Vincents Rivulet Bridge
Total Page:16
File Type:pdf, Size:1020Kb
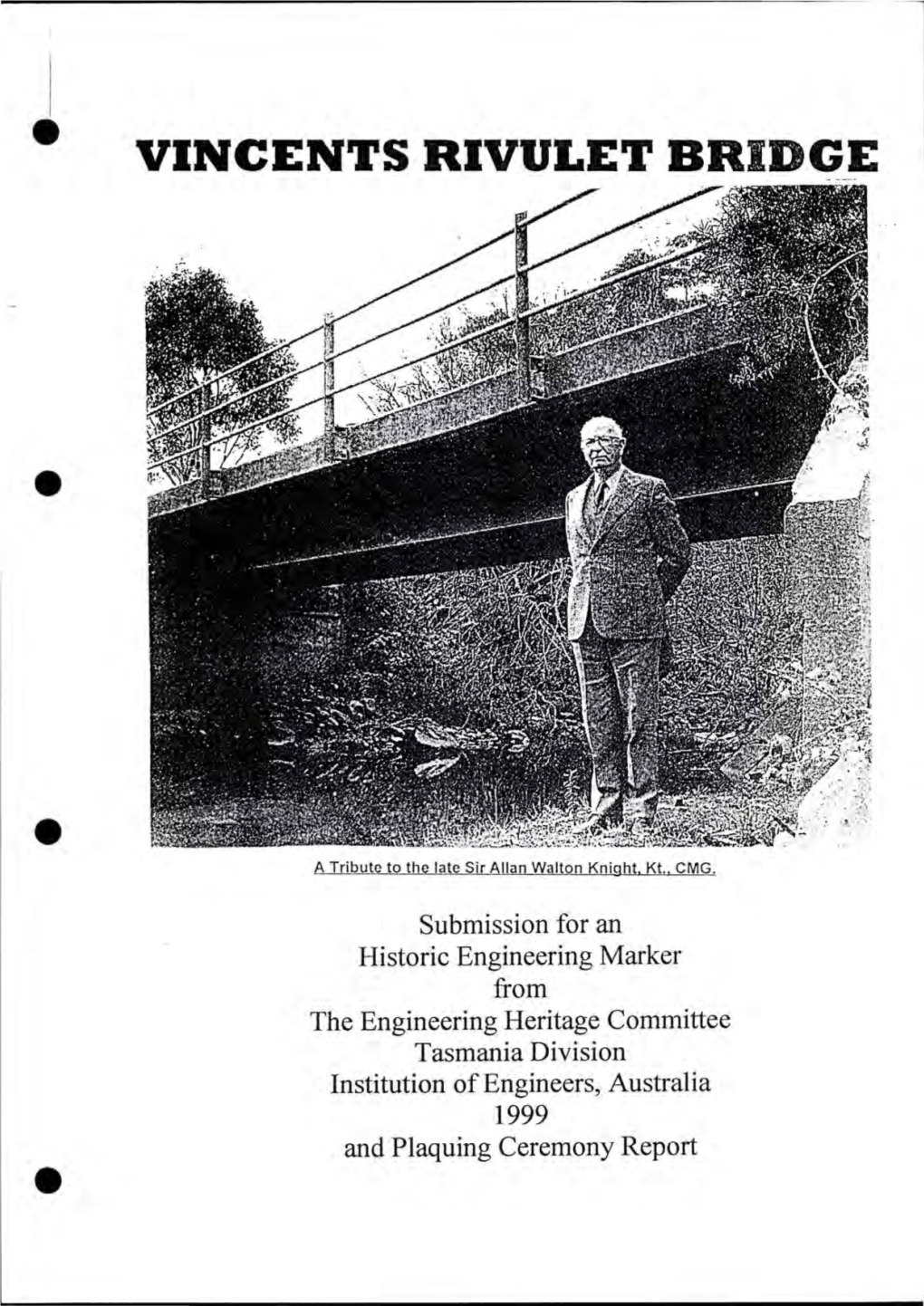
Load more
Recommended publications
-
House of Assembly Tuesday 17 March 2020
Tuesday 17 March 2020 The Speaker, Ms Hickey, took the Chair at 10 a.m., acknowledged the Traditional People and read Prayers. STATEMENT BY PREMIER COVID-19 [10.02 a.m.] Mr GUTWEIN (Bass - Premier - Statement) - Madam Speaker, we are in difficult and challenging times but I know that all of us, along with all Tasmanians, will work together to ensure the health and wellbeing of Tasmanians and importantly we will work hard to ensure that they remain in jobs. It is important that important public institutions like parliament, and also private institutions that provide services to Tasmanians, all do our bit to ensure that we can continue, taking into account effective appropriate social distancing measures. I want to thank all of the members, importantly the Leader of the Opposition, Rebecca White, and the Leader of the Greens, Cassy O'Connor, along with yourself and all of your staff for being prepared to work together to ensure that this parliament can continue with its important work. I also acknowledge the Clerks in both Houses for the work they have undertaken with the staff who work here in Parliament House to ensure that, likewise, there is appropriate social distancing and this place can continue. Madam Speaker, thank you. Statement noted. MOTION Sessional Orders - Interim Arrangements [10.04 a.m.] Mr FERGUSON (Bass - Leader of Government Business) (by leave) - Madam Speaker, before question time commences I wish to move a minor change to the Standing Orders in relation to Sessional Orders being established for an interim period. Madam Speaker, I move - That for the remainder of this session: 1. -
A Geophysical Investigation of the Derwent Estuary
A Geophysical Investigation of the Derwent Estuary David J Gibbons B. Sc. UNIVERSITY OF TASMANIA A research thesis submitted in partial fulfillment of the requirements of the Degree of Bachelor of Science with Honours School of Earth Sciences, University of Tasmania November, 2001 \. Acknowledgements (, Michael Roach, my supervisor and chief guru for your assistance, expertise and support (even if you did reckon the funny bits in the seismic were basalt!). Thanks especially for scraping together the funds for the project after the grant application got rejected. I hope you enjoyed your holiday, you certainly deserved it. (, James Reid - stand-in guru and all-around good guy - for your help and good humour, particularly in Michael's absence. Thanks also for your lessons in the dark art fortran 77. Alan Jordan and Miles Lawler from the Tasmanian Aquaculture and Fisheries " Institute, without whom this project could not have proceeded. Alan for providing' 'mates rates' for the vessels and Miles for piloting them back and forth, back and forth, back and forth....thank you both. David Mitchell from the University of Sydney, for his willingness to come to Hobart /, in the colder months (straight from the North West SheW) to conduct our seismic survey. His good humour and patience with my clumsiness ("Please don't stand on the eel, Dave!") certainly made the seismic survey a more pleasant experience than it might otherwise have been. .. Pat Quilty for his willingness to help whenever required (particularly in terms of my' literature review). Thanks also to Peter Harris, for looking at my seismic data early in the year and allowing me to use his carbonate distribution map in my thesis. -
Tasman Bridge Disaster: 25Th Anniversary Memorial Service
