19680005421.Pdf
Total Page:16
File Type:pdf, Size:1020Kb
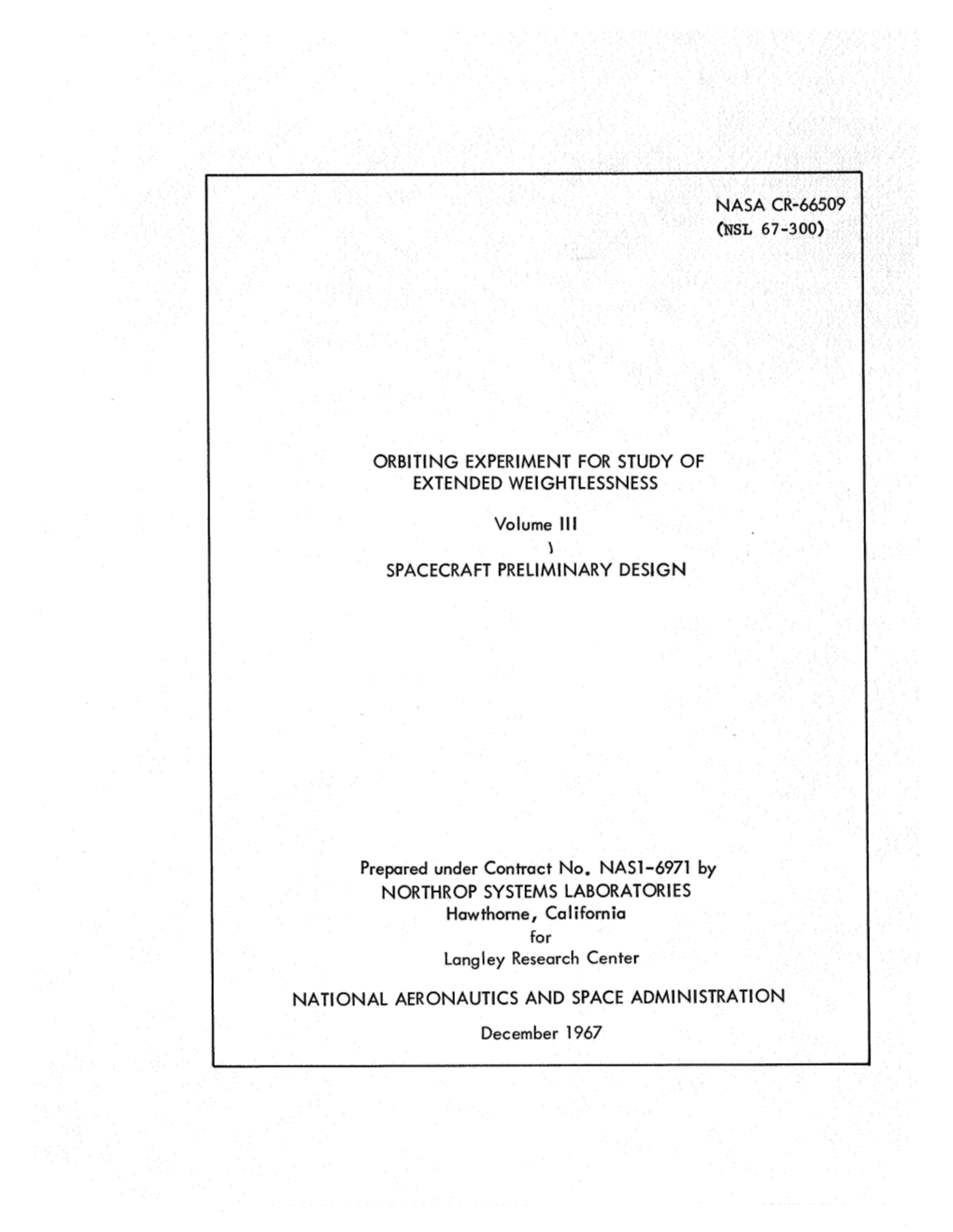
Load more
Recommended publications
-
Satcom for Net-Centric Warfare November/December 2010 Milsatmagazine
SatCom For Net-Centric Warfare November/December 2010 MilsatMagazine Ka-band Mounted Battle Command On-The-Move Photo courtesy of EM Solutions milsatmagazine pAYLOAD — nov/dec 2010 CHRONICLES intel The Orbiting Vehicles Series: OV2 + Onwards Satellites + Remotely Piloted Aircraft by Jos Heyman ......................................26 Colonel Keith W. Balts, USAF .................04 Iran: Space Launch Capabilities Tiffany Chow ........................................50 COMMAND CENTER Securing Tactical Mobile Networks Martin Roesch .......................................63 James Ramsey, President MTN Government Services MilsatMagazine Editors .........................38 focus The Antenna Challenge William Hafner & James Montgomery .....18 Enhanced Situational Awareness Rick Lober ............................................34 Enhancing Mobility Through COTM Karl Fuchs ............................................45 The Importance Of Compression Sandy Johnson ......................................58 Mission Critical Audio Conferencing Sudhir Gupta ........................................68 2 MILSATMAGAZINE — SEPTEMBER/OCTOBER 2010 Satellites + Remotely Piloted Aircraft Colonel Keith W. Balts, USAF .................04 Iran: Space Launch Capabilities Tiffany Chow ........................................50 intel Satellites + Remotely Piloted Aircraft author: Colonel Keith W. Balts, U.S.A.F. Vice-commander, 30th space wing, vandenberg afb Advances in technology allow modern in person and on the battlefield, the forces to fight battles at extreme -
10/2/95 Rev EXECUTIVE SUMMARY This Report, Entitled "Hazard
10/2/95 rev EXECUTIVE SUMMARY This report, entitled "Hazard Analysis of Commercial Space Transportation," is devoted to the review and discussion of generic hazards associated with the ground, launch, orbital and re-entry phases of space operations. Since the DOT Office of Commercial Space Transportation (OCST) has been charged with protecting the public health and safety by the Commercial Space Act of 1984 (P.L. 98-575), it must promulgate and enforce appropriate safety criteria and regulatory requirements for licensing the emerging commercial space launch industry. This report was sponsored by OCST to identify and assess prospective safety hazards associated with commercial launch activities, the involved equipment, facilities, personnel, public property, people and environment. The report presents, organizes and evaluates the technical information available in the public domain, pertaining to the nature, severity and control of prospective hazards and public risk exposure levels arising from commercial space launch activities. The US Government space- operational experience and risk control practices established at its National Ranges serve as the basis for this review and analysis. The report consists of three self-contained, but complementary, volumes focusing on Space Transportation: I. Operations; II. Hazards; and III. Risk Analysis. This Executive Summary is attached to all 3 volumes, with the text describing that volume highlighted. Volume I: Space Transportation Operations provides the technical background and terminology, as well as the issues and regulatory context, for understanding commercial space launch activities and the associated hazards. Chapter 1, The Context for a Hazard Analysis of Commercial Space Activities, discusses the purpose, scope and organization of the report in light of current national space policy and the DOT/OCST regulatory mission. -
STS-S26 Stage Set
