Investigation of Inoculant Effect on Cast Iron
Total Page:16
File Type:pdf, Size:1020Kb
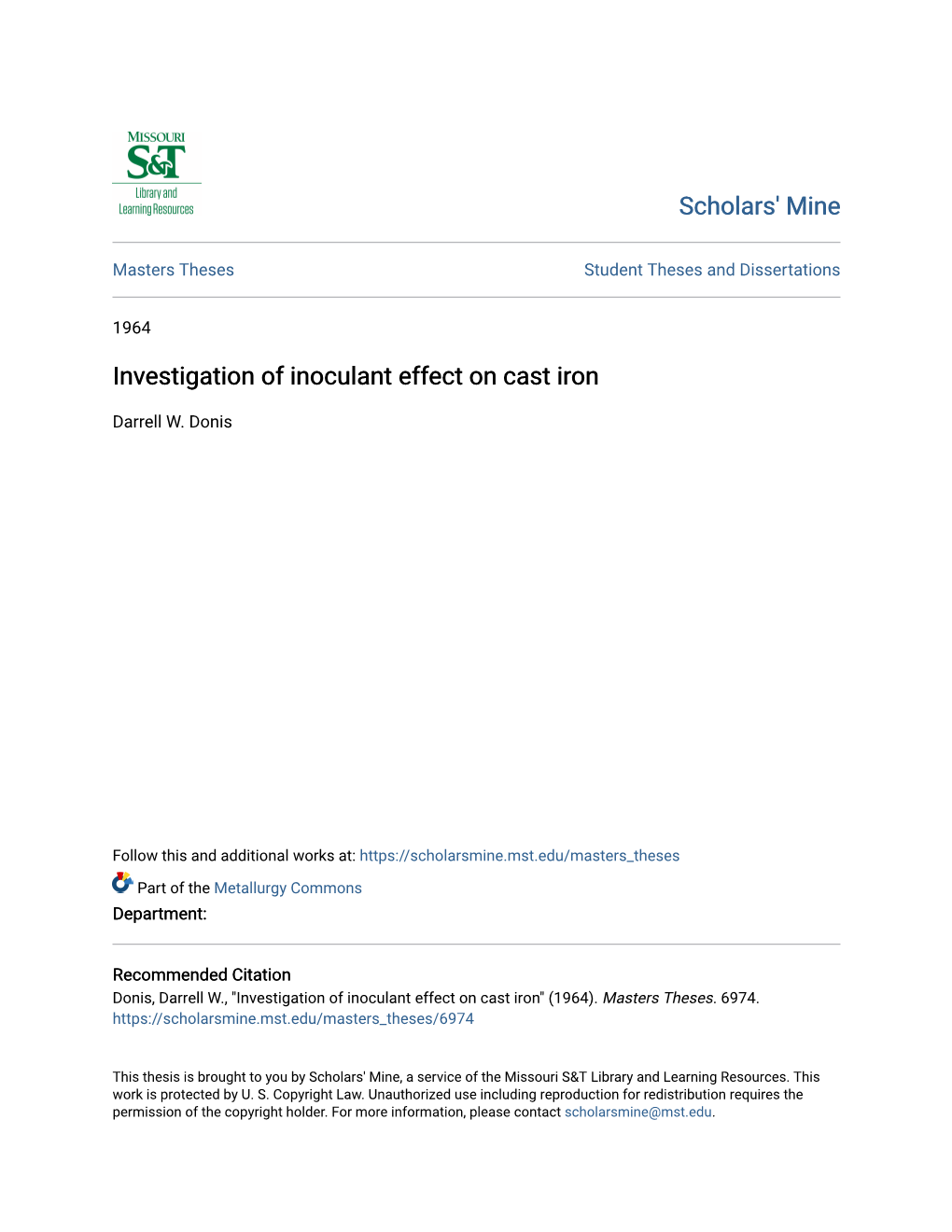
Load more
Recommended publications
-
Magnesium Ferrosilicon Alloy and Use Thereof in Manufacture of Nodular Cast Iron
:uropaisches Patentamt 0 1 08 1 07 $ QJll Europeaniuropean Patent Office ® Publication number: B 1 Office)ffice europeen des brevets g) EUROPEAN PATENT SPECIFICATION §) Date of publication of patent specification: 13.01.88 (g) int. CI.4: C 22 C 33/08 |j) Application number: 83901516.1 Date of filing: 28.03.83 ® International application number: PCT/US83/00428 @ International publication number: WO 83/03848 10.11.83 Gazette 83/26 g) MAGNESIUM FERROSILICON ALLOY AND USE THEREOF IN MANUFACTURE OF NODULAR CAST IRON. (§) Priority: 21.04.82 US 370185 (73) Proprietor: SKW ALLOYS INC. 3801 Highland Avenue Niagara Falls New York 14305 (US) (§) Date of publication of application: 16.05.84 Bulletin 84/20 ® Inventor: DREMANN, Charles Earl Buckwalter Road (§) Publication of the grant of the patent: Phoenixville, PA 19460 (US) 13.01.88 Bulletin 88/02 @ Representative: Hale, Stephen Geoffrey et al ® Designated Contracting States: J.Y. & G.W. Johnson Furnival House 14/18 High DE FR GB Holborn London WC1V 6DE (GB) (58) References cited: FR-A-2443 510 GB-A-746406 GB-A- 885 896 GB-A-1 273 319 CD US-A-2 762 705 US-A-2873188 US-A-3 537 842 O US-A-3 703 922 US-A-4004 630 US-A-4224 069 00 Note: Within nine months from the publication of the mention of the grant of the European patent, any person may give notice to the European Patent Office of opposition to the European patent granted. Notice of opposition shall CL be filed in a written reasoned statement. It shall not be deemed to have been filed until the opposition fee has been LU paid. -
Charcoal As an Alternative Reductant in Ferroalloy Production: a Review
processes Review Charcoal as an Alternative Reductant in Ferroalloy Production: A Review Gerrit Ralf Surup 1,*, Anna Trubetskaya 2 and Merete Tangstad 1 1 Department of Materials Science and Engineering, Norwegian University of Science and Technology, 7491 Trondheim, Norway; [email protected] 2 Department of Chemical Sciences, University of Limerick, V94 T9PX Castletroy, Ireland; [email protected] * Correspondence: [email protected]; Tel.: +47-934-73-184 Received: 12 October 2020; Accepted: 3 November 2020; Published: 9 November 2020 Abstract: This paper provides a fundamental and critical review of biomass application as renewable reductant in integrated ferroalloy reduction process. The basis for the review is based on the current process and product quality requirement that bio-based reductants must fulfill. The characteristics of different feedstocks and suitable pre-treatment and post-treatment technologies for their upgrading are evaluated. The existing literature concerning biomass application in ferroalloy industries is reviewed to fill out the research gaps related to charcoal properties provided by current production technologies and the integration of renewable reductants in the existing industrial infrastructure. This review also provides insights and recommendations to the unresolved challenges related to the charcoal process economics. Several possibilities to integrate the production of bio-based reductants with bio-refineries to lower the cost and increase the total efficiency are given. A comparison of challenges related to energy efficient charcoal production and formation of emissions in classical kiln technologies are discussed to underline the potential of bio-based reductant usage in ferroalloy reduction process. Keywords: charcoal; pyrolysis; bio-based reductant; ferroalloy industry; kiln 1. -
