Elimination of SF6 from Transmission System Equipment
Total Page:16
File Type:pdf, Size:1020Kb
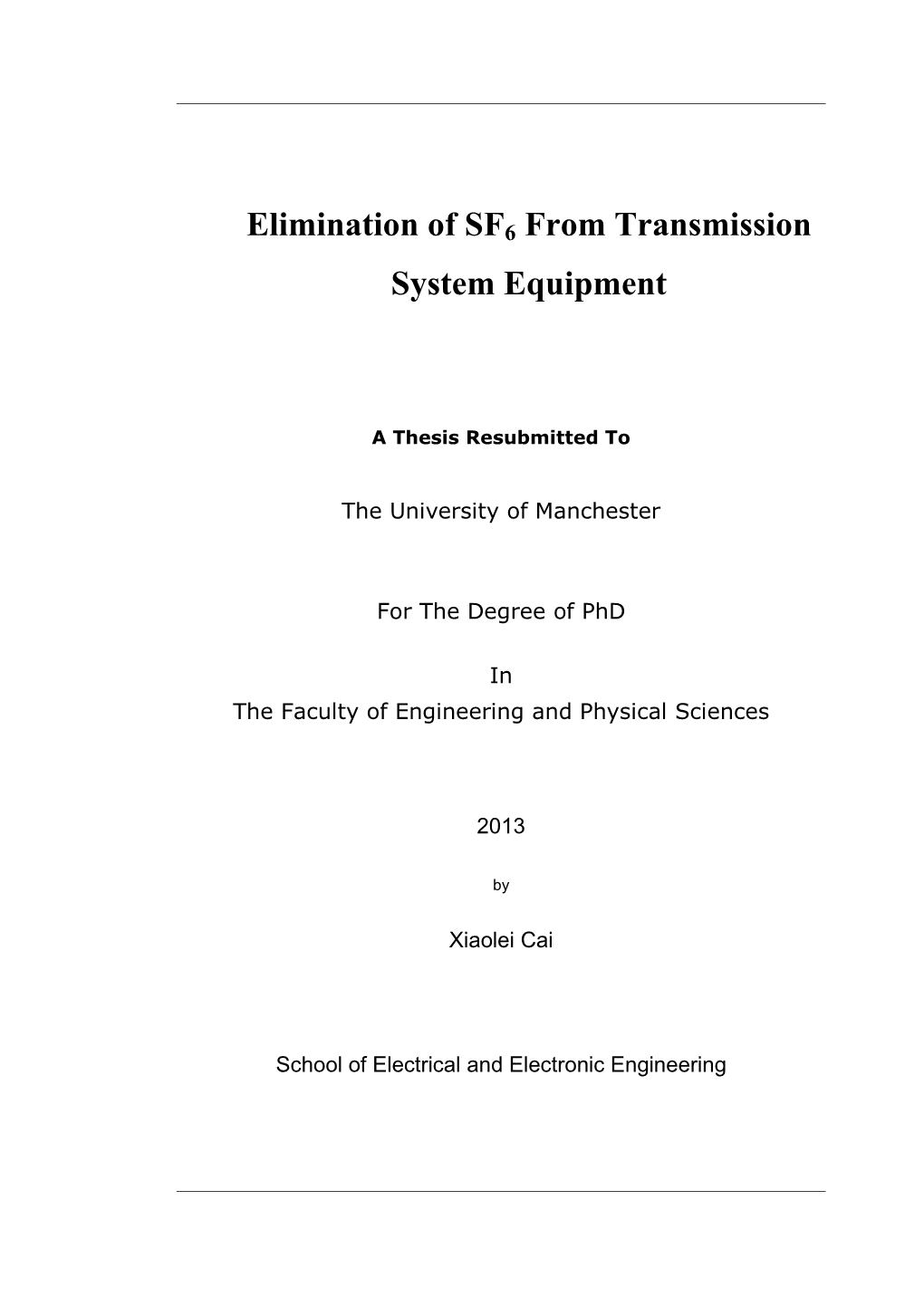
Load more
Recommended publications
-
Liquid Dielectrics, Their Classification, Properties, and Breakdown Strength
CHAPTER 6 LIQUID DIELECTRICS, THEIR CLASSIFICATION, PROPERTIES, AND BREAKDOWN STRENGTH From the point of view of molecular arrangement, a liquid can be described as “ highly compressed gas ” in which the molecules are very closely arranged. This is known as kinetic model of the liquid structure. A liquid is characterized by free movement of the constituent molecules among themselves but without the tendency to separate. However, the movement of charged particles, their microscopic streams, and interface conditions with other materials cause a distortion in the otherwise undisturbed molecular structure of the liquids. The well known terminology describ- ing the breakdown mechanisms in gaseous dielectrics — such as impact ionization, mean free path, electron drift, and so on — are, therefore, also applicable for liquid dielectrics. Liquid dielectrics are accordingly classifi ed in between the two states of matter; that is, gaseous and solid insulating materials. Wide range of application of liquid dielectircs in power apparatus also characterizes this intermediate position of liquid dielectrics. Insulating oils are used in power and instrument transformers, power cables, circuit breakers, power capacitors, and so on. Liquid dielectrics perform a number of functions simultaneously, namely: • insulation between the parts carrying voltage and the grounded container, as in transformers • impregnation of insulation provided in thin layers of paper or other materials, as in transformers, cables and capacitors, where oils or impregnating com- pounds are used • cooling action by convection in transformers and oil fi lled cables through circulation • fi lling up of the voids to form an electrically stronger integral part of a com- posite dielectric • arc extinction in circuit breakers High Voltage and Electrical Insulation Engineering, First Edition. -
“Contribution to Liquid Lens Technology”
“CONTRIBUTION TO LIQUID LENS TECHNOLOGY” Thesis submitted in partial fulfillment of the requirement for the PhD Degree issued by the Universitat Politècnica de Catalunya, in its Electronic Engineering Program Nom del doctorand Maziar Ahmadi Zeidabadi Directors: Prof. Dr. Luis Castañer Prof. Dra. Sandra Bermejo data de lectura de la tesi Mayo 2016 2 3 4 Contents Contents .............................................................................................................................. 5 1 Summary ................................................................................................................... 21 1.1 Introduction........................................................................................................ 23 1.2 Thesis challenges and outlines .......................................................................... 25 2 Liquid lens (Fundamentals and theory) ................................................................... 27 2.1 Liquid lens devices overview ............................................................................ 29 2.2 Basic principles of capillarity and wetting ........................................................ 30 2.3 Hydrophobic surfaces ........................................................................................ 32 2.3.1 Wenzel model ............................................................................................. 33 2.3.2 Cassie-Baxter model................................................................................... 34 2.4 Electrical -
