June 2014 5.1Mb
Total Page:16
File Type:pdf, Size:1020Kb
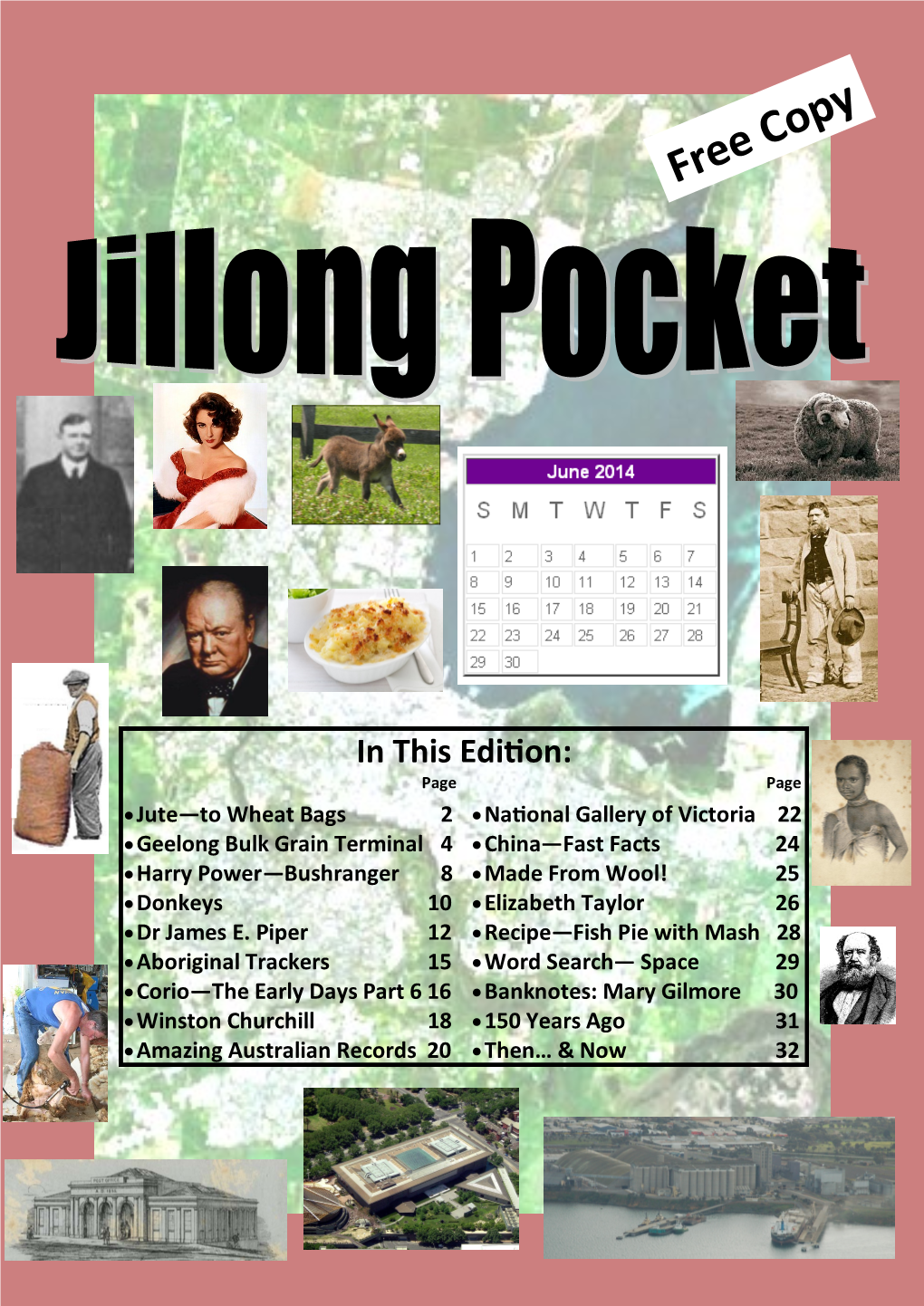
Load more
Recommended publications
-
Time Booksellers September 2020 Latestacquisitions
Time Booksellers September 2020 Latest Acquisitions Uploaded on our website on September 1st some 467 titles. To view a Larger image click on the actual image then the back arrow. To order a book, click on 'Click here to ORDER' and then the ORDER button. If you wish to continue viewing books, click the back arrow. You will return to the list of books you were viewing. To continue adding books to your order simply repeat on the next book you want. When you have finished viewing or searching click on 'View shopping cart'. Your list of books will be shown. To remove any unwanted books from the shopping cart simply click 'Remove the item'. When satisfied with your order click "Proceed with order" follow the prompts, this takes you to the Books and Collectibles secure ordering page. To search our entire database of books (over 30000 titles), go to our website. www.timebookseller.com.au 111933 A'BECKETT, GILBERT ABBOTT; CRUIKSHANK, GEORGE. The Comic Blackstone. Part II.- of Real Property. Post 12mo; pp. xiv, 92 - 252; engraved title page, text illustrated with one other engraving, bound in contemporary half leather with marbled boards, good copy.London; Published at The Punch Office, 92 Fleet Street; 1856. Click here to Order $50 98279 ADAMS, JOHN D. The Victorian Historical Journal. Index to Volumes. 51 to 60. Issues Nos. 199 to 233 1980 - 1989. Firs Edition; Demy 8vo; pp. xi, 203; original stiff wrapper, minor browning to edges of wrapper, volume numbers written in ink on spine, otherwise a very good copy. -
THOTKG Production Notes Final REVISED FINAL
SCREEN AUSTRALIA, LA CINEFACTURE and FILM4 Present In association with FILM VICTORIA ASIA FILM INVESTMENT GROUP and MEMENTO FILMS INTERNATIONAL A PORCHLIGHT FILMS and DAYBREAK PICTURES production true history of the Kelly Gang. GEORGE MACKAY ESSIE DAVIS NICHOLAS HOULT ORLANDO SCHWERDT THOMASIN MCKENZIE SEAN KEENAN EARL CAVE MARLON WILLIAMS LOUIS HEWISON with CHARLIE HUNNAM and RUSSELL CROWE Directed by JUSTIN KURZEL Produced by HAL VOGEL, LIZ WATTS JUSTN KURZEL, PAUL RANFORD Screenplay by SHAUN GRANT Based on the Novel by PETER CAREY Executive Producers DAVID AUKIN, VINCENT SHEEHAN, PETER CAREY, DANIEL BATTSEK, SUE BRUCE-SMITH, SAMLAVENDER, EMILIE GEORGES, NAIMA ABED, RAPHAËL PERCHET, BRAD FEINSTEIN, DAVID GROSS, SHAUN GRANT Director of Photography ARI WEGNER ACS Editor NICK FENTON Production Designer KAREN MURPHY Composer JED KURZEL Costume Designer ALICE BABIDGE Sound Designer FRANK LIPSON M.P.S.E. Hair and Make-up Designer KIRSTEN VEYSEY Casting Director NIKKI BARRETT CSA, CGA SHORT SYNOPSIS Inspired by Peter Carey’s Man Booker prize winning novel, Justin Kurzel’s TRUE HISTORY OF THE KELLY GANG shatters the mythology of the notorious icon to reveal the essence behind the Life of Ned KeLLy and force a country to stare back into the ashes of its brutal past. Spanning the younger years of Ned’s Life to the time Leading up to his death, the fiLm expLores the bLurred boundaries between what is bad and what is good, and the motivations for the demise of its hero. Youth and tragedy colLide in the KeLLy Gang, and at the beating heart of this tale is the fractured and powerful Love story between a mother and a son. -
Twenty One Australian Bushrangers and Their Irish Connections
