Mineralogical Characterization of Slags from the Oiola Site
Total Page:16
File Type:pdf, Size:1020Kb
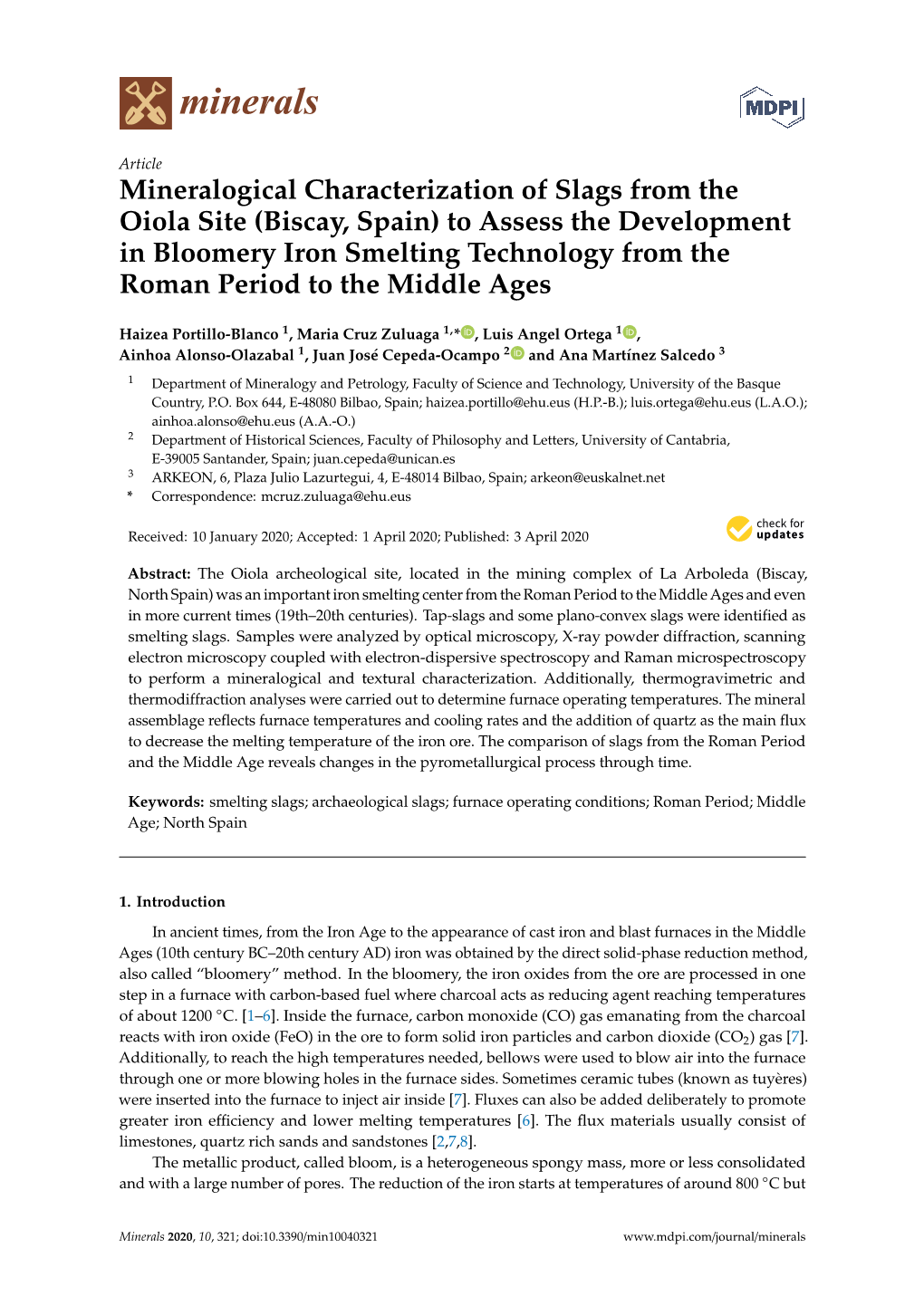
Load more
Recommended publications
-
From Base Metals and Back – Isamills and Their Advantages in African Base Metal Operations
The Southern African Institute of Mining and Metallurgy Base Metals Conference 2013 H. de Waal, K. Barns, and J. Monama From base metals and back – IsaMills and their advantages in African base metal operations H. de Waal, K. Barns, and J. Monama Xstrata IsaMill™ technology was developed from Netzsch Feinmahltechnik GmbH stirred milling technology in the early 1990s to bring about a step change in grinding efficiency that was required to make Xstrata’s fine-grained lead/zinc orebodies economic to process. From small-scale machines suited to ultrafine grinding, the IsaMill™ has developed into technology that is able to treat much larger tonnages, in coarser applications, while still achieving high energy efficiency, suited for coarser more standard regrind and mainstream grinding applications. The unique design of the IsaMillTM, combining high power intensity and effective internal classification, achieves high energy efficiency and tight product distribution which can be effectively scaled from laboratory scale to full-sized models. The use of fine ceramic media also leads to significant benefits in downstream flotation and leaching operations. These benefits are key drivers for the adoption of the technology into processing a diverse range of minerals worldwide, and offer major opportunities for power reduction and improved metallurgy for the African base metal operations. Keywords: IsaMill, regrind, energy efficiency, inert grinding. Introduction The development of the IsaMillTM, by MIM (now GlencoreXstrata) and Netzsch Feinmahltechnik GmbH, was initiated to enable the development of the fine-grained ore deposits at Mt Isa and McArthur River in Northern Australia. To liberate the valuable minerals and so produce a saleable concentrate this ultrafine-grained ore needed to be ground to a P80 of 7 μm. -
Mineral Processing
Mineral Processing Foundations of theory and practice of minerallurgy 1st English edition JAN DRZYMALA, C. Eng., Ph.D., D.Sc. Member of the Polish Mineral Processing Society Wroclaw University of Technology 2007 Translation: J. Drzymala, A. Swatek Reviewer: A. Luszczkiewicz Published as supplied by the author ©Copyright by Jan Drzymala, Wroclaw 2007 Computer typesetting: Danuta Szyszka Cover design: Danuta Szyszka Cover photo: Sebastian Bożek Oficyna Wydawnicza Politechniki Wrocławskiej Wybrzeze Wyspianskiego 27 50-370 Wroclaw Any part of this publication can be used in any form by any means provided that the usage is acknowledged by the citation: Drzymala, J., Mineral Processing, Foundations of theory and practice of minerallurgy, Oficyna Wydawnicza PWr., 2007, www.ig.pwr.wroc.pl/minproc ISBN 978-83-7493-362-9 Contents Introduction ....................................................................................................................9 Part I Introduction to mineral processing .....................................................................13 1. From the Big Bang to mineral processing................................................................14 1.1. The formation of matter ...................................................................................14 1.2. Elementary particles.........................................................................................16 1.3. Molecules .........................................................................................................18 1.4. Solids................................................................................................................19 -
A History of Tailings1
