High-Fidelity Aerothermal Engineering Analysis for Planetary Probes Using DOTNET Framework and OLAP Cubes Database
Total Page:16
File Type:pdf, Size:1020Kb
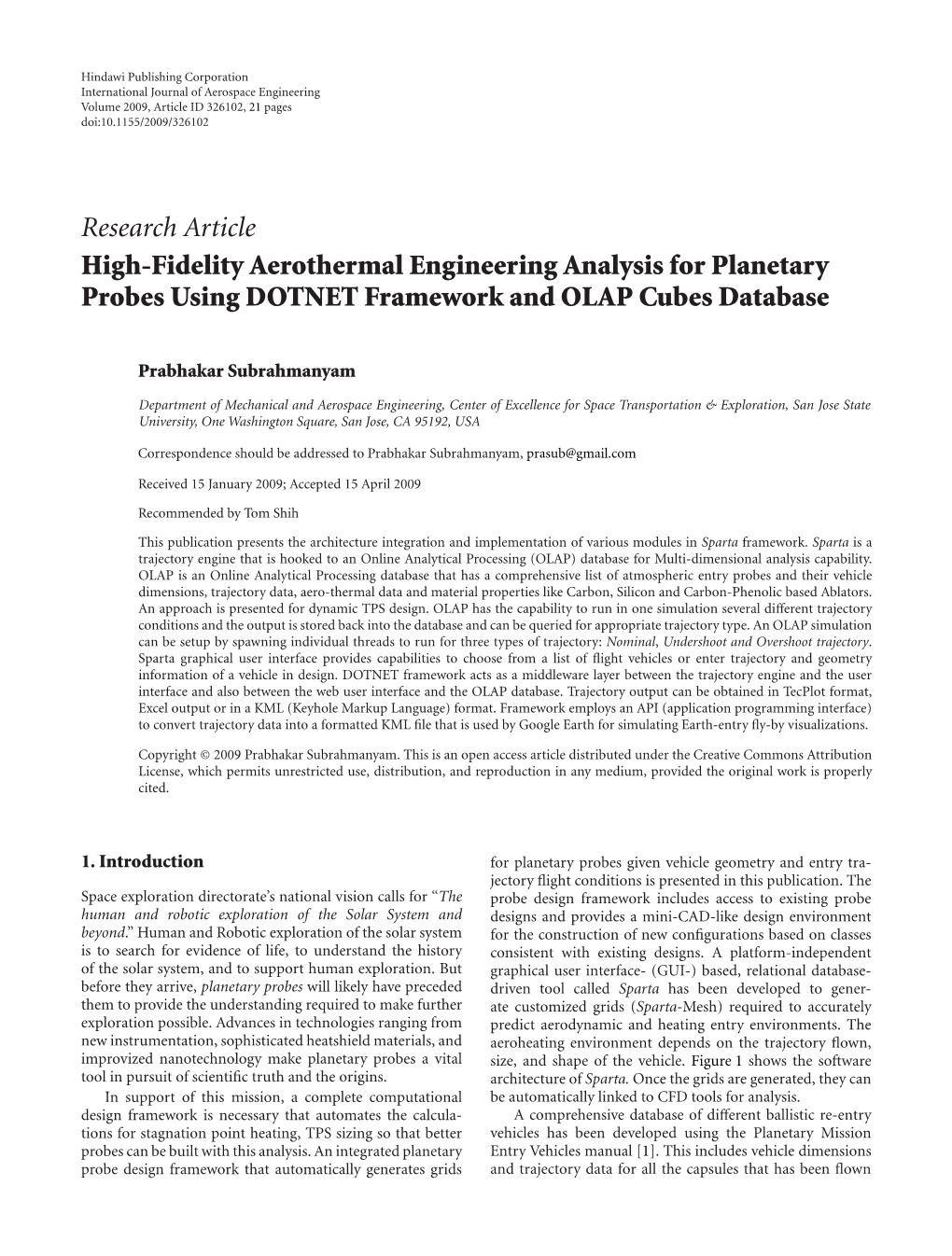
Load more
Recommended publications
-
APOLLO EXPERIENCE REPORT - THERMAL PROTECTION SUBSYSTEM by Jumes E
NASA TECHNICAL NOTE NASA TN D-7564 w= ro VI h d z c Q rn 4 z t APOLLO EXPERIENCE REPORT - THERMAL PROTECTION SUBSYSTEM by Jumes E. Puulosky und Leslie G, St. Leger Ly12d012 B. Johlzson Space Center Honst0~2, Texus 77058 NATIONAL AERONAUTICS AND SPACE ADMINISTRATION WASHINGTON, 0. C. JANUARY 1974 ~--_. - .. 1. Report No. 2. Government Accession No. 3. Recipient's Catalog No. D-7564 4. Title and Subtitle 5. Report Date January 1974 APOLLOEXPERIENCEREPORT THERMAL PROTECTION SUBSYSTEM 6. Performing Organization Code I 7. Author(s) I 8. Performing Organization Report No. JSC S-383 James E. Pavlosky and Leslie G. St. Leger, JSC 10. Work Unit No. I 9. Performing Organization Name and Address 11. Contract or Grant No. Lyndon B. Johnson Space Center Houston, Texas 77058 13. Type of Report and Period Covered 12. Sponsoring Agency Name and Address 14. Sponsoring Agency Code National Aeronautics and SDace Administration Washington, D. C. 20546 1 15. Supplementary Notes The JSC Director waived the use of the International System of Units (SI) for this Apollo Experienc Report because, in his judgment, the use of SI units would impair the usefulness of th'e report or result in excessive cost. 16. Abstract The Apollo command module was the first manned spacecraft to be designed to enter the atmos- phere of the earth at lunar-return velocity, and the design of the thermal protection subsystem for the resulting entry environment presented a major technological challenge. Brief descrip- tions of the Apollo command module thermal design requirements and thermal protection con- figuration, and some highlights of the ground and flight testing used for design verification of the system are presented. -
Preparation of Papers for AIAA Technical Conferences
Thermal Protection Systems Technology Transfer from Apollo and Space Shuttle to the Orion Program Michael Stewart 1 Lockheed Martin, Kennedy Space Center, Florida, 32899 and William J. Koenig2 NASA Kennedy Space Center, Florida, 32899 and Richard F. Harris 3 NASA Kennedy Space Center, Florida, 32899 This paper describes how the Orion program is utilizing the Thermal Protection System (TPS) experience from the Apollo and Space Shuttle programs to reduce program risk and improve affordability to meet NASA’s future manned exploration missions. The Orion program successfully completed the Exploration Flight Test (EFT-1) mission in 2014 and is currently assembling, integrating, and testing the next spacecraft for the Exploration Mission (EM-1) to meet the flight test objectives of an unmanned orbital mission to the moon and return to earth in 2019. The Orion spacecraft production operations are located in the Neil Armstrong Operations and Checkout (O&C) facility at the Kennedy Space Center (KSC) providing an affordable and seamless delivery approach of vehicles directly to the launch site eliminating spacecraft transportation and additional checkout testing. Innovative vehicle design, manufacturing and test operations approaches are maturing and evolving with each Orion vehicle build to support the challenging NASA exploration mission requirements beyond Low Earth Orbit (LEO) while reducing program cost and schedule impacts. An example of Orion’s evolution is the incorporation of an improved heat shield design, assembly and testing approach to meet the higher re-entry velocities for a lunar return for the EM-1 mission. The EFT- 1 heat shield was based on the Apollo heat shield manufacturing processes and was assembled at a supplier location and then transported to KSC for final integration. -
