1 Introduction
Total Page:16
File Type:pdf, Size:1020Kb
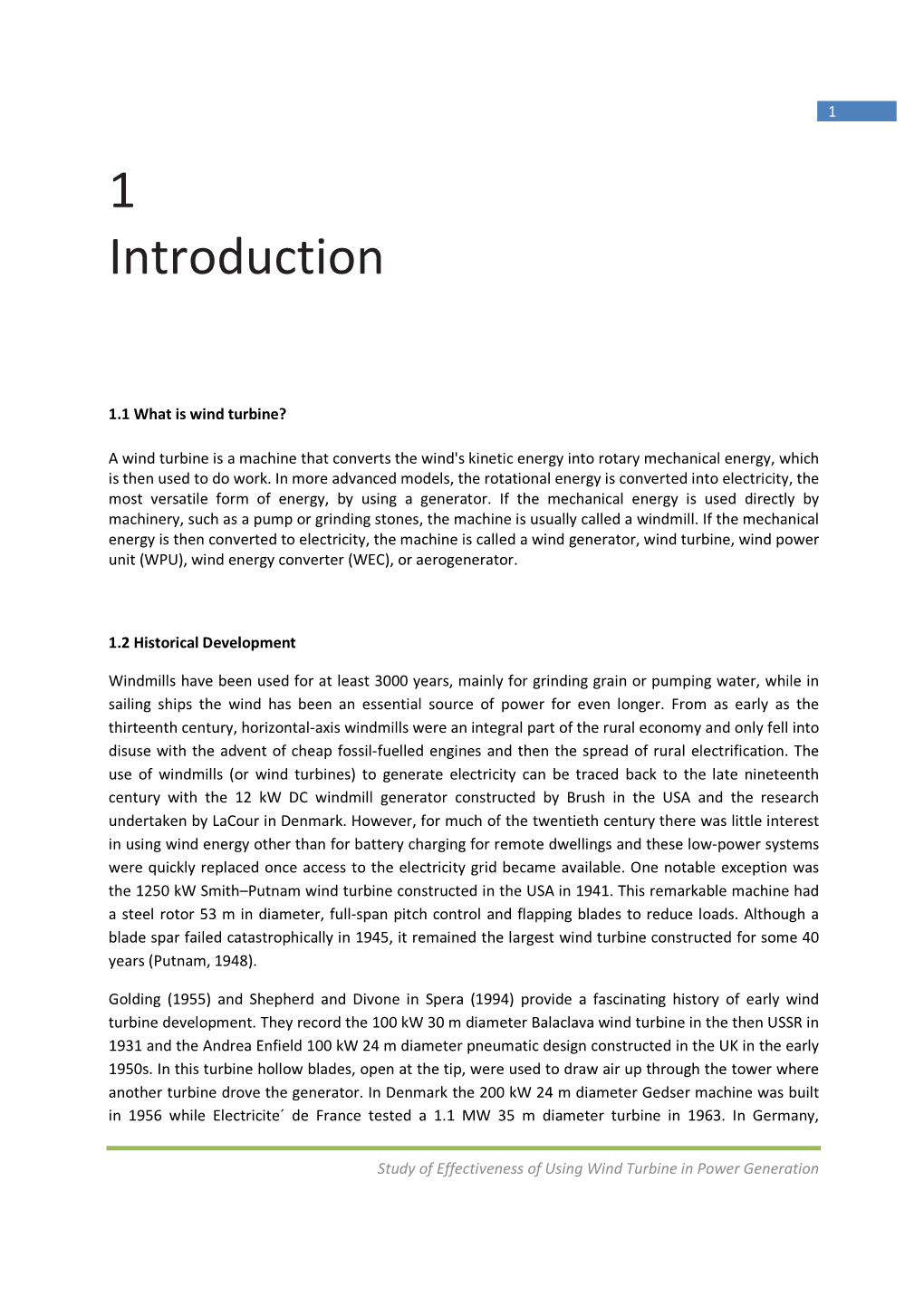
Load more
Recommended publications
-
Analyzing the Energy Industry in United States
+44 20 8123 2220 [email protected] Analyzing the Energy Industry in United States https://marketpublishers.com/r/AC4983D1366EN.html Date: June 2012 Pages: 700 Price: US$ 450.00 (Single User License) ID: AC4983D1366EN Abstracts The global energy industry has explored many options to meet the growing energy needs of industrialized economies wherein production demands are to be met with supply of power from varied energy resources worldwide. There has been a clearer realization of the finite nature of oil resources and the ever higher pushing demand for energy. The world has yet to stabilize on the complex geopolitical undercurrents which influence the oil and gas production as well as supply strategies globally. Aruvian's R'search’s report – Analyzing the Energy Industry in United States - analyzes the scope of American energy production from varied traditional sources as well as the developing renewable energy sources. In view of understanding energy transactions, the report also studies the revenue returns for investors in various energy channels which manifest themselves in American energy demand and supply dynamics. In depth view has been provided in this report of US oil, electricity, natural gas, nuclear power, coal, wind, and hydroelectric sectors. The various geopolitical interests and intentions governing the exploitation, production, trade and supply of these resources for energy production has also been analyzed by this report in a non-partisan manner. The report starts with a descriptive base analysis of the characteristics of the global energy industry in terms of economic quantity of demand. The drivers of demand and the traditional resources which are used to fulfill this demand are explained along with the emerging mandate of nuclear energy. -
Jp Elektroprivrede Hz Herceg Bosne
Vjesnik JP ELEKTROPRIVREDE HZ HERCEG BOSNE CHE Čapljina – 30 godina www.ephzhb.ba INFORMATIVNO - STRUČNI LIST / Godina X. / Broj 44 / Mostar, srpanj 2009. Informativno-stručni list, Vjesnik Glavni i odgovorni urednik: JP Elektroprivreda HZ HB d.d., Mostar Vlatko Međugorac Izdaje: Uredništvo: Sektor za odnose s javnošću Vlatko Međugorac, Mira Radivojević, mr. sc. Irina Budimir, Vanda Rajić, Zoran Pavić Ulica dr. Mile Budaka 106A, Mostar tel.: 036 335-727 Naklada: 800 primjeraka faks: 036 335-779 e-mail: [email protected] Tisak: www.ephzhb.ba FRAM-ZIRAL, Mostar Rukopisi i fotografije se ne vraćaju. 2 INFORMATIVNO STRUČNI LIST JAVNOGA PODUZEĆA ELEKTROPRIVREDE HZ HERCEG BOSNE Sadržaj Novim informacijskim sustavom (SAP-om) do boljega poslovanja .......4 Održana VII. skupština Elektroprivrede HZ HB ................................7 Izvješće neovisnoga revizora ..................................................................8 str. 4 Potpisani ugovori o istražnim radovima na CHE Vrilo.......................10 Elektroprivreda i liberalizacija tržišta ..................................................11 30. rođendan CHE Čapljina ...............................................................13 Posjet njemačkoga veleposlanika i predstavnika KfW banke hidroelektrani Rama ............................................................................14 Primjena novih Općih uvjeta i Pravilnika o priključcima ....................16 HE Mostarsko Blato u izgradnji .........................................................17 str. 7 Uspješno provedena -
