Sustainable Value Report 2014 Contents
Total Page:16
File Type:pdf, Size:1020Kb
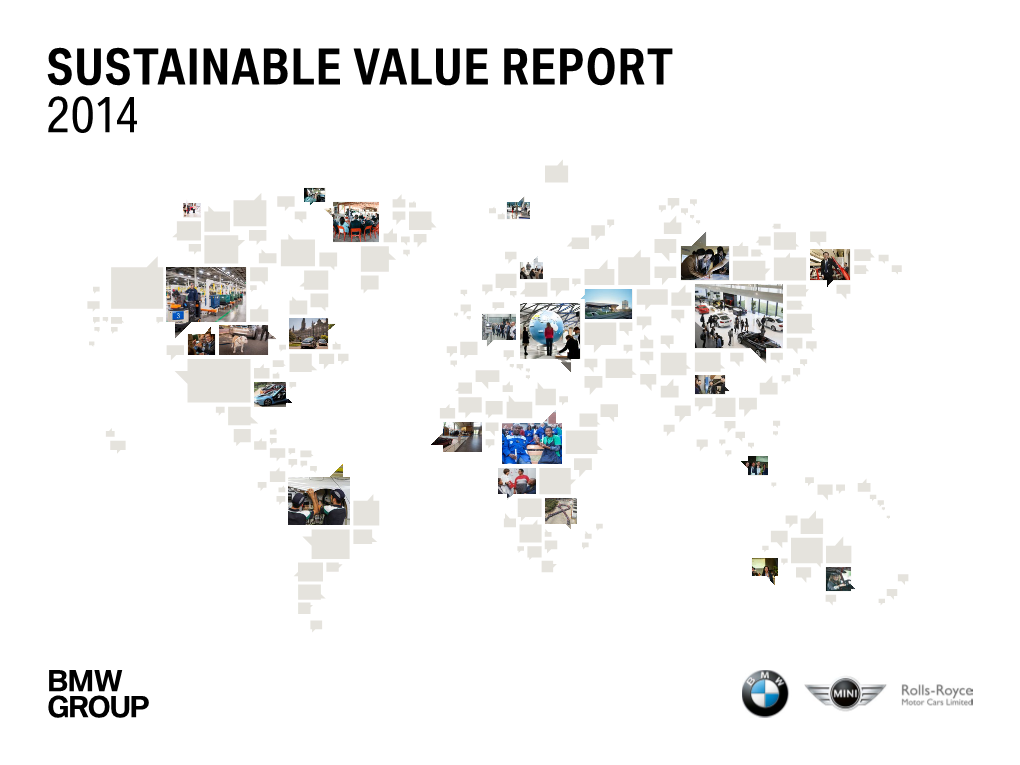
Load more
Recommended publications
-
We Are Shaping the Mobility of the Future, Annual Report 2017
WE ARE SHAPING THE MOBILITY OF THE FUTURE ANNUAL REPORT 2017 The new era of electric mobility requires visionaries and people of action. Find out in our image brochure how BMW Group is shaping the mobility of the future. CONTENTS 1 4 TO OUR SHAREHOLDERS CORPORATE Page 4 BMW Group in Figures GOVERNANCE Page 8 Report of the Supervisory Board Page 198 Statement on Corporate Governance Page 18 Statement of the Chairman of the (Part of the Combined Management Report) Board of Management Page 198 Information on the Company’s Governing Constitution Page 199 Declaration of the Board of Management and of the Page 24 BMW Stock and Capital Markets in 2017 Supervisory Board pursuant to § 161 AktG Page 200 Members of the Board of Management Page 201 Members of the Supervisory Board Page 204 Composition and Work Procedures of the Board of 2 Management of BMW AG and its Committees Page 206 Composition and Work Procedures of the COMBINED Super visory Board of BMW AG and its Committees Page 213 Disclosures pursuant to the Act on Equal MANAGEMENT REPORT Gender Participation Page 214 Information on Corporate Governance Practices Applied Page 30 General Information and Group Profile beyond Mandatory Requirements Page 30 Organisation and Business Model Page 216 Compliance in the BMW Group Page 40 Management System Page 221 Compensation Report Page 44 Report on Economic Position (Part of the Combined Management Report) Page 44 General and Sector-specific Environment Page 239 Responsibility Statement by the Page 48 Overall Assessment by Management Company’s -
Mobility Ecosystems Striving Towards a Seamless Interface for Customers
May 2019 Digital Ecosystems Series Mobility ecosystems striving towards a seamless interface for customers 01 Executive summary 03 Trends reshaping the mobility landscape 08 New mobility business models are emerging 18 Contrasting perspectives on value within mobility ecosystems 25 Building blocks for integrated mobility 28 Implications for re/insurers 44 Conclusion The rapid growth of megacities and conurbations means that societies will need evermore sustainable and resilient mobility solutions to fulfil their potential. Evangelos Avramakis, Head Digital Ecosystems R&D Executive summary Mobility has been at the heart of insurance since merchants pooled their maritime risks in the 14th century. The automobile was the strongest growth engine for insurance in the 20th century, but mobility in the 21st could look very different. Urbanisation, changing demographics and greater environmental consciousness are putting pressure on existing mobility infrastructure. As the world looks for more sustainable means of moving goods and people, we all need to make better and more dynamic use of existing systems, as well as experiment with newer tech-enabled mobility platforms. Executive summary New mobility business models are Highly networked, data-driven mobility business models are emerging, led by a emerging and transforming the way variety of industry participants working closely with technology players. Automakers people and goods get around. have launched mobility services to remain relevant, and a new class of mobility companies are connecting multiple networks through GPS-enabled smart phones. The most advanced companies are simplifying the entire customer journey and have integrated payments across all modes of transportation. Insurers have key roles to play in de-risking Insurers have key roles to play within these new data-centric mobility models. -
Momentum the Volkswagen Group Magazine
