Aircraft Design (Cambridge Aerospace)
Total Page:16
File Type:pdf, Size:1020Kb
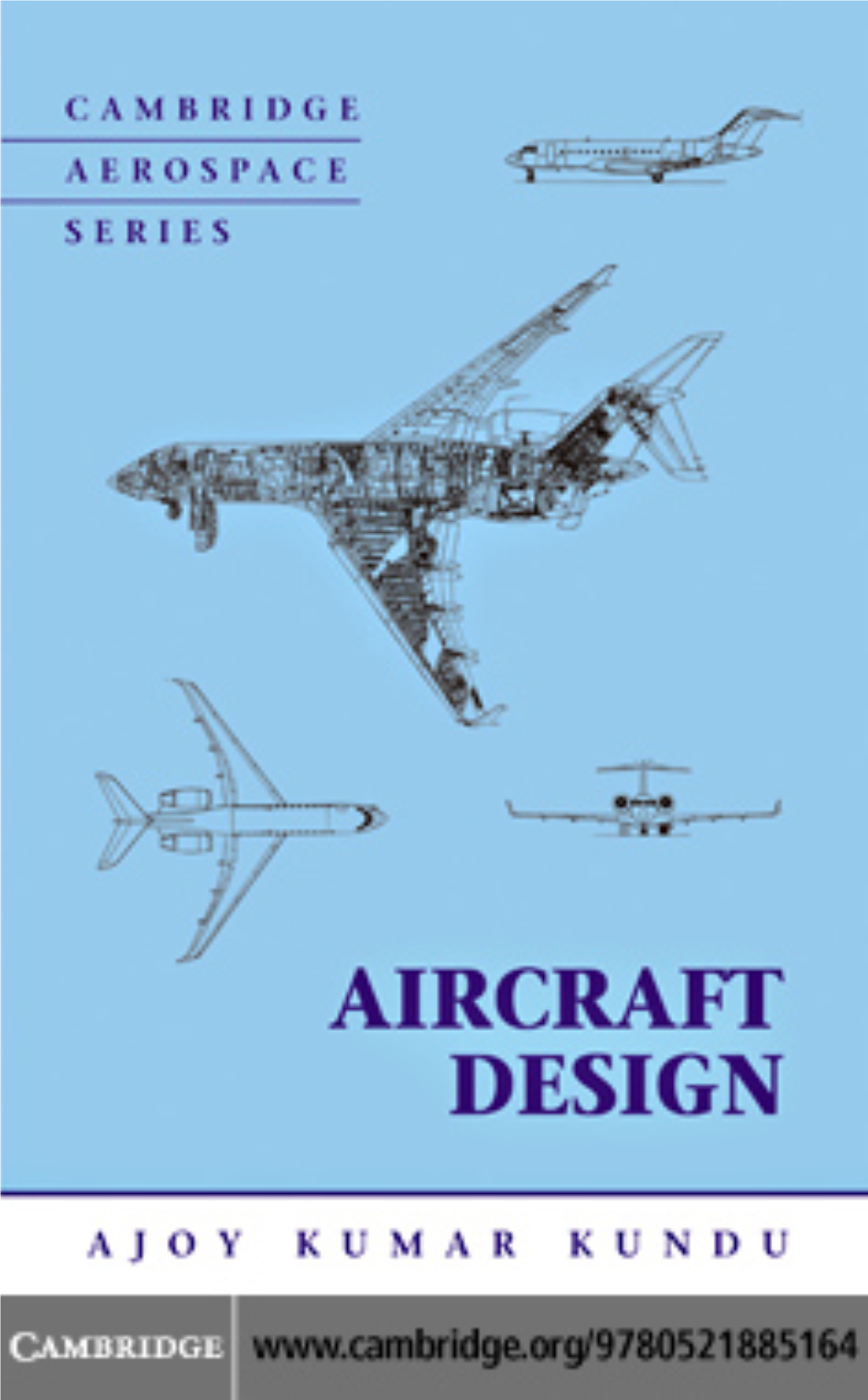
Load more
Recommended publications
-
Years Years Service Or 20,000 Hours of Flying
VOL. 9 NO. 1 OCTOBER 2001 MAGAZINE OF THE ASSOCIATION OF ASIA PACIFIC AIRLINES 50 50YEARSYEARS Japan Airlines celebrating a golden anniversary AnsettAnsett R.I.PR.I.P.?.? Asia-PacificAsia-Pacific FleetFleet CensusCensus UPDAUPDATETE U.S.U.S. terrterroror attacks:attacks: heavyheavy economiceconomic fall-outfall-out forfor Asia’Asia’ss airlinesairlines VOL. 9 NO. 1 OCTOBER 2001 COVER STORY N E W S Politics still rules at Thai Airways International 8 50 China Airlines clinches historic cross strait deal 8 Court rules 1998 PAL pilots’ strike illegal 8 YEARS Page 24 Singapore Airlines pulls out of Air India bid 10 Air NZ suffers largest corporate loss in New Zealand history 12 Japan Airlines’ Ansett R.I.P.? Is there any way back? 22 golden anniversary Real-time IFE race hots up 32 M A I N S T O R Y VOL. 9 NO. 1 OCTOBER 2001 Heavy economic fall-out for Asian carriers after U.S. terror attacks 16 MAGAZINE OF THE ASSOCIATION OF ASIA PACIFIC AIRLINES HELICOPTERS 50 Flying in the face of bureaucracy 34 50YEARS Japan Airlines celebrating a FEATURE golden anniversary Training Cathay Pacific Airways’ captains of tomorrow 36 Ansett R.I.P.?.? Asia-Pacific Fleet Census UPDATE S P E C I A L R E P O R T Asia-Pacific Fleet Census UPDATE 40 U.S. terror attacks: heavy economic fall-out for Asia’s airlines Photo: Mark Wagner/aviation-images.com C O M M E N T Turbulence by Tom Ballantyne 58 R E G U L A R F E A T U R E S Publisher’s Letter 5 Perspective 6 Business Digest 51 PUBLISHER Wilson Press Ltd Photographers South East Asia Association of Asia Pacific Airlines GPO Box 11435 Hong Kong Andrew Hunt (chief photographer), Tankayhui Media Secretariat Tel: Editorial (852) 2893 3676 Rob Finlayson, Hiro Murai Tan Kay Hui Suite 9.01, 9/F, Tel: (65) 9790 6090 Kompleks Antarabangsa, Fax: Editorial (852) 2892 2846 Design & Production Fax: (65) 299 2262 Jalan Sultan Ismail, E-mail: [email protected] Ü Design + Production Web Site: www.orientaviation.com E-mail: [email protected] 50250 Kuala Lumpur, Malaysia. -
A PERSONAL VIEW by Dr Ken Ramsden 2010
THE PAST PRESENT AND FUTURE WITH AIRCRAFT AND THEIR ENGINES A PERSONAL VIEW BY Dr Ken Ramsden 2010 1 CONTENTS HISTORY OF FLIGHT EARLY COMMERCIAL AVIATION COMPETITION CURRENT TECHNOLOGY OF CIVIL AIRCRAFT THE NEAR FUTURE WITH CIVIL AIRCRAFT THE LONG TERM FUTURE FOR CIVIL AIRCRAFT?? HISTORICAL DEVELOPMENT OF AIRCRAFT ENGINES CURRENT AIRCRAFT ENGINES FUTURE ENGINE DEVELOPMENT MODERN MILITARY AIRCRAFT AND ENGINES 2 HISTORY OF FLIGHT 1903 Wright Brothers – First Powered Flight - Kittyhawk OR SANTOS DUMONT 1947 Chuck Yeager Sound Barrier X-1 1961 Yurij Gagarin – Space Flight 3 HISTORY OF FLIGHT THE THIRTIES AND FORTIES BATTLE OF BRITAIN FLIGHT SUPERMARINE SPITFIRE AVRO LANCASTER HAWKER HURRICANE 4 HISTORY OF FLIGHT THE FIFTIES AND SIXTIES THE AVIATION MONOPOLY RACE BLIGHTED BY POLITICS TSR2 Mach 0.9 at sea level Mach 2.2 at 60000 ft Commercially unsuccessful ?? CONCORDE – MACH 2 AT 60000 FT “OLYMPIC ENGINES” FF IN MARCH 69, LAUNCHED IN 1976 5 HISTORY OF FLIGHT TSR2 AND (FLYING) VULCAN AT DUXFORD TSR 2 - XR222 6 EARLY COMMERCIAL AVIATION COMPETITION 7 EARLY COMMERCIAL AVIATION COMPETITION TECHNICALLY UNSUCCESSFUL ?? COMET - Mach 0.85 AT 36000 FT SQUARE WINDOWS FF JULY 49 WITH HIGH CORNER STRESS LAUNCHED JAN 52 Ken’s theory DeH GHOST ENGINES LOW FREQUENCY PISTON ENGINES WITHDRAWN EARLY 80’s VERSUS HIGH FREQUENCY GT’S ?? 8 EARLY COMMERCIAL AVIATION COMPETITION COMMERCIALLY SUCCESSFUL BOEING 707 FF JULY 54 LAUNCHED OCT 58 ENGINES JT3D OR CFM56 BOEING 737 FF APRIL 67 LAUNCHED FEB 68 ENGINES JT8D OR CFM56 9 CURRENT TECHNOLOGY OF CIVIL AIRCRAFT 10 CURRENT -
