Waste Minimization Issues and Options Volume I
Total Page:16
File Type:pdf, Size:1020Kb
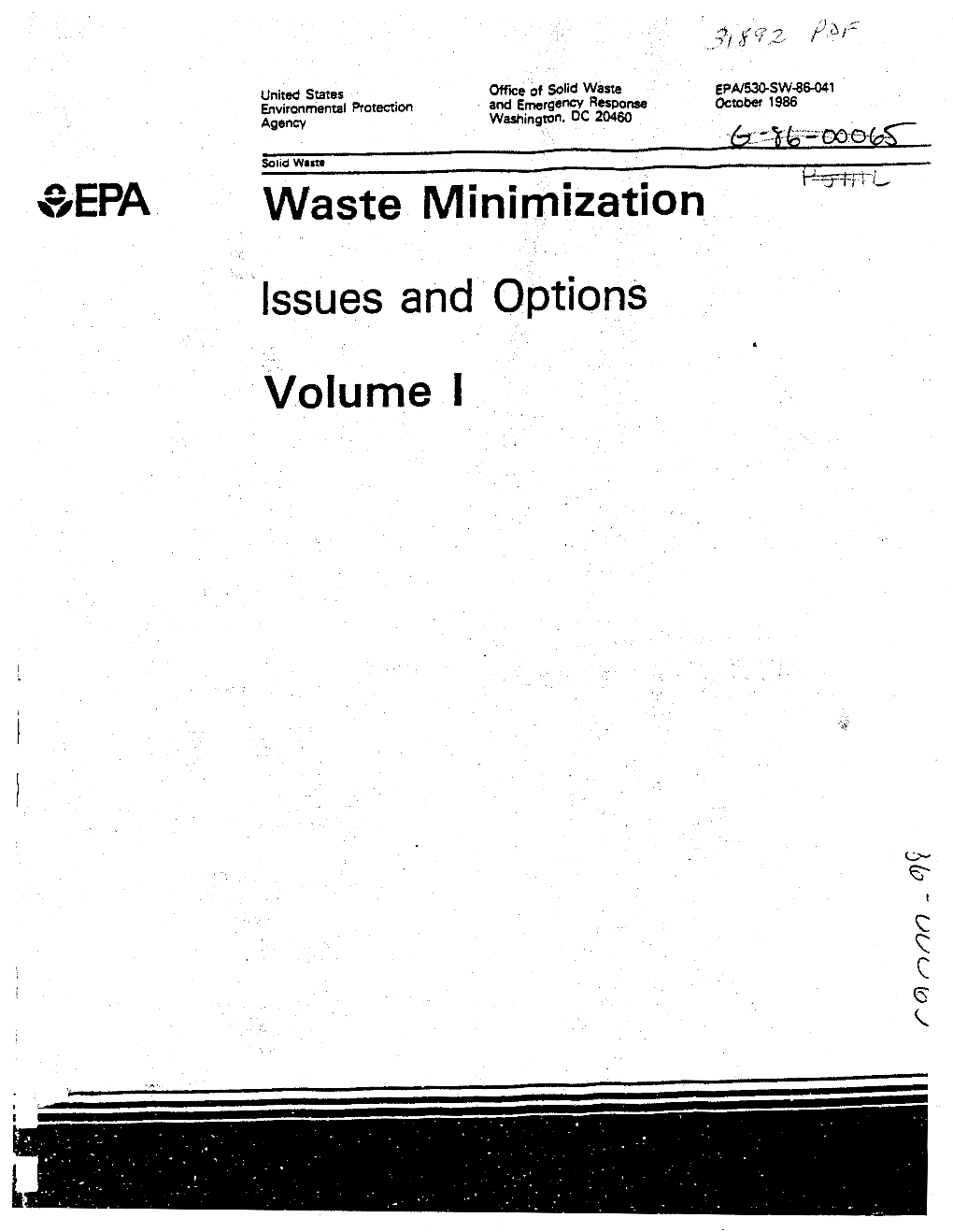
Load more
Recommended publications
-
Toxicological Profile for 1,1,2,2-Tetrachloroethane
1,1,2,2-TETRACHLOROETHANE 161 9. REFERENCES ACGIH. 2005. Threshold limit values for chemical substances and physical agents and biological exposure indices. Cincinnati, OH: American Conference of Governmental Industrial Hygienists. Adinolfi M. 1985. The development of the human blood-CSF-brain barrier. Dev Med Child Neurol 27:532-537. Adlercreutz H. 1995. Phytoestrogens: Epidemiology and a possible role in cancer protection. Environ Health Perspect Suppl 103(7):103-112. Agency for Toxic Substances and Disease Registry. 1989. Decision guide for identifying substance- specific data needs related to toxicological profiles. Atlanta, GA: Agency for Toxic Substances and Disease Registry, Division of Toxicology. Fed Regist 54(174):37618-37634. *Agency for Toxic Substances and Disease Registry. 1996. Toxicological profile query; list of all toxicological profiles. Atlanta, GA: Agency for Toxic Substances and Disease Registry. http://www.atsdr.cdc.gov/toxpro2.html. April 17, 2006. Agency for Toxic Substances and Disease Registry. 1997. Toxicological profile for tetrachloroethylene (update). Atlanta, GA: Agency for Toxic Substances and Disease Registry. PB98101181AS. http://www.atsdr.cdc.gov/toxprofiles/tp18.html. July 15, 2006. AIChE. 1995. 1,1,2,2-Tetrachloroethane. C2H2Cl4. In: Physical and thermodynamic properties of pure chemicals. American Institute of Chemical Engineers, Design Institute for Physical Property Data. Philadelphia, PA: Taylor and Francis. Altman PL, Dittmer DS. 1974. Biological handbooks: Biology data book. Vol. III. 2nd ed. Bethesda, MD: Federation of American Societies for Experimental Biology, 1987-2008, 2041. Amaral OC, Olivella L, Grimalt JO, et al. 1994. Combined solvent extraction-purge and trap method for the determination of volatile organic compounds in sediments. -
Guidelines for Local Governments on Solid Waste Management. INSTITUTION Environmental Protection Agency, Washington, D.C
DOCUMENT Isms ND 092 346 SE 017 241 TITLE Guidelines for Local Governments on Solid Waste Management. INSTITUTION Environmental Protection Agency, Washington, D.C. Solid Waste Management Office.; National Association of Counties, Washington, D.C. Research Foundation. REPORT NO PHS-2048; SW-17c PUB DATE 71 NOTE 196p.; An environmental protection publication in the solid waste management series AVAILABLE FROM Superintendent of Documents, U. S. Government Printing Office, Washington, D. C. 20402 (Stock No. 5502-0047, $1.50) EDRS PRICE MP-$0.75 HC-$9.00 PLUS POSTAGE DESCRIPTORS *Administrator Guides; City Planning; *Ecology; *Guides; *Leaders Guides; Management Systems; Regional Planning; *Waste Disposal; Wastes IDENTIFIERS *Solid Waste Management ABSTRACT This document consists of ten guides on Solid Waste Management to assist local elected and appointed policy-making officials. They are entitled: Areavide Approaches; Legal Authority, Planning, Organization Design and Operation, Financing, Technical and Financial Assistance, Citizen Support, Personnel, and Action Plan and Bibliography. The guides were prepared by the National Association of Counties Research Foundation (NACORD). They are designed to present in clear, concise form information'to help local officials and interested citizens make dedisions on the planning, organization, financing, staffing, legal aspects, and operation of comprehensive areawide solid waste management systems. (JP) U S DEPARTMVO EDUCATION OF HEALtti. NATIONAL /WELFARE THIS NSTITUTE. OF DOCUMENTtOUCATiON DUCED HAS BEEN THE PEEXACTLY AS RSON OR REPRO ATING, IT RECEIVEDFROM POIN TSORGANIZATION Of STATED 00 VIEW ORORIGIN NOT OPINIONS SENT OFFICIAL NECESSARILY EDUCATION NATIONAL REPRE POSITION ORINSTITUTE OF POLICY guidelines for local governments on solid waste management this publication (SW-17c) was developed for the federal solid waste management program by the national association of counties research foundation under contract no. -
