The Trolley Coach Development and State Of
Total Page:16
File Type:pdf, Size:1020Kb
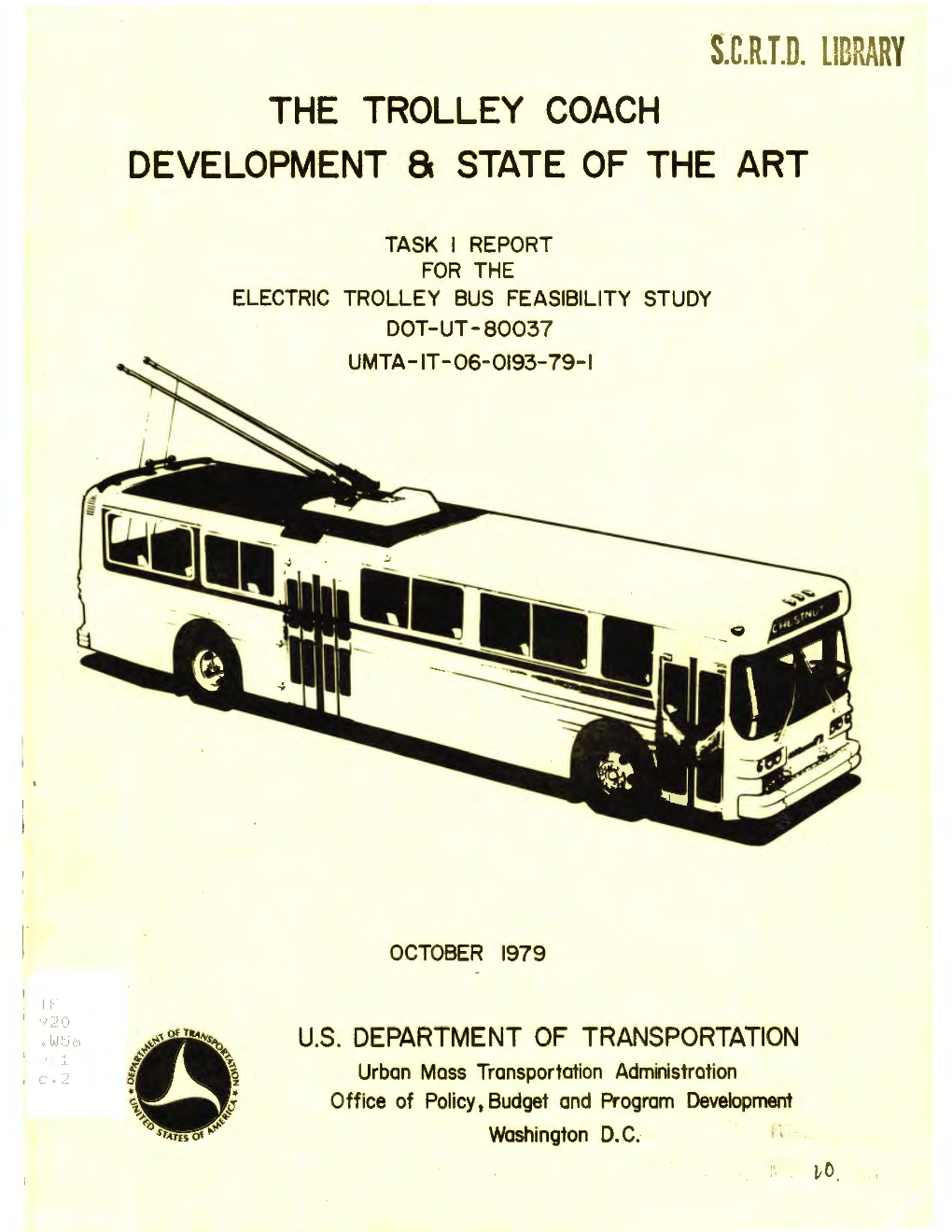
Load more
Recommended publications
-
Minibus Or Coach Module 4 Driver CPC Questions and Answers
Minibus or coach Module 4 Driver CPC questions and answers The Initial Driver CPC qualification was introduced into the bus and coach industry on September 10th 2008. Exactly one year before Driver CPC came into force for the commercial goods (HGV) industry (September 10th 2009). Part of acquiring the PCV Initial Driver CPC qualification means having to pass the module 4 examination. Module 4 is the practical associated knowledge test that is carried out at a DSA approved test centre. There is no driving required (suffice for the rolling brake check.) Students will need a DSA approved vehicle to demonstrate their answers. This test is all about scenarios a professional PCV driver may encounter in his or her working life. It includes PCV drivers legal obligations (vehicles checks, not overloading, pre-use checking), as well as checking for illegal immigrants, dealing with emergency situations etc. The Module 4 exam will last approximately 20-30 minutes and the DSA examiner will ask approximately 5-6 questions. To be successful you must attain at least 75% for each question and at least 80% overall. This post looks at the possible questions you may be given for your minibus or coach Driver CPC module 4 examination. If you need HGV Module 4 questions and answers we recommend your visit our Module 4 HGV Driver CPC page. Module 4 requires competence of skills and knowledge in the following areas. Carrying passengers with due regard for safety rules and proper vehicle use. Ensuring passenger, comfort, safety and security. Preventing criminality and trafficking of illegal immigrants Assessing emergency situations Preventing physical risk The following should be used as a guide only. -
New Buses May Be "Most Expensive"
"Superbus" preliminary specifications New buses may be "most expensive" Out to manufacturers for review Residents in suburban areas of Indicating the increased costs of Preliminary specifications have gone seats, leg room and the feeling of Alameda and Contra Costa counties labor, materials and parts, Fresno out to American and European bus space, and comfortable temperature. who are receiving special bus ex Transit received an apparent low bid manufacturers for a high capacity bus All bus drivers polled liked the way tension service to BART stations may early this month from AM General offering more seats for riders while the bus handled and many felt its tur be riding in the most expensive Corp, of $66,895 per unit delivered, for holding down expenses and keeping ning response was superior to the 40- coaches in the urban transit industry. a standard 51-passenger bus with air fares stabilized. foot coach. Ease of steering also was Bids for 36 deluxe buses, opened this conditioning. General Motors, the only Seven transit properties are con mentioned, as were good acceleration, month, clearly showed how inflation other bidder, came in with $68,542 per sidering an initial joint order of ap braking and good curb pull-out. has hit coach manufacturers. bus delivered. The same bus a year ago proximately 160 articulated "Superbus" Nine year experiment Apparent low bidder was Flxible Co. had a unit price of $42,500. coaches for use in different areas of the AC Transit, which has experimented with a bid of $71 ,108 per bus delivered. Chicago Transit received a low bid country, with an articulated coach since 1966, General Motors, the only other bidder, on Dec. -
State of Good Repair Performance Measures: Assessing Asset Condition, Age, and Performance Data Final Report
State of Good Repair Performance Measures: Assessing Asset Condition, Age, and Performance Data Final Report June 2016 Project No. 2117-9060-02-B PREPARED FOR National Center for Transit Research (NCTR) II State of Good Repair Performance Measures: Assessing Asset Condition, Age, and Performance Data Final Report Prepared for: National Center for Transit Research University of South Florida Joel Volinski, Project Manager Prepared by: Lehman Center for Transportation Research (LCTR) Florida International University (FIU) 10555 West Flagler Street, EC 3609 Miami, FL 33174 Fabian Cevallos, Ph.D. Transit Program Director Phone: (305) 348-3144 Email: [email protected] June 2016 i II Disclaimer The contents of this report reflect the views of the authors, who are responsible for the facts and the accuracy of the information presented herein. This document is disseminated under the sponsorship of the University of South Florida’s National Center for Transit Research (NCTR) in the interest of information exchange. The University of South Florida and the National Center for Transit Research assume no liability for the contents or use thereof. The opinions, findings, and conclusions expressed in this publication are those of the authors and not necessarily those of the National Center for Transit Research. ii II TECHNICAL REPORT STANDARD TITLE PAGE 1. Report No. 2. Government Accession No. 3. Recipient's Catalog No. 4. Title and Subtitle 5. Report Date June 2016 State of Good Repair Performance Measures: Assessing Asset Condition, Age, and Performance Data 6. Performing Organization Code 7. Author(s) 8. Performing Organization Report No. Fabian Cevallos, Ph.D. 9. Performing Organization Name and Address 10. -
Dayton, Ohio Invests in High Tech Trolleybuses with In-Motion Charging
Published by the Electric Traction Committee, Edmonton Trolley Coalition Edited by Retired Employees of the Edmonton Transit Service VOL. 36 Adopting Tomorrow’s Technology Today: Dayton, Ohio invests in High Tech Trolleybuses with In-Motion Charging After lengthy testing, the Greater Dayton Regional Transit Authority (GDRTA) is buying 26 NexGen Electric Trolleys and will put the first production model in service by 2019. The RTA Board authorized spending up to $57.4 million for the 26 vehicles and parts, plus 15 more NexGen Trolleys that will be bought once federal funding is in place, Executive Director Mark Donaghy told reporters. It is the largest bus contract in RTA history. The NexGen Electric Trolleybus bus costs 63 percent more than a standard diesel transit bus, but has a 20-year, 800,000 mile life compared to the diesel’s 12-year, 500,000 mile life, Donaghy said. Electric trolleys are cheaper to operate, better for the environment and quieter than a diesel bus, he explained. “Using electric instead of diesel buses is a step towards a clean air environment for Dayton,” said Peggy Ann Berry, an occupational safety and health professional and Climate Reality Project leader in Dayton. “Diesel buses release dirty fossil fuel emissions into the environment. These emissions exacerbate asthma attacks as well as add to the cardiac burden of older adults.” RTA is now finalizing the cost of the NexGen after making several modifications to the prototype. The US Federal Transit Administration (FTA) is picking up 80 percent of the cost, and the rest comes from the local sales tax and rider fares. -
The Influence of Passenger Load, Driving Cycle, Fuel Price and Different
Transportation https://doi.org/10.1007/s11116-018-9925-0 The infuence of passenger load, driving cycle, fuel price and diferent types of buses on the cost of transport service in the BRT system in Curitiba, Brazil Dennis Dreier1 · Semida Silveira1 · Dilip Khatiwada1 · Keiko V. O. Fonseca2 · Rafael Nieweglowski3 · Renan Schepanski3 © The Author(s) 2018 Abstract This study analyses the infuence of passenger load, driving cycle, fuel price and four diferent types of buses on the cost of transport service for one bus rapid transit (BRT) route in Curitiba, Brazil. First, the energy use is estimated for diferent passenger loads and driving cycles for a conventional bi-articulated bus (ConvBi), a hybrid-electric two- axle bus (HybTw), a hybrid-electric articulated bus (HybAr) and a plug-in hybrid-electric two-axle bus (PlugTw). Then, the fuel cost and uncertainty are estimated considering the fuel price trends in the past. Based on this and additional cost data, replacement scenarios for the currently operated ConvBi feet are determined using a techno-economic optimisa- tion model. The lowest fuel cost ranges for the passenger load are estimated for PlugTw amounting to (0.198–0.289) USD/km, followed by (0.255–0.315) USD/km for HybTw, (0.298–0.375) USD/km for HybAr and (0.552–0.809) USD/km for ConvBi. In contrast, C the coefcient of variation ( v ) of the combined standard uncertainty is the highest for C PlugTw ( v : 15–17%) due to stronger sensitivity to varying bus driver behaviour, whereas C it is the least for ConvBi ( v : 8%). -
Totaltrack Holds the Line for Action Distribution Warehouse
Top Transport Vehicle Manufacturer Uses Intelligent Video to Prevent Intrusion and Scrap Metal Theft ioimage intelligent-video system installed to upgrade existing indoor and outdoor security at the Merkavim Merkavim Metal Works Ltd. Description: Transport & Bus Manufacturer founded in 1946 Cesarea Plant Employees: Approx. 300 Produces: Entire range of mini-buses, low-floor and articulated The theft and removal of items low-floor city buses, inter-city buses, tourist coaches, armored from outdoor sites that store and prisoner buses and other specialized passenger transport materials and equipment for solutions. Central Distribution Center: Production facility, covering over manufacturing and building 100,000 sqm, is located in Central Israel construction is becoming more widespread. Most often the damage far exceeded The assembly plant is located in the street or scrap value of the items an area that is surrounded by Worldwide equipment and scrap stolen farmland and open field areas. metal theft is costing billions of dollars and there are few ways Merkavim found that thieves were Thieves can easily scale to prevent these crimes or catch taking parts from busses and doing landscape walls and commercial these criminals. considerable damage in the process. wrought iron fences that protect Most often the damage far exceeded the the site. Just beyond the semi- The common reasons for the street or scrap value of the items stolen. decorative fences are access outbreak is an inability to watch On several occasions component steel roads, main streets and rail lines over expansive areas, absence used for manufacturing was stolen by that provide thieves access to the of security, or patchy traditional scrap metal thieves from the outdoor property as well as offer a means security that is too labor storage areas. -