Airlines and Tourism Development: the Case of Zimbabwe 69 Brian Turton
TOURISM AND TRANSPORT ISSUES AND AGENDA FOR THE NEW MILLENNIUM ADVANCES IN TOURISM RESEARCH Series Editor: Professor Stephen J. Page University of Stirling, U.K. [email protected] Advances in Tourism Research series publishes monographs and edited volumes that comprise state-of-the-art research findings, written and edited by leading researchers working in the wider field of tourism studies. The series has been designed to provide a cutting edge focus for researchers interested in tourism, particularly the management issues now facing decision makers, policy analysts and the public sector. The audience is much wider than just academics and each book seeks to make a significant contribution to the literature in the field of study by not only reviewing the state of knowledge relating to each topic but also questioning some of the prevailing assumptions and research paradigms which currently exist in tourism research. The series also aims to provide a platform for further studies in each area by highlighting key research agendas which will stimulate further debate and interest in the expanding area of tourism research. The series is always willing to consider new ideas for innovative and scholarly books, inquiries should be made directly to the Series Editor. Published: THOMAS Small Firms in Tourism: International Perspectives KERR Tourism Public Policy and the Strategic Management of Failure WILKS & PAGE Managing Tourist Health and Safety in the New Millennium BAUM & LUNDTORP Seasonality in Tourism ASHWORTH & TUNBRIDGE The Tourist-Historic -
New Trends in Future Aircraft Development
NEW TRENDS IN FUTURE AIRCRAFT DEVELOPMENT S. Tsach and D. Penn Engineering Division Israel Aircraft Industries (IAI) Ben-Gurion Airport, Israel ABSTRACT This paper reviews the new trends that are emerging in the development of air vehicles of the future. Technological developments in many fields are reviewed, including aerodynamics, propulsion, flight control, structures, materials, production techniques, avionics, communications, computerization, miniaturization and others. The paper addresses the future needs and requirements of both the military and civil aerospace markets. The needs of military intelligence are expressed in the considerable progress made in the development of UAVs. The transportation needs of passengers and cargo are expressed in the continuous search for greater efficiency and cost reduction in an ever-expanding market place. The review includes examples of developments in the field of civilian aircraft such as Airbus 380, Sonic Cruiser, BWB configuration and supersonic business jet; and discusses technological developments in small business aircraft like the Eclipse 500 and the SATS programs of NASA. Developments in the sphere of unmanned aircraft are described, including UCAVs, OAV, CRW, solar HALE, micro-UAVs and also sensor craft goals are addressed. The paper examines the technological goals which industry has defined for the improvement of aviation and air vehicles, highlighting the American and European long term plans as published in the American Aerospace Commission report, “NASA Aeronautics Blueprint” and the European document “ARTE21”. Some examples of IAI’s recent activities in aircraft development and the integration of advanced technologies are described. This includes the use of CFD for design and improvement of advanced aircraft and the use of production techniques for composite materials with reference to the G150, Airtruck and the family of Heron UAVs. -
