Sintering and Devitrification of Glass-Powder Compacts in the Akermanite–Gehlenite System
Total Page:16
File Type:pdf, Size:1020Kb
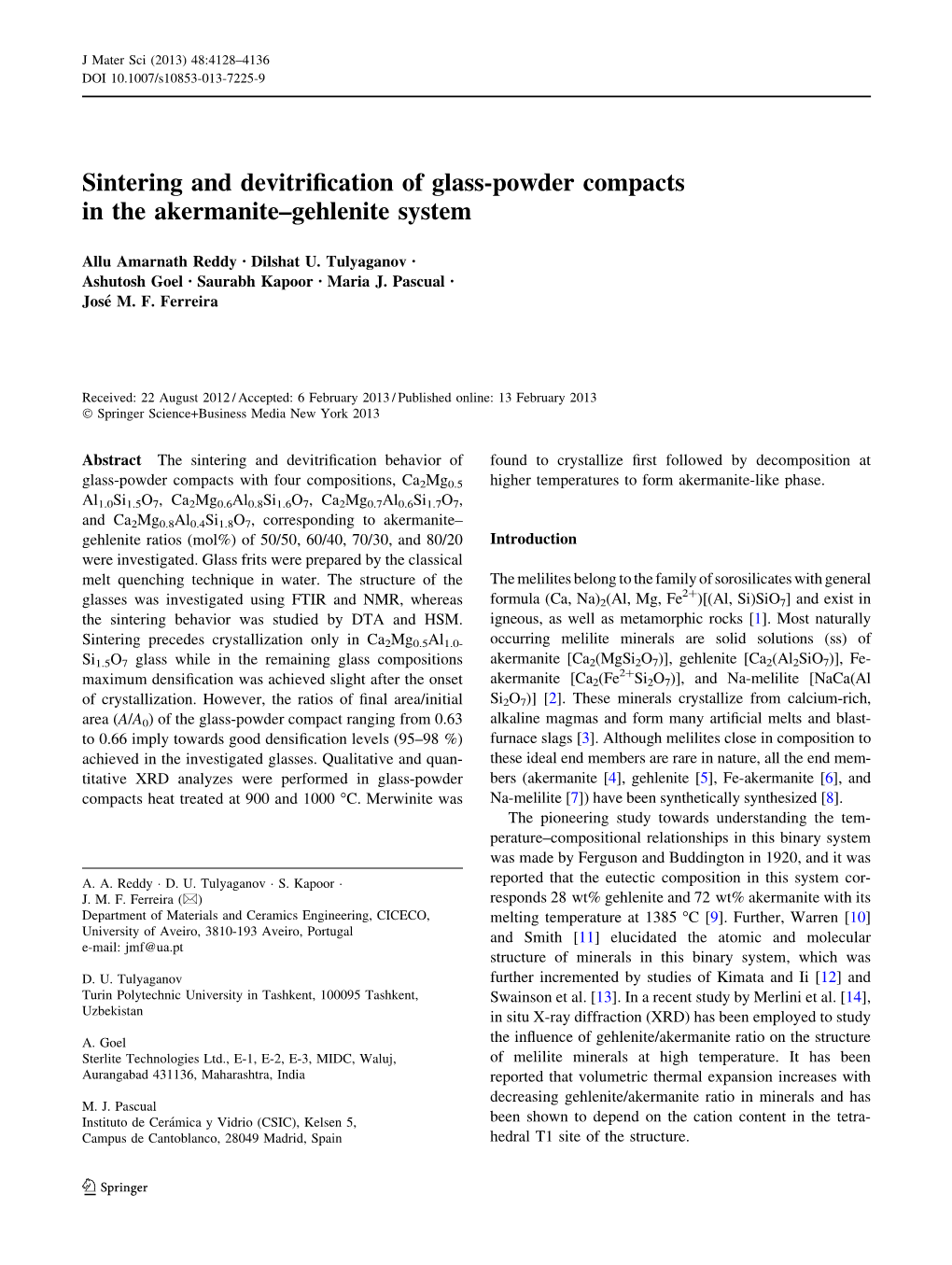
Load more
Recommended publications
-
Understanding the Formation of Caal2si2o8 in Melilite-Based Glass-Ceramics: Combined Diffraction and Spectroscopic Studies
This is an open access article published under an ACS AuthorChoice License, which permits copying and redistribution of the article or any adaptations for non-commercial purposes. Article http://pubs.acs.org/journal/acsodf Understanding the Formation of CaAl2Si2O8 in Melilite-Based Glass- Ceramics: Combined Diffraction and Spectroscopic Studies † ‡ † ‡ § ∥ ⊥ Amarnath R. Allu,*, , Sathravada Balaji, Dilshat U. Tulyaganov, , Glenn C. Mather, Fabian Margit, ∥ # ¶ # ∇ María J. Pascual, Reneé Siegel, Wolfgang Milius, Jürgen Senker, Dmitrii A. Agarkov, ∇ ‡ Vladislav V. Kharton, and JoséM. F. Ferreira*, † Glass Science and Technology Section, CSIRCentral Glass and Ceramic Research Institute, 700032 Kolkata, India ‡ Department of Materials and Ceramics Engineering, CICECO, University of Aveiro, 3810-193 Aveiro, Portugal § Turin Polytechnic University in Tashkent, 17, Small Ring, 100095 Tashkent, Uzbekistan ∥ Instituto de Ceramicá y Vidrio (CSIC), C/Kelsen 5, Campus de Cantoblanco, 28049 Madrid, Spain ⊥ Centre for Energy Research, Konkoly-Thege Street 29-33, 1121 Budapest, Hungary # ¶ Inorganic Chemistry III and Inorganic Chemistry I, University of Bayreuth, 95440 Bayreuth, Germany ∇ Institute of Solid State Physics RAS, 142432 Chernogolovka, Moscow District, Russia *S Supporting Information ABSTRACT: An assessment is undertaken for the formation of anorthite crystalline phase in a − − − melilite-based glass composition (CMAS: 38.7CaO 9.7MgO 12.9Al2O3 38.7SiO2 mol %), used as a sealing material in solid oxide fuel cells, in view of the detrimental effect of anorthite on the sealing properties. Several advanced characterization techniques are employed to assess the material after prolonged heat treatment, including neutron powder diffraction (ND), X-ray powder diffraction (XRD), 29Si and 27Al magic-angle spinning nuclear magnetic resonance (MAS-NMR), and in situ Raman spectroscopy. -
Progressive Metamorphism of Permian Siliceous Limestone and Dolomite
New Mexico Geological Society Downloaded from: http://nmgs.nmt.edu/publications/guidebooks/31 Progressive metamorphism of Permian siliceous limestone and dolomite - a complete sequence around a monzonite intrusion, Marble Canyon, Diablo Plateau, west Texas Thomas E. Bridge, 1980, pp. 225-229 in: Trans Pecos Region (West Texas), Dickerson, P. W.; Hoffer, J. M.; Callender, J. F.; [eds.], New Mexico Geological Society 31st Annual Fall Field Conference Guidebook, 308 p. This is one of many related papers that were included in the 1980 NMGS Fall Field Conference Guidebook. Annual NMGS Fall Field Conference Guidebooks Every fall since 1950, the New Mexico Geological Society (NMGS) has held an annual Fall Field Conference that explores some region of New Mexico (or surrounding states). Always well attended, these conferences provide a guidebook to participants. Besides detailed road logs, the guidebooks contain many well written, edited, and peer-reviewed geoscience papers. These books have set the national standard for geologic guidebooks and are an essential geologic reference for anyone working in or around New Mexico. Free Downloads NMGS has decided to make peer-reviewed papers from our Fall Field Conference