Recent Development of Cardanol Based Polymer Materials-A Review
Total Page:16
File Type:pdf, Size:1020Kb
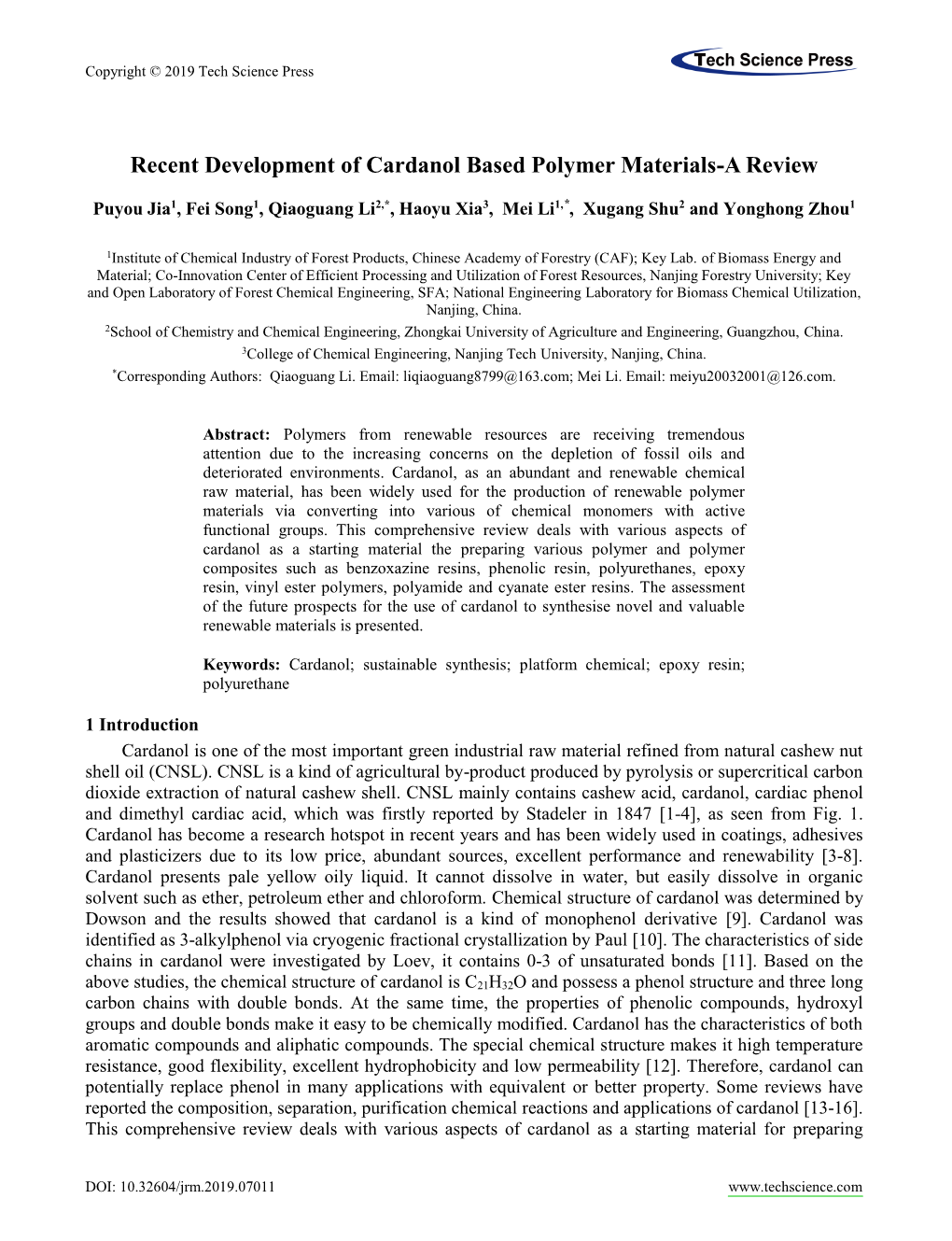
Load more
Recommended publications
-
United States Patent (19) 11 Patent Number: 5,077,324 Kistner Et Al
United States Patent (19) 11 Patent Number: 5,077,324 Kistner et al. 45 Date of Patent: Dec. 31, 1991 (54) REACTIVE SET AND MULTIPLE CHAMBER 3,915,297 0/1975 Rausch ................................ 206/29 CARTRIDGE AND PROCESS FOR 3,968,016 0/1976 Wisner ................................. 525/31 ADHESIVE ANCHORNG OF FASTENERS 4,105,114 0/1978 Knox et al. ......................... 405/261 4,343,921 0/1982 Piestert ................................ 52.5/531 INA BASE 4,58,283 0/1985 Gebauer et al. .................... 523/500 75 Inventors: Herbert Kistner, Freiburg; Christian 4,729,696 3/1988 Goto et al. ............................ 52.5/53 Weber, Emmendingen, both of Fed. Rep. of Germany OTHER PUBLICATIONS 73 Assignee: UPAT GmbH & Co., Emmendingen, Soviet "Inventions Illustrated', 1983, Week K11, Der Fed. Rep. of Germany went Publications, p. 36. Primary Examiner-Kriellion S. Morgan (21) Appl. No.: 315,892 Assistant Examiner-P. D. Niland 22 PCT Filed: Oct. 29, 1987 Attorney, Agent, or Firm-Baker & Daniels (86 PCT No.: PCT/DE87148700 57 ABSTRACT S371 Date: Feb. 14, 1989 A reactive composition for preparing synthetic resin bodies used in destructible multible-chamber cartridges S 102(e) Date: Feb. 14, 1989 and a process for anchoring a fastening element to the 87 PCT Pub. No.: WO88/03599 fastening base by introducing the destruction multiple chamber cartridges containing the components of a PCT Pub. Date: May 19, 1988 curable adhesive in a drilling in the fastening base. (30) Foreign Application Priority Data When the fastening element is driven into the hole, the cartridge is destroyed, the synthetic resin components Nov. 13, 1986 (DE) Fed. -
Engineering Plastics[PDF:166KB]
Daicel Group Businesses and Growth Strategies Engineering plastics TOPICS Contribution to Circular Economy with PET Bottle labels that Values Group Daicel for Framework Conceptual float on water While plastics are highly convenient and essential for modern higher specific gravity than water, do not float. Labels using society, they also become a cause of marine litter and TOPAS® COC (cyclic olefin copolymer), a material developed Supporting the sustainable global warming. To solve these issues, the easily recyclable by Polyplastics, fit this strategy because they do float in water, development of society by material for plastic beverage bottle labels was developed by enabling bottles and labels to be collected separately, simply Polyplastics. by placing bottle flakes in water and thereby accelerating offering plastics with special Since the raw materials used for plastic bottle bodies, the recycling process, while at the same time retaining the features such as mechanical caps, and labels differ, recycling plastic beverage bottles printability, shrinkability, and adhesiveness of conventional requires separating by resin type. In Europe, recycling labels. Moreover, although TOPAS® is different from strength and resistance to plants are equipped with a machine that removes labels polypropylene (PP) or polyethylene terephthalate (PET), labels Highlights Financial/Non-Financial heat and chemicals. from the bodies, and consumers must peel off the labels made of TOPAS® can be recycled as an olefin material. before disposal. Still, such approaches are rather ineffective As the demand for TOPAS® COC rapidly grows, it has in terms of both cost and results. As the search for a more become necessary to enhance our supply system for the efficient solution continues, a spotlight has been cast on a product. -