Preparation of Monodisperse Microbubbles in a Capillary Embedded T-Junction Device and the Influence of Process Control Parameters on Bubble Size and Stability
Preparation of monodisperse microbubbles in a capillary embedded T-Junction device and the influence of process control parameters on bubble size and stability A thesis submitted in partial fulfilment of the requirements for the degree of Doctor of Philosophy By Maryam Parhizkar Department of Mechanical Engineering University College London Torrington Place, London WC1E 7JE U.K March, 2014 Declaration I, Maryam Parhizkar, confirm that the work presented in this thesis is my own. Where information has been derived from other sources, I confirm that this has been indicated in the thesis. ………………………………….. Maryam Parhizkar 1 Abstract The main goal for this work was to produce microbubbles for a wide range of applications with sizes ranging between 10 to 300 µm in a capillary embedded T- junction device. Initially the bubble formation process was characterized and the factors that affected the bubble size; in particular the parameters that reduce it were determined. In this work, a polydimethylsiloxane (PDMS) block (100 x 100 x 10 mm3) was used, in which the T-shaped junction was created by embedded capillaries of fixed outer diameter. The effect of the inner diameter was investigated by varying all the inlet and outlet capillaries’ inner diameter at different stages. In addition, the effect of changes in the continuous phase viscosity and flow rate (Ql) as well as the gas pressure (Pg) on the resulting bubble size was studied. Aqueous glycerol solutions were chosen for the liquid phase, as they are widely used in experimental studies of flow phenomena and provide a simple method of varying properties through dilution. -
Studies on Breakdown Voltages of Liquid Dielectrics
ISSN (Online) 2278-1021 IJARCCE ISSN (Print) 2319-5940 International Journal of Advanced Research in Computer and Communication Engineering ISO 3297:2007 Certified Vol. 7, Issue 4, April 2018 Studies on Breakdown Voltages of Liquid Dielectrics S Vasudevamurthy1, Girisha2, Shubham Shah3, Varun kumar B L4 , Uday N5 1 Associated Professor, Electrical and Electronics Engineering, Dr.AIT, Bengaluru, India 2,3,4,5 B.E in Electrical and Electronics Engineering, Dr AIT, Bengaluru, India Abstract: The objective of proposed work is to study the dielectric behavior of the natural ester based oil and it is compared with the transformer oil to find their suitability for use as liquid dielectric. Mineral oil contains a lot of toxic inhibitors to improve their properties. Due to this it is necessary to find a new source and that will be substitute for the mineral oil. For use as insulating liquids in power transformers, Natural ester based oils are gaining worldwide attention as biodegradable alternatives and competitors to the mineral based oils. Keywords: Liquid insulation, breakdown voltage, moisture content. INTRODUCTION Transformer plays a vital role in the field of transmission and distribution of electrical power. It is used to transforms electrical energy from one circuit to another circuit without change in frequency. Power transformers are used in transmission network of higher voltages for step-up and step-down .PT generally rated above 200MVA.A distribution transformer provides the final voltages transformation in the electrical power distribution system. it is used to stepping down the voltages as per the power requirement level of the customer. Transformer encounters lightning and other switching surges, hence it requires proper insulation. -
