SPECIFICATION Description of the Works (Particular Specification) General Technical Requirement
Total Page:16
File Type:pdf, Size:1020Kb
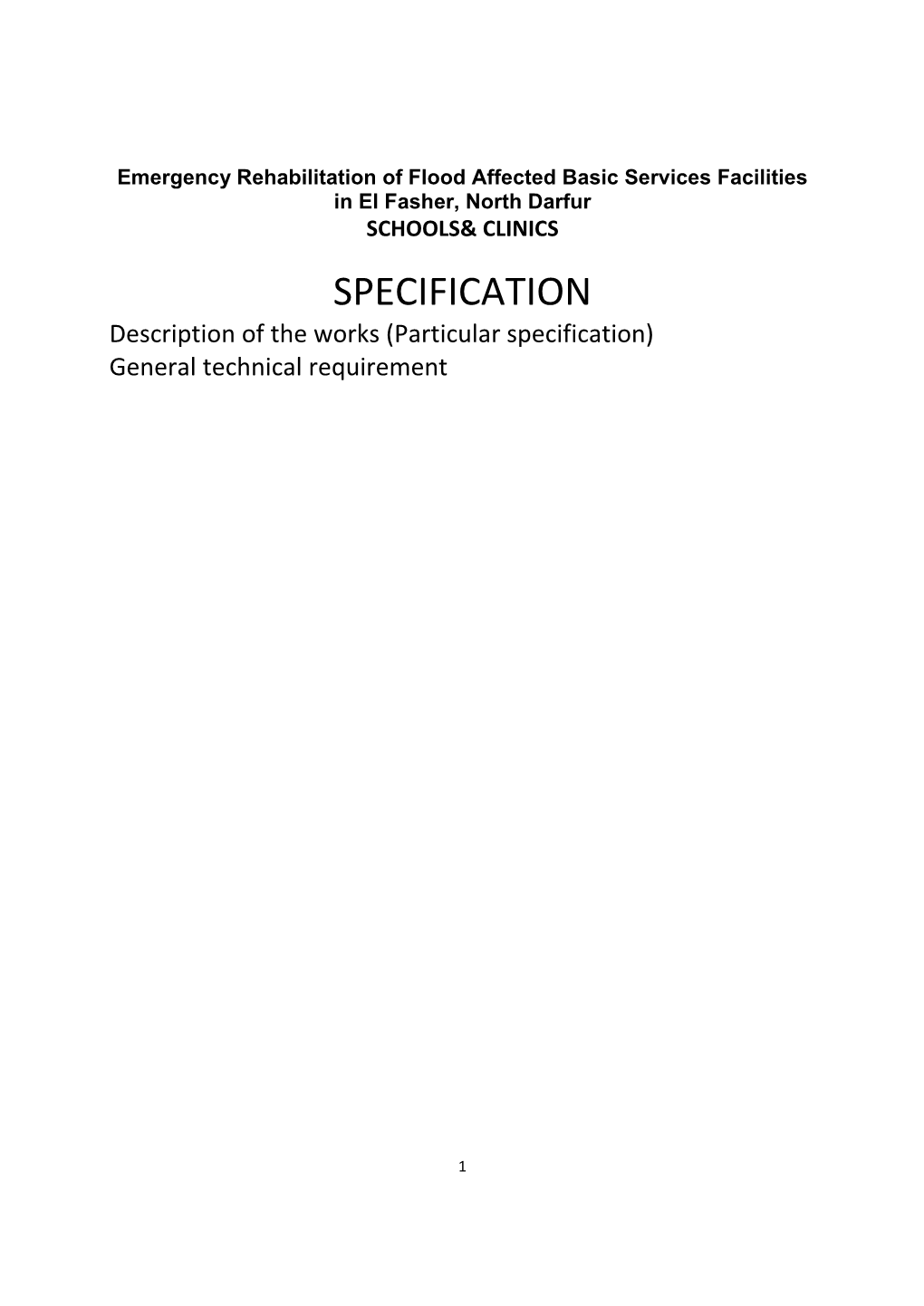
Load more
Recommended publications
-
3.4 Stone Masonry
Table of contents 3.0 Introduction 5 3.1 Excavating and backfilling for foundations 6 3.1.1 Excavating and preparing foundations 7 3.1.2 Backfilling foundations 10 3.2 Building foundations 12 3.2.1 Defining the size and type of foundations 12 3.2.2 General rules for the construction of foundations 14 3.3 Brick and block masonry works 16 3.3.1 Wall and bond types 16 3.3.2 Preparatory activities for brick masonry works 17 3.3.3 Materials for brick masonry works 18 3.3.4 Bricklaying 21 3.3.5 Pointing for brick masonry 28 3.4 Stone masonry 30 3.4.1 Wall and masonry types 30 3.4.2 Preparatory activities for stone masonry works 31 3.4.3 Material for stone masonry works 32 3.4.4 Laying stone 35 3.4.5 Pointing for stone masonry 39 3.5 Installing doors, windows, lintels and ventilators 41 3.5.1 Installing frames for doors and windows 41 3.5.2 Constructing lintels and sunshades 43 3.5.3 Installation of ventilators 43 3.6 Plastering 46 3.7 IPS flooring 49 Learning Unit 3 Masonry works 3.0 Introduction The purpose of this Learning Unit is to: enable a rural mason to build various masonry structures using brick, block or stone and fix ready-to-install doors, windows and ventilators. By the end of this Learning Unit the rural mason should be able to: (i) Manage excavation works for foundations, (ii) Construct foundations for rural houses, (iii) Perform brick masonry for construction of foundations, footings, load bearing and non-load bearing walls, columns, and including plinths and DPC, (iv) Perform rubble stone masonry for construction of foundation walls, including plinths and DPC, (v) Fix ready-to-install doors, windows, lintels and ventilators, (vi) Carry out pointing and plastering of wall surfaces, and (vii) Lay IPS floor slabs. -
The Art of Stone Masonry in the Rockbridge County Area (1700 to Present)
The Art of Stone Masonry In the Rockbridge County Area (1700 to present) Steven Connett Archaeology 377 5/25/83 Dr. McDaniel The art of stone masonry in the Shenandoah valley seems to be somewhat of a mystery prior to the nineteenth century. However, as some of us have learned from the anthropology 101 course: The absence of artifacts (documents in this case) is just as important as the presence of artifacts. In order to make sure that the lack of information was not due to my possible incompetence in research, I spoke with a current day stone masoner named Alvis Reynolds. Mr. Reynolds relayed t o me that when he was trying to learn the skills of stone masonry he, too, had great difficulty in obtaining information and thus decided to teach himself this art through the process of trial and error. Although this information did not directly aid me in my research, Mr. Reynolds did provide me with a bit of information that allowed me to derive a hypothesis on why there is this unusual lack of information in this line of study. I will state my hypothesis in this paper, however, I will not be able to prove it or disprove it due to the deficiency in available information. Mr. Reynolds explained to me that in the eighteenth century there were nomadic stone masoners. These nomadic workers went from valley to valley in search of people who needed help with building their houses. Since these people did not know how to cut stone themselves (after all, stone cutting is not the type of thing that is innate to most people) they had no choice but to p~y these men for their services or go unsheltered. -
