Solar Desalination with HD Cycle
Total Page:16
File Type:pdf, Size:1020Kb
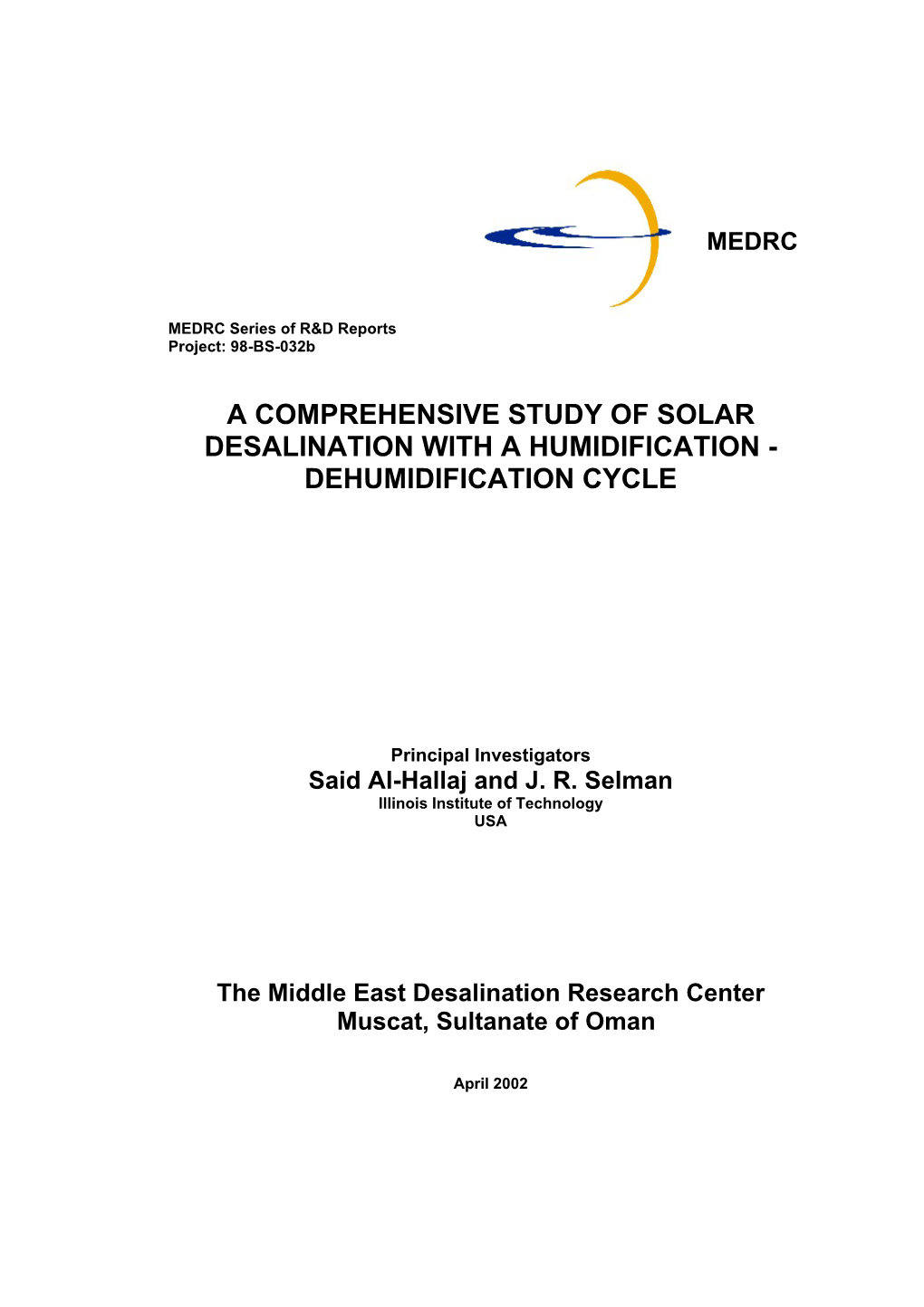
Load more
Recommended publications
-
Cweee 2020071714005325.Pdf
Computational Water, Energy, and Environmental Engineering, 2020, 9, 48-74 https://www.scirp.org/journal/cweee ISSN Online: 2168-1570 ISSN Print: 2168-1562 A Review Study of Experimental and Theoretical Humidification Dehumidification Solar Desalination Technology Mohamed M. Khairat Dawood1, Ahmed Amer2, Tamer Mansour1, Mohamed A. Teamah3, Attia Aref1 1Mechanical Engineering Department, Faculty of Engineering, Suez Canal University, Ismailia, Egypt 2Mechanical Engineering Department, College of Engineering and Technology, American University of the Middle East, Egaila, Kuwait 3Mechanical Engineering Department, Faculty of Engineering, Alexandria University, Alexandria, Egypt How to cite this paper: Dawood, M.M.K., Abstract Amer, A., Mansour, T., Teamah, M.A. and Aref, A. (2020) A Review Study of Experi- Most of the desalination technologies consume a huge quantity of energy re- mental and Theoretical Humidification De- sulting from petroleum products in the form of heat or electrical energy. So- humidification Solar Desalination Technolo- lar desalination is a promisingly sustainable freshwater production technolo- gy. Computational Water, Energy, and En- vironmental Engineering, 9, 48-74. gy. Solar desalination humidification dehumidification process showed the https://doi.org/10.4236/cweee.2020.93005 best approach as it is of the highest overall energy efficiency. In this review paper, a detailed study of the previous work is performed on solar humidifi- Received: June 9, 2020 cation dehumidification desalination techniques experimentally and theoret- Accepted: July 17, 2020 Published: July 20, 2020 ically. Also in this review, different types of HDH systems were mentioned. The review showed that the humidification dehumidification desalination Copyright © 2020 by author(s) and systems are suitable for decentralized demand. -
Chapter 9 Solar Desalination 1. Introduction
CHAPTER 9 SOLAR DESALINATION John H. Lienhard,1,¤ Mohamed A. Antar,2 Amy Bilton,1 Julian Blanco,3 & Guillermo Zaragoza4 1 Center for Clean Water and Clean Energy, Room 3-162, Department of Mechanical Engineering, Massachusetts Institute of Technology, 77 Massachusetts Avenue, Cambridge, Massachusetts 02139-4307, USA 2 Department of Mechanical Engineering, King Fahd University of Petroleum and Minerals, Dhahran, Saudi Arabia 3 Plataforma Solar de Almeria, Carretera de Senes s/n, 04200 Tabernas (Almeria), Spain 4 Visiting Professor of Electrical Engineering, King Saud University, Riyadh, Saudi Arabia ¤Address all correspondence to John H. Lienhard E-mail: [email protected] In many settings where freshwater resources or water supply infrastructure are inadequate, fossil energy costs may be high whereas solar energy is abundant. Further, in the industri- alized world, government policies increasingly emphasize the replacement of fossil energy by renewable, low-carbon energy, and so water scarce regions are considering solar-driven desalination systems as a supplement to existing freshwater supplies. Even in regions where petroleum resources are copious, solar-driven desalination is attractive as a means of con- serving fossil fuel resources and limiting the carbon footprint of desalination. Finally, in set- tings that are remote and ‘off-the-grid,” a solar driven desalination system may be more eco- nomical than alternatives such as trucked-in water or desalination driven by diesel-generated electricity. This article reviews various technologies that couple thermal or electrical solar energy to thermal or membrane based desalination systems. Basic principles of desalination are reviewed. Solar stills and humidification-dehumidification desalination systems are dis- cussed. -