A HISTORY OF MINERAL CONCENTRATION: A HISTORY OF TAILINGS1 by Timothy c. Richmond2 Abstract: The extraction of mineral values from the earth for beneficial use has been a human activity- since long before recorded history. Methodologies were little changed until the late 19th century. The nearly simultaneous developments of a method to produce steel of a uniform carbon content and the means to generate electrical power gave man the ability to process huge volumes of ores of ever decreasing purity. The tailings or waste products of mineral processing were traditionally discharged into adjacent streams, lakes, the sea or in piles on dry land. Their confinement apparently began in the early 20th century as a means for possible future mineral recovery, for the recycling of water in arid regions and/or in response to growing concerns for water pollution control. Additional Key Words: Mineral Beneficiation " ... for since Nature usually creates metals in an impure state, mixed with earth, stones, and solidified juices, it is necessary to separate most of these impurities from the ores as far as can be, and therefore I will now describe the methods by which the ores are sorted, broken with hammers, burnt, crushed with stamps, ground into powder, sifted, washed ..•. " Agricola, 1550 Introduction identifying mining wastes. It is frequently used mistakenly The term "tailings" is to identify all mineral wastes often misapplied when including the piles of waste rock located at the mouth of 1Presented at the 1.991. National mine shafts and adi ts, over- American. Society for Surface burden materials removed in Mining and Reclamation Meeting surface mining, wastes from in Durango, co, May 1.4-17, 1.991 concentrating activities and sometimes the wastes from 2Timothy c. -
Mineral Beneficiation Contents
Lecture 10: Mineral Beneficiation Contents: Preamble What constitutes mineral beneficiation Size reduction technology Concentration technologies: Basics Recovery and grade Separation efficiency Illustration on separation efficiency Concentration methods Conclusions References Keywords: mineral beneficiation, Milling, gravity concentration flotation Preamble Mineral beneficiation is the first step in extraction of metal from natural resources. With the depletion of high grade metal ores it is important to increase the metal grade of an ore by physical methods; which are termed mineral beneficiation .The objectives of mineral beneficiation are • To increase the metal grade of ore • To reduce the amount of gangue minerals so that lower volume of slag forms in pyromettallurgical extraction of metals .Slag contains mostly gangue minerals. • To decrease the thermal energy required to separate liquid metal from gangue minerals. • To decrease the aqueous solution requirement in hydrometturgical extraction of metals. In this lecture, mineral beneficiation science and technology are briefly reviewed so that readers can apply materials balance principles. Details about the mineral beneficiation can be studied in the reference given in this lecture. What constitutes mineral beneficiation? Ore is an aggregate of minerals and contains valuable and gangue minerals .The mineral beneficiation involves separations of gangue minerals from ore and is done in the following two stages: 1. Liberation of valuable mineral by size reduction technologies. In most ores the valuable minerals is distributed in the matrix of ore. 2. Concentration technologies to separate the gangue minerals and to achieve increase in the content of the valuable mineral to increase the metal grade. Sizes reduction technologies Size reduction or communication is an important step and may be used 9 To produce particles of required sizes and shapes 9 To liberate valuable mineral so that it can be concentrated. -
Isamill™ Technology Used in Efficient Grinding Circuits
1 IsaMill™ Technology Used in Efficient Grinding Circuits B.D. Burford1 and L.W. Clark2 High intensity stirred milling is now an industry accepted method to efficiently grind fine and coarse particles. In particular, the IsaMill™, which was invented for, and transformed the fine grinding industry, is now being included in many new comminution circuits in coarser applications. While comminution has always been regarded as important from a processing perspective, the pressure being applied by environmental concerns on all large scale power users, now make highly energy efficient processes more important than ever. The advantages that were developed in fine grinding in the early IsaMill™ installations have been carried over into coarse grinding applications. These advantages include a simple grinding circuit that operates in open circuit with a small