TWENTY ONE AUSTRALIAN BUSHRANGERS AND THEIR IRISH CONNECTIONS FATHER–JAMES KENNIFF FROM IRELAND–CAME FREE TO NSW. AFTER ONE BOOK WRITTEN ON PATRICK AND JAMES HARRY POWER CALLED (JNR) WERE CONVICTED FATHER – THOMAS SCOTT OF CATTLE STEALING AN ANGLICAN CLERGYMAN ALL THE FAMILY MOVED CAPTAIN MOONLITE FROM RATHFRILAND IN CO. THE BUSHRANGER TO QUEENSLAND BUT (1842-1880) DOWN WHERE ANDREW HARRY POWER THE BROTHERS WERE MARTIN CASH ANDREW GEORGE SCOTT WAS BORN. HARRY POWER TUTOR OF NED KELLY AGAIN CONVICTED. (1819-1891) BY PASSEY AND DEAN LATER THEY TOOK UP A MOTHER - JESSIE JEFFARIES 1991 LARGE GRAZING LEASE FROM THE SAME AREA. AT UPPER WARRIGO NEAR MARYBOROUGH IN SOUTHERN QUEELSLAND ANDREW TRAINED AS AN ENGINEER IN LONDON INSTEAD OF BECOMING A MOTHER – MARY CLERGYMAN AS HIS FATHER WISHED. THE FAMILY MOVED TO NEW (1810-1878) STAPLETON BORN NSW. PATRICK KENNIFF JAMES KENNIFF ZEALAND IN 1861, WHERE ANDREW BECAME AN OFFICER IN THE MAORI PRISON PHOTO (1863-1903) WARS AND WAS WOUNDED IN BOTH LEGS. HE WAS COURT MARSHALLED (1869-1940) BORN 1810 IN ENISCORTHY CO. WEXFORD AND GOT INTO TROUBLE IN 1828 FOR MALINGERING BUT WAS NOT CONVICTED. IN 1868 HE MOVED TO THE KENNIFF BROTHERS STARTED OFF AS CATTLE DUFFERS AND SPENT TIME FOR SHOOTING A RIVAL SUITOR AND TRANSPORTED TO NSW FOR 7 YEARS. MELBOURNE AND BEGAN HIS STUDIES FOR THE CLERGY. HE WAS SENT TO BORN HENRY JOHNSTON (JOHNSON) IN CO. WATERFORD C.1820. HE MIGRATED TO ENGLAND BUT GOT CAUGHT IN JAIL IN NSW. AFTER MOVING WITH THE REST OF THE FAMILY INCLUDING STEALING A SADDLE AND BRIDLE (SOME SAY IT WAS SHOES) AND TRANSPORTED TO VAN DIEMENS LAND FOR 7 HE WORKED OUT HIS SENTENCE BUT GOT INTO TROUBLE FOR BRANDING BROTHERS THOMAS AND JOHN TO QUEENSLAND, THEY RACED HORSES THE GOLDFIELDS BUT GOT MIXED UP IN A BANK SWINDLE AND WAS SENT TO PRISON. -
Australian Fiction
Ahmad, Michael Mohammed The Lebs F AHM:M As far as Bani Adam is concerned, Punchbowl Boys is the arse end of the earth. Though he’s a Leb and they control the school, Bani feels at odds with the other students, who just don't seem to care. He is a romantic in a sea of hyper-masculinity. Bani must come to terms with his place in this hostile, hopeless world, while dreaming of so much more. Aldridge, James The True Story of Spit MacPhee F ALD:J Young Spit lives a hand to mouth existence with his eccentric grandfather, Fyfe MacPhee, in an old shanty on the banks of the Murray River. The townspeople think Spit would be better cared for in a Boys' Home - and when old Fyfe dies, a fierce battle to decide Spit's destiny begins. Attwood, Alan Burke’s Soldier F ATT:A 1871 - John King is dying and he is finally ready to tell his story. He was with Wills as he penned his final letter and at Burke's side when he died. Then he was alone, the sole survivor. This is his story. Baillie, Allan The First Voyage F BAI:A An adventure story set in our very distant past, 30,000 years ago, when the first tribes from Timor braved the ocean on primitive rafts to travel into the unknown, and reached the land mass of what is now Australia. Birch, Tony The White Girl F BIR:T Indigenous storyteller Tony Birch explores the lengths we will go to in order to save the people we love. -
The Camera, the Convict and the Criminal Life1
