Compliant Mechanism Suspensions
Total Page:16
File Type:pdf, Size:1020Kb
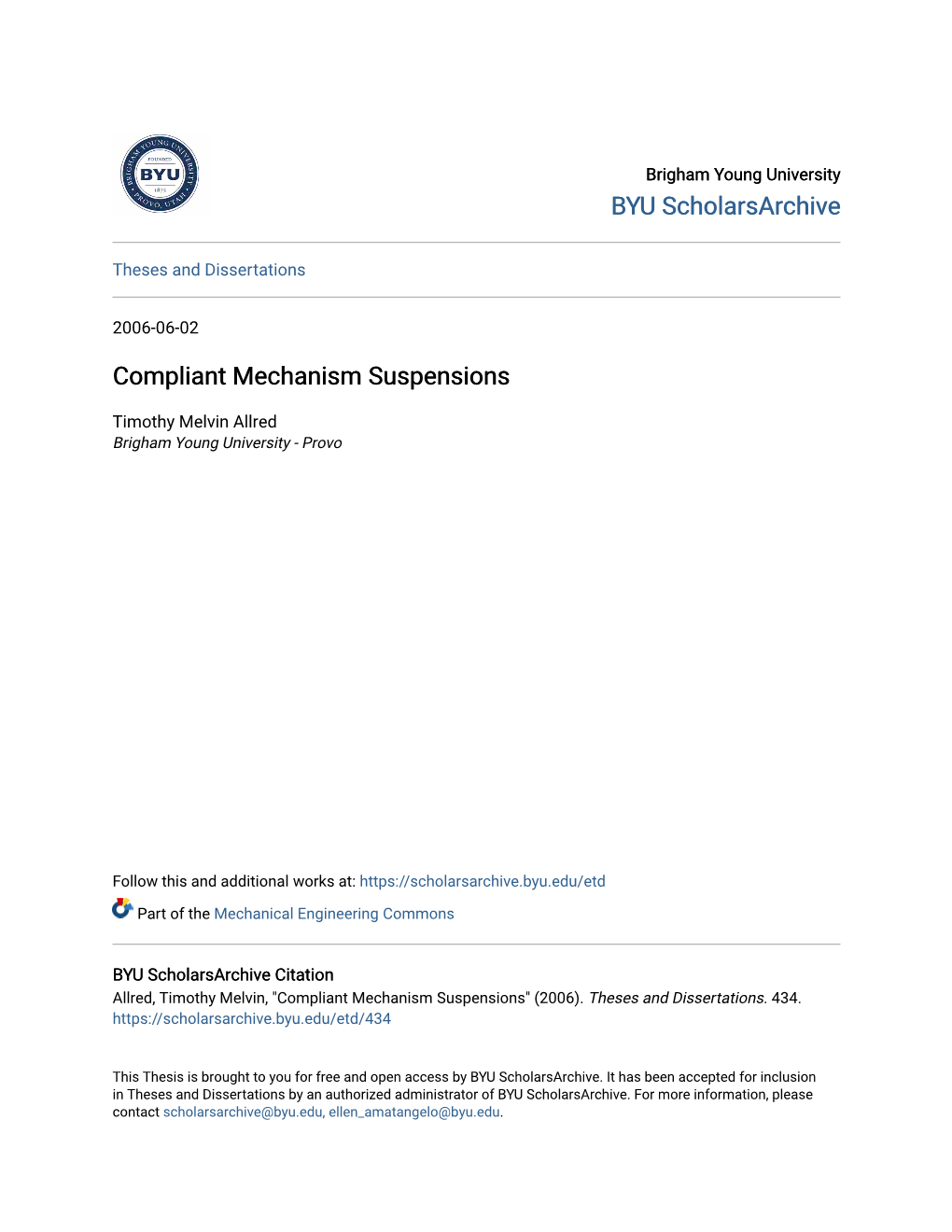
Load more
Recommended publications
-
Suspension Geometry and Computation
Suspension Geometry and Computation By the same author: The Shock Absorber Handbook, 2nd edn (Wiley, PEP, SAE) Tires, Suspension and Handling, 2nd edn (SAE, Arnold). The High-Performance Two-Stroke Engine (Haynes) Suspension Geometry and Computation John C. Dixon, PhD, F.I.Mech.E., F.R.Ae.S. Senior Lecturer in Engineering Mechanics The Open University, Great Britain. This edition first published 2009 Ó 2009 John Wiley & Sons Ltd Registered office John Wiley & Sons Ltd, The Atrium, Southern Gate, Chichester, West Sussex, PO19 8SQ, United Kingdom For details of our global editorial offices, for customer services and for information about how to apply for permission to reuse the copyright material in this book please see our website at www.wiley.com. The right of the author to be identified as the author of this work has been asserted in accordance with the Copyright, Designs and Patents Act 1988. All rights reserved. No part of this publication may be reproduced, stored in a retrieval system, or transmitted, in any form or by any means, electronic, mechanical, photocopying, recording or otherwise, except as permitted by the UK Copyright, Designs and Patents Act 1988, without the prior permission of the publisher. Wiley also publishes its books in a variety of electronic formats. Some content that appears in print may not be available in electronic books. Designations used by companies to distinguish their products are often claimed as trademarks. All brand names and product names used in this book are trade names, service marks, trademarks or registered trademarks of their respective owners. The publisher is not associated with any product or vendor mentioned in this book. -
Everyone's Path Is Different
Protecting What Moves You Everyone’s path is different. We customize your plan to fit your needs. BLUE VEHICLE SERVICE CONTRACTS Add an additional $190 to each Average Repair Costs occurrence for estimated towing Did You Know? Navigation System and rental car expenses that $2,163.87 may be incurred. • If you drive more than 12,000 miles per year, your factory warranty may Engine expire before it reaches its time limit. • Repair frequency increases as mileage increases. $9,818.42 • A vehicle service contract can improve the value of your vehicle. Fuel Injectors $530.50 Covered by the Rear-View Cameras manufacturer Hybrid Vehicle Generator $554.43 MILES $3,854.96 Covered by you Cylinder Head $4,076.43 Vehicle service contracts Electronic Control Module purchased after the Timing Belt & Chain vehicle sale require a $1,181.23 $1,571.87 vehicle inspection. Air Conditioner Compressor Transmission $1,299.30 Repair your vehicle at any licensed repair facility. $6,238.70 TIME Repair costs were calculated using a national average of $125 per hour for labor. The vehicles used in the calculation are as follows: BMW 328i 2.0L Turbo, Chevrolet C1500 Silverado 5.3L, Nissan Maxima 3.5L, Ford Explorer 3.5L V6, Mercedes-Benz CLS400 3.0L V6 , Toyota Camry 3.5L V6, Dodge Grand Caravan V6, Honda Accord 2.4L, Volkswagen Jetta GLI 2.0L Turbo, Mazda 6 - 2.5L V4. Vehicles are model year 2015. All vehicles and manufacturers are registered trademarks of their respective corporations. Included With Your Coverage Emergency Car Rental Towing Trip Interruption Roadside Transferable Renewable Reimbursement Reimbursement Reimbursement Assistance Providing reimbursement Reimbursement for Food and lodging One year of Emergency You can transfer the You can purchase a for transportation when towing (up to $50) if reimbursement of up Roadside Assistance, which coverage to another new contract for your vehicle is in for a needed for a covered to $300 ($100 per day) includes towing (up to $100), private owner of the vehicle prior to covered repair. -
Late Model Sportsman Car Specifications Updated June 4, 2019