momentum The Volkswagen Group magazine NEW BEGINNING A journey into the mobile future momentum New beginning – Journey into the mobile future 3 The Volkswagen Group is transforming itself from one of the largest car manufacturers into a globally leading provider of sustainable mobility. This metamorphosis is already visible in many areas today: new powertrains, strong partnerships for new forms of mobility, and new digital products and services. This issue of momentum brings you stories about people who have set out to drive this change. The journey into the mobile future has begun. 4 Destinations momentum This issue of momentum takes you to places where the Volkswagen Group is working on the future of mobility. The people our authors and photographers met reflect the many answers to one simple question: how will we move in tomorrow’s world? Hong Kong, Midlands, China ― 26 UK ― 32 London, UK ― 42 Mladá Boleslav, Czech Republic ― 80 Stuttgart-Zuffenhausen, Germany ― 70 Sant’Agata Bolognese, Italy ― 78 Bologna, Italy ― 82 Wolfsburg, Germany ― 86 Potsdam, Germany ― 14 Berlin, Germany ― 8, 76 momentum Destinations 5 Södertälje, Barcelona, Sweden Spain ― 48 ― 64 Molsheim, Reykjavík, France ― 52 Munich, Iceland ― 22 Germany ― 84 Bremen, Las Vegas, Germany ― 66 USA ― 38 Oslo, Norway ― 58 6 Contents momentum A question of values ― 8 New demands on mobility On tour with the Crafter ― 22 Anna María Karlsdóttir: through Iceland with the Crafter AILA and me ― 66 Robot lady AILA: real-life machine Symbiosis ― 52 Etienne Salomé, Bugatti: symbiosis between -
Milestones in Future Mobility, Annual Report 2018
ANNUAL REPORT 2018 #Milestones in Future Mobility ANNUAL 2018 ANNUAL REPORT We are inventing the mobility of the future, in which we think and work in new ways. We invite you to learn more about how we see the future today. CONTENTS 1 4 TO OUR SHAREHOLDERS CORPORATE Page 4 BMW Group in Figures GOVERNANCE Page 8 Report of the Supervisory Board Page 200 Statement on Corporate Governance Page 16 Statement of the Chairman of the (Part of the Combined Management Report) Board of Management Page 200 Information on the Company’s Governing Constitution Page 201 Declaration of the Board of Management and of the Page 20 BMW AG Stock and Capital Markets in 2018 Supervisory Board Pursuant to § 161 AktG Page 202 Members of the Board of Management Page 203 Members of the Supervisory Board Page 206 Composition and Work Procedures of the Board of 2 Management of BMW AG and its Committees Page 208 Composition and Work Procedures of the COMBINED Super visory Board of BMW AG and its Committees Page 215 Disclosures Pursuant to the Act on Equal MANAGEMENT REPORT Gender Participation Page 216 Information on Corporate Governance Practices Applied Page 26 General Information and Group Profile beyond Mandatory Requirements Page 26 Organisation and Business Model Page 218 Compliance in the BMW Group Page 36 Management System Page 223 Compensation Report Page 40 Report on Economic Position (Part of the Combined Management Report) Page 40 General and Sector-specific Environment Page 239 Responsibility Statement by the Page 44 Overall Assessment by Management Company’s -
07 2008 2009 2010 2011 2012 2013 2014 2015 2016
Helping you to improve the quality of life in your city. Belgian Workspace Association Congres EARPA Conference October 5th 2017 Christian Lambert – DriveNow Belgium As a continual trend, more and more people keep moving into larger cities, creating densely packed urban agglomerations. Shanghai New York City Mexico City 20m 28m (+40%) 20m 24m (+20%) Moscow Beijing 20m 25m (+25%) 11m 13m (+18%) 16m 23m (+44%) London 8m 9m (+14%) Tokyo 37m 39m (+5%) Los Angeles 13m 16m (+23%) Rio de Janeiro 12m 14m (+17%) New Delhi Sao Paolo 23m 33m (+43%) 20m 23m (+15%) Manila Buenos Aires 12m 16m (+33%) 14m 16m (+14%) 2011 2025 (%-Change) Helping you to improve the quality of life in your city 2 DriveNow Brussels Urban Mobility is Changing Challenges For Cities Global trends Urbanization (Car) Ownership More Congestion Digitalization More Emission Flexibility DriveNow Fully flexible premium carsharing 3 DriveNow Brussels Simplicity is the name of the game! Find It. Drive it. Drop It. 4 DriveNow Brussels Fleet and Business Zone. BMW: i3, 1 Series, 2 Active Tourer Business Area: 60km2 MINI: Cabriolet, Cooper, Clubman Airport: 22 spots 310 cars 5 …which they frequently use for all kinds of trip purposes. Typical use cases include evening trips to bars and restaurants, ... … inner-city business trips, … One Multi Round Uni Ad Hoc Planned Way Modal Trip Modal … trips to and from the airport, … … or transportation of larger goods. Round Uni One Multi Planned Ad Hoc Trip Modal Way Modal Helping you to improve the quality of life in your city 6 DriveNow at a glance. 900,000+ Members in 9 Countries and 13 Cities. -