1 ‘Through a Glass, Darkly’: the Camera, the Convict and the Criminal Life1 Julia Christabel Clark B.A. (Hons.) Thomas Fleming Taken at Port Arthur 1873-4 Photographer: probably A.H. Boyd Queen Victoria Museum & Art Gallery Submitted in fulfilment of the requirements for the Degree of Doctor of Philosophy (Ph.D) University of Tasmania November 2015 1 ‘For now we see through a glass, darkly; but then face to face: now I know in part; but then shall I know even as also I am known.’ 1 Corinthians 13:12, King James Bible. 2 This thesis contains no material which has been accepted for a degree or diploma by the University or any other institution, except by way of background information and duly acknowledged in the thesis, and to the best of my knowledge and belief no material previously published or written by another person except where due acknowledgement is made in the text of the thesis, nor does the thesis contain any material that infringes copyright. This thesis may be made available for loan and limited copying in accordance with the Copyright Act 1968. Julia C. Clark, 14 November 2015 3 ABSTRACT A unique series of convict portraits was created at Tasmania’s Port Arthur penal station in 1873 and 1874. While these photographs are often reproduced, their author remained unidentified, their purpose unknown. The lives of their subjects also remained unexamined. This study used government records, contemporary newspaper reportage, convict memoirs, historical research and modern criminological theory to identify the photographer, to discover the purpose and use of his work, and to develop an understanding of the criminal careers of these men. -
The Myth of Certainty and the Matrix of Uncertainty: Five Contemporary Australian Novels Confront History
The Myth of Certainty and the Matrix of Uncertainty: Five Contemporary Australian Novels Confront History by Charles Scott Nesbitt A dissertation submitted to the Graduate Faculty of Auburn University in partial fulfillment of the requirements for the Degree of Doctor of Philosophy Auburn, Alabama August 7, 2021 Keywords: Historiographic Metafiction, British Literature, Contemporary British and Antipodean Novels, Australia, Postmodernism, Postcolonialism Copyright 2021 by Charles Scott Nesbitt Approved by Dr. Jon Bolton, Chair, Department of English Dr. Alicia Carroll, Department of English Dr. Ernest L. Gibson III, Department of English Dr. Chris Keirstead, Department of English Dr. Rupali Mishra, Department of History Abstract The intersection of postcolonialism and historiographic metafiction can be seen in novels written over the last several decades by British and Antipodean authors concerning the British colonial era in Australia and its aftermath. Novels from this sub-group of writers of historiographic metafiction fit both Linda Hutcheon’s description of historiographic metafiction and some of the concerns of postcolonial writers and theorists, as they revisit the colonial era and critique or reassess the historiographic writings that helped galvanize pro-colonial perspectives and marginalize and dehumanize the Indigenous communities there. While there is much scholarship on historiographic metafiction and postcolonialism, this volume focuses on the specific nexus of those two concepts and its coalescence in contemporary Australian novels of the colonial and postcolonial experience. The novels covered in this volume—by Peter Carey, Matthew Kneale, Rachel Leary, Richard Flanagan, and Alexis Wright—share an interest in 19th Century Australia, the violence and injustice that were an inescapable part of the foundation of the country during that period, and the potential dubiousness of historical documentation. -
Ned Kelly Touring Route
