Research on Distributed Jet Blowing Wing Based on the Principle of Fan-Wing Vortex-Induced Lift and Thrust
Total Page:16
File Type:pdf, Size:1020Kb
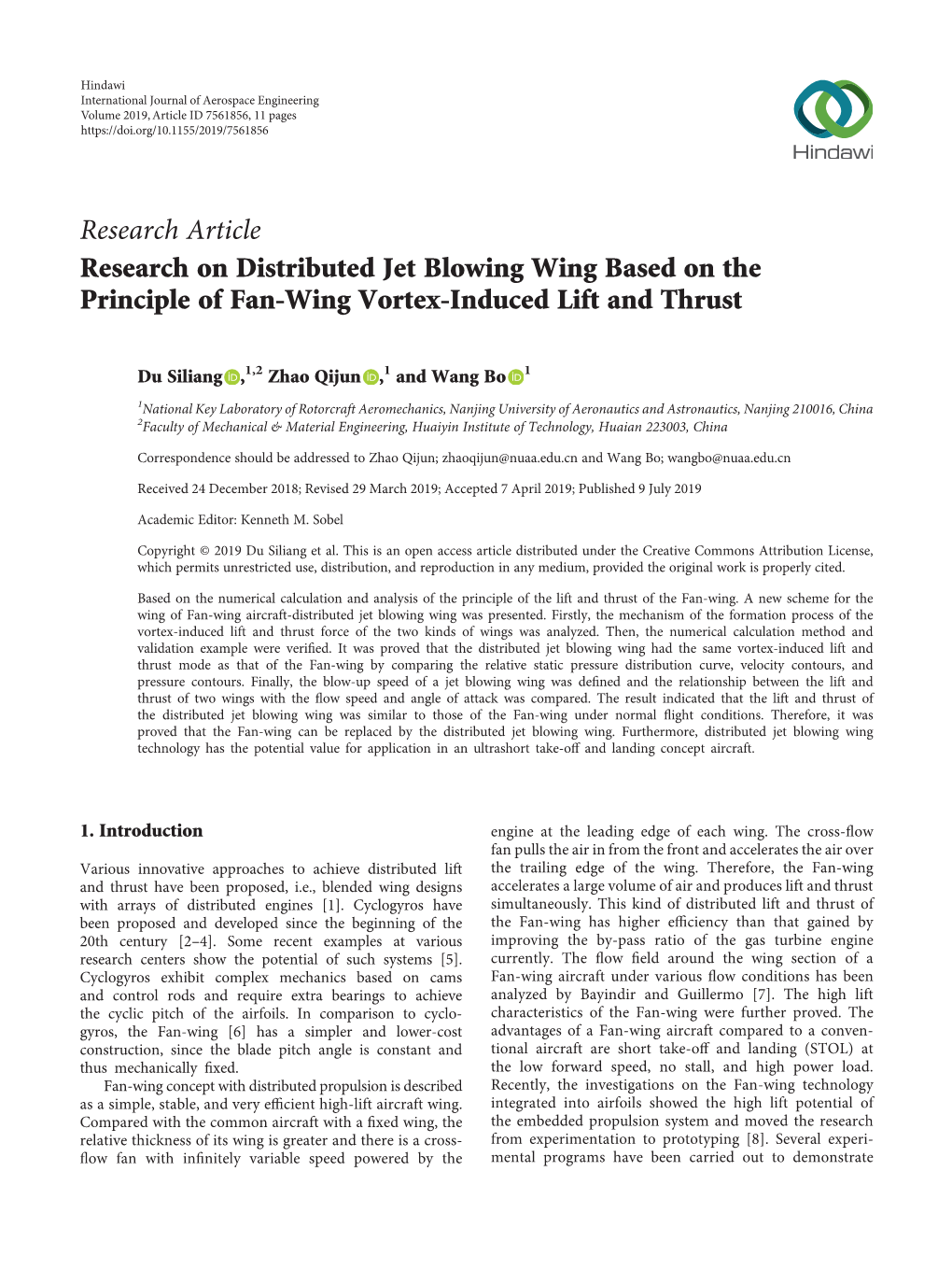
Load more
Recommended publications
-
The Tricopter: an Agile UAV 117 6.1 Design of the Tricopter
ECOLE DOCTORALE UNIVERSITÉ PARIS-SUD ÉCOLE DOCTORALE : Sciences et Technologie de l’Information, des Télécommunications et des Systèmes Laboratoire des Signaux et Systèmes (L2S) Centre de Robotique MinesParisTech (CAOR) DISCIPLINE : Physique THÈSE DE DOCTORAT Présentée et soutenue publiquement par Étienne SERVAIS le 18 septembre 2015. TRAJECTORY PLANNING AND CONTROL OF COLLABORATIVE SYSTEMS: APPLICATION TO TRIROTOR UAVS. Directeurs de thèse : Brigitte d’ANDRÉA-NOVEL Professeur (Mines ParisTech) Hugues MOUNIER Professeur (Université Paris XI) Composition du jury : Rapporteurs : Tarek HAMEL Professeur (Université de Nice Sophia Antipolis) Miroslav KRSTIC´ Professeur (Université de Californie à San Diego) Examinateurs : Jean-Michel CORON Professeur (Université Pierre et Marie Curie) Joachim RUDOLPH Professeur (Université de la Sarre) Claude SAMSON Directeur de recherche (INRIA) Membres invités : Silviu-Iulian NICULESCU Directeur de recherche (CNRS) Arnaud QUADRAT Ingénieur (Sagem-DS) Planification de trajectoire et contrôle d’un système collaboratif : Application à un drone trirotor. Résumé : L’objet de cette thèse est de proposer un cadre complet, du haut niveau au bas niveau, de génération de trajectoires pour un groupe de systèmes dynamiques indé- pendants. Ce cadre, basé sur la résolution de l’équation de Burgers pour la génération de trajectoires, est appliqué à un modèle original de drone trirotor et utilise la platitude des deux systèmes différentiels considérés. La première partie du manuscrit est consacrée à la génération de trajectoires. Celle-ci est effectuée en créant formellement, par le biais de la platitude du système considéré, des so- lutions à l’équation de la chaleur. Ces solutions sont transformées en solution de l’équation de Burgers par la transformation de Hopf-Cole pour correspondre aux formations voulues. -
Recent Developments in Aerial Robotics: a Survey and Prototypes Overview Chun Fui Liew, Danielle Delatte, Naoya Takeishi, Takehisa Yairi
1 Recent Developments in Aerial Robotics: A Survey and Prototypes Overview Chun Fui Liew, Danielle DeLatte, Naoya Takeishi, Takehisa Yairi Abstract—In recent years, research and development in aerial cite all related papers in a short paper. To date, there is no sur- robotics (i.e., unmanned aerial vehicles, UAVs) has been growing vey that attempt to list all the UAV papers in a systematic way. at an unprecedented speed, and there is a need to summarize In this work, we systematically identify 1,318 UAV papers that the background, latest developments, and trends of UAV research. Along with a general overview on the definition, types, categories, appear in the top robotic journals/conferences since 2001. The and topics of UAV, this work describes a systematic way to identification process includes screening paper abstracts with identify 1,318 high-quality UAV papers from more than thirty a program script and eliminating non-UAV papers based on thousand that have been appeared in the top journals and several criteria with meticulous human checks. We categorize conferences. On top of that, we provide a bird’s-eye view of the selected UAV papers in several ways, e.g., with regard UAV research since 2001 by summarizing various statistical information, such as the year, type, and topic distribution of to UAV types, research topics, onboard camera systems, off- the UAV papers. We make our survey list public and believe that board motion capture system, countries, years, etc. In addition, the list can not only help researchers identify, study, and compare we provide a high-level view of UAV research since 2001 by their work, but is also useful for understanding research trends summarizing various statistical information, including year, in the field. -