15112 National Pike, Hagerstown, MD 21740 PHONE (301) 582-0640 FAX (301) 582-3618 [email protected] Late Model Sportsman Car Specifications Updated June 4, 2019 CAR SPECIFICATIONS: LUCAS OIL AND WORLD OF OUTLAW LATE MODELS SPECS APPLY. The following is an excerpt from the Lucas Oil Late Model Rules for reference. BODIES A.) Nose piece and roof must match body style of car. B.) All cars must have a minimum of one half inch (1/2”) and a maximum of two (2”) inches of roll at top of fenders, doors, and quarter panels. A sharp edge or angle will not be permitted. Body roll must go from sides over interior, not interior over sides. C.) Floorboards and firewall must cover the driver’s area and be constructed to provide maximum safety. D.) Driver’s seat must remain on the left side of the drive line. E.) Front window bars are mandatory. F.) Legible numbers, at least eighteen inches (18”) high are required on each side of the car and roof. G.) No fins or raised lips of any kind are permitted anywhere along the entire length of the car. H.) Body line must be a smooth even line from front to rear. I.) No “slope noses” or “wedge cars” permitted. Noses must be stock appearing, subject to Series template. J.) No “belly pans” or any type of enclosure on bottom of cars will be permitted. Skid plate to protect oil pan is permitted. K.) No wings or tunnels of any kind are permitted underneath the body or chassis of the Page 1 of 9 car. -
1700 Animated Linkages
Nguyen Duc Thang 1700 ANIMATED MECHANICAL MECHANISMS With Images, Brief explanations and Youtube links. Part 1 Transmission of continuous rotation Renewed on 31 December 2014 1 This document is divided into 3 parts. Part 1: Transmission of continuous rotation Part 2: Other kinds of motion transmission Part 3: Mechanisms of specific purposes Autodesk Inventor is used to create all videos in this document. They are available on Youtube channel “thang010146”. To bring as many as possible existing mechanical mechanisms into this document is author’s desire. However it is obstructed by author’s ability and Inventor’s capacity. Therefore from this document may be absent such mechanisms that are of complicated structure or include flexible and fluid links. This document is periodically renewed because the video building is continuous as long as possible. The renewed time is shown on the first page. This document may be helpful for people, who - have to deal with mechanical mechanisms everyday - see mechanical mechanisms as a hobby Any criticism or suggestion is highly appreciated with the author’s hope to make this document more useful. Author’s information: Name: Nguyen Duc Thang Birth year: 1946 Birth place: Hue city, Vietnam Residence place: Hanoi, Vietnam Education: - Mechanical engineer, 1969, Hanoi University of Technology, Vietnam - Doctor of Engineering, 1984, Kosice University of Technology, Slovakia Job history: - Designer of small mechanical engineering enterprises in Hanoi. - Retirement in 2002. Contact Email: [email protected] 2 Table of Contents 1. Continuous rotation transmission .................................................................................4 1.1. Couplings ....................................................................................................................4 1.2. Clutches ....................................................................................................................13 1.2.1. Two way clutches...............................................................................................13 1.2.1. -
RACING FLATHEAD by Mark Dees
*&) 8 Sgg* CAR l^Xttituwna 5»«iMa 726031/ JBfe '•>*3_s Deuces up. Two new Fords served as official cars at the Indianapolis Motor Speedway in 1932. Eddie Rickenbacker and Ibng-time IMS Vice-President, "Pop" Myers, are in the Cabriolet; speedboat champion Gar Wood is at the wheel of the Roadster. Credit IMS. fl TECHNICAL HISTORY of the RACING FLATHEAby Mark Dees D APOLOGY-We printed a short article entitled "Racing History of the Flathead Ford" in the Sept/Oct V-8 Times that had appeared in "Deuce News" as written by Randy Leech of Mission Trail R.G. Unhappily,the piece had been taken from a series authored by long-time Early Ford V-8 Club member Mark L. Dees for Petersen Publishing Com pany's ROD &• CUSTOM magazine in 1973. I am the one atfault —for not checking with Mr. Leech before borrow ing the item, and I apologize to Mark Dees and to Peter sen Publishing for my carelessness. In return, they have been so gracious as to permit us to reprint the entire four- part series in The V-8 Times, commencing here. My thanks to Mr. Dees and to Bob Gottlieb of Petersen Pub lishing for their broad-minded attitude. — Roger Neiss, editor. _^<!