Pad Printing – Theory and Practice
Total Page:16
File Type:pdf, Size:1020Kb
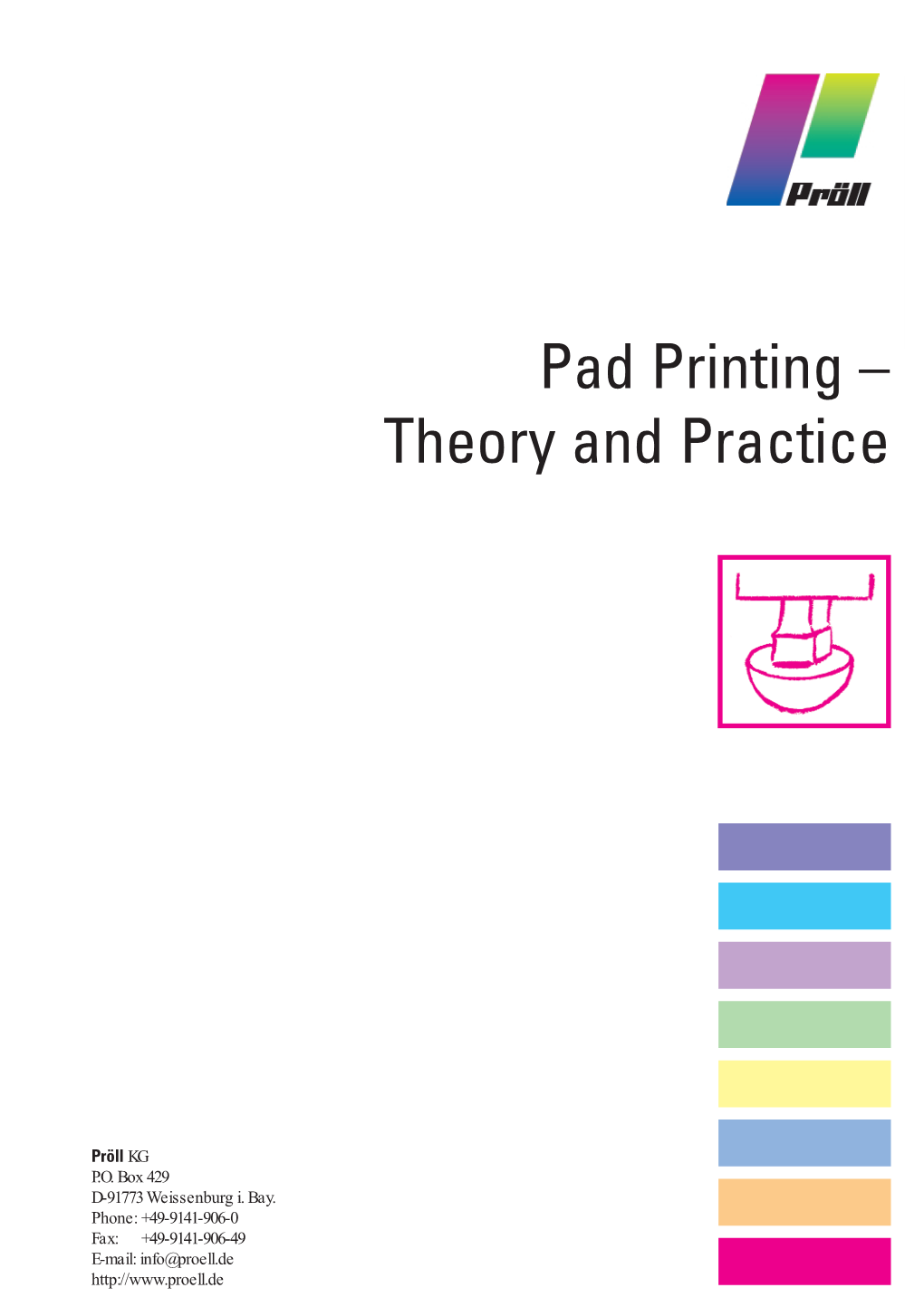
Load more
Recommended publications
-
Pad Printing Vs. Screen Printing Advantages and Applications Introduction
Pad Printing vs. Screen Printing Advantages and Applications Introduction Choosing a graphical printing technique requires extensive consideration into the process, equipment, and mediums you’ll be working with. Two of the most prominent printing methods available today are Pad Printing and Screen Printing. It’s important to understand the advantages and disadvantages of both, especially if you’ll be transferring designs to different surfaces. Depending on the object you’re printing on, you’ll want to understand the strengths and weaknesses for both Pad Printing and Screen Printing. PRIME PRODUCTS, INC. 2755 Remico, S.W., Wyoming, MI 49519 Phone: 616.531.8970 Fax: 616.301.0033 [email protected] www. primeproductsinc.com 2 Screen Printing Overview With origins tracing back to the Chinese Song Dynasty around 960 AD, Screen Printing, otherwise known as Silk- screening, or Serigraphy, involves a woven mesh screen made from polyester, steel, or nylon. The mesh is usually coated with a special emulsion that blocks specific areas of the screen, forming the actual image you’re transferring, also known as the stencil. Screens can also be produced differently depending on the size and shape of the object that your design will transfer onto. The screen mesh itself is stretched and tensioned using a wood or metal frame, similar to a window or door screen. This allows the operator to force ink only into select areas where the design is transferred on to the surface of an object, otherwise known as the substrate. Once the screen is properly placed and secured over the substrate, the operator pours a specific volume of ink over the screen. -
Laser Printer - Wikipedia, the Free Encyclopedia
Laser printer - Wikipedia, the free encyclopedia http://en. rvi kipedia.org/r,vi ki/Laser_pri nter Laser printer From Wikipedia, the free encyclopedia A laser printer is a common type of computer printer that rapidly produces high quality text and graphics on plain paper. As with digital photocopiers and multifunction printers (MFPs), Iaser printers employ a xerographic printing process but differ from analog photocopiers in that the image is produced by the direct scanning of a laser beam across the printer's photoreceptor. Overview A laser beam projects an image of the page to be printed onto an electrically charged rotating drum coated with selenium. Photoconductivity removes charge from the areas exposed to light. Dry ink (toner) particles are then electrostatically picked up by the drum's charged areas. The drum then prints the image onto paper by direct contact and heat, which fuses the ink to the paper. HP I-aserJet 4200 series printer Laser printers have many significant advantages over other types of printers. Unlike impact printers, laser printer speed can vary widely, and depends on many factors, including the graphic intensity of the job being processed. The fastest models can print over 200 monochrome pages per minute (12,000 pages per hour). The fastest color laser printers can print over 100 pages per minute (6000 pages per hour). Very high-speed laser printers are used for mass mailings of personalized documents, such as credit card or utility bills, and are competing with lithography in some commercial applications. The cost of this technology depends on a combination of factors, including the cost of paper, toner, and infrequent HP LaserJet printer drum replacement, as well as the replacement of other 1200 consumables such as the fuser assembly and transfer assembly. -
PRINTING MACHINES OR PRESSES (Manifolding Devices Or Office