United States Patent Office Patented Dec
3,781,233 United States Patent Office Patented Dec. 25, 1973 1. 2 3,781,233 1 to 4 carbon atoms, hydroxyl or nitro groups or halo BLOWING AGENTS gen atoms and Erwin Muller, Leverkusen, Wolf-Dieter Wirth, Odenthal, X denotes a bond or a radical such as phenylene, naphthyl Johannes Blahak, Cologne, and Harry Rohr, Lever ene, diphenylene substituted with nitro or alkyl groups, kusen, Germany, assignors to Bayer Aktiengesellschaft, enediamine and N,N-dimethyl-N,N-dimethylene Leverkusen, Germany ylene, methylene dicyclohexylene, cyclohexylene, ethyl No Drawing. Filed May 25, 1972, Ser. No. 256,730 ene, dimethylene carbonate, N,N'-dimethylene-ethyl Claims priority, application Germany, May 26, 1971, enediamine and N,N'-dimethyl - N,N'-dimethylene P 21. 26 145.0 Int. C. C08 1/20 ethylenediamine or a radical obtained by removal of U.S. C. 260-2S R 13 Claims O two hydrogen atoms from a diphenylether or from ca as blowing agents for the production of cellular or porous ABSTRACT OF THE DISCLOSURE synthetic resin articles based on acrylonitrile, butadiene The invention relates to the use of bisbenzazimide com and styrene copolymers. pounds as blowing agents for the production of cellular The compounds according to the invention are suitable and porous articles from acrylonitrile, butadiene and for the production of foam plastics from thermoplastic styrene copolymers. The blowing agents do not liberate synthetic resins. The following are examples of com any corrosive, discoloring, malodorous or toxic decon pounds according to the invention: position products. 5,5'-dinitro-bisbenzazimide; 20 5,5'-dichloro-bisbenzazimide; This invention relates to the use of compounds of the 4,4'-dichloro-bisbenzazimide; bisbenzazimide series as blowing agents for the production 5,5'-dimethyl-bisbenzazimide; of cellular and porous articles based on acrylonitrile, 4,4'-dimethyl-bisbenzazimide; butadiene and styrene copolymers. -
Oosea/31 Maasa by 1%-A- 7%Retc., 16-Ce Ya 47%Ily 3,562,985 United States Patent Office Patented Feb
Feb. 16, 1971 J. A. NICOSA 3,562,985 REINFORCED SYNTHETIC RESIN STRUCTURAL PANELS Original Filed Oct. 23, l965 RSSSSK2 S 12 INVENI ()R. oosea/31 Maasa BY 1%-a- 7%retc., 16-ce Ya 47%ily 3,562,985 United States Patent Office Patented Feb. 16, 1971 2 ing panels constructed in accordance with the present in 3,562,985 vention; REINFORCED SYNTHETIC RESEN FIG. 2 is an elevational side view taken along the lines STRUCTURAL PANELS Joseph A. Nicosia, 819 N. Thatcher Ave., II-II of FIG. 1; River Forest, III. 60305 FIG. 3 is a top plan view of the building board of Continuation of application Ser. No. 503,736, Oct. 23, FIGS. 2 and 3; 1965. This application Jan. 13, 1969, Ser. No. 793,225 FIG. 4 is a plan elevational view of part of the panel Int, C. E04c 2/46 of FIGS. 1-3; U.S. C. 52-24 4 Claims FIGS. 5 and 6 are top plan views similar to that of O FIG. 3, of two alternative constructions of the panels. As shown on the drawings, the structural boards and ABSTRACT OF THE DISCLOSURE panels of the present invention are made from any suit A building structure comprising a plurality of inter able foamed synthetic resin i.e. foamed polystyrene beads connecting barriers, said barriers comprising a plurality such as Pelaspan 8 and Pelaspan 18, polystyrene flakes, of interconnecting panels, said panels comprising a rigid epoxy resin, polyurethane of the polyester and polyure molded synthetic resin foam having embedded therein a thane of the polyether type. -
Manufacturing of Synthetic Resins with Formulation
