Environmentally Friendly Deinking Process by Enzymes
Total Page:16
File Type:pdf, Size:1020Kb
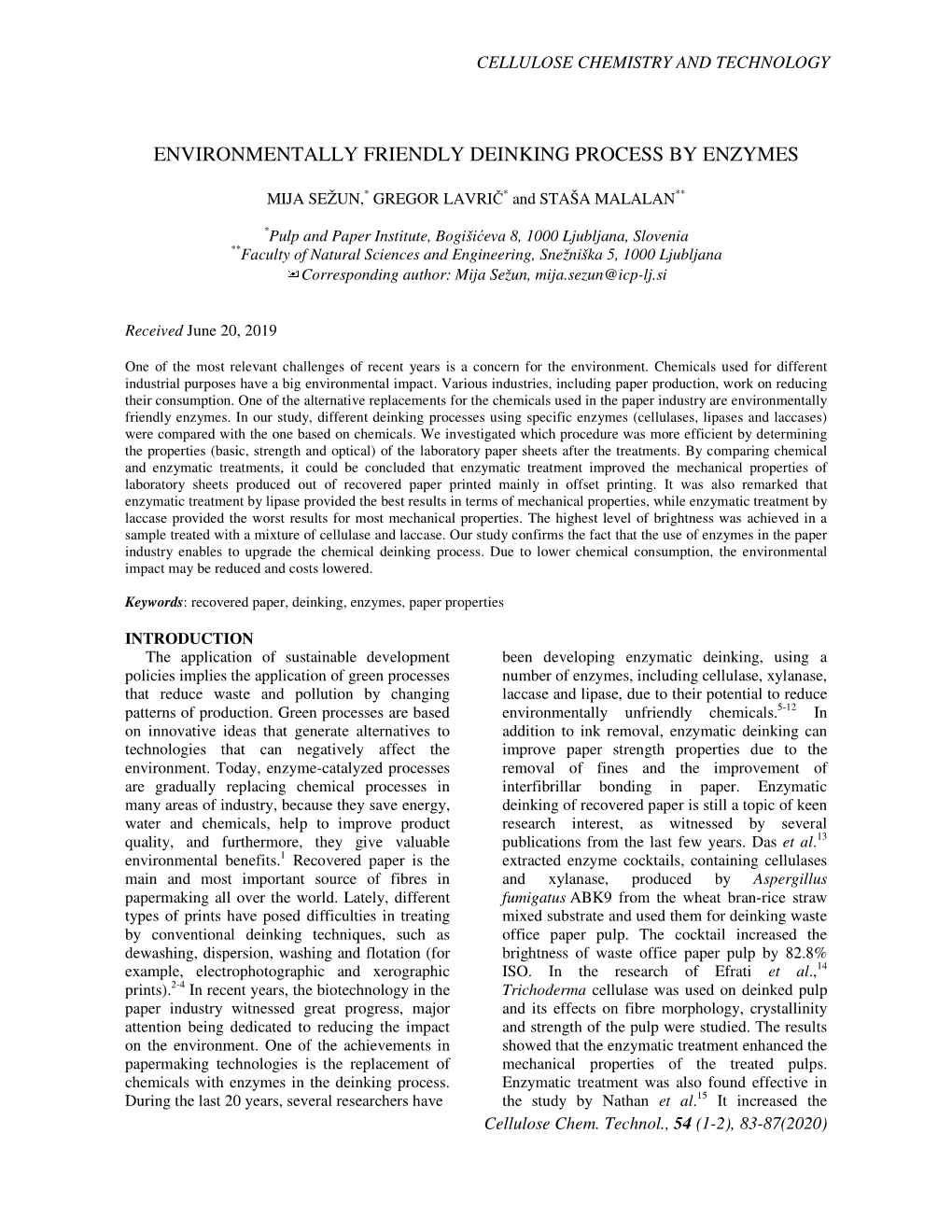
Load more
Recommended publications
-
CHAPTER 47 PULP of WOOD OR of OTHER FIBROUS CELLULOSIC MATERIAL; WASTE and SCRAP of PAPER OR PAPERBOARD X 47-1 Note L
)&f1y3X CHAPTER 47 PULP OF WOOD OR OF OTHER FIBROUS CELLULOSIC MATERIAL; WASTE AND SCRAP OF PAPER OR PAPERBOARD X 47-1 Note l. For the purposes of heading 4702, the expression "chemical wood pulp, dissolving grades" means chemical woodpulp having by weight an insoluble fraction of 92 percent or more for soda or sulfate woodpulp or of 88 percent or more for sulfite woodpulp after one hour in a caustic soda solution containing 18 percent sodium hydroxide (NaOH) at 20oC, and for sulfite woodpulp an ash content that does not exceed 0.15 percent by weight. )&f2y3X X 47-2 4701.00.00 00 4 Mechanical woodpulp................................ t....... Free Free 4702.00.00 Chemical woodpulp, dissolving grades............... ........ Free Free 20 9 Sulfite....................................... t 40 5 Sulfate or soda............................... t 4703 Chemical woodpulp, soda or sulfate, other than dissolving grades: Unbleached: 4703.11.00 00 9 Coniferous............................... t....... Free Free 4703.19.00 00 1 Nonconiferous............................ t....... Free Free Semibleached or bleached: 4703.21.00 Coniferous............................... ........ Free Free 20 3 Semibleached........................ t 40 9 Bleached............................ t 4703.29.00 Nonconiferous............................ ........ Free Free 20 5 Semibleached........................ t 40 1 Bleached............................ t 4704 Chemical woodpulp, sulfite, other than dissolving grades: Unbleached: 4704.11.00 00 8 Coniferous............................... t....... Free Free 4704.19.00 00 0 Nonconiferous............................ t....... Free Free Semibleached or bleached: 4704.21.00 00 6 Coniferous............................... t....... Free Free 4704.29.00 00 8 Nonconiferous............................ t....... Free Free 4705.00.00 00 0 Semichemical woodpulp.............................. t....... Free Free 4706 Pulps of other fibrous cellulosic material: 4706.10.00 00 7 Cotton linters pulp.......................... -
Q2 2021 Presentation 16 July 2021
Q2 2021 presentation 16 July 2021 Follow us on LinkedIn www.norskeskog.com Sustainable and innovative industry ENTERING Biochemicals 1,000 tonnes of 500 tonnes of 300 tonnes of ▪ Leading publication paper producer with five & materials biochemicals capacity1 CEBINA capacity CEBICO capacity (pilot) industrial sites globally Q1 2023 Q4 2021 ▪ Ongoing transition into higher growth and ENTERING higher value markets Renewable Interliner 760k tonnes of ~200k tonnes of ▪ Becoming a leading independent European packaging containerboard capacity Interliner capacity recycled containerboard company in 2023 Q4 2022 ▪ Packaging market growth and margin EXPANDING outlook strengthened since announcement Waste-to- Green bio- Sustainable energy plant mass energy ▪ High return waste-to-energy project +400 GWh of waste- ~425 GWh of wood ~28 GWh of biogas ~1,000 GWh of biomass energy based energy capacity pellets capacity energy capacity energy capacity2 improving green energy mix in Q2 2022 Q2 2022 ▪ Promising biochemicals and materials projects spearheaded by Circa PRESENT ▪ Industrial sites portfolio provide foundation for Publication 1,400k tonnes of 400k tonnes of 360k tonnes of further industrial development paper Newsprint capacity LWC capacity SC capacity Under construction Date Estimated start-up date 2 1) Norske Skog is the largest shareholder with ~26% ownership position in Circa; 2) Installed capacity for biofuel and waste from recycled paper of 230 MW Second quarter in brief Final investment decision made for Golbey conversion to containerboard -