The Energy-Pack APU-Replacement for Catenary Free Operation of Overhead Wired Buses
The Energy-Pack APU-Replacement for Catenary Free Operation of Overhead Wired Buses Vinzenz V. Haerri, Senior Member IEEE, Manuel Neumaier, Member IEEE, Philippe Schwartz Competence Center IIEE (Integral, Intelligent & Efficient Energy Systems) Lucerne University of Applied Sciences and Arts Technikumstrasse 21, 6048 Horw, Switzerland [email protected], [email protected], [email protected] Abstract—The so called Energy-Pack (EP) is a storage based replacement unit for traditional emergency auxiliary power units for overhead wired buses or trolleybuses. Besides the replacement, other important functions such as normal catenary free operation are possible. The design, realization, testing and pilot run in Switzerland are presented in this paper. The previous work of several other projects and investigations are first summarized and consist of concepts for the additional use of supercapacitors, the multifunctional use of the EP and simulations for understanding the significance for the supply quality of the EP’s use for several buses on the same line and at the same time. Secondly, the specification and realization of the EP are commented on. Finally, the results, testing procedure, commissioning and pilot run of a bus operator in Switzerland are described, followed by conclusions of this extensive and for future transport application very important project. Fig. 1. New 24m HESS trolleybus for 220 passengers (ref. VVL1) Keywords—batteries; supercapacitors; electric buses; overhead wired buses; energy management; electrical drive chain Since 1994, engineers at the Competence Center Integral, I. INTRODUCTION Intelligent and Efficient Energy Systems (CC IIEE) of The transport sector in Switzerland amounts to 37% of the Lucerne’s University of Applied Sciences & Arts are doing national energy demand, which is mainly based on oil. -
Monroe-Sachs Interchange
Table of Contents Chassis Section Nova Bus 22 Binkley 1 Orion Bus 23 Bluebird School Bus 1 Oshkosh 23 Brockway School Bus 1 Page Suspension 23 Built Rite Trailer 1 Pai Corporation 23 Cascade Trailer 1 Peerles Trailer 23 Chalmers Suspension 1 Peterbilt 23 Chance Bus 1 Prevost 24 Chevrolet 1 Reyco Suspension 24 Duplex Truck 2 Ridewell Corporation 24 Dura Suspension 3 Sterling 25 East Manufacturing Trailer 3 Trailmobile Canada Corp. 25 Ford 3 Turner Quick-Lift Corporation 26 Freightliner 3 Tuthill Technologies 26 Freightliner Custom Chassis 7 Twin Coach 26 Fruehauf 8 Utility Trailer 26 General Trailer Co. 8 Volvo 27 Gillig 8 Watson & Chain Suspension 28 GMC 8 Western Star 28 Great Dane Trailer 10 Western Unit 29 Hardee Manufacturing 10 Hendrickson 11 Highway Product 12 Cab Section Holland 12 Freightliner 30 Hutchens Suspension 12 Link Cabmate Air Suspension 30 Ikarus Bus 12 Western Star 31 International 12 Isuzu 15 Kenworth 16 Lodal Refuse Haulers 18 OEM Interchange 32 Mack 18 Gabriel - SACHS Interchange 37 Marmon Motor 20 Meritor - SACHS Interchange 38 Mitsubishi – Fuso 20 Monroe - SACHS Interchange 39 Neway 20 Specification Chart 40 North American Bus Industries 22 Customer Service & Technical Hotline Back Cover Important Notice The purpose of this catalog is to furnish ZF Services, LLC customers with as complete a listing of their parts requirements as possible. All listings, applications, and interchanges have been compiled as carefully as possible with all available information however, ZF Services, LLC cannot assume any responsibility for possible errors in listings, applications, or interchanges. All references by ZF Services, LLC to the original manufacturer trade names and part numbers are for identification purposes only. -