Thesis Introducing Efficient Waste Water Treatment And
THESIS INTRODUCING EFFICIENT WASTE WATER TREATMENT AND RE-USE TECHNIQUES IN NORTH CYPRUS by LUTFIYE GUNES 4055778 Submitted in partial fulfillment of the requirements for the degree of Master of Landscape Architecture Anhalt University of Applied Sciences Bernburg, Germany 2014 1stAdvisor: Alexander Kader 2ndAdvisor: Johannes Cox INTRODUCING EFFICIENT WASTE WATER TREATMENT AND RE-USE TECHNIQUES IN NORTH CYPRUS Master Arbeit vorgelegt im Wintersemester 2013-2014 Master Thesis submitted during winter semester 2013-2014 An der Hochschule Anhalt At the Anhalt University of Applied Sciences Abteilung Landwirtschaft, Ökotrophologie und Landschaftsbau Department of Agriculture, Ecotrophology and Landscaping Studiengang Landschaftsarchitektur Study course Landscape Architecture Verfasserin: Author: Lütfiye Günes Bachelor of Architecture (BSc) Gutachter: Examiners: Erstgutachter: Prof.Dr.Alexander Kader 1st Examiner Zweitgutachter: Dipl.Ing- Johannes Cox 2nd Examiner February 2014 2 “A drop of water is worth more than a sack of gold to a thirsty man.” Anonymous “Do not waste water even if you were at a running stream.” Hz. Mohammed To my beloved unbeknown country… 3 i. Abstract Due to its geographical location Cyprus has semi-arid climate. This fact makes water more vital and vulnerable. For all of its time Cyprus has had a lack of and low quality water, if we count the yearly average rainfall ~ 500 mm. Rainwater coming from the Trodos mountains on the South side (largest mountain range of Cyprus-peak 1,952 meters), with the Besparmak mountain and Girne mountains on the North side, is collected in big tanks and distributed to the public. However for many years water has been supplemented to NC from Turkey with tanks and balloons. -
Global Lithium Sources—Industrial Use and Future in the Electric Vehicle Industry: a Review
resources Review Global Lithium Sources—Industrial Use and Future in the Electric Vehicle Industry: A Review Laurence Kavanagh * , Jerome Keohane, Guiomar Garcia Cabellos, Andrew Lloyd and John Cleary EnviroCORE, Department of Science and Health, Institute of Technology Carlow, Kilkenny, Road, Co., R93-V960 Carlow, Ireland; [email protected] (J.K.); [email protected] (G.G.C.); [email protected] (A.L.); [email protected] (J.C.) * Correspondence: [email protected] Received: 28 July 2018; Accepted: 11 September 2018; Published: 17 September 2018 Abstract: Lithium is a key component in green energy storage technologies and is rapidly becoming a metal of crucial importance to the European Union. The different industrial uses of lithium are discussed in this review along with a compilation of the locations of the main geological sources of lithium. An emphasis is placed on lithium’s use in lithium ion batteries and their use in the electric vehicle industry. The electric vehicle market is driving new demand for lithium resources. The expected scale-up in this sector will put pressure on current lithium supplies. The European Union has a burgeoning demand for lithium and is the second largest consumer of lithium resources. Currently, only 1–2% of worldwide lithium is produced in the European Union (Portugal). There are several lithium mineralisations scattered across Europe, the majority of which are currently undergoing mining feasibility studies. The increasing cost of lithium is driving a new global mining boom and should see many of Europe’s mineralisation’s becoming economic. The information given in this paper is a source of contextual information that can be used to support the European Union’s drive towards a low carbon economy and to develop the field of research. -
