University of Oklahoma Graduate College
Total Page:16
File Type:pdf, Size:1020Kb
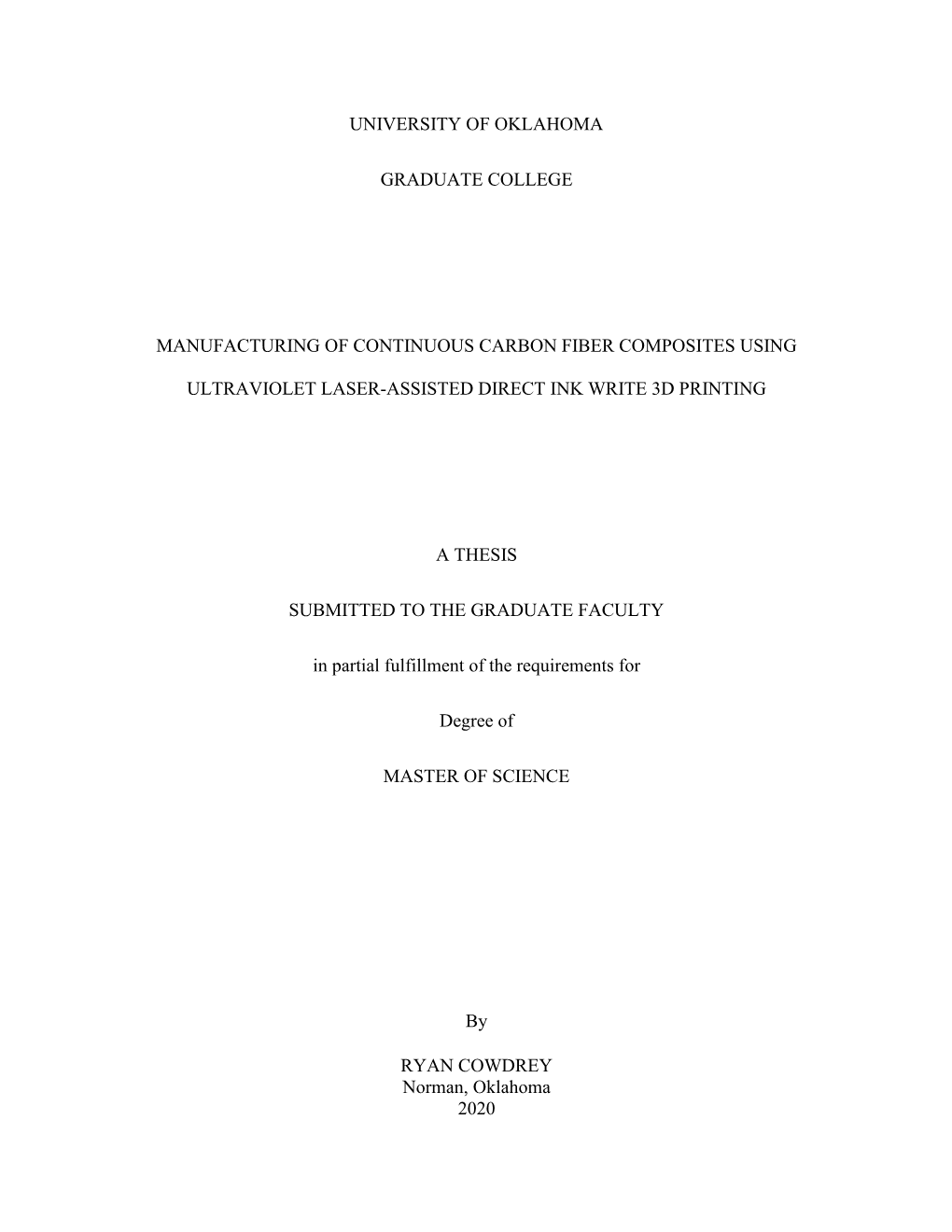
Load more
Recommended publications
-
Additive Manufacturing Lead Contractor of the PP5 – RDA Pilsen Deliverable: Authors: PP5 – RDA Contractual Delivery 31.01.2022 Date
WPT3 D.T3.2.10 Virtual demonstration centre – Additive Version 1 manufacturing 03/2021 Project information Project Index Number: CE1519 Project Acronym: CHAIN REACTIONS Project Title: Driving smart industrial growth through value chain innovation Website: https://www.interreg-central.eu/Content.Node/CHAIN-REACTIONS.html Start Date of the Pro- 01.04.2019 ject: Duration: 36 Months Document Control page DT3.2.10 – Joint implementation report for the pilot in the advanced manu- Deliverable Title: facturing sector – virtual demonstration centre – additive manufacturing Lead Contractor of the PP5 – RDA Pilsen Deliverable: Authors: PP5 – RDA Contractual Delivery 31.01.2022 Date: Actual Delivery Date: 25.03.2021 Page I Table of content 1 Introduction ......................................................................................... 1 2 Division of 3D printing technologies ............................................................. 1 2.1 Selective Laser Sintering – SLS ............................................................................................... 1 2.2 Selective laser melting - SLM ................................................................................................. 2 2.3 Stereolithography - SLA ......................................................................................................... 2 2.4 Fused deposition Modelling - FDM ....................................................................................... 3 2.5 Electronic beam melting - EBM ............................................................................................ -
The Application of Additive Manufacturing / 3D Printing in Ergonomic Aspects of Product Design: a Systematic Review
Applied Ergonomics 97 (2021) 103528 Contents lists available at ScienceDirect Applied Ergonomics journal homepage: www.elsevier.com/locate/apergo Review article The application of additive manufacturing / 3D printing in ergonomic aspects of product design: A systematic review Tjaˇsa Kermavnar a, Alice Shannon b, Leonard W. O’Sullivan a,* a School of Design, Confirm Smart Manufacturing Centre and Health Research Institute, University of Limerick, Limerick, Ireland b School of Design, University of Limerick, Limerick, Ireland ARTICLE INFO ABSTRACT Keywords: Additive Manufacturing (AM) facilitates product personalization and iterative design, which makes it an ideal 3D printing technology for ergonomic product development. In this study, a systematic review was conducted of the liter Additive manufacturing ature regarding the use of AM in ergonomic-product design, and methodological aspects of the studies were Ergonomics analyzed. A literature search was performed using the keywords “3D print*,” “additive manufacturing,” “ergo Human factors nomic*” and “human factors”. Included were studies reporting the use of AM specificallyin ergonomic design of products/prototypes including the detailing of an ergonomic testing methodology used for evaluation. Forty studies were identified pertaining to the fields of medicine, assistive technology, wearable technology, hand tools, testing devices and others. The most commonly used technology was fused deposition modeling with polylactic acid, but the overall preferred material was acrylonitrile butadiene styrene. Various combinations of objective/subjective and qualitative/quantitative product evaluation methods were used. Based on the findings, recommendations were developed to facilitate the choice of most suitable AM technologies and materials for specific applications in ergonomics. 1. Introduction modifications based on user evaluations of prototypes. -