WO 2017/155686 Al 14 September 2017 (14.09.2017) P O P C T
(12) INTERNATIONAL APPLICATION PUBLISHED UNDER THE PATENT COOPERATION TREATY (PCT) (19) World Intellectual Property Organization International Bureau (10) International Publication Number (43) International Publication Date WO 2017/155686 Al 14 September 2017 (14.09.2017) P O P C T (51) International Patent Classification: (81) Designated States (unless otherwise indicated, for every C07D 265/30 (2006.01) C07D 223/04 (2006.01) kind of national protection available): AE, AG, AL, AM, C07D 211/08 (2006.01) C07C 217/26 (2006.01) AO, AT, AU, AZ, BA, BB, BG, BH, BN, BR, BW, BY, C07D 241/04 (2006.01) BZ, CA, CH, CL, CN, CO, CR, CU, CZ, DE, DJ, DK, DM, DO, DZ, EC, EE, EG, ES, FI, GB, GD, GE, GH, GM, GT, (21) International Application Number: HN, HR, HU, ID, IL, IN, IR, IS, JP, KE, KG, KH, KN, PCT/US20 17/0 18780 KP, KR, KW, KZ, LA, LC, LK, LR, LS, LU, LY, MA, (22) International Filing Date: MD, ME, MG, MK, MN, MW, MX, MY, MZ, NA, NG, 22 February 2017 (22.02.2017) NI, NO, NZ, OM, PA, PE, PG, PH, PL, PT, QA, RO, RS, RU, RW, SA, SC, SD, SE, SG, SK, SL, SM, ST, SV, SY, (25) Filing Language: English TH, TJ, TM, TN, TR, TT, TZ, UA, UG, US, UZ, VC, VN, (26) Publication Language: English ZA, ZM, ZW. (30) Priority Data: (84) Designated States (unless otherwise indicated, for every 62/306,947 11 March 2016 ( 11.03.2016) US kind of regional protection available): ARIPO (BW, GH, GM, KE, LR, LS, MW, MZ, NA, RW, SD, SL, ST, SZ, (71) Applicant: 3M INNOVATIVE PROPERTIES COM¬ TZ, UG, ZM, ZW), Eurasian (AM, AZ, BY, KG, KZ, RU, PANY [US/US]; 3M Center, Post Office Box 33427, Saint TJ, TM), European (AL, AT, BE, BG, CH, CY, CZ, DE, Paul, Minnesota 55 133-3427 (US). -
Development of a Biodegradable Electro-Insulating Liquid and Its Subsequent Modification by Nanoparticles
energies Article Development of a Biodegradable Electro-Insulating Liquid and Its Subsequent Modification by Nanoparticles Vaclav Mentlik, Pavel Trnka * ID , Jaroslav Hornak ID and Pavel Totzauer Department of Technologies and Measurement, Faculty of Electrical Engineering, University of West Bohemia, 30614 Pilsen, Czech Republic; [email protected] (V.M.); [email protected] (J.H.); [email protected] (P.T.) * Correspondence: [email protected]; Tel.: +420-377-634-518 Received: 23 January 2018; Accepted: 23 February 2018; Published: 27 February 2018 Abstract: The paper is focused on the possibility of replacing petroleum-based oils used as electro-insulating fluids in high voltage machinery. Based on ten years of study the candidate base oil for the central European region is rapeseed (Brassica napus) oil. Numerous studies on the elementary properties of pure natural esters have been published. An advantage of natural ester use is its easy biodegradability, tested according to OECD–301D (Organisation for Economic Co-operation and Development) standard, and compliance with sustainable development visions. A rapeseed oil base has been chosen for its better resistance to degradation in electric fields and its higher oxidation stability. The overall ester properties are not fully competitive with petroleum-based oils and therefore have to be improved. Percolation treatment and oxidation inhibition by a phenolic-type inhibitor is proposed and the resulting final properties are discussed. These resulting fluid properties are further improved using titanium dioxide (TiO2) nanoparticles with a silica surface treatment. This fluid has properties suitable for use in sealed distribution transformers with the advantage of a lower price in comparison with other currently used biodegradable fluids. -
