Tooling System BT Interface Series
Total Page:16
File Type:pdf, Size:1020Kb
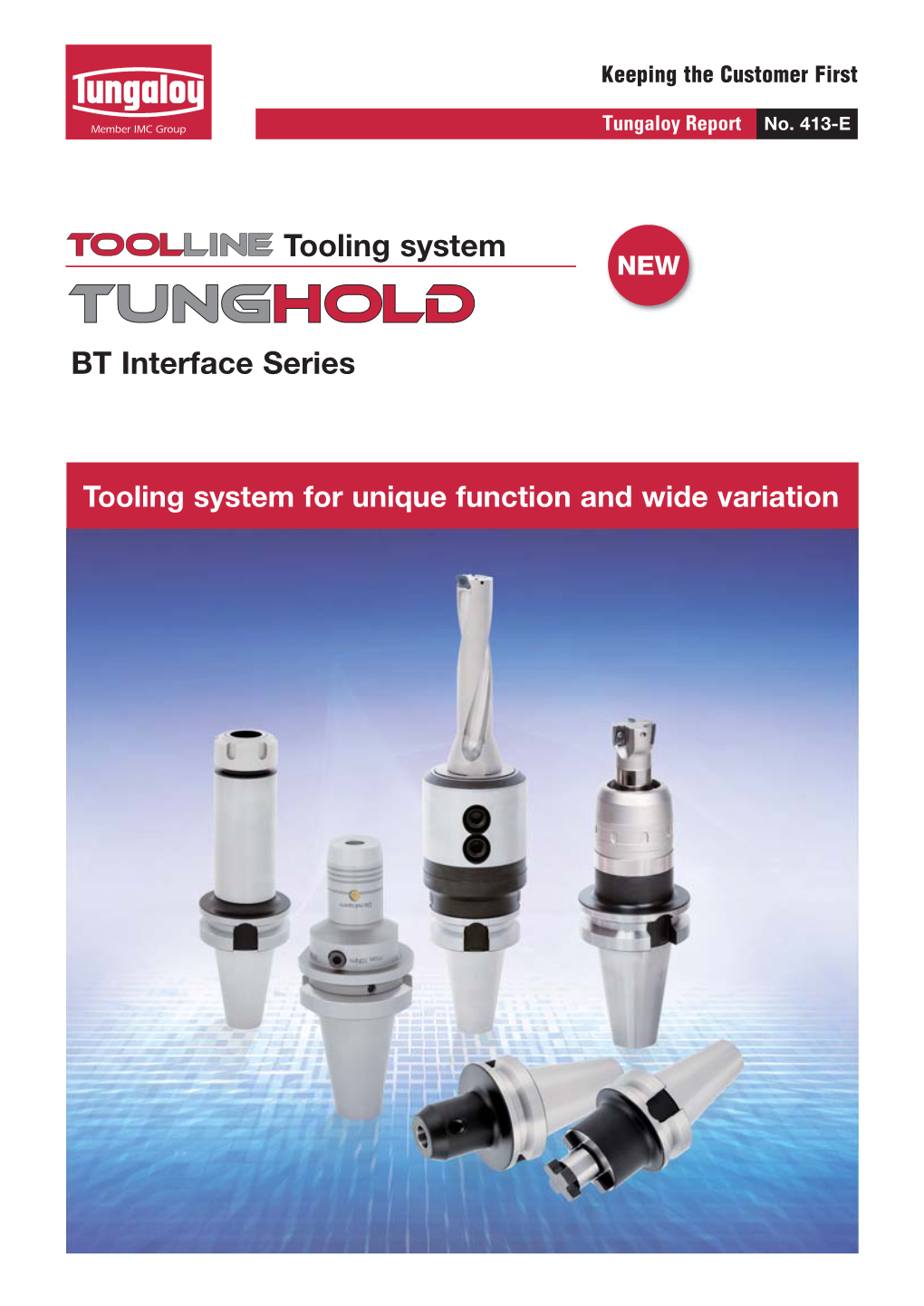
Load more
Recommended publications
-
Success Measured Beyond Tool Life
SUCCESS MEASURED BEYOND TOOL LIFE ENGINEERING CASE STUDIES 04 USING SMARTER TOOL MANAGEMENT FEATURES IN MAKINO A-51NX MILLS Manufacturing Mastery Since 1924 Central Screw Products Company (CSP) is a 3rd generation machin- ing company, founded in 1924. CSP leverages the latest in robot- ics and automation technology to achieve one of the machining industry’s most efficient engineer- ing to production ratios. The re- sult is mastery and control of the manufacturing process, maximum customer value, and unparalleled quality. We machine Titanium, Inconel, and other hard materials to precise tol- erances for the most demanding industries such as defense, medi- cal, aerospace, and automotive. Our global supply chain provides a reliable single source for diverse secondary operations and value added logistics. The Makino brand is universally renowned for high-power, high-speed precision equipment. However, all of this capability comes to a halt without smart tool CSP is ISO 9001:2015 Certified, management. AS 9100 Compliant, ITAR Regis- tered, and a proud recipient of a Central Screw Products use our Makinos to machine demanding superalloys like number of industry and OEM sup- Inconel 718. Using the tool management features built into our Makino, in con- plier quality awards. junction with Haimer holders and OSG drills, our OEE (Overall Equipment Effec- tiveness) has nearly doubled! This increased uptime in our spindles makes DGW www.centralscrewproducts.com a leader in superalloy machining. Read all CSP case studies here The Makino A51NX provides a sophisticated array of tool management features. Subscribe to CSP news For example, we can monitor and replace tools based on time, the number of workpieces, or even active parameters from spindle load monitoring or external broken tool detection. -
Tool Management
TOOL MANAGEMENT www.haimer-usa.com HAIMER TOOL MANAGEMENT LOGISTICS SYSTEM – OVERVIEW Corner module with perforated wall Connection part shrink fit machine Power Clamp Premium Plus Connection part measuring and balancing system Tool Dynamic Preset Waste disposal module Shelf module folders Assembly station Vertical cabinet universal Tool holder rack 2 Workbench assembly module Corner module with rear wall for storing collets and tools Workbench info module Shelf module parts Magazine cabinet Vertical cabinet tool holders 3 TOOL MANAGEMENT – FOR EFFICIENT WORKING Use: The HAIMER Tool Management completes the HAIMER product program as a sys- tem partner around tool clamping. That means HAIMER offers the complete Tool Management equipment from a single source. As a complete solution for tool pre- setting and tool management, the HAIMER Tool Management provides you with functional and ergonomic criteria for the design of work stations. The storage, setup and management of tools is simplified and optimized by the HAIMER solutions so that efficient working is guaranteed. – Modular room design according to the customer's requirements – Shrinking, balancing and presetting already integrated into the concept – Tidy and isolated solution for concentrated working 4 Technical data subject to change without prior notice CORNER MODULE Corner module with perforated wall Use: The perforated back wall and drawer unit provide a clean and structured workspace. The three integrated LED spots ensure a continually bright and comfortable working atmosphere. Delivery includes: – Corner module with a perforated wall, roof with LED lighting, drawer unit Description Order No. Corner module 4.0 84.802.00.3 Technical data subject to change without prior notice 5 WORKBENCH ASSEMBLY MODULE Picture shows: Assembly module with special configuration, Order No. -
Management and Monitoring of Rfidbased Cutting Tool Information
ISSN (Print) : 2319-8613 ISSN (Online) : 0975-4024 Mior Uzair Mior Hassan et al. / International Journal of Engineering and Technology (IJET) Management and Monitoring of RFID- based Cutting Tool Information for Integrated Manufacturing Mior Uzair Mior Hassan#1 , Aini Zuhra Abdul Kadir#2 # Faculty of Mechanical Engineering, Universiti Teknologi Malaysia, UTM Skudai, Johor, Malaysia 1 [email protected] 2 [email protected] Abstract—The demand of integrating manufacturing design and process planning with actual production activities such as cutting tool information is essential to enhance planning efficiency as well as improve simulation accuracy. However, cutting tools information that involves static and dynamic data is difficult to track causing the planning and simulation activities to be isolated, using outdated information and lack of reliability. This paper presents the initial functions of an Integrated Cutting Tool Management and Monitoring system (ICTMMs) utilizing RFID technology. RFID is used as a device to identify individual cutting tool as well as to track cutters data at production floor. Integration is possible with the use of STEP-NC as the exchange data format. User interface is designed using Labwindows. General overview are discussed based on STEP-NC input file. The development of ICTMMs helps to simplify management of cutting tool at production floor and support the integration of tool information throughout the manufacturing chain. Keyword-Tool management, RFID, STEP-NC I. INTRODUCTION Integrated manufacturing environment involves continuous interaction of various computer-aided (CAx) systems functions to ensure full information can be utilized in assisting various manufacturing activities. For example, during production planning activities, cutting tools data is essential for effective machining operation which is normally obtained beforehand based on operator’s experience, catalogues or any theoretical documents. -
End Mill Holders
MASTER TOOLHOLDING CATALOG Toolholding, Tapping, and Boring solutions Toolholding Tapping Boring HISTORY Parlec is established in Rochester N.Y., as a job shop specializing in 1948 the manufacturing of Sulky Hubs. Parlec begins producing and distributing the Numertap and 1973 Autofacer product lines. Parlec expands its product line with the introduction of Toolholders, 1977 which are sold as Numertap and Autofacer accessories. 1980 The first Parsetter TMM® is produced. Parlec builds a new 42,000 square-foot, state-of-the-art 1985 manufacturing facility just outside of Rochester in Fairport, N.Y. Parlec begins to manufacture and distribute its own line of 1992 Boring Tools. Parlec becomes ISO 9001 certified. Parlec’s sales triple from 1997 1992-1997. Parlec further enhances its product line to include Workholding. 1998 Construction of a 58,000 square-foot plant addition begins. Parlec enters the Asian market with the opening of a sales and 2003 service office in Nanjing China. Parlec acquires Bristol Tool. Driven and static tools are added 2004 to Parlec’s extensive product line. A new sales, engineering and distribution facility opens in Bristol, England. Parlec continues to expand its world wide footprint by opening a Wholly Owned Foreign Enterprise in Nanjing. This gives the 2006 company full sales, engineering, customer support and distribution capabilities on 3 continents. Sales offices are opened in Tianjin, Xian, Wuxi, and Chengdu to 2009 expand the China presence. Parlec partners with Gerardi for distribution of Driven & Static 2010 Tooling in Europe. Parlec begins distribution of Right angle heads in China. Parlec successfully completes a $5 million dollar capital investment 2012 campaign to automate and expand its manufacturing capabilities in the United States. -