Tasman Bridge disaster: 25th anniversary memorial service Introduction growth in both after the opening of the The collision of the vessel ss Lake Illa- by Rod McGee, Manager Asset Strategies, bridge warra with Tasman Bridge on 5 January The bridge however suffered storm and Department of Infrastructure, Energy and 1975 had a major impact on the lives of corrosion damage and increasing traffic the people of southern Tasmania The Resources, Tasmania and Lynn Young, congestion, especially during the opera- event had a number of unique charac- State Recovery Coordinator, Department tion of the lift span As a result, consultants teristics and occurred at a time when the of Health and Human Services, Tasmania were commissioned in 1956 to investigate effects of disasters on communities were options for a bridge to replace the floating less well understood Assistance to the arch A number of bridge and tunnel community in this regard was thus stream Population growth on the eastern options were considered during the limited shore had been slow to that time, but preliminary design stage and review by An approach to the Tasmanian State accelerated after the opening of the the Parliamentary Standing Committee on Government by a local Lions Club led to a bridge generating increasing traffic Public Works Navigation issues, including memorial service to mark the 25th anni- demand Figure 1 shows population on the possibility of ship collision, were versary of the disaster This paper the eastern shore and cross river vehi- assessed comprehensively While -
Burnie to Hobart Freight Corridor Strategy Freight Demand Analysis and Future 1 Productivity Improvements
REPORT TO DEPARTMENT OF STATE GROWTH JANUARY 2017 BURNIE TO HOBART FREIGHT CORRIDOR STRATEGY FREIGHT DEMAND ANALYSIS AND FUTURE PRODUCTIVITY IMPROVEMENTS Public report ACIL ALLEN CONSULTING PTY LTD ABN 68 102 652 148 LEVEL FIFTEEN 127 CREEK STREET BRISBANE QLD 4000 AUSTRALIA T+61 7 3009 8700 F+61 7 3009 8799 LEVEL ONE 15 LONDON CIRCUIT CANBERRA ACT 2600 AUSTRALIA T+61 2 6103 8200 F+61 2 6103 8233 LEVEL NINE 60 COLLINS STREET MELBOURNE VIC 3000 AUSTRALIA T+61 3 8650 6000 F+61 3 9654 6363 LEVEL ONE 50 PITT STREET SYDNEY NSW 2000 AUSTRALIA T+61 2 8272 5100 F+61 2 9247 2455 LEVEL TWELVE, BGC CENTRE 28 THE ESPLANADE PERTH WA 6000 AUSTRALIA T+61 8 9449 9600 F+61 8 9322 3955 161 WAKEFIELD STREET ADELAIDE SA 5000 AUSTRALIA T +61 8 8122 4965 ACILALLEN.COM.AU AUTHORS SIMON SAGERER | YUAN CHOU RELIANCE AND DISCLAIMER THE PROFESSIONAL ANALYSIS AND ADVICE IN THIS REPORT HAS BEEN PREPARED BY ACIL ALLEN CONSULTING FOR THE EXCLUSIVE USE OF THE PARTY OR PARTIES TO WHOM IT IS ADDRESSED (THE ADDRESSEE) AND FOR THE PURPOSES SPECIFIED IN IT. THIS REPORT IS SUPPLIED IN GOOD FAITH AND REFLECTS THE KNOWLEDGE, EXPERTISE AND EXPERIENCE OF THE CONSULTANTS INVOLVED. THE REPORT MUST NOT BE PUBLISHED, QUOTED OR DISSEMINATED TO ANY OTHER PARTY WITHOUT ACIL ALLEN CONSULTING’S PRIOR WRITTEN CONSENT. ACIL ALLEN CONSULTING ACCEPTS NO RESPONSIBILITY WHATSOEVER FOR ANY LOSS OCCASIONED BY ANY PERSON ACTING OR REFRAINING FROM ACTION AS A RESULT OF RELIANCE ON THE REPORT, OTHER THAN THE ADDRESSEE. -
Greater Hobart Transport Data
Background Paper 3: Greater Hobart Transportation Document title 1 Contents Introduction ............................................................................................................................................ 1 Transport Corridors ............................................................................................................................... 2 Major Corridors ..................................................................................................................................... 2 Northern Corridor .............................................................................................................................. 3 Eastern Corridor ................................................................................................................................ 3 Southern Corridor .............................................................................................................................. 3 Congestion ........................................................................................................................................ 4 Hobart Traffic Origin-Destination Report 2017 ...................................................................................... 6 Morning Peak Destinations (7:30am to 9:30am) ................................................................................ 6 Afternoon Peak Origins (4:30pm to 6:30pm) ...................................................................................... 6 Conclusion ....................................................................................................................................... -
