Ignition Timing,” in This Section
Total Page:16
File Type:pdf, Size:1020Kb
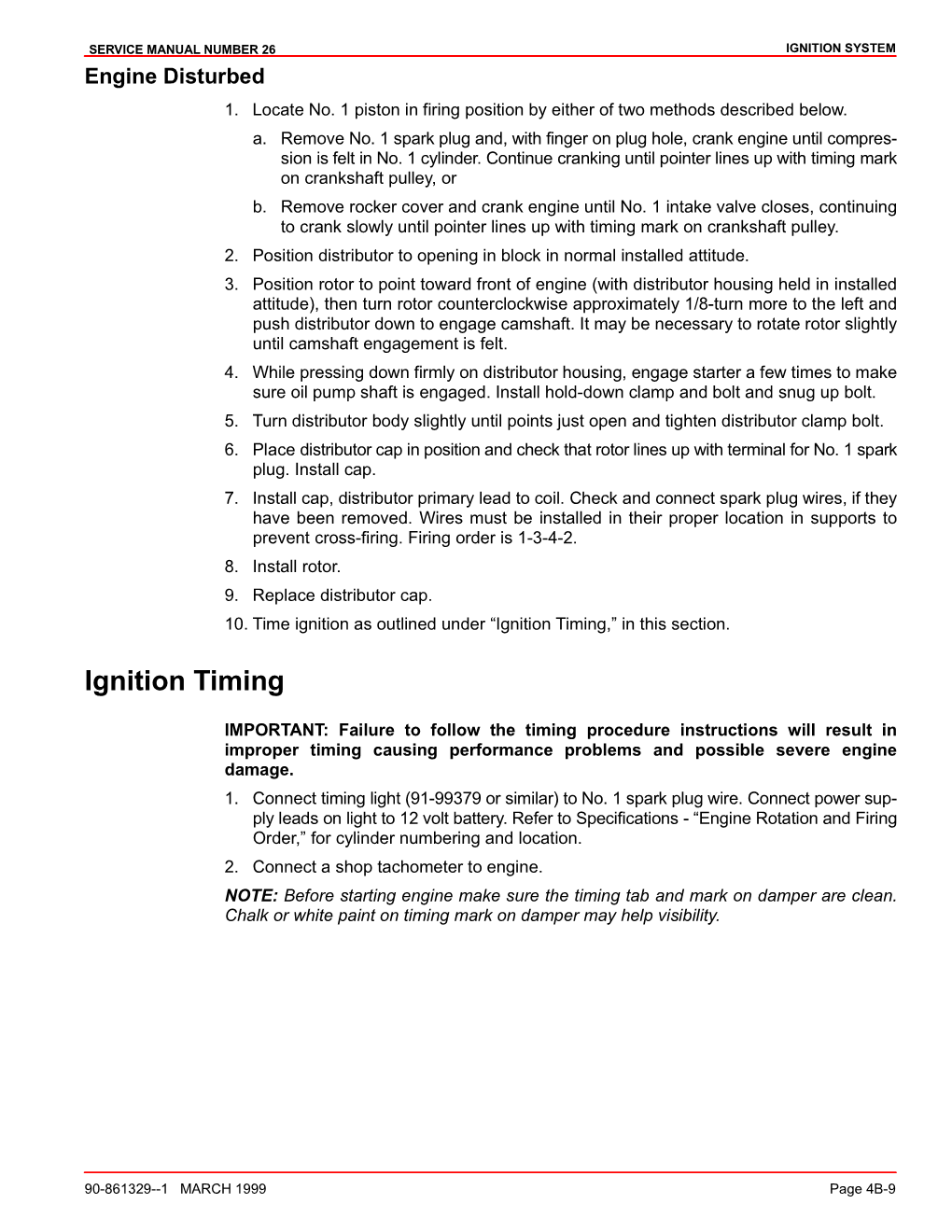
Load more
Recommended publications
-
TR3-TR3B Supercharger Installation Instructions for TR3 from TS13052E Through TR3B ("High Port" TR3’S) PART# 150-128, 150-130 440 Rutherford St
TR3-TR3B Supercharger Installation Instructions For TR3 from TS13052E through TR3B ("High port" TR3’s) PART# 150-128, 150-130 440 Rutherford St. Goleta, CA 93117 1-800-642-8295 • FAX 805-692-2525 • www.MossMiata.com Tools required: The vehicle shown in most of the illustrations is a Triumph TR3 with a steering rack conversion and an electric fan • TR3 Shop manual conversion. Although the instructional photographs may differ from your specific application, they are adequate to • Strap Wrench provide you with the information you need to complete a • Timing light successful installation of this product. Focus on the parts that are similar, rather than focus on the differences. • Thread sealer or Teflon tape • Phillips screwdrivers Note that the fuel lines will be replaced as part of the installation and that the tank will need to be filled with • Flat-blade screwdrivers at least 91-octane fuel before the car is started. For • Torque wrench up to 65 ft-lbs maximum safety drain the tank before starting the installation process. • 3/16" Allen wrench • Hack saw or cut-off wheel Warning: Never smoke or work around open flames. • Wire cutters, strippers and crimpers If your car is + (positive) ground (earth), we will be • Side cutters (dikes) converting it to – (negative) ground (earth) during this installation. You must follow the extra steps detailed • 1/4", 3/8", & 1/2" ratchets in the back of these instructions regarding the proper • 3" and 6" extensions for above ratchets procedure to convert the subject vehicle to negative ground. • Combination wrenches and sockets in the following sizes: Note: For maximum performance and to prevent • 7mm, 8mm, 10mm, 12mm, 13mm, 17mm premature failure, your engine should be in good mechanical condition and been recently tuned. -
SV470-SV620 Service Manual
SV470-SV620 Service Manual IMPORTANT: Read all safety precautions and instructions carefully before operating equipment. Refer to operating instruction of equipment that this engine powers. Ensure engine is stopped and level before performing any maintenance or service. 2 Safety 3 Maintenance 5 Specifi cations 13 Tools and Aids 16 Troubleshooting 20 Air Cleaner/Intake 21 Fuel System 31 Governor System 33 Lubrication System 35 Electrical System 44 Starter System 47 Emission Compliant Systems 50 Disassembly/Inspection and Service 63 Reassembly 20 690 01 Rev. F KohlerEngines.com 1 Safety SAFETY PRECAUTIONS WARNING: A hazard that could result in death, serious injury, or substantial property damage. CAUTION: A hazard that could result in minor personal injury or property damage. NOTE: is used to notify people of important installation, operation, or maintenance information. WARNING WARNING CAUTION Explosive Fuel can cause Accidental Starts can Electrical Shock can fi res and severe burns. cause severe injury or cause injury. Do not fi ll fuel tank while death. Do not touch wires while engine is hot or running. Disconnect and ground engine is running. Gasoline is extremely fl ammable spark plug lead(s) before and its vapors can explode if servicing. CAUTION ignited. Store gasoline only in approved containers, in well Before working on engine or Damaging Crankshaft ventilated, unoccupied buildings, equipment, disable engine as and Flywheel can cause away from sparks or fl ames. follows: 1) Disconnect spark plug personal injury. Spilled fuel could ignite if it comes lead(s). 2) Disconnect negative (–) in contact with hot parts or sparks battery cable from battery. -
