertations Graduate School 2007 MOLECULAR TRANSPORT PROPERTIES THROUGH CARBON NANOTUBE MEMBRANES Mainak Majumder University of Kentucky, [email protected] Right click to open a feedback form in a new tab to let us know how this document benefits ou.y Recommended Citation Majumder, Mainak, "MOLECULAR TRANSPORT PROPERTIES THROUGH CARBON NANOTUBE MEMBRANES" (2007). University of Kentucky Doctoral Dissertations. 557. https://uknowledge.uky.edu/gradschool_diss/557 This Dissertation is brought to you for free and open access by the Graduate School at UKnowledge. It has been accepted for inclusion in University of Kentucky Doctoral Dissertations by an authorized administrator of UKnowledge. For more information, please contact [email protected]. ABSTRACT OF DISSERTATION Mainak Majumder The Graduate School University of Kentucky 2007 MOLECULAR TRANSPORT PROPERTIES THROUGH CARBON NANOTUBE MEMBRANES ABSTRACT OF DISSERTATION A dissertation submitted in partial fulfillment of the requirements for the degree of Doctor of Philosophy in the College of Engineering at the University of Kentucky By Mainak Majumder Lexington, Kentucky Director: Dr. Bruce J. Hinds, William Bryan Professor of Materials Engineering Lexington, Kentucky 2007 Copyright © Mainak Majumder 2007 ABSTRACT OF DISSERTATION MOLECULAR TRANSPORT PROPERTIES THROUGH CARBON NANOTUBE MEMBRANES Molecular transport through hollow cores of crystalline carbon nanotubes (CNTs) are of considerable interest from the fundamental and application point of view. This dissertation focuses on understanding molecular transport through a membrane platform consisting of open ended CNTs with ~ 7 nm core diameter and ~ 1010 CNTs/cm2 encapsulated in an inert polymer matrix. While ionic diffusion through the membrane is close to bulk diffusion expectations, gases and liquids were respectively observed to be transported ~ 10 times faster than Knudsen diffusion and ~ 10000-100000 times faster than hydrodynamic flow predictions. -
Carbon Nanotube Based Functional Superhydrophobic Coatings
© 2010 SUNNY SETHI ALL RIGHTS RESERVED CARBON NANOTUBE BASED FUNCTIONAL SUPERHYDROPHOBIC COATINGS A Dissertation Presented to The Graduate Faculty of The University of Akron In Partial Fulfillment of the Requirements for the Degree Doctor of Philosophy Sunny Sethi May, 2010 CARBON NANOTUBE BASED FUNCTIONAL SUPERHYDROPHOBIC COATINGS Sunny Sethi Dissertation Approved: Accepted: Advisor Department Chair Dr. Ali Dhinojwala Dr. Ali Dhinojwala Committee Member Dean of the College Dr. Gustavo Carri Dr. Stephen Z. D. Cheng Committee Member Dean of the Graduate School Dr. Li Jia Dr. George R. Newkome Committee Member Date Dr. Purushottam Gujrati Committee Member Dr. Jutta Luettmer-Strathmann ii ABSTRACT The main objective of this dissertation is synthesis of carbon nanotube (CNT) based superhydrophobic materials. The materials were designed such that electrical and mechanical properties of CNTs could be combined with superhydrophobicity to create materials with unique properties, such as self-cleaning adhesives, miniature floatation devices, ice-repellant coatings, and coatings for heat transfer furnaces. The coatings were divided into two broad categories based on CNT structure: Vertically aligned CNT arrays (VA coatings) and mesh-like (non-aligned) carbon nanotube arrays (NA coatings). VA coatings were used to create self-cleaning adhesives and flexible field emission devices. Coatings with self cleaning property along with high adhesiveness were inspired from structure found on gecko foot. Gecko foot is covered with thousands of microscopic hairs called setae; these setae are further divided into hundreds of nanometer sized hairs called spatulas. When gecko presses its foot against any surface, these hairs bend and conform to the topology of the surface resulting into very large area of contact. -
Manufacturing 101 an Education and Training Curriculum for Hardware Entrepreneurs
Cover photo “ContourPlot_01_300” by Siemens FLM Software via Flickr (CC BY-ND 2.0) https://flic.kr/p/rq1ty3 Manufacturing 101 An Education and Training Curriculum for Hardware Entrepreneurs September 2016 Initial Draft: July 2016 Report Number: MF-RR-2016-0103 MForesight: Alliance for Manufacturing Foresight serves as the voice of the national advanced manufacturing community, providing government and industry with information and analysis about emerging technologies, workforce training, and opportunities for public-private partnerships that strengthen U.S. competitiveness. MForesight is funded by the National Science Foundation (NSF) and National Institute for Standards and Technology (NIST) thorough a cooperative agreement with the University of Michigan (Dr. Sridhar Kota, Director.) www.mforesight.org This material is based upon work supported by the National Science Foundation under Grant No. 1552534 to the University of Michigan (Dr. Sridhar Kota, Director). Any opinions, findings, and conclusions or recommendations expressed in this material are those of MForesight and do not necessarily reflect the views of the National Science Foundation or the University of Michigan. i TABLE OF CONTENTS 1.0 EXECUTIVE SUMMARY ................................................................................................................................. 