Heat Flux at a Point on the Vehicle (W/Cm2)
Entry Aerothermodynamics • Review of basic fuid parameters • Heating rate parameters • Stagnation point heating • Heating on vehicle surfaces • Slides from 2012 NASA Termal and Fluids Analysis Workshop: https://tfaws.nasa.gov/TFAWS12/Proceedings/ Aerothermodynamics%20Course.pdf © 2016 David L. Akin - All rights reserved http://spacecraft.ssl.umd.edu U N I V E R S I T Y O F Entry Aerothermodynamics MARYLAND ENAE 791 - Launch and Entry Vehicle Design1 Background 2 • The kinetic energy of an entry vehicle is dissipated by transformation into thermal energy (heat) as the entry system decelerates • The magnitude of this thermal energy is so large that if all of this energy were transferred to the entry system it would be severely damaged and likely vaporize – Harvey Allen - the blunt body concept • Only a small fraction of this thermal energy is transferred to the entry system – The thermal transfer fraction is dependant on vehicle shape, size, aerodynamic regime and velocity – Near peak heating, 1% to 5% of the total thermal energy is transferred to the entry system – Example: at the peak heating point the freestream energy transfer for 1 3 2 2 Pathfinder was q Ý Ñ = 2 r V ~ 4 , 000 W/cm but only about 110 W/cm (2.7%) was actually transferred to the surface Example 3 E V2 Energy density: = + g h m 2 o V E/m Entry (km/s) (MJ/kg) MER 5.6 16 Note that: Apollo 11.4 66 Water boils @ 2.3 MJ/kg Carbon vaporizes @ 60.5 MJ/kg Mars 14.0 98 Return Galileo 47.4 1130 In each case goh is about 1% of total Side Note: What Can We Test? 4 Missions of Interest Live here Blunt Body Rationale 5 • Why is a blunt body used for planetary entry? – Slender body: low drag, highly maneuverable – Blunt body: high drag, not very maneuverable • Blunt bodies generate strong shock waves – Efficient energy dissipation. -
Post-Flight Assessment of Avcoat Thermal Protection System for The
Post-Flight Assessment of Avcoat Thermal Protection System for the Exploration Flight Test-1 Deepak Bose, Jose Santos, Erika Rodriguez, Milad Mahzari, Brian Remark, and Suman Muppidi NASA Ames Research Center, Moffett Field, CA NASA Johnson Space Center, Houston, TX On December 5, 2014 NASA conducted the first flight test of its next generation human-class Orion spacecraft. The flight was called the Exploration Flight Test -1 (EFT-1) which lasted for 4 hours and culminated into a re-entry trajectory at 9 km/s. This flight test of the 5-meter Orion Crew Module demonstrated various sub-systems including the Avcoat ablative thermal protection system (TPS) on the heat shield. The Avcoat TPS had been developed from the Apollo-era recipe with a few key modifications. The engineering for thermal sizing was supported by modeling, analysis, and ground tests in arc jet facilities. This paper will describe a postlfight analysis plan and present results from post-recovery inspections, data analysis from embedded sensors, TPS sample extraction and characterization in the laboratory. After the recovery of the vehicle, a full photographic survey and surface scans of the TPS were performed. The recovered vehicle showed physical evidence of flow disturbances, varying degrees of surface roughness, and excessive recession downstream of compression pads. The TPS recession was measured at more than 200 locations of interest on the Avcoat surface. The heat shield was then processed for sample extraction prior to TPS removal using the 7-Axis Milling machine at Marshall Space Flight Center. Around 182 rectangular TPS samples were extracted for subsequent analysis and investigation. -