Renewable Energy in Small Islands
Renewable Energy on Small Islands Second edition august 2000 Sponsored by: Renewable Energy on Small Islands Second Edition Author: Thomas Lynge Jensen, Forum for Energy and Development (FED) Layout: GrafiCO/Ole Jensen, +45 35 36 29 43 Cover photos: Upper left: A 55 kW wind turbine of the Danish island of Aeroe. Photo provided by Aeroe Energy and Environmental Office. Middle left: Solar water heaters on the Danish island of Aeroe. Photo provided by Aeroe Energy and Environmental Office. Upper right: Photovoltaic installation on Marie Galante Island, Guadeloupe, French West Indies. Photo provided by ADEME Guadeloupe. Middle right: Waiah hydropower plant on Hawaii-island. Photo provided by Energy, Resource & Technology Division, State of Hawaii, USA Lower right: Four 60 kW VERGNET wind turbines on Marie Galante Island, Guadeloupe, French West Indies. Photo provided by ADEME Guadeloupe. Printing: Vesterkopi Printing cover; Green Graphic No. printed: 200 ISBN: 87-90502-03-5 Copyright (c) 2000 by Forum for Energy and Development (FED) Feel free to use the information in the report, but please state the source. Renewable Energy on Small Islands – Second Edition August 2000 Table of Contents Table of Contents Foreword and Acknowledgements by the Author i Introduction iii Executive Summary v 1. The North Atlantic Ocean Azores (Portugal) 1 Canary Island (Spain) 5 Cape Verde 9 Faeroe Islands (Denmark) 11 Madeira (Portugal) 13 Pellworm (Germany) 17 St. Pierre and Miquelon (France) 19 2. The South Atlantic Ocean Ascension Island (UK) 21 St. Helena Island (UK) 23 3. The Baltic Sea Aeroe (Denmark) 25 Gotland (Sweden) 31 Samsoe (Denmark) 35 4. -
Solutions for Energy Crisis in Pakistan I
Solutions for Energy Crisis in Pakistan i ii Solutions for Energy Crisis in Pakistan Solutions for Energy Crisis in Pakistan iii ACKNOWLEDGEMENTS This volume is based on papers presented at the two-day national conference on the topical and vital theme of Solutions for Energy Crisis in Pakistan held on May 15-16, 2013 at Islamabad Hotel, Islamabad. The Conference was jointly organised by the Islamabad Policy Research Institute (IPRI) and the Hanns Seidel Foundation, (HSF) Islamabad. The organisers of the Conference are especially thankful to Mr. Kristof W. Duwaerts, Country Representative, HSF, Islamabad, for his co-operation and sharing the financial expense of the Conference. For the papers presented in this volume, we are grateful to all participants, as well as the chairpersons of the different sessions, who took time out from their busy schedules to preside over the proceedings. We are also thankful to the scholars, students and professionals who accepted our invitation to participate in the Conference. All members of IPRI staff — Amjad Saleem, Shazad Ahmad, Noreen Hameed, Shazia Khurshid, and Muhammad Iqbal — worked as a team to make this Conference a success. Saira Rehman, Assistant Editor, IPRI did well as stage secretary. All efforts were made to make the Conference as productive and result oriented as possible. However, if there were areas left wanting in some respect the Conference management owns responsibility for that. iv Solutions for Energy Crisis in Pakistan ACRONYMS ADB Asian Development Bank Bcf Billion Cubic Feet BCMA -
Renewable Generation Data for European Energy System Analysis