Cta 2016 Historical Calendar Cta 2016 January
cta 2016 Historical Calendar cta 2016 January Chicago Motor Coach Company (CMC) bus #434, manufactured by the Ford Motor Company, was part of a fleet of buses operated by the Chicago Motor Coach Company, one of the predecessor transit companies that were eventually assimilated into the Chicago Transit Authority. The CMC originally operated buses exclusively on the various park boulevards in Chicago, and became known by the marketing slogan, “The Boulevard Route.” Later, service was expanded to operate on some regular streets not served by the Chicago Surface Lines, particularly on the fringes of the city. Chicagoans truly wanted a unified transit system, and it was for this reason that the Chicago Transit Authority was established by charter in 1945. The CMC was not one of the initial properties purchased that made up CTA’s inaugural services on October 1, 1947; however, it was bought by CTA in 1952. D E SABCDEFG: MDecember 2015 T February 2016 W T F S CTA Operations Division S M T W T F S S M T W T F S Group Days Off 1 2 3 4 5 1 2 3 4 5 6 t Alternate day off if you 6 7 8 9 10 11 12 7 8 9 10 11 12 13 work on this day 13 14 15 16 17 18 19 14 15 16 17 18 19 20 l Central offices closed 20 21 22 23 24 25 26 21 22 23 24 25 26 27 27 28 29 30 31 28 29 1New Year’s Day 2 E F G A B C D 3 4 5 6 7 8 9 D E F G A B C 10 11 12 13 14 15 16 C D E F G A B 17 18Martin Luther King, Jr. -
Edmonton Trolley Coalition Bulletin
Edmonton Trolley Coalition Bulletin Don’t pull the shade on Edmonton’s Environment Volume #5 Published by the Edmonton Trolley Coalition, c/o 6811-31 Avenue, Edmonton, AB Canada T6K 3T5 www.geocities.com/trolley_coalition E-mail: [email protected] Editor: Robert R. Clark, retired supervisor of transit planning In this Issue: Where do we go from here? . .. p. 1 Our Editorial: Do the savings add up? . p. 1 Local News . .. p. 2 North American News . .. p. 3 Where do we go from here? At the March 16th Meeting of Council’s Transportation and Public Works Committee, city administrators put forward a proposal to hold public hearings on the future of the trolley system on April 8th, along with a recommendation that the city discontinue all trolley service permanently this summer. After hearing concerns from the Edmonton Transit System Advisory Board, the Edmonton Federation of Community Leagues, the Edmonton Trolley Coalition and an Inglewood resident, Council’s committee decided to defer the hearings until late June. One of the main concerns presented was the apparent haste to rush into an irreversible decision on an important issue; other concerns surrounded the controversial consultants report which administration had used to support its recommendation. In the interim, administration has been directed to consult with citizens. Consultation is now planned to take place at two public meetings, by telephone, as well as though on-board surveys of transit riders. It is hoped the consultation process will be objective in its method as well as in any information provided to citizens. Objectivity and balance were two problems identified in the consultants study. -
1983 Ketron Inc