1. Introduction Ferrosilicon Smelting Is a Continuous Process Carried out In
Arch. Metall. Mater., Vol. 61 (2016), No 1, p. 265–270 DOI: 10.1515/amm-2016-0050 B. MACHULEC*,#, W. BIALIK** COMPARISON THE PHYSICO-CHEMICAL MODEL OF FERROSILICON SMELTING PROCESS WITH RESULTS OBSERVATIONS OF THE PROCESS UNDER THE INDUSTRIAL CONDITIONS Based on the minimum Gibbs Free Enthalpy algorithm (FEM), model of the ferrosilicon smelting process has been presented. It is a system of two closed isothermal reactors: an upper one with a lower temperature T1, and a lower one with a higher temperature T2. Between the reactors and the environment as well as between the reactors inside the system, a periodical exchange of mass occurs at the moments when the equilibrium state is reached. The condensed products of chemical reactions move from the top to the bottom, and the gas phase components move in the opposite direction. It can be assumed that in the model, the Reactor 1 corresponds to the charge zone of submerged arc furnace where heat is released as a result of resistive heating, and the Reactor 2 corresponds to the zones of the furnace where heat is produced by electric arc. Using the model, a series of calculations was performed for the Fe-Si-O-C system and was determined the influence of temperatures T1, T2 on the process. The calculation results show a good agreement model with the real ferrosilicon process. It allows for the determination of the effects of temperature conditions in charge zones and arc zones of the ferrosilicon furnace on the carbothermic silica reduction process. This allows for an explanation of many characteristic states in the ferrosilicon smelting process. -
Reduce Ductile Iron Processing Costs Through The
Nodulizing and Inoculation Approaches for Year 2000 and Beyond - Part 1 by Dr. R. L. (Rod) Naro ASI International, Ltd. – July 30, 2001 Original Paper presented June 15, 2000 DIS Meeting, Wichita, Kansas Abstract: Nodu-Bloc, a new iron-magnesium briquette, offers ductile iron foundries a powerful alloy that can be used to replace traditional magnesium ferrosilicon (MgFeSi) as well as other magnesium containing master-alloys. Controlled laboratory tests show that Nodu-Bloc can replace up to 50 weight percent of MgFeSi. Field trials with Nodu-Bloc confirm these results and show that Nodu-Bloc replacement of MgFeSi can provide significant cost savings. Foundries converting to Nodu-Bloc will experience reduced melting costs because less MgFeSi is consumed, less steel and pig iron is required in the charge and far greater levels of foundry returns can be utilized. Foundries can easily save up to $10 or more per ton on molten ductile iron processing costs by incorporating Nodu-Bloc technology. Introduction: Since the commercialization of ductile iron in 1948, foundries have used numerous methods to introduce magnesium into molten cast iron. Figure 1 lists some of the approaches and techniques used over the years. Although some of these processes gained a brief following, and some have even been used successfully, most have fallen out of favor because of numerous shortcomings. Today, the majority of ductile iron castings made throughout the world are produced using ladle-metallurgy practices with MgFeSi alloys. It is estimated that MgFeSi alloys are used in 65 percent of all ductile irons produced worldwide. In the United States, MgFeSi alloys account for an estimated 75 percent of ductile iron production. -