Design of a Machine for Manufacture of Elements Using Additive Manufacturing Technology
Principles of diploma at the Faculty of Mechanical Engineering, TUL POLITECHNIKA ŁÓDZKA WYDZIAŁ MECHANICZNY Instytut obrabiarek i Technologii budowy maszyn Nicolás Montilla 903077 ENGINEERING WORK in the field of Mechanical Engineering Erasmus scholarship TOPIC Design of a machine for manufacture of elements using Additive Manufacturing technology Work manager: Dr inż. Piotr Zgórniak ŁÓDŹ, 2020 Nicolás Montilla Díaz Łódź 2020 ENGINEERING WORK in the field of Mechanical Engineering Erasmus scholarship TOPIC Design of a machine for manufacture of elements using Additive Manufacturing technology 1 Nicolás Montilla Díaz Łódź 2020 General Index List of abbreviations 4 1. Introduction 5 2. State of the Art 5 2.1 Stereolithography (SLA) 6 2.2 Selective Laser Sintering (SLS) 7 2.3 Binder Jetting (BJ) 7 2.4 Fused Deposition Modeling (FDM) 8 3. 3D Printers review 11 3.1 Remarkable designs for 3D printers 11 3.1.1 Ultimaker 11 3.1.2 MakerBot 12 3.1.3 Prusa 13 3.1.4 Zortrax 14 3.2 Printers Specifications 15 3.3 Design requirements 16 3.3.1 Print dimensions 16 3.3.2 Structural design 16 3.3.3 Resolution 17 3.3.4 Handling and control 17 3.3.5 Control electronics 17 3.3.6 Control programs 17 4. Solution Analysis 18 4.1 Structure 18 4.1.1 Support structure 18 4.1.2 Base 19 4.2 Mechanics 20 4.2.1 Motors 20 4.2.2 Guides 20 4.2.3 Extruder 21 4.2.4 Pulleys and spindles 22 4.3 Electronics 23 5. Final results 26 6. -
Desktop Firearms: Emergent Small Arms Craft Production Technologies
ARES Research Report No. 8 Desktop Firearms: Emergent Small Arms Craft Production Technologies G. Hays & Ivan T. March 2020 with N.R. Jenzen-Jones COPYRIGHT NOTICE Published in Australia by Armament Research Services (ARES). © Armament Research Services Pty. Ltd. Published in March 2020. All rights reserved. No part of this publication may be reproduced, stored in a retrieval system, or transmitted, in any form or by any means, without the prior permission in writing of Armament Research Services, or as expressly permitted by law, or under terms agreed with the appropriate reprographics rights organisation. Enquiries concerning reproduction outside the scope of the above should be sent to the Publications Manager, Armament Research Services: [email protected] ISBN 978-0-6485267-5-9 2 Credits Authors: G. Hays & Ivan T. with N.R. Jenzen-Jones Editor: N.R. Jenzen-Jones Technical reviewers: Jonathan Ferguson & Bruce Koffler Layout & Design: Justin Baird Bibliographic Information Hays, G. & Ivan T. with N.R. Jenzen-Jones. 2020. Desktop Firearms: Emergent Small Arms Craft production Technologies. Perth: Armament Research Services (ARES). DESKTOP FIREARMS About the Authors G. Hays G. Hays is a firearms researcher with a specific interest in improvised and craft-produced weapons. He has documented hundreds of different designs and examined methods of manufacture, design influences, and user types. He has produced original research for ARES and other organizations, mostly focusing on the design, development, and employment of improvised and craft-produced small arms and light weapons. Together with N.R. Jenzen-Jones he authored one of the foundational works on craft-produced weapons, Beyond State Control: Improvised and Craft-produced Small Arms and Light Weapons, published by the Small Arms Survey in 2018. -
Opportunities and Scope of Desktop 3D Printers in India