Use of Fungi Biodegradation Environmental Microbiology
The following chapter: Use of Fungi Biodegradation by J. W. BENNET, K. G. WUNCH, AND B. D. FAISON Has been taken from the book: Manual of Environmental Microbiology Second Edition Editor in Chief Christon J. Hurst ASM Press Washington, D.C. 2002. Useof Fungiin Biodeadation l. \7. BENNETI K. G.\yUNCH, AND B. D. FAISON 87 In nature, fungi do much of the dirty work. Th"y are par- Stramenopila, and four protist phyla. ln this classification, ticularly efficient at degrading the major plant polymers, the kingdom Fungi encompassesfour phyla: Chytridiomy- cellulose and lignin, but they also decomposea huge array cota, Zygomycota, Ascomycota, and Basidiomycota (18, of other organic molecules including waxes, rubber, feath- 26). The Stramenopila encompassesthree phyia' Oomy- ers, insect cuticles, and animal flesh. Although industrial cota, Hyphochytriomycota, and Labyrinthulornycota. From microbiologists regularly hamess fungal metabolism for the perspectiveof researchon fungal degradation,most of brewing, baking, cheesepreparation, and for production of the speciesof interest are in the kingdom Fungi. antibiotics, commercial enzymes, and a number of com- In filamentous forms, the individual thread-like cells are modity chemicals, fungi are best known for their dirry called hyphae. A fungal colony, or porrion of a colony, work. They spoil our foods, blight our crops, rot our build- composed of many hyphae together is called a mycelium. ings, contaminate our petri dishes, and cause some rather The filamentous/mycelial growth form poses problems in loathsome diseases.Paradoxically, despite this notoriety, determining the sizeof a single organism and in measuring "thal- the use of fungi in bioremediation has been limited com- the growth of fungi. -
NRC Collection of Abbreviations
I Nuclear Regulatory Commission c ElLc LI El LIL El, EEELIILE El ClV. El El, El1 ....... I -4 PI AVAILABILITY NOTICE Availability of Reference Materials Cited in NRC Publications Most documents cited in NRC publications will be available from one of the following sources: 1. The NRC Public Document Room, 2120 L Street, NW., Lower Level, Washington, DC 20555-0001 2. The Superintendent of Documents, U.S. Government Printing Office, P. 0. Box 37082, Washington, DC 20402-9328 3. The National Technical Information Service, Springfield, VA 22161-0002 Although the listing that follows represents the majority of documents cited in NRC publica- tions, it is not intended to be exhaustive. Referenced documents available for inspection and copying for a fee from the NRC Public Document Room include NRC correspondence and internal NRC memoranda; NRC bulletins, circulars, information notices, inspection and investigation notices; licensee event reports; vendor reports and correspondence; Commission papers; and applicant and licensee docu- ments and correspondence. The following documents in the NUREG series are available for purchase from the Government Printing Office: formal NRC staff and contractor reports, NRC-sponsored conference pro- ceedings, international agreement reports, grantee reports, and NRC booklets and bro- chures. Also available are regulatory guides, NRC regulations in the Code of Federal Regula- tions, and Nuclear Regulatory Commission Issuances. Documents available from the National Technical Information Service Include NUREG-series reports and technical reports prepared by other Federal agencies and reports prepared by the Atomic Energy Commission, forerunner agency to the Nuclear Regulatory Commission. Documents available from public and special technical libraries include all open literature items, such as books, journal articles, and transactions. -