Installation Instructions Cloyes® 3-Keyway Crank Sprockets
February 2, 2009 Installation Instructions Cloyes ® 3-Keyway Crank Sprockets The Cloyes® Patented 3-Keyway crank sprocket allows adjustment of the crankshaft timing by ± 4°. Remember: The camshaft angle is half of the crankshaft angle, therefore the camshaft will correspondingly advance or retard by ± 2°. By changing the cam timing, enhancements to the camshaft characteristics can be achieved. For example, retarding the cam timing will increase high RPM horsepower, and advancing the cam timing will increase low-end torque. The following examples illustrate which timing mark is used with its corresponding keyway: GM and Chrysler Ford Retard keyway To retard the camshaft timing, use the timing mark on the crank sprocket and the retard keyway shown above. GM and Chrysler Ford Factory keyway For factory specified timing, use the Ο timing mark on the crank sprocket and the factory keyway shown above. GM and Chrysler Ford Advance keyway To advance the camshaft timing, use the ∆ timing mark on the crank sprocket and the advance keyway shown above. Notes: After determining which setting to use, we advise marking (with white marker or similar) the corresponding timing mark and keyway. This will make them easier to identify during installation. Some high performance camshafts are ground with advance or retard built in. In this case the cam manufacturer intends the cam to be set at the factory specified timing. Also, during and after installation, observe for any interference between the timing set and engine block. If interference is found, remove or grind that area of the block so adequate clearance is obtained. When removing a press fit crank sprocket, a proper pulling tool should be used. -
Ins 151 VW Timing Belt How to TDI BEW(PD)
PLEASEREAD THEFOLLOWING BULLETINBEFORE CONTINUING WITH YOUR TIMING BELT REPLACEMENT Bulletin: PreventPremature Water PumpFailure! BLAUfergnugen!Inc.recommendsthatan Audi VwFactory Trained ASECertified Technicianinstallyourparts toensureyoursafety. AlwaysreadRobertBentleyfactoryservicemanualsafetyinstructionsandguidelines. ALWAYS WEARSAFETY GLASSES ANDOTHERSAFETY ITEMS WHENPERFORMING THEFOLLOWING WORK! InstallersResponsibility: Blaupartsrecommendsthatinstallerstakethenecessarytimetothoroughlyfollowthestepsoutlinedinthisbulletintopreventfuturelabor costs,aswellasanyinconvenienceaftertheinstallationofthewaterpumpincludedinthistimingbeltkit.Ithasbeennotedthatduetotime constraints,inconvenience,andprofit,manyindividualsandmechanicsalike,donottaketheextratimeneededtothoroughlyflushtheentire vehiclecoolingsystempriortotheinstallationofthenewwaterpump.Justdrainingthecoolingsystemandrefillingthesystemisnotenough! Prematurewaterpumpfailure(waterpumpsealsandbearings)canoccurbecauseoffailingtotakethetimetoflushtheentirecoolingsystem anditsrelatedcomponents.Oftenwhenproblemsarise,suchasacoolantleak,thenewwaterpumpisblamedasthecausewheninfactthe oppositeistrue.Itisusuallybecausetheinstallerhasneglectedtofollowthesestepslistedbelow. FlushingtheCoolingSystem: Itisimperativethatthecoolingsystembethoroughlyflushedofallaccumulatedsiltandsedimentbuildup,includingallaftermarketcooling systemadditives,orstopleakproductsthatmayhavebeenaddedtothecoolingsystem,pastorpresent. Thiswouldentailflushingtheradiator, engineblock,heatercoreandhosesetc.UseOnlyTap Water -