Air Travel, Life-Style, Energy Use and Environmental Impact
Air travel, life-style, energy use and environmental impact Stefan Kruger Nielsen Ph.D. dissertation September 2001 Financed by the Danish Energy Agency’s Energy Research Programme Department of Civil Engineering Technical University of Denmark Building 118 DK-2800 Kgs. Lyngby Denmark http://www.bvg.dtu.dk 2001 DISCLAIMER Portions of this document may be illegible in electronic image products. Images are produced from the best available original document Report BYG DTU R-021 2001 ISSN 1601-2917 ISBN 87-7877-076-9 Executive summary This summary describes the results of a Ph.D. study that was carried out in the Energy Planning Group, Department for Civil Engineering, Technical University of Denmark, in a three-year period starting in August 1998 and ending in September 2001. The project was funded by a research grant from the Danish Energy Research Programme. The overall aim of this project is to investigate the linkages between energy use, life style and environmental impact. As a case of study, this report investigates the future possibilities for reducing the growth in greenhouse gas emissions from commercial civil air transport, that is passenger air travel and airfreight. The reason for this choice of focus is that we found that commercial civil air transport may become a relatively large energy consumer and greenhouse gas emitter in the future. For example, according to different scenarios presented by Intergovernmental Panel on Climate Change (IPCC), commercial civil air transport's fuel burn may grow by between 0,8 percent a factor of 1,6 and 16 between 1990 and 2050. The actual growth in fuel consumption will depend on the future growth in airborne passenger travel and freight and the improvement rate for the specific fuel efficiency. -
Air Travel, Life-Style, Energy Use and Environmental Impact
Stefan Krüger Nielsen Air travel, life-style, energy use and environmental impact DTU BYG DANMARKS T EKNISKE UNIVERSITET Rapport BYG·DTU R-021 2001 ISSN 1601-2917 ISBN 87-7877-076-9 $LUWUDYHOOLIHVW\OHHQHUJ\XVH DQGHQYLURQPHQWDOLPSDFW Stefan Krüger Nielsen Ph.D. Dissertation September 2001 Financed by the Danish Energy Agency's Energy Research Programme Energy Planning Group Department of Civil Engineering (BYG•DTU) Technical University of Denmark Brovej, DK-2800 Kgs-Lyngby Denmark Website: www.byg.dtu.dk, e-mail: [email protected] Report BYG•DTU R-021 2001 ISSN 1601-2917 ISBN 87-7877-076-9 Executive summary This summary describes the results of a Ph.D. study that was carried out in the Energy Planning Group, Department for Civil Engineering, Technical University of Denmark, in a three-year period starting in August 1998 and ending in September 2001. The project was funded by a research grant from the Danish Energy Research Programme. The overall aim of this project is to investigate the linkages between energy use, life style and environmental impact. As a case of study, this report investigates the future possibilities for reducing the growth in greenhouse gas emissions from commercial civil air transport, that is passenger air travel and airfreight. The reason for this choice of focus is that we found that commercial civil air transport may become a relatively large energy consumer and greenhouse gas emitter in the future. For example, according to different scenarios presented by Intergovernmental Panel on Climate Change (IPCC), commercial civil air transport’s fuel burn may grow by between 0,8 percent a factor of 1,6 and 16 between 1990 and 2050. -
How Airbus Surpassed Boeing: a Tale of Two Competitors
