Pre-Feasibility Report
Total Page:16
File Type:pdf, Size:1020Kb
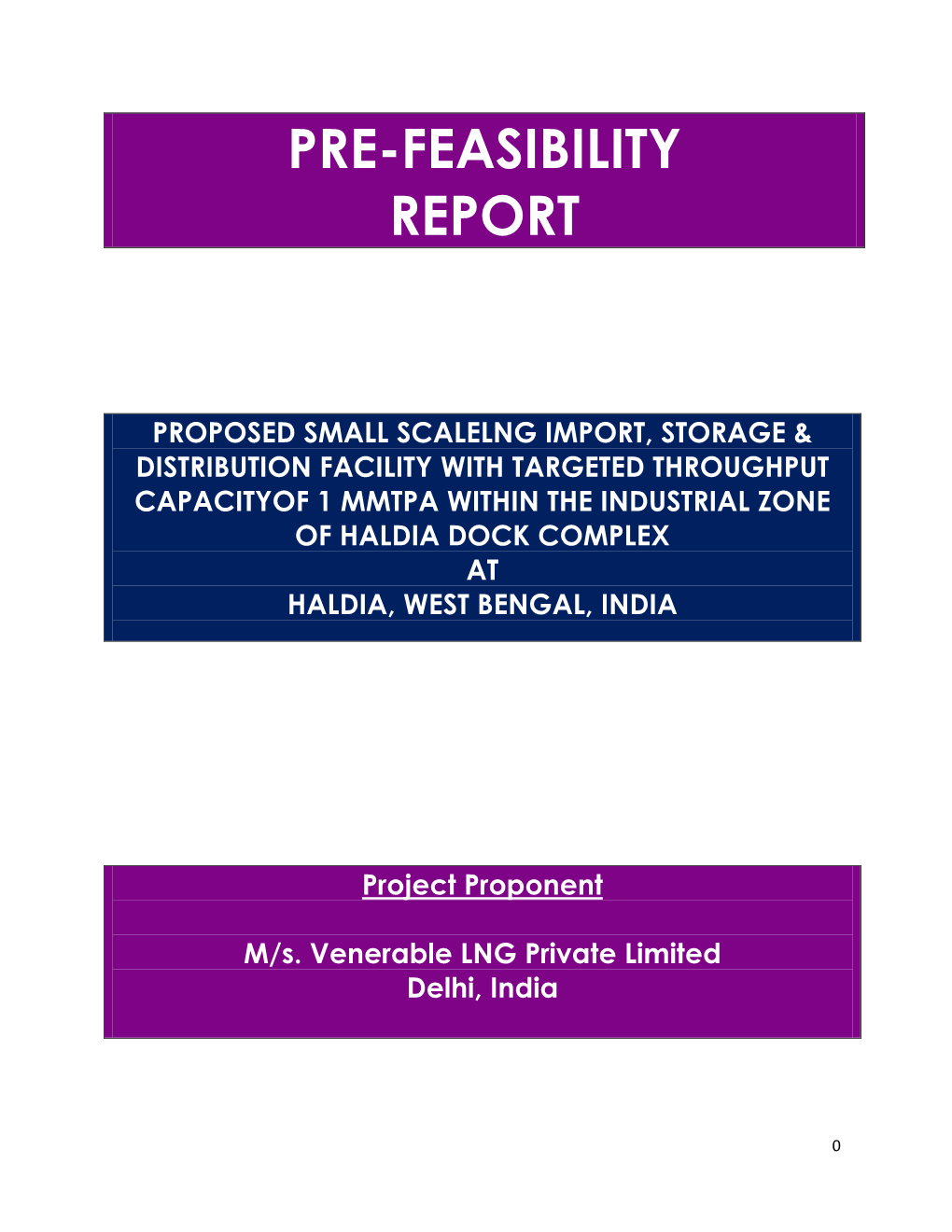
Load more
Recommended publications
-
Kolkata Customs Committed to Excellence
KOLKATA CUSTOMS COMMITTED TO EXCELLENCE KOLKATA CUSTOMS COMMITTED TO EXCELLENCE 2� KOLKATA CUSTOMS u COMMITTED TO EXCELLENCE FOREWORD This is the first Coffee Table Book of Kolkata Customs brought out on the occasion of International Customs Day, 2019. The Coffee Table Book depicts and tells the history and work done by Kolkata Customs at Port, Airport, Land and Marine Divisions in collection of reve- nue, anti-smuggling, countering export/ import offences, trade facilitation and passenger clearance. Kolkata Customs plays a vital role in strengthening eco- nomic security and national security. The Coffee Table Book also informs about future plans and direction of Kolkata Customs. (MANISH CHANDRA) Commissioner of Customs (Port, Airport & Administration) Custom House Kolkata KOLKATA CUSTOMS u COMMITTED TO EXCELLENCE �3� PROJECT COORDINATION 27/B, SIDHPURA INDUSTRIAL ESTATE, NEAR SRL DIAGNOSTICS CENTRE, OFF S. V. ROAD, GOREGAON WEST, MUMBAI - 400062 | TEL: 022-28729291 TITLE KOLKATA CUSTOMS COMMITTED TO EXCELLENCE DESIGNERS VISHWAS MACHIVALE VINAYAK DHURI MARKETING TEAM MK JAIKUMAR 9594987725 [email protected] APURBA CHAKRAVARTHY 9830045650/7980388433 [email protected] PRINTED AT PRINT HOUSE, MUMBAI 4� KOLKATA CUSTOMS u COMMITTED TO EXCELLENCE CONTENTS 06 CHAPTER 1 Organisation 08 CHAPTER 2 Genesis 18 CHAPTER 3 Commissionerate of Customs (Port) 52 CHAPTER 4 Commissionerate of Customs (Airport & Administration) 58 CHAPTER 5 Commissionerate of Customs (Preventive), West Bengal 80 CHAPTER 6 The Future and Next Generation Trade Facilitations 84 CHAPTER 7 Kolkata Customs Club KOLKATA CUSTOMS u COMMITTED TO EXCELLENCE �5� 6� KOLKATA CUSTOMS u COMMITTED TO EXCELLENCE ORGANISATION The Kolkata Customs Zone is headed by a Chief Commissioner. There are three Commissionerates, namely, Kolkata (Port), Kolkata (Airport & Administration) & Commissionerate of Customs (Preventive) or CCP, West Bengal, each having their own jurisdic- tion headed by a Commissioner. -
Along River Ganga
Impact assessment of coal transportation through barges along the National Waterway No.1 (Sagar to Farakka) along River Ganga Project Report ICAR-CENTRAL INLAND FISHERIES RESEARCH INSTITUTE (INDIAN COUNCIL OF AGRICULTURAL RESEARCH) BARRACKPORE, KOLKATA 700120, WEST BENGAL Impact assessment of coal transportation through barges along the National Waterway No.1 (Sagar to Farakka) along River Ganga Project Report Submitted to Inland Waterways Authority of India (Ministry of Shipping, Govt. of India) A 13, Sector 1, Noida 201301, Uttar Pradesh ICAR – Central Inland Fisheries Research Institute (Indian Council of Agricultural Research) Barrackpore, Kolkata – 700120, West Bengal Study Team Scientists from ICAR-CIFRI, Barrackpore Dr. B. K. Das, Director & Principal Investigator Dr. S. Samanta, Principal Scientist & Nodal Officer Dr. V. R. Suresh, Principal Scientist & Head, REF Division Dr. A. K. Sahoo, Scientist Dr. A. Pandit, Principal Scientist Dr. R. K. Manna, Senior Scientist Dr. Mrs. S. Das Sarkar, Scientist Ms. A. Ekka, Scientist Dr. B. P. Mohanty, Principal Scientist & Head, FREM Division Sri Roshith C. M., Scientist Dr. Rohan Kumar Raman, Scientist Technical personnel from ICAR-CIFRI, Barrackpore Mrs. A. Sengupta, Senior Technical Officer Sri A. Roy Chowdhury, Technical Officer Cover design Sri Sujit Choudhury Response to the Query Points of Expert Appraisal Committee POINT NO. 1. Long term, and a minimum period of one year continuous study shall be conducted on the impacts of varying traffic loads on aquatic flora and fauna with particular reference to species composition of different communities, abundance of selective species of indicator value, species richness and diversity and productivity Answered in page no. 7 – 12 (methodology) and 31 – 71 (results) of the report POINT NO.2. -