Umi-Umd-2588.Pdf
ABSTRACT Title of Dissertation: EXPERIMENTAL AND COMPUTATIONAL INVESTIGATION OF PLANAR ION DRAG MICROPUMP GEOMETRICAL DESIGN PARAMETERS Vytenis Benetis, Doctor of Philosophy, 2005 Dissertation directed by: Professor Michael Ohadi Department of Mechanical Engineering To deal with increasing heat fluxes in electronic devices and sensors, innovative new thermal management systems are needed. Proper cooling is essential to increasing reliability, operating speeds, and signal-to-noise ratio. This can be achieved only with precise spatial and temporal temperature control. In addition, miniaturization of electric circuits in sensors and detectors limits the size of the associated cooling systems, thereby posing an added challenge. An innovative answer to the problem is to employ an electrohydrodynamic (EHD) pumping mechanism to remove heat from precise locations in a strictly controlled fashion. This can potentially be achieved by micro-cooling loops with micro-EHD pumps. Such pumps are easily manufactured using conventional microfabrication batch technologies. The present work investigates ion drag pumping for applications in reliable and cost effective EHD micropumps for spot cooling. The study examines the development, fabrication, and operation of micropumps under static and dynamic conditions. An optimization study is performed using the experimental data from the micropump prototype tests, and a numerical model is built using finite element methods. Many factors were involved in the optimization of the micropump design. A thorough analysis was performed of the major performance-controlling variables: electrode and inter-electrode pair spacing, electrode thickness and shape, and flow channel height. Electrode spacing was varied from 10 µm to 200 µm and channel heights from 50 µm to 500 µm. -
Understanding Water in Transformer Systems
Chemist’s Perspective nderstanding Water U in Transformer Systems The Relationship Between Relative Saturation and Parts per Million (ppm) ater content in transformer oil in parts per million (ppm) is a familiar concept to most in our industry, and limits of 30 to 35 W ppm are generally referenced. However, these simple concen- by Lance Lewand tration limits have limited value in diagnosing the condition of trans- Doble Engineering former systems and, thus, the concept of relative saturation (RS) of water in transformer oil has been re-introduced over the past 15 years. The concept of relative saturation of water in transformer oil is not a new one and was originally championed by Frank Doble as early as as the water content in the paper the mid 1940s.Thus, this article discusses and details the relationship doubles so does the aging rate of the paper. The deterioration of the between RS and ppm. paper insulation results from the It is well known that moisture continues to be a major cause of prob- weakening of the hydrogen bonds lems in transformers and a limitation to their operation. Particularly prob- of the molecular chains of the pa- lematic is excessive moisture in transformer systems, as it affects both per fibers. For these reasons it is solid and liquid insulation with the water in each being interrelated. Water important to have a means of as- affects the dielectric breakdown strength of the insulation, the tempera- sessing the moisture content of ture at which water vapor bubbles are formed, and the aging rate of the transformer systems and to main- insulating materials. -