Water Desalination by Humidification and Dehumidification of Air, Seawater Greenhouse Process - Karim Bourouni, Mohamed Thameur Chaibi, Ali Al Taee
SOLAR ENERGY CONVERSION AND PHOTOENERGY SYSTEMS - Water Desalination by Humidification and Dehumidification of Air, Seawater Greenhouse Process - Karim Bourouni, Mohamed Thameur Chaibi, Ali Al Taee WATER DESALINATION BY HUMIDIFICATION AND DEHUMIDIFICATION OF AIR, SEAWATER GREENHOUSE PROCESS Karim Bourouni, Mohamed Thameur Chaibi and Ali Al Taee UR EBSS Ecole Nationale d’Ingénieurs de Tunis, BP 37, 1002 Le Belvédère, Tunisie INGREF Keywords: Water Desalination, Humidification, Dehumidification, Seawater greenhouse Contents 1. Introduction 2. Desalination Process by Humidification and Dehumidification 2.1. Moist Air 2.2. Humidifying with Cooling and Dehumidifying Processes 2.3. Using Humidification Dehumidification (HD) Process in Desalination 2.4. Heat and Mass Transfer in HD Desalination Process 2.5. Overview on Some Desalination HD Projects 3. Seawater Greenhouse Process (SWGH): Principles and Fundamentals 3.1. Process Description 3.2. The Condenser in the SWGH 3.2.1. Different Condenser Layouts in SWGH 3.2.2. Cooling the Condenser 3.3. The Evaporator (Humidifier) in the SWGH 3.4. The planting area in the SWGH 3.5. Construction and Materials 3.6. Energy Requirements 3.7. Economics and Applications 4. Design of SWGH 4.1. Simplified Model of Heat and Mass Transfer inside the SWGH 4.2. Efficiency of the Evaporative cooling 4.3. Design of Condensers 4.4. Venting System 4.5. Detailed Thermodynamic Model for SWGH 5. Overview on the installed SWGH projects: Case Studies 5.1. Case Study 1: The SWGH project in Tenerife 5.1.1. Description of the Pilot Plant 5.1.2. Performances of the SWGH 5.2. Case Study 2: The SWGH Project in UAE 5.2.1. -
Design and Experimental Study on a New Closed-Cycle Desalination System Based on Ambient Temperature
processes Article Design and Experimental Study on a New Closed-Cycle Desalination System Based on Ambient Temperature Jun Liu 1, Yong Sun 2, Sanjiang Yv 2, Jiaquan Wang 3,* and Kaixuan Hu 1 1 School of Civil Engineering, Hefei University of Technology, Hefei 230009, China; [email protected] (J.L.); hkx1994091066 @163.com (K.H.) 2 Anhui Tongsu Environment Protection Technology Co Ltd., Hefei 230009, China; [email protected] (Y.S.); [email protected] (S.Y.) 3 School of Resources and Environmental Engineering, Hefei University of Technology, Hefei 230009, China * Correspondence: [email protected] or [email protected] Received: 7 August 2020; Accepted: 9 September 2020; Published: 10 September 2020 Abstract: The use of seawater desalination technology to solve water shortages in energy- and resource-scarce regions has attracted widespread attention worldwide. In this paper, the performance of a closed-cycle humidification–dehumidification desalination system with a heat pump was experimentally investigated. The system is a closed-cycle system, which includes humidifiers, a heat pump, dehumidifiers, and an air heat exchanger. The heat pump is used by the system to carry energy. The effects of different parameters on the system performance were studied. Scale and economic analyses of the system were conducted to explore the application prospects of the system. The maximum gained output ratio of the system was 4.82. The maximum freshwater production was 960 kg/h, and the cost per kilogram of freshwater was USD 0.03, which are more considerable compared with other systems. This system provides an effective way to save energy in remote areas with energy shortages and freshwater resource shortages. -
