Injection and Micro Injection of Polymeric Plastics Materials: a Review
Total Page:16
File Type:pdf, Size:1020Kb
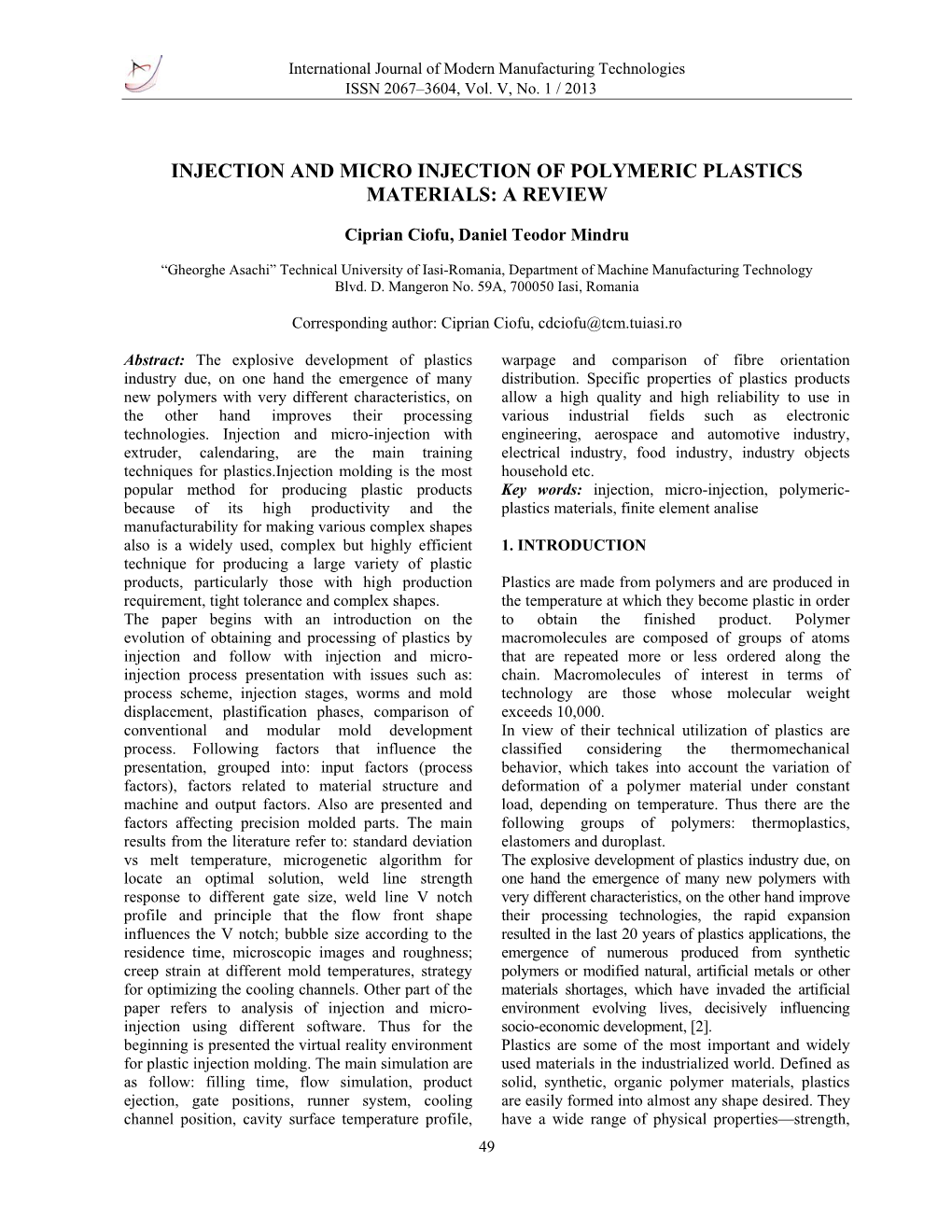
Load more
Recommended publications
-
Type of the Paper
polymers Review Tuning Power Ultrasound for Enhanced Performance of Thermoplastic Micro-Injection Molding: Principles, Methods, and Performances Baishun Zhao 1,2 , Yuanbao Qiang 1,2, Wangqing Wu 1,2,* and Bingyan Jiang 1,2 1 State Key Laboratory of High-Performance Complex Manufacturing, Central South University, Lushan South Road 932, Changsha 410083, China; [email protected] (B.Z.); [email protected] (Y.Q.); [email protected] (B.J.) 2 School of Mechanical and Electrical Engineering, Central South University, Lushan South Road 932, Changsha 410083, China * Correspondence: [email protected]; Tel.: +86-158-7429-5500 Abstract: With the wide application of Micro-Electro-Mechanical Systems (MEMSs), especially the rapid development of wearable flexible electronics technology, the efficient production of micro-parts with thermoplastic polymers will be the core technology of the harvesting market. However, it is significantly restrained by the limitations of the traditional micro-injection-molding (MIM) process, such as replication fidelity, material utilization, and energy consumption. Currently, the increas- ing investigation has been focused on the ultrasonic-assisted micro-injection molding (UAMIM) and ultrasonic plasticization micro-injection molding (UPMIM), which has the advantages of new Citation: Zhao, B.; Qiang, Y.; Wu, W.; plasticization principle, high replication fidelity, and cost-effectiveness. The aim of this review is Jiang, B. Tuning Power Ultrasound to present the latest research activities on the action mechanism of power ultrasound in various for Enhanced Performance of polymer micro-molding processes. At the beginning of this review, the physical changes, chemical Thermoplastic Micro-Injection changes, and morphological evolution mechanism of various thermoplastic polymers under different Molding: Principles, Methods, and application modes of ultrasonic energy field are introduced. -
Micro-Nanostructured Polymer Surfaces Using Injection Molding: a Review K
View metadata, citation and similar papers at core.ac.uk brought to you by CORE provided by Constellation Micro-Nanostructured Polymer Surfaces Using Injection Molding: A Review K. Maghsoudi*, R. Jafari, G. Momen, M. Farzaneh Department of Applied Sciences, University of Quebec in Chicoutimi (UQAC) 555, boul. de l'Université, Chicoutimi, Quebec, G7H 2B1, Canada * E-mail: [email protected] Abstract Micro injection molding is in great demand due to its efficiency and applicability for industry. Polymer surfaces having micro-nanostructures can be produced using injection molding. However, it is not as straightforward as scaling-up of conventional injection molding. The paper is organized based on three main technical areas: mold inserts, processing parameters, and demolding. An accurate set of processing parameters is required to achieve precise micro injection molding. This review provides a comparative description of the influence of processing parameters on the quality of final parts and the precision of final product dimensions in both thermoplastic polymers and rubber materials. It also highlights the key parameters to attain a high quality micro-nanostructured polymer and addresses the contradictory effects of these parameters on the final result. Moreover, since the produced part should be properly demolded to possess a high quality textured polymer, various demolding techniques are assessed in this review as well. Keywords: injection molding; micro-nanostructure; processing parameters; demolding; replication 1. Introduction Among the different polymer processing techniques used to produce materials having a specifically desired size and shape, injection molding is highly preferred for mass production systems, and has been used for many years in the polymer industry 1-2. -
The Micro Injection Moulding Process for Polymeric Components Manufacturing