Life Cycle Oriented Milling Tool Management in Small Scale Production
Available online at www.sciencedirect.com ScienceDirect Procedia CIRP 29 ( 2015 ) 293 – 298 The 22nd CIRP conference on Life Cycle Engineering Life cycle oriented milling tool management in small scale production a b a Dominik Heeschen * Fritz Klocke Kristian Arntz aFraunhofer-Institute for Production Technology (IPT), Steinbachstraße 17, 52074 Aachen, Germany bLaboratory for Machine Tools and Production Engineering (WZL), RWTH Aachen University, Steinbachstrasse 19, 52074 Aachen, Germany * Corresponding author. Tel.: +49-241-8904-324; fax: +49-241-8904-6324. E-mail address: [email protected] Abstract The milling technology is characterized as the most important manufacturing technology in a variety of industries. Moreover, recent developments in hardware and software issues have increased technology’s complexity which is, beyond others, caused by different milling variants and a high number of different milling tools. Milling tools are responsible for a significant cost position in manufacturing driven companies which is shown in the paper by an industry wide survey. Due to the costly and wasteful production it can be shown that this is a significant cost driver. This paper introduces an integrated life cycle oriented approach for the standardization and optimization (including the reuse of tools by standardized repair processes) of milling tools in order to enhance the life cycle of milling tools, reduce overall costs and therefore raise the company’s sustainability. © 20152015 The Authors. Published by Elsevier B.V. This is an open access article under the CC BY-NC-ND license (Peerhttp://creativecommons.org/licenses/by-nc-nd/4.0/-review under responsibility of the International). Scientific Committee of the Conference “22nd CIRP conference on Life Cycle PeerEngineering.-review under responsibility of the scientifi c committee of The 22nd CIRP conference on Life Cycle Engineering Keywords: Life Cycle Management; Life Cycle Optimization; Life Cycle Costing; LCC; Manufacturing; Milling Tools 1. -
Tool Solutions Focus Segments for the Aerospace Industry Our Introdution
Tool solutions Focus segments for the aerospace industry Our introdution OPTIMISED PRODUCTION KYOCERA UNIMERCO Tooling A/S Norms and ECR – your full-service tooling partner – guarantee of identical tools, whether new or RE•NEW® KYOCERA UNIMERCO offers a complete tooling programme for All of our companies utilise integrated CAD/CAM for design and machining aerospace metals and fibre composites. As the choice production. The solution is part of the guarantee of 100% iden- of tool is always based on a cost-benefit assessment, the solution tical design and production. All tools have been designed in ac- often includes standard, customised carbide and diamond tools. cordance with our norms (a norm is an instruction that controls This allows you to get the best total solution from one source, thus the geometry, measurement and manufacturing process). The reducing your supplier base. norms are developed and maintained centrally and subsequently distributed to all companies in KYOCERA UNIMERCO via our High performance tooling solutions central server. To machine a component at the lowest possible costs, you need For this specific purpose, the central programme database the best