guidebooks available for free download. Non-members will have access to guidebook papers two years after publication. Members have access to all papers. This is in keeping with our mission of promoting interest, research, and cooperation regarding geology in New Mexico. However, guidebook sales represent a significant proportion of our operating budget. Therefore, only research papers are available for download. Road logs, mini-papers, maps, stratigraphic charts, and other selected content are available only in the printed guidebooks. -
Oxygen and Hydrogen Diffusion in Minerals
Bowling Green State University ScholarWorks@BGSU Earth, Environment, and Society Faculty Publications School of Earth, Environment and Society 2010 Oxygen and Hydrogen Diffusion In Minerals John Richard Farver Bowling Green State University, [email protected] Follow this and additional works at: https://scholarworks.bgsu.edu/sees_pub Part of the Earth Sciences Commons Repository Citation Farver, John Richard, "Oxygen and Hydrogen Diffusion In Minerals" (2010). Earth, Environment, and Society Faculty Publications. 2. https://scholarworks.bgsu.edu/sees_pub/2 This Article is brought to you for free and open access by the School of Earth, Environment and Society at ScholarWorks@BGSU. It has been accepted for inclusion in Earth, Environment, and Society Faculty Publications by an authorized administrator of ScholarWorks@BGSU. Reviews in Mineralogy & Geochemistry Vol. 72 pp. 447-507, 2010 10 Copyright © Mineralogical Society of America Oxygen and Hydrogen Diffusion in Minerals John R. Farver Department of Geology Bowling Green State University Bowling Green, Ohio 43403, U.S.A. [email protected] INTRODUCTION This chapter provides a summary and review of experimentally determined oxygen and hydrogen volume diffusion in minerals. A very extensive and detailed review of stable isotope exchange processes including oxygen and hydrogen volume diffusion can be found in Cole and Chakraborty (2001) and a detailed review of hydrogen diffusion in minerals, especially nominally anhydrous minerals, can be found in Ingrin and Blanchard (2006). In addition, a detailed review of oxygen and hydrogen diffusion in silicate melts is provided by Zhang and Ni (2010), and oxygen and hydrogen diffusion rates can also be found in the chapters, in this volume, on specific minerals and mineral groups (e.g., Van Orman and Crispin 2010; Cherniak 2010). -
The Crystal Structure of Synthetic Soda Melilite, Canaaisi207 1. Introduction
Zeitschrift fUr Kristallographie, Bd. 131, S. 314--321 (1970) The crystal structure of synthetic soda melilite, CaNaAISi207 By S. JOHN LOUISNATHAN Department of the Geophysical Sciences, The University of Chicago, Chicago (Received 25 August 1969) Auszug Die Kristallstruktur von synthetischem N atriummelilith wurde aus Dif- fraktometerdaten bis R = 5,10/0 verfeinert. Die Verbindung hat die gleiche Struktur wie die iibrigen, natiirlich vorkommenden Melilithe. Die Aluminium- und Siliciumatome sind in der Struktur geordnet, die Calcium- und Natrium- atome statistisch verteilt. Abstract The crystal structure of synthetic soda melilite was refined to R = 5.10/0 from three-dimensional diffractometer data. Soda melilite is isostructural with the other naturally-occuring melilites. Aluminum and Si atoms are ordered in the structure while Ca and N a atoms are disordered. 