HOUSING REPORT Rubble-Stone Masonry House
World Housing Encyclopedia an Encyclopedia of Housing Construction in Seismically Active Areas of the World an initiative of Earthquake Engineering Research Institute (EERI) and International Association for Earthquake Engineering (IAEE) HOUSING REPORT Rubble-stone masonry house Report # 58 Report Date 05-06-2002 Country SLOVENIA Housing Type Stone Masonry House Housing Sub-Type Stone Masonry House : Rubble stone without/with mud/lime/cement mortar Author(s) Marjana Lutman, Miha Tomazevic Reviewer(s) Svetlana N. Brzev Important This encyclopedia contains information contributed by various earthquake engineering professionals around the world. All opinions, findings, conclusions & recommendations expressed herein are those of the various participants, and do not necessarily reflect the views of the Earthquake Engineering Research Institute, the International Association for Earthquake Engineering, the Engineering Information Foundation, John A. Martin & Associates, Inc. or the participants' organizations. Summary Rubble-stone masonry houses are still found throughout Slovenia. This housing type with its special history represents a typical, older residential building in the northwestern part of Slovenia. After their destruction during World War I, these houses were rebuilt, mostly with the recycled stone material from demolished buildings. Many houses of this type were subsequently damaged during the last two earthquakes in Slovenia (1976 Friuli and 1998 Bovec). In order to preserve the country's architectural heritage, about 66% of these houses were strengthened following these earthquakes. http://www.world-housing.net/whereport1view.php?id=100025 1. General Information Buildings of this construction type can be found in the area of Upper Posocje. The residential housing stock built before the World War II in that area is generally of this type. -
A Short Text-Book on Masonry Construction, In- Cluding Descriptions of the Materials Used, Their Preparation and Arrangement in Structures
WORKS OF PROF. M. A. HOWE PUBLISHED BY JOHN WILEY & SONS, Inc. Masonry. A short Text-book on Masonry Construction, in- cluding Descriptions of the Materials Used, their Preparation and Arrangement in Structures. 8vo, ix +160 pages. 115 figures. Cloth, $1.50 net. Foundations. A short Text-book on Ordinary Foundations, including a brief Description of the Methods Used for Difficurt Foundations. 8vo, vii + 110 pages. 56 figures. Cloth, $1.25 net. Influence Diagrams for the Determination of Maximum Moments in Trusses and Beams 8vo, vii+65 pages, 42 figures. Cloth, $1.25 net. The Design of Simple Roof=trusses in Wood and Steel. With an Introduction to the Elements of Graphic Statics. Third edition, revised and enlarged. 8vo, vi+173 pages, 124 figures and 3 folding plates. Cloth, $1.80 net. Retaining-walls for Earth. Including the theory of Earth-pressure as Devel- oped from the Ellipse of Stress. With a Short Treatise on Foundations. Illustrated with Ex- amples from Practice. Sixth edition, revised and enlarged. 12mo, xv +194 pages, 110 figures. Cloth, $1.25 net. A Treatise on Arches. Designed for the use of Engineers and Students in Technical Schools. Second edition, revised and enlarged. 8vo, xxv +369 pages, 74 figures. Cloth, $4.00 net. Symmetrical Masonry Arches. Including Natural Stone, Plain concrete and Rein- forced concrete arches, for the use of Technical Schools, Engineers and Computers .in Designing Arches according to the Elastic Theory. Second edition, revised and enlarged. 8vo, xxiv -r245 pages. Profusely illustrated with figures in the text and folding plates. Cloth, $2.50 net. -