>>3- Dual-downdraft Winfield SR as used on the 1935 Welch Indy cars and a number of other early V-8 hot rods. Credit: Dees -10- This aerodynamic Ford-based special managed 104 mph to become 2nd alternate starter in 1934. Engine modifications, if any, are unknown. Note the 16-inch Firestone Air Balloon street" tires and wheels. -
Integrated Circuit Design Macmillan New Electronics Series Series Editor: Paul A
Integrated Circuit Design Macmillan New Electronics Series Series Editor: Paul A. Lynn Paul A. Lynn, Radar Systems A. F. Murray and H. M. Reekie, Integrated Circuit Design Integrated Circuit Design Alan F. Murray and H. Martin Reekie Department of' Electrical Engineering Edinhurgh Unit·ersity Macmillan New Electronics Introductions to Advanced Topics M MACMILLAN EDUCATION ©Alan F. Murray and H. Martin Reekie 1987 All rights reserved. No reproduction, copy or transmission of this publication may be made without written permission. No paragraph of this publication may be reproduced, copied or transmitted save with written permission or in accordance with the provisions of the Copyright Act 1956 (as amended), or under the terms of any licence permitting limited copying issued by the Copyright Licensing Agency, 7 Ridgmount Street, London WC1E 7AE. Any person who does any unauthorised act in relation to this publication may be liable to criminal prosecution and civil claims for damages. First published 1987 Published by MACMILLAN EDUCATION LTD Houndmills, Basingstoke, Hampshire RG21 2XS and London Companies and representatives throughout the world British Library Cataloguing in Publication Data Murray, A. F. Integrated circuit design.-(Macmillan new electronics series). 1. Integrated circuits-Design and construction I. Title II. Reekie, H. M. 621.381'73 TK7874 ISBN 978-0-333-43799-5 ISBN 978-1-349-18758-4 (eBook) DOI 10.1007/978-1-349-18758-4 To Glynis and Christa Contents Series Editor's Foreword xi Preface xii Section I 1 General Introduction -
Design and Analysis of Leaf Spring in a Heavy Truck
View metadata, citation and similar papers at core.ac.uk brought to you by CORE provided by International Journal of Innovative Technology and Research (IJITR) Godatha Joshua Jacob * et al. (IJITR) INTERNATIONAL JOURNAL OF INNOVATIVE TECHNOLOGY AND RESEARCH Volume No.5, Issue No.4, June – July 2017, 7041-7046. Design And Analysis Of Leaf Spring In A Heavy Truck GODATHA JOSHUA JACOB Mr M.DEEPAK M.Tech (machine design) Student, Dept.of Assistant professor, Dept.of Mechanical Engineering, Mechanical Engineering, Kakinada Institute Of Kakinada Institute Of Engineering And Technology, Engineering And Technology, (Approved by AICTE (Approved by AICTE and Affiliated to Jawaharlal and Affiliated to Jawaharlal Nehru Technological Nehru Technological University , Kakinada) University , Kakinada) Abstract: A leaf spring is a simple form of spring, commonly used for the suspension in wheeled vehicles. Leaf Springs are long and narrow plates attached to the frame of a trailer that rest above or below the trailer's axle. There are monoleaf springs, or single-leaf springs, that consist of simply one plate of spring steel. These are usually thick in the middle and taper out toward the end, and they don't typically offer too much strength and suspension for towed vehicles. Drivers looking to tow heavier loads typically use multileaf springs, which consist of several leaf springs of varying length stacked on top of each other. The shorter the leaf spring, the closer to the bottom it will be, giving it the same semielliptical shape a single leaf spring gets from being thicker in the middle. Springs will fail from fatigue caused by the repeated flexing of the spring. -