Introduction Synthetic resins are materials with a property of interest that is similar to natural plant resins: they are viscous liquids that are capable of hardening permanently. Otherwise, chemically they are very different from the various resinous compounds secreted by plants. Synthetic resins comprise a large class of synthetic products that have some of the physical properties of natural resins but are different chemically. Synthetic resins are not clearly differentiated from plastics. www.entrepreneurindia.co In modern industry natural resins have been almost entirely replaced by synthetic resins, which are divided into two classes, thermoplastic resins, which remain plastic after heat treatment, and thermosetting resins, which become insoluble and infusible on heating. Thermoplastic resin softens repeatedly by heating. Thermosetting resin, on the other hand, hardens only once when heated. Thermoplastics produced by the local industry include Polystyrene (PS), Polyvinyl Chloride (PVC), Alkyds and Polyester Fiber, while those of thermosetting resins include Phthalic Anhydride, Aluminum Paste Resin, Adhesive Resin, Acrylic Resin Urea- and Phenol-Formaldehyde, and Colored Pellets. www.entrepreneurindia.co Thermosetting and thermoplastic resins respectively fall under two broad industrial categories. Thermosetting resins fall under the surface coating branch of the chemicals industry. Thermoplastic resins fall under plastic and plastic- based products. The surface coating chemicals branch includes the manufacture of paint, adhesives, printing ink, and specialty resins of the thermosetting type. Synthetic resins required pigments to be grinded, which provides excellent transparency and pigment wetting. The pigment concentrate must be let down with a synthetic resin that will provide the finished ink or coating attributes. www.entrepreneurindia.co These attributes may require a synthetic resin to have water resistance, alkali resistance and solvent resistance, as well as adhesion to the designated substrate. -
Expanded Plastics, Polyurethane, Polyamide and Polyester Fibres
Expanded Plastics, Polyurethane, Polyamide and Polyester Fibres (Polyepoxides and Epoxy Resins, Polyamides and Polyimides, Polyesters, Polyolefins, Polycondensation, Fiber Production, Prepolymer Production, Polyether Polyols with Epoxy Resins, Polyimides, Closed Cell Foamed Films and Sheets, Plastic Deformation, Closed Cell Polyimides) www.entrepreneurindia.co Introduction Expanded plastics are also known as foamed plastics or cellular plastics. Expanded plastics can be flexible, semi flexible, semi rigid or rigid. They can also be thermoplastic or thermosetting and can exist as open celled or closed celled materials. Expanded plastics may be prepared from most synthetic and many natural polymers. Most of the industrially important ones are made from polystyrene, polyvinyl chloride, polyurethanes and polyethylene, as well as from resins that derive from phenol, epoxy, etc. Polyurethane (PUR and PU) is polymer composed of a chain of organic units joined by carbamate (urethane) links. www.entrepreneurindia.co Polyurethane polymers are formed by combining two bi or higher functional monomers. One contains two or more isocyanate functional groups and the other contains two or more hydroxyl groups. More complicated monomers are also used. Polyurethane (PUR and PU) is a polymer composed of organic units joined by carbamate (urethane) links. While most polyurethanes are thermosetting polymers that do not melt when heated, thermoplastic polyurethanes are also available. www.entrepreneurindia.co Polyurethane polymers are traditionally and most commonly formed by reacting a di- or poly-isocyanate with a polyol. Both the isocyanates and polyols used to make polyurethanes contain, on average, two or more functional groups per molecule. A polyamide is a macromolecule with repeating units linked by amide bonds. -