To: Panel [email protected] From: Katty Law Date: 11/09/2014 11
CB(1)2000/13-14(01) To: [email protected] From: Katty Law Date: 11/09/2014 11:38AM Subject: Objection to the proposed pumping station at the Flagstaff House Monument, Hong Kong Park (See attached file: Flagstaff house paper.pdf) (See attached file: Flagstaff House Paper Appendices.pdf) (See attached file: photo2.jpg) (See attached file: photo7.jpg) (See attached file: photo8.jpg) (See attached file: photo29.jpg) (PLEASE CIRCULATE TO ALL MEMBERS OF THE DEVELOPMENT PANEL) Legislative Councillors Members of the Panel on Development Legislative Council Hong Kong Dear Councillors, On behalf of the Central & Western Concern Group and Heritage Watch, I would like to bring to your attention the serious threat posed to the Flagstaff House monument at Hong Kong Park by the proposed repositioning of the Harcourt Road Freshwater pumping station. Our consultant conservation architect Mr Ken Borthwick has written a detailed assessment of this proposed scheme and the paper is attached herewith for your consideration. In his assessment (which closely examines aspects of WSD's HIA) Mr Borthwick looks at the original positioning of Flagstaff House on the crest of the slope, as well as at what he assesses to be its original grounds based on historical plans and early pictures of Flagstaff House in the HIA. He has made an assessment of an historic, rubble stone, fortified defensive wall with loopholes for firing through, which he opines may be the earliest example of British military fortification surviving in Hong Kong and a vital piece of historic evidence. WSD's HIA totally fails to identify this feature for what it is, nor assess its historical and cultural importance. -
Streatham and Streatham Hill Conservation Area Statement
Streatham High Road and Streatham Hill conservation area statement Location 1The Streatham High Road & Streatham Hill Conservation Area is in the southern part of the London Borough of Lambeth. The Conservation Area stretches from Telford Avenue to the Streatham United Reform Church encompassing buildings on Streatham Hill (not including those already within the Leigham Court Estate CA31) and those that line the length of Streatham High Road. The Conservation Area includes the impressive length of commercial and purpose built residential apartment blocks dating from the late Victorian, Edwardian and inter-war eras and includes the Free Tate Library, the Police Station, St. Leonard’s Church, the Odeon and ABC Cinemas and other public buildings, which form an important centre for shopping, recreation and commerce. Origins of development and settlement Streatham High Road is one of London’s major arterial roads. From Roman times, and perhaps earlier, it has been an important highway running between London and the 2Weald. Traces of pre Christian burials were discovered when St. Leonard’s was rebuilt in the 19th century and demonstrate that this was a burial place over 2000 years ago. Also discovered were Roman masonry, coins and a Roman ditch. It is probably that the Romans built a military station on the site of St. Leonard’s consisting of a small fort enclosing 2 or three acres surrounded by an earthwork and a ditch. The derivation of the name “Streatham” being from the Saxon “Strat” Street and “Ham” Settlement. Streatham probably evolved as scattered settlements of Saxon farms along the two Roman roads, which ran through the area. -