Decontamina Tion and Waste Treatment Facility for the Lawrence Livermore National Laboratory Livermore, California
DOE/EIS-O 133-D DRAFT ENVIRONMENT AL IMPACT STATEMENT Decontamina tion and Waste Treatment Facility for the Lawrence Livermore National Laboratory Livermore, California JUNE 1988 UNITED STATES DEPARTMENT OF ENERGY OOE/EIS-O 133-0 DRAFT ENVIRONMENTAL IMPACT STATEMENT Decontamination and Waste Treatment Facility for the Lawrence Livermore National Laboratory Livermore, California JUNE 1988 UNITED STATES DEPARTMENT OF ENERGY DOE/EIS-0133-D COVER SHEET DRAFT ENVIRONMENTAL IMPACT STATEMENT DECONTAM INATION AND WASTE TREATMENT FACIL ITY, LAWRENCE LIVERM ORE NATIONAL LABOPATORY, LIVERMORE, CALI FORNIA a) Lead Agency : U.S. Department of Energy (DOE) b) Proposed Action: to construct and operate a Decontami nation and Waste Treatment Facil ity (DWTF ) for nonradioactive (hazardous and nonhazardous). mixed. and radioact ive wastes at Lawrence Livermore National Laboratory . c) For additional co.pies or further information on this stat ement and pro gr am. please cont act : Mr. 1iJilliam Holman Envi ronmental Branch Environment. Safety and Quality As surance Division Department of Energy San Franci sco Operations Office 1333 Broadway Oakland . California 94612 Telephone : (415) 273-6370 For general information on DOE's Environment al Impact Stat ement (EIS ) process. please contact : Ms . Carol M. Borgstrom U.S. Department of Energy Office of NEPA Proj ect As sistance 1000 Independence Av enue. SW Washington. DC 20585 Telephone : (202) 586-4600 d) Designation: Draft EIS (DEIS) i DOE/E IS-0 133-D e) Ab stract This statement assesses the environmental impact s of alternatives proposed for the management of waste generated by the Lawrence Livermore Na tional Laboratory (LLNL) . The four primary waste management strategy alternatives that were initially evaluated are : 1) no action (i. -
Recycling Works Volume 20, Number 1 Winter 2014
Recycling Works Volume 20, Number 1 Winter 2014 A cooperative effort of the N.C. Department Job Growth in NC Recycling of Environment and Natural Resources and the N.C. Department Industry, Study Shows of Commerce. by Sherry Yarkosky, Recycling Business Development Specialist Private sector recycling jobs in North The total estimated annual payroll Carolina have increased by nearly 12 for North Carolina recycling busi- percent since 2010 as recycling busi- nesses is $442 million. nesses in the Tar Heel State continue Forty-five percent of recycling to grow and thrive, according to a businesses surveyed anticipate cre- study released by the N.C. Department ating more jobs during the next of Environment and Natural Re- two years. sources. Eighty-one recycling businesses The study’s major findings include: reported spending $79.6 million in equipment, facilities, and land in- There are more than 17,000 direct vestments from 2011 to 2013. private sector recycling-related jobs in North Carolina. Fifty-one percent of recycling busi- nesses surveyed plan on investing Private sector recycling jobs have $47.3 million in equipment, facili- increased by 11.95 percent since ties, or land in the next two years. 2010. Twenty-eight percent of businesses surveyed report manufacturing a product, using a combined 2,264,565 tons of recycled materi- als. (JOB GROWTH continued on page 2) Inside Recycling Works 2014 CRA Annual Conference..………………… 3 EarthStone Products Poised for Growth...….……4 Rain Water Solutions’ Recycled Content Barrel.......6 State Disposal Trends Down..……………………8 Results published since 1994 document consistent expansion in RBAC Says Farwell to Staffer…………………….9 recycling employment in North Carolina. -