4 The Micro Injection Moulding Process for Polymeric Components Manufacturing R. Surace, G. Trotta, V. Bellantone and I. Fassi ITIA-CNR, Institute of Industrial Technology and Automation, National Research Council, Italy 1. Introduction In recent years, there is an increasing demand for small and even micro scale parts and this trend towards miniaturization makes the micro system technologies of growing importance. Microfabrication process capabilities should expand to encompass a wider range of materials and geometric forms, by defining processes and related process chains that can satisfy the specific functional and technical requirements of new emerging multi-material products, and ensure the compatibility of materials and processing technologies throughout these manufacturing chains. Example technologies to be investigated either individually or in combination are technologies for direct- or rapid manufacturing, energy assisted technologies, microreplication technologies, qualification and inspection methods, functional characterisation methods and integration of "easy and fast" on-line control systems. The processes should demonstrate significantly high production rates, accuracy and enhanced performance or quality, creating capabilities for mass manufacture of microcomponents and miniaturised parts incorporating micro- or nanofeatures in different materials. Processes should also provide high flexibility and seamless integration into new micro- and nanomanufacture scenario. Micro- and nano-manufacturing technologies can provide the basis of the next industrial revolution that could dramatically modify the way in which businesses are setup, run and marketed. Micro injection moulding can be defined as one of the key technologies for micro manufacturing because of its mass production capability and relatively low production cost. It is the process of transferring the micron or even submicron features of metallic moulds to a polymeric product. -
Microinjection Molding of Microsystem Components: New Aspects in Improving Performance
IOP PUBLISHING JOURNAL OF MICROMECHANICS AND MICROENGINEERING J. Micromech. Microeng. 23 (2013) 093001 (21pp) doi:10.1088/0960-1317/23/9/093001 TOPICAL REVIEW Microinjection molding of microsystem components: new aspects in improving performance Can Yang1, Xiao-Hong Yin and Guang-Ming Cheng Laboratory for Advanced Material Processing, Zhejiang Normal University, Jinhua, Zhejiang, 321004, People’s Republic of China E-mail: [email protected] Received 17 March 2013, in final form 17 May 2013 Published 1 August 2013 Online at stacks.iop.org/JMM/23/093001 Abstract Microinjection molding (μIM) is considered to be one of the most flexible, reliable and cost effective manufacturing routes to form plastic micro-components for microsystems. The molding machine, mold tool fabrication, material selection and process controlling in this specific field have been greatly developed over the past decades. This review aims to present the new trends towards improving micro-component performance by reviewing the latest developments in this area and by considering potential directions. The key concerns in product and mold designing, essential factors in simulation, and micro-morphology and resultant properties are evaluated and discussed. In addition, the applications, variant processes and outlook for μIM are presented. Throughout this review, decisive considerations in seeking improved performance for microsystem components are highlighted. (Some figures may appear in colour only in the online journal) 1. Introduction required in certain applications. Since the 1990s, polymer materials have been increasingly incorporated into MEMS Micro-electromechanical-systems (MEMS) or microsystem industries. An important reason is that they provide not only technology (MST) has already become a familiar part of controllable thermal, mechanical and electrical properties, but our daily life in that various micro-components can be also unique chemical, structural and biological functionalities found in a number of devices such as laptops, microphones, not available in any other material. -
Study on Relevant Factors Influencing the Strength of Weld Line Defect in Micro Injection Molding Process
Materialwissenschaft und Werkstofftechnik Lei Xie Doctor Dissertation Study on relevant factors influencing the strength of weld line defect in micro injection molding process Prof. Dr.-Ing. Gerhard Ziegmann Kunstofftechnik Institute of Polymer Materials and Plastics Engineering Study on relevant factors influencing the strength of weld line defect in micro injection molding process Dissertation Zur Erlangung des Grades eines Doktor-Ingenieurs Vorgelegt von Lei Xie aus Shanxi, P.R.China genehmigt von der Fakultät für Natur- und Materialwissenschaften Der Technischen Universität Clausthal Tag der mündlichen Prüfung 02.07.2010 Acknowledgement At the moment of this dissertation finishing in Institute of Polymer Materials and Plastics Engineering, Clausthal University of Technology, I would like express my speechless appreciate to all the colleagues, friends and my family who supported, encouraged and guided me through all the duration of my doctoral research and study. Especially, I want to say thanks to Prof. Gerhard Ziegmann, as my doctoral supervisor, his priceless guidance, encouragement, and support throughout this work help me finally reach the goal. He not only plays the role as the advisor in academic aspect, he is also a kind and helpful friend and eldership in my daily life. I learned not only the scientific knowledge but also the spirit and philosophy to being an active, motivated, passionate, thoughtful and helpful person, which I will benefit of in rest of my life. I also want to give my thanks to Prof. Michael Gehde for being the reviewer and defense opponent of my dissertation. His constructive suggestion and careful correction are quite helpful for me to improve the dissertation finally to be able to be published. -
Material Behavior in Micro Molding
® ® Material Behavior In WORLD LEADERS IN MICRO-MOLD MANUFACTURING SOLUTIONS Micro Molding Comparison of Thermoplastic Material, Microscopic Size, Tight Tolerance and Thin Wall Characteristics Injection molding microscopic thermoplastic components while observ- ing micron tolerances and high precision geometries is what we have perfected and continue to improve for over three decades. Background Accumold is a world leader in high-volume precision micro molding and has expertise in micro electronics, medical technology, wearables, emerging technologies, automotive and fiber / micro optics. The company began operations in a rented garage when the founders discovered there was a growing need to manufacture small and micro injection molded components that went well-beyond the available mold- ing systems of the day. This discovery led to the invention of our first Micro-Mold® platform in 1985. Since those early days, our focus has remained steadfast to the art and science of micro injection molding. In fact, Accumold is the only compa- ny that has been continuously dedicated to micro molding for over 30 years. We remain committed to serving high-tech industries that require high-volume, small, complex micro injection molded parts with high qual- ity and fast turn-around. There is probably little doubt that just about everything we come in contact with today has some form of plastic as part of its design. Plastic has played an interesting role in our history if you think about some of the transforma- tions in the recent past. Many of us have watched everyday items slowly evolve from other materials such as wood, metal, leather and even cotton. -
Development of Innovative Gas- Assisted Foam Injection Molding
Development of Innovative Gas- Assisted Foam Injection Molding Technology By Peter Ungyeong Jung A thesis submitted in conformity with the requirements for the degree of Doctor of Philosophy Department of Mechanical and Industrial Engineering University of Toronto © Copyright by Peter Ungyeong Jung 2013 Development of Innovative Gas-Assisted Foam Injection Molding Technology Peter Ungyeong Jung Degree of Doctor of Philosophy, 2013 Department of Mechanical and Industrial Engineering University of Toronto ABSTRACT Injection molding technology is utilized for a wide range of applications from mobile phone covers to bumper fascia of automotive vehicles. Foam injection molding (FIM) is a branched manufacturing process of conventional injection molding, but it was designed to take advantage of existing foaming technology, including material cost saving and weight reduction, and to provide additional benefits such as improvement in dimensional stability, faster cycle time, and so on. Gas-assisted injection molding (GAIM) is another supplemental technology of injection molding and offers several advantages as well. This thesis study takes the next step and develops innovative gas-assisted foam injection molding (GAFIM) technology, which is the result of a synergistic combination of two existing manufacturing technologies, FIM and GAIM, in order to produce a unique thermoplastic foam structure with proficient acoustic properties. The foam structure manufactured by GAFIM consists of a solid skin layer, a foam layer, and a hollow core; and its 6.4-mm thick sample outperformed the conventional 22-mm thick polyurethane foam in terms of the acoustic absorption coefficient. With respect to ii foaming technology, GAFIM was able to achieve a highly uniform foam morphology by completely decoupling the filling and foaming phases.