Print This Article
Total Page:16
File Type:pdf, Size:1020Kb
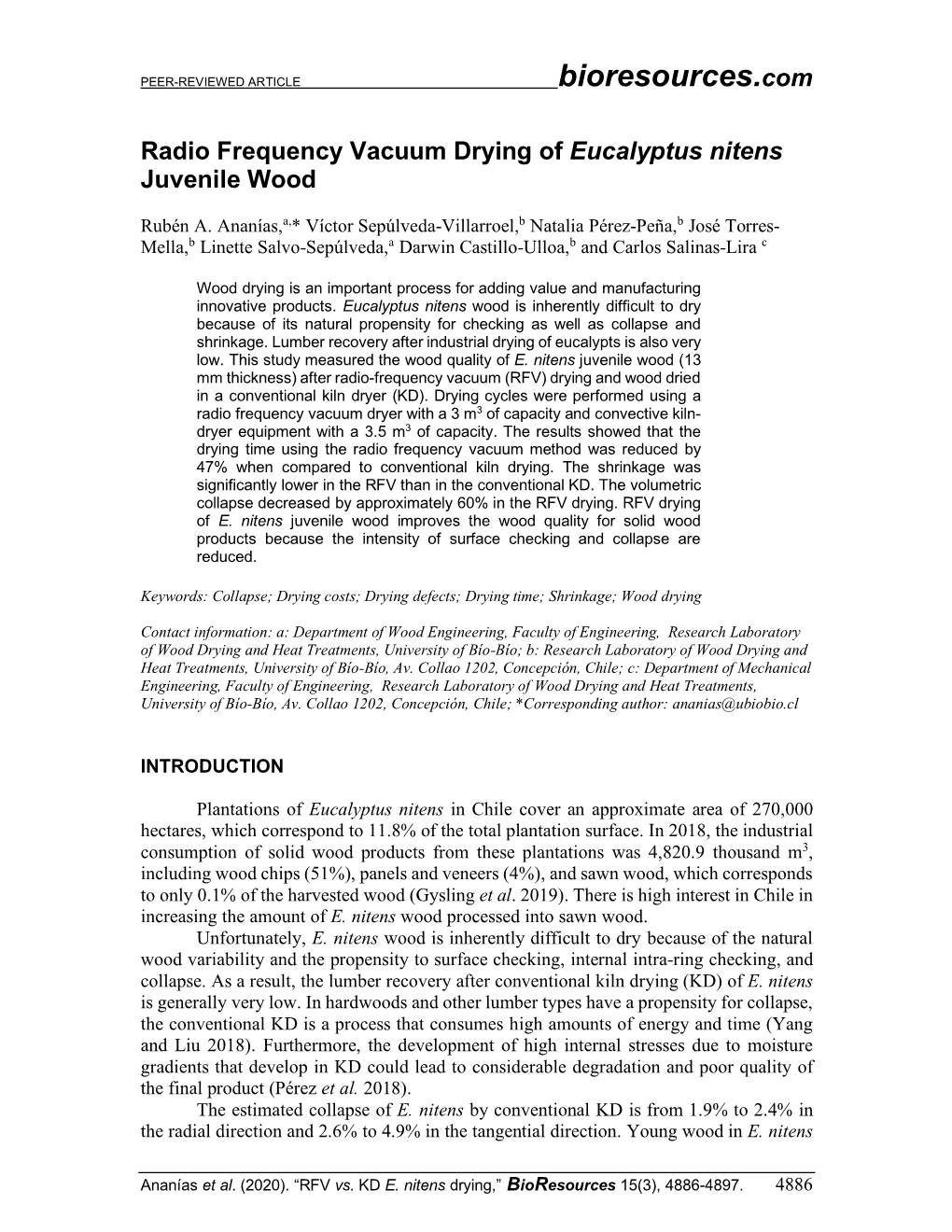
Load more
Recommended publications
-
The Moisture-Excluding Effectiveness of Finishes on Wood Surfaces
United States Department of Agriculture The Moisture- Forest Service Forest Excluding Products Laboratory Research Paper Effectiveness FPL 462 of Finishes on Wood Surfaces William C. Feist James K. Little Jill M. Wennesheimer Abstract Permeability to water vapor is one of the more important properties affecting the performance of coatings and other wood finishes. Often, one of the main purposes of finishing wood is to restrict moisture movement from the surroundings. We evaluated the moisture-excluding effectiveness (MEE) of 91 finishes on ponderosa pine sapwood, using the Forest Products Laboratory method in which finished and unfinished wood specimens in equilibrium with 30 percent relative humidity (RH) at 80 °F are weighed before and after exposure to 90 percent RH at 80 °F. Finishes with the best MEE were pigmented, nonaqueous (solvent-borne) finishes. Two-component epoxy paint systems had MEE values greater than 85 percent after 14 days when three coats were put on the wood. Molten paraffin wax and a sheathing grade, two-component epoxy material with no solvent were the very best finishes found in this study for controlling moisture vapor movement into wood. The MEE is a direct function of the number of coats of finish applied to the wood (film thickness) and the length of time of exposure to a particular humidity. Only 11 finishes were found to retard moisture vapor movement into wood with any degree of success over the relatively short time of 14 days, and then only when two or three coats were applied. These studies include evaluations of MEE by finish type, number of coats, substrate type, sample size, and time of exposure, and describe the effect on MEE of repeated adsorption/desorption cycles. -
Understanding Wood Bonds–Going Beyond What Meets the Eye: a Critical Review
Understanding Wood Bonds–Going Beyond What Meets the Eye: A Critical Review Christopher G. Hunt1*, Charles R. Frihart1, Manfred Dunky2 and Anti Rohumaa3 1Forest Products Laboratory, Madison, Wisconsin, USA 2Kronospan GmbH Lampertswalde, Lampertswalde, Germany 3FibreLaboratory, South-Eastern Finland University of Applied Sciences (XAMK), Savonlinna, Finland Abstract: Understanding why wood bonds fail is an excellent route toward understanding how to make them better. Certifying a bonded product usually requires achieving a specifc load, percent wood failure, and an ability to withstand some form of moisture exposure without excessive delamination. While these tests protect the public from catastrophic failures, they are not very helpful in understanding why bonds fail. Understanding failure often requires going beyond what meets the naked eye, conducting additional tests, probing the wood surface, the fracture surface, adhesive properties, and the interaction of wood and adhesive during bond formation and service. This review of wood bond analysis methods reviews fundamentals of wood bonding and highlights recent developments in the analyses and understanding of wood bonds. It concludes with a series of challenges facing the wood bonding community. Keywords: Wood adhesive, wood bond, microscopy, penetration, failure List of Abbreviations AFM Atomic Force Microscopy AP Average Penetration CLSM Confocal Laser Scanning Microscopy CV Collapsed Vessel CWBL Chemical Weak Boundary Layer DCB Dual Cantilever Beam DIC Digital Image Correlation DMA -