Envi Ronm Ental Services Report
ENVI RONM ENTAL SERVICES REPORT November 15,2012 Ponderosa Landfill . EAW update o Permit Update . CON update - Don Kyser retires . Cell Construction early 2013 o Public Service Building - time frame . Adjacent Property . New Haul Road . Jersey Barriers ¡ Annual Flyover/Annual Reporting ¡ Xcel Contract for Ash Placement Solid Waste/ Recycling . Recycling Operations Contract (WMl) o New State Rule under discussion: Concrete disposal o Solid Waste Management Plan r Waste Pharmaceuticals and Sharps r FullCircle Organics Household Hazardous Waste o Closed for Season . Off Season Activity r STS processing Miscellaneous . County Web Site o Credit Card Machine - and at Landfill . Web Portal Evaluation . Buffer Project NEXT SCHEDULED MEETING - January 17,2013 lnformation Articles Minnesota Pollution Control Solid Waste Plan Review Checklist Agency Mankato Free Press Single-sort in store of Mankato Mankato Free Press Briefs: 'Sharps' now accepted at Hy-Vee Lake CrystalTibune Convenient Disposal Options Available to Area Residents Mankato Free Press Callfor compost site review rejected Mankato Free Press Township agreements'operating very well' Waste and Recycling News Partnerships push progress of Coke's plant-based bottles Waste and Recycling News Facilities overwhelmed by piles of CRT glass Mankato Free Press Do Your Part: Top five solutions to recycling problems Post-Bulletin We all pay for illegaltrash disposal Star Tribune Ol' Man River is fullof life again Star Tribune Residential thirst straining, draining White Bear Lake Minnesota Pollution Control How's the water? Much better after 40 years of Clean Water Act Agency Minnesota Public Radio Businesses and boaters pinched by low river levels in Minnesota Star Tribune Sweeping cleanup of St. -
Environmental Newsletter Spring 2011
INSIDE THIS ISSUE “GREEN” ELECTRONICS DISPOSAL 2 LANDSCAPE LESSONS 6 RAIN BARREL/COMPOSTER SALE 7 EnvironmentalC nnections Spring 2011 CHISAGO COUNTY ENVIRONMENTAL NEWS Chisago County Household Hazardous Waste Facility celebrates 10 years of service! In the spring of 2000, construction of the permanent facility began on a moderately wooded site, removing very few of the oak trees that dotted the property. Trees that were removed were fashioned into paneling for the walls of the facility meeting room. The The staff of the Chisago County facility officially opened for business on Household Hazardous Waste November 27, 2000. Based on previ- Facility (HHWF) is excited to ous participation in the one-day collec- announce that the facility has turned tion events, staff assumed that the ten! During that time, they have taken first year of operation would bring in in over TWO MILLION POUNDS of 525 participants; however over 900 household hazardous waste from households were served, resulting in county residents, including unwanted 32 tons of safely disposed waste! In paints, cleaners, pesticides, aerosols, 2010, the tenth year of service, the batteries, fluorescent lights and more. facility served nearly 2000 households. Historically, these items were simply The household hazardous waste pro- tossed in the trash or just stored in a gram continues to improve to better garage or barn—primarily because no serve the needs of its customers and other option existed. Eventually, how- the environment. Recent changes ever, those substances, some of them include the addition of 5-gallon plastic extremely toxic, may find their way into bucket recycling. Central Converting our groundwater. -