International Journal of Engineering and Advanced Technology (IJEAT) ISSN: 2249 – 8958, Volume-8 Issue-6, August 2019 Opportunities and Scope of Desktop 3D Printers in India Vishwa Poswal, Ram Dayal, Ravi Kant Gupta in many fields of engineering and industry such as aircraft, Abstract. AM is an advanced manufacturing technology used dental restorations, medical implants, automotive products, for fabricating parts in layers, from a CAD file. Various methods construction and prototyping [3]. With the reduced cost and and materials have been developed to cater to its expanding size of 3D printers in the recent-past, the category of personal applications. AM has seen tremendous growth in the recent past. While growth in the technical aspect is essential for the or desktop 3D printers was introduced. Personal or low-cost development of new techniques, growth in the economic aspect desktop 3D printers are those AM machines which have a unit provides the need of innovation. With its ever-increasing cost of less than $5,000 [4]. Personal 3D printers are chiefly industrial and personal applications, the 3D printing technology based on FDM, as complex geometrical parts can be produced has experienced advancements in both the aspects. Yet its full safely in an office-friendly environment using thermoplastics potential has not been harnessed in developing countries. In this [5]. Hence, the range of its applications were expanded to work, it is proposed to optimize the existing desktop 3D printers for developing countries. A market survey was conducted to homes, schools, offices, libraries and laboratories. recognise the lagging areas and the design modifications were When compared to industrial 3D printers, the market made accordingly to produce a compact, efficient and segment of personal 3D printers is recent, yet, it has achieved cost-effective personal 3D printer for the respective needs and an average annual growth rate of about 170% from 2008 to applications in developing countries. -
The Pennsylvania State University Schreyer Honors College
THE PENNSYLVANIA STATE UNIVERSITY SCHREYER HONORS COLLEGE DEPARTMENT OF MECHANICAL ENGINEERING 3D Printing of Barium Titanate Using the Direct Ink Writing (DIW) Technique KARIM BARSOM SPRING 2021 A thesis submitted in partial fulfillment of the requirements for a baccalaureate degree in Mechanical Engineering with honors in Mechanical Engineering Reviewed and approved* by the following: Zoubeida Ounaies Professor of Mechanical Engineering Thesis Co-supervisor Amrita Basak Assistant Professor of Mechanical Engineering Thesis Co-supervisor Bo Cheng Associate Professor of Mechanical Engineering Honors Adviser * Electronic approvals are on file i ABSTRACT Barium titanate (BaTiO3) is a smart ceramic known for its piezoelectric and ferroelectric properties. 3D printing, also known as additive manufacturing, of BaTiO3 has crucial applications across the medical, robotics, and electronics industries. 3D printing allows engineers to consider innovative designs with increasingly complex geometries which can lead to innovations that are unimaginable today. The development of a process that produces ceramic parts with 3D printing can also enhance the reliability and reduce the cost of manufacturing small-scale electronic components. The Direct Ink Writing (DIW) process was selected for its relatively low cost of entry, ease of use, and for its use of ceramic pastes and slurries similar to those used traditionally in tape casting and slip casting ceramic manufacturing methods. To execute the DIW process, I am using a modified off-the-shelf consumer 3D printer. Understanding how the controllable parameters of the DIW process and hardware can affect the quality, precision, speed, and capabilities when printing a BaTiO3 based slurry is the first step towards optimizing the DIW process for prototyping and mass commercial applications. -