United States Patent [191 [11] Patent Number: 4,710,707 Knowles Et Al
United States Patent [191 [11] Patent Number: 4,710,707 Knowles et al. [45] Date of Patent: Dec. 1, 1987 [54] HIGH VOLTAGE ELECTRONIC Primary Examiner-Reinhard J. Eisenzopf COMPONENT TEST APPARATUS Assistant Examiner-W. Burns Attorney, Agent, or Firm-Cornelius J. O’Connor; [75] Inventors: Terence J. Knowles, Lincolnshire; Thomas Hill Francis M. Ray, Glenview; Charles E. Shewey, Mundelein, all of I11. [57] ABSTRACT [73] Assignee: Zenith Electronics Corporation, A high voltage electronic component test apparatus Glenview, Ill. includes a test chamber containing a pair of electrodes [21] Appl. No.: 692,583 across which a high voltage is applied and between which a component is placed in circuit by means of a [22] Filed: Jan, 16, 1985 movable component gripper assembly for the testing thereof. Voltage generating and electrical measurement [51] Int. C1.4 . .. G01R 19/15 [52] U S Cl .................... .. 324/158 F; 324/158 R apparatus is coupled to the electrodes for applying a [58] Fina or Search ..................... .. 200/149 A, 149 R; high voltage thereacross and for measuring the result 324/158 R, 158 P, 158 F, 73 PC; 336/84 R, 84 ing current within the electronic component. From the C component testing, the remotely operated gripper as [56] References Cited sembly then removes the tested component from the test chamber and introduces another component for U.S. PATENT DOCUMENTS testing therein. A closed, circulating liquid-vapor sys 611,719 10/1898 Tesla ............................. .. 200/149 R tem coupled to the test chamber introduces an electri 3,268,698 8/1966 Bober et al. .. .. 200/149 A cally inert vapor, such as Freon or a ?uorinated hydro 3,715,662 2/1973 Richelmann ... -
Dynamics of a Liquid Dielectric Attracted by a Cylindrical Capacitor
Dynamics of a liquid dielectric attracted by a cylindrical capacitor Rafael Nardi∗ and Nivaldo A. Lemos†1 1Departamento de F´ısica, Universidade Federal Fluminense, Av. Litorˆanea s/n, Boa Viagem CEP 24210-340, Niter´oi - RJ, Brazil. (Dated: February 2, 2008) The dynamics of a liquid dielectric attracted by a vertical cylindrical capacitor is studied. Contrary to what might be expected from the standard calculation of the force exerted by the capacitor, the motion of the dielectric is different depending on whether the charge or the voltage of the capacitor is held constant. The problem turns out to be an unconventional example of dynamics of a system with variable mass, whose velocity can, in certain cir- cumstances, suffer abrupt changes. Under the hypothesis that the voltage remains constant the motion is described in qualitative and quantitative details, and a very brief qualitative discussion is made of the constant charge case. PACS numbers: 41.20.Cv, 45.20.D-, 45.20.da Keywords: cylindrical capacitor, force on a dielectric, variable-mass system I. INTRODUCTION Electric forces on insulating bodies are notoriously difficult to calculate [1]. Only in very special instances can the calculation be performed by elementary means. The simplest case, treated in every undergraduate textbook on electricity and magnetism, is that of a dielectric slab attracted by a parallel-plate capacitor. Nearly as simple is the determination of the force of attraction on a liquid dielectric by a vertical cylindrical capacitor. It is remarkable that, under appropriate conditions, in both cases conservation of energy alone leads to a simple expression for the force with no need to know the complicated fringing field responsible for the attraction. -