Rover SD1 Suspension – the Macpherson the SD1 Has
Rover SD1 Suspension – The MacPherson The SD1 has independent front suspension. Each front wheel moves individually from the other and the following types are common. • Leading/trailing link systems • Double wishbones • Multi link systems • MacPherson Multi link systems can provide the best comfort and handling. Next best is the double wishbone if properly set up. For instance most American cars use it but the geometry often leaves room for improvement. And then there is the MacPherson, giving good comfort and reasonable handling. Why then, did Rover choose a slightly inferior system? They preferred the double wishbone approach but it would not leave room to locate the catalytic converters needed for the U.S. market, plus the cost was higher. So the simple MacPherson was chosen which consists basically of a coil spring and shock absorber built into the spring leg. The leg pivots on a ball joint on the lower control arm. This can be either an ordinary A- arm or a narrow lower control arm which locates the lower end of the strut in the transverse direction and a separate member called a radius rod locating the assembly in the longitudinal direction. However on the SD1 the anti-roll bar serves a double function as the longitudinal link taking the drive and brake forces and thereby eliminating the separate radius rod. At the top, the SD1 has a roller bearing (not shown here) to allow the spring leg to turn without the spring winding up. The strut itself is the load-bearing member in the assembly. ie: - The spring and shock absorber hold the car up. -
Four-Bar Linkage Synthesis for a Combination of Motion and Path-Point Generation
FOUR-BAR LINKAGE SYNTHESIS FOR A COMBINATION OF MOTION AND PATH-POINT GENERATION Thesis Submitted to The School of Engineering of the UNIVERSITY OF DAYTON In Partial Fulfillment of the Requirements for The Degree of Master of Science in Mechanical Engineering By Yuxuan Tong UNIVERSITY OF DAYTON Dayton, Ohio May, 2013 FOUR-BAR LINKAGE SYNTHESIS FOR A COMBINATION OF MOTION AND PATH-POINT GENERATION Name: Tong, Yuxuan APPROVED BY: Andrew P. Murray, Ph.D. David Myszka, Ph.D. Advisor Committee Chairman Committee Member Professor, Dept. of Mechanical and Associate Professor, Dept. of Aerospace Engineering Mechanical and Aerospace Engineering A. Reza Kashani, Ph.D. Committee Member Professor, Dept. of Mechanical and Aerospace Engineering John Weber, Ph.D. Tony E. Saliba, Ph.D. Associate Dean Dean, School of Engineering School of Engineering & Wilke Distinguished Professor ii c Copyright by Yuxuan Tong All rights reserved 2013 ABSTRACT FOUR-BAR LINKAGE SYNTHESIS FOR A COMBINATION OF MOTION AND PATH-POINT GENERATION Name: Tong, Yuxuan University of Dayton Advisor: Dr. Andrew P. Murray This thesis develops techniques that address the design of planar four-bar linkages for tasks common to pick-and-place devices, used in assembly and manufacturing operations. The analysis approaches relate to two common kinematic synthesis tasks, motion generation and path-point gen- eration. Motion generation is a task that guides a rigid body through prescribed task positions which include position and orientation. Path-point generation is a task that requires guiding a reference point on a rigid body to move along a prescribed trajectory. Pick-and-place tasks often require the exact position and orientation of an object (motion generation) at the end points of the task. -
Transverse Leaf Springs: a Corvette Controversy