SatCom For Net-Centric Warfare September/October 2010 MilsatMagazine STS-S26 stage set Military satellites Kodiak Island Launch Complex, photo courtesy of Alaska Aerospace Corp. PAYLOAD command center intel Colonel Carol P. Welsch, Commander Video Intelligence ..................................................26 Space Development Group, Kirtland AFB by MilsatMagazine Editors ...............................04 Zombiesats & On-Orbit Servicing by Brian Weeden .............................................38 Karl Fuchs, Vice President of Engineering HI-CAP Satellites iDirect Government Technologies by Bruce Rowe ................................................62 by MilsatMagazine Editors ...............................32 The Orbiting Vehicle Series (OV1) by Jos Heyman ................................................82 Brig. General Robert T. Osterhaler, U.S.A.F. (Ret.) CEO, SES WORLD SKIES, U.S. Government Solutions by MilsatMagazine Editors ...............................76 India’s Missile Defense/Anti-Satellite NEXUS by Victoria Samson ..........................................82 focus Warfighter-On-The-Move by Bhumika Baksir ...........................................22 MILSATCOM For The Next Decade by Chris Hazel .................................................54 The First Line Of Defense by Angie Champsaur .......................................70 MILSATCOM In Harsh Conditions.........................89 2 MILSATMAGAZINE — SEPTEMBER/OCTOBER 2010 Video Intelligence ..................................................26 Zombiesats & On-Orbit -
Desind Finding
NATIONAL AIR AND SPACE ARCHIVES Herbert Stephen Desind Collection Accession No. 1997-0014 NASM 9A00657 National Air and Space Museum Smithsonian Institution Washington, DC Brian D. Nicklas © Smithsonian Institution, 2003 NASM Archives Desind Collection 1997-0014 Herbert Stephen Desind Collection 109 Cubic Feet, 305 Boxes Biographical Note Herbert Stephen Desind was a Washington, DC area native born on January 15, 1945, raised in Silver Spring, Maryland and educated at the University of Maryland. He obtained his BA degree in Communications at Maryland in 1967, and began working in the local public schools as a science teacher. At the time of his death, in October 1992, he was a high school teacher and a freelance writer/lecturer on spaceflight. Desind also was an avid model rocketeer, specializing in using the Estes Cineroc, a model rocket with an 8mm movie camera mounted in the nose. To many members of the National Association of Rocketry (NAR), he was known as “Mr. Cineroc.” His extensive requests worldwide for information and photographs of rocketry programs even led to a visit from FBI agents who asked him about the nature of his activities. Mr. Desind used the collection to support his writings in NAR publications, and his building scale model rockets for NAR competitions. Desind also used the material in the classroom, and in promoting model rocket clubs to foster an interest in spaceflight among his students. Desind entered the NASA Teacher in Space program in 1985, but it is not clear how far along his submission rose in the selection process. He was not a semi-finalist, although he had a strong application. -
INTRODUCTION This Study of Reentry Vehicle (RV)
INTRODUCTION This study of Reentry Vehicle (RV) systems and their associated operations was conducted for the Department of Transportation/Office of Commercial Space Transportation. The purpose of the study was to investigate and present an overview of reentry vehicle systems and to identify differences in mission requirements and operations. This includes reentry vehicle system background, system design considerations, description of past/present/future reentry systems, and hazards associated with reentry vehicles that attain orbit, reenter, and are recovered. A general literature search that included the OCST data base, NASA, Air Force, and other technical libraries and personal contact with various government or private industry organizations knowledgeable in reentry system vehicles was performed. A reference page is provided at the end of this report. A history of early manned reentry vehicle launches is shown in Appendix I. A listing of some of the agencies and companies found to be most knowledgeable in the reentry vehicle area is provided in Appendix II. The following sections provide more detailed information on reentry system vehicles. A. Background - The development of reentry vehicles began in the late 1950's due to the need for Department of Defense and Central Intelligence Agency photo reconnaissance of Soviet ICBM sites. NASA has also been involved in the use of reentry vehicles since the early 1960's, including manned space programs Mercury, Gemini and Apollo. The following sections describe the evolution of reentry system development in the United States and foreign countries: 1. Discoverer1 - The Discoverer program was of major importance because it provided a vehicle for testing orbital maneuvering capability and reentry techniques and it played a large role in enabling the first United States manned space flights to be conducted in Project Mercury. -
The Cold War and Beyond
Contents Puge FOREWORD ...................... u 1947-56 ......................... 1 1957-66 ........................ 19 1967-76 ........................ 45 1977-86 ........................ 81 1987-97 ........................ 117 iii Foreword This chronology commemorates the golden anniversary of the establishment of the United States Air Force (USAF) as an independent service. Dedicated to the men and women of the USAF past, present, and future, it records significant events and achievements from 18 September 1947 through 9 April 1997. Since its establishment, the USAF has played a significant role in the events that have shaped modem history. Initially, the reassuring drone of USAF transports announced the aerial lifeline that broke the Berlin blockade, the Cold War’s first test of wills. In the tense decades that followed, the USAF deployed a strategic force of nuclear- capable intercontinental bombers and missiles that deterred open armed conflict between the United States and the Soviet Union. During the Cold War’s deadly flash points, USAF jets roared through the skies of Korea and Southeast Asia, wresting air superiority from their communist opponents and bringing air power to the support of friendly ground forces. In the great global competition for the hearts and minds of the Third World, hundreds of USAF humanitarian missions relieved victims of war, famine, and natural disaster. The Air Force performed similar disaster relief services on the home front. Over Grenada, Panama, and Libya, the USAF participated in key contingency actions that presaged post-Cold War operations. In the aftermath of the Cold War the USAF became deeply involved in constructing a new world order. As the Soviet Union disintegrated, USAF flights succored the populations of the newly independent states. -
Classification of Geosynchrono
ESA UNCLASSIFIED - Limited Distribution ! esoc European Space Operations Centre Robert-Bosch-Strasse 5 D-64293 Darmstadt Germany T +49 (0)6151 900 F +31 (0)6151 90495 www.esa.int TECHNICAL NOTE Classification of Geosynchronous objects. Prepared by ESA Space Debris Office Reference GEN-DB-LOG-00270-OPS-SD Issue/Revision 21.0 Date of Issue 19 July 2019 Status Issued ESA UNCLASSIFIED - Limited Distribution ! Page 2/234 Classification of Geosynchronous objects. Issue Date 19 July 2019 Ref GEN-DB-LOG-00270-OPS-SD ESA UNCLASSIFIED - Limited Distribution ! Abstract This is a status report on (near) geosynchronous objects as of 1 January 2019. Based on orbital data in ESA’s DISCOS database and on orbital data provided by KIAM the situation near the geostationary ring is analysed. From 1578 objects for which orbital data are available (of which 14 are outdated, i.e. the last available state dates back to 180 or more days before the reference date), 529 are actively controlled, 831 are drifting above, below or through GEO, 195 are in a libration orbit and 21 are in a highly inclined orbit. For 2 object the status could not be determined. Furthermore, there are 60 uncontrolled objects without orbital data (of which 55 have not been catalogued). Thus the total number of known objects in the geostationary region is 1638. Finally, there are 130 rocket bodies crossing GEO. If you detect any error or if you have any comment or question please contact: Stijn Lemmens European Space Agency European Space Operations Center Space Debris Office (OPS-GR) Robert-Bosch-Str. -
19760022256.Pdf