CHAPTER I Introduction 1.1 Thermosets Thermosetting
Ph.D. Thesis Savitribai Phule Rune University CHAPTER I Introduction 1.1 Thermosets Thermosetting polymers/resins are pre-polymers in a soft solid or viscous liquid state. They change irreversibly into an infusible, insoluble three dimensional polymer network of covalent bonds as a result of a chemical reaction taking place in presence of a curing agent/hardener. The resultant structure is known as a thermosetting plastic or thermoset. They can be heated and shaped only once. If re-heated they cannot soften as polymer chains are interlinked. Thus, these polymers are synthesized as a final material of desired shape (polymerization and final shaping is done in the same process or mould is the true chemical reactor). They offer high thermal stability, good rigidity, hardness, and resistance to creep [1]. A good solvent can swell the thermoset but cannot dissolve it. Thermosets are usually amorphous (crosslinks inhibit the movement of polymer chains to pack or crystallize and restrict ordering of network structure) in nature. Thermosets do often exhibit high glass transition temperatures. Their glass transition temperature is higher than the temperature at which they are used (Tuse), therefore, they behave as glasses during their use [2]. The main thermosetting resins are epoxy, melamine formaldehyde, polyester, polyurethane and urea formaldehyde. Thermosets find applications where thermoplasfics cannot compete because of their properties and cost. When fire resistance is required, phenolics are the first choice. Urea formaldehyde is the material used as an adhesive for wood. Melamine formaldehyde is an excellent quality and low cost material used for furniture coating. Polyester resin is used to make fiber reinforced structural parts and epoxy resins constitute a very important class of thermosets used in aeronautical applications. -
Plastic Any of Numerous Synthetic Materials That Consist of Giant Molecules Called Polymers, with Extremely Long Chains of Repea
Plastic Any of numerous synthetic materials that consist of giant molecules called polymers, with extremely long chains of repeating units derived from short molecules. Plastics can be formed into products by molding or otherwise shaping. A significant property of most plastics is that they soften when heated, so that they can be formed into shapes, then become rigid on cooling. This property derives from their physical structure, which consists of a network of polymers, the constituent units of which separate under heat sufficiently to slide apart, but on cooling become firmly entangled again. The first plastic developed was celluloid, consisting of nitrocellulose softened by vegetable oils and camphor, patented in 1870 by an American printer, John W. Hyatt. The first completely synthetic plastic was Bakelite, produced from phenol and formaldehyde by Leo Baekeland in 1909. Advances in basic understanding of molecular physics facilitated the subsequent development of nylon, polyethylene, and other plastics. All plastics are manufactured by some method of polymerization, the process of forming the long chains and networks of molecules. The two major divisions of plastics are the thermosetting resins and thermoplastic resins. Thermosetting resins become insoluble and infusible on heating. Among thermosetting resins are the phenolic resins, furan resins, aminoplastics, alkyds and polyesters of unsaturated acids, epoxy resins, polyurethanes, and silicones. Thermoplastic resins, which can be melted and solidified repeatedly, unlike thermosetting resins, include cellulose derivatives, addition polymers (polyethylene, polypropylene, vinyls, acrylics, fluorocarbon resins, and polystyrenes), and condensation polymers (nylons, polyethylene terephthalate, polycarbonates, and polyamides). Other types of resins include oil-soluble or modified resins, plastics such as casein and lignin extracted from natural products, and special-application synthetics such as resins used as adhesives and as additives to paper and textiles. -
Packaging Specifications
Number: 010-101136-01 ENGINEERING STANDARD Revision: 2 Original 12/20/2006 Date: Subject: Packaging Labeling and Page: 1 of 29 Design for Environment Guidelines Original Tracy Zhou Approved by: ECO Process Prepared by: Updated by: Ardy Chan – June 29, 2009 Approved by: ECO Process Table of Contents 1. INTRODUCTION ......................................................................................................................... 3 1.1. Abstract .............................................................................................................................. 3 1.2. Purpose .............................................................................................................................. 3 1.3. Scope .................................................................................................................................. 4 1.4. Regulatory References for Global Compliance ................................ ............................... 4 2. RESPONSIBILITY OF PACKAGING SUPPLIER ................................ ....................................... 6 3. PACKAGING MATERIAL SELECTION ...................................................................................... 8 3.1. Reduction of Non-recyclable Content .............................................................................. 8 3.2. Use of Recycled Cellulosic Materials ............................................................................... 8 3.2.1. Guideline for Recycled Fiber Content ...................................................................... -
Crystic Composites Handbook | Scott Bader
Composites Handbook Performance Resins in Composites 50 years of reliability, experience and innovation. The Crystic family of resins is at the heart of our success. In 1946 Scott Bader were the first UK company to manufacture unsaturated polyester resins in Europe. In 1953 the Crystic range of polyesters was introduced and its revolutionary applications have meant that Crystic has been the byword for superior technological achievement ever since. CONTENTS Introduction Plastics The nature of reinforced plastics Materials Resins Unsaturated polyesters - DCPD polyesters - Epoxies - Vinyl esters - Phenolics - Hybrids Reinforcements Glass fibre - Carbon fibre - Polyaramid fibre - Glass combinations - Hybrid combinations Speciality materials Catalysts MEKP’s - CHP’s - AAP’s - BPO’s - TBPO’s & TBPB’s Accelerators Cobalts - Amines Fillers Calcium carbonate - Talc - Metal powders - Silica - Microspheres - Alumina tri-hydrate Pigments Polyester pigment pastes Release Agents Polyvinyl alcohol - Wax - Semi-permanents - Wax/semi- permanent hybrids - Release film - Internal release systems Core materials 2-component polyurethane foam - Polyurethane foam sheet - PVC foam - Polyetheramide foam - Styrene acryilonitrile foam - Balsa wood - Honeycomb cores - Non-woven cores Adhesives Polyesters - Epoxies - Acrylics (methacrylates) - Polyurethanes - Urethane acrylates (Crestomer) Mould making materials Flexible materials - Plaster & clay - Composites Ancillary products Polishing compounds Processes Open mould processes Gelcoating - Laminating - Hand lay-up -