STONE MASONRY in CLAY MORTAR with GABION BANDS
RUBBLE STONE MASONRY IN MUD MORTAR with “GABION BANDS” [submittal by Conservationtech Consulting] STONE MASONRY IN CLAY MORTAR with GABION BANDS Submittal Randolph Langenbach Conservationtech Consulting Oakland, Ca. 94618, USA. +1-510-428-2252 www.conservationtech.com www.traditional-is-modern.net/Nepal.html TYPE OF HOUSE: SCALE: DATE: Nepal Housing GABION BAND submitted proposal None 26/11/2015 26 November, 2015 Reconstruction Programme DRAWING TITLE : DESIGNED BY: 1 Randolph Langenbach (USA) 1 RUBBLE STONE MASONRY IN MUD MORTAR with “GABION BANDS” [submittal by Conservationtech Consulting] GABION BANDS Alternative to timber bands for masonry in mud mortar A report submitted to the Nepal DUDBC by Randolph Langenbach, Conservationtech Consulting, www.conservationtech.com This proposal is not for a single house type, but is rather a simple modification of what is already permitted in the Nepal National Building Code (NBC) in response to following criteria: First, the geography of Nepal makes access to industrially produced heavy construction materials such as concrete and steel prohibitively expensive and difficult or impossible to deliver to many of the rural mountainside sites in the country. Second, there is a profound need to provide a technology for the safe reconstruction of owner-built rubble stone houses that is not dependent on high quality timber in areas where timber has been depleted or is too costly for many families to afford. The system proposed here, which has been invented and named “Gabion Bands” by Randolph Langenbach of Conservationtech Consulting, is intended to be an alternative means to meet the provisions of the National Building Code, but with a substitution of wire mesh (or polypropylene geogrid mesh) instead of the timber or reinforced concrete that are shown in the NBC for bands (ring beams) in the masonry walls of code compliant buildings. -
Gabion Wall–A Cost Effective Solution
Journal of Basic and Applied Engineering Research p-ISSN: 2350-0077; e-ISSN: 2350-0255; Volume 3, Issue 3; January-March, 2016, pp. 290-292 © Krishi Sanskriti Publications http://www.krishisanskriti.org/Publication.html Gabion Wall–A Cost Effective Solution Radha Joshi Graduate Member IStructE, MWH E-mail: [email protected] Abstract—Gabion walls are in the industry since many years now. Efficiency in gabion structures, rather than decreasing with However the use of Gabion walls in the Indian market has not gained age, actually increases. During early periods of use, silt and as much popularity as in the foreign countries. Gabions are useful vegetation will collect with the rock fill to form a naturally not only due to their aesthetic appearance but the cost consideration permanent structure and may be used to remove solid of this wall is also an important aspect that has to be considered pollutants or "floatables" from the water. while choosing the type of wall for construction. India being a developing country, infrastructure development cost is In India now with the growing challenges to the construction a major issue. The reduction of cost in any infrastructural element industry, engineers are putting forward the option of Gabion along with increased construction speed is very valuable. From a wall and we will talk about the two projects where the Gabion general market survey, I have observed that the difference between the construction cost of RCC and gabion wall of medium height (1 to wall is implemented as solution and cost comparison. 4m) is around 40%. Many of the private builders have taken this option very seriously and implemented also. -