An Overview of Industrial Desalination Technologies ASME Industrial Demineralization (Desalination): Best Practices & Future Directions Workshop
An Overview of Industrial Desalination Technologies ASME Industrial Demineralization (Desalination): Best Practices & Future Directions Workshop Washington, D.C. Shahid Chaudhry January 28-29, 2013 1 • The Challenge: Increasing Demand of Water & Energy Resources; Decreasing Supplies of Conventional Water & Energy Resources. Sustainable Management of Water & Energy Resources 2 • Eight Major Water Using Industries Oil & Gas Refining & Petrochemicals Power Generation Food and Beverage Pharmaceutical Microelectronics Pulp & Paper, and Mining GWI: Industrial Desalination & Water Reuse: Ultrapure water, challenging waste streams and improved efficiency, 3 Strategies: Water Conservation / Water Use Efficiency Unaccounted / Water Losses Water Recycling Desalination - Most Energy Intensive / Expensive Water? 4 • Desalination An Energy Intensive Process, An Integral Part of the Future Water Supply Portfolio Source Waters – Generally Four Types Brackish Ground Water, Surface Water, Municipal WW, Agricultural Runoff, Industrial Effluents, Sea Water, etc. Main Processes Categories: Thermal 4 - 6 kWh / m3 + Steam Heating of Contaminated Water under Vacuum Conditions to Create Pure Water Vapors) Membranes 1 - 6 kWh / m3 Energy Requirements - Function of: Plant Capacity, Feed Water Quality, Pretreatment, Desalination Process/Technology, and Level of Treatment Desalination Technology of Most Interest Today Reverse Osmosis 5 • Desalination Methods Distillation Multi-Stage Flash Distillation (MSF) Multiple-Effect Distillation (MED / ME) Vapor-Compression -
An Applied Review of Water Desalination Technologies and an Introduction to Capillary-Driven Desalination
water Article Looking Beyond Energy Efficiency: An Applied Review of Water Desalination Technologies and an Introduction to Capillary-Driven Desalination Seyedsaeid Ahmadvand 1,* , Behrooz Abbasi 1,*, Babak Azarfar 1, Mohammed Elhashimi 2, Xiang Zhang 2 and Bahman Abbasi 2,* 1 Department of Mining and Metallurgical Engineering, University of Nevada, Reno, NV 89557, USA; [email protected] 2 School of Mechanical, Industrial and Manufacturing Engineering, Oregon State University, Bend, OR 97702, USA; [email protected] (M.E.); [email protected] (X.Z.) * Correspondence: [email protected] (S.A.); [email protected] (B.A.); [email protected] (B.A.) Received: 4 March 2019; Accepted: 1 April 2019; Published: 4 April 2019 Abstract: Most notable emerging water desalination technologies and related publications, as examined by the authors, investigate opportunities to increase energy efficiency of the process. In this paper, the authors reason that improving energy efficiency is only one route to produce more cost-effective potable water with fewer emissions. In fact, the grade of energy that is used to desalinate water plays an equally important role in its economic viability and overall emission reduction. This paper provides a critical review of desalination strategies with emphasis on means of using low-grade energy rather than solely focusing on reaching the thermodynamic energy limit. Herein, it is argued that large-scale commercial desalination technologies have by-and-large reached their engineering potential. They are now mostly limited by the fundamental process design rather than process optimization, which has very limited room for improvement without foundational change to the process itself. The conventional approach toward more energy efficient water desalination is to shift from thermal technologies to reverse osmosis (RO). -
Design, Construction and Performance Analysis of a Solar Powered Dual Mode Desalination System for Water Purification
Design, Construction and Performance Analysis of a Solar Powered Dual Mode Desalination System for Water Purification A Thesis Submitted in partial Fulfillment of the Requirements for the Degree of Master of Science in Renewable Energy Technology At the Institute of Energy University of Dhaka September 2016 Supervised By: Prof. Dr. Saiful Huque Director Institute of Energy University of Dhaka Submitted By: Asif Jaman Shishir Exam Roll: 7001 Registration No: HA-1911 Session: 2006-2007 Institute of Energy University of Dhaka i Candidate’s Declaration I confirm that this thesis represents my own work; the contribution of any supervisors and others to the research and to the thesis was consistent with normal supervisory practice. External contributions to the research are acknowledged. _______________________ Asif Jaman Shishir Exam Roll: 7001 Registration No: HA-1911 Session: 2006-2007 Institute of Energy University of Dhaka Date: ________________ ii Supervisor’s Declaration The MS level thesis report titled by “Design, Construction and Performance Analysis of a Solar Powered Dual Mode Desalination System for Water Purification” has been carried out and dissertation was prepared under my supervision. Herby I confirm that, to the best of my knowledge the thesis represents the original research work of the candidate; the contribution made to the research by me, by others of the University was consistent with normal supervisory practice, and external contributions to the research are acknowledged. I believe the thesis to be in a suitable presentational form and is ready for examination. _______________________________ Prof. Dr. Saiful Huque Director Institute of Energy University of Dhaka Date: _______________ iii Acknowledgments First and foremost, All credit and gratitude goes to our Almighty Allah for the wisdom and perseverance that he has been bestowed upon me during this research. -
Experimental and Numerical Analysis of a PCM-Supported Humidification-Dehumidification Solar Desalination System
Technische Universität München Institut für Energietechnik Lehrstuhl für Thermodynamik Experimental and Numerical Analysis of a PCM-Supported Humidification-Dehumidification Solar Desalination System Abdel Hakim M. A. Hassabou Vollständiger Abdruck der von der Fakultät für Maschinenwesen der Technischen Universität München zur Erlangung des akademischen Grades eines DOKTOR – INGENIEURS genehmigten Dissertation. Vorsitzender: Univ.-Prof. Dr.-Ing. Dirk Weuster-Botz Prüfer der Dissertation: 1. Univ.-Prof. Wolfgang H. Polifke, Ph. D. (CCNY) 2. Prof. Abdalla Hanafi, Ph. D., University of Kairo / Ägypten Die Dissertation wurde am 27.09.2011 bei der Technischen Universität München eingereicht und durch die Fakultät für Maschinenwesen am 10.11.2011 angenommen. Preface First and foremost I thank the Greatest Creator for his countless blessings and neat creation: “He sends down rain from the sky and with it gives life to the earth after it is dead: Verily in that are signs for those who are wise.” [Al- Qur’aan 30:24]. “It is He Who has let free the two bodies of flowing water: one palatable and sweet, and the other salty and bitter; yet has He made a barrier between them, and a partition that is forbidden to be passed.” [Al-Qur’aan 25:53]. “It is He Who created The Night and the Day, and the sun and the moon: All (the celestial bodies) Swim along, each in its rounded course.” [Al-Qur’aan 21:33]. “It is not permitted to the Sun to catch up the Moon, nor can the Night outstrip the Day: Each (just) swims along in (its own) orbit (According to Law).” [Al-Qur’aan 36:40]. -
State of Art Water Desalination Technologies Using Conventional and Sustainable Energy Sources
STATE OF ART WATER DESALINATION TECHNOLOGIES USING CONVENTIONAL AND SUSTAINABLE ENERGY SOURCES Mahmoud Shatat1, Saffa Riffat2, Said Ghabayen3 1: PhD researcher, Institute of Sustainable Energy Technology, University of Nottingham, Nottingham NG7 2RD, UK, [email protected] 2: Chair Professor, Institute of Sustainable Energy Technology, University of Nottingham, Nottingham NG7 2RD, UK, [email protected] 3: Assistant Professor, Environmental Engineering Department, IUG, Gaza, [email protected] ABSTRACT There is an acute shortage of potable water in many countries over the world especially in the Middle East region. Currently over one-third of the world's population lives in areas where people are unable to meet their water demand of fresh water [1]. Hence it has become viable that water desalination can be relied on it as a new sustainable water resource. Nevertheless water is covering about three quarters of the planet’s surface, about 97.5% of the earth’s water is salty water in the oceans and only 2.5% is fresh water in ground water, lakes and rivers and this supplies most human and animal needs. Tackling the water scarcity problem must involve better and more economic ways of desalinating seawater. For instance, the survey of desalination technologies showed that the rapid developments in membrane desalination technology have made it cost competitive with thermal processes. The current estimated water production cost for the world’s largest RO seawater desalination plant is $0.52/m3 [48]. However the use of renewable sustainable energies for desalination becomes a reasonable and technically mature alternative towards a sustainable solution for water scarcity which could be suitable for different desalination process at viable cost and are uniquely suited to provide fresh water in the Gaza strip where water and electricity infrastructure is currently lacking. -
The Potential of Solar-Driven Humidification-Dehumidification Desalination for Small-Scale Decentralized Water Production
The potential of solar-driven humidification-dehumidification desalination for small-scale decentralized water production The MIT Faculty has made this article openly available. Please share how this access benefits you. Your story matters. Citation Narayan, G. Prakash et al. “The potential of solar-driven humidification-dehumidification desalination for small-scale decentralized water production.” Renewable and Sustainable Energy Reviews 14.4 (2010): 1187-1201. As Published http://dx.doi.org/10.1016/j.rser.2009.11.014 Publisher Elsevier Version Author's final manuscript Citable link http://hdl.handle.net/1721.1/52624 Terms of Use Attribution-Noncommercial-Share Alike 3.0 Unported Detailed Terms http://creativecommons.org/licenses/by-nc-sa/3.0/ The potential of solar-driven humidification-dehumidification desalination for small-scale decentralized water production G. Prakash Narayan 1, Mostafa H. Sharqawy 1, Edward K. Summers 1, John H. Lienhard 1,*, Syed M. Zubair 2 and M. A. Antar 2. 1Department of Mechanical Engineering, Massachusetts Institute of Technology, Cambridge, USA. 2 Department of Mechanical Engineering, King Fahd University of Petroleum and Minerals, Saudi Arabia. Abstract World-wide water scarcity, especially in the developing world, indicates a pressing need to develop inexpensive, decentralized small-scale desalination technologies which use renewable resources of energy. This paper provides a comprehensive review of the state- of-the-art in one of the most promising of these technologies, solar-driven humidification-dehumidification (HDH) desalination. Previous studies have investigated many different variations on the HDH cycle. In this paper, performance parameters which enable comparison of the various versions of the HDH cycle have been defined and evaluated. -