System Three Clear Finishing of Outdoor Wood
apply a second coat. See Product Application Guide for complete Sanding: Allow the unassembled wood parts to cure for instructions. several days before sanding. Wipe each piece with a damp The epoxy coating is as thick as ten coats of dry varnish or sponge prior to sanding. Begin sanding with 80 or 100 polyurethane, so only two or three coats of clear varnish or LPU grit paper. Finish with 150 or 220 paper. Wet sanding will usually be required to build a deep, rich fi nish. on thoroughly coated pieces is acceptable as the wood is now waterproof. Maintenance: If the fi nish becomes dull or begins to fl ake after PREMIUM ADHESIVES & COAT INGS several years of exposure it can easily be sanded to remove any Assembly: After sanding, put the parts together once loose or chalky material, and recoated. Reapplying varnish or more without glue to make sure that the joints still LPU before it weathers off will allow you to avoid reapplying the fi t. Sand to a fi t if necessary. Use System Three T- epoxy coating. 88® structural epoxy adhesive to glue the parts. It is waterproof and will not shrink on curing. Apply mixed With the System Three resin and varnish combination protecting adhesive to both bonding surfaces, with an excess on your clear-fi nished project from the elements, it will remain bright and beautiful for years to come. CLEAR the concave or female surface. Press the pieces together and wipe up any excess glue. Keep glued parts in place during cure. Avoid excess clamping pressure. -
Western Timber Frame™ SCAPE
Made by: Western Timber Frame™ SCAPE TM ® The Ultimate Pergola & Pavilion Guide Everything you wanted to know about: Pergolas • Pavilions • Arbors • Trellises & More Coauthored by: Steven Bunker & Marilynn Thompson SCAPE TM ® Table of Contents Coauthored by: Steven Bunker and Marilynn Thompson Ultimate Pergola and Pavilion Guide Table of Contents ------------------------------ 6 What is a Pergola? ----------------------------- 8 What are Pavilions and Gazebos? ------------ 9 What is an Arbor or Trellis? ------------------ 10 Other Structures ----------------------------- 11 The Dovetail Difference™ -------------------- 12 Benefits of the Dovetail Difference™ --------- 14 Conventional Timber Framing --------------- 15 What makes us different -------------------- 16 Features and Benefits ----------------------- 17 Heavy Timber Kits ---------------------------- 18 Douglas Fir -------------------------------- 19 Douglas Fir Cont... Free Of Heart --------- 20 Vinyl --------------------------------------- 21 Aluminum ---------------------------------- 21 Customized Design --------------------------- 22 Choose your Style ---------------------------- 23 Tuscany Style -------------------------------- 26 Southwest Style ------------------------------ 26 ShadeScape™ series -------------------------- 27 Attached Kits - Extend your Home ---------- 38 Standard Options ----------------------------- 39 Color Selection ------------------------------- 49 Concept to Creation -------------------------- 76 Meet your Design Manager ------------------ 77 3D -
Investigating the Mechanisms of the Formation of Spiral Grain and Interlocked Grain in Wood