Extending Cellulose-Based Polymers Application in Additive Manufacturing Technology: a Review of Recent Approaches
polymers Review Extending Cellulose-Based Polymers Application in Additive Manufacturing Technology: A Review of Recent Approaches Denesh Mohan 1,2 , Zee Khai Teong 1,2, Afifah Nabilah Bakir 1,2, Mohd Shaiful Sajab 1,2,* and Hatika Kaco 3 1 Research Center for Sustainable Process Technology (CESPRO), Faculty of Engineering and Built Environment, Universiti Kebangsaan Malaysia, Bangi 43600, Selangor, Malaysia; [email protected] (D.M.); [email protected] (Z.K.T.); afi[email protected] (A.N.B.) 2 Department of Chemical and Process Engineering, Faculty of Engineering and Built Environment, Universiti Kebangsaan Malaysia, Bangi 43600, Selangor, Malaysia 3 Kolej GENIUS Insan, Universiti Sains Islam Malaysia, Bandar Baru Nilai, Nilai 71800, Negeri Sembilan, Malaysia; [email protected] * Correspondence: [email protected]; Tel.: +60-3-8921-6425 Received: 17 July 2020; Accepted: 18 August 2020; Published: 20 August 2020 Abstract: The materials for additive manufacturing (AM) technology have grown substantially over the last few years to fulfill industrial needs. Despite that, the use of bio-based composites for improved mechanical properties and biodegradation is still not fully explored. This limits the universal expansion of AM-fabricated products due to the incompatibility of the products made from petroleum-derived resources. The development of naturally-derived polymers for AM materials is promising with the increasing number of studies in recent years owing to their biodegradation and biocompatibility. Cellulose is the most abundant biopolymer that possesses many favorable properties to be incorporated into AM materials, which have been continuously focused on in recent years. This critical review discusses the development of AM technologies and materials, cellulose-based polymers, cellulose-based three-dimensional (3D) printing filaments, liquid deposition modeling of cellulose, and four-dimensional (4D) printing of cellulose-based materials. -
3D Printing 27 August 2019
******** Thematic Research: Technology GDTMT-TR-S222 3D Printing 27 August 2019 Has 3D printing come of age? 3D printing is in its mid-thirties and is now approaching market growth that Inside Chuck Hull could only have dreamt about when he invented it in 1983. Players . Technology briefing By 2025, 3D printing, or additive manufacturing, will be a $32bn industry, rising . Trends to over $60bn by 2030. The compound annual growth rate (CAGR) between . Industry analysis 2018 and 2025 will be 16%, according to GlobalData estimates, with software . Value chain growing slightly faster than hardware, materials and services. Disruptive impact Yet behind the optimism, competition and casualties are increasing: UK . Companies powder maker Metalysis recently went into administration before being . Who’s who in 3DP rescued by Power Resources, a mining company; SLM Solutions, a German . Glossary manufacturer of 3D metal printers, had a poor first half of 2019, selling a third of the machines it sold in the first half of 2018 with revenues down 45%; and Organovo is considering its strategic options after biological performance issues with its 3D-printed liver tissues. 3D printing has always been most closely associated with prototyping and short production runs. But now it is becoming a key part of the manufacturing mix alongside injection molding and computer numerical control machining. The use of polymers – particularly plastics – in 3D printing still exceeds metals, but the gap is narrowing, and metals could outstrip polymers from 2021. Healthcare is a strong adopter, with applications from medical training to the operating table. Great Ormond Street Hospital’s use of 3D printed models for an operation to separate twins joined at the head has increased awareness. -
Increasing 3D Printer Throughput with Automated Part Removal
