STANLEY PLANES and SCREW THREADS by John Bates
Total Page:16
File Type:pdf, Size:1020Kb
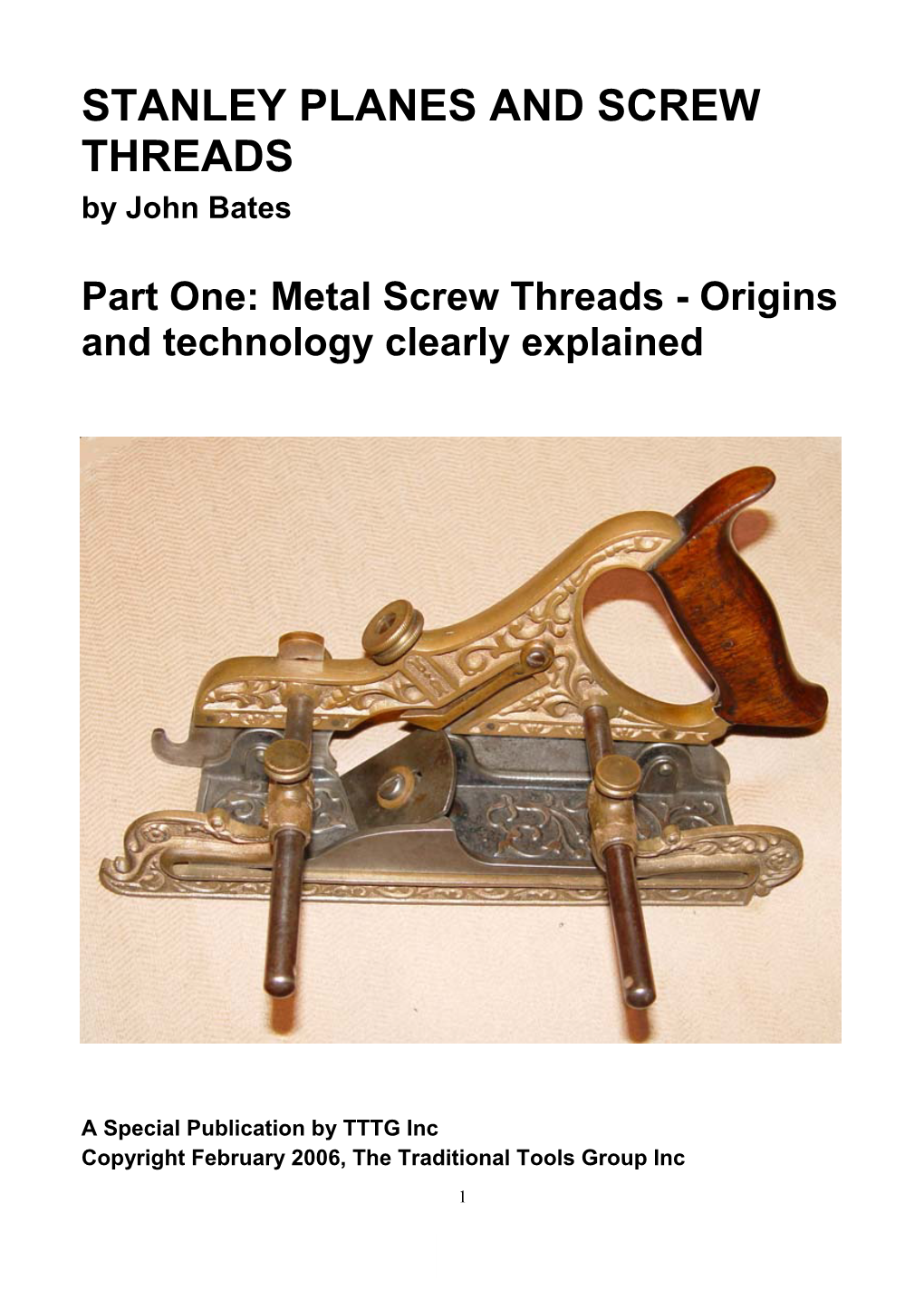
Load more
Recommended publications
-
Manufacturing Processes
Module 1 Classification of Metal Removal Processes and Machine tools Version 2 ME IIT, Kharagpur Lesson 2 Basic working principle, configuration, specification and classification of machine tools Version 2 ME IIT, Kharagpur Instructional Objectives At the end of this lesson, the students should be able to : (a) Describe the basic functional principles of machine tools (i) Illustrate the concept of Generatrix and Directrix (ii) Demonstrate Tool – work motions (iii) Give idea about machine tool drives (b) Show configuration of basic machine tools and state their uses (c) Give examples of machine tools - specification (d) Classify machine tools broadly. Basic functional principles of machine tool operations Machine Tools produce desired geometrical surfaces on solid bodies (preformed blanks) and for that they are basically comprised of; • Devices for firmly holding the tool and work • Drives for providing power and motions to the tool and work • Kinematic system to transmit motion and power from the sources to the tool-work • Automation and control systems • Structural body to support and accommodate those systems with sufficient strength and rigidity. For material removal by machining, the work and the tool need relative movements and those motions and required power are derived from the power source(s) and transmitted through the kinematic system(s) comprised of a number and type of mechanisms. (i) Concept of Generatrix and Directrix • Generation of flat surface The principle is shown in Fig. 2.1 where on a flat plain a straight line called Generatrix (G) is traversed in a perpendicular direction called Directrix (D) resulting a flat surface. • Generation of cylindrical surfaces The principles of production of various cylindrical surfaces (of revolution) are shown in Fig. -
Sliding Headstock Type CNC Automatic Lathe
Sliding Headstock Type CNC Automatic Lathe Introducing Citizen's newest development, the D25, equipped with The large number of tools, for both main and sub spindle, provides double gang tool posts and B axis (Type VIII). The double gang lay- cost effective production of complex workpieces. out enables short cycle times for high productivity at low part cost. • Next generation CNC system with touch screen and qwerty keyboard. Easy set up with on screen graphical prompts. 3 × Y axis, 3 × Z axis • B axis (Type VIII) for front-back machining • Independent adjustable angle rotary tools to sub spindle • Power and speed: 5.5 kW and 10,000 rpm • With/without guide bushing – switchable operation 02 Cincom D25 Axis Structure and Tool Layout Z2 axis to second gang for opposed balance cutting to rst gang equipped with adjustable rotary tool for face, radial or angle ma- and for simultaneous rough and nish machining. Back tool post chining. B axis is on the rst gang for complex machining on main (Y3 axis) accepts radial or face modular xed/rotary tools and is and sub spindles. Y2 Front Spindle Z2 Z1 X2 Gang tool post No.2 Y1 Y3 X1 Back tool post B1 Gang tool post No.1 Opposite tool post X3 Z3 Back Spindle Tooling Code Description DTF116 4 Tools (5/8" sq./ cut-off: ¾" sq.) Turning holder DTF216 3 Tools (5/8" sq.) Sleeve holder DDF101 4 Front + 7 Back (1" dia.) 3 Modular stations U31B(S4) 1 Adjustable rotary tool (0-90 deg.: option) is available Gang rotary tool on the top postion 4 × double ended spindles, rotary tools U32B(S3) B-axis (0-135 deg.) Back rotary tool U151B(S5) 4 Modular stations Opposite tool post U120B 2 Fixed tools (¾" dia.) B Axis 4 × double ended spindles, 0-135 deg, usable for both main and sub spindles. -