B41F CPC COOPERATIVE PATENT CLASSIFICATION B PERFORMING OPERATIONS; TRANSPORTING (NOTES omitted) PRINTING B41 PRINTING; LINING MACHINES; TYPEWRITERS; STAMPS B41F PRINTING MACHINES OR PRESSES (manifolding devices or office printing machines B41L) NOTE Attention is drawn to Notes 1 and 2 following the title of subclass B41L. WARNING In this subclass non-limiting references (in the sense of paragraph 39 of the Guide to the IPC) may still be displayed in the scheme. 1/00 Platen presses, i.e. presses in which printing is 1/58 . Arrangements of counting devices for counting effected by at least one essentially-flat pressure- sheets applying member co-operating with a flat type-bed 1/60 . Safety devices 1/02 . Hand-operated platen presses 1/62 . for preventing injury to operator 1/04 . for mono-impression printing, e.g. on sheets 1/64 . to the hands of the operator 1/06 . with platen maintained parallel to bed during 1/66 . responsive to incorrect operating conditions movement 1/08 . on webs 3/00 Cylinder presses, i.e. presses essentially comprising at least one cylinder co-operating with at least one 1/10 . for multi-impression printing in one or more flat type-bed colours, e.g. on webs 3/02 . with impression cylinder or cylinders rotating 1/12 . on sheets unidirectionally 1/14 . using swinging platens, or forme supports 3/04 . intermittently; Stop-cylinder presses 1/16 . for offset printing {(pad printing B41F 17/001)} 3/06 . continuously 1/18 . for lithography 3/08 . Single-revolution presses 1/20 . for perfecting sheets, i.e. for printing on both sides 3/10 . -
Computer Organization (Keyboard & Display Control, and Printers)
Computer Organization (Keyboard & Display Control, and Printers) KR Chowdhary Professor & Head Email: [email protected] Website:krchowdhary.com Department of Computer Science and Engineering MBM Engineering College, Jodhpur November 15, 2013 kr chowdhary Keyboard & Display Control, Printers 1/ 24 Printing history 1. Printing press 1454 11. Phototypesetting 1960s 2. Lithography 1796 12. Photocopier 1960s 3. Chromolithography 1837 13. Pad printing 1960s 4. Rotary press 1843 14. Dot matrix printer 1964 5. Flexography 1873 15. Laser printer 1969 6. Mimeograph 1876 16. Thermal printer 1970s 7. Hot metal typesetting 1886 17. Inkjet printer 1976 8. Offset press 1903 18. 3D printing 1986 9. Screen-printing 1907 19. Stereolithography 1986 10. Dye-sublimation 1957 20. Digital press 1993 kr chowdhary Keyboard & Display Control, Printers 2/ 24 Classification ◮ All printers have three main components: printing mechanism itself, paper feed mechanism, and the control and interface electronics. 1. Impact Printers ◮ Line printers 1. Dot matrix: Comb, Multihead 2. Engraved: Drum, Band, Belt ◮ Character printers 1. Dot matrix: 9-pin, 24-pin 2. Engraved: Teletype, Daisy wheel 2. Non-impact printers 1. Inkjet 2. Thermal 3. Electrophotographic(Laser) 4. other kr chowdhary Keyboard & Display Control, Printers 3/ 24 Dot matrix printer ◮ Print head runs back and forth, power of a tiny on the page and prints by electromagnet/solenoid, either impact, striking an ink-soaked directly or through small levers cloth ribbon against the paper, ◮ Moving print head, generally much like the print mechanism prints one line of text at a time. on a typewriter. ◮ Most dot matrix printers have a ◮ Letters are drawn out of a dot single vertical line of dots, others matrix, and thus, varied fonts have a few interleaved rows in and arbitrary graphics can be order to improve dot density. -
Choosing a Pad Print Machine by Peter Kiddell
Choosing A Pad Print Machine by Peter Kiddell In the padprinting industry purchasing decisions are often based on assumptions that are simply nuts - literally. The president of a company will see a padprinting machine printing nuts at an exhibition and be suckered by the sales person into believing that, This process will print on anything. And when asked how fast the machine will print the sales person replies, 1500 per hour, hand fed. Dream on! During more than 20 years of involvement with pad printing, I have not come across a truly bad press. I've also never encountered an ideal one. A variety of dierent press styles are available today, each with strengths and weaknesses. Understanding the dierences between the press styles and how they may aect the application at hand will help you determine which press is best for your needs. Pad-printing applications tend to fall into three main categories, listed in descending order