1. Turn the Crankshaft Clockwise (Right Turn) to Align Each Timing Mark and to Set the Number 1 Cylinder at Compression Top Dead Center
1. Turn the crankshaft clockwise (right turn) to align each timing mark and to set the number 1 cylinder at compression top dead center. 2. Loosen the tension pulley fixing bolt. CAUTION: If the timing belt is to be re-used, use chalk to mark (on its flat side) an arrow indicating the clockwise direction. 3. Place a screwdriver against the tensioner pulley and pry it fully back in the direction of the arrow. 4. Temporarily tighten the tensioner pulley bolt. 5. Remove the timing belt. INSTALLATION SERVICE POINTS ]]A[[ TIMING BELT INSTALLATION CAUTION: After installing the timing belt, try to rotate the camshaft sprocket in the reverse direction. Recheck to be sure that the belt is fully tensioned and that each timing mark is in the proper position. 1. With the timing belt tensioner pulley bolt loosened, use a screwdriver to pry the tensioner pulley as close to the engine mount as possible. Then temporarily tighten tensioner bolt. 2. Align each of the camshaft and crankshaft sprocket timing marks. 3. Install the timing belt in the following order, while making sure that the tension side of the belt is not loose. 1) Crankshaft sprocket 2) Water pump sprocket 3) Camshaft sprocket 4) Tensioner pulley ]]B[[ TIMING BELT TENSION ADJUSTMENT 1. Initially loosen the fixing bolt of the tensioner pulley fixed to the engine mount side by 1/4 - 1/2 turn , and use the force of the tensioner spring to apply tension to the belt. CAUTION: As the purpose of this procedure is to apply the proper amount of tension to the tension side of the timing belt by using the cam driving torque, turn the crankshaft only by the amount given below. -
S&S® Cycle, Inc
® Instruction 51-1018 S&S Cycle, Inc. 02-18-13 14025 Cty Hwy G PO Box 215 Copyright © 1980, 1985, 1988, 1991, Viola, Wisconsin 54664 1992, 2002, 2006, 2005, 2010, 2013 Phone: 608-627-1497 • Fax: 608-627-1488 by S&S® Cycle, Inc. Technical Service Phone: 608-627-TECH (8324) Technical Service Email: [email protected] All rights reserved. Printed in the U.S.A. Website: www.sscycle.com General Instructions for All Flywheel Installations and Instructions for 37/16" - 31/2" Bore Big Twin Stroker Kit 1936–1999 DISCLAIMER: IMPORTANT NOTICE: S&S parts are designed for high performance, off road, racing applications and Statements in this instruction sheet preceded by the following words are of are intended for the very experienced rider only. The installation of S&S parts special significance. may void or adversely effect your factory warranty. In addition such installation and use may violate certain federal, state, and local laws, rules and ordinances WARNING as well as other laws when used on motor vehicles used on public highways, Means there is the possibility of injury to yourself or others. especially in states where pollution laws may apply. Always check federal, state, CAUTION and local laws before modifying your motorcycle. It is the sole and exclusive responsibility of the user to determine the suitability of the product for his or Means there is the possibility of damage to the part or motorcycle. her use, and the user shall assume all legal, personal injury risk and liability and NOTE all other obligations, duties, and risks associated therewith. -