Increasing 3D Printer Throughput with Automated Part Removal IN PARTIAL FULFILLMENT OF A MAJOR QUALIFYING PROJECT WORCESTER POLYTECHNIC INSTITUTE Submitted by: Nicholas Colucci (ECE) Noah Donald (ECE/ME) Alexander Johnson (ME) Andrew Kacherski (ME) Dante Mauriello (ME) Owen Smallcomb (ME) Project Advisors: Prof. Pradeep Radhakrishnan (ME) Prof. Joseph Stabile (ECE) August 2019 – May 2020 [email protected] This report represents the work of WPI undergraduate students submitted to the faculty as evidence of completion of a degree requirement. WPI routinely publishes these reports on its website without editorial or peer review. For more information about the projects program at WPI, please see http://www.wpi.edu/academics/ugradstudies/project-learning.html Copyright Notice The work presented in this document is copyrighted by students Nicholas Colucci, Noah Donald, Alexander Johnson, Andrew Kacherski, Dante Mauriello, and Owen Smallcomb and Professors Pradeep Radhakrishnan and Joe Stabile (Department of Mechanical Engineering, Worcester Polytechnic Institute). 1 Abstract A 3D printer is a powerful machine that allows for rapid realization of designs. Reducing the downtime between print cycles is essential for use in mass production or when multiple users are using the same printer. Presently, an operator manually removes the print from the machine and starts a new print. This project is an improved system from a previous Major Qualifying Project (MQP) to automate this process and eliminate downtime. The system consists of modular sub-systems, making it compatible with any i3 style printer. In the case of a printer with a removable bed, our system removes parts by lifting the bed from the printer and feeding it through a curved track that causes the bed to bend. -
The Effect of Nozzle Hole Diameter of 3D Printing on Porosity and Tensile
Open Eng. 2020; 10:762–768 Research Article Joko Triyono, Heru Sukanto*, Rizki Mica Saputra, and Dharu Feby Smaradhana The effect of nozzle hole diameter of 3D printing on porosity and tensile strength parts using polylactic acid material https://doi.org/10.1515/eng-2020-0083 part through layer by layer method as piling papers up to Received Jan 07, 2020; accepted Apr 10, 2020 become a rim. The types of AM are laser sintering, fused deposition modelling, stereolithography, etc. The form of Abstract: Nozzle hole diameter of 3D printer (3DP) can materials like powder, filament and liquid materials will be varied to obtain required product quality as well as to be referred to determine the type of AM process [2]. reduce manufacturing times. The use of larger diameter 3D printing (3DP) is one of the fastest developed of may accelerate manufacturing times of products, yet the desktop AM. The principle of this process is creation of a product quality, including the mechanical properties, still product by continuous solidifying of slice by slice molten needs to be investigated profoundly. The purpose of this material (usually a plastic polymer) on a bed after it reach work is to investigate experimentally the effect of nozzle the cooling temperature in each slice or layer [3]. Compar- hole diameter of 3DP to the surface quality, accuracy, and ing to conventional process, 3DP have benefits through the strength of the product. The specimens were manufac- a material waste less and its capability to make a com- tured by fused deposition modelling (FDM) 3D printing us- plex shape product. -