Explore the Ned Kelly Touring Route Now you can explore for yourself the many pieces of the Kelly puzzle by visiting the various Kelly sites in Melbourne, north east Victoria and southern New South Wales on the Ned Kelly Touring Route. From the newly launched Ned Kelly Vault at Beechworth, to the spectacular views of Powers Lookout in the King Valley and the broad plains of Jerilderie, visit as many or as few sites as time or interest allows. There is no need Ned Kelly Vault, Beechworth to visit the sites in any order – the choice is up to you. All the major Kelly sites are marked with informative signs such as the one shown here, recognisable by the distinctive helmet symbol. The signs provide commentary on the events that occurred at the site and expand on the information contained in this brochure. Some Explore the Kelly sites of sites and townships also have MELBOURNE, NORTH EAST VICTORIA a centrally located larger sign providing an overview to help you & SOUTHERN NEW SOUTH WALES get the most from your visit. EL DORADO AND THE WOOLSHED Court trial and subsequent hanging. Ned’s Sites VALLEY mother, Ellen, also appeared in the Beechworth EUROA Court in 1878, and was held in Beechworth Gaol The Woolshed Valley had spawned a chain of gold before being taken to Melbourne to complete her The infamous robbery of the Euroa National rush towns during the 1850s and 60s. It sprang sentence. The Courthouse is just one of a number of Bank by the Kelly Gang in December 1878 was to new life with the Kelly Outbreak in 1878. -
Ned Kelly Txt SI.Indd 3 26/5/09 9:13:24 AM for Inspection Teachers' Time Line of Ned Kelly’S Early Years
Ned Kelly Ned Kelly This biography tells the story of the short life of Ned Kelly, Australia’s most famous outlaw. As a young man, Ned was commended for his bravery. When he formed the Kelly Gang, he was a wanted man. Make up your own mind about this fascinating character. 8.8 9.2 Other Biographies in Springboard 4: Mother Teresa: Saint of the Gutters Springboard 4 Edmund Hillary Written by Ashley Marks For inspection teachers' Ned Kelly ONLY Contents Beginnings . 6 An Act of Bravery . 7 Moving House . 8 The Kelly Family . 10 Trouble with the Law . 11 The Beginnings of the Kelly Gang . 14 Outlaws . 16 Support for the Kelly Gang. 17 Letters from an Outlaw. 18 Taking on the Police . 19 Surrounded! . 20 The End of Ned Kelly . 21 Glossary . 23 Index . 24 Ned Kelly_Txt_SI.indd 3 26/5/09 9:13:24 AM For inspection teachers' Time Line of Ned Kelly’s Early Years ONLY The Kelly family moves to Eleven Mile Creek. Ned's father dies. Ned saves Richard Shelton from drowning. Ned Kelly The Kelly family moves is born. to Avenel, Victoria. 1855 1856 1857 1858 1860 1861 1862 1863 1864 1865 1866 1867 1868 1859 4 Ned Kelly_Txt_SI.indd 4 26/5/09 9:13:26 AM For inspection teachers' ONLY Ned is arrested for robbery and assault on Ah Fook, held for 10 days, then released for lack of evidence. Ned later meets bushranger Harry Power. Ned, his stepfather George, and others are involved in Ned is accused of stealing stock from aiding Harry Power. -
The Australian Register Unesco Memory of the World Program