Deinking of Screen-Printed Electrodes Printed on Invasive Plant-Based Paper
sustainability Article Article DeinkingDeinking of of Screen-Printed Screen-Printed Electrodes Printed on InvasiveInvasive Plant-Based Plant-Based Paper UrškaUrška Kav Kavˇciˇc*čič *, Igor, Igor Karlovits Karlovits and and Janja Janja Zule Zule PulpPulp and and Paper Paper Institute, Institute, Bogiši Bogiši´ceva8,ćeva 8, 1000 Ljubljana, Slov Slovenia;enia; igor.karlovits@icp-lj. [email protected] (I.K.); janja.zule@icp- [email protected] (J.Z.) (J.Z.) * Correspondence: [email protected] Received: 21 January 2020; Accepted: 6 February 2020; Published: date Received: 21 January 2020; Accepted: 9 February 2020; Published: 12 February 2020 Abstract: The deinking of paper-based printed electronics is a growing concern regarding the Abstract: The deinking of paper-based printed electronics is a growing concern regarding the increase increase of printed electronics products. The benefits of using paper-based substrates instead of of printed electronics products. The benefits of using paper-based substrates instead of polymer polymer or ceramic for the single-use printed electrodes can contribute to sustainability goals. The or ceramic for the single-use printed electrodes can contribute to sustainability goals. The use of use of invasive plant species for making paper substrates for printed electronics is a unique invasive plant species for making paper substrates for printed electronics is a unique opportunity opportunity to have several environmental benefits. In this study, the recycling issue of these to have several environmental benefits. In this study, the recycling issue of these products through products through the use of the deinking technique was evaluated. Screen-printed electrodes the use of the deinking technique was evaluated. -
ANNUAL REPORT 1997 1 Main Figures Per Area
NORSKE SKOG ANNUAL REPORT 1997 1 Main figures per Area 1997 1996 1995 1994 1993 1992 1991 1990 1989 Area Paper Operating revenue NOK million 9,284 9,493 8,066 5,831 4,731 4,773 5,855 6,733 5,768 Operating profit NOK million 1,134 2,078 1,708 454 469 95 656 721 398 Operating margin % 12.2 21.9 21.2 7.8 9.9 2.0 11.2 10.7 6.9 Area Fibre Operating revenue NOK million 1,376 1,222 2,171 1,498 1,052 1,202 1,247 1,709 2,025 Operating profit NOK million 49 -127 682 178 -187 -176 -164 327 615 Operating margin % 3.6 -10.4 31.4 11.9 -17.8 -14.6 -13.2 19.1 30.4 Area Building Materials Operating revenue NOK million 2,667 2,579 2,333 2,048 1,704 1,688 1,725 1,960 1,911 Operating profit NOK million -16 27 96 146 85 64 9 107 93 Operating margin % -0.6 1.0 4.1 7.1 5.0 3.8 0.5 5.5 4.9 Operating revenue per market Operating revenue per product Rest of Other world 8% 2% Pulp 8% Norway 23% Newsprint Special grades 1% USA 10% 40% SC magazine paper 20% Other Europe 25% Germany 15% LWC magazine paper 9% UK 11% France 8% Building materials 20% 2 NORSKE SKOG ANNUAL REPORT 1997 1997 Highlights Price decline caused weaker result Growth in sawn timber Expansion in Eastern Europe Prices of paper and pulp fell during the In September, Norske Skog took over In November, Norske Skog took over first quarter of 1997. -