DOT-TSC-U MT A -83-2 Wheelchair Lifts on U.S.Department of Transportation Transit Buses Urban Mass Transportation Administration Prepared by: January 1983 Ketron Inc. H: 3 1 ~ 190 i EQUIPM ENT ENGlNEERING DEPARTMENT NOTICE This document is disseminated under the sponsorship of the Department of Trans portation in the interest of information exchange. The United States Government assumes no liability for its contents or use thereof. The United States Government does not endorse products or manufacturers. Trade or manufacturers' names appear herein solely because they are considered essential to th e object of this report. DOT-TSC-U tv'IT A-83-2 S.C.R. T.D. LIBRARY Wheelchair Lifts on U.S. Department of Transportation Urban Mass Transit Buses Transportation Administration Summary of U. S. Experience Prepared by: Ketron Inc. One Broadway Cambridge MA 02142 Office of Technical Assistance Office of Bus and Paratransit Systems Washington DC 20590 0-7548 ~ .. PREFACE This project was conducted for the USDOT Transportati on Systems Center (TSC) and the Urban Mass Transportation Administration (UMTA) by KETRON, Inc . - Cambridge Facility. The contract \vas initiated in September, 1980 betv1een TSC and Applied Resour ce Integration, Ltd. (ARI) of Boston - Contract r~o . DTRS57-80-C-00150 . In 1981 KETRON acquired ARI and t he project was continued and completed by the same project teom . The successful completion of t he project is attr ibutabl e to the cooperation of a large number of organizations and personnel representing t r ansit properties, bus manuf ac t ur Prs, lift su pp liers , and others concerned v1ith the problem of acccssi bil ity on public transit systems. -
Motor Vehicle Make Abbreviation List Updated As of June 21, 2012 MAKE Manufacturer AC a C AMF a M F ABAR Abarth COBR AC Cobra SKMD Academy Mobile Homes (Mfd
Motor Vehicle Make Abbreviation List Updated as of June 21, 2012 MAKE Manufacturer AC A C AMF A M F ABAR Abarth COBR AC Cobra SKMD Academy Mobile Homes (Mfd. by Skyline Motorized Div.) ACAD Acadian ACUR Acura ADET Adette AMIN ADVANCE MIXER ADVS ADVANCED VEHICLE SYSTEMS ADVE ADVENTURE WHEELS MOTOR HOME AERA Aerocar AETA Aeta DAFD AF ARIE Airel AIRO AIR-O MOTOR HOME AIRS AIRSTREAM, INC AJS AJS AJW AJW ALAS ALASKAN CAMPER ALEX Alexander-Reynolds Corp. ALFL ALFA LEISURE, INC ALFA Alfa Romero ALSE ALL SEASONS MOTOR HOME ALLS All State ALLA Allard ALLE ALLEGRO MOTOR HOME ALCI Allen Coachworks, Inc. ALNZ ALLIANZ SWEEPERS ALED Allied ALLL Allied Leisure, Inc. ALTK ALLIED TANK ALLF Allison's Fiberglass mfg., Inc. ALMA Alma ALOH ALOHA-TRAILER CO ALOU Alouette ALPH Alpha ALPI Alpine ALSP Alsport/ Steen ALTA Alta ALVI Alvis AMGN AM GENERAL CORP AMGN AM General Corp. AMBA Ambassador AMEN Amen AMCC AMERICAN CLIPPER CORP AMCR AMERICAN CRUISER MOTOR HOME Motor Vehicle Make Abbreviation List Updated as of June 21, 2012 AEAG American Eagle AMEL AMERICAN ECONOMOBILE HILIF AMEV AMERICAN ELECTRIC VEHICLE LAFR AMERICAN LA FRANCE AMI American Microcar, Inc. AMER American Motors AMER AMERICAN MOTORS GENERAL BUS AMER AMERICAN MOTORS JEEP AMPT AMERICAN TRANSPORTATION AMRR AMERITRANS BY TMC GROUP, INC AMME Ammex AMPH Amphicar AMPT Amphicat AMTC AMTRAN CORP FANF ANC MOTOR HOME TRUCK ANGL Angel API API APOL APOLLO HOMES APRI APRILIA NEWM AR CORP. ARCA Arctic Cat ARGO Argonaut State Limousine ARGS ARGOSY TRAVEL TRAILER AGYL Argyle ARIT Arista ARIS ARISTOCRAT MOTOR HOME ARMR ARMOR MOBILE SYSTEMS, INC ARMS Armstrong Siddeley ARNO Arnolt-Bristol ARRO ARROW ARTI Artie ASA ASA ARSC Ascort ASHL Ashley ASPS Aspes ASVE Assembled Vehicle ASTO Aston Martin ASUN Asuna CAT CATERPILLAR TRACTOR CO ATK ATK America, Inc.