1. Introduction The literature on the melilite group of minerals with a discussion of the various proposed end-members was reviewed by CHRISTIE (1961 a and b; 1962). After prolonged discussion it is now generally accepted that CaNaAlSi207, called soda melilite, can be established as an end member, partly represented in some natural melilites. YODER (1964) showed that pure soda melilite is stable only at pressures in excess of 4 kbar. Its optical properties were determined by SCHAIRER, YODER and TILLEY (1965). The crystal-structure determination of soda melilite was under- taken as a part of a systematic structural study of the melilite group. The general composition of a melilite can be written as (Ca,Na)2 (Mg,Al)(Al,Si)207. Order-disorder of Mg,Al and Si among the tetra- hedral sites and diadochy of Ca, N a etc. -
Akermanite in the Cascade Slide Xenolith and Its Signi¯Cance for Regional Metamorphism in the Adirondacks
Aºkermanite Ca2MgSi2O7 c 2001 Mineral Data Publishing, version 1.2 ° Crystal Data: Tetragonal. Point Group: 42m: Crystals short prismatic to thin tabular, which may resemble squashed, octahedrally-modi¯ed cubes; granular, massive. Twinning: On 100 and 001 , cruciform. f g f g Physical Properties: Cleavage: Distinct on 001 , poor on 110 . Fracture: Uneven to conchoidal. Tenacity: Brittle. Hardness = 5{6 f D(mg eas.) = 2.f944 gD(calc.) = 2.922 Optical Properties: Transparent to translucent. Color: Colorless, yellowish gray, green, brown; in thin section, colorless to yellow. Luster: Vitreous to resinous. Optical Class: Uniaxial (+). Absorption: Weak; E > O. ! = 1.630{1.632 ² = 1.639{1.648 Cell Data: Space Group: P 421m (synthetic). a = 7.8288(8) c = 5.0052(5) Z = 2 X-ray Powder Pattern: Synthetic. 2.87 (100), 3.09 (30), 1.764 (30), 2.039 (20), 2.488 (18), 3.73 (14), 5.55 (12) Chemistry: (1) (2) (3) SiO2 46.55 44.07 44.08 TiO2 0.05 Al2O3 0.96 0.33 Fe2O3 0.00 FeO 0.12 0.47 MnO 0.00 0.11 ZnO 1.56 MgO 13.30 12.87 14.78 CaO 39.30 40.09 41.14 Na2O < 0.05 Total 100.23 [99.55] 100.00 (1) Vesuvius, Italy. (2) Cascade Mountain, New York, USA; by electron microprobe; original total given as 99.52%. (3) Ca2MgSi2O7: Polymorphism & Series: Forms a series with gehlenite. Mineral Group: Melilite group. Occurrence: A product of contact metamorphism of siliceous limestones and dolostones, and in rocks of the sanidinite facies. Also forms from alkalic magmas rich in calcium. -
This Article Appeared in a Journal Published by Elsevier. the Attached Copy Is Furnished to the Author for Internal Non-Commerci
This article appeared in a journal published by Elsevier. The attached copy is furnished to the author for internal non-commercial research and education use, including for instruction at the authors institution and sharing with colleagues. Other uses, including reproduction and distribution, or selling or licensing copies, or posting to personal, institutional or third party websites are prohibited. In most cases authors are permitted to post their version of the article (e.g. in Word or Tex form) to their personal website or institutional repository. Authors requiring further information regarding Elsevier’s archiving and manuscript policies are encouraged to visit: http://www.elsevier.com/copyright Author's personal copy Applied Clay Science 42 (2009) 345–355 Contents lists available at ScienceDirect Applied Clay Science journal homepage: www.elsevier.com/locate/clay Mineralogical transformations of calcareous rich clays with firing: A comparative study between calcite and dolomite rich clays from Algarve, Portugal M.J. Trindade a ⁎, M.I. Dias a, J. Coroado b, F. Rocha c a Instituto Tecnológico e Nuclear, EN 10, 2686-953 