Paper Recycling Technology Detailed Part 1A
Paper Recycling Technology and Science Dr. Richard A. Venditti Paper Science and Engineering Forest Biomaterials Department North Carolina State University Lecture: Paper recycling and technology course introduction and objectives Dr. Richard Venditti Faculty member in the Paper Science and Engineering Program in the Forest Biomaterials Department at North Carolina State University PhD in Chemical Engineering, BS in Pulp and Paper Science and Chemical Engineering Research areas: � Paper recycling � Utilization of forest/agricultural materials for new applications � Life cycle analysis Named a TAPPI Fellow in 2012 Relevant research projects: – The detection of adhesive contaminants – The changes in fibers upon recycling – Automatic sorting of recovered papers – Flotation deinking surfactants – Agglomeration deinking – Screening phenomena and pressure sensitive adhesives – Deposition of adhesive contaminants – Neural networks to control deinking operations – Sludge conversion to bio-ethanol and to bio- materials Course Outline The US Paper Recycling Industry Recovered Paper Grades and Contaminants Effect of Recycling on Fibers/Paper Unit Operations � Pulping, Cleaning, Screening, Washing, Flotation, Dispersion, Bleaching, ….. Image Analysis, Deinking Chemicals System Design Advanced/Additional Topics Course Activities Viewing of the Videos of Lectures � Base lectures by Venditti � Guest lectures from industry leaders Homework assignments Final Exam Critical Issues in Recycling: Going deeper into the recovered paper stream -
The Effects of Deinking on the Coating Compounds Used on Carbonless Business Forms
Rochester Institute of Technology RIT Scholar Works Theses 11-1-1991 The Effects of deinking on the coating compounds used on carbonless business forms Brooke Merrill Tinney Follow this and additional works at: https://scholarworks.rit.edu/theses Recommended Citation Tinney, Brooke Merrill, "The Effects of deinking on the coating compounds used on carbonless business forms" (1991). Thesis. Rochester Institute of Technology. Accessed from This Thesis is brought to you for free and open access by RIT Scholar Works. It has been accepted for inclusion in Theses by an authorized administrator of RIT Scholar Works. For more information, please contact [email protected]. School ofPrinting Management and Sciences Rochester Institute of Technology Rochester, New York Certificate of Approval Master's Thesis This is to certify that the Master's Thesis of Brooke Merrill Tinney With a major in Printing Technology has been approved by the Thesis Committee as satisfactory for the thesis requirement for the Master of Science degree at the convocation of Thesis Committee: Joseph E. Brown Thesis Advisor Andreas Lenger Research Advi$or Joseph L. Noga Graduate Program Coordinator George H. Ryan Director or Designate The Effects of Deinking on the Coating Compounds Used on Carbonless Business Forms by Brooke Merrill Tinney A thesis submitted in partial fulfillment of the requirements for the degree of Master of Science in the School of Printing Management and Sciences in the College of Graphic Arts and Photography of the Rochester Institute of Technology November 1991 Thesis Advisor: Professor Joseph E. Brown Research Advisor: Dr. Andreas Langner Title of Thesis: The Effects of Deinking on the Coating Compounds Used on Carbonless Business Forms I, Brooke Merrill Tinney, hereby grant permission to the Wallace Memorial Library of R.I.T. -