Multi- Hazard District Disaster Management Plan
DISTRICT DISASTER MANAGEMENT PLAN 2019-20 DISTRICT DISASTER MANAGEMENT SECTION PURBA MEDINIPUR 1 Government of West Bengal Shri Partha Ghosh(WBCS Exe.) Office of the District Magistrate & Collector District Magistrate & Collector Tamralipta,Purba Medinipur,Pin-721236 Tamralipta,Purba Medinipur,Pin-721236 Ph. No.-03228-263329, Fax No.:– 03228–263728 Ph. No.-03228-263098, Fax No.:– 03228–263500 Email address: [email protected] Email address: [email protected] Foreword Purba Medinipur district is situated in the southern part of the state of West Bengal.Total geographical area covered by the district is 4713 sq Km.This district extended from 22031‘ North to 21038‘ North latitude and from 88012‘ East to 87027‘ East longitudes. This District has a Multi-Hazard geographical phenomenon having a large area falls under Bay of Bengal Coastal Zone. Digha,Mandarmoni,Shankarpur and Tajpur are the important tourist spots where a huge numbers of tourists come regularly.To ensure the safety and security of tourist involving all stakeholders is also a challenge of our District. The arrangement of Nulias for 24x7 have been made for safety of tourist.200 Disaster Management volunteers have been trained under ―Aapda Mitra Scheme‖ for eleven(11) Blocks,43 nos Multi-Purpose Cyclone Shelters(PMNRF-15,NCRMP-28) have also been constructed to provide shelter for people and cattle during any emergency need. Basic training for selected volunteers(@10 for each Block and @5 for Each GP) have also been started for strengthening the Disaster Management group at each level.A group of 20 nos of Disaster Management volunteers in our district have also been provided modern divers training at Kalyani. -
Chapter - One: Agriculture and Allied Activities
Chapter - One: Agriculture and Allied Activities I. AGRICULTURE AND ALLIED ACTIVITIES A. Agriculture a) The target fixed by Govt. of India for agricultural growth at 4% for the State of West Bengal which is around 3.5% now. Considering the agro-climatic condition, infrastructure, resources etc. the projected foodgrains production growth rate has been revised and fixed at 4.5% during XIth plan period. Previously the average foodgrains productivity growth was calculated taking into account Xth plan average productivity and XIth plan projected average productivity and which was projected 5.91% i.e. around 6% and production growth was calculated considering the production of 2011-12 (The last year of XIth plan) and present level of production (which was around 160 lakh tonnes) which was around 15%. However, all the data are revised for Xlth plan period and the strategy for achieving new growth rate are sending for consideration along with revised target. The production of foodgrains will be increased due to increase of cropping intensity. b) Discussion on Food Security West Bengal is surplus in production of rice but there are deficits in the production of wheat and pulses. The requirement of foodgrains during 2006-07 was around 168.39 lakh M.T. and the production was 159.75 lakh M.T. The deficit was mainly due to less production of wheat and pulses. Keeping this in mind various state plan and Centrally Sponsored Scheme will be in operation during eleventh plan period. National Food Security Mission has been started across 12 districts of the State to boost up the production of wheat, pulses and rice. -
Field Diary Kolkata-Haldia-Kolaghat Triangle Jithin Sabu Research Associate, CUTS International
Field Diary Kolkata-Haldia-Kolaghat Triangle Jithin Sabu Research Associate, CUTS International About the Field Visit Under the project entitled ‘Enabling a political economy discourse over multimodal connectivity in the BBIN sub-region (M-Connect)’, a team from CUTS International, comprising Jithin Sabu, Srijata Deb and Bijaya Roy, visited Kolkata, Haldia and Kolaghat in West Bengal. The purpose of the visit was to assess and investigate the infrastructure, trade logistics and to do stakeholder consultations for exploring ways and means of encouraging and promoting multimodal connectivity among the BBIN countries. Major observations and experiences of the CUTS’ team during the visit are summarised below. Visited Locations 1 Kolkata Days The CUTS team landed at Netaji Subhash Chandra Bose International airport, Kolkata, for a week-long field visit in the Southern region of West Bengal. It was night when the team reached Kolkata and the visual of the ‘City of Joy’ was very beautiful with all the lights and glow. A view of Kolkata city The accommodation was arranged in a hotel near Ballygunge. It was very close to the famous Victoria Memorial Museum, which is dedicated to the memory of Queen Victoria. The erstwhile capital of British India, Kolkata, is now a large metropolitan city, where one can see the hand-drawn rickshaws and the underground metro hand-in- hand. Both extremities of life are visible in Kolkata, the slums and the multi-floored glass buildings. The wind in Kolkata was revealing its rich heritage of festivals, music, architecture, antiques, soccer matches and a culture that is long associated with the great Hooghly (Bhagirathi) river. -
UNCTAD/LDC/114 2 July 2001 ENGLISH ONLY TRADE AND
UNCTAD/LDC/114 2 July 2001 ENGLISH ONLY TRADE AND DEVELOPMENT BOARD Fifth Meeting of Governmental Experts from Landlocked and Transit Developing Countries and Representatives of Donor Countries and Financial and Development Institutions, New York, 30 July – 3 August 2001 Agenda items of the provisional agenda REVIEW OF PROGRESS IN THE DEVELOPMENT OF TRANSIT TRANSPORT SYSTEMS IN THE INDIA, NEPAL AND BHUTAN SUBREGION Chakra Infrastructure Consultants Pvt Ltd UNCTAD consultants */ */ The views expressed in this study are those of the author and do not necessarily reflect the views of the UNCTAD secretariat or of any official administration. The designations employed, including in the maps, and the presentation of the material do not imply the expression of any opinion whatsoever on the part of the Secretariat of the United Nations concerning the legal status of any country, territory, city or area, or of its authorities, or concerning the delimitation of its frontiers or boundaries. - 2 - CONTENTS Pages Abbreviations..........................................................................................................3 Executive summary.................................................................................................4 A. NEPAL’S EXTERNAL TRADE AND TRANSIT SITUATION ...............6 1. Introduction.................................................................................................6 2. Nepal’s external trade..................................................................................7 3. Treaties with India.....................................................................................10 -