The australian register unesco memory of the World program The australian register unesco memory of the World program Published by the UNESCO Australian Memory of the World Committee PO Box 9177 Deakin ACT 2600 www.amw.org.au Text © UNESCO Australian Memory of the World Committee and individual authors (go to www.amw.org.au/Contact us to obtain permission to reproduce material from this book). Images © as per credits accompanying images (please contact custodial institutions and individuals for information on obtaining and reproducing images). All rights reserved First edition 2015 ISBN: 978-0-646-93390-0 Edited by Roslyn Russell and Anne-Marie Condé Designed by Racheal Brühn Printed by Bytes n’ Colours The ideas and opinions expressed in this publication are those of the authors and are not necessarily those of UNESCO and do not commit the Organization. The UNESCO Australian Memory of the World Committee operates under the auspices of the Australian National Commission for UNESCO. Front cover images: (top row, left to right) Munggurrawuy Yunupingu, Port of Macassar, 1947, crayon on brown paper, 114 x 74 cm, Berndt Museum, The University of Western Australia © Estate of the artist. Acc. No. 6970; For the benefit of J. Butler and W. Bryant … [Sydney Playbill] nla.aus-vn4200235-s1, National Library of Australia; Torres Strait pigeon eating the fruit of the wild plum, watercolour by Segar Passi, Margaret Lawrie Torres Strait Island Collection, State Library of Queensland. (Bottom row, left to right) Letter by William Light to George Jones, 22 November 1836, State Library of South Australia; Petition for reprieve of Ned Kelly, Public Record Office Victoria; Coffer fish from William Buelow Gould’s Sketchbook of Fishes, Allport Library and Museum of Fine Arts, Hobart; Migrant Selection Documents for Antoni Poboka, Series A12522, R50-R53, National Archives of Australia; Driver Jack, Norman Tindale, Charles P. -
Reading the Historical Phenomenon of Australian Bushrangers
READING THE HISTORICAL PHENOMENON OF AUSTRALIAN BUSHRANGERS Yohanes Hartadi English Department, Atma Jaya Indonesian Catholic University, Jln. Jenderal Sudirman No. 51, Jakarta Selatan 12930 ABSTRACT Outlaws in their various images have been important parts of history. In Australia, the longest lasting image of outlaws is the bushranger. Despite its popularity, there is a range of depictions of bushrangers and these are not necessarily similar. Interpretation of the bushrangers in colonial time differs from contemporary imagining. This papers aims at unfolding the various interpretations of the bushrangers in different periods in many types of artifact. Information was collected and interpreted by library research. The artifact analysis will be seen through a postmodernism theory by Michel Foucault and Roland Barthes. Since the phenomenon of bushranger stemmed from the colonial period, this study will commence from the period up to contemporary period. It can be concluded that a study of the different periods finds out that knowledge of the bushrangers does not make up a linear history, but rather a discontinuity in the historical narratives. Keywords: history, bushranger, Australian bushranger ABSTRAK Orang yang tidak taat hukum (penjahat) dalam gambaran yang berbeda adalah merupakan bagian sejarah yang penting. Di Australia, gambaran nyata bagi orang tak taat hukum adalah pengembara/petualang di hutan. Selain popularitas, terdapat berbagai gambaran berbeda tentang petualang tersebut. Interpretasi pada jaman kolonial berbeda dengan gambaran di masa kontemporer. Artikel bertujuan menunjukkan berbagai interpretasi terhadap petualang pada masa dan artefak berbeda. Informasi diperoleh dengan penelitian pustaka. Analisis artefak dilakukan dengan teori postmodernisme dari Michel Foucault dan Roland Barthes. Disimpulkan, studi dalam berbagai masa menunjukkan bahwa pengetahuan tentang petualang bukan merupakan sejarah linier, tetapi lebih pada ketidakberlangsungan dalam cerita sejarah. -