Alternative Use of Deinking Sludge As a Source of Fibers in Fiber-Cement Manufacture
CORE Metadata, citation and similar papers at core.ac.uk Provided by EPrints Complutense CELLULOSE CHEMISTRY AND TECHNOLOGY ALTERNATIVE USE OF DEINKING SLUDGE AS A SOURCE OF FIBERS IN FIBER-CEMENT MANUFACTURE ANGELES BLANCO, CARLOS NEGRO, ELENA FUENTE and LUIS MIGUEL SÁNCHEZ Department of Chemical Engineering, Chemistry Faculty, Avda. Complutense s/n 28040 Madrid, Spain The present paper, contributing to solving two different problems related both to the chemical industry and the environment, is a feasibility study on the utilization of the deinking sludge (the most important waste from papermaking) as a raw material for fiber-cement manufacture, in which asbestos has been recently replaced by other fibers because of the hazard it induces. The results obtained show that the use of deinking sludge as a source of cellulose in fiber-cement manufacture is feasible and could improve product strength, if 5% of the virgin fibers are replaced by fibers and fines from the deinking sludge. It is also possible to replace up to 10% of the virgin fibers, with no loss in product strength. These results, if confirmed on a mill scale, would improve the economy of the process, as due to lower waste costs. Keywords: fiber-cement, deinking sludge, recycling, waste management, sustainability, papermaking wastes INTRODUCTION As known, papermaking is an industry However, recycling operations, espe- leader from the standpoint of recycling and cially deinking, generate an important sustainability, the main reason being that quantity of wastes, representing 70% of the virgin and recycled fibers can be used wastes produced by the European pulp and together, sometimes contributing with paper industry. -
Benefits of Polycups Stock Over Other Waste Paper Grades in Paper Recycling
EDITORIAL bioresources.com Benefits of Polycups Stock over Other Waste Paper Grades in Paper Recycling Avdhesh K. Gangwar It is never too late or too early to invent alternative processes for the betterment of our routine life. For paper production, trees are being cut in huge quantities each day, and this directly affects our day to day life by making atmospheric conditions less favorable. Waste paper can be recycled on average 4 to 6 times while maintaining acceptable qualities in recycled paper. To save forest resources, we should move ahead towards using more and more waste paper for paper production. A wasted resource can be recycled either to make the same product or by manufacturing new products, e.g. cardboard boxes, newspaper, writing and printing papers, and paper bags, etc. Several waste paper grades are not being fully utilized, and their use might allow increased paper recycling to produce new recovered paper with specified paper qualities. Polycup stock is an example of an under-utilized type of wastepaper that has the potential to substitute effectively for virgin pulp production. Keywords: Deinking; Paper grades; Paper recycling; Polycups Contact information: Department of Biotechnology, Thapar University, P. O. Box 32, Pin- 147004, Patiala, India; [email protected] Recycle more to save our environment, but is it really easy to do? This editorial considers a way to minimize waste by using a neglected waste paper grade for the manufacture of paper. Ordinarily, for this to happen, adequate deinking of recycled fibre is needed to remove all ink and other unwanted materials from the secondary fibres. -
True-Neutral Deinking