Sacavém, Portugal b Instituto Politécnico de Tomar, Dep. Arte, Conservação e Restauro, 2300—313 Tomar, Portugal c MIA, Dep. de Geociências. Univ. de Aveiro, Campus de Santiago, 3810-193 Aveiro, Portugal article info abstract Article history: Mineralogical transformations during firing of two extremely calcareous clays, one calcite and other dolomite Received 1 August 2007 rich, and relatively poor in silica were studied. Original clays were mineralogical and chemically characterized Received in revised form 17 February 2008 with X-ray diffraction (XRD) and X-ray fluorescence (XRF). -
ON SUB-SOLIDUS RELATIONS of SILICATES I 257 Co 700 Melilite O
NORSK GEOLOGISK TIDSSKRIFT ON SUB-S OLIDUS RELATIONS OF SILICATES I. The Lower Breakdown Temperature of the Akermanite Gehlenite Mixed Crystal Series at Moderate Water Pressure By OLAV H. J. CHRISTIE (Mineralogisk-Geologisk Museum, Oslo NO) Abs t ra c t. Some sub solidus relations in systems of åkermanite gehlenite compositions in the range 200° C - 700° C have been studied. Åkermanite was reported to decompose to wollastonite and monticellite at approximately 700° C (HARKER and TuTTLE, 1956). At 6 kbar water pressure and 500° C, wollastonite and clinopyroxene form from åkermanite. At the same pressure and ca. 450 °C. clinopyroxene and xonotlite seem to be the stable mineral association. The decomposition temperature of the åkermanite-gehlenite mixed crystal series at 4.8 bar to 6.7 kbar depends upon the composition of the mixed crystal and is situated between 500° C and 650° C. The decomposition products are vesuv ianite and hydrogarnet, hydrogarnet, or hydrogarnet and xonotlite in addition to clinopyroxene and wollastonite formed from the åkermanite-rich batches. The hydrogarnets formed during the experiments are mixed crystals in the series hydrogrossular - hydropyrope. Previous work Åkermanite (Ca2MgSi207) and gehlenite (Ca2AlSiAl07) are the two most important end members of the melilite group. Akermanite was described by J. H. L. VoGT (1884), who found it as an artificial mineral in slags. ZAMBONINI (1910) described natural åkermanite from Vesuvius, and FERGUSON and BuDDINGTON (1919) determined the chemical composition of it. 256 OLA V H. J. CHRISTIE Gehlenite was described by FuCHs (1815). It was subject to doser study by RANKIN and WRIGHT (1915). -
Mineralogic Notes Series 3
DEPARTMENT OF THE INTERIOR FRANKLIN K. LANE, Secretary UNITED STATES GEOLOGICAL SURVEY . GEORGE OTIS SMITH, Director Bulletin 610 MINERALOGIC NOTES SERIES 3 BY WALDEMAR T. SCHALLER WASHINGTON GOVERNMENT PRINTING OFFICE 1916 CONTENTS. Page. Introduction................................................................ 9 Koechlinite (bismuth molybdate), a new mineral............................ 10 Origin of investigation................................................... 10 Nomenclature......................................................... 10 Locality............................................................... 11 Paragenesis........................................................... 11 Crystallography........'............................................... 14 General character of crystals....................................... 14 Calculation of elements............................................. 14 Forms and angles................................................. 15 Combinations..................................................... 19 < Zonal relations and markings...................................... 19 Habits........................................................... 21 Twinning........................................................ 23 Measured crystals................................................. 26 Etch figures...................................................... 27o Intergrowths........................................................ 31 Relation to other minerals.......................................... 31 Physical properties................................................... -
Metamorphic Conditions of Adirondack Rocks Robert S
4: EPISODES IN GEOLOGICAL INVESTIGATIONS OF THE ADIRONDACKS 5 METAMORPHIC CONDITIONS OF ADIRONDACK ROCKS ROBERT S. DARLING1 AND WILLIAM H. PECK2 1. Department of Geology, SUNY Cortland, Cortland, NY 13045, 607.753.2923, [email protected] 2. Department of Geology, Colgate University, Hamilton, NY 13346, 315.228.6798, [email protected] KEYWORDS: Adirondacks, Metamorphism, Pressure-Temperature-Path, Fluid Composition, New York ABSTRACT The Adirondack Highlands were metamorphosed to granulite facies conditions during the Ottawan phase (1090 to 1020 Ma) of the Grenville Orogenic Cycle, whereas the Adirondack Lowlands were metamorphosed to mid to upper amphibolite facies conditions during the Shawinigan phase (1190 to 1140) of the Grenville Orogenic Cycle. Metamorphic temperatures ranged from 750 °C to 850 °C in the Highlands and 650 °C to 750 °C in the Lowlands. Metamorphic pressures were between 6.0 and 8.6 kilobars in the Highlands and 6.5 to 7.5 kilobars in the Lowlands. Following the peak of metamorphism, Adirondack rocks took a counter-clockwise path in pressure-temperature space. The activity of water is generally low in Adirondack metamorphic rocks, and many rocks did not contain a free fluid phase during metamorphism. INTRODUCTION Ever since Emmons (1842) first reported geological descriptions of the Adirondack region, scores of geologists have travelled to northern New York to study the Mesoproterozoic basement rocks the make up the Adirondack Mountains. Early studies tended to focus on mining and economic resources of the region, but a number of researchers attempted 60 THE ADIRONDACK JOURNAL OF ENVIRONMENTAL STUDIES VOLUME 21 61 5: METAMORPHIC CONDITIONS OF ADIRONDACK ROCKS to better understand the rocks types and their interrelationships (see Peck, this issue). -
Download Article (PDF)
Crystal Structures of New Pyrovanadates A2MnV2O7 (A =Rb,K) Hamdi Ben Yahia, Etienne Gaudin, and Jacques Darriet Institut de Chimie de la Mati`ere Condens´ee de Bordeaux-CNRS, Universit´e Bordeaux 1, 87 avenue du docteur A. Schweitzer, 33608 Pessac Cedex, France Reprint requests to Dr. E. Gaudin. Fax: (+33)540002761. E-mail: [email protected] Z. Naturforsch. 2007, 62b, 873 – 880; received March 3, 2007 Dedicated to Dr. Bernard Chevalier on the occasion of his 60th birthday The new compounds A2MnV2O7 (A = K, Rb) with structures related to the melilite-type have been synthesized by a solid state reaction route. The crystal structures of K2MnV2O7,Rb2MnV2O7 and KRbMnV2O7 have been determined using X-ray single crystal diffraction data. The com- pound K2MnV2O7 crystallizes with a melilite-type structure with tetragonal unit cell parameters a = 8.609(3), c = 5.538(4) A˚ and space group P42¯ 1m. The structures of Rb2MnV2O7 and KRbMnV2O7 are derived from the melilite-type structure with space group P42/mnm and unit cell parameters a = 8.577(6), c = 11.809(6) A,˚ and a = 8.530(6), c = 11.466(5) A,˚ respectively. The three structures consist 2− + 2− of [MnV2O7] layers perpendicular to the c axis separated by A layers. The [MnV2O7] layers feature corner-sharing MnO4 tetrahedra and V2O7 pyrovanadate units, the linkage leading to rings of five tetrahedra. The doubling of the c parameter for Rb2MnV2O7 or RbKMnV2O7 is explained by the existence of a mirror plane perpendicular to the [001] direction between two [MnV O ]2− + 2 7 layers. -