footprint, the ability to offer sharp product size classification, as well as the use of inert media in a high energy intensive environment. This paper will examine the use of IsaMill™ technology in fine grinding (P80 below 15 micron), and examine the use of the technology in conventional grinding applications (P80 20 - 150 µm). Recent installations will be examined, including fine and coarse grinding applications, as well as the recent test work that was undertaken using an IsaMill™ in a primary grinding circuit, and the resulting circuit proposal for this site. While comminution has been relatively unchanged for the last century, the need to install energy efficient technology will promote further growth in IsaMill™ installations, and result in one of the biggest challenges to traditional comminution design. 1. Senior Process Engineer, Xstrata Technology, L4, 307 Queen Street, Brisbane 4000, Qld, Australia 2. -
Damage Cases and Environmental Releases from Mines and Mineral Processing Sites
DAMAGE CASES AND ENVIRONMENTAL RELEASES FROM MINES AND MINERAL PROCESSING SITES 1997 U.S. Environmental Protection Agency Office of Solid Waste 401 M Street, SW Washington, DC 20460 Contents Table of Contents INTRODUCTION Discussion and Summary of Environmental Releases and Damages ......................... Page 1 Methodology for Developing Environmental Release Cases ............................... Page 19 ARIZONA ASARCO Silver Bell Mine: "Waste and Process Water Discharges Contaminate Three Washes and Ground Water" ................................................... Page 24 Cyprus Bagdad Mine: "Acidic, Copper-Bearing Solution Seeps to Boulder Creek" ................................ Page 27 Cyprus Twin Buttes Mine: "Tank Leaks Acidic Metal Solution Resulting in Possible Soil and Ground Water Contamination" ...................................... Page 29 Magma Copper Mine: "Broken Pipeline Seam Causes Discharge to Pinal Creek" ................................ Page 31 Magma Copper Mine: "Multiple Discharges of Polluted Effluents Released to Pinto Creek and Its Tributaries" .................................................... Page 33 Magma Copper Mine: "Multiple Overflows Result in Major Fish Kill in Pinto Creek" ............................... Page 36 Magma Copper Mine: "Repeated Release of Tailings to Pinto Creek" .......................................... Page 39 Phelps Dodge Morenci Mine: "Contaminated Storm Water Seeps to Ground Water and Surface Water" ................................................................ Page 43 Phelps Dodge -
Ore, Iron, Artefacts and Corrosion
. SERIE C NR 626 AVHANDLINGAR OCH UPPSATSER ARSBOK 61 NR 11 OLOF ARRHENIUS ORE, IRON, ARTEFACTS AND CORROSION WITH 4 PLATES STOCKHOLM 1967 SVERTGES GEOLOGISKA UNDERSOKNING SERIE C NR 626 ARSBOK 6 l NR I I OLOF ARRHENIUS ORE, IRON, ARTEFACTS AND CORROSION WITH 4 PLATES STOCKHOLM 196 7 Contents The conditions of the investigation ....................... Elements on which studies are made. ...................... Methods and sources of material ........................ Conditions of analysis ............................ What ores were first used in the production of iron? ................ The formation, occurrence and chemical composition of limonite ores ........ Synopsis of regions in which lake iron ore has a relatively high frequency of high con- centration of the elements indicated ...................... Rock ores. ................................. Synopsis of regions in which rock ores have a relatively high frequency of high concentra- tions of the elements indicated ........................ Artefacts .................................. Synopsis of regions where artefacts show relatively high frequencitl of the elements indicated ................................. Phosphorus in iron ............................. Coal in iron ............................... Alloying elements. Rust ........................... Summary .................................. Appendix: The microstructure after reduction of phosphorus-rich iron ore with charcoal at different temperatures. By Torsten Hansson and Sten Modin .......... Literature. ................................ -
Identification and Description of Mineral Processing Sectors And