BRP MP62/S1 Supercharger Kit 1999 - 2005 Mazda Miata
BR Performance, LLC 15-B International Ct. PO Box 1226 Mauldin, SC 29662 Tech Support Phone: (800) 301-4122 E-mail: [email protected] Live Chat Accessed from our website. www.brperformance.com Also see our forum for more info.. BRP MP62/S1 Supercharger Kit 1999 - 2005 Mazda Miata Congratulations! Tools: Congratulations on your purchase of the No special tools or equipment will be BR Performance (BRP) MP62 Supercharger Kit. needed to install your BRP MP62 kit. This supercharger kit was designed for the Miata, Common mechanics tools will be by true Miata aficionados. We don’t just build needed. Following is a list of tools that may be necessary and sell kits for the Miata. We love them and depending upon how your Miata is currently equipped. drive them, HARD, every day. That said, we put ◊ Wrenches: 17mm, 14mm,13mm, 12mm, 10mm. A torque a lot of time and effort into the design and devel- wrench is also recommended. opment of our MP62 supercharger kit. ◊ Sockets: 3/4”, 1/4”, 5/16”, 17mm, 14mm, 13mm, 12mm, “So how long is this going to take to 10mm, 8mm, and assorted extentions may come in handy install anyway?” Well, that really depends upon as well. you. We suggest reading through the ◊ Screwdrivers: Phillips and Flat Head. instructions a couple of times to familiarize ◊ Pliers: Slip Joint and Needle Nose. yourself with the components, your car, and how ◊ Allen Wrenches (Hex Key): 8mm, 6mm they all fit together. If this is your first time ◊ Wiring Tools: Wire stripper/cutter, Crimper (although we installing a modification of this degree, then we suggest the use of a soldering iron & solder for electrical suggest you give yourself at least a full day, to a connections when possible). -
Camshaft Installation and Degreeing Procedure
1 INSTRUCTIONS Camshaft Installation and Degreeing Procedure Thank you for choosing COMP Cams® products; we are proud to be your manufacturer of choice. Please read this instruction booklet carefully before beginning installation and also take a moment to review the included limited warranty information. This instruction booklet is broken down into several categories for ease of use. Some of the topics may not apply to every application, but all of the information will be very beneficial during the cam installation process. For step-by-step visual detail, it is recommended to watch the COMP Cams® DVD “The Proper Procedure to Install and Degree a Camshaft” (Part #190DVD). If you have any questions or problems during the installation, please do not hesitate to contact the toll free CAM HELP® line at 1-800-999-0853, 7am to 8pm CST Monday through Friday, 9am to 4pm CST Saturday. Important: In order for your new COMP Cams® camshaft to be covered under any warranty, you must use the recommended COMP Cams® lifters and valve springs. Failure to install new COMP Cams® lifters and valve springs with your new cam can cause the lobes to wear excessively and cause engine failure. If you have any questions about this application, please contact our technical department immediately. Camshaft Installation Procedure 1. Prepare a clean work area and assemble the tools needed for the camshaft installation. It is suggested to use an automotive manual to help determine which items must be removed from the engine in order to expose the timing chain, lifters and camshaft. A good, complete automotive manual will save time and frustration during the installation. -
03343 Timing Light Manual.P65
AUTOMOTIVE TIMING LIGHT - XENON Model 03343 ASSEMBLY and OPERATING INSTRUCTIONS ® 3491 Mission Oaks Blvd., Camarillo, CA 93011 Visit our Web site at http://www.harborfreight.com Copyright © 2003 by Harbor Freight Tools®. All rights reserved. No portion of this manual or any artwork contained herein may be reproduced in any shape or form without the express written consent of Harbor Freight Tools . For technical questions and replacement parts, please call 1-800-444-3353 Specifications Overall Dimensions 7.5” L x 2” Dia. and a 3.5” Handle Grip Lead Length 4 Feet Features: Xenon bulb, Clamp on inductive pick up, automatic reverse polarity, overload protection, trigger activated pistol grip Save This Manual You will need the manual for the safety warnings and precautions, assembly instructions, operating and maintenance procedures, parts list and diagram. Keep your invoice with this manual. Write the invoice number on the inside of the front cover. Keep the manual and invoice in a safe and dry place for future reference. Safety Warnings and Precautions WARNING: When using tool, basic safety precautions should always be followed to reduce the risk of personal injury and damage to equipment. Read all instructions before using this tool! 1. Keep work area clean. Cluttered areas invite injuries. 2. Observe work area conditions. Do not use the timing light in damp or wet locations. Don’t expose to rain. Keep work area well lighted. Do not use electrically powered tools in the presence of flammable gases or liquids. 3. Keep children away. Children must never be allowed in the work area. -
Timing Belt - Removal and Installation • 2014 Ford Fusion • Motologic
12/14/2017 Engine - 1.5L EcoBoost (118kW/160PS) - Timing Belt - Removal and Installation • 2014 Ford Fusion • MotoLogic 2014 Fusion Report a problem with this article 303-01A Engine - 1.5L EcoBoost (118kW/160PS) 2013 - 2014 Fusion Removal and Installation Procedure revision date: 05/28/2014 Timing Belt Special Tool(s) / General Equipment 303-1097 Locking Tool, Variable Camshaft Timing Oil Control Unit TKIT-2010B-FLM TKIT-2010B-ROW 303-1550 Alignment Tool, Crankshaft Vibration Damper TKIT-2012A-FL TKIT-2012A-ROW 303-393-02 Adapter for 303-393 TKIT-2012A-FL TKIT-2012A-ROW 303-393A Locking Tool, Flywheel TKIT-2012A-FL TKIT-2012A-ROW 303-748 Locking Tool, Crankshaft TKIT-2010B-FLM TKIT-2010B-ROW Trolley Jack Hose Clamp Remover/Installer Wooden Block Removal https://www.motologic.com/car/2014_fd_fusion_5445/article/a3520a51ac196dcba4cc1b7646072098?returnPath=%2Fcar%2F2014_fd_fusion_5445%… 1/33 12/14/2017 Engine - 1.5L EcoBoost (118kW/160PS) - Timing Belt - Removal and Installation • 2014 Ford Fusion • MotoLogic NOTE: Do not loosen or remove the crankshaft pulley bolt without first installing the special tools. The crankshaft pulley and the crankshaft timing sprocket are not keyed to the crankshaft. Before any repair requiring loosening or removal of the crankshaft pulley bolt, the crankshaft and camshafts must be locked in place by the special service tools, otherwise severe engine damage can occur. NOTE: During engine repair procedures, cleanliness is extremely important. Any foreign material, including any material created while cleaning gasket surfaces, that enters the oil passages, coolant passages or the oil pan can cause engine failure. 1. Refer to: Jacking and Lifting - Overview (100-02 Jacking and Lifting, Description and Operation). -
Comparison of the Exhaust Emissions from a Synchronous