1 2.0 INTRODUCTION ............................................................................................................................................ 2 2.1 PROBLEM STATEMENT................................................................................................................................ -
Nanofluidics in Carbon Nanotubes
Nanofluidics in carbon nanotubes Extremely high aspect ratios, molecularly smooth hydrophobic graphitic walls, and nanoscale inner diameters of carbon nanotubes give rise to the unique phenomenon of ultra-efficient transport of water and gas through these ultra-narrow molecular pipes. Water and gas molecules move through nanotube pores orders of magnitude faster than through other pores of comparable size. The proposed water transport mechanism has a distinct similarity to the transport mechanisms of biological ion channels. Molecular dynamics simulations and experimental measurements of water transport underscore the importance of nanotube structure in enabling ultra-efficient transport through the pore. Aleksandr Noya*, Hyung Gyu Parka,b, Francesco Fornasieroa, Jason K. Holta, Costas P. Grigoropoulosb, and Olgica Bakajina† aMolecular Biophysics and Functional Nanostructures Group, Chemistry, Materials and Life Sciences Directorate, Lawrence Livermore National Laboratory, Livermore, CA 94550, USA bDepartment of Mechanical Engineering, University of California at Berkeley, Berkeley, CA 94720-1740, USA E-mail: *[email protected], †[email protected] A rare combination of transport efficiency and selectivity makes to the position in the fluid and to time. Thus the continuum theory carbon nanotube (CNT) membranes a promising technology for formalism is independent of the nature of the molecular structure the next generation of water desalination, water purification, and configuration1. Advances in nanoscience, which have relentlessly nanofiltration, -
3D Printed Lab-On-A-Chip Platform for Chemical Stimulation and Parallel Analysis of Ion Channel Function
micromachines Article 3D Printed Lab-on-a-Chip Platform for Chemical Stimulation and Parallel Analysis of Ion Channel Function Daniel Aschenbrenner, Oliver Friedrich and Daniel F. Gilbert * Institute of Medical Biotechnology, Friedrich-Alexander-Universität Erlangen-Nürnberg, 91052 Erlangen, Germany * Correspondence: [email protected] Received: 16 July 2019; Accepted: 16 August 2019; Published: 19 August 2019 Abstract: Functional imaging has been a widely established method for the assessment of ion channel function in vitro. Conventional infrastructure used for in vitro functional analysis of ion channels is typically proprietary, non-customizable, expensive, and requires a high level of skill to use and maintain. 3D desktop printing, which is employed in the rapid prototyping field, allows for quick engineering of alternatives to conventional imaging infrastructure that are customizable, low cost, and user friendly. Here, we describe an ultra-low-cost microfluidic lab-on-a-chip (LOC) device manufactured using acrylonitrile butadiene styrene (ABS) for in vitro functional imaging of ion channels that can quickly and easily be reconstructed using three-dimensional (3D) desktop printing. The device is light weight (<5 g), small (20 mm 49 mm), and extremely low cost (<EUR 1). × We simulate fluidics within the printed channels and assess the suitability of the engineered chamber to generate homogeneous mixtures during solution exchange. We demonstrate the usability of the 3D printed microfluidic device in a case study using Fluo-4-loaded human embryonal kidney-derived (HEK293) cells, recombinantly expressing the capsaicin receptor, transient receptor potential vanilloid receptor type 1 (TRPV1), as a model system. In the case study, we confirm its applicability to solution exchange for chemical stimulation and parallel functional time-lapse fluorescence microscopy-based calcium imaging. -
Nano-Fluidics Challenges of Fluid Mechanics Part 1 Why, What, How and Where We Need It?
Micro- & Nano-fluidics challenges of fluid mechanics Part 1 Why, what, how and where we need it? Tomasz A. Kowalewski Department of Mechanics and Physics of Fluids IPPT PAN, Warszawa http://fluid.ippt.gov.pl/nano/ http://fluid.ippt.gov.pl/nano/ Small is beautiful! There’s Plenty of Room at the Bottom! R.P. Feynman 1959 All bio-systems are driven by nano-scale mechanism – typical mechanics barriers broken: gecko, ant, bee, blood cell, bacteria and virus – minimum energy and large mechanical /chemical outcome Integration and multifunctionality! New functions due to the scaling effects, new materials Faster (parallel work), cheaper (by massive production), low energy consumption, lighter (flying robo-labs) By moving individual molecules - can we make them to do any work we wish (!?) …after 50 years billions of devices like inkjet, conductive polymers, fuel injection, ABS, airbag, blood analysis, DNA chips, drug testing and delivery, high definition screen, micro heat exchangers, scanning microscope, AFM ... http://fluid.ippt.gov.pl/nano/ Scale effect At the nanoscale, fundamental mechanical, electronic, optical, chemical, biological, and other properties may differ significantly from properties of micrometer-sized particles or bulk materials. One reason is surface area. Surface area counts because most chemical reactions involving solids happen at the surfaces, where chemical bonds are incomplete. http://fluid.ippt.gov.pl/nano/ Nano technology 21st Century revolution! • 2001 National Nanotechnology Initiative (USA) http://www.nano.gov ~ $1.3mld/year • 2003 NMP priority: Nano-technologies and Nano- science: http://cordis.europa.eu/nanotechnology/ ~ 1.4mld € / 4 years – direct EU funding Nanotechnology - the science, engineering, and technology related to the understanding and control of matter at the length scale of approximately 1 to 100 nanometers. -
Development of Fluidic Device in SIT for Korean Next Generation Reactor ( I )
KAERI/TR-1363/99 KR9900234 SIT Ml Fluidic Device nm I ) Development of Fluidic Device in SIT for Korean Next Generation Reactor ( I ) 31-02 SIT vfl Fluidic Device 7fl^ (I)"ofl 1999. 7. -g- o] o ofc fe LBLOCA*! Sl#^ ^(Safety Injection BOM- =1^3 ^-2^. ^*}7] $M Fluidic Device Fluidic Device^ sl^fl glj }} Q Fluidic Device^] -^-5O^^# ^3-Xf <^^- AEA Technology^ Fluidic Device Fluidic Device^) 1/7 scaled full height, full pressure fe 7171 ^-^.S.^, ^^6fl 4^ Fluidic Device^ ^7j| Ml*l Mf-g-oJ 7}#5|^cf. -y^^^^ 71 71 ^ A^-A^ AlTi^ Cfl^l; ^-3O>( 6V^ 3J ^Cjel ^*1 3t7ll^-AiAS ^ 5l E|S Sii 7HV ^^^1 ^MS. •%•%<>] IL^JLS. ^H^lfe 717151 ^-^^ ^^^^<H1 nj-ef 4-§-^ Fluidic Device-^ 51 ^Aov A^^^-^i ^^1-8- FORTRAN ^ Ufl, £ -§•% ^ si-a- SUMMARY The KNGR uses Fluidic Device to control the flow rate of safety injection coolant from SITOafety Injection Tank) during LBLOCA. This Fluidic Device is a passive safety equipment and it is installed at the bottom of the inner space of the SIT. During the past two years, a scale model test to obtain the required flow characteristics of the device under the KNGR specific conditions has been performed using the experience and existing facility of AEA Technology(UK) with appropriate modifications. The performance verification test is to be performed this year to obtain the optimum characteristics and design data of full size Fluidic Device. This report summarizes the results of the model test. The purpose of the model test was to check the feasibility of developing the device and to produce a generic flow characteristic data. -
DNA Assembly in 3D Printed Fluidics
DNA Assembly in 3D Printed Fluidics William G. Patrick, Alec A. K. Nielsen, Steven J. Keating, Taylor J. Levy, CheWei Wang, Jaime J. Rivera, Octavio MondragónPalomino, Peter A. Carr, Christopher A. Voigt, Neri Oxman, David S. Kong Published: December 30, 2015 DOI: 10.1371/journal.pone.0143636 Abstract The process of connecting genetic parts—DNA assembly—is a foundational technology for synthetic biology. Microfluidics present an attractive solution for minimizing use of costly reagents, enabling multiplexed reactions, and automating protocols by integrating multiple protocol steps. However, microfluidics fabrication and operation can be expensive and requires expertise, limiting access to the technology. With advances in commodity digital fabrication tools, it is now possible to directly print fluidic devices and supporting hardware. 3D printed micro and millifluidic devices are inexpensive, easy to make and quick to produce. We demonstrate Golden Gate DNA assembly in 3Dprinted fluidics with reaction volumes as small as 490 nL, channel widths as fine as 220 microns, and per unit part costs ranging from $0.61 to $5.71. A 3Dprinted syringe pump with an accompanying programmable software interface was designed and fabricated to operate the devices. Quick turnaround and inexpensive materials allowed for rapid exploration of device parameters, demonstrating a manufacturing paradigm for designing and fabricating hardware for synthetic biology. Citation: Patrick WG, Nielsen AAK, Keating SJ, Levy TJ, Wang CW, Rivera JJ, et al. (2015) DNA Assembly in 3D Printed Fluidics. PLoS ONE 10(12): e0143636. doi:10.1371/journal.pone.0143636 Editor: Meni Wanunu, Northeastern University, UNITED STATES Received: July 30, 2015; Accepted: November 6, 2015; Published: December 30, 2015 Copyright: © 2015 Patrick et al.