deinking True-Neutral Deinking Katahdin Paper Company’s East Millinocket, Maine mill switches to a new technology with ONP/OMG furnish and reduced chemical costs while stabilizing deinking operations. — By Herman Morrow, Bob Horacek, Kevin Hale, Scott Rosencrance In March 2004 Katahdin Paper Co.’s uncoated The primary benefits of true-neutral deinking can be groundwood paper mill in East Millinocket, Maine, became substantial, including significantly reduced chemical costs the first ongoing true-neutral deinking facility in the world (typically ranging from $2-$5 per ton) due to the elimina- using old newspapers (ONP) and old magazine grade tion of caustic, peroxide, chelant, biocide/catalase control, (OMG) recovered paper furnishes. and all or part of the sodium silicate from the pulper. Often, During the past year and a half of operations with the all or part of the sulfuric acid normally used prior to hydro- new true-neutral process, implemented in cooperation with sulfite bleaching is also eliminated. There are other related its developer Kemira Chemicals Inc., the mill has significantly advantages as well, since several of these eliminated chemi- reduced pulping and bleaching costs by completely eliminat- cals have serious safety and environmental implications. ing the usage of several chemicals, while maintaining pulp The quest for neutral or low-alkali deinking at quality, yield, and production. Switching to true-neutral has ONP/OMG mills has been increasing recently, partly due to also improved deinking process stability compared with the the highly competitive newsprint market in North America alkaline process previously used at East Millinocket. and the need for mills to reduce costs wherever possible. -
Deinking of HP Digital Commercial Prints: Effect of Chemicals and Their Loadings on Deinkability
Deinking of HP Digital Commercial Prints: Effect of Chemicals and Their Loadings on Deinkability Hou T. Ng, Manoj K. Bhattacharyya, Laurie S. Mittelstadt, Eric G. Hanson HP Laboratories HPL- 2009-310 Keyword(s): deinking, LEP, neutral chemistry, ethoxylated fatty alochol Abstract: Here we show that the effect of chemicals and their specific loadings play a dominant role on the outcome of a deinking process. More specifically, we demonstrate that good deinkability of HP digital commercial prints (i.e. liquid-electrophotographic (LEP), dry-EP and inkjet (IJ) prints) can be achieved with our highly efficient neutral deinking chemistry (coded HPE6S4), which is based on readily available non-proprietary chemicals. We found a direct correlation of the chemical effects to the ink-particle speck contamination and its particle-size distribution. Our excellent results compared favorably to that obtained with the traditional deinking chemistry. Our approach can be readily scalable for adaption in the paper recycling mills. External Posting Date: Septembe r 18, 2009 [Fulltext] Approved for External Publication Internal Posting Date: Sept ember 18, 2009 [Fulltext] © Copyright 2009 Hewlett-Packard Development Company, L.P. Deinking of HP Digital Commercial Prints: Effect of Chemicals and Their Loadings on Deinkability Hou T. Ng, Manoj K. Bhattacharyya, Laurie S. Mittelstadt, Eric G. Hanson HP Labs, Hewlett-Packard Company, 1501 Page Mill Rd, Palo Alto, CA 94304, USA Abstract a pulp consistency of 5% and stored for 60 min in a water bath Here we show that the effect of chemicals and their specific maintained at 45°C. Before the flotation stage, the stock was loadings play a dominant role on the outcome of a deinking further diluted with 45°C warm water to a consistency of process. -