COMPARISON OF THE EXHAUST EMISSIONS FROM A SYNCHRONOUS CHARGE TRAPPING ENGINE AND A ROTAX E-TEC ENGINE A Thesis Presented in Partial Fulfillment of the Requirements for the Degree of Master of Science with a Major in Mechanical Engineering in the College of Graduate Studies University of Idaho by Alexander Fuhrman October 2013 Major Professor: Karen Den Braven, Ph.D. ii Authorization to Submit Thesis This thesis of Alexander Fuhrman, submitted for the degree of Master of Science with a major in Mechanical Engineering and titled “COMPARISON OF THE EXHAUST EMISSIONS FROM A SYNCHRONOUS CHARGE TRAPPING ENGINE AND A ROTAX E-TEC ENGINE,” has been reviewed in final form. Permission, as indicated by the signatures and dates given below, is now granted to submit final copies to the College of Graduate Studies for approval. Major Professor _______________________________ Date ________ Karen Den Braven, Ph.D. Committee Member _______________________________ Date ________ Daniel Cordon, Ph.D. Committee Member _______________________________ Date ________ David McIlroy, Ph.D. Department Administrator _______________________________ Date ________ John Crepeau, Ph.D. Discipline’s College Dean _______________________________ Date ________ Larry Stauffer, Ph.D. Final Approval and Acceptance by the College of Graduate Studies _____________________________ Date ________ Jie Chen, Ph.D. iii Abstract The University of Idaho has been developing synchronous charge trapping (SCT) two-stroke engines since 2010 for the recreational products industry. Previous testing of SCT engines has shown promise for reduced emissions and fuel consumption, while maintaining performance. The primary goal of this thesis was to complete an EPA 5 Mode emissions test of the parallel rotary synchronous charge trapping (PR-SCT) engine along with defining its maximum performance, as all previous testing had been completed at low load operating points. -
CHBTL1 Timing Light.Fm
HIGH BEAM TIMING LIGHT MODEL NO: CHBTL1 PART NO: 4003402 USER INSTRUCTIONS ORIGINAL INSTRUCTIONS GC1219 - ISS 1 INTRODUCTION Thank you for purchasing this CLARKE Timing Light. Before use, read the following information we are sure that you will enjoy many years of service from your timing light and maintain the efficiency of your car engine. The Xenon bulb used in this light will provide the bright flash needed to see engine timing marks under bright lighting conditions including daylight. The bulb can be replaced by the user when necessary, reducing the need to return the light to your CLARKE dealer for repair. CONTENTS PAGE BASICS OF ENGINE TIMING.. 3 When to check timing . 3 Timing specifications . 5 SAFETY PRECAUTIONS . 6 GENERAL OPERATING PROCEDURES . 7 Using an advance timing light . .. 8 Adjusting timing to specifications . 9 Testing centrifugal advance . 10 Testing vacuum advance . 10 Checking distributor cam wear . 11 Small engines . 11 Rotary engines . 11 FAULTFINDING . 13 CARE AND MAINTENANCE . 14 Replacing the xenon lamp . 14 ENVIRONMENTAL RECYCLING POLICY . .. 15 GUARANTEE . 15 2 Parts & Service: 020 8988 7400 / E-mail: [email protected] or [email protected] BASICS OF ENGINE TIMING In order for an automobile engine to function, three things are necessary: air, fuel and a spark to ignite the air/fuel mixture and create an explosion. The precise instant of that explosion must be such that the maximum power is delivered to the engine piston. This is ”timing”. Each engine manufacturer determines the exact timing necessary for various engines so that optimum power is obtained from the fuel used.