House of Assembly Wednesday 4 September 2019
Wednesday 4 September 2019 The Speaker, Ms Hickey, took the Chair at 10 a.m., acknowledged the Traditional People and read Prayers. RECOGNITION OF VISITORS Madam SPEAKER - Honourable members, it is my great privilege to welcome to parliament grade 5 and 6 students from Hagley Farm Primary School. Members - Hear, hear. QUESTIONS Tasmanian Industrial Commission - Alleged Leaking of Submission Ms WHITE question to MINISTER for JUSTICE, Ms ARCHER [10.03 a.m.] You are the minister responsible for the Tasmanian Industrial Commission. Yesterday the member for Clark, Sue Hickey, claims that her submission to the Industrial Commission arguing for an $80 000 pay rise was leaked to the media in order to damage her. Did anyone in your office, did you or anyone associated with you, leak the member for Clark's submission? ANSWER Madam Speaker, I would normally thank the Leader of the Opposition for her question. It shows they have already run out of questions in question time. They are going to the absolute gutter in terms of questions. Yes, I have responsibility for the Tasmanian Industrial Commission but to have some loose and tenuous link on this matter is really quite ludicrous and to ask your first question - Ms White - It is a yes or no answer. Madam SPEAKER - Order. Ms ARCHER - I can answer the question, no. Madam SPEAKER - Warning number one, Leader of the Opposition. Tasmanian Industrial Commission - Alleged Leaking of Submission Ms WHITE question to PREMIER, Mr HODGMAN [10.04 a.m.] Will you ask Tasmania Police to investigate allegations from the member for Clark, Sue Hickey, that her confidential submission to the Industrial Commission was leaked to the media? 1 4 September 2019 ANSWER Madam Speaker, I thank the Leader of the Opposition for the question. -
River Derwent Anglers Access
Inland Fishing Regulations Apply Protect our Waters Inland angling regulations and licensing requirements Recreational anglers have a responsibility to look after apply upstream from a straight line running from fisheries resources for the benefit of the environment River Derwent Dowsings Point on the western shore to Store Point on and future generations. the eastern shore. • Do not bring live or dead fish, fish products, animals or aquatic plants into Tasmania. Anglers • Do not bring used fishing gear or any other Angling Regulations freshwater recreational equipment that may be damp, wet or contain water into Tasmania. Check, Access To fish for all species upstream of the Bridgewater clean and dry your fishing equipment before Bridge or to take trout or Atlantic salmon downstream entering Tasmania. REGION: SOUTH of the Bridgewater Bridge to a line between Dowsings • Do not transfer any freshwater fish, frogs, tadpoles, Point and Store Point, you must hold a current Inland invertebrates or plants between inland waters. Angling Licence unless you are under 14 years of age. • Check your boat, trailer, waders and fishing gear A summary of the regulations are contained within the for weed and other pests that should not be Tasmanian Inland Fishing Code. transferred before moving between waters. • Do not use willow (which is a plant pest) as a rod Method Season support as it has the ability to propagate from a Upstream of the Bridgewater cutting. Bridge: Fly fishing From the first Saturday in August to the Sunday nearest Artificial lures the 30th April. Report any unusual fish captures or algal sightings Bait fishing Downstream of the immediately to the Inland Fisheries Service. -
Department of Premier and Cabinet