Kolkata Port : Challenges of Geopolitics and Globalisation
KOLKATA PORT : CHALLENGES OF GEOPOLITICS AND GLOBALISATION SUBIR BHAUMIK Much before Calcutta ( now Kolkata) became an ‘Imperial city” , it had ‘docks for repair- ing and fitting ships’ bottoms’ 1. Armenian traders possibly used these docks to trade with ‘China to the East and Persia to the West’ much before Job Charnock set foot on the swampy villages of Kalikata, Sutanuti and Gobindapur to lay the foundation of a port city from where the British went out to create an empire “ at which they looked with in- credulous elation , shot with sharp tinges of doubt, of a village grocer who had inherited a chain of department stores.” 2. The Bhagirathi river on which the Calcutta port came up, has been and remains a huge navigational challenge ,but its location never failed to entice the freebooter and the brave. A Dutch fleet of seven ships even negotiated the channel without pilots (as ships entering Calcutta rarely dare to) in 1759, two years af- ter Plassey in a futile bid to deny the Englishmen the control of the Calcutta port. But the bid failed and after the opening of the Suez Canal in 1869, the importance of the Calcutta port went up several times, both for world trade and for British interests. Muslim League stalwart H.S Suhrawardy , the mastermind of the 1946 Great Calcutta Killings, could not imagine an East Pakistan without Calcutta and pushed for its inclu- sion in the newly created country. India’s current Prime Minister Narendra Modi has now designated Calcutta as the ‘starting point’ of his ‘Act East’ policy for connecting In- dia to South-east and East Asia. -
Disentangling Transit Costs and Time in South Asia
December 2015 Report Disentangling transit costs and time in South Asia Lessons from firms in Bhutan and Nepal importing through Kolkata and Haldia ports Prabir De Shaping policy for development odi.org Acknowledgements This background research paper is an output of a DFID-funded project titled Regional infrastructure for trade facilitation – impact on growth and poverty reduction. We are grateful for support from DFID. However, the views expressed are those of the authors and not necessarily those of DFID or ODI. The team for the overall study is coordinated by Marie-Agnès Jouanjean and Dirk Willem te Velde and involves a range of ODI researchers (including Judith Tyson, Neil Balchin, Linda Calabrese, Alberto Lemma, Andrew Scott and Catherine Simonet) and international experts (including Olivier Cadot, Douglas Brooks, Ben Shepherd and Marie Gachassin) and others. ODI Report ii Table of contents Acknowledgements ii Abbreviations iv 1 Introduction 1 2 Trade and transit agreements and procedures involving Bhutan, India and Nepal 3 2.1 Bhutan–India Agreement 3 2.2 India–Nepal Agreement 3 3 Bhutan and Nepal in comparative context 6 4 Data and methodology 10 5 Barriers affecting trade and transit of imports to Bhutan and Nepal 13 5.1 Onerous documentation and import procedures 13 5.2 Lengthy transaction times at gateway ports and in transit 14 5.3 High costs incurred at gateway ports and in transit 16 5.4 Falling productivity of transporters 19 5.5 Structural inflexibility and lack of competition among transporters 19 5.6 Perceived barriers -
Haldia: Logistics and Its Other(S) Samata Biswas: Draft 3