Studies of Different Types of Insulating Oils and Their Mixtures As An
Received: 31 July 2018 Studies of different types of Revised: 1 December 2018 Accepted: insulating oils and their 21 January 2019 Cite as: Jilani Rouabeh, mixtures as an alternative to Lotfi M’barki, Amor Hammami, Ibrahim Jallouli, mineral oil for cooling power Ameni Driss. Studies of different types of insulating oils and their mixtures as an transformers alternative to mineral oil for cooling power transformers. Heliyon 5 (2019) e01159. doi: 10.1016/j.heliyon.2019. e01159 Jilani Rouabeh a,∗, Lotfi M’barki b,∗∗, Amor Hammami c, Ibrahim Jallouli a, Ameni Driss d a Research Laboratory RL 18ES19, Faculty of Sciences Monastir, Tunisia b Electric Transport Base of Gafsa e Tunisia, BTEGF e STEG, Tunisia c Research Unit for High Frequency Electronic Circuits and Systems, Faculty of Science, University of El Manar, Tunis, Tunisia d DFT of Faculty of Sciences Gafsa, Tunisia ∗ Corresponding author. ∗∗ Corresponding author. E-mail addresses: [email protected] (J. Rouabeh), [email protected], [email protected] (L. M’barki). Abstract Because of their availability and low cost, mineral oils have been widely used for a long time in power transformers to allow their insulation and cooling. However, their low fire safety and low biodegradability potential have made it necessary to look for other insulating liquids as an alternative to this mineral oil used in high voltage electrical equipment. This work presents an experimental study to compare between the physicochemical characteristics of mineral oil, olive oil, sunflower oil and different oil mixtures. In order to determine mainly the breakdown voltage and the electrical field intensity of electro-convection, oils insulating should be mixed in precise amounts. -
Electrical Breakdown in Polar Liquids
Old Dominion University ODU Digital Commons Electrical & Computer Engineering Theses & Dissertations Electrical & Computer Engineering Winter 2004 Electrical Breakdown in Polar Liquids Shu Xiao Old Dominion University Follow this and additional works at: https://digitalcommons.odu.edu/ece_etds Part of the Electrical and Computer Engineering Commons Recommended Citation Xiao, Shu. "Electrical Breakdown in Polar Liquids" (2004). Doctor of Philosophy (PhD), Dissertation, Electrical & Computer Engineering, Old Dominion University, DOI: 10.25777/vm33-5163 https://digitalcommons.odu.edu/ece_etds/147 This Dissertation is brought to you for free and open access by the Electrical & Computer Engineering at ODU Digital Commons. It has been accepted for inclusion in Electrical & Computer Engineering Theses & Dissertations by an authorized administrator of ODU Digital Commons. For more information, please contact [email protected]. Electrical Breakdown in Polar Liquids by Shu Xiao B.S. July 1996, Gannan Teacher College M.S. August 1999, University of Electronic Science and Technology of China A Dissertation Submitted to the Faculty of Old Dominion University in Partial Fulfillment of the Requirement for the Degree of DOCTOR OF PHILOSOPHY ELECTRICAL ENGINEERING OLD DOMINION UNIVERSITY December 2004 Approved bw Karl H. Schoenldach (Director) Ravindra P. Joshi (Member) Moimir Laroussi (Member) Reproduced with permission of the copyright owner. Further reproduction prohibited without permