SANDIA REPORT a Review of the Available Technologies for Sealing
Total Page:16
File Type:pdf, Size:1020Kb
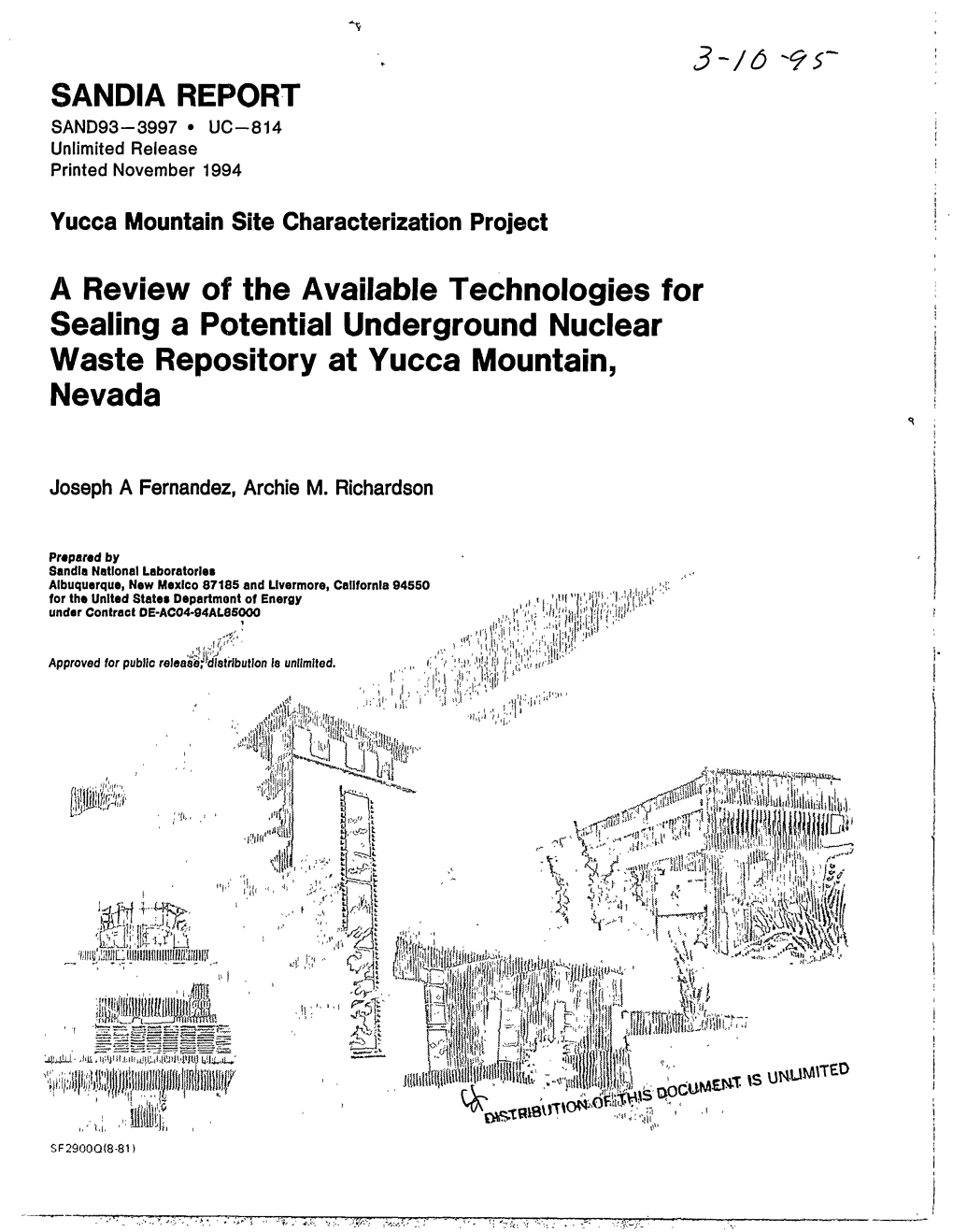
Load more
Recommended publications
-
Open Thesis-Rev3.Pdf
The Pennsylvania State University The Graduate School Department of Energy and Mineral Engineering STUDY OF UTILIZATION FACTOR AND ADVANCE RATE OF HARD ROCK TBMS A Dissertation in Energy and Mineral Engineering by Ebrahim Farrokh 2012 Ebrahim Farrokh Submitted in Partial Fulfillment of the Requirements for the Degree of Doctor of Philosophy May 2013 The dissertation of Ebrahim Farrokh was reviewed and approved* by the following: Jamal Rostami Assistant Professor of Energy and Mineral Engineering Mark S. Klima Department Head, Associate Professor of Mineral Processing and Geo-Environmental Engineering R. Larry Grayson Professor of Energy and Mineral Engineering Antonio Nieto Associate Professor of Energy and Mineral Engineering Prasenjit Basu Assistant Professor of Civil and Environmental Engineering *Signatures are on file in the Graduate School iii ABSTRACT Estimating the penetration rate (PR), utilization (U), and advance rate (AR) is a critical factor in successful selection and application of tunnel boring machines (TBM), but it has remained a challenge to most engineers and contractors. While there have been many studies on accurate prediction of penetration rate with some progress in accounting for various geological parameters, the amount of research performed on TBM utilization and advance rate is still very limited. The primary objective of this research was to develop a comprehensive database of TBM utilization and advance rate from different hard-rock tunneling projects using a TBM to develop a new model for estimation of machine utilization and advance rate through statistical analysis of available machine field performance information and a new rock mass characterization system. For this purpose, information for 300 tunnel projects, including rock properties, TBM specification, TBM operational parameters, and achieved performance were compiled in a database to seek significant correlations between these parameters. -
Course Structure & Syllabus of B Tech Mining Machinery
COURSE STRUCTURE & SYLLABUS OF B TECH MINING MACHINERY ENGINEERING (EFFECTIVE FROM 2015-16 ACADEMIC SESSION) COURSE STRUCTURE OF B TECH MINING MACHINERY ENGINEERING (EFFECTIVE FROM 2015-16 ACADEMIC SESSION) FIRST SEMESTER (GROUP-I) S No. Course No. Name of the Course L T P CP THEORY 1. APC11101 Physics 3 0 0 6 2. AMC11101 Mathematics - I 3 1 0 7 3. EEC 11101 Electrical Technology 3 1 0 7 4. HSC 11101 Value Education, Human Rights & 3 0 0 6 Legislatives procedure 5. MCC11101 Engineering Mechanics 3 1 0 7 SESSIONAL 6. GLD11301 / Earth System Science 3 0 0 6 ESD 11301 PRACTICAL & OTHERS 7. APC11201 Physics 0 0 2 2 8. EEC11201 Electrical Technology 0 0 2 2 9. MCC11201 Engineering Graphics 1 0 3 5 Total Credit Hours - - - 48 Total Contact Hours: 29 19 3 7 FIRST SEMESTER (GROUP-II) S No. Course No. Name of the Course L T P CP THEORY 1. ACC11101 Chemistry 3 0 0 6 2. AMC11101 Mathematics - I 3 1 0 7 3. CSC11101 Computer Programming 3 0 0 6 4. ECC 11101 Electronics Engineering 3 0 0 6 5. HSC 11102 English for Science & Technology 3 0 0 6 SESSIONAL 6. MSD11301 / Disaster Management 3 0 0 6 APD11301 & Energy Resources PRACTICAL & OTHERS 7. ACC11201 Chemistry 0 0 2 2 8. CSC11201 Computer Programming 0 0 2 2 9. ECC11201 Electronics Engineering 0 0 2 2 10. MCC11202 Manufacturing process 1 0 3 5 Total Credit Hours - - - 48 Total Contact Hours=29 19 1 9 1 SECOND SEMESTER (GROUP I) S No. -