Haldia: Logistics and its Other(s) Samata Biswas: Draft 3 Haldia: Logistics and its Other(s) What does logistics mean? Oxford English Dictionary attaches the term to military science by relating it to procurement, maintenance and transportation of material, personnel and facilities. Another definition emphasises the concept of coordination of complex operations „involving many people, facilities, or supplies‟ (New Oxford American Dictionary). The most comprehensive definition, however, seems to be the one employed by the Council of Logistics Management, quoted in the logisiticsworld website, one that holds logistics to be “the process of planning, implementing, and controlling the efficient, effective flow and storage of goods, services, and related information from point of origin to point of consumption for the purpose of conforming to customer requirements.” Note that this definition includes inbound, outbound, internal, and external movements. Neilson and Rossiter in their pamphlet, Logistical Worlds: Infrastructure, Software, Labour, as they persuasively argue that logistics is something more than a system of for searching out and connecting diverse firms and labour forces on the basis of cost and other parameters. Logistics also actively produces environments and subjectivities, including those of workers and labour forces, through techniques of measure, coordination and optimisation. That is to say, it is not simply a socio-technical system that adapts to existing economic and material conditions (5). Neilson and Rossiter diverge from the first three definitions crucially by emphasising on logistics as something beyond an impersonal chain or system, and by bringing to focus the possibility of a logistical weltanschauung. Moving beyond an analysis of chains and networks that revolve around services and materials, this definition opens up the scope for human action, subjectivisation and meaning making. -
LOGISTICAL WORLDS INFRASTRUCTURE, SOFTWARE, LABOUR No. 2 Kolkata 7 ‘BUY CHEAP, SELL DEAR’ Brett Neilson & Ned Rossiter
Logistical Worlds Infrastructure, Software, Labour No. 2 Kolkata LOGISTICAL WORLDS INFRASTRUCTURE, SOFTWARE, LABOUR No. 2 Kolkata 7 ‘BUY CHEAP, SELL DEAR’ Brett Neilson & Ned Rossiter 15 KOLKATA PORT: CHALLENGES OF GEOPOLITICS AND GLOBALIZATION Subhir Baumik 23 WAREHOUSE AND TRANSPORT FACILITIES IN THE PORT OF CALCUTTA, 1870–1950 Kaustubh Mani Sengupta 33 SPACE(S) OF CALCULABILITY AND FINANCIALIZATION IN THE KOLKATA PORT Iman Mitra 41 TRADE UNIONS, INFORMALIZATION AND CONTRACT LABOUR IN WEST BENGAL’S DOCKS Immanuel Ness 51 WHO ARE THE PORT WORKERS AND HOW DO WE STUDY THEM? Mithilesh Kumar 57 A LOGISTICAL EARTHQUAKE: BETWEEN KOLKATA AND VALPARAÍSO Elisabeth Simbürger 65 VARIETIES OF PORT LABOUR POLITICS Carolin Philipp 77 HALDIA, A PORT CITY IN INDIA Samata Biswas 83 THE ‘UNTIMELY’ METROPOLIS OF SILIGURI Atig Ghosh 91 RESILIENT HOPE Orit Halpern 101 CONCEPTS 112 COLOPHON 7 ‘BUY CHEAP, SELL DEAR’ Brett Neilson & Ned Rossiter Moving through the Burrabazar district along Kolkata’s Strand the immediate buzz of hustling and trade obscures the crumbling warehouses that line the thoroughfare. According to a popular saying, ‘Everything is available in Burrabazar’. This ethos of ready supply, at least for those who are prepared to haggle (and almost everyone is), comes with an infrastructural and informational layer. ‘Everyone wants to buy cheap and sell dear’, writes Clifford Geertz in a classic article on the bazaar economy from the 1970s. ‘In the bazaar information is poor, scarce, maldistributed, inefficiently communicated, and intensely valued’. What are the material conduits that support this game of information procurement and coveting and what are the historical and political conditions that have allowed it to flourish? That the root-covered warehouses set back from the Strand look like structures straight out of Victorian England provides a clue. -