Renewable Generation Data for European Energy System Analysis Alexander Kies1, Bruno U. Schyska2, Mariia Bilousova1;3, Omar El Sayed1;3, Jakub Jurasz4;5;6, Horst Stoecker1;3;7 1Frankfurt Institute for Advanced Studies, Goethe-University Frankfurt, Ruth-Moufang-Str. 1, 60438 Frankfurt, Germany 2German Aerospace Center (DLR), Institute of Networked Energy Systems, Carl-von-Ossietzky-Straße 15, 26129 Oldenburg, Germany 3Goethe-University, Frankfurt, Germany 4Faculty of Environmental Engineering, Wroclaw University of Science and Technology, 50-370 Wroclaw, Poland 5Faculty of Management, AGH University, 30-059 Cracow, Poland 6School of Business, Society and Engineering, M¨alardalens H¨ogskola,72113 V¨aster˚as, Sweden 7GSI Helmholtzzentrum f¨urSchwerionenforschung, Planckstraße 1, 64291 Darmstadt, Germany Abstract In the process of decarbonization, the global energy mix is shifting from fossil fuels to renewables. To study decarbonization pathways, large-scale energy system models are utilized. These models require accurate data on renewable generation to develop their full potential. Using different data can lead to conflicting results and policy advice. In this work, we compare several datasets that are commonly used to study the transition towards highly renewable European power system. We find significant differences between these datasets and cost-difference of about 10% result in the different energy mix. We conclude that much more attention must be paid to the large uncertainties of the input data. Keywords: Energy System Analysis, Renewable Generation Data, Energy arXiv:2101.08741v1 [physics.soc-ph] 21 Jan 2021 Meteorology, MERRA-2, ERA5, renewables.ninja, EMHires Preprint submitted to Journal Name January 22, 2021 1. Introduction Sustainable energy sources are a major solution for the imminent thread of climate change [1, 2]. -
Power and Wind Shear Implications of Large Wind Turbine Scenarios in the US Central Plains
energies Article Power and Wind Shear Implications of Large Wind Turbine Scenarios in the US Central Plains Rebecca J. Barthelmie 1,* , Tristan J. Shepherd 2 , Jeanie A. Aird 1 and Sara C. Pryor 2 1 Sibley School of Mechanical and Aerospace Engineering, Cornell University, Ithaca, NY 14853, USA; [email protected] 2 Department of Earth and Atmospheric Sciences, Cornell University, Ithaca, NY 14853, USA; [email protected] (T.J.S.); [email protected] (S.C.P.) * Correspondence: [email protected] Received: 13 July 2020; Accepted: 11 August 2020; Published: 18 August 2020 Abstract: Continued growth of wind turbine physical dimensions is examined in terms of the implications for wind speed, power and shear across the rotor plane. High-resolution simulations with the Weather Research and Forecasting model are used to generate statistics of wind speed profiles for scenarios of current and future wind turbines. The nine-month simulations, focused on the eastern Central Plains, show that the power scales broadly as expected with the increase in rotor diameter (D) and wind speeds at hub-height (H). Increasing wind turbine dimensions from current values (approximately H = 100 m, D = 100 m) to those of the new International Energy Agency reference wind turbine (H = 150 m, D = 240 m), the power across the rotor plane increases 7.1 times. The mean domain-wide wind shear exponent (α) decreases from 0.21 (H = 100 m, D = 100 m) to 0.19 for the largest wind turbine scenario considered (H = 168 m, D = 248 m) and the frequency of extreme positive shear (α > 0.2) declines from 48% to 38% of 10-min periods. -
Offshore Technology Yearbook
Offshore Technology Yearbook 2 O19 Generation V: power for generations Since we released our fi rst offshore direct drive turbines, we have been driven to offer our customers the best possible offshore solutions while maintaining low risk. Our SG 10.0-193 DD offshore wind turbine does this by integrating the combined knowledge of almost 30 years of industry experience. With 94 m long blades and a 10 MW capacity, it generates ~30 % more energy per year compared to its predecessor. So that together, we can provide power for generations. www.siemensgamesa.com 2 O19 20 June 2019 03 elcome to reNEWS Offshore Technology are also becoming more capable and the scope of Yearbook 2019, the fourth edition of contracts more advanced as the industry seeks to Wour comprehensive reference for the drive down costs ever further. hardware and assets required to deliver an As the growth of the offshore wind industry offshore wind farm. continues apace, so does OTY. Building on previous The offshore wind industry is undergoing growth OTYs, this 100-page edition includes a section on in every aspect of the sector and that is reflected in crew transfer vessel operators, which play a vital this latest edition of OTY. Turbines and foundations role in servicing the industry. are getting physically larger and so are the vessels As these pages document, CTVs and their used to install and service them. operators are evolving to meet the changing needs The growing geographical spread of the sector of the offshore wind development community. So is leading to new players in the fabrication space too are suppliers of installation vessels, cable-lay springing up and players in other markets entering vessels, turbines and other components. -
Eco-Collaboration Between Higher Education and Ecovillages A
Partnerships for Sustainability: Eco-Collaboration between Higher Education and Ecovillages A PROJECT SUBMITTED TO THE FACULTY OF THE GRADUATE SCHOOL OF THE UNIVERSITY OF MINNESOTA BY Kiernan Jeanette Gladman IN PARTIAL FULFILLMENT OF THE REQUIREMENTS FOR THE DEGREE OF MASTER OF LIBERAL STUDIES February 2014 ©Kiernan Jeanette Gladman 2014 For John May the soles of our shoes wear down together. i Paradise (John Prine) When I was a child, my family would travel Down to western Kentucky where my parents were born And there's a backwards old town that's often remembered So many times that my memories are worn Chorus: And Daddy, won't you take me back to Muhlenberg County Down by the Green River where Paradise lay Well, I'm sorry, my son, but you're too late in asking Mister Peabody's coal train has hauled it away Well sometimes we'd travel right down the Green River To the abandoned old prison down by Adrie Hill Where the air smelled like snakes and we'd shoot with our pistols But empty pop bottles was all we would kill Chorus And the coal company came with the world's largest shovel And they tortured the timber and stripped all the land Well, they dug for their coal till the land was forsaken Then they wrote it all down as the progress of man Chorus When I die let my ashes float down the Green River Let my soul roll on up to the Rochester dam I'll be halfway to Heaven with Paradise waitin' Just five miles away from wherever I am Chorus ii CONTENTS ILLUSTRATIONS ............................................................................................................... -
Ecovillage Community Hostel “Living Space Inspired by Nature Connection for Youth and the Young at Heart to Transform”