Packing in Ionic Minerals
BULLETIN OF THE GEOLOGICAL SOCIETY OF AMERICA VOL. 54, PP. 1305-1374, 28 FIGS. SEPTEMBER I, 1943 PACKING IN IONIC MINERALS BY H . W. FAIRBAIKN CONTENTS Page Abstract.................................................................................................................................... 1306 Introduction............................................................................................................................ 1307 Acknowledgments.................................................................................................................. 1308 Concept of packing index.................................................................................................... 1308 Development of methods of volume determination.............................................. 1308 The packing index......................................................................................................... 1310 Sources of error.............................................................................................................. 1311 Selection of ion radii..................................................................................................... 1311 Degree of accuracy of packing index........... ............................................................ 1315 Correlation of crystal packing with packing of uniform spheres..................... 1316 Mineralogic correlations of packing index........................................................................ 1320 Correlation of refractive index and density -
The Microscopic Determination of the Nonopaque Minerals
DEPARTMENT OF THE INTERIOR ALBERT B. FALL, Secretary UNITED STATES GEOLOGICAL SURVEY GEORGE OTIS SMITH, Director Bulletin 679 THE MICROSCOPIC DETERMINATION OF THE NONOPAQUE MINERALS BY ESPER S. LARSEN WASHINGTON GOVERNMENT PRINTING OFFICE 1921 CONTENTS. CHAPTER I. Introduction.................................................. 5 The immersion method of identifying minerals........................... 5 New data............................................................. 5 Need of further data.................................................... 6 Advantages of the immersion method.................................... 6 Other suggested uses for the method.................................... 7 Work and acknowledgments............................................. 7 CHAPTER II. Methods of determining the optical constants of minerals ....... 9 The chief optical constants and their interrelations....................... 9 Measurement of indices of refraction.................................... 12 The embedding method............................................ 12 The method of oblique illumination............................. 13 The method of central illumination.............................. 14 Immersion media.................................................. 14 General features............................................... 14 Piperine and iodides............................................ 16 Sulphur-selenium melts....................................... 38 Selenium and arsenic selenide melts........................... 20 Methods of standardizing