Department of State Growth Salamanca Building, Parliament Square 4 Salamanca Place, Hobart TAS 7000 GPO Box 536, Hobart TAS 7001 Australia Phone 1800 030 688 Fax (03) 6233 5800 Email [email protected] Web www.stategrowth.tas.gov.au John Ramsay Delegate (Chair) The Tasmanian Planning Commission Level 3, 144 Macquarie Street HOBART TAS 7000 By email: [email protected] Clarence draft Local Provisions Schedule hearing - further information directions Dear Mr Ramsay Responses to the directions to provide further information dated the 16 and 20 November 2020 issued to the Department of State Growth (State Growth) are set out in the attached table. Please contact Lucy Thorne, A/G Manager Planning Policy, on (03)6166 3481 or by email at [email protected] who can arrange for the relevant officers to address further questions in relation to this submission. Yours sincerely James Verrier Director Transport Systems and Planning Policy 27 November 2020 Cc: [email protected] Attachment: Further information table Attachment – Further information table Directions issued 16 November 2020 Direction Advertised maps DSG response 3.1 (a) Rural Living Zone (Area B) to Rural Living Zone (Area A) at: i. the Acton Densification of existing urban areas compared to growth in peri-urban areas is generally preferred by State Growth. It is also assumed based on Park/Cambridge existing land development controls and the relevant regional land use strategy for example, for transport network (State Roads and Passenger corridor Transport) planning purposes. State Road’s draft Rokeby Corridor Planning study for South Arm Road between Pass and Acton Roads only assumed a low growth rate in through traffic ie. -
Hartill, Eric
30/05/2020 Secretariat to PESRAC E: [email protected] Re Tasmanian economic and social recovery strategy Thank you for the opportunity to provide some suggestions and ideas for re- progressing the Tasmanian economy and social fabric. I am sure that you will be made aware of a myriad of possible projects similar in nature to a number of mine. It will be a difficult task to assess the best of those ranging from community benefit upgrades right through to state-wide mega infrastructure impacts. Given the current situation where our people are transiting out of the Covid-19 pandemic lockdown how do we now commence this undertaking? Certainly it is recognised that one of the important factors for the mental well- being of our communities will be a return to engaging in sports and the arts. It is also recognised that for our economy to return to a semblance of normality it will require proceeding with a variety of infrastructure developments. Some of these could already be termed as “shovel ready” whilst others can proceed over the ensuing budget years to achieve lasting effects. What is important to realise is that humanity has always proven resilient in its nature and that it will be quicker than many might estimate for economic upturns to occur. Which is why it is essential that we revitalise our economic situation for the new return waves of visitors who undoubtedly will be seeking us out. Therefore I wish to list the following segmental lists for consideration. A. Currently either planned or stage listed for future. -
Urban Cycling Network Hobart
Campania Principal Urban Cycling Network Hobart G l en L ea R Pontville oa t d e e r t S t Tea Tree h g i r w t Brighton r a - Mapped ACgainst PopulatiM on Density Midland Hwy Brighton i Elder dd slie R le oad #11438 T e a Enfield Tr ee R o ad B r ig g s R o a d Hill Road Dromedary Cove Road East Derwent Hwy - E of Midland Hwy Brinktop Wellington Street # 11260 Orielton Pawleena Bridgewater Richmond t Eddington Stree B la ck H i T lls S o R c tte o o n a t h d t Gagebrook a R m # o R a o Lyell Hwy w of Brooker d ad Bundella d a Brooker Nth of Rst Rd Road o 6637 Gage R l # 25685 il H Granton e e tr s s a r Magra G d a o G R len or r d a e R a o v ad i o R R h k c c a d a d e a a B o B o d R R l le a O il n rv e e e sk l d a w oa B a R P e P ad iff e o l n R d c t Road rn Lawitta rn n ugen fe a N n A a Gle o R R Austins Ferry o n Boyer a o t East Derwent Hwy nr Fouche Rd d l i H Old Beach B t ee # 6630 l r a St i h r ig Penna S H H t r u e m Sorell Creek Grasstree Hill e t p h r e Dulcot y Abbottsfield Rd/Main Rd Sorell S t A 18 r bbo (! e tsfiel e d Ro t ad Claremont d a o Intercity Cycleway/Cadbury Rd R 45 n Brooker Hwy Nth Claremont Link Rd (! a l h c 30806 # a L Malbina P e n n a R Molesworth M o a o d le s w Chigwell o r d Otago th a R o o R a a Hobart Inset d g n Risdon Vale u ll East Derwent Hwy nr Bowen Bridge A 9488 Berri Main Rd/Berriedale Rd # edale R oad ! 5 (! Glenlusk M Berrieda(le #East Derwent Hwy nr Grass Tree Hill Rd a Bowen Bridge ry Glen Dhu ad s 9 12765 Ro H k o lus p len e Brooker Hwy nr Foreshore Rd G R o a # 34030 -