University of Tennessee, Knoxville TRACE: Tennessee Research and Creative Exchange Masters Theses Graduate School 5-2007 How Airbus Surpassed Boeing: A Tale of Two Competitors William Alexander Burns University of Tennessee - Knoxville Follow this and additional works at: https://trace.tennessee.edu/utk_gradthes Part of the Aerospace Engineering Commons Recommended Citation Burns, William Alexander, "How Airbus Surpassed Boeing: A Tale of Two Competitors. " Master's Thesis, University of Tennessee, 2007. https://trace.tennessee.edu/utk_gradthes/252 This Thesis is brought to you for free and open access by the Graduate School at TRACE: Tennessee Research and Creative Exchange. It has been accepted for inclusion in Masters Theses by an authorized administrator of TRACE: Tennessee Research and Creative Exchange. For more information, please contact [email protected]. To the Graduate Council: I am submitting herewith a thesis written by William Alexander Burns entitled "How Airbus Surpassed Boeing: A Tale of Two Competitors." I have examined the final electronic copy of this thesis for form and content and recommend that it be accepted in partial fulfillment of the requirements for the degree of Master of Science, with a major in Aviation Systems. Robert B. Richards, Major Professor We have read this thesis and recommend its acceptance: Richard Ranaudo, U. Peter Solies Accepted for the Council: Carolyn R. Hodges Vice Provost and Dean of the Graduate School (Original signatures are on file with official studentecor r ds.) To the Graduate Council: I am submitting herewith a thesis written by William A. Burns entitled “How Airbus Surpassed Boeing: A Tale of Two Competitors” I have examined the final electronic copy of this thesis for form and content and recommend that it be accepted in partial fulfillment of the requirements for the degree of Master of Science, with a major in Aviation Systems. -
Global Instability and Strategic Crisis
Global Instability and Strategic Crisis This is a truly important book, one that should be read by policy makers in London and Washington and elsewhere throughout the world. Lucidly written by a distinguished British academic with a strong background in natural science and military technology as well as in the humanities, the text reviews remarkably comprehensively the world outlook and strategic thinking in the aftermath of 9/11. It is also rich in constructive policy proposals for the future. Professor Milton C.Cummings, Jr., Johns Hopkins University, USA Global Instability and Strategic Crisis brings new perspectives to current debates surrounding missile defence and argues that it should have a limited role only. Looking to the future, the author radically extends the customary remit of strategic studies in order to address the new world situation. This book explores the diverse factors—military, scientific, economic, social, ecological and cosmological—bearing upon the quest for stability and peace and anticipates future possibilities. The interventions in Iraq and Afghanistan are both discussed at some length while the Holy Land, Central Southern Africa, Indonesia, China and the Arctic are all seen as foci of special concern in their respective ways. Thematically, the text addresses a raft of topics, among them the redefinition of terror; lethal lasers; internalized arms control; the non- weaponization of space; Guantanamo Bay; regional security pacts; latter-day Marshall Plans; climate change; a ubiquitous urban crisis; instability latent in Western society; a two-tier European Union; and pre-emption doctrine. Salience is given to the military and civil exploitation of space; biowarfare is treated as a singularly serious mass destruction threat. -
Preliminary Description of the Future Aerospace Business Environment