Mgfesi Alloys Psi English.Pdf
Product Safety Information 1. Identification of the Product and Supplier Product name: Elkem MgFeSi Alloys Elmag®, Lamet® and Remag® Nodularisers, CompactMag® Alloy Product application: Additive to liquid metal in foundries for production of cast iron. Address/Phone No.: Elkem AS Foundry Products P.O. Box 334 Skøyen, N-0213 Oslo, Norway Telephone: + 47 22 45 01 00 Telefax: + 47 22 45 01 11 http://www.foundry.elkem.com [email protected] REACH registration numbers: 01-2119485286-28-0033 (FeSi) 01-2119537203-49-0046 (Mg) REACH and CLP helpdesk: http://echa.europa.eu/support/helpdesks/ Emergency Phone No.: https://poisoncentres.echa.europa.eu/home 2. Hazards Identification Classification: The product does not meet the criteria for hazard classification in accordance with Regulation (EC) No 1272/2008 (CLP) and the UN Globally Harmonized System of Classification and Labelling of Chemicals (GHS), 6th revision. Hazard pictogram: N/A (not applicable) Signal word: N/A (not applicable) Hazard statements: N/A (not applicable) Precautionary statements: N/A (not applicable) Flammable and noxious gases may be formed in contact with moisture, acids or bases. See section 10 and 11. Dust from the product if suspended in air may under certain conditions cause dust explosions. See section 10. © COPYRIGHT ELKEM AS 2017 103/PSI/ENG Page 1 of 7 Rev. 04, 2017-10-16 3. Composition/Information on Ingredients Synonyms/Trade names: Ferrosilicon magnesium, Magnesium alloy. CAS No. Ferrosilicon: 8049-17-0 CAS No. Magnesium: 7439-95-4 REACH registrations: Elkem MgFeSi is a mixture of FeSi and Mg and has for hazard classification purposes been assessed as an entity in accordance with CLP. -
Magnesium-Titanium-Ferrosilicon Alloys for Producing Compacted
Europaisches Patentamt ® European Patent Office © Publication number: 0 192 090 Office europeen des brevets A1 © EUROPEAN PATENT APPLICATION © Application number: 86101151.8 © intCI.*: C 22 C 35/00 C 21 C 1/10 @ Date of filing: 29.01.86 ® Priority: 11.02.85 US 700796 © Applicant: SKW Alloys, Inc. P.O. Box 368 Niagara Falls, N.Y. 14302(US| (§) Date of publication of application: 27.08.86 Bulletin 86/35 © Inventor: Dremann, Charles E. Bruckwafter Road © Designated Contracting States: Phoenixville PA 19460(US) DE FR IT @ Inventor: Fugiel, Thomas F. 1514 West Suffield Village of Arlington Heights IllinoisfUSf © Representative: Weickmann, Heinrich, Dipl.-lng. et al, Patentanwahe Dipl.-lng. H.Weickmann Dipl.-Phys.Dr. K.Fincke Dipl.-lng. F.A. Weickmann Dipl.-Chem. B. Huber Dr.-lng. H. Liska Dipl.-Phys.Dr. J. Prechtel Mohistrasse 22 D-8000 Munchen 80(DE) © Magnesium-titanium-f errosilicon alloys for producing compacted graphite iron in the mold and process using same. Compacted graphite (CG) cast iron is obtained in the inmold casting process employing as an additive an alloy comprising 1.5-3 percent magnesium, 10-20 percent tita- nium, 40-80 percent silicon, 0-2 percent rare earth, 0-0.5 percent calcium, 0-2 percent aluminum and balance iron. This invention relates to novel magnesium-titanium-ferrosilicon-containing alloys for. producing compacted graphite (CG) iron in the mold and to a casting process using such alloys. Background of the Invention Compacted graphite is the name usually given to flake graphite which has become rounded, thickened and shortened as compared to normal elongated flakes commonly found in gray cast iron. -
The Application of Sic in Converter Steelmaking Hailing Li