A Review of the Magnus Effect in Aeronautics
Progress in Aerospace Sciences 55 (2012) 17–45 Contents lists available at SciVerse ScienceDirect Progress in Aerospace Sciences journal homepage: www.elsevier.com/locate/paerosci A review of the Magnus effect in aeronautics Jost Seifert n EADS Cassidian Air Systems, Technology and Innovation Management, MEI, Rechliner Str., 85077 Manching, Germany article info abstract Available online 14 September 2012 The Magnus effect is well-known for its influence on the flight path of a spinning ball. Besides ball Keywords: games, the method of producing a lift force by spinning a body of revolution in cross-flow was not used Magnus effect in any kind of commercial application until the year 1924, when Anton Flettner invented and built the Rotating cylinder first rotor ship Buckau. This sailboat extracted its propulsive force from the airflow around two large Flettner-rotor rotating cylinders. It attracted attention wherever it was presented to the public and inspired scientists Rotor airplane and engineers to use a rotating cylinder as a lifting device for aircraft. This article reviews the Boundary layer control application of Magnus effect devices and concepts in aeronautics that have been investigated by various researchers and concludes with discussions on future challenges in their application. & 2012 Elsevier Ltd. All rights reserved. Contents 1. Introduction .......................................................................................................18 1.1. History .....................................................................................................18 -
Charting the Future of Flight
12–14 AUGUST 2O13 LOS ANGELES, CALIFORNIA CHARTING THE FUTURE OF FLIGHT FINAL PROGRAM Sponsored by www.aiaa.org/aviation2013 #aiaaAviation GET YOUR CONFERENCE INFO ON THE GO! Download the FREE AIAA 2013 Conference Mobile App FEATURES • Browse Program – View the program at your fingertips • My Itinerary – Create your own conference schedule • Conference Info – Including special events • Take Notes – Take notes during sessions • Venue Map – Hyatt Regency Century Plaza • City Map – See the surrounding area • Connect to Twitter – Tweet about what you’re doing and who you’re meeting with #aiaaAviation HOW TO DOWNLOAD Any version can be run without an active Internet connection! You can also sync an itinerary you created online with the app by entering your unique itinerary name. Compatible with MyItinerary Mobile App MyItinerary Web App • For optimal use, we recommend • For optimal use, we recommend: iPhone/iPad, rd iPhone 3GS, iPod Touch (3 s iPhone 3GS, iPod Touch (3rd Android, and generation), iPad iOS 4.0, or later generation), iPad iOS 4.0, or later • Download the MyItinerary app by s Most mobile devices using Android searching for “ScholarOne” in the BlackBerry! 2.2 or later with the default browser App Store directly from your mobile device. Or, access the link below or s y BlackBerr Torch or later device using scan the QR code to access the iTunes BlackBerry OS 7.0 with the default page for the app. http://itunes.apple. browser com/us/app/scholarone-my-itinerary/ • Download the MyItinerary app by id497884329?mt=8 scanning the QR code or accessing • Select the meeting “AIAA AVIATION http://download.abstractcentral.com/ 2013” aiaa-mav13/index.htm • Once downloaded, you can bookmark the site to access it later or add a link to your home screen. -