Few Return to the Sunlit Lands': Lewis's Classical Underworld in the Is Lver Chair Benita Huffman Muth Macon State College
Inklings Forever Volume 8 A Collection of Essays Presented at the Joint Meeting of The Eighth Frances White Ewbank Article 17 Colloquium on C.S. Lewis & Friends and The C.S. Lewis & The Inklings Society Conference 5-31-2012 'Few Return to the Sunlit Lands': Lewis's Classical Underworld in The iS lver Chair Benita Huffman Muth Macon State College Follow this and additional works at: https://pillars.taylor.edu/inklings_forever Part of the English Language and Literature Commons, History Commons, Philosophy Commons, and the Religion Commons Recommended Citation Muth, Benita Huffman (2012) "'Few Return to the Sunlit Lands': Lewis's Classical Underworld in The iS lver Chair," Inklings Forever: Vol. 8 , Article 17. Available at: https://pillars.taylor.edu/inklings_forever/vol8/iss1/17 This Essay is brought to you for free and open access by the Center for the Study of C.S. Lewis & Friends at Pillars at Taylor University. It has been accepted for inclusion in Inklings Forever by an authorized editor of Pillars at Taylor University. For more information, please contact [email protected]. INKLINGS FOREVER, Volume VIII A Collection of Essays Presented at the Joint Meeting of The Eighth FRANCES WHITE EWBANK COLLOQUIUM ON C.S. LEWIS & FRIENDS and THE C.S. LEWIS AND THE INKLINGS SOCIETY CONFERENCE Taylor University 2012 Upland, Indiana Few Return to the Sunlit Lands: Lewis’s Classical Underworld in The Silver Chair Benita Huffman Muth Macon State College Muth, Benita Huffman. “Few Return to the Sunlit Lands: Lewis’s Classical Underworld in The Silver Chair.” Inklings Forever 8 (2012) www.taylor.edu/cslewis 1 Few Return to the Sunlit Lands: Lewis’s Classical Underworld in The Silver Chair Benita Huffman Muth Macon State College In re-reading the Narnia books as asserts his commitment to individual free an adult, classical studies professor Emily will. -
Proto-Cinematic Narrative in Nineteenth-Century British Fiction
The University of Southern Mississippi The Aquila Digital Community Dissertations Fall 12-2016 Moving Words/Motion Pictures: Proto-Cinematic Narrative In Nineteenth-Century British Fiction Kara Marie Manning University of Southern Mississippi Follow this and additional works at: https://aquila.usm.edu/dissertations Part of the Literature in English, British Isles Commons, and the Other Film and Media Studies Commons Recommended Citation Manning, Kara Marie, "Moving Words/Motion Pictures: Proto-Cinematic Narrative In Nineteenth-Century British Fiction" (2016). Dissertations. 906. https://aquila.usm.edu/dissertations/906 This Dissertation is brought to you for free and open access by The Aquila Digital Community. It has been accepted for inclusion in Dissertations by an authorized administrator of The Aquila Digital Community. For more information, please contact [email protected]. MOVING WORDS/MOTION PICTURES: PROTO-CINEMATIC NARRATIVE IN NINETEENTH-CENTURY BRITISH FICTION by Kara Marie Manning A Dissertation Submitted to the Graduate School and the Department of English at The University of Southern Mississippi in Partial Fulfillment of the Requirements for the Degree of Doctor of Philosophy Approved: ________________________________________________ Dr. Eric L.Tribunella, Committee Chair Associate Professor, English ________________________________________________ Dr. Monika Gehlawat, Committee Member Associate Professor, English ________________________________________________ Dr. Phillip Gentile, Committee Member Assistant Professor, -