Appendix K. Traffic Impact Assessment Received 21.08.2020
Received 21.08.2020 East Derwent Highway Upgrade Development Application Change the document title using the properties option on the Jacobs RibbonProject NameClient Name Appendix K. Traffic Impact Assessment Received 21.08.2020 East Derwent Highway Upgrade – Golf Links Road to Sugarloaf Road Traffic Impact Assessment IS262318 | 3 14 August 2020 Department of State Growth Traffic Impact Assessment Department of State Growth Received 21.08.2020 East Derwent Highway Upgrade Project No: IS262318 Document Title: Traffic Impact Assessment Document No.: IS262318 Revision: 2 Document Status: Final Date: 30 July 2020 Client Name: Department of State Growth Project Manager: Clayton Johnston Author: Jonathan Bryce and Cassandra Min File Name: IS262318-0000-CT-RPT-0001 Jacobs Group (Australia) Pty Limited ABN 37 001 024 095 Floor 11, 452 Flinders Street Melbourne VIC 3000 PO Box 312, Flinders Lane Melbourne VIC 8009 Australia T +61 3 8668 3000 F +61 3 8668 3001 www.jacobs.com © Copyright 2019 Jacobs Group (Australia) Pty Limited. The concepts and information contained in this document are the property of Jacobs. Use or copying of this document in whole or in part without the written permission of Jacobs constitutes an infringement of copyright. Limitation: This document has been prepared on behalf of, and for the exclusive use of Jacobs’ client, and is subject to, and issued in accordance with, the provisions of the contract between Jacobs and the client. Jacobs accepts no liability or responsibility whatsoever for, or in respect of, any use of, or reliance upon, this document by any third party. Document history and status Revision Date Description Author Checked Reviewed Approved 1.0 22/04/20 Initial Draft JB & CM MD MD SF 2.0 30/07/20 Final Version for Client Review JB & CM MD MD SF 3.0 14/08/20 Final Version JB, CM, HG MD MD CJ & NG IS262318 1 Received 21.08.2020 Contents 1. -
Engagement on Reference Design New Bridgewater Bridge Project
Engagement on Reference Design New Bridgewater Bridge Project January 2021 Contents 1 Overview ................................................................................................................................................. 3 1.1 About the Project .................................................................................................................................. 3 1.2 Purpose of consultation ........................................................................................................................ 3 1.3 Reference Design ................................................................................................................................... 3 1.4 Overview of activities ............................................................................................................................ 4 1.5 Early Contractor Involvement process .................................................................................................. 4 2 How we asked .......................................................................................................................................... 5 2.1 Online engagement ............................................................................................................................... 5 2.1.1 Project webpage .................................................................................................................................... 5 2.1.2 Social Pinpoint ......................................................................................................................................