3rd International Conference on Mechatronics and Information Technology (ICMIT 2016) The Application of SiC in Converter Steelmaking Hailing Li1,a, Qichun Peng1,b,Youhua Wang2 1school of Material and Metallurgy ,Wuhan University of Science and Technology,China. 2Hunan Valin Xiangtan iron and Steel Co. Ltd. [email protected], [email protected] Key words: Silicon carbide converter deoxidation mechanical properties inclusions Abstract. Silicon carbide has better deoxidization ability than ferrosilicon and recarburizer by the thermodynamic analysis,the gas of CO produed by the deoxidation reaction can agitates molten steel which could purify the molten steel .In this article, we choose HRB400 as our testing steel,it is found that the usage of SiC can reach the aim of recarburization and silicon increasing in the statistical analysis,the various properties of the testing steel are stable, and the use of Silicon carbide can further improve the economic benefits of steel plants as the price of SiC is lower. Introduction Silicon carbide with the molecular weight of 40.07 and the density of 3.209g / cm3 is a kind of synthetic compounds, molecular formula is SiC. SiC is made from high quality quartz sand and petroleum coke in the resistance furnace, it can be used as compound deoxidizer in metallurgy field as its widespread application. SiC is a new kind of compound deoxidizer with more stable physical and chemical performances and good deoxidization effection as the replacement of the traditional solid silicon powder and carbon powder.Furthermore, -
Low-Carbon Ferrochromium Imports Not Causing Serious !~Jury
UNITED STATES INTERNATIONAL TRADE COMMISSION WW-CARBON FERROCHROMIUM Report to the President on Investigation No. TA-201-20 Under Section 201 of the Trade Act of 1974 USITC Publication 825 Washington, D. C. July 1977 UNITED STATES INTERNATIONAL TRADE COMMISSION COMMISSIONERS Daniel Minchew, Chairman Joseph O. Parker, Vice Chairman George M. Moore Catherine Bedell Italo H. Ablondi Kenneth R. Mason, Secretary to the Commission This report was principally prepared by Nicholas C. Talerico, Minerals and Metals Division James S. Kennedy, Minerals and Metals Division assisted by Marvin C. Claywell, Operations Division N. Timothy Yaworski, Office of the General Counsel Charles W. Ervin, Supervisory Investigator Address all communications to United States International Trade Commission Washington, D .. c. 20436 FOR RELEASE AT WILL CONTACT: Kenneth R. Mason July 11,.1977 (202) 523-0161 USITC 77-052 LOW-CARBON FERROCHROMIUM IMPORTS NOT CAUSING SERIOUS !~JURY The United States International Trade Commission today reported to the President pursuant to the provisions of section 201 of the Trade Act of 1974 that imports of low-carbon ferro- chromium are not causing serious injury or the threat there- of to the relevant U.S. industry. Commissioners Daniel Minchew, Catherine Bedell, and Italo H. Ablondi formed the majority with their negative findings. Commissioner George M. Moore found in the affirmative that increased imports of low-carbon ferrochromium were a sub- stantial cause of the threat of serious iTijury to the domestic industry. Commissioner Joseph 0. Parker did not participate in the decision. There are three U.S. producers of low-carbon ferrochromi~m: Satralloy, Inc.; Globe Metallurgical Division, Interlake, Inc.; and Union Carbide Corp. -
Geosciences and Mining Journal 2020
GEOSCIENCES AND MINING JOURNAL Series-01 GEOSCIENCES AND MINING JOURNAL Series-01 TABLE OF CONTENT FOREWORD .......................................................................................................................i MESSAGE FROM THE DIRECTOR GENERAL ............................................................ii EDITORIAL ..................................................................................................................... iii GEOSCIENCE FOR SOCIETY .........................................................................................1 GEOLOGY AND MINERAL RESOURCES OF BHUTAN - AN OVERVIEW ..............4 MINERAL EXPLORATION FOR MINING DEVELOPMENT .....................................11 LANDSLIDE HAZARD IN BHUTAN ............................................................................14 National EarthQUAKE Monitoring NETWORK ...........................................19 INTEGRATED GEOPHYSICAL IMAGING TECHNIQUES FOR SLOPE STABILITY STUDY AT CHAPCHA .................................................................28 REFORMS IN THE MINING SECTOR ..........................................................................42 MINING CADASTRE AND ITS INTRODUCTION IN BHUTAN ...............................47 VALUE ADDITION OF MINERALS ..............................................................................55 THE MIDDLE PATH : STRATEGIZING ENVIRONMENTAL COMPLIANCE IN MINING IN BHUTAN .....................................................................................................59 MINING Sector at A GLANCE -
Overview of the Silicon Carbide Market Cover Story • Overview of the Sic Market
Ductile Iron News Home Page To Promote the production and application of ductile iron castings Issue 3 1999 FEATURES Overview of the Silicon Carbide Market Cover Story • Overview of the SiC Market Thermal Analysis Testing • for Acceptable Mg Content Rapid Determination • of Mg in Ductile Iron Experience • with Recarburizers Additional Info. • Resources FEF College • Industry Conference Henych • Announces Retirement • William Beatty Obituary DEPARTMENTS • News Briefs Associate Member • Profile AP Southridge, Inc. • Advertisers • Back Issues • DIS Home page file:///C|/WEBSHARE/062013/magazine/1999_3/index.htm[6/19/2013 7:51:46 AM] Overview of the Silicon Carbide Market Overview of the Silicon Carbide Market By Gustov O. Hughes Abstract Silicon carbide is a versatile, useful, manmade material. It is made by blending coke and sand and applying heat. The North American market has grown significantly while a large part of it is now imported. The major users of silicon carbide grain are the abrasive, refractory, and alloy industry. The iron foundry industry uses a significant amount of silicon carbide in the form of refractories and alloy additions. Trends in the market point to stable to slightly decreasing pricing for SiC in the near future. Silicon Carbide Production Silicon carbide is a black to green material that is a combination of 70% silicon and 30% carbon. In nature, only a small amount exists, where coal and sand have been exposed to each other in the presence of a significant amount of hear. No commercially viable deposits exist, so for practical use, the material is manufactured. To make silicon carbide, usually low sulfur petroleum coke and high purity sand are selected as the raw materials. -
Silicon Metal from the People’S Republic of China