Oregon Caves Domain of the Cavemen
Oregon Caves NM: Historic Resource Study OREGON CAVES Domain of the Cavemen: A Historic Resource Study of Oregon Caves National Monument DOMAIN OF THE CAVEMEN A Historic Resource Study of Oregon Caves National Monument by Stephen R. Mark Historian 2006 National Park Service Pacific West Region TABLE OF CONTENTS orca/hrs/index.htm Last Updated: 06-Mar-2007 http://www.nps.gov/history/history/online_books/orca/hrs/index.htm[10/30/2013 3:19:32 PM] Oregon Caves NM: Historic Resource Study (Table of Contents) OREGON CAVES Domain of the Cavemen: A Historic Resource Study of Oregon Caves National Monument TABLE OF CONTENTS Cover (HTML) Cover (PDF) Preface (PDF) Acknowledgments (PDF) Introduction: The Marble Halls of Oregon (PDF) 1: Locked in a Colonial Hinterland, 1851-1884 (PDF) Exploration and westward expansion Cultural collision and its consequences Social and economic transition Discovery of the Oregon Caves 2: The Closing of a Frontier, 1885-1915 (PDF) Developing a "private" show cave Into a void The advent of federal land management 3: Boosterism's Public-Private Partnership, 1816-1933 (PDF) Highways to Oregon Caves Beginnings of a recreational infrastructure Transfer to the National Park Service 4: Improving a Little Landscape Garden, 1934-1943 (PDF) New Lights, but an old script Camp Oregon Caves, NM-1 Development of Grayback Campground CCC projects at Oregon Caves Expanded concession facilities NPS master plans for Oregon Caves Other vehicles for shaping visitor experience 5: Decline from Rustic Ideal, 1944-1995 (PDF) Postwar park development -
6Th Grade READING LEVEL BOOK LIST
Required List (Choose One) Featured Novel: Title: Swindle Author: Gordan Korman Reading Level:T/40 Summary: After unscrupulous collector S. Wendell Palamino cons him out of a valuable baseball card, sixth-grader Griffin Bing puts together a band of misfits to break into Palomino's heavily guarded store and steal the card back, planning to use the money to finance his father's failing invention, the SmartPick fruit picker. Title: All Alone in the Universe Author: Lynne Rae Perkins Reading Level: S/40 Summary: When her best friend since the third grade starts acting as though Debbie doesn't exist, Debbie finds out the hard way that life can be a lonesome place. But in the end the heroine of this wryly funny coming-of-age story--a girl who lives in a house covered with stuff that is supposed to look like bricks but is just a fake brick pattern-- discovers that even the hourly tragedies of junior high school can have silver linings, just as a house covered with Insul-Brick can protect a real home. This first novel shines--fun, engrossing, bittersweet, and wonderfully unpredictable. Title: The Alphabet City Ballet Author: Erika Tamar Reading Level: N/30 Summary: Marisol has always loved to dance— to the salsa at family parties, to the boom boxes on Loisada Avenue. Then she wins a scholarship to ballet school and discovers an inspiring new world of beauty and discipline. But when violence erupts in Alphabet City, Marisol’ s dream starts to slip away. To keep dancing she must make heartbreaking choices— perhaps impossible ones. -
The Silver Chair by C