Table of Contents
Planning and Development Department General Technical Specifications Government of AJ&K Version-2014 TABLE OF CONTENTS 12. STONE MASONRY 12-1 12.A SCOPE 12-1 12.0 RANDOM RUBBLE STONE MASONRY 12-1 12.1 MATERIAL 12-1 12.1.1 STONE 12-1 12.1.2 SIZE OF STONES 12-2 12.1.3 DRESSING 12-2 12.1.4 MORTAR 12-2 12.1.5 LAYING 12-2 12.1.6 BOND STONES 12-3 12.1.7 QUOIN AND JAMB STONES 12-3 12.1.8 JOINTS 12-3 12.1.9 SCAFFOLDING 12-4 12.1.10 CURING 12-4 12.1.11 PROTECTION 12-4 12.2 UNCOURSED & COURSED RUBBLE MASONRY 12-4 12.2.1 GENERAL 12-4 12.2.2 UNCOURSED RUBBLE MASONRY 12-4 12.2.3 COURSED RUBBLE MASONRY 12-4 12.2.4 DRY RUBBLE MASONRY 12-5 12.3 PLAIN ASHLAR MASONRY 12-6 12.3.1 SIZE OF STONE 12-6 12.3.2 DRESSING 12-6 12.3.3 MORTAR 12-6 12.3.4 LAYING 12-6 12.3.5 BOND STONES 12-7 12.3.6 JOINTS 12-7 12.3.7 POINTING 12-7 12.3.8 CURING 12-7 12.3.9 PROTECTIONS 12-7 12.3.10 SCAFFOLDING 12-7 12.4 PUNCHED ASHLAR (ORDINARY) MASONRY 12-7 12.4.1 STONE 12-7 12.4.2 SIZE OF STONE 12-7 12.4.3 DRESSING 12-8 Planning and Development Department General Technical Specifications Government of AJ&K Version-2014 12.4.4 OTHER DETAILS 12-8 12.5 MOULDED, SINK, CARVED ASHLAR MASONRY 12-8 12.5.1 STONE 12-8 12.5.2 DRESSING 12-8 12.5.3 SAMPLE 12-8 12.5.4 OTHER DETAILS 12-8 12.5.5 CENTERING AND SHUTTERING 12-8 12.6 SHELVES, COPING, PLAIN, CORNICES, STRING COURSES ETC. -
Stone Masonry
STONE MASONRY Definition: The art of building a structure in stone with any suitable masonry is called stone masonry. Types of Stone Masonry: Stone masonry may be broadly classified into the following two types: 1. Rubble Masonry 2. Ashlar Masonry 1. Rubble Masonry: The stone masonry in which either undressed or roughly dressed stone are laid in a suitable mortar is called rubble masonry. In this masonry the joints are not of uniform thickness. Rubble masonry is further sub-divided into the following three types: Random rubble masonry Squared rubble masonry Dry rubble masonry 1. Random rubble masonry: The rubble masonry in which either undressed or hammer dressed stones are used is called random rubble masonry. Further random rubble masonry is also divided into the following three types: a. Un coursed random rubble masonry: The random rubble masonry in which stones are laid without forming courses is known as un coursed random rubble masonry. This is the roughest and cheapest type of masonry and is of varying appearance. The stones used in this masonry are of different sizes and shapes. before lying, all projecting corners of stones are slightly knocked off. Vertical joints are not plumbed, joints are filled and flushed. Large stones are used at corners and at jambs to increase their strength. Once "through stone" is used for every square meter of the face area for joining faces and backing. Suitability: Used for construction of walls of low height in case of ordinary buildings. b. Coursed random rubble masonry: The random rubble masonry in which stones are laid in layers of equal height is called random rubble masonry. -