Riverine Group the Group Overview
Riverine Group The Group Overview: A Business House in its Fourth year with Group companies for distinct businesses well diversified & specialized in complete Value chain of Multi modal movement of bulk cargo by Inland Water Transport (IWT) managed by recognized Industry experts with a team of specialized manpower duly supported by concrete network of Equipment, Infrastructure, Jetties and offices guided by Vision & Values of promising Promoters recognized as Industry icons. Business Overview: The core competence of the Group is in providing Bulk/Project cargo logistics, dredging, 3PL, and Equipment hire for the energy and manufacturing sectors Industry Overview: Logistics today is a high priority sector both nationally & internationally. Direct sourcing of Coal/Coking Coal/Clinker/Ore from the overseas markets and acquiring overseas mine is the latest trend with Power, Steel, Cement, and Ferro industries. With the increased imports the Railways and Roadways are unable to cope up supply with high demand with the volumes growing and increasing draft restriction at Kolkata/Haldia Port to handle the required parcel sizes the IWT sector (Inland Water Transport) become the viable option available to handle the volumes in the short and Long hauls as the major cargo for these is headed to the Land locked North Eastern States. The Group Strategy: o Concentrating in the Eastern and North Eastern Regions of India to supply raw materials to manufacturing plants, Food products etc. o ODC (Over Dimensional Cargo) transportation by IWT o Bulk / Bagged -
Download 322.05 KB
ASIAN DEVELOPMENT BANK TAR:STU 37030 TECHNICAL ASSISTANCE FOR PREPARING THE SUBREGIONAL TRANSPORT CONNECTIVITY PROJECT (INDIA) December 2003 CURRENCY EQUIVALENTS (as of 30 October 2003) Currency Unit – Indian rupee/s (Re/Rs) Re1.00 = $0.022 $1.00 = Rs45.34 ABBREVIATIONS ADB – Asian Development Bank BRO – Border Roads Organization EA – executing agency EIA – environmental impact assessment IPDP – indigenous people’s development plan km – kilometer MORTH – Ministry of Road Transport and Highways RP – resettlement plan PSP – private sector participation SASEC – South Asia Subregional Economic Cooperation SAGQ – South Asia Growth Quadrilateral SGOS – State Government of Sikkim SGOWB – State Government of West Bengal TA – technical assistance NOTES (i) The fiscal year (FY) of the Government ends on 31 March. (ii) In this report, “$” refers to US dollars. This report was prepared by T. Duncan, South Asia Transport and Communications Division. 1 I. INTRODUCTION 1. The Government of India has requested the Asian Development Bank (ADB) for technical assistance (TA) to prepare the Subregional Transport Connectivity Project. The TA is included in the country strategy and program for India. Following the Reconnaissance Mission on 6–14 May 2003, a TA Fact-Finding Mission visited India on 25 July 2003 and held discussions with the Government on the goals, purpose, scope, implementation arrangements, costs, and terms of reference of the TA. 1 II. ISSUES 2. The West Bengal transport corridor is of strategic importance to the economic development of northeast India and the neighboring countries of Bangladesh, Bhutan, and Nepal. The corridor extends from Haldia port off the Bay of Bengal via Kolkata to Shiliguri in the north of West Bengal, and then east along the national east-west corridor as far as the state of Assam.