C 2017 Przemyslaw Rostkowski UNCERTAINTY QUANTIFICATION of VISTA CHARRING ABLATOR MATERIAL DATABASE USING BAYESIAN INFERENCE
c 2017 Przemyslaw Rostkowski UNCERTAINTY QUANTIFICATION OF VISTA CHARRING ABLATOR MATERIAL DATABASE USING BAYESIAN INFERENCE BY PRZEMYSLAW ROSTKOWSKI THESIS Submitted in partial fulfillment of the requirements for the degree of Master of Science in Aerospace Engineering in the Graduate College of the University of Illinois at Urbana-Champaign, 2017 Urbana, Illinois Adviser: Assistant Professor Marco Panesi Abstract During hypersonic trajectory through a planetary atmosphere a high heat flux environment is generated due to the friction between gas particles and the vehi- cle. To protect it from the excessive heat energy that is transferred to it, Thermal Protection Systems are implemented in the spacecraft's design. Current modeling tools used for the design of heat shields, however, have been shown to be unable to fully replicate material response data recorded during flight. Collaborative efforts aimed at improving current models are also difficult to establish due to restrictions placed on the access to material response data. In response, a material model free of access restrictions dubbed VISTA was devised by a research group at Univer- sity of Kentucky upon which synergistic projects aimed at studying performance of charring ablators can be readily organized. In the present thesis a sensitivity study of the VISTA material model is performed with both Pearson correlation coefficients and the method of Sobol; Sobol indices are shown to be a much more robust sensitivity metric in the context of charring ablators. Uncertain param- eters of the material database are then calibrated through the use of Bayesian inference rather than basic deterministic methods often used throughout scien- tific works. -
The Apollo Spacecraft Chronology, Takes up the Story Where the First Left Off, in November 1962
A CHRONOLOGY NASA SP-4009 THE APOLLO SPACECRAFT A CHRONOLOGY VOLUME II November 8, 1962--September 80, 1964 by Mary Louise Morse and Jean Kernahan Bays THE NASA HISTORICAL SERIES Scientific and Technical ln[ormation Office 1973 /LS.P,. / NATIONAL AERONAUTICS AND SPACE ADMINISTRATION Washington, D.C. For sale by the Superintendent of Documents U.S. Government Printing Office, Washington, D.C. 20402 Price $3.20 Stock Number 3300-0455 (Paper Cover) Library o] Congress Catalog Card Number 69-60008 FOREWORD This, tile second volume of the Apollo Spacecraft Chronology, takes up the story where the first left off, in November 1962. The first volume dealt with the birth of the Apollo Program and traced its early development. The second concerns its teenage period, up to September 30, 1964. By late 1962 the broad conceptual design of the Apollo spacecraft and the Apollo lunar landing mission was complete. The Administrator formally advised the President of the United States on December 10 that NASA had selected lunar orbit rendezw)us over direct ascent and earth orbit rendezvous as the mode for landing on the moon. All major spacecraft contractors had been selected; detailed system design and early developmental testing were under way. On October 20, 1962, soon after Wally Schirra's six-orbit mission in .Sigma 7, the first formal overall status review of the Apollo spacecraft and flight mission effort was given to Administrator James E. _Vebb. The writer of this foreword, who was then the Assistant Director for Apollo Spacecraft Development, recalls George Low, then Director of Manned Spacecraft and Flight Missions trader D. -