in terms of quality demands: Printing involves the precise application of ink onto a substrate. Images normally contain lettering or symbols and may be single or multicolour. Decorating is where a design or eect is applied to a product to enhance the look of the product. Designs are purely artistic, serving no functional purpose , and may again be either single or multicolour. Eects include unusual patterns, simulated wood grain, etc. Coding involves printed information that must be legible, but not necessarily of high quality. An example is date stamping on containers and other packaging. Coding should not be confused with barcoding, where print quality is very important, particularly with regard to contrast and edge denition. -
Printing from Wikipedia, the Free Encyclopedia
Create account Log in Article Talk Read Edit More Search Printing From Wikipedia, the free encyclopedia Main page This article is about the process of reproducing text. For the handwriting method often called printing, see block letters. For other uses, see Print (disambiguation). Contents Printing is a process for reproducing text and images using a master form or template. The earliest examples include Cylinder seals and other objects such as the Cyrus Cylinder and the Part of a series on the Featured content [1] Current events Cylinders of Nabonidus. The earliest known form of woodblock printing came from China dating to before 220 A.D. Later developments in printing include the movable type, first History of printing [2] Random article developed by Bi Sheng in China. The printing press, a more efficient printing process for western languages with their more limited alphabets, was developed by Johannes Gutenberg in Woodblock printing 200 Donate to Wikipedia the fifteenth century.[3] Movable type 1040 Wikipedia store Printing press c. 1440 Modern printing is done typically with ink on paper using a printing press. It is also frequently done on metals, plastics, cloth and composite materials. On paper it is often carried out as a Etching c. 1515 Interaction large-scale industrial process and is an essential part of publishing and transaction printing. Mezzotint 1642 Help Aquatint 1772 About Wikipedia Contents [hide] Lithography 1796 Community portal 1 History Chromolithography 1837 Recent changes 1.1 Woodblock printing Contact page Rotary -
The Pad Printing Process
The Pad Printing Process The pad printing overview: pad printing, printing pads, plates, pad printing inks, adhesion und antistatic Inhalt Teca-Print Teca-Print was founded in 1973 in Thayngen, Switzerland, Since 2002 Teca-Print AG has been an independent and belongs to the world‘s leading pad printing machi- part of the French Groupe Dubuit SA enterprises, that ne manufacturers. The high-quality Swiss products are specialises in different fields of printing. Within the group developed and produced in-house by Teca-Print. By we offer not only pad printing but also screen printing, the further dynamic development of the products and digital printing and hot stamping. the constant adding of technical innovations we have succeeded to integrate pad printing into new market Our multilingual website www.teca-print.com contains segments. information that is constantly updated. Here you can find news regarding recent developments and current offers. The Teca-Print product range includes pad printing Additionally, all our product data sheets are available to machines and systems, peripheral devices, accesso- download. ries as well as consumables as pads, plates and inks. For every product Teca-Print offers training, service and We are pleased to welcome you at Teca-Print in maintenance. Thayngen. In our showroom we will show you our different pad printing machines and how they work. You can also In addition to our head offi ce in Thayngen, Teca-Print visit us at an exhibition. Further information can be found also has subsidiaries in Germany, France, Hungary and on our website. the USA. Our 29 mostly long-standing distribution part- ners provide deliveries and customer service worldwide. -
Colored Prosthetic Skins