Russian Precision Metal-Cutting Machines
SREDNEVOLGSKY STANKOZAVOD LTD. FEDERAL STATE UNITARY ENTERPRISE FEDERAL RESEARCH AND PRODUCTION CENTER «PA «START» named after M.V.PROTSENKO» HIGH-QUALITY SOLUTIONS IN THE FIELD OF METAL- WORKING RUSSIAN PRECISION METAL-CUTTING MACHINES www.svsz.ru www.startatom.ru SREDNEVOLGSKY STANKOZAVOD LTD. TECHNOLOGICAL CAPABILITIES OF SREDNEVOLGSKY STANKOZAVOD LTD. The Srednevolgsky stankozavod Ltd. was established in 1876. It is one of the oldest machine building enterprises, not only in Russia, but also in the world. During more than 100 years the plant has produced more than half a million of lathes. Legendary models of machines 1А616 and 16B16 are still respected by turner for its high reliability, easy operation and high processing accuracy. The plant was the first in the USSR to master the production of CNC machines. Srednevolgsky stankozavod Ltd. has all the technological competencies for production of high precision lathes. The Machine Plant range of products includes more than 200 units of technological equipment which enables high-pre- cision machining of large pieces of casting, gear process- ing, ultra-precise finishing operations of surface grinding of spindles, shafts, gears, precision boring operations. All me- chanical components of machines, including base frame, spindle assembly, stand, tailstock are made directly at the facilities of Srednevolgsky stankozavod Ltd. To ensure the required accuracy and its long-term opera- tion, all basic parts of machines are subjected to various stabilization of geometrical sizes (natural and artificial ag- ing), bed guides of high quality cast iron are heat treated at high frequency current installations. Critical parts of ma- chines (spindles, quill, lead screws, gears, etc., are made of alloy steels which are subjected to various heat treatment methods, including ionic and gas nitriding, nitrogen and ionic carbonization, etc. -
Validation of Thermal Errors Compensation Models for Different Machine Tool Structures Via Test Pieces
Validation of thermal errors compensation models for different machine tool structures via test pieces Otakar Horejš, Martin Mareš, Lukáš Havlík 1. Introduction 3. Six-spindle automatic lathe Although real-time software compensations of thermal errors exist, The test pieces can be also employed for the evaluation of the majority of these models are not sufficiently validated in real machine tool thermal errors. This application is illustrated on a six- finishing operations using a test piece. The accuracy and spindle automatic lathe. The basic scheme of the test piece, robustness of the developed models are mostly examined using manufactured by a specific technology, is depicted in Figure below. non-cutting measurements. In contrast, machining tests can be more intuitively understood to evaluate the machine’s accuracy for typical machine tool users. Moreover, the machined test piece represents a suitable method to verify thoroughly the industrial applicability of the developed thermal errors compensation model for machine tool builders. The paper presents the authors’ recent research on these issues. Specific test pieces for different machine tool structures are illustrated (test pieces for a gantry-type 5-axis milling centre with a rotary table, a six-spindle automatic lathe and a vertical turning lathe). 2. Gantry-type 5-axis milling centre The test piece material was an aluminium alloy covered with an The diameter denominated as D1 of the test piece is manufactured eloxal coating for better visibility of cutting tool imprints on the at the first machining position (MP), the diameter denominated as surface caused by thermal error at the TCP in Z-direction. -