EcoVillage Community Hostel “Living space inspired by nature connection for youth and the young at heart to transform” Findhorn EcoVillage: Findhorn Ecovillage is an experimental architectural community based at The Park, in Moray, Scotland, near the village of Findhorn. The project's main aim is to demonstrate a sustainable development in environmental, social, and economic terms. Findhorn Foundation, founded in 1962 is a “dynamic experiment where everyday life is guided by the inner voice of spirit, where we work in co-creation with the intelligence of nature and take inspired action towards our vision of a better world. Findhorn Foundation shares learning and way of life in experiential workshops, conferences and events that take place within a thriving community and ecovillage” Demand Findhorn Ecovillage enjoys 4,000 attendees at programmes and conferences and around 10,000 visitors each year and generates over £5m for the local economy each year. Orignally the Findhorn Foundation encompassed all areas of community life and ran all courses, programmes and facilities. Today there is a thriving community of around 600 people (NFA estimate) connected to Findhorn EcoVillage with its 35 independent organisations. Findhorn Foundation has over 50,000 followers across the world on Facebook. New accommodation is needed ● To replace capacity being lost with the change of use of various bed and breakfast facilities ● Visiting friends and family as part of the expanding local community ● Overflow for conferences, events and festivals several times -
3.8.5.Post0+Ug.Gdd887c5.D20201118
InVEST User’s Guide, Release 3.8.5.post0+ug.gdd887c5.d20201118 InVEST User’s Guide Integrated Valuation of Ecosystem Services and Tradeoffs Version 3.8.5.post0+ug.gdd887c5.d20201118 Editors: Richard Sharp, James Douglass, Stacie Wolny. Contributing Authors: Katie Arkema, Joey Bernhardt, Will Bierbower, Nicholas Chaumont, Douglas Denu, James Douglass, David Fisher, Kathryn Glowinski, Robert Griffin, Gregory Guannel, Anne Guerry, Justin Johnson, Perrine Hamel, Christina Kennedy, Chong-Ki Kim, Martin Lacayo, Eric Lonsdorf, Lisa Mandle, Lauren Rogers, Richard Sharp, Jodie Toft, Gregory Verutes, Adrian L. Vogl, Stacie Wolny, Spencer Wood. Citation: Sharp, R., Douglass, J., Wolny, S., Arkema, K., Bernhardt, J., Bierbower, W., Chaumont, N., Denu, D., Fisher, D., Glowinski, K., Griffin, R., Guannel, G., Guerry, A., Johnson, J., Hamel, P., Kennedy, C., Kim, C.K., Lacayo, M., Lonsdorf, E., Mandle, L., Rogers, L., Toft, J., Verutes, G., Vogl, A. L., and Wood, S. 2020, InVEST 3.8.5.post0+ug.gdd887c5.d20201118 User’s Guide. The Natural Capital Project, Stanford University, University of Minnesota, The Nature Conservancy, and World Wildlife Fund. 1 InVEST User’s Guide, Release 3.8.5.post0+ug.gdd887c5.d20201118 2 CONTENTS 1 Introduction 5 1.1 Data Requirements and Outputs Summary Table............................5 1.2 Why we need tools to map and value ecosystem services........................5 1.2.1 Introduction...........................................5 1.2.2 Who should use InVEST?...................................5 1.2.3 Introduction to InVEST..................................... 10 1.2.4 Using InVEST to Inform Decisions.............................. 12 1.2.5 A work in progress....................................... 15 1.2.6 This guide............................................ 15 1.3 Getting Started............................................. -
Unlocking the Potential of Biomass Energy in Pakistan