The 4-Hour Flight and Fiery Re-Entry That Could Give NASA Its Mojo Back Page 24
November 2014 ORION The 4-hour flight and fiery re-entry that could give NASA its mojo back page 24 Proactive on cybersecurity/page 30 Earth-observing Sentinels/page 34 Aireon’s Thoma on airliner surveillance page 22 A PUBLICATIONPUBLICATION OFOF THETHE AMERICANAMERICAN INSTITUTEINSTITUTE OFOF AERONAUTICSAERONAUTICS ANDAND ASTRONAUTICSASTRONAUTICS Preparing to install Orion’s heat shield at Kennedy Space Center in anticipation of its Dec. 4 liftoff. 26 AEROSPACE AMERICA/NOVEMBER 2014 TIME TO FLY If NASA is going to deliver astronauts to Mars or an asteroid, Lockheed Martin is designing the crew capsules that will take them there. The Orion project has been unfolding for years in board rooms and cleanrooms, but things will get real on Dec. 4 when an unmanned test version blasts off from Florida. Natalia Mironova describes the road to Exploration Flight Test-1 and the technical challenges to come. f all goes as planned, an unmanned could become a problem as NASA closes in Orion multipurpose crew vehicle will on the first crewed launch in 2021. splash down in the Pacific Ocean For Lockheed and NASA, the stakes on southwest of San Diego on Dec. 4, hav- Dec. 4 could not be higher. A smooth mis- ing ventured 3,600 miles into space, sion would be a confidence builder that Ifarther than any crew vehicle has gone since could shore up faith in the U.S.’ decision to the Apollo 17 mission in 1972. This early shelve its desire for a single-stage-to-orbit version of an Orion capsule will be coming space plane in favor of a simpler capsule back hot because of a trajectory designed to and rocket approach. -
1 Design of an Integral Thermal Protection System
DESIGN OF AN INTEGRAL THERMAL PROTECTION SYSTEM FOR FUTURE SPACE VEHICLES By SATISH KUMAR BAPANAPALLI A DISSERTATION PRESENTED TO THE GRADUATE SCHOOL OF THE UNIVERSITY OF FLORIDA IN PARTIAL FULFILLMENT OF THE REQUIREMENTS FOR THE DEGREE OF DOCTOR OF PHILOSOPHY UNIVERSITY OF FLORIDA 2007 1 © 2007 Satish Kumar Bapanapalli 2 To my loving wife Debamitra, my parents Nagasurya and Adinarayana Bapanapalli, brother Gopi Krishna and sister Lavanya 3 ACKNOWLEDGMENTS I would like to express my sincere gratitude to my advisor and mentor Dr. Bhavani Sankar for his constant support (financial and otherwise) and motivation throughout my PhD studies. He allowed me to work with freedom, was always supportive of my ideas and provided constant motivation for my research work, which helped me grow into a mature and confident researcher under his tutelage. I also thank my committee co-chair Dr. Rafi Haftka for his invaluable inputs and guidance, which have been instrumental for my research work. I am also grateful to him for getting my interest into the field of Structural Optimization, which I hope would be a huge part of all my future research endeavors. I am also thankful to Dr. Max Blosser (NASA Langley) for his crucial inputs in my research work, which kept us on track with the expectations of NASA. I sincerely thank my dissertation committee members Dr. Ashok Kumar and Dr. Gary Consolazio for evaluating my research work and my candidature for the PhD degree. I also would like to acknowledge Dr. Peter Ifju and Dr. Nam-Ho Kim for their useful inputs and comments. -