Aerodynamics and Aircraft Design
RESTRICTED AND AIRCRAFT DESIGN A REPORT PREPARED FOR THE AAF SCIENTIFIC ADVISORY GROUP By H. S. TSIEN Gllggenheim Laboratory California Institllte of Technology W. R. SEARS AND IRVING ASHKENAS Northrop Aircraft Company, Hawthorne, California C. N. HASERT Captain, Air Corps N. M. NEWMARK Talbot Laboratory Unif!ersity of Illinois • Pllblished MIIY, 1946 by HEADQUARTERS AIR MATERIEL COMMAND PUBLICATIONS BRANCH. INTELLIGENCE T-2 •• WRIGHT FIELD, DAYTON, OHIO RESTRICTED The AAF Scientific Advisory Group was activated late in 1944 by General of the Army H. H. Arnold. He se cured the services of Dr. Theodore von Karman, re nowned scientist and consultant in aeronautics, who agreed to organize and direct the group. Dr. von Karman gathered:wbout him a group of Ameri can scientists from every field of research having a bearing on air power. These men then analyzed im portant developments in the basic sciences, both here and abroad, and attempted to evaluate the effects of their application to air power. This volume is one of a group of reports made to the Army Air Forces by the Scientific Advisory Group. This document contains information affedlng the national defense of the United States within the meaning of the Espionage Act, SO U. S. C., 31 and 32, as amended. Its transmission or the revelation of its contents in any manner to an unauthorized person is prohibited by law. AA. SCIENTI.IC ADVISORY GROUP Dr. Th. von Karman Director Colonel F. E. Glantzberg Dr. H. L. Dryden Deputy Director, Military Deputy Director, Scientific Lt Col G. T. McHugh, Executive Capt C. H. -
Parametric Analysis of a Large-Scale Cycloidal Rotor in Hovering Conditions
Chalmers Publication Library Parametric Analysis of a Large-scale Cycloidal Rotor in Hovering Conditions This document has been downloaded from Chalmers Publication Library (CPL). It is the author´s version of a work that was accepted for publication in: Journal of Aerospace Engineering (ISSN: 0893-1321) Citation for the published paper: Xisto, C. ; Leger, J. ; Páscoa, J. et al. (2016) "Parametric Analysis of a Large-scale Cycloidal Rotor in Hovering Conditions". Journal of Aerospace Engineering http://dx.doi.org/10.1061/(ASCE)AS.1943- 5525.0000658 Downloaded from: http://publications.lib.chalmers.se/publication/235793 Notice: Changes introduced as a result of publishing processes such as copy-editing and formatting may not be reflected in this document. For a definitive version of this work, please refer to the published source. Please note that access to the published version might require a subscription. Chalmers Publication Library (CPL) offers the possibility of retrieving research publications produced at Chalmers University of Technology. It covers all types of publications: articles, dissertations, licentiate theses, masters theses, conference papers, reports etc. Since 2006 it is the official tool for Chalmers official publication statistics. To ensure that Chalmers research results are disseminated as widely as possible, an Open Access Policy has been adopted. The CPL service is administrated and maintained by Chalmers Library. (article starts on next page) PARAMETRIC ANALYSIS OF A LARGE-SCALE CYCLOIDAL ROTOR IN HOVERING CONDITIONS Carlos M. Xisto (corresponding author)1, J. A. Leger 2, J. C. P´ascoa 3, L. Gagnon4, P. Masarati 5, D. Angeli6 and A. Dumas 7 ABSTRACT In this work, four key design parameters of cycloidal rotors, namely the airfoil section; the number of blades; the chord-to-radius ratio; and the pitching axis location, are addressed. -
SBIR A02.07: VTOL to Transonic Aircraft
Acuity Technologies Proprietary SBIR A02.07: VTOL to Transonic Aircraft Final Technical Report July 24, 2006 Acuity Technologies Inc. Principal Investigator: Robert Clark 3475 Edison Way Unit P Menlo Park, CA 94025 650-369-6783 Issued by NASA Dryden Flight Research Center PO Box 273, Mailstop 1422 Edwards, California 93523-0273 Attn: Michelle L. Vial, (661) 276-3513 Contract No. NND06AA26C Effective Date: 1/26/2006 Technical Liaison Richard Maine 661-276-3316 [email protected] SBIR Rights Notice (Mar 1994) These SBIR data are furnished with SBIR rights under Contract No. NND06AA26C. For a period of 4 years after acceptance of all items to be delivered under this contract, the Government agrees to use these data for Government purposes only, and they shall not be disclosed outside the Government (including disclosure for procurement purposes) during such period without permission of the Contractor, except that, subject to the foregoing use and disclosure prohibitions, such data may be disclosed for use by support Contractors. After the aforesaid 4-year period the Government has a royalty-free license to use, and to authorize others to use on its behalf, these data for Government purposes, but is relieved of all disclosure prohibitions and assumes no liability for unauthorized use of these data by third parties. This Notice shall be affixed to any reproductions of these data, in whole or in part.” The views and conclusions contained in this document are those of the authors and should not be interpreted as representing the official policies, either express or implied, of NASA or the U.S. -
Replace with Your Title
Journal of Aeronautical History Paper 2021/01 Ludwig, Rudolf and Emil Rüb – Forgotten German Aeronautical and Rotating-Wing Pioneers Berend G. van der Wall Senior Scientist German Aerospace Center (DLR), Braunschweig, Germany ABSTRACT Ludwig Rudolf Rüb, a passionate inventor and enthusiastic – but mostly under-funded – visionary lived in poverty most of his life and is virtually unknown in the rotorcraft community. His first inventions covered combustion engines and motorcycles. Around 1900 he built a paddle-wheel plane under contract to Count Zeppelin, next he designed and built a first version of a coaxial rotor helicopter in Munich, and then he moved to Augsburg to build a large fixed-wing aircraft. None of these were ever finished. At the beginning of the First World War, with support of the German army, he took up a refined version of his coaxial rotor helicopter concept as a highly agile and maneuverable replacement of the observation balloons used in those times, which also was intended to take an active part in warfare by installing a machine gun or dropping bombs. It included some astonishing advanced features and, with the help of his sons, construction was finished and ground testing started in June 1918. The end of the war immediately stopped all work. The Treaty of Versailles demanded the destruction of that vehicle, bringing an end to Rüb’s aeronautical work. Ludwig Rüb, a bright yet uneducated person with good ideas, died in 1918 without having seen his rotors turning. 1. INTRODUCTION An inventor par excellence subordinates all other matters of life – Ludwig Rudolf Rüb (the middle name is rarely mentioned) was given that characterization by his son Rudolf in his unpublished life memories of 108 pages (1). -
Personal Air Vehicle & VTOL
PERSPECTIVEPERSPECTIVE ARTICLE 21(69), July 1, 2014 ISSN 2278–5469 EISSN 2278–5450 Discovery Personal Air Vehicle & VTOL: An Insight Ravi Katukam҉ Convener Engineering Innovation, Cyient Limited, Hyderabad, India ҉Corresponding author: Convener Engineering Innovation, Cyient Limited, Hyderabad, India; Email: [email protected] Publication History Received: 06 May 2014 Accepted: 13 June 2014 Published: 1 July 2014 Citation Ravi Katukam. Personal Air Vehicle & VTOL: An Insight. Discovery, 2014, 21(69), 128-134 Publication License This work is licensed under a Creative Commons Attribution 4.0 International License. General Note Article is recommended to print as color digital version in recycled paper. ABSTRACT The rapid progress seen in the areas of Science and Technology have not resolved even some of our basic transportation issues. The challenges only seem to have increased with the passage of time. The ever increasing population coupled with the increasing trends of transportation requirements is pushing the scientists and the R&D engineers across the globe to invent and discover more efficient aircrafts which are not only eco-friendly but also provide a convenient and cost effective means of transportation of man and material. The evolution of Personal Air Vehicles (PAV) is expected to provide a possible solution for this problem. The design of the PAV was evolved from the appearance of a flightless bird named Puffin which is eco-friendly in nature and so, its structure is incorporated in the basic skeleton of the vehicles by few scientists. The striking appearance includes an unusual landing tail sitter which has its landing gear covered while it is in flight mode. -
Amphibious Aircrafts
Amphibious Aircrafts ...a short overview i Title: Amphibious Aircrafts Subtitle: ...a short overview Created on: 2010-06-11 09:48 (CET) Produced by: PediaPress GmbH, Boppstrasse 64, Mainz, Germany, http://pediapress.com/ The content within this book was generated collaboratively by volunteers. Please be advised that nothing found here has necessarily been reviewed by people with the expertise required to provide you with complete, accurate or reliable information. Some information in this book may be misleading or simply wrong. PediaPress does not guarantee the validity of the information found here. If you need specific advice (for example, medical, legal, financial, or risk management) please seek a professional who is licensed or knowledge- able in that area. Sources, licenses and contributors of the articles and images are listed in the section entitled ”References”. Parts of the books may be licensed under the GNU Free Documentation License. A copy of this license is included in the section entitled ”GNU Free Documentation License” All third-party trademarks used belong to their respective owners. collection id: pdf writer version: 0.9.3 mwlib version: 0.12.13 ii Contents Articles 1 Introduction 1 Amphibious aircraft . 1 Technical Aspects 5 Propeller.............................. 5 Turboprop ............................. 24 Wing configuration . 30 Lift-to-drag ratio . 44 Thrust . 47 Aircrafts 53 J2F Duck . 53 ShinMaywa US-1A . 59 LakeAircraft............................ 62 PBYCatalina............................ 65 KawanishiH6K .......................... 83 Appendix 87 References ............................. 87 Article Sources and Contributors . 91 Image Sources, Licenses and Contributors . 92 iii Article Licenses 97 Index 103 iv Introduction Amphibious aircraft Amphibious aircraft Canadair CL-415 operating on ”Fire watch” out of Red Lake, Ontario, c. -
(2017) Improving the Aerodynamic Performance of a Cycloidal Rotor Through Active Compliant Morphing
Ferrier, L., Vezza, M. and Zare-Behtash, H. (2017) Improving the aerodynamic performance of a cycloidal rotor through active compliant morphing. Aeronautical Journal, 121(1241), pp. 901- 915. (doi:10.1017/aer.2017.34) This is the author’s final accepted version. There may be differences between this version and the published version. You are advised to consult the publisher’s version if you wish to cite from it. http://eprints.gla.ac.uk/138205/ Deposited on: 08 June 2017 Enlighten – Research publications by members of the University of Glasgow http://eprints.gla.ac.uk33640 Improving the Aerodynamic Performance of a Cycloidal Rotor through Active Compliant Morphing Liam Ferrier, Marco Vezza, and Hossein Zare-Behtash School of Engineering, University of Glasgow, Scotland G12 8QQ, UK PhD student, [email protected] Abstract Cycloidal rotors are a novel form of propulsion system which can be adapted to various forms of transport such as air and marine vehicles, with a geometrical design differing significantly from the conventional screw propeller. Research on cycloidal rotor design began in the early 1930s and has developed throughout the years to the point where such devices now operate as propulsion systems for various aerospace applications such as MAVs, UAVs and compound helicopters. The majority of research conducted on the cycloidal rotor's aerodynamic performance have not assessed mitigating the dynamic stall effect which can have a negative impact on the rotor performance when the blades operate in the rotor retreating side. A solution has been proposed to mitigate the dynamic stall effect through employment of active, compliant leading edge morphing. -
Project Final Report
Cycloidal Rotor Optimized for Propulsion Project Final Report Grant Agreement number: 323047 Project acronym: CROP Project title: Cycloidal Rotor Optimized for Propulsion Data of latest version of Annex I against which the assessment will be made: Final report: ■ Period covered: from 01/01/2013 to 31/12/2014 Name, title and organisation of the scientific representative of the project’s coordinator: Prof. Dr. José Pascoa, Universidade da Beira Interior (UBI), Covilhã, Portugal Tel: +351 275329763 E-mail: [email protected] Cycloidal Rotor Optimized for Propulsion 4.1Final publishable report 4.1.1 Executive summary In CROP project the preliminary design of a radically different propulsion system for aerial vehicles was achieved. The CROP concept is environmentally friendly and can be implemented in existing aircraft designs, which can be considered a key element for its rapid deployment into the air transport industry. It was indeed the resulting “crop” from a large scope of scientific developments that enabled to present this concept as feasible. The project have demonstrated the possibility of a novel propulsion system based on the cycloidal device referred as PECyT (acronym of “Plasma Enhanced Cycloidal Thruster”). With PECyT, CROP have shown that it is possible to conjugate the benefits of the strong unsteadiness of the flow with a plasma based boundary layer control. 4.1.2 Project context and the main objective The project scientific approach relies upon CFD simulations coupled with experimental validation in order to prove the feasibility of the system and to define the optimal configurations, the operative regimes and the possible limitations related to its application.