Three-Dimensional Additive Manufacturing Jayasangeetha J
J. Jayasangeetha et al.; International Journal of Advance Research, Ideas and Innovations in Technology ISSN: 2454-132X Impact factor: 6.078 (Volume 6, Issue 2) Available online at: www.ijariit.com Three-dimensional additive manufacturing Jayasangeetha J. Swarna Pragna [email protected] [email protected] Panimalar Institute of Technology, Chennai, Tamil Nadu Panimalar Institute of Technology, Chennai, Tamil Nadu Marlapati G. Pravallika M. Jayashree [email protected] [email protected] Panimalar Institute of Technology, Chennai, Tamil Nadu Panimalar Institute of Technology, Chennai, Tamil Nadu ABSTRACT manufacturing layers of adhesive coated paper,plastic, metal laminates are sucessively joint together and cut to particular The technology we used in this project was once a dream shape using laser cutter.This paper also gives us different dreamt by several people, wondering whether they could bring materials used to create objects,those are, A. Acrylonitrile their imagination into reality. This report gives us detailed Butadiene Styrene, B.Poly Lactic Acid C.High impact information of using a three-dimensional printer to create an polystyrene. object. The method we have used here is FDM (Fused Deposition Modelling). 3. PROPOSED SYSTEM In our project we have used FDM (fused deposition modelling) Keywords⸻ Three-dimensional printer, FDM (Fused technique to create a specific 3d object. As we already know this Deposition Modelling) technique uses a thermoplastic material in which it melts and 1. INTRODUCTION forms layers. First we have to create a 3d model,this Can either We have all known and are much aware of two dimensional be done using Autodesk 3ds Max,or we can download 3d models printers than three-dimensional printers.The difference between Which are available open source. -
SAMG Proposal on Feasibility Study for 3D Printer Project - Peter Gheude 9-9-2017
SAMG proposal on feasibility study for 3D printer project - Peter Gheude 9-9-2017 What is RAMPS ? The Replication Rapid-Prototyper Project (RepRap) is an open source hobbyist “do it yourself” low cost 3D printer project. RepRap Arduino Mega Pololu Shield, or RAMPS for short is a motor controller shield for the Arduino Mega2560. See: http://reprap.org/wiki/RAMPS_1.2 Basic components and considerations when building a 3D Printer. ACME Leadscrews Rods, Belts and Shafts Linear Guides Hot Ends Extruders Heat Beds Filaments Build Volume X, Y and Z Motor drivers Motor Types Cubic Frames Dual Z Axis A key component kit for a 220x220 version can be obtained from various suppliers such as; Note there are latter choices with the RAMPS and Arduino combined. https://www.aliexpress.com/item/3D-Printer-Kit-set-Ramps-1-4-board-12864-LCD-Screen-MK2B- Heatbed-A4988-motor- driver/32769335220.html?smToken=072e46394ee3431f8ce4b89a35422f9c&smSign=1QzGOzizwG p9H%2F%2B04WI3NA%3D%3D Example of an incomplete basic kit for around $50 Example of ACME Lead Screw There are numerous providers of Kit Projects with a multitude of designs and electronic controllers. Cartesian Core xy Delta Laser etch and cutters Printer Types FDM - Fused Deposition Modeling MJ - Material Jetting - Wax Casting DLP - Digital Light Processing SLA - Stereolithography SLS - Selective Laser Sintering SLM - Selective Laser Melting BJ - Binder Jetting LOM - Laminated Object Manufacturing EBM - Electron Beam Melting There is much room for improvement including; Stability