A Strategic Insight Into Carsharing Market Developments and Dynamics
A Strategic Insight Into Carsharing Market Developments and Dynamics Franck Leveque Vice President Automotive & Transportation Europe September 21 st 2011 Agenda A review of the key urbanisation trends driving the development of new mobility solutions Definition of the current market size (membership & vehicles) and growth expected in Europe An assessment of the various business models and leading organisations Key conclusions and takeaways to drive Car-Sharing adoption 2 The urbanisation and mega trends that will shape tomorrow’s mobility and transportation needs Mega Cities & Mega Vehicle Ownership Regions (Over 50 cities /Sharing Trends (Over 10 by 2025 <10 millions million members of carsharing in inhabitants) Europe and North America by 2016) Integrated Technology Mobility (smooth Developments inter-modality – (Integration - mobile metro, bus, vehicle payment, cloud sharing, etc.) computing, security) New Economic Developments (BRIC Smart and and Next BRIC Sustainable Cities Infrastructure (Over 100 smart cities with developments) state of the art mobility & connectivity) Standardisation & Harmonisation (inter- operability across systems) 3 Top 20 megacities & car ownership trend: Cities in the developing economies expected to see a decline in car ownership for the first time Evolution of Megacities: Top 20 Megacities – Car Ownership Growth (Global), 2009 - 2025 Per capita 2025 Cars per 1000 - Cars per 1000 – Population (Million) (USD) 2009 2025 Tokyo 38.5 46,494 353 340 New York 25.9 67,591 230 220 London 14.4 57,746 400 340 Mexico -
Car Sharing and Carpooling Initiatives UNITED NATIONS ECONOMIC COMMISSION for EUROPE TECHNICAL COOPERATION PROJECT
UNECE Strengthening the capacity of Central Asian countries to develop sustainable urban mobility policy on car sharing and carpooling initiatives UNITED NATIONS UNITED ECONOMIC COMMISSION FOR EUROPE TECHNICAL COOPERATION PROJECT Strengthening the capacity of Central Asian countries to develop sustainable urban mobility policy on car sharing and carpooling initiatives United Nations Geneva, 2020 II STRENGTHENING THE CAPACITY OF CENTRAL ASIAN COUNTRIES TO DEVELOP SUSTAINABLE URBAN MOBILITY POLICY ON CAR SHARING AND CARPOOLING INITIATIVES © 2020 United Nations All rights reserved worldwide Requests to reproduce excerpts or to photocopy, for sales purposes, should be addressed to the Copyright Clearance Center at copyright.com. All other queries on rights and licenses, including subsidiary rights, should be addressed to: United Nations Publications, 405 East 42nd Street, S–09FW001, New York, NY 10017, United States of America. Email: [email protected]; website: https://shop.un.org. The designations employed and the presentation of material on any map in this work do not imply the expression of any opinion whatsoever on the part of the United Nations concerning the legal status of any country, territory, city or area or of its authorities, or concerning the delimitation of its frontiers or boundaries. United Nations publication issued by the United Nations Economic Commission for Europe. ECE/TRANS/302 UNITED NATIONS PUBLICATION Sales No.: E.20.II.E.35 ISBN: 978-92-1-117249-2 eISBN: 978-92-1-005147-7 STRENGTHENING THE CAPACITY OF CENTRAL ASIAN COUNTRIES TO DEVELOP SUSTAINABLE III URBAN MOBILITY POLICY ON CAR SHARING AND CARPOOLING INITIATIVES UNITED NATIONS ECONOMIC COMMISSION FOR EUROPE The United Nations Economic Commission for Europe (UNECE) is one of the five United Nations regional commissions, administered by the Economic and Social Council (ECOSOC). -
Car-Sharing Economics Increased from 3