possible combination of machinery, machining param- secures that all CNC-controlled machines in all our companies use eters and tooling solutions. Therefore, we analyse all aspects of the exact same machining data. All CNC machines are from the the production process involving cutting tools and systematically same manufacturer and are also calibrated to a master machine. optimise them. Subsequently, our tool developers define the opti- Programmes are automatically deleted from each machine imme- mum tooling solution customised to fit your requirements. -
Virtual Cutting Tool Management System for Milling Process
148 IJCSNS International Journal of Computer Science and Network Security, VOL.10 No.2, February 2010 Virtual Cutting Tool Management System for Milling Process Haslina Arshad† , Rosilah Hassan††, Nazlia Omar†† and Shahnorbanun Sahran†, †Department of Industrial Computing, ††Department of Computer Science, Faculty of Information Science and Technology Universiti Kebangsaan Malaysia, Malaysia catalogues. On the other hand, the manual catalogue Summary provided by the manufacturer is limited to single user only Information of cutting tools is very important for the and when more than one user needs to use the catalogue at effectiveness of cutting process. Previously, traditional search the same time the problem will surface. This will be a methods by referring to the catalogues for the right cutting tool waste of time that could delay the whole cutting process has been a burden to the user. As a result, the probabilities of and eventually the lead time of the whole process. Fast choosing the wrong cutting tools were high. In this work, a new and accurate access to information about available cutting tools management system for milling process has been developed for training students before they actually perform the manufacturing resources and data is critical to reducing milling process. With the specific parameters such as cutter type, production cost and maximizing machine productivity [1]. part number, dimension and material types and its properties, the Problems also arise when new cutting tools for milling user can easily get detail information of the cutting tools such as process are introduced to the market. This might take a cutter dimension, insert types and its properties. -
Mastercam Mill Has Been Shop-Tested More Than Any CAM Program in the World
THE FUTURE STARTS HERE MILL LATHE MILL-TURN WIRE ROUTER Mastercam for DESIGN SOLIDWORKS® (L-R) Mark Summers, Chairman; Meghan West, President and CEO; and Brian Summers, Executive Vice President MOVING OUR INDUSTRY FORWARD As the world’s most widely used CAM software, Mastercam has a tremendous community of THE FUTURE IS FAST. users around the globe. It is our intention to leverage that combined energy and intelligence for our mutual benefit. That’s the heart of our new Masters of CAM initiative. We should know. We are helping to shape it. Over the coming weeks, month, and years, we will be collecting stories, tips, tricks, and For Mastercam, speed and efficiency have been driving innovation for years. Dynamic Motion™, innovative solutions from our extended Mastercam community. This input will be available to everyone milling and turning toolpaths, and now Accelerated Finishing™ have put us at the leading edge of efficiency at MastersofCAM.com. and reduced cycle times. By dramatically reducing cycle times while extending tool and machine life, we’ve helped our users to not only stay ahead of the competition, but define the standards of the industry. It takes more than one or two clever ideas to stay competitive these days. So we’ll be collecting as many good ideas as we can. Some ideas will help your shop’s productivity. Some ideas will Today, there is a growing need for collecting, analyzing, and using data across the entire manufacturing inspire creativity. And some ideas may direct our future software development. We know a lot process — often referred to as Industry 4.0. -