Investigating the mechanisms of the formation of spiral grain and interlocked grain in wood A thesis submitted in partial fulfilment of the requirements for the Degree of Master of Science in Plant Biotechnology in the University of Canterbury by Stephanie M. Dijkstra University of Canterbury 2020 Chapter 1 Acknowledgements Firstly, I would like to thank my supervisory team. To my original senior supervisor Dr David Collings – thank you for your crazy ideas that made this thesis possible. To Dr Ashley Garrill, thank you for your tireless support during this journey. To Dr Clemens Altaner, thank you for Secondly, I would like to acknowledge the Ngāi Tahu Research Centre, both for the two scholarships that I received from them and for the whanaungatanga and mātauranga that being part of their scholars brought. I would like to acknowledge the technical staff from the school of biological sciences, the school of forestry and the school of geology for their support. Thank you for going along with the many left-field ideas that I often arrived with, and the generosity that each of you had with your time and knowledge. Thanks to the most amazing lab group (both past and present) that I could have asked for. Not only have you been fantastic co-workers, but I feel privileged to count you among my close friends (Cell bio Jedi for life!). Special thanks to Liz, Louise, Azy and Annabella for coffee, tea, chocolate and laughter when it was most needed Thanks to my family for always believing in me and providing support in all its forms. -
Mathematical Modelling and Life-Cycle Energy and Financial Analysis Of
Mathematical modelling and life‐cycle energy and financial analysis of solar kilns for wood drying A thesis submitted in fulfilment of the requirements for the degree of Doctor of Philosophy By Mahmudul Hasan B.Sc. (Mechanical Engineering) School of Chemical and Biomolecular Engineering Faculty of Engineering and Information Technologies The University of Sydney, Australia June 2017 Declaration I, Mahmudul Hasan, declare that the entire contents of this thesis are, to the best of my knowledge and belief, original, except where otherwise acknowledged. This thesis contains no material that has been submitted previously, in whole or in part, for the award of any other academic degree or diploma. …………………………. Mahmudul Hasan June 2017 i Dedications Dedicated To My parents and wife who are my inspirations. ii Acknowledgment I would like to express my heartiest gratefulness and indebtedness to my principal supervisor, Professor Timothy Langrish, for his scholastic supervision, inestimable help, proper guidance/suggestions throughout my study and research at The University of Sydney. His constant encouragement, time‐to‐time feedback, and immense knowledge in the research context were the key motivation and inspiration throughout my study. I have been especially fortunate to work with such a great supervisor. I also express my sincere gratitude to my co‐supervisor, A/Prof. Ali Abbas, for his insightful suggestions and valuable advice. As an auxiliary supervisor, he was strong and supportive. I would also like to express my special thanks to Dr. Nawshad Haque (CSIRO, Australia) for his insightful advice and intellectual support. I gratefully acknowledge the financial support from The University of Sydney for this research. -
A Classic Case a Project Plan for a Case with a Modern Take on an Arts and Crafts Classic