M32 Sliding Headstock Type CNC Automatic Lathe
M32 Sliding Headstock Type CNC Automatic Lathe M32-VIII Ultimate Gang + Turret: The M32 is Reborn While inheriting the basic configuration of “gang tool post + turret”, the new M32 has pursued the optimal balance of strength and weight through structural analysis, and greatly improves the rigidity that is the cornerstone of machining. In addition, a single drive mechanism is introduced for rotary tools on the turret tool post, together with updated tooling. The rotary tool drive motor on each tool post has also been enhanced. 5.5/7.5 kW high-power spindle motors are adopted for both front and back spindles, achieving powerful machining and high acceleration/deceleration. The gang tool post features a B-axis spindle (Type VIII) that supports contouring through 5-axis control. The back tool post is equipped with an adjustable angular spindle (Type VII/VIII) for more complex machining in combination with the Y axis. Enhanced back machining capability is also increased due to the flexibilty of the machining process. In addition, a 38mm oversized specification option is available, and it is possible to switch between guide bush and guide bushless operation. 4 M32 Citizen Basic Structure The image shows the type VIII Rear tool post X1 Type V: 5 stations Main spindle Type VII: Max. of 9 stations (including 3 adjustable angle tools) Y1 Main spindle speed: 8,000 min-1 Type VIII: Max. of 9 stations (including 3 adjustable angle tools) Motor: 5.5/7.5 kW Y3 Max. machining length: 320 mm/1 chucking (GB) B1 X3 Z1 Opposed spindle Main spindle speed: -
Manufacuting Technology
ME 6402 -Manufacturing Technology - II IV Sem / II Year B.E. (Mechanical Engineering) Department of Mechanical Engineering R.M.K.ENGINEERINGCOLLEGE R.S.M. Nagar, Kavaraipettai – 601 206. UNIT I - THEORY OF METAL CUTTING INTRODUCTION: CUTTING TOOL: SINGLE POINT CUTTING TOOL: NOMENCLATURE SINGLE POINT TOOL: MECHANICS OF METAL CUTTING: TYPES OF CHIPS: COOLANT OR CUTTING FLUIDS OR EMULSIONS: FUNCTIONS OR USES OF COOLANTS OR CUTTING FLUIDS: TYPICAL PROPERTIES OF TOOL MATERIALS: ------------------------------X-------------------------------- UNIT-II - CENTRE LATHE AND SPECIAL PURPOSE LATHE INTRODUCTION: TYPES OF LATHE: SPEED LATHE: CENTRE LATHE OR ENGINE LATHE: BENCH LATHE: TOOL ROOM LATHE: CAPSTAN AND TURRET LATHE: SPECIAL PURPOSE LATHE: AUTOMATIC LATHE: CONSTRUCTION OF LATHE MACHINE: BED: HEAD STOCK: TAIL STOCK: CARRIAGE: THREAD CUTTING MECHANISM: ACCESSORIES AND ATTACHMENTS OF LATHE: SPECIFICATION OF LATHE: LATHE OPERATIONS: TAPERS AND TAPER TURNING: TAPER TURNING BY SWIVELLING THE COMPOUND REST: TAPER TURNING ATTACHMENT METHOD: TAPER TURNING WITH TAILSTOCK SET OVER METHOD: FORM TOOL METHOD: TAPER TURNING WITH DOUBLE HEADS: THREAD CUTTING: DRILLING ON A LATHE: CUTTING SPEED: FEED: ---------------------------X------------------------------ UNIT-III, OTHER MACHINE TOOLS DRILLING INTRODUCTION: CONSTRUCTION OF DRILLING MACHINE: TYPES OF DRILLING MACHINE: PORTABLE DRILLING MACHINE: SENSITIVE DRILLING MACHINE: UPRIGHT DRILLING MACHINE: RADIAL DRILLING MACHINE: GANG DRILLING MACHINE: MULTIPLE-SPINDLE DRILLING MACHINE: TYPES OF DRILLS: TWIST DRILL -
Quantity Production
QUANTITY PRODUCTION By: Jitender Jadon Shobhit Institute of Engineering and Technology Deemed to be University CONTENTS Quantity production: Introduction, Characteristics and properties Economic Order Quantity Applications of quantity production Process planning and scheduling for quantity production Single spindle automatic lathe Transfer machines CNC machine tools Design and use of jigs and fixtures in machine shops. INTRODUCTION Manufacture of discrete parts or assemblies using a continuous process are called Quantity production. This production system is justified by very large volume of production. The machines are arranged in a line or product layout. Product and process standardization exists and all outputs follow the same path. Helical Gear produced in Quantity CHARACTERISTICS OF QP Standardization of product and process sequence. Large volume of products. Shorter cycle time of production. Lower in process inventory. Perfectly balanced production lines. Production planning and control is easy. Material handling can be completely automatic. PROPERTIES OF QP ECONOMIC ORDER QUANTITY Economic order quantity (EOQ) is the ideal order quantity a company should purchase to minimize inventory costs such as holding costs, shortage costs, and order costs. This production-scheduling model was developed in 1913 by Ford W. Harris and has been refined over time. The formula assumes that demand, ordering, and holding costs all remain constant. Production cost curve and Economic Order Quantity FORMULA AND CALCULATION OF ECONOMIC ORDER QUANTITY The formula for EOQ is: where: Q = EOQ units D = Demand in units (typically on an annual basic) S = Order cost (per purchase order) H = Holding costs (per unit, per year) ADVANTAGES OF QP Higher rate of production with reduced cycle time. -
Automatic Lathe AUTOMATIC LATHE These Are Machine Tools in Which Components Are Machined Automatically
Automatic lathe AUTOMATIC LATHE These are machine tools in which components are machined automatically. The working cycle is fully automatic that is repeated to produce duplicate parts with out participation of operator. All movements of cutting tools, their sequence of operations, applications, feeding of raw material, parting off, un loading of finished parts all are done on machine. All working & idle operations are performed in definite sequence by control system adopted in automatic which is set up to suit a given work. Only operation reqd to be performed manually is loading of bar stock/ individual casting/ forged blanks. These machines are used when production requirements are too high for turret lathes to produce economically Classification of automatic lathe . Depending up on type of work machined these machines are classified as: 1. Magazine loaded Automatics: . Machines used for producing components from separate blanks. Also called as automatic checking machines. • 2.Automatic Bar Machines: . designed for machining components from bar/ pipe stock. M/c’s are used for manufacture of high quality fasteners (screws, nuts), bushings, shafts, rings, rollers, handles which are usually made of bar / pipe stock. • Depending upon number of work spindles, automatic lathes are classified as: 1. Single Spindle Automatics. 2. Multi Spindle Automatics. • Depending upon purpose & arrangement of spindle also automatics are classified as: 1. Purpose General & single purpose m/c. 2. Arrangement of spindle Horizontal & vertical 1. Single spindle lathe:- • These machines produce short w/p’s of simple form by means of cross sliding tools. Machines are simple in design. • Head stock with spindle is mounted on bed. -