V. SUMMARY OF FINDINGS As shown in Exhibit 5-1, EPA determined that 48 commodity sectors generated a total of 527 waste streams that could be classified as either extraction/beneficiation or mineral processing wastes. After careful review, EPA determined that 41 com modity sectors generated a total of 354 waste streams that could be designated as mineral processing wastes. Exhibit 5-2 presents the 354 mineral processing wastes by commodity sector. Of these 354 waste streams, EPA has sufficient information (based on either analytical test data or engineering judgment) to determine that 148 waste streams are potentially RCRA hazardous wastes because they may exhibit one or more of the RCRA hazardous characteristics: toxicity, ignitability, corro sivity, or reactivity. Exhibit 5-3 presents the 148 RCRA hazardous mineral processing wastes that will be subject to the Land Disposal Restrictions. Exhibit 5-4 identifies the mineral processing commodity sectors that generate RCRA hazardous mineral processing wastes that are likely to be subject to the Land D isposal Restrictions. Exhibit 5-4 also summarizes the total number of hazardous waste streams by sector and the estimated total volume of hazardous wastes generated annually. At this time, however, EPA has insufficient information to determine whether the following nine sectors also generate wastes that could be classified as mineral processing wastes: Bromine, Gemstones, Iodine, Lithium, Lithium Carbonate, Soda Ash, Sodium Sulfate, and Strontium. -
Improving Energy Efficiency Across Mineral Processing and Smelting Operations – a New Approach
Improving Energy Efficiency Across Mineral Processing and Smelting Operations – A New Approach C L Evans1, B L Coulter2, E Wightman3 and A S Burrows4 ABSTRACT now reporting their performance in this area using a range of sustainability indicators. Among these, energy use and its impact With their commitment to sustainable development in an increasingly carbon-constrained world, many resources companies are focused on on climate change are priorities, with many company reducing the energy required to create their final products. In particular, sustainability reports including total energy use and associated the comminution and smelting of metal-bearing ores are both highly greenhouse gas (GHG) emissions in both absolute and relative energy-intensive processes. If resource companies can optimise the terms (ie normalised to a per unit product) among their key energy efficiency across these two processing stages, they can directly environmental sustainability indicators. Companies are setting reduce their overall energy consumption per unit mass of metal produced targets to achieve improvements in these indicators, but at the and thus reduce their greenhouse gas footprint. same time there is a global trend to more complex and lower Traditional grinding and flotation models seek to improve the grade orebodies which are more energy-intensive to process. As efficiency of mineral processing, but they do not consider the energy used a result, resource companies are having to become more by downstream metal production, eg smelting and refining. Concentrators innovative to improve the environmental sustainability and the and smelters individually may be running efficiently, but are they optimising energy consumption of the overall system? A key step towards efficiency of their operations. -
Gravity Concentration in Artisanal Gold Mining
minerals Review Gravity Concentration in Artisanal Gold Mining Marcello M. Veiga * and Aaron J. Gunson Norman B. Keevil Institute of Mining Engineering, University of British Columbia, Vancouver, BC V6T 1Z4, Canada; [email protected] * Correspondence: [email protected] Received: 21 September 2020; Accepted: 13 November 2020; Published: 18 November 2020 Abstract: Worldwide there are over 43 million artisanal miners in virtually all developing countries extracting at least 30 different minerals. Gold, due to its increasing value, is the main mineral extracted by at least half of these miners. The large majority use amalgamation either as the final process to extract gold from gravity concentrates or from the whole ore. This latter method has been causing large losses of mercury to the environment and the most relevant