Solar Desalination: a Critical Review
International Journal of Mechanical Engineering and Technology (IJMET) Volume 10, Issue 08, August 2019, pp. 244-270, Article ID: IJMET_10_08_021 Available online at http://iaeme.com/Home/issue/IJMET?Volume=10&Issue=8 ISSN Print: 0976-6340 and ISSN Online: 0976-6359 © IAEME Publication SOLAR DESALINATION: A CRITICAL REVIEW Devesh Singh and Freddie L. Inambao* Green Energy Solutions Research Group, Discipline of Mechanical Engineering University of Kwazulu-Natal, 238 Mazisi Kunene Road, Glenwood, Durban, 4041, South Africa *[email protected] ABSTRACT Rapid population growth and insufficient conservation of water resources in water scarce regions are but two reasons for the predicted water shortages that are likely to plague future generations. Desalination, over the last two decades, has seen major strides made in the production of potable water in large scale projects. Through continuous research and development new and improved methods have been found and implemented across the world. The viability of desalination as a reliable alternative potable water source has been proven on numerous occasions through various studies, projects and devices. This paper reviews the need for research into alternative water purification methods in general, desalination methods in particular, their working principles and mathematical modelling. The economics of thermal and membrane based desalination is noted. Key words: Solar, Water desalination, Water purification, Potable water Cite this Article: Devesh Singh and Freddie L. Inambao, Solar Desalination: A Critical Review. International Journal of Mechanical Engineering and Technology 10(8), 2019, pp. 244-270. http://iaeme.com/Home/issue/IJMET?Volume=10&Issue=8 1. INTRODUCTION The global population rapidly increases by approximately 80 million people per year [1] and is estimated to reach 9.1 billion by the year 2050 [2]. -
Integration of Membrane Distillation and Solar Thermal Systems for Co- Production of Purified Water and Heat
Integration of Membrane Distillation and Solar Thermal Systems for Co- production of Purified Water and Heat Uday Kumar N T Doctoral Thesis 2017 KTH School of Industrial Engineering and Management Department of Energy Technology Division of Heat and power technology SE-100 44 STOCKHOLM To my father Nutakki Subba Rao (Late), my beloved mother Indira and my lovely wife Vyplavi. ISBN: 978-91-7729-581-5 TRITA- KRV-17-10 ISSN 1100-7990 ISRN KTH-KRV-17-10-SE © Uday Kumar N T, 2017 Doctoral Thesis / Uday Kumar N T Page I Abstract In the Middle East and North Africa region fresh water resources are very scarce and the existing sources are depleting rapidly. Desalination is the method to fulfill increasing water demand, and people depend mostly upon bottled water for drinking purposes. Bottled water is resource and energy demanding, hence there is a need for supplying drinkable water in a sustainable way. The main objective of this research is to develop solutions for providing potable water to urban communities through integrating membrane distillation water purification units with solar driven hot water installations. A single-cassette Air Gap Membrane Distillation (AGMD) unit was tested on laboratory scale to investigate the influence of various operating parameters on the distillate production. Particular attention was given for identifying process conditions relevant to the design of solar energy integrated systems. In parallel, a simplified empirical model using response surface methods was developed and validated against bench scale experimental results. The developed model for performance indicators was later employed in dynamic simulations of a solar thermal integrated membrane distillation system.