Atmospheric Reentry - Wikipedia, the Free Encyclopedia Page 1 of 14
Atmospheric reentry - Wikipedia, the free encyclopedia Page 1 of 14 AtmosphericHelp reentryus provide free content to the world by donating today ! From Wikipedia, the free encyclopedia Further information: Re-Entry (Marley Marl album) and Re-Entry (Big Brovaz album) Atmospheric reentry refers to the movement of human-made or natural objects as they enter the atmosphere of a planet from outer space, in the case of Earth from an altitude above the "edge of space." This article primarily addresses the process of controlled reentry of vehicles which are intended to reach the planetary surface intact, but the topic also includes uncontrolled (or minimally controlled) cases, such as the intentionally or circumstantially occurring, destructive deorbiting of satellites and the falling back to the planet of "space junk" due to orbital decay. Vehicles that typically undergo this process include ones returning from orbit (spacecraft) and ones on exo-orbital (suborbital) trajectories (ICBM reentry vehicles, some spacecraft.) Typically this process requires special methods to protect against aerodynamic heating. Various advanced technologies have been developed to enable atmospheric reentry and flight at extreme velocities. Contents 1 History 2 Terminology, definitions and jargon 3 Blunt body entry vehicles 4 Entry vehicle shapes 4.1 Sphere or spherical section 4.2 Sphere-cone 4.3 Biconic 4.4 Non-axisymmetric shapes 5 Shock layer gas physics 5.1 Perfect gas model 5.2 Real (equilibrium) gas model 5.3 Real (non-equilibrium) gas model 5.4 -
Apollo Seals: a Basis for the Crew Exploration Vehicle Seals
Apollo Seals: A Basis for the Crew Exploration Vehicle Seals Joshua R. Finkbeiner,1 Patrick H. Dunlap, Jr.,2 and Bruce M. Steinetz3 NASA Glenn Research Center, Cleveland, OH 44135 Christopher C. Daniels4 University of Akron, Akron, OH 44325–3901 The National Aeronautics and Space Administration is currently designing the Crew Exploration Vehicle (CEV) as a replacement for the Space Shuttle for manned missions to the International Space Station, as a command module for returning astronauts to the moon, and as an earth reentry vehicle for the final leg of manned missions to the moon and Mars. The CEV resembles a scaled-up version of the heritage Apollo vehicle; however, the CEV seal requirements are different than those from Apollo because of its different mission requirements. A review is presented of some of the seals used on the Apollo spacecraft for the gap between the heat shield and backshell and for penetrations through the heat shield, docking hatches, windows, and the capsule pressure hull. I. Introduction T he Crew Exploration Vehicle (CEV) is currently being designed by the National Aeronautics and Space Administration (NASA) as the United States’ newest manned space vehicle to replace the Space Shuttle for missions to low earth orbit (LEO) and to enable long duration exploration missions to the moon and Mars. Several mission profiles envisioned for the CEV are described in Ref. 1. The CEV will carry as many as six astronauts to the International Space Station (ISS), where it will remain docked for up to six months to serve as a “lifeboat” escape capsule. -
Orion Heat Shield Progressing Toward Completion at Textron Defense Systems