73 The Silver Chair by C. S. Lewis Overview Plot Aslan calls Eustace Scrubb and Jill Pole into Narnia to help old King Caspian find his long-lost son, Prince Rilian, who has been kidnapped by an evil enchantress. Conflict Can Jill and Eustace find and save the lost prince? (Man vs. Man, Man vs. Nature) Will the children learn to trust and obey the signs that Aslan has given them? Will they believe what Aslan says about the world, or will they trust the evidence of their senses? (Man vs. Self) Setting Experiment House, the English boarding school; the wildlands of Narnia; Underworld, the domain of the enchantress. Characters Eustace Scrubb and Jill Pole, the English children; Puddleglum, the Narnian Marshwiggle who accompanies them on their quest; Prince Rilian; the witch and her subjects, who inhabit Underworld; Aslan the Lion Theme The Nature of Faith; Appearances vs. Reality Literary Devices Simile; Irony; Foreshadowing; Motif The Silver Chair 74 Questions About Structure: Setting (1) Where does the story happen? The frame for this story is a horrid English boarding school called Experiment House. Co-educational and modern, it is a den of bullies and abusive teachers. The two protagonists, Jill and Eustace, are students trying to survive the term when they are whisked away to Narnia. The central tale is set in the outskirts of Narnia. The story ranges from the wild northern border of Narnia and its marshes, to Ettinsmoor, the country of the giants, and then through Underland. (1.c) Does the story happen in one spot or does it unfold across a wide area? The action unfolds across a wide area due to the nature of the children’s quest. -
Portland's Artisan Economy
Portland State University PDXScholar Urban Studies and Planning Faculty Nohad A. Toulan School of Urban Studies and Publications and Presentations Planning 1-1-2010 Brew to Bikes: Portland's Artisan Economy Charles H. Heying Portland State University, [email protected] Follow this and additional works at: https://pdxscholar.library.pdx.edu/usp_fac Part of the Entrepreneurial and Small Business Operations Commons, and the Urban Studies and Planning Commons Let us know how access to this document benefits ou.y Citation Details Heying, Charles H., "Brew to Bikes: Portland's Artisan Economy" (2010). Urban Studies and Planning Faculty Publications and Presentations. 52. https://pdxscholar.library.pdx.edu/usp_fac/52 This Book is brought to you for free and open access. It has been accepted for inclusion in Urban Studies and Planning Faculty Publications and Presentations by an authorized administrator of PDXScholar. Please contact us if we can make this document more accessible: [email protected]. Brew to bikes : Portland's artisan economy Published by Ooligan Press, Portland State University Charles H. Heying Portland State University Urban Studies Portland, Oregon This material is brought to you for free and open access by PDXScholar, Portland State University Library (http://archives.pdx.edu/ds/psu/9027) Commitment to Sustainability Ooligan Press is committed to becoming an academic leader in sustainable publishing practices. Using both the classroom and the business, we will investigate, promote, and utilize sustainable products, technolo- gies, and practices as they relate to the production and distribution of our books. We hope to lead and encour- age the publishing community by our example. -
Henry Thoreau’S Journal for 1837 (Æt
HDT WHAT? INDEX 1839 1839 EVENTS OF 1838 General Events of 1839 SPRING JANUARY FEBRUARY MARCH SUMMER APRIL MAY JUNE FALL JULY AUGUST SEPTEMBER WINTER OCTOBER NOVEMBER DECEMBER Following the death of Jesus Christ there was a period of readjustment that lasted for approximately one million years. –Kurt Vonnegut, THE SIRENS OF TITAN 1839 January February March Su Mo Tu We Th Fr Sa Su Mo Tu We Th Fr Sa Su Mo Tu We Th Fr Sa 1 2 3 4 5 1 2 1 2 6 7 8 9 10 11 12 3 4 5 6 7 8 9 3 4 5 6 7 8 9 13 14 15 16 17 18 19 10 11 12 13 14 15 16 10 11 12 13 14 15 16 20 21 22 23 24 25 26 17 18 19 20 21 22 23 17 18 19 20 21 22 23 27 28 29 30 31 24 25 26 27 28 24 25 26 27 28 29 30 31 April May June EVENTS OF 1840 HDT WHAT? INDEX 1839 1839 Su Mo Tu We Th Fr Sa Su Mo Tu We Th Fr Sa Su Mo Tu We Th Fr Sa 1 2 3 4 5 6 1 2 3 4 1 7 8 9 10 11 12 13 5 6 7 8 9 10 11 2 3 4 5 6 7 8 14 15 16 17 18 19 20 12 13 14 15 16 17 18 9 10 11 12 13 14 15 21 22 23 24 25 26 27 19 20 21 22 23 24 25 16 17 18 19 20 21 22 28 29 30 26 27 28 29 30 31 23 24 25 26 27 28 29 30 July August September Su Mo Tu We Th Fr Sa Su Mo Tu We Th Fr Sa Su Mo Tu We Th Fr Sa 1 2 3 4 5 6 1 2 3 1 2 3 4 5 6 7 7 8 9 10 11 12 13 4 5 6 7 8 9 10 8 9 10 11 12 13 14 14 15 16 17 18 19 20 11 12 13 14 15 16 17 15 16 17 18 19 20 21 21 22 23 24 25 26 27 18 19 20 21 22 23 24 22 23 24 25 26 27 28 28 29 30 31 25 26 27 28 29 30 31 29 30 October November December Su Mo Tu We Th Fr Sa Su Mo Tu We Th Fr Sa Su Mo Tu We Th Fr Sa 1 2 3 4 5 1 2 1 2 3 4 5 6 7 6 7 8 9 10 11 12 3 4 5 6 7 8 9 8 9 10 11 12 13 14 13 14 15 16 17 18 19 10 11 12 13 14 15 16 15 16 17 18 19 20 21 20 21 22 23 24 25 26 17 18 19 20 21 22 23 22 23 24 25 26 27 28 27 28 29 30 31 24 25 26 27 28 29 30 29 30 31 Read Henry Thoreau’s Journal for 1837 (æt. -
The Cave Book Study Guide &Workbook
STUDY GUIDE & WORKBOOK THE CAVE BOOK STUDY GUIDE & WORKBOOK ® First printing: March 2009 Copyright © 2009 by Master Books. All rights reserved. No part of this book may be used or reproduced in any manner whatsoever without written permission of the publisher, except in the case of brief quotations in articles and reviews. For information write: Master Books®, P.O. Box 726, Green Forest, AR 72638. Printed in the United States of America Please visit our website for other great titles: www.masterbooks.net For information regarding author interviews, please contact the publicity department at (870) 438-5288. CONTENTS Introduction.................................................................4 1. Humans and Caves ..............................................6 2. Caves and Mythology ..........................................9 3. Caves and Karst ................................................ 12 4. Classifying Caves ............................................... 15 5. Exploring Caves ................................................ 18 6. Studying Caves .................................................. 20 Answer Key ............................................................... 22 INTRODUCTION Text: Pages 6–7 Terms to Know and Spell karst karst aquifers Short Answer 1. What is the probable reason some of our ancestors may have entered the “underland” of cave systems? 2. The strange event near the ________________ not only split the once unified population, but scattered those with different skills and abilities. 3. How much of the world’s drinking water comes from limestone (karst) terrains? 4. How much is it estimated to be by 2025? 4 • The Cave Book STUDY GUIDE Discussion Questions 1. What role did caves play for our ancestors? 2. How did the events surrounding the Tower of Babel affect the ancient groups of people who disbursed from that area? Activity 1. Read through the account of the Tower of Babel (Genesis 11:1–9), and discuss issues that would have affected the various people groups when this event occurred. -
48641Fbea0551a56d8f4efe0cb7