ERP-The Dynamics of Supply Chain and Process Management.Pdf
ERP Avraham Shtub • Reuven Karni ERP The Dynamics of Supply Chain and Process Management Second Edition Avraham Shtub Reuven Karni Faculty of Industrial Department of Industrial Engineering & Management Engineering & Management Technion - Israel Institute of Technology Shenkar College of Engineering & Design 32000 Haifa 52526 Ramat Gan Israel Israel [email protected] [email protected] ISBN 978-0-387-74523-7 e-ISBN 978-0-387-74526-8 DOI 10.1007/978-0-387-74526-8 Springer New York Dordrecht Heidelberg London Library of Congress Control Number: 2009933263 © Springer Science+Business Media, LLC 2010 All rights reserved. This work may not be translated or copied in whole or in part without the written permission of the publisher (Springer Science+Business Media, LLC, 233 Spring Street, New York, NY 10013, USA), except for brief excerpts in connection with reviews or scholarly analysis. Use in connection with any form of information storage and retrieval, electronic adaptation, computer software, or by similar or dissimilar methodology now known or hereafter developed is forbidden. The use in this publication of trade names, trademarks, service marks, and similar terms, even if they are not identified as such, is not to be taken as an expression of opinion as to whether or not they are subject to proprietary rights. Printed on acid-free paper Springer is part of Springer Science+Business Media (www.springer.com) We would like to dedicate this book to our loving wives Doreen Karni and Ailona Shtub, to Reuven Karni’s sister, Avis Goldberg and to Avy Shtub’s late brother, Israel Shtub. -
PLM Industry Summary Jillian Hayes, Editor Vol
PLM Industry Summary Jillian Hayes, Editor Vol. 14 No 23 Friday 8 June 2012 Contents Acquisitions _______________________________________________________________________ 3 Autodesk Acquires Vela Systems ___________________________________________________________3 CIMdata News _____________________________________________________________________ 4 CIMdata Publishes “Executing Effectively from Design to Manufacturing” __________________________4 LMS 2012 European Vehicle Conference: CIMdata Commentary _________________________________5 Company News _____________________________________________________________________ 7 Assemble Systems and TotalCAD Systems Partner to Launch BIM Software Integration Platform________7 Bentley Systems Makes $300,000 Commitment to Habitat for Humanity of Chester County for Coatesville, Pa., Housing Project _____________________________________________________________________8 BobCAD-CAM Software Sponsors Massachusetts Highschool Industrial Engineering Program __________9 Cadence Collaborates on 3D-IC Design Infrastructure with TSMC _______________________________10 CadFaster|Collaborate™ Awarded Best of Show Mobile App for Architects at the American Institute of Architects (AIA) National Convention ______________________________________________________11 Cadgroup Australia and CADPRO Systems Join Forces to Increase the Level of Support for Their Autodesk Customers in Australia and New Zealand ___________________________________________________12 CAIPros to Use Geomagic for 3D CAI, Metrology Automation __________________________________13 -
ENTERPRISE RESOURCE PLANNING Copyright © 2011 Y