WTAUNTON’S A Classic Case A project plan for case with a modern a take on an Arts and Crafts classic For more FREE project plans from Build an Oak Bookcase Fine Woodworking Simple, SturdyFrom Getting Workbench Started in Woodworking, Season 2 Simple,From Sturdy Getting Started Workbench in Woodworking, Season 2 ou can thank Mike Pekovich, B y A s Fine Woodworking’s art direc A C h r i s t i Ytor, for designing this simple but From Getting Startedstylish bookcase. in Woodworking, He took a straightfor Season 2 A ward form--an oak bookcase with dado n A B y A s A C h r i s t i - and rabbet joints--and added nice pro- A n A B yportions A s A and C elegant h r icurves. s t i A n A - We agreed that screws would reinforce his workbench is easy and the joints nicely, and that gave us a de- inexpensive to build, yet is sturdy and sign option on the sides. Choose oak T Lu Mber, har versatileplugs, and align the grain carefully, andDware an D supp enough for any woodworker. 4 Lies Lis T his workbench is easy and inexpensiveThe basethe plugs isLu disappear.Mber, har MakeDware 8-ft.-longthem from an 2x4s, Da supp kiln-driedLies LisT construction lumber (4x contrasting wood, like walnut,2 and the Tto build, yet is sturdy and versatile4s and 2x4s), joined4 8-ft.-long 2x4s,8-ft.-long kiln-dried 4x4s, kiln-dried rows of plugs add a nice design feature simply with long bolts and s 1 4x8 sheet of MDF enough for any woodworker. -
How to Cite Complete Issue More Information About This
Logos (La Serena) ISSN: 0717-3644 ISSN: 0718-221X Universidad de La Serena/Facultad de Humanidades. Departamento de Artes y Letras. Korkut, Süleyman; As, Nusreta; Büyüksarı, Ümit Comparison of two kiln-drying schedules for turkish hazel ( Corylus colurna ) lumber of 5-cm thickness Logos (La Serena), vol. 20, no. 1, 2018, pp. 129-138 Universidad de La Serena/Facultad de Humanidades. Departamento de Artes y Letras. Available in: http://www.redalyc.org/articulo.oa?id=48557573012 How to cite Complete issue Scientific Information System Redalyc More information about this article Network of Scientific Journals from Latin America and the Caribbean, Spain and Journal's webpage in redalyc.org Portugal Project academic non-profit, developed under the open access initiative ISSN impresa 0717-3644 Maderas. Ciencia y tecnología 20(1): 129 - 138, 2018 ISSN online 0718-221X DOI: 10.4067/S0718-221X2018005011101 COMPARISON OF TWO KILN-DRYING SCHEDULES FOR TURKISH HAZEL (Corylus colurna) LUMBER OF 5-CM THICKNESS Süleyman Korkut1,♠, Nusret As2, Ümit Büyüksarı1 ABSTRACT Turkish hazel (Corylus colurna) lumber with a nominal thickness of 5 cm from the Kastamonu region, Turkey, was dried through conventional kiln drying using two different programs, a non- protective drying schedule and a protective drying schedule. The goal of the study was to obtain a kiln schedule that would maintain wood quality and also save drying time until a final moisture content of 8 ± 2% was reached. The intensity of warping (twisting, bowing, cupping, crooking), superficial, internal, and end checks, residual stresses, drying rate, and moisture gradient of the dried woods were measured, and the results were evaluated according to the classification of the European Drying Group. -
Eastern Red Cedar Is Easy to Air-Dry. but If Too Dry, It's Hard to Work With