Colored Prosthetic Skins Anika Lohrentz Chou Mai Rexxi Prasasya Alice Tang Advisor: Professor William Murphy Client: Greg Gion Date: October 24, 2007 [1] Table of Contents Abstract ........................................................................................................................................... 3 Background ..................................................................................................................................... 3 Current Method ........................................................................................................................... 3 Problem Statement ...................................................................................................................... 4 Design Requirements .................................................................................................................. 4 Problem Motivation..................................................................................................................... 5 Competition ................................................................................................................................. 5 Design Proposals ............................................................................................................................. 6 Pad Printing ................................................................................................................................. 6 Offset Lithographic Printing ...................................................................................................... -
Occupational Hazards in Printing Industry
Int. J. Environ. Sci. Technol. (2016) 13:955–972 DOI 10.1007/s13762-016-0937-z ORIGINAL PAPER Occupational hazards in printing industry 1 1 2 1 1 J. S. Kiurski • B. B. Maric´ • S. M. Aksentijevic´ • I. B. Oros • V. S. Kecic´ Received: 27 July 2015 / Revised: 9 December 2015 / Accepted: 11 January 2016 / Published online: 25 January 2016 Ó Islamic Azad University (IAU) 2016 Abstract This paper, through certain printing techniques, Introduction examines the types of occupational pollutants and the adverse impacts of the printing process. Also, it proposes In the late eighties, human society evolved from basic the measures for better preservation and environmental concepts of social reproduction to the concept of sustain- protection. The paper analyzes the results of the quantita- able development, which generally implies changes in the tive identification of hazardous materials from various structure, functions and activities of the system. Sustain- printing techniques: pad, screen, offset, flexographic, and able development is often related to the environment and digital. The study included the analysis of waste printing involves changes in society concerning the available inks and purification of printing wastewater with adsorp- resources, endangering natural systems and providing the tion methods. Besides that, the preliminary monitoring of long-term survival of the same. It is possible to investigate, ambient indoor air quality was performed. The multiple analyze and draw conclusions to ensure sustainable regression analysis was applied on the obtained experi- development, as well as to optimize its components (Wallis mental results, in order to determine the mutual correlation et al. 2011; Bilen et al. -
Hanover Printers Advantage
Hanover Printers Advantage SUPPLEM ENTAL APPLICATION—AGENT WORKSHEET A. GENERAL APPLICANT INFORMATION Applicant Name: ___________________________________________ Agency Name: __________________________________ Mailing Address: ______________________________________________________________________________________________ Expiration Date: ______________________________________________________________________________________________ Website Address: _____________________________________________________________________________________________ B. PROCESSES AND PRESSES 1. Which processes does your company perform? (check all that apply) Digital Printing Flexography Gravure Letterpress Lithography Pad Printing Screenprinting Waterless Offset Thermography Xerography Bindery Quick Printing or copy shop