www.lpude.in DIRECTORATE OF DISTANCE EDUCATION ENTERPRISE RESOURCE PLANNING Copyright © 2011 Y. Venugopala Rao All rights reserved Produced & Printed by EXCEL BOOKS PRIVATE LIMITED A-45, Naraina, Phase-I, New Delhi-110028 for Directorate of Distance Education Lovely Professional University Phagwara Directorate of Distance Education LPU is reaching out to the masses by providing an intellectual learning environment that is academically rich with the most affordable fee structure. Supported by the largest University1 in the country, LPU, the Directorate of Distance Education (DDE) is bridging the gap between education and the education seekers at a fast pace, through the usage of technology which significantly extends the reach and quality of education. DDE aims at making Distance Education a credible and valued mode of learning by providing education without a compromise. DDE is a young and dynamic wing of the University, filled with energy, enthusiasm, compassion and concern. Its team strives hard to meet the demands of the industry, to ensure quality in curriculum, teaching methodology, examination and evaluation system, and to provide the best of student services to its students. DDE is proud of its values, by virtue of which, it ensures to make an impact on the education system and its learners. Through affordable education, online resources and a network of Study Centres, DDE intends to reach the unreached. 1 in terms of no. of students in a single campus SYLLABUS Enterprise Resource Planning Objectives: The objective of ERP is: l To provide the real time information. l To enrich students with concepts and knowledge of ERP. l To prepare them to become knowledgeable ERP user professionals suitable to Industry and Information Technology Companies. -
Tool Management in Manufacturing Systems Equipped with CNC Machines
PRODUCAO Tool Management in Manufacturing Systems Equipped With CNC Machines Giovanni Tani Dipartimento di Meccanica e Tecnologie Industriali - Facolta di Ingegneria Universita di Firenze - Via S. Marta 3 - FIRENZE - ITALIA Key words: Tool file, Tool Card, Automatic Tool Selection ABSTRACT This wolk has been carned out for the purpose ofrealizing an automated system for the integrated management of tools within a company. By integrating planning, inspection and tool-room functions, automated tool management can ensure optimum utilization of tools on the selected machines, guaranteeing their effective availability. The first stage of the wolk consisted of defining and developing a Tool Management System whose central nucleus is a unified Data Base for all of the tools, forming part of the company's Technological Files (files on machines, materials, equipment, methods, etc.), interfaceable with all of the company departments that require information on tools. The system assigns code numbers to the individual components ofthe tools and file them on the basis of their morphological and functional characteristics. The system is also designed to effect assemblies of tools, from which are obtained the "Tool Cards" required for compiling wotking cycles (CAPP), for CAM progranuning and for the Tool-room where the tools are physically prepared Methods for interfacing with suitable systems for the aforesaid functions have also been devised. Belo Horizonte, Vol 7, N" 2, p.177-187 Nov. 1997 177 PRODUCAo 1. Introduction tools are taken from the warehouse, prepared for machining, preset, reground or regenerated. While tool management is a particularly urgent need in FMS Within the sphere of Production installations, it is also becoming Systems, the development of the concept increasingly important in shops that of integration has subsequently led to produce small lots.