Bioelectrochemical Treatment of Municipal Solid Waste Landfill Mature Leachate and Dairy Wastewater As Co-Substrates
Environmental Science and Pollution Research (2021) 28:24639–24649 https://doi.org/10.1007/s11356-020-10167-7 WASTE AND BIOMASS MANAGEMENT & VALORIZATION Bioelectrochemical treatment of municipal solid waste landfill mature leachate and dairy wastewater as co-substrates Silvia Bolognesi1,2 & Daniele Cecconet1,3 & Arianna Callegari1 & Andrea G. Capodaglio1 Received: 16 April 2020 /Accepted: 16 July 2020 / Published online: 22 July 2020 # The Author(s) 2020 Abstract Despite solid wastes’ landfill disposal limitation due to recent European legislation, landfill leachate disposal remains a signif- icant problem and will be for many years in the future, since its production may persist for years after a site’s closure. Among process technologies proposed for its treatment, microbial fuel cells (MFCs) can be effective, achieving both contaminant removal and simultaneous energy recovery. Start-up and operation of two dual-chamber MFCs with different electrodes’ structure, fed with mature municipal solid waste landfill leachate, are reported in this study. Influent (a mix of dairy wastewater and mature landfill leachate at varying proportions) was fed to the anodic chambers of the units, under different conditions. The maximum COD removal efficiency achieved was 84.9% at low leachate/dairy mix, and 66.3% with 7.6% coulombic efficiency (CE) at a leachate/dairy ratio of 20%. Operational issues and effects of cells’ architecture and electrode materials on systems’ performance are analyzed and discussed. Keywords Bioelectrochemical systems . Bioelectricity . Leachate treatment . Agrofood industry wastewater . Electrode materials Introduction possible spread of harmful pollutants (Capodaglio et al. 2016a). Municipal solid waste (MSW) disposal is a problem with no Leachate characteristics are quite variable, affected by easy or unique solution. -
Re-FREAM Re-Thinking of Fashion in Research and Artist Collaborating Development Art for Urban Manufacturing Tech
Re-FREAM Re-Thinking of Fashion in Research and Artist collaborating development Art for Urban Manufacturing Tech ToolboxRe-FREAM is funded by the European Union’s Horizon 2020 research and innovation programme under grant agreement No 825647. 1 2 PURPOSE This booklet syntetizes the results of the desktop research phase of the Re-FREAM project WP2 - Art transfer Further information about the project can be found on the project website www.re-fream.eu AUTHORS Floriana Benigno, Consorzio ARCA (Graphic Design) Marta Ferreira, IED Blanca Gomara, IED Luca Leonardi, Consorzio ARCA Margot Matesanz, IED Isabel Bertz, IED Fabio Maria Montagnino, Consorzio ARCA (Editor) STATEMENT OF ORIGINALITY This booklet contains original unpublished work except where clearly indicated otherwise. Acknowledgment of previously published material and of the work of others has been made through appropriate citation, quotation or both. COPYRIGHT This work is licensed under a Creative Commons Attribution-ShareAlike 4.0 International License, 2015-2016. DISCLAIMER All information included in this document is subject to change without notice. The authors make no warranty of any kind with regard to this document, including, but not limited to, the implied warranties of merchantability and fitness for a particular purpose. The authors shall not be held liable for errors contained herein or direct, indirect, special, incidental or consequential damages in connection with the furnishing, performance, or use of this material. ACKNOWLEDGEMENTS Re-FREAM is funded by the EU