Cylinder or Platemaking Pre-Press for others Post-Press for others under Printing on substrate for others under contract contract, including bindery other than paper Publishing of books, Design or development Printing of labels for drugs, periodicals or newspapers of websites pharmaceuticals or medical products 2. Describe any other processes used by your company: _________________________________________________________________________________________________________ _________________________________________________________________________________________________________ 3. Which is the predominant kind of ink you use? Water-based Soy-based Electron-beam or Ultra violet cured Solvent-based Other _________________________________________________________________________________________________ -
Common Product Name Hkhs Code "Kevlar" Polyamides Filament Yarn High Tenacity More Than 60Cn/Tex
COMMON PRODUCT NAME HKHS CODE "KEVLAR" POLYAMIDES FILAMENT YARN HIGH TENACITY MORE THAN 60CN/TEX. 54021100 "LYCRA" ELASTANE YARN (100% POLYURETHANE FILAMENT SINGLE YARN) 54024410 {O-2-(DIALKYL AMINO ETHYL} HYDROGEN ALKYL PHOSPHONITES AND THEIR O-ALKYL 29310007 ESTERS; ALKYLATED OR PROTONATED SALTS THEREOF {S-2-(DIALKYL AMINO) ETHYL} HYDROGEN ALKYL PHOSPHONOTHIOATES AND THEIR O- 29309001 ALKYL ESTERS; ALKYLATED OR PROTONATED SALTS THEREOF 0,0-DIETHYL S-{2-(DIETHYLAMINO) ETHYL} PHOSPHOROTHIOATE AND ITS ALKYLATED OR 29309011 PROTONATED SALTS 0-ALKYL (< OR = C10, INCLUDING CYCLOALKYL) ALKYL (METHYL, ETHYL, N-PROPYL OR 29310001 ISOPROPYL) PHOSPHONOFLUORIDATES 1 1 1-TRICHLOROETHANE 29031910 1 1-DICHLORO-1-FLUOROETHANE 29034908 1 1-DICHLORO-2 2 2-TRIFLUOROETHANE 29034904 1 2-DICHLOROETHYLENE 29032900 1-(1,3-BENZODIOXOL-5-YL)PROPAN-2-ONE 29329200 1,1 - DIFLUOROETHANE (HFC-152A) 29033946 1,1,1 - TRIFLUOROETHANE (HFC-143A) 29033945 1,1,1,2,2,3,4,5,5,5 - DECAFLUOROPENTANE (HFC-43-10MEE) 29033943 1,1,1,2,3,3,3-HEPTAFLUOROPROPANE 29033951 1,1,1,2-TETRAFLUOROETHANE 29033920 1,1,1,3,3 - PENTAFLUOROPROPANE (HFC-245FA) 29033954 1,1,1,3,3,3 - HEXAFLUOROPROPANE (HFC-236FA) 29033952 1,1,1-TRICHLOROETHANE 29031910 1,1,2,2,3 - PENTAFLUOROPROPANE (HFC-245CA) 29033953 1,1,3,3,3-PENTAFLUORO-2-(TRIFLUOROMETHYL) PROP-1-ENE 29033910 1,2-BIS (2-CHLOROETHYLTHIO) ETHANE 29309005 1,3-BIS (2-CHLOROETHYLTHIO) -N-PROPANE 29309006 1,4-BIS (2-CHLOROETHYLTHIO) -N-BUTANE 29309007 1,5-BIS (2-CHLOROETHYLTHIO) -N-PENTANE 29309008 1.8 M/M 65%POLYESTER STAPLE FIBRE 35%RAYON STAPLE FIBRE YARN DYED IN HANK 55095100 1/16NM 100%TRUE HEMP R.W. -
Printing Roller Coverings
PRINTING ROLLER COVERINGS Printing Overview Offset printing is a widely used printing technique 4. In Offset Printing, the more you Print, the Less where the inked image is transferred (or “offset”) you pay, because most of the price goes into from a plate to a rubber blanket, then to the the preparation undergone before the first sheet printing surface. When used in combination with of paper is printing and ready for distribution. the lithographic process, which is based on the Any additional paper print will only cost the repulsion of oil and water, the offset technique client paper price, which is very minimal. employs a flat image carrier on which the image to be printed obtains ink from ink rollers, while the non- 5. High speed and high volume printing. printing area attracts a film of water, keeping the Flexography also called surface printing), non-printing areas ink-free. often abbreviated to flexo, is a method of printing most commonly used for packaging Advantages of offset printing compared to other (labels, tape, bags, boxes, banners, etc.). printing methods include: A flexographic print is made by creating a positive mirrored master of the required image 1. Consistent high image quality. as a 3D relief in a rubber or polymer material. Offset printing produces sharper and cleaner A measured amount of ink is deposited upon the images and type than letterpress printing surface of the printing plate (or printing cylinder) because the rubber blanket conforms to the using an engraved anilox roll whose texture texture of the printing surface. holds a specific amount of ink.