Janet Achurch, Ibsen, and the New Woman, Australia
The Woman Who Did: Janet Achurch, Ibsen, and the New Woman, Australia 1889–1891 by Christine Judith Angel, BTourism, B.A. (Hons) School of Humanities, English Program Submitted in fulfilment of the requirements for the degree of Doctor of Philosophy (PhD) University of Tasmania September 2014 Declaration of Originality I declare that this thesis contains no material which has been accepted for a degree or diploma by the University or any other institution, except by way of background information and duly acknowledged in the thesis, and to the best of my knowledge and belief no material previously published or written by another person except where due acknowledgement is made in the text of the thesis, nor does the thesis contain any material that infringes copyright. ………………………… September 2014 Authority of access This thesis may be made available for loan and limited copying and communication in accordance with the Copyright Act 1968. ………………………… September 2014 Abstract The Australian theatre in the late nineteenth century was in transition: it was, like the country, seeking its own identity in a period of social change. The contributions made to its development by men are well documented. Those made by women have received much less recognition. This thesis addresses that hiatus, by examining the life, celebrity, and influence of English actress, Janet Achurch. It focuses on her 1889–91 Australian tour and the ambivalent responses to her portrayal of Nora in Henrik Ibsen’s A Doll’s House. Achurch, with her husband, actor Charles Charrington, came to Australia under contract to entrepreneurs Williamson, Garner, and Musgrove. On 14 September, 1889 she opened at the Princess’s Theatre in Melbourne with A Doll’s House, the play now most closely connected with the concept of the New Woman. -
Episode 32 – Package (PDF)
Episode 32 10th November 2020 US Election Result 1. Discuss the BTN US Election Result story as a class. 2. It is compulsory to vote in the US. True or false? 3. Why did many Americans mail in their vote? 4. Donald Trump accused his opposition of… a. Not wearing a mask to the polling booth b. Playing golf instead of voting c. Rigging the election 5. Why were some of Donald Trump’s supporters protesting outside ballot-counting centres? 6. Who has been elected the President of the United States? 7. Which political party do they belong to? 8. Complete the following sentence. Donald Trump is demanding a recount of _______ in some states. 9. What words would you use to describe what you saw in this news story? 10. What questions do you have about this story? UK Lockdown 1. Discuss the BTN UK Lockdown story with another student. 2. Where does Sam live in England? Find on a map. 3. Why is Sam’s mum more likely to catch the coronavirus? 4. What is Sam’s routine when he gets home from school? 5. What challenges has Sam been doing to raise money? 6. How has the second lockdown helped Sam and his mum? 7. Where in the UK has one of the highest rates of COVID-19? 8. At Mikey’s school they have bubbles for each year group. What does this mean? 9. How does Mikey make sure he is staying active during lockdown? 10. How did you feel watching the BTN UK Lockdown story? Conscription 1.