Eastern Red Cedar — How Dry? Eastern Red Cedar is easy to air-dry. But if too dry, it's hard to work with. May 27, 2014 Whether to Use Reclaimed Pickle-Vat Lumber for Stickers An interesting discussion on the properties of old-growth lumber that has been used in a vat for brining pickles. June 13, 2014 Managing Airflow in the Pre-Dryer Advice on using temporary baffles to keep air flowing through the remaining stacks as some wood is removed. June 13, 2014 Automatic Water-Fill Dry-Wet Bulb RH Metering Advice on the fine points of keeping a relative humidity monitoring setup supplied with water for the wet bulb. June 13, 2014 Test for Honeycomb A method for testing dried lumber to detect honeycomb, with advice on how to prevent the checking that leads to honeycomb. June 13, 2014 Mold on Green Lumber Quick drying should contain most mold problems encountered on freshly-sawn green lumber arriving at the kiln. June 13, 2014 Sticker Stain in Hickory Sticker stain is a warm-weather phenomenon. Here's advice about a suitable schedule for drying Hickory. May 27, 2014 Drying 6" X 8" Pine Beams Estimates of the required drying time for large pine timbers. May 27, 2014 Moisture Meters and Frozen Wood The science of using a moisture meter on freezing-cold wood. May 27, 2014 Troubleshooting Mold on Oak in the Drying Kiln A question about a mold problem leads to a discussion about process control and kiln conditions. June 13, 2014 Weighing Down Stacked Lumber Weighing down the lumber stack with concrete can help the wood dry flatter. -
Conservation of Waterlogged Wood—Past, Present and Future Perspectives
Review Conservation of Waterlogged Wood—Past, Present and Future Perspectives Magdalena Broda 1,2,* and Callum A. S. Hill 3,4 1 Department of Wood Science and Thermal Techniques, Faculty of Forestry and Wood Technology, Pozna´nUniversity of Life Sciences, Wojska Polskiego 38/42, 60-637 Pozna´n,Poland 2 The BioComposites Centre, Bangor University, Deiniol Road, Bangor LL57 2UW, UK 3 JCH Industrial Ecology Ltd., Bangor LL57 1LJ, UK; [email protected] 4 Norwegian Institute of Bioeconomy Research (NIBIO), P.O. Box 115, Postboks 115, NO-1431 Ås, Norway * Correspondence: [email protected] Abstract: This paper reviews the degradation, preservation and conservation of waterlogged ar- chaeological wood. Degradation due to bacteria in anoxic and soft-rot fungi and bacteria in oxic waterlogged conditions is discussed with consideration of the effect on the chemical composition of wood, as well as the deposition of sulphur and iron within the structure. The effects on physical properties are also considered. The paper then discusses the role of consolidants in preserving water- logged archaeological wood after it is excavated as well as issues to be considered when reburial is used as a means of preservation. The use of alum and polyethylene glycol (PEG) as consolidants is presented along with various case studies with particular emphasis on marine artefacts. The properties of consolidated wood are examined, especially with respect to the degradation of the wood post-conservation. Different consolidants are reviewed along with their use and properties. The merits and risks of reburial and in situ preservation are considered as an alternative to conservation. -
University of Cincinnati