Mechanism and Novel Deinking Methods for Non-Impact Printed Paper
MECHANISM AND NOVEL DEINKING METHODS FOR NON-IMPACT PRINTED PAPER A Thesis Presented to The Academic Faculty By Daniel T. Lee In Partial Fulfillment Of the Requirements for the Degree Master of Science in Chemical and Biomolecular Engineering Georgia Institute of Technology August 2014 Copyright © Daniel T. Lee 2014 DEINKING OF HYDROPHILIC INKS BY DECREASED INK REATTACHMENT DURING PULPING Dr. Jeffery S. Hsieh, Advisor School of Chemical and Biomolecular Engineering Georgia Institute of Technology Dr. Martha A. Grover School of Chemical and Biomolecular Engineering Georgia Institute of Technology Dr. Dennis W. Hess School of Chemical and Biomolecular Engineering Georgia Institute of Technology Date Approved: June 12, 2014 ACKNOWLEDMENTS I would like to express my sincere thanks to my advisor Jeffery Hsieh for his support, advice, and significant time commitment to my research while at Georgia Tech. I would also like to thank Dr. Hsieh’s research group for all of their assistance. Specifically, I would like to thank Xiaotang (Tony) Du for his thought provoking questions, expertise, and advice along the way. Also, I would like to thank Alex Jordan for introducing me to the lab and Mary Johnson for her patience while supporting our lab. Finally, I would like to thank my committee members, Dr. Grover and Dr. Hess, for committing their time to serve on my thesis committee as well as their insightful critiques of my work. iii TABLE OF CONTENTS ACKNOWLEDMENTS ................................................................................................... -
Deinking and Reuse of Old Coloured Newsprint
---_._------_._---,------------- Journal of Scientific & Industrial Research Vol. 60, August 2001, pp 649-654 Deinking and Reuse of Old Coloured Newsprint Magda G El-Meligy' and Maha M Ibrahim Cellulose and Paper Department, National Research Centre, Dokki, Cairo, Egypt Received: 28 August 2000; accepted: 30 April 2001 Due to increase in paper product requirements and the sources for production gradually decreasing the percentage of deinked newsprint and other grades is expected to increase considerably over the next few years. About 80 per cent of all waste paper comes from three sources: Corrugated boxes, Newspapers, and Office papers. It is also observed that the biggest users of deinked waste paper are newsprint, tissue or other bright grades'.As a result of the technological progress, use of colour in newspaper is becoming increasingly popular. In this work, oxidant acids such as sulphuric or acetic acids however play an important role for disintegrating the coloured materials from the old coloured newsprint in certain condition such as temperature. concentration of acid, and time. The paper produced has satisfactory optical and physical properties but a slight decrease in the mechanical properties, where addition of some additives such as polyvinyl alcohol, new pulp or paper shaving at certain percent- age, improved these properties. Introduction is affected not only by the amount of ink present but also by the size distribution of the ink particles". Typically, new ink consists of carbon black and a high viscosity mineral oil blended with low-viscosity min- Hayashi" has claimed that both oil absorbency and erai oil to give the desired viscosity but coloured news- opacity of recycled fiber newsprint were lower than those print ink consists of mineral oil blended with pigment of virgin-fiber newsprint.