The Ldpe Resin-Casting Method Applied to Vessel
IAWA Journal, Vol. 21 (3), 2000: 347–359 THE LDPE RESIN-CASTING METHOD APPLIED TO VESSEL CHARACTERISATION by Tomoyuki Fujii1 & Yasunori Hatano2 Wood Anatomy Laboratory1 & Adhesion Laboratory2, Forestry and Forest Products Research Institute, Tsukuba Norin P.O. Box 16, Ibaraki 305-8687, Japan SUMMARY Low-density polyethylene (LDPE) was used as a casting medium to study vessel attributes. The LDPE had a low crystallinity and melted around 102 °C. The glass transition point was very low (-20 °C) in com- parison to polystyrene (105 °C). The viscosity decreased exponentially as the temperature was raised. Dry sample blocks of selected hardwoods, fixed in tubes and previ- ously heated, were impregnated with melted LDPE under vacuum or under compression. After the removal of cell-wall materials, the resin casts obtained almost entirely consisted of vessels clearly showing three- dimensional arrangement. These casts were dissected with a thin steel knife for SEM observation. Vessel-casts were usually not accompanied by casts of vasicentric elements. Resin-casts of fibres, tracheids and parenchyma cells were observed only near the surface of the blocks. Cell wall sculpturing such as pits and helical thickenings were observed in detail. The depth of LDPE drawn into vessel lumina depended on the time of evacuation and diameter of vessels. Key words: Resin casting method, LDPE, thermoplastic polymer, SEM, vessel network. INTRODUCTION Vessels are the most important flow path for longitudinal water conduction in the tree trunk and also for the penetration of liquid in wood quality improvement. Vessels may be short to very long and are composed of few to very many vessel elements (Zimmermann 1983). -
Process for Preparing Synthetic Resin Powder Having Improved Blocking Resistance
Europäisches Patentamt *EP000629660B1* (19) European Patent Office Office européen des brevets (11) EP 0 629 660 B1 (12) EUROPEAN PATENT SPECIFICATION (45) Date of publication and mention (51) Int Cl.7: C08L 51/04, C08L 55/02, of the grant of the patent: C08J 3/00 05.09.2001 Bulletin 2001/36 (21) Application number: 94109089.6 (22) Date of filing: 14.06.1994 (54) Process for preparing synthetic resin powder having improved blocking resistance Verfahren zur Herstellung von Kunstharzpulver mit verbesserter Blockierungsfestigkeit Procédé pour la préparation d’une poudre de résine synthétique ayant une résistance au blocage améliorée (84) Designated Contracting States: • Mori, Toshiyuki BE DE ES FR GB IT NL Kobe-shi, Hyogo-ken (JP) • Shimatani, Toshiro (30) Priority: 18.06.1993 JP 14788293 Takasago-shi, Hyogo-ken (JP) • Hasegawa, Toshihiko (43) Date of publication of application: Kako-gun, Hyogo-ken (JP) 21.12.1994 Bulletin 1994/51 (74) Representative: (73) Proprietor: KANEGAFUCHI KAGAKU KOGYO Gille Hrabal Struck Neidlein Prop Roos KABUSHIKI KAISHA Patentanwälte Kita-ku Osaka-shi (JP) Brucknerstrasse 20 40593 Düsseldorf (DE) (72) Inventors: • Takaki, Akira (56) References cited: Koba-shi, Hyogo-ken (JP) EP-A- 0 066 382 EP-A- 0 418 685 EP-A- 0 506 036 Note: Within nine months from the publication of the mention of the grant of the European patent, any person may give notice to the European Patent Office of opposition to the European patent granted. Notice of opposition shall be filed in a written reasoned statement. It shall not be deemed to have been filed until the opposition fee has been paid.