This document is classified as VIVACE Public PRELIMINARY DESCRIPTION OF THE FUTURE AEROSPACE BUSINESS ENVIRONMENT By Johanna Bramham, Wathi Er, Richard Farr, Bart MacCarthy (University of Nottingham) Ole-Jakob Dannemark (Volvo Aero Corporation) Abstract: This document presents a preliminary description of approaches to model factors, themes, scenarios and value chains in the aerospace sector. Three key activities are described: (1) development of a detailed map of the factors that impact on the aerospace business environment and their inter-relationships; (2) an initial set of business scenarios and a preliminary tool for investigating future scenarios of most relevance - VIBES (VIVACE Interactive Business Environment Simulator); (3) a review of the System Dynamics scenario modelling approach and its application in the aerospace market. The report also outlines the next phase of the Business Environment research and the expected research outputs. Dissemination: PU Deliverable/Output n°: VIVACE 2.1/Unott/T/04002-0.1 Issue n°: 2 Keywords: Business environment, business factors, value chain, scenarios, modelling, systems dynamics VIVACE 2.1/UNott/T/04002-0.1 Page: 1/ 128 © 2004 VIVACE Consortium Members. All rights reserved. VIVACE Preliminary Description of the Future Aerospace Business Environment This document is classified as VIVACE Public TABLE OF CONTENTS 0. EXECUTIVE SUMMARY ...................................................................................8 1. CHAPTER 1: INTRODUCTION TO THE RESEARCH....................................10 -
A Way to Improve Profitability of Revolutionary Civil Aircraft Projects
KNUV 2016; 3(49): 152-172 Christoph Winter Uniwersytet Ekonomiczny we Wrocławiu A WAY TO IMPROVE PROFITABILITY OF REVOLUTIONARY CIVIL AIRCRAFT PROJECTS Summary Revolutionary new civil aircraft projects oft en struggle to amortize the investments made. Th e starting point is: reduction of risk of costs overruns (diff erence between actual and planned cost) and consequently aligned further variables of investment calculation would increase profi tability of a project if it is implemented at all. Th at means, if project volume could be predicted more precisely, project´s appraisal could either assume more realistic parameters, like with aircraft pricing or reconsider the project with regard to technical content or market conditions. Th is questions the effi ciency of presently applied planning and investment calculation methods to yield a realistic business case of a “revolutionary” new aircraft . The paper verifies the problem by comparing list price changes of revolutionary aircraft projects (Airbus A380, Airbus A350 and Boeing B787) over time with those of legacy aircraft projects in search for anomalies correlated with signifi cant cost overruns. As a second step, this paper proposes an approach to overcome above defi ciencies combining a dedicated parametric estimate model (CER) to determine project volume for future aircraft projects with a verifi ed parameter setting in investment calculation of those projects. The model uses the degree of new technologies applied (Technical Complexity, TC) and the number of countries, suppliers and fi nal assemblies (Organizational Complexity, OC) as independent variables in order to refl ect the revolutionary character of the projects analyzed. As a result, the approach meets the requirements of application in practice and is likely, when applied, to improve investment decision making. -
Amphibious Aircrafts