MONTHLY ACCOMPLISHMENTS July 2013 orion Orion heat shield progressing toward completion at Textron Defense Systems Progress continues toward completion of the Orion Exploration Flight be transferred to a vacuum cart for bagging and curing. After this Test-1 (EFT-1) heat shield at Textron Defense Systems in Wilmington, intermediate cure, the heat shield will be prepped for post cure, Mass. followed by the commencement of the machining operation. To date, the Textron Orion team has applied more than 80 percent The heat shield is scheduled to be shipped to Kennedy Space Center of the Avcoat ablative material and completed the intermediate in early October, where it will be integrated onto the Orion crew cure process for the third of four Avcoat gunning cycles for the heat module in preparation for EFT-1 in 2014. The heat shield’s Avcoat shield. In parallel, the seams for the fourth and final gunning cycle ablative coating will burn away from the crew module, protecting it were trimmed, eliminating the need for a heat shield lift-and-transfer from heat as the spacecraft endures temperatures as high as 5,000 operation after the intermediate curing process was completed for degrees Fahrenheit upon entering the Earth’s atmosphere at more the third cycle. than 20,000 mph from a high altitude orbit. In August, the Orion team will complete gunning the remaining The Orion heat shield is the world’s largest structure of its kind and is open areas on the heat shield with Avcoat. The heat shield will then critical for crew safety. Aerojet Rocketdyne tests new graphite material for Orion jettison motor Orion supplier Aerojet Rocketdyne successfully conducted a test plan objectives, providing data to enable performance key Orion jettison motor (JM) test this month that demonstrated assessment of the new graphite material. -
Thermal Protection Systems Technology Transfer from Apollo and Space Shuttle to the Orion Program
https://ntrs.nasa.gov/search.jsp?R=20180006812 2019-08-31T18:53:50+00:00Z View metadata, citation and similar papers at core.ac.uk brought to you by CORE provided by NASA Technical Reports Server Thermal Protection Systems Technology Transfer from Apollo and Space Shuttle to the Orion Program Michael Stewart 1 Lockheed Martin, Kennedy Space Center, Florida, 32899 and William J. Koenig2 NASA Kennedy Space Center, Florida, 32899 and Richard F. Harris 3 NASA Kennedy Space Center, Florida, 32899 This paper describes how the Orion program is utilizing the Thermal Protection System (TPS) experience from the Apollo and Space Shuttle programs to reduce program risk and improve affordability to meet NASA’s future manned exploration missions. The Orion program successfully completed the Exploration Flight Test (EFT-1) mission in 2014 and is currently assembling, integrating, and testing the next spacecraft for the Exploration Mission (EM-1) to meet the flight test objectives of an unmanned orbital mission to the moon and return to earth in 2019. The Orion spacecraft production operations are located in the Neil Armstrong Operations and Checkout (O&C) facility at the Kennedy Space Center (KSC) providing an affordable and seamless delivery approach of vehicles directly to the launch site eliminating spacecraft transportation and additional checkout testing. Innovative vehicle design, manufacturing and test operations approaches are maturing and evolving with each Orion vehicle build to support the challenging NASA exploration mission requirements beyond Low Earth Orbit (LEO) while reducing program cost and schedule impacts. An example of Orion’s evolution is the incorporation of an improved heat shield design, assembly and testing approach to meet the higher re-entry velocities for a lunar return for the EM-1 mission.