Transverse Leaf Springs: A Corvette Controversy By Matt Miller Introduction A lot of people give Corvettes flack because they employ leaf springs. The mere mention of leaf springs conjures up images of suspensions on horse-drawn buggies, old cars and trucks, and Harbor Freight utility trailers. Even magazine reviews of the latest Corvettes talk about how “antiquated” their leaf spring designs are, and many a Corvette enthusiast has converted his car to aftermarket coilovers in the belief that they are inherently better than the composite transverse leaf springs found on the front and rear suspensions of all Corvettes since 1984. But is that true? Does the Corvette’s use of transverse leaf springs mean it has an inferior, outdated suspension design? The short answer is “No!” To find out why, we’ll cover some basics on springs and suspensions and see how the facts add up. Page 1 What is a Spring, Anyway? We all intuitively know what springs are. But technically speaking, a spring is an elastic mechanical device that stores potential energy. When mechanical energy is put into a spring, it deforms and can release that energy back in the opposite direction. We measure a spring’s energy storage by its “spring rate,” which defines its energy storage. The spring rate defines the increase in force required to move the spring a certain amount. For example, if a spring has a rate of 100 lb/in (pounds per inch), it means that 100 lbs of force will move one end of it 1”, an additional 100 lbs will move it another inch, and so on. -
Glossary Definitions
TC 9-524 GLOSSARY ACRONYMS AND ABBREVIATIONS TC - Training Circular sd - small diameter TM - Technical Manual Id - large diameter AR - Army Regulation ID - inside diameter DA - Department of the Army TOS- Intentional Organization for Standardization RPM - revolutions per minute LH - left hand SAE - Society of Automotive Engineers NC - National Coarse SFPM - surface feet per minute NF - National Fine tpf -taper per foot OD - outside diameter tpi taper per inch RH - right hand UNC - Unified National Coarse CS - cutting speed UNF - Unified National Fine AA - aluminum alloys SF -standard form IPM - feed rate in inches per minute Med - medical FPM - feet per minute of workpiece WRPM - revolutions per minute of workpiece pd - pitch diameter FF - fraction of finish tan L - tangent angle formula WW - width of wheel It - length of taper TT - table travel in feet per minute DEFINITIONS abrasive - natural - (sandstone, emery, corundum. accurate - Conforms to a standard or tolerance. diamonds) or artificial (silicon carbide, aluminum oxide) material used for making grinding wheels, Acme thread - A screw thread having a 29 degree sandpaper, abrasive cloth, and lapping compounds. included angle. Used largely for feed and adjusting screws on machine tools. abrasive wheels - Wheels of a hard abrasive, such as Carborundum used for grinding. acute angle - An angle that is less than 90 degrees. Glossary - 1 TC 9-524 adapter - A tool holding device for fitting together automatic stop - A device which may be attached to various types or sizes of cutting tools to make them any of several parts of a machine tool to stop the interchangeable on different machines. -
Performance Shock Absorbers
PERFORMANCE SHOCK ABSORBERS SINCE 1857 | koni-na.com SHOCK ABSORBER & SUSPENSION TECH 101 It’s easy to think of a powerful engine to make a car fast “dampers” as their job is to damp or control the car body and but ultimately the car is connected to the ground by the suspension motion as it goes over undulations and bumps small contact patches of the tires. We must optimize tire in the road. In a nutshell, the suspension’s springs carry the grip through the cars suspension to go faster. When the car weight of the car and for a given road input will establish accelerates, brakes, and turns, many forces of physics are how much motion the car will likely have. The shock absorber trying to make the mass of the car go in a different direction or damper serves as a timing device to regulate how long it from where the driver wants and road surface needs it to go. takes for this suspension motion to occur. The car’s suspension is the interface between tires and A good performing shock absorber will be firm enough to the car body in motion. If the suspension can control and slow or eliminate excessive body and suspension motion optimize the body motion and tire grip while smoothing the yet to allow enough motion to provide a good ride quality road impacts and the driver inputs, then the carSINCE goes faster,1857 is | koni-na.comand tire grip. If a suspension is too soft or too firm, the car, safer, and has better ride quality.