Amphibious Aircrafts ...a short overview i Title: Amphibious Aircrafts Subtitle: ...a short overview Created on: 2010-06-11 09:48 (CET) Produced by: PediaPress GmbH, Boppstrasse 64, Mainz, Germany, http://pediapress.com/ The content within this book was generated collaboratively by volunteers. Please be advised that nothing found here has necessarily been reviewed by people with the expertise required to provide you with complete, accurate or reliable information. Some information in this book may be misleading or simply wrong. PediaPress does not guarantee the validity of the information found here. If you need specific advice (for example, medical, legal, financial, or risk management) please seek a professional who is licensed or knowledge- able in that area. Sources, licenses and contributors of the articles and images are listed in the section entitled ”References”. Parts of the books may be licensed under the GNU Free Documentation License. A copy of this license is included in the section entitled ”GNU Free Documentation License” All third-party trademarks used belong to their respective owners. collection id: pdf writer version: 0.9.3 mwlib version: 0.12.13 ii Contents Articles 1 Introduction 1 Amphibious aircraft . 1 Technical Aspects 5 Propeller.............................. 5 Turboprop ............................. 24 Wing configuration . 30 Lift-to-drag ratio . 44 Thrust . 47 Aircrafts 53 J2F Duck . 53 ShinMaywa US-1A . 59 LakeAircraft............................ 62 PBYCatalina............................ 65 KawanishiH6K .......................... 83 Appendix 87 References ............................. 87 Article Sources and Contributors . 91 Image Sources, Licenses and Contributors . 92 iii Article Licenses 97 Index 103 iv Introduction Amphibious aircraft Amphibious aircraft Canadair CL-415 operating on ”Fire watch” out of Red Lake, Ontario, c. -
Technika W Dziejach Cywilizacji – Z Myślą O Przyszłości
Fundacja Otwartego Muzeum Techniki Technika w dziejach cywilizacji – z myślą o przyszłości TOM 16 Wrocław 2020 Fundacja Otwartego Muzeum Techniki Technika w dziejach cywilizacji – z myślą o przyszłości TOM 16 pod red. Stanisława Januszewskiego Dofinansowano ze środków Narodowego Centrum Kultury w ramach Programu Kultura – Interwencje 2020 Wrocław 2020 Redakcja: Stanisław Januszewski Recenzenci: prof. dr hab. inż. Jan Biliszczuk dr hab. prof. nadzw. Andrzej Olejko dr Jakub Marszałkiewicz Opracowanie graficzne, skład: Joanna Kowalska Tłumaczenia na język angielski: dr Jakub Marszałkiewicz Korekta: Gabryela Januszewska Projekt okładki: Michał Stawicki © Copyright by Stanisław Januszewski Wszelkie prawa zastrzeżone. Żadna część niniejszej książki, zarówno w całości, jak i we fragmentach, nie może być reprodukowana w sposób elektroniczny, fotograficzny i inny bez zgody wydawcy i właścicieli praw autorskich. ISBN 978-83-64688-31-7 Druk i oprawa: ul. Strefowa 15, 58-200 Dzierżoniów [email protected] Publikacja wydana z pomocą: Ministerstwo Kultury i Dziedzictwa Narodowego PKP S.A. Wimarol Sp. J., Wrocław Betard Sp. z o.o., Długołęka Świdnicka Rada Federacji SNT NOT Zakład Szybowcowy „Jeżów” w Jeżowie Sudeckim Przedsiębiorstwo Budowlane ABM Sp. z o.o., Wrocław Federacja Firm Lotniczych Bielsko – Śląski Klaster Lotniczy Stowarzyszenie Inżynierów i Techników Mechaników Polskich. Oddział Wałbrzych Celem Fundacji Otwartego Muzeum Techniki jest praca na rzecz: • rozwijania świadomości uniwersalnych walorów dziedzictwa przemysłowego i technicznego, a poprzez ochronę dzieł cywilizacji technicznej, wspólnych europejskiemu kręgowi kulturowemu, budowanie więzi między ludźmi i narodami, • ochrony spuścizny techników polskich działających w kraju i na obczyźnie, • aktywnej ochrony dziedzictwa przemysłowego i technicznego w Polsce, przede wszystkim na obszarze Wrocławia i regionów nadodrzańskich oraz włączanie go w obieg współczesnej kultury, • organizacji Otwartego Muzeum Techniki.