University of Birmingham Unlocking the potential of biomass energy in Pakistan Saghir, Muhammad; Zafar, Shagufta ; Tahir, Amiza ; Ouadi, Miloud; Siddique, Beenish; Hornung, Andreas DOI: 10.3389/fenrg.2019.00024 License: Creative Commons: Attribution (CC BY) Document Version Publisher's PDF, also known as Version of record Citation for published version (Harvard): Saghir, M, Zafar, S, Tahir, A, Ouadi, M, Siddique, B & Hornung, A 2019, 'Unlocking the potential of biomass energy in Pakistan', Frontiers in Energy Research. https://doi.org/10.3389/fenrg.2019.00024 Link to publication on Research at Birmingham portal Publisher Rights Statement: Checked for eligibility: 04/04/2019 First published by Frontiers Media Saghir M, Zafar S, Tahir A, Ouadi M, Siddique B and Hornung A (2019) Unlocking the Potential of Biomass Energy in Pakistan. Front. Energy Res. 7:24. doi: 10.3389/fenrg.2019.00024 General rights Unless a licence is specified above, all rights (including copyright and moral rights) in this document are retained by the authors and/or the copyright holders. The express permission of the copyright holder must be obtained for any use of this material other than for purposes permitted by law. •Users may freely distribute the URL that is used to identify this publication. •Users may download and/or print one copy of the publication from the University of Birmingham research portal for the purpose of private study or non-commercial research. •User may use extracts from the document in line with the concept of ‘fair dealing’ under the Copyright, Designs and Patents Act 1988 (?) •Users may not further distribute the material nor use it for the purposes of commercial gain. -
Findhorn Ecovillage Demonstration Site 1
Maria Cooper Duneland shareholder representing Findhorn community youth April 2019 Findhorn Ecovillage Demonstration Site A proposal for North Whins off grid site My vision is a site which serves as: a learning centre through demonstration of small-scale ecovillage technologies and solutions; an entrance point for young people to the community through volunteering/woofing; a safe environment for children and youth to immerse themselves in practical ecovillage life experience; and a space open for community members of all ages to engage with ecovillage ideas and concepts. It would be sponsored by the community, built with local volunteers and woofers, and for the benefit of the community. Physical design Building Small south facing dwelling built in locally available materials (timber frame, stone, cob), equipped with solar panels and PV, woodstove, rainwater tanks. Design: Large common space/kitchen to be used as a space for learning, produce preparation and preservation, and social hang out. Sleeping loft or similar for 2-3 people. Potentially one or two other tiny homes for more private accommodation. Compost toilets and constructed wetland for grey water Vegetable garden and Orchard Producing enough fruit and vegetables for 3-4 people throughout the year Animals Chickens/ducks Experiments with, and demonstration of, simple sustainable technologies e.g. off grid living, biochar, biogas, hot composting, permaculture, biodynamics, etc. Working with the landscape Small and slow solutions through low impact techniques would mean we stay in tune with natural rhythms and can collaborate with the natural features of the site. Social design Run by an onsite manager (myself), together with skilled volunteers/woofers As well as serving as a smallholding livelihood for the site manager, it would be an entrance point for young people who want to stay in the community short term and share/learn practical sustainability skills.