The De mystification of Car Sharing An in-depth analysis of customer perspective, underlying economics, and secondary effects The Demystification of Car Sharing 1 Key Messages Only a small group of members uses car sharing on a regular basis—the substitution effect between car sharing and private 1 car use is limited. It is primarily seen as a complementary service, at best substituting for public transportation. People still value the inherent advantages of private car ownership, such as permanent availability, privacy, and a feeling 2 of personal freedom, which will make it challenging to increase car sharing’s penetration rate. At the same time, current car-sharing members primarily choose 3 car sharing for economic and convenience reasons, resulting in an economically challenging business model. The lack of major urban agglomerations and the relatively low population density of many major European cities prove to be key limitations to increasing the vehicle usage and financial success 4 of car sharing. In Germany, only 5 percent of the theoretical market can be served in economically viable terms. Recommendations for Action Collaborate closely with city administrators to integrate car sharing in the public transportation network and gain exclusive 1 benefits, such as reserved parking. Select car-sharing cities based on population density, availability 2 of interconnected hot-spot areas, and local government support. Proactively use positive secondary effects of car sharing such as brand image building, customer relationship management, and 3 data collection to balance likely financial losses (especially in the start-up phase). Target potential younger customers through marketing efforts, since they’re more open to alternative value propositions based 4 on vehicle offerings compared to potential older customers. -
Whats Ahead for Car Sharing?
What’s Ahead for Car Sharing? The New Mobility and Its Impact on Vehicle Sales The Boston Consulting Group (BCG) is a global management consulting firm and the world’s leading advisor on business strategy. We partner with clients from the private, public, and not-for- profit sectors in all regions to identify their highest-value opportunities, address their most critical challenges, and transform their enterprises. Our customized approach combines deep in sight into the dynamics of companies and markets with close collaboration at all levels of the client organization. This ensures that our clients achieve sustainable compet itive advantage, build more capable organizations, and secure lasting results. Founded in 1963, BCG is a private company with 82 offices in 46 countries. For more information, please visit bcg.com. What’s Ahead for Car Sharing? The New Mobility and Its Impact on Vehicle Sales Julien Bert, Brian Collie, Marco Gerrits, and Gang Xu February 2016 AT A GLANCE The sharing economy is disrupting markets around the globe, including the market for mobility services. Although car sharing will expand quickly and widely, its effect on new-car sales will be muted, because most drivers will not forgo car ownership entirely and because some share of lost sales will be offset by sales into car-sharing fleets in large urban areas. How the Industry Will Change The trend toward car sharing should nonetheless make automotive OEMs consider reconceiving their mission, at least in part. While continuing to serve as manufac- turers and distributors of personally owned vehicles, OEMs should also experiment with providing mobility services and devise new business models accordingly. -
Business Innovations in the New Mobility Market During the COVID-19 with the Possibility of Open Business Model Innovation
Journal of Open Innovation: Technology, Market, and Complexity Article Business Innovations in the New Mobility Market during the COVID-19 with the Possibility of Open Business Model Innovation Katarzyna Turo´n* and Andrzej Kubik * Department of Road Transport, Faculty of Transport and Aviation Engineering, Silesian University of Technology, 8 Krasinskiego Street, 40-019 Katowice, Poland * Correspondence: [email protected] (K.T.); [email protected] (A.K.) Abstract: The current difficult situation in the world caused by the spread of the COVID-19 virus has led to the development of problems in many branches of the economy. However, it has significantly affected transport, which on the one hand, is the bloodstream of the economy and, on the other hand, creates a threat for virus infection. Thus, in various countries, different mobility-related restrictions during pandemic policies around the world have been introduced. What is more, plans for initiatives after lockdown have also started to