MS24-6 CNC Multi-Spindle Automatic Lathe for High Productivity and Short Cycle and Setup Times
MS24-6 CNC multi-spindle automatic lathe for high productivity and short cycle and setup times better.parts.faster. INDEX MS24-6 INDEX CNC multi-spindle automatic lathe: high level of flexibility, shorter setup and cycle times With the INDEX MS24-6 multi-spindle automatic lathe, which The INDEX quick-clamping system, patented W-serration, and can be configured according to manufacturers' specific ergonomic open-front work area minimize setup times. needs, INDEX is presenting a machine concept that meets Maximum dynamic response and minimum non-productive stringent requirements and the highest demands. times also contribute to low part costs. Six main spindles, up to two swiveling synchronized spindles, and up to twelve tool carriers, which can be freely configured as cross slides X/Y/Z or boring slides Z, enable highly produc- tive machining options. Flexible, highly productive, and quick to set up – the machine concept of the INDEX MS24-6: • Highly-dynamic cross slide with sliding guide (X axis) • Extremely fast swiveling synchronized spindles with C axis • Non-wearing Z axis thanks to quills with hydrostatic support - the swivel arm is locked in its working position by a three- • Freely accessible working area, making setup particularly piece Hirth coupling providing maximum rigidity easy • Up to 6 tools for rear end machining per swiveling synchro- • Fast tool setup with the INDEX quick clamping system and nized spindle its W-serration interface • High productivity per unit area thanks to reduced footprint • Chucked part machining with loading and unloading by lin- ear or robot handling units 3 INDEX MS24-6 The core: it’s original, when it originates from INDEX Our hallmark: the spindle drum The results are optimized material removal, maximum surface The compact spindle drum ensures maximum precision in quality, short production times per piece, and extended tool each and every position through the use of a Hirth coupling. -
CNC Precision Automatic Lathe Sliding Headstock Type Automatic Lathe That Encompasses the Entire Process 12-Station Turret +
External View BH20/BH20Z (20) 185 700 1,405 1,585 520 425 (160) CNC Precision Automatic Lathe 1 ,910 570 ( 560 ) 2 ,480 3 ,040 1,733 1,000 (Center height) 1,000 External View BH38 1,790 610 810 1 ,130 1 ,200 2 ,330 400 ( 100 ) ( 563 ) 2 ,730 810 980 3 ,393 1,700 1,000 Sliding headstock type automatic lathe that encompasses the entire process 12-station turret + Gang type tool post + Back spindle Export permission by the Japanese Government may be required for exporting our products in accordance with the Foreign Exchange and Foreign Trade Law. Please contact our sales office before exporting our products. The specifications of this catalogue are subject to change without prior notice. 12-20, TOMIZAWA-CHO, NIHONBASHI, CHUO-KU, TOKYO 103-0006, JAPAN Phone : 03-3808-1172 Facsimile : 03-3808-1175 CAT.NO.E112524.JUN.3T(H) Complex-shaped parts can be machined from bar stocks ■ 12-station turret with independent drive mechanism ■ Cycle time drastically shortened using three-path control ■ Complete machining from bar stock BH20, BH20Z: Max. 35 tools BH38: Max. 34 tools ■ Powerful main-spindle and back-spindle motors ■ Many NC features are provided as standard. ■ Automatic programming system for BH (optional) Photo: BH20/BH20Z Machining example Material SUS303 Bar stock diameter φ25 Conventional model Simultaneous machining time 45 18 Main BH20 spindle Z1 M16 1 6 4 -0.01 -0.03 230sec. Y3 φ3 Y3 φ17 Back spindle ±0.03 X1 φ8 Y1 X3 Z3 φ22 X3 Z3 φ24 BH38 X2 BH20Z (10) 5 5 10 2-M4 Simultaneous machining time Z2 (30) 40 Main spindle 70 160sec. -