cave The Earth series traces the historical significance and cultural history of natural phenomena. Written by experts who are passionate about their subject, titles in the series bring together science, art, literature, mythology, religion and popular culture, exploring and explaining the planet we inhabit in new and exciting ways. Series editor: Daniel Allen In the same series Air Peter Adey Cave Ralph Crane and Lisa Fletcher Desert Roslynn D. Haynes Earthquake Andrew Robinson Fire Stephen J. Pyne Flood John Withington Islands Stephen A. Royle Moon Edgar Williams Tsunami Richard Hamblyn Volcano James Hamilton Water Veronica Strang Waterfall Brian J. Hudson Cave Ralph Crane and Lisa Fletcher reaktion books For Joy Crane and Vasil Stojcevski Published by Reaktion Books Ltd 33 Great Sutton Street London ec1v 0dx, uk www.reaktionbooks.co.uk First published 2015 Copyright © Ralph Crane and Lisa Fletcher 2015 All rights reserved No part of this publication may be reproduced, stored in a retrieval system, or transmitted, in any form or by any means, electronic, mechanical, photocopying, recording or otherwise, without the prior permission of the publishers Printed and bound in China by 1010 Printing International Ltd A catalogue record for this book is available from the British Library isbn 978 1 78023 431 1 contents Preface 7 1 What is a Cave? 9 2 Speaking of Speleology 26 3 Troglodytes and Troglobites: Living in the Dark Zone 45 4 Cavers, Potholers and Spelunkers: Exploring Caves 66 5 Monsters and Magic: Caves in Mythology and Folklore 90 6 Visually Rendered: The Art of Caves 108 7 ‘Caverns measureless to man’: Caves in Literature 125 8 Sacred Symbols: Holy Caves 147 9 Extraordinary to Behold: Spectacular Caves 159 notable caves 189 references 195 select bibliography 207 associations and websites 209 acknowledgements 211 photo acknowledgements 213 index 215 Preface ‘It’s not what you’d expect, down there,’ he had said. -
Lilydale Quarry, Former (Kinley)
Lilydale Quarry, former (Kinley) Heritage Interpretation Strategy 4 Melba Avenue, Lilydale, Victoria April 2020 Prepared by Prepared for HBI Lilydale Pty Ltd This report is released subject to the following qualifications and conditions: • The report may only be used by named addressee for the purpose for which it was commissioned and in accordance with the corresponding conditions of engagement. • The report may only be reproduced in full. • The report shall not be considered as relieving any other party of their responsibilities, liabilities and contractual obligations • The content of this document is copyright protected. The copyright of all images, maps and diagrams remains with Lovell Chen or with the photographer/ collection as indicated. Historical sources and reference material used in the preparation of this report are acknowledged and referenced. Reasonable effort has been made to identify, contact, acknowledge and obtain permission to use material from the relevant copyright owners. You may not display, print or reproduce any image, map or diagram without the permission of the copyright holder, who should be contacted directly. Cover: ‘Bunjil's anger cave, Lilydale’ painting (cropped), 2000, by Tiriki Onus, Centre for Australian Indigenous Studies, Monash University, Melbourne (copied from, Duane Hamacher, ‘Recorded Accounts of Meteoritic Events in the Oral Traditions of Indigenous Australians’, The Journal of Astronomy in Culture, Volume 25, 2014). TABLE OF CONTENTS 1.0 SCOPE AND PURPOSE 1 1.1 Comprehensive Development Plan