appear. Moreover, not have only cities introduced appropriate management policies, but companies have also started providing logistics services, especially those offering new mobility solutions. We found a literature and research gap indicating the recording or combination of the different types of business practices and innovations used worldwide in new mobility companies in the case of a pandemic situation. Therefore, this article is dedicated to the business innovations that appear in the new mobility industry during the COVID-19 pandemic in connection to post-pandemic transportation plans in Asia, Europe, and America. In this work, we conducted two-level research based on the desk research and expert research methodologies. -
Update on the Global Transition to Electric Vehicles Through 2019
BRIEFING © 2020 INTERNATIONAL COUNCIL ON CLEAN TRANSPORTATION JULY 2020 Update on the global transition to electric vehicles through 2019 Prepared by Hongyang Cui, Dale Hall, and Nic Lutsey Many national and local governments around the world motivated to achieve climate, air quality, and industrial growth objectives have announced bold vehicle electrification goals. Many of the governments are turning those goals into action by implementing policies to overcome the prevailing barriers and accelerate electric vehicle uptake. This briefing provides an update on market and policy developments through the end of 2019 related to the global transition to electric vehicles. It provides a summary of vehicle electrification goals set by major markets globally, actions adopted to achieve those goals, and progress toward those goals. Data and supporting actions are summarized, including where enforceable regulations are in place. The briefing focuses primarily on passenger electric vehicles (EVs), including battery electric vehicle (BEV) and plug-in hybrid electric vehicles (PHEV) technologies, where there has been the most market and policy progress. Where related policies and market data are available, associated heavy-duty vehicle and fuel cell vehicle (FCV) information are also included. VEHICLE ELECTRIFICATION TARGETS Table 1 provides a list of vehicle electrification targets announced by national governments. Most goals focus on light-duty vehicles, especially passenger cars. More than a dozen countries, mostly in Europe, have proposed a timeline to phase out new sales of fossil fuel passenger cars or to only sell zero-emission models by 2050. Among www.theicct.org them, Norway has the most ambitious target, aiming to achieve a 100% electric vehicle share of new passenger vehicle and light-duty van sales by 2025. -
Size & Economics of Public Transport Worldwide
14 centrespread centrespread 15 DECEMBER 13-19, 2015 DECEMBER 13-19, 2015 Current addition to GDP from making public World’s Longest Metro transport more efficient* Projected addition Networks in 2014 to GDP in 2030 from Length (km) GETTING AROUND A CITY $119 billion making public transport more efficient Shanghai 548 Public transport is the lifeline of any big city, be it New York, London, Paris or Mumbai. Some have considerably more effi cient *Includes 35 commercially important cities on six modes of mobility than others, as is evident from the data below. Moreover, smaller cities like Copenhagen and Stockholm are continents, including Mumbai and New Delhi $238 billion Beijing 527 Source: Credo Consultancy ahead of the rest in pushing their citizens to use mass transit systems (and also cycling) rather than private vehicles. ET Magazine London 436 brings together different rankings which give you a snapshot of the size and economics of public transport worldwide: Seoul 423 :: G Seetharaman New York 394 Tokyo 381 Urban Mobility Urban Transit Price Index Index 2014*: Moscow 327 Top Performers PUBLIC TRANSPORT TAXI UBER Madrid 293 Score/100 Cheapest Cities Cheapest Cities Cheapest Cities Guangzhou 241 Hong Kong 58.2 (in $) (in $) (in $) Mexico City 226 Stockholm 57.4 New Delhi 0.22 Mumbai 2.32 Jakarta 3.77 Amsterdam 57.2 Jakarta 0.23 New Delhi 2.62 Mumbai 4.35 Copenhagen 56.4 Beijing 0.28 Bangkok 2.72 New Delhi 4.4 Vienna 56 Mumbai 0.3 Jakarta 3.57 Ho Chi Minh City 5.03 Singapore 55.6 Ho Chi Minh City Kuala Lumpur Kuala Lumpur Paris 55.4