world’s mercury pollution. For years, international agencies and researchers have been promoting gravity concentration methods as a way to eventually avoid the use of mercury or to reduce the mass of material to be amalgamated. This article reviews typical gravity concentration methods used by artisanal miners in developing countries, based on numerous field trips of the authors to more than 35 countries where artisanal gold mining is common. Keywords: artisanal mining; gold; gravity concentration 1. Introduction Worldwide, there are more than 43 million micro, small, medium, and large artisanal miners extracting at least 30 different minerals in rural regions of developing countries (IGF, 2017) [1]. Approximately 20 million people in more than 70 countries are directly involved in artisanal gold mining (AGM), with an estimated gold production between 380 and 450 tonnes per annum (tpa) (Seccatore et al., 2014 [2], Thomas et al., 2019 [3], Stocklin-Weinberg et al., 2019 [4], UNEP, 2020 [5]). -
Early Rejection of Gangue – How Much Energy Will It Cost to Save Energy?
Early rejection of gangue – How much energy will it cost to save energy? Grant Ballantyne 1,2 , Marko Hilden 1,2 and Malcolm Powell 1,2 1The University of Queensland, JKMRC-SMI 2Co-Operative Research Centre for Optimising Resource Extraction (CRC ORE) Contact: [email protected] ABSTRACT Comminution accounts for approximately 30 to 40% of the energy consumed on an average mine site (DOE, 2007) and somewhere from 4 to 9% of Australia’s total energy consumption (Tromans, 2008). Additionally, if one includes the energy embodied in steel grinding consumables, this may increase comminution energy by more than 50% (Musa and Morrison, 2009). Energy savings of up to 50% are theoretically possible by employing novel circuit designs and using smart separation techniques, which reject coarse liberated gangue. A range of different strategies such as selective mining, screening, ore sorting, coarse flotation and dielectrophoresis can be used to reject the coarse liberated gangue at different particle sizes. These technological advances have the potential to increase the throughput in the comminution circuit, while decreasing the energy consumed per tonne or ounce of metal produced. This paper investigates the energy consumed through sorting, and the optimum position of these technologies in the flow sheet, in terms of energy, cost and risk. The findings form the basis of a methodology that can identify the potential upgrades/changes required to obtain a positive return from these sorting and coarse separation techniques. Reference as: Ballantyne, G.R., Hilden, M., Powell, M.S., 2012. Early rejection of gangue – How much energy will it cost to save energy?, In Comminution '12, ed. -
Iron, Steel and Swords Script
Iron Ores General Remarks This planet consists of iron (32.1%), oxygen (30.1%), silicon (15.1%), magnesium (13.9%), sulfur (2.9%), nickel (1.8%), calcium (1.5%), and aluminium (1.4%); the remaining 1.2% are "trace amounts" of the 80 or so remaining elements. Most of that iron constitutes the core of the planet but we will not run out of iron compounds or iron ore found near to the surface for some time to come. Why is iron so prominent in this (and other) planet ? Because planets were formed from the stuff bred inside the first stars. The reaction chain for generating energy by nuclear fusion starts with hydrogen and stops after iron has been bred. Iron, if you like, is the ash eventually produced by fusing hydrogen to helium, helium and hydrogen to lithium, and so on. When those first stars "burnt out" after a few billon years, some of them coughed up their ashes in a mighty supernova explosion. In time, new stars were formed. Some of these are still burning and visible at night. One (our very own sund) is only visible during the day from a clumped-together iron-rich ash ball called earth. Advanced From the viewpoint of chemistry, iron (like copper) is a tricky element that can form many oxides, sulfides, carbonates, and so on. All these compounds could be used for smelting iron but some are better for that purpose than others. Sulfides are usually bad news. We know that from smelting copper and expect similar problems when smelting iron.