General Purpose Machine Tools “LATHE OPERATIONS”
General Purpose Machine Tools “LATHE OPERATIONS” V.Gunasegaran Assistant Professor Department of Mechanical Engineering School of Mechanical Sciences BSAU, Chennai - 48 V.Gunasegaran, Assistant Professor, Department of Mechanical Engineering, BSACIST, Chennai - 48 Introduction Lathe is a machine, which removes the metal from a piece of work to the required shape & size Used to manufacture cylindrical shapes from a range of materials including; steels and plastics The Lathe may be operated by – Manual lathes – Computer controlled lathes (CNC machines) V.Gunasegaran, Assistant Professor, Department of Mechanical Engineering, BSACIST, Chennai - 48 Photograph of lathe V.Gunasegaran, Assistant Professor, Department of Mechanical Engineering, BSACIST, Chennai - 48 Principal parts V.Gunasegaran, Assistant Professor, Department of Mechanical Engineering, BSACIST, Chennai - 48 Types of Lathe According to the configuration – Vertical – Horizontal • Centre lathe, Engine lathe, bench lathe According to the Purpose or use – General purpose – Single purpose – Special purpose • Tool room lathe, tracer / copying lathe V.Gunasegaran, Assistant Professor, Department of Mechanical Engineering, BSACIST, Chennai - 48 Contd., According to the size and capacity – Small (low duty) – Medium (medium duty) – Large (heavy duty) – Mini or micro • Table top lathe According to the degree of automation – Non-automatic – Semi-automatic – Automatic V.Gunasegaran, Assistant Professor, Department of Mechanical Engineering, BSACIST, Chennai - 48 Contd., According -
CNC Precision Automatic Lathe 60 60.9 340
Tooling zone SS20/SS26/SS32/SS32L 70 22 65 ( T01 ~T03 ) (Stroke) (SS32L) 17 65 51 16 51 T01 51 60 29 T02 CNC Precision Automatic Lathe 60 60.9 340 (X2 Stroke) (X2 T03 38.5 30.5 SUPER SWISSTURN 238 55 66.1 332 348 45 (Y1 Stroke) (Y1 35 350 38 16 (Z2 Stroke) 35 38 45.5 38 51 14 SS20=368 83 2 38 SS26=369 41.5 SS32 ,SS32L= 3 6 8 Stroke) (Y2 Z1 Stroke 69 2 16 Option 5-φ22 3-φ20 SS20=220 (Double face spindle) 71 SS26=270 22.5 (Stroke) SS32=320 26 69 26 2 2 Reference tool position 70 Z1 Stroke Guide-bushing-less 30.5 SS20 =45 SS26 =50 SS32L=70 Appearance Opposed gang tool combination machine Modular tool zone effectively handles complex parts 580 Ideal for short run or extended production. 2020 1630 1295 1050 2020 170 1000 505 1675 The export of this product is subject to an authorization from the government of the exporting country and/or Japan. Check with the government agency for authorization. The specifications of this catalogue are subject to change without prior notice. 1-9-10, Horidome-cho, Nihonbashi, Chuo-ku, Tokyo, 103-0012, JAPAN 910 Day Hill Road Windsor, CT. 06095 Phone : 03-3808-1172 Phone: (860)687-3400 Facsimile : 03-3808-1175 Fax: (860)687-3401 http://www.remsales.com CAT.NO.E (H) Highly capable tool zone enables simultaneous machining Wide tooling zone Long stroke rotary guide bushing Simultaneous operation of main and sub spindle. Y-axis back tool post with cross tool spindle shortens drastically the cycle time ■Back slitting ■Vertical traverse milling with back endmill ■Back cross drilling and cross tapping ■Deburring of front