Heritage at Risk Register 2014, East of England
2014 HERITAGE AT RISK 2014 / EAST OF ENGLAND Contents Heritage at Risk III Norfolk Broads (NP) 48 North Norfolk 48 Norwich 54 The Register VII South Norfolk 56 Content and criteria VII Peterborough, City of (UA) 59 Criteria for inclusion on the Register VIII Southend-on-Sea (UA) 63 Reducing the risks X Suffolk 64 Key statistics XIII Babergh 64 Publications and guidance XIV Forest Heath 65 Ipswich 66 Key to the entries XVI Mid Suffolk 66 Entries on the Register by local planning XVIII St Edmundsbury 68 authority Suffolk Coastal 71 Waveney 75 Bedford (UA) 1 Thurrock (UA) 76 Cambridgeshire 2 Cambridge 2 East Cambridgeshire 3 Fenland 6 Huntingdonshire 7 South Cambridgeshire 10 Central Bedfordshire (UA) 15 Essex 17 Braintree 17 Brentwood 18 Chelmsford 19 Colchester 20 Epping Forest 21 Harlow 23 Maldon 23 Tendring 24 Uttlesford 27 Hertfordshire 28 Broxbourne 28 Dacorum 29 East Hertfordshire 29 North Hertfordshire 30 St Albans 33 Stevenage 33 Three Rivers 33 Watford 33 Welwyn Hatfield 34 Luton (UA) 34 Norfolk 35 Breckland 35 Broadland 40 Great Yarmouth 42 King's Lynn and West Norfolk 44 II EAST OF ENGLAND Heritage at Risk is our campaign to save listed buildings and important historic sites, places and landmarks from neglect or decay. At its heart is the Heritage at Risk Register, an online database containing details of each site known to be at risk. It is analysed and updated annually and this leaflet summarises the results. Over the past year we have focused much of our effort on assessing listed Places of Worship, and visiting those considered to be in poor or very bad condition as a result of local reports. -
Stone and Brick Masonary
Sagar Institute of Science and Technology Gandhi Nagar Bhopal, 462036 Approved by AICTE, New Delhi & Govt. of M.P. Affiliated to RGPV & BU, Bhopal Tel: 7024368999, 9977995985|www.sistecgn.ac.in CONSTRUCTION OF SUPER STRUCTURE STONE AND ITS MAJOR TYPES BASED ON FORMATION • Building stone is a natural engineering material. • Stone is obtained from rock by applying certain disintegration techniques like manual quarrying and blasting etc. • Stones obtained from rocks are irregular in shape and size and thus need proper dressing before using for construction purpose. Based on formation of the parent rock it has three types 1. Igneous rock formed by the solidification of molten lava such as volcanic activity For example: Granite 2. Sedimentary formed from silt, marine life, and rocks that have been deposited by running water For example: Limestone, Sandstone 3. Metamorphic igneous or sedimentary rock that have been changed by pressure, heat, or moisture For example: Marble, Slate The stone masonry and its uses • Stone blocks laid with cement or lime mortar in a systematic manner forming a structural mass which can resist load without disintegration is called stone masonry. • Stone masonry is used for the construction of walls, foundation, columns, lintels, arches and other components of structures. • If abundantly available it can serve as an economical building material keeping in view the dressing cost and time of construction. • Undressed or rounded shape stone masonry with insufficient mortar is disastrous in earthquake hazard areas like Balakot, Abbottabad etc. Classification of stone masonry • Masonry can be classified according to the thickness of joints, continuity of courses and finish of face.