NASA TECHNICAL NASA TM x-73073 MEMORANDUM 0 roSKYLAB LESSONS LEARNED AS APPLICABLE TO A LARGE SPACE STATION William C. Schneider Office Of Space Flight Headquarters NASA April 1976 Report On Period 1967-1974 National Aeronautics And Space Administration Washington, D. C. 20546 .76-293 4 _ ~SyyJAB LESSONS LanD - ., - X-373) _ I,, sTATION, (-&ASA-M- O A LARGE SIACB . Uiv. of JnclaS AP tIcABLEpfl Thesis pr6- 97 Ph.D. T e~ - CatholiC CSC 223 3 1 48953 1 (ASA) 286 P HC $9.25 C 9 AM 28 ?324 %C 197, P' S INDEX SUMMARY I INTRODUCTION 3 PURPOSE AND SCOPE OF PAPER 3 GENERAL DESCRIPTION 3 HISTORY OF SKYLAB 21 MISSION SUMMARY 35 SKYLAB LESSONS LEARNED 74 INTRODUCTION 74 LESSONS LEARNED 75 COMMENTS BY SKYLAB OFFICIALS 120 INTRODUCTION 120 COMMENTS 120 LETTERS 130 AXIOMS 173 CONCLUS IONS 174 ACRONYMS 177 APPENDIX I - HA-RDWARE DESCRIPTION 178 APPRENIX II - EXPERIMENT DESCRIPTION 217 REFERENCES 279 BIBLOGRAPHY 282 1. Report No. 2. Government Accession No. 3. Recipient's Catalog No. NASA TMX-73073 4. Title and Subtitle 5. Report Date April 1976 Skylab Lessons Learned As Applicable To A Large 6. Performing Organization Code Space Station 7. Author(si 8. Performing Organization Report No. William C. Schneider 10. Work Unit No. 9. Performing Organization Name and Address NASA Headquarters, Office of Space Flight 11 Contrac or Grant No. 13. Type of Report and Period Covered 12. Sponsoring Agency Name and Address Technical Memorandum pTQr7- g7a) National Aeronautics and Space Administration 14. Sponsoring Agency Code Washington, D.C. 20546 15. Supplementary Notes Report prepared for variety of purposes; History records; reference; training; dissertation for Doctoral Thesis at Catholic University of America. -
Passive Gravity- Gradient Libration Dampers
NASA NASA SP-8071 SPACE VEMCLE DESIGN CRITERIA (GUIDANCE AND CONTROL PASSIVE GRAVITY- GRADIENT LIBRATION DAMPERS e FEBRUARY 1971 NATIONAL AERONAUTICS AND SPACE ADMINISTRATION GUIDE TO THE USE OF THIS MONOGRAPH The purpose of this monograph is to organize and present, for effective use in spacecraft devel- opment, the significant experience and knowledge accumulated in development and operational programs to date. It reviews and assesses current design practices, and from them establishes firm guidance for achieving greater consistency in design, increased reliability in the end product, and greater efficiency in the design effort. The monograph is organized into three major sections that are preceded by a brief Introduction and complemented by a set of References. The State of the Art, section 2, reviews and discusses the total design problem, and identifies which design elements are involved in successful designs. It describes succinctly the current tech- nology pertaining to these elements. When detailed information is required, the best available references are cited. This section serves as a survey of the subject that provides background material and prepares a proper technological base for the Design Criteria and Recommended Practices. The Design Criteria, shown in section 3, state clearly and briefly what rule, guide, limitation, or standard must be imposed on each essential design element to insure successful design. The Design Criteria can serve effectively as a checklist for the project manager to use in guiding a design or in assessing its adequacy. The Recomniended Practices, as shown in section 4, state how to satisfy each of the criteria. When- ever possible, the best procedure is described; when this cannot be done concisely, appropriate references are provided. -
Krafft Arnold Ehricke Papers
Krafft Arnold Ehricke Papers Paul Silbermann 2014 National Air and Space Museum Archives 14390 Air & Space Museum Parkway Chantilly, VA 20151 [email protected] https://airandspace.si.edu/archives Table of Contents Collection Overview ........................................................................................................ 1 Administrative Information .............................................................................................. 1 Arrangement................................................................................................................... 21 Scope and Contents...................................................................................................... 21 Biographical/Historical note.............................................................................................. 2 Names and Subjects .................................................................................................... 23 Container Listing ........................................................................................................... 24 Series 1: Writings, Lectures, Appearances............................................................ 24 Series 2: Graphics.................................................................................................. 92 Series 3: Company Files...................................................................................... 112 Series 4: Reference Files..................................................................................... 154 Series 5: -
Environmental Research Satellite, ERS-20
Environmental Research Satellite, ERS-20 ERS-20 is a small United States Air Force material radiation research satellite that was launched as one of three secondary payloads from Cape Canaveral by a Titan 3C rocket in 1967. ERS-20 conducted a United States Air Force Rocket Propulsion Laboratory (AFRPL) material studies experiment to determine the effects of the space environment, particularly of deep vacuum and radiation, on the coefficient of friction of various materials as stainless steel, Teflon, gold and silver. Both static and sliding surface frictions were investigated. ERS-17, an example of an ORS Mark III satellite The experiment consisted of two identical assemblies mounted on opposite vertices of the satellite for redundancy. Each assembly had a sealed electric motor driving a cam that linked through a flexible bellows to sixteen wiper arms outside the satellite that swept across the exposed material samples. In normal operation, wiper arm motion would occur only while the satellite is in communication with a NASA STADAN ground tracking station and upon ground command after verification of housekeeping data and at the discretion of the experimenter. This was to minimize the effects of wear on the frictional surfaces and to give greater flexibility to the experimenter. The experiment lifetime was estimated to be six months. This satellite was one of a series of environmental research satellites that were built by TRW Systems Group for the United States Air Force Office of Aerospace Research (AFOAR). The satellite is also known by the USAF designation of OV5-3, Orbital Vehicle series 5, article 3 or by the TRW designation of Octahedron Research Satellite, ORS Mark III, Item C. -
Part Iii : Space Transportation, Propulsion and Pathway Options
SICSA SPACE ARCHITECTURE SEMINAR LECTURE SERIES PART III : SPACE TRANSPORTATION, PROPULSION AND PATHWAY OPTIONS www.sicsa.uh.edu LARRY BELL, SASAKAWA INTERNATIONAL CENTER FOR SPACE ARCHITECTURE (SICSA) GERALD D.HINES COLLEGE OF ARCHITECTURE, UNIVERSITY OF HOUSTON, HOUSTON, TX The Sasakawa International Center for SICSA routinely presents its publications, Space Architecture (SICSA), an research and design results and other organization attached to the University of information materials on its website Houston’s Gerald D. Hines College of (www.sicsa.uh.edu). This is done as a free Architecture, offers advanced courses service to other interested institutions and that address a broad range of space individuals throughout the world who share our systems research and design topics. In interests. 2003 SICSA and the college initiated Earth’s first MS-Space Architecture This report is offered in a PowerPoint format with degree program, an interdisciplinary 30 the dedicated intent to be useful for academic, credit hour curriculum that is open to corporate and professional organizations who participants from many fields. Some wish to present it in group forums. The document students attend part-time while holding is the third in a series of seminar lectures that professional employment positions at SICSA has prepared as information material for NASA, affiliated aerospace corporations its own academic applications. We hope that and other companies, while others these materials will also be valuable for others complete their coursework more rapidly