UNIVERSITY OF CINCINNATI DATE: May 16th, 2003 I, Joshua Craig Summers , hereby submit this as part of the requirements for the degree of: Master in: Architecture It is entitled: Materials and Craft in Architecture Approved by: David Niland Barry Stedman MATERIALS AND CRAFT IN ARCHITECTURE – A WORKSHOP FOR THE STUDY OF CRAFT A thesis submitted to the Division of Research and Advanced Studies of the University of Cincinnati in partial fulfillment of the requirements for the degree of MASTER OF ARCHITECTURE in the Department of Architecture of the College of Design, Architecture, Art and Planning 2003 by Joshua Summers B.S. Arch., University of Cincinnati, 2001 Committee Chair: David Niland Barry Stedman, PhD A BSTRACT With a loss of understanding for the use of materials and craft in the majority of buildings today, the public has not been exposed to works that are inspiring. A workshop devoted to the study of craftsmanship will help individuals better understand materials and connections. The architecture of the workshop will serve as both a teaching tool and will be an object of craft unto itself. A workshop devoted to the study of craftsmanship will help to teach individuals about materials and craft by establishing a program that will allow individuals hands-on experience in woodworking and furniture design. The workshop will be located at the intersection of Sycamore and East Liberty Streets just north of downtown Cincinnati. The workshop will be designed to be a foreground building that will serve as a gateway into the Over-the-Rhine neighborhood. M ATERIALS AND C RAFT IN A RCHITECTURE – A Workshop for the Study of Craft T ABLE OF C ONTENTS 1 I NTRODUCTION 1.1 List of Illustrations/Diagrams 2-4 1.2 Introduction 5-9 T HESIS 2.1 Craft in Architecture 10-24 2.2 Precedents 2.21 Gamble House – Greene and Greene 25-29 2.22 Tjibaou Cultural Centre – Renzo Piano 30-33 P ROJECT / L OCATION 3.1 History of Project Type / Project Precedent 34-36 3.2 Site Analysis / Features 37-39 P ROGRAM 4.1 Spaces / Overall Square Footage 40 4.2 Individual Space Description and Sq. -
Moisture Content & Humidity
Electrophysics MOISTURE METER MODEL CT858 Electrophysics Box 310, Dutton, Ontario N0L 1J0, Canada Phone or Fax: (519) 768-2146 www.electrophysics.on.ca OPERATING INSTRUCTIONS & INFORMATION NOTES ZERO AND CALIBRATION INSTRUCTIONS: MODEL CT858 FIRST: CHECK THE ZERO POINT AND RE-ADJUST IF NECESSARY AS FOLLOWS: Turn the meter off then on again after a few seconds, to reset. Now set the density to “00” (the main instructions tell you how to push the “menu” and “scroll” buttons to do this) and leave the meter turned on until zero and calibration are done. On the body of the sensor probe casing there are two small white plastic screws. Remove the screw giving access to the zero adjustment (see photograph below). A small brass screw will be visible through the exposed hole. Hold the sensor probe in mid-air with the sensor pad well away from any material objects, and with a small flat-bladed screwdriver slowly turn the brass screw until the meter reads “00”. Re-insert the white plastic screw now, to avoid later confusion. CALIBRATION ADJUSTMENT There are two plates. Place the copper-coated plate on a table top or other convenient flat non-metallic surface, with the copper side facing down. Place the clear plastic plate on top of the copper plate. Set the density to 0.50 and place the sensing pad directly on the top plate and press gently. The meter should read 14%. If it does not, proceed as follows. Remove the white plastic screw in the sensor pad casing, which gives access to the calibration adjustment (see photograph below).