A-570-806 NSR: 6/01/05-5/31/06 Public Document AD/CVD9:MJQ DATE: October 9, 2007 MEMORANDUM TO: David M. Spooner Assistant Secretary for Import Administration FROM: Stephen J. Claeys Deputy Assistant Secretary for Import Administration SUBJECT: Issues and Decision Memorandum for the Final Results of 2004/2006 Antidumping Duty New Shipper Reviews of Silicon Metal from the People’s Republic of China ______________________________________________________________________________ SUMMARY We have analyzed the case and rebuttal briefs of interested parties in the 2005/2006 new shipper reviews (“NSR”) of the antidumping duty order on silicon metal from the People’s Republic of China (“PRC”). The period of review (“POR”) is June 1, 2005, to May 31, 2006. As a result of our analysis, we have made changes to the preliminary results. See Silicon Metal From the People's Republic of China: Preliminary Results of the 2005/2006 New Shipper Reviews, 72 FR 28467 (May 21, 2007) (“Preliminary Results”). We recommend that you approve the positions described in the “Discussion of the Issues” section of this Issues and Decision Memorandum. Below is a complete list of issues for which we have received comments: General Issues Comment 1: Selection of Surrogate Country Comment 2: Electricity Valuation Comment 3: Selection of Financial Statements Comment 4: Quartz Valuation Comment 5: Silica Fume By-Product Valuation Comment 6: Steam Coal Valuation Comment 7: Charcoal Valuation Comment 8: Electrode Usage Company-Specific Issues: Jiangxi Gangyuan Comment 9: Clerical Errors in Calculating Freight Comment 10: June 2005 Electricity Consumption Comment 11: Work-In-Process Inventory Comment 12: Silica Fume Offset During POR Company-Specific Issues: Datong Jinneng/Shanghai Jinneng Comment 13: Silicon Metal Fines Valuation Comment 14: Polyethylene Bag Valuation Comment 15: High Aluminum Quartz Comment 16: Quartz Yield Loss Comment 17: Instructions to Customs Comment 1: Selection of Surrogate Country Shanghai Jinneng International Trade Co., Ltd. -
The Production, Properties, and Selection of Ferrosilicon Powders for Heavy-Medium Separation by B
The production, properties, and selection of ferrosilicon powders for heavy-medium separation by B. COLLlNS*. B.Se. Eng. (Rand) (Fellow). T. J. NAPIER-MUNNt. B.Sc. (Eng.). A.R.S.M. (Visitor). and M. SCIARONEt. M.Se. Eng. (Delft) (Visitor). SYNOPSIS There are basically two types of ferrosilicon powder available to operators of heavy-medium plants in South Africa: spherical and milled grades. The production processes are described, and the properties of the two types are examined and compared. Guidelines are given for the selection of the correct grade of ferrosilicon for any particular application. SAMEVATTING Daar is basies twee so::>rte ferrosilikonpoeier beskikbaar vir diegene wat swaarmediumaanlegginge in Suid-Afrika bedryf: steriese en gemaalde grade. Die produksieproses word beskryf en die eienskappe van die twee soorte word ondersoek en vergelyk. Daar word leidrade aangegee vir die keuse van die korrekte graad ferrosilikon vir enige bepaalde gebruik. INTRODUCTION THE PRODUCTION OF of milled ferrosilicon. The following FERROSILICON POWDERS Ferrosilicon of 14 to 16 per cent are the characeristics of this furnace: Shell diameter 6400 mm silicon has become widely accepted At present there are basically Hearth diameter 4000 mm as the most suitable medium for the two types of ferrosilicon available Electrode diameter 890 mm heavy-medium separation of ores in South Africa to the operators of Secondary voltage 90 to 120 v having a specific gravity in the heavy-medium plants. These are Resistance 0,85 m 0 range of approximately 2,5 to 4,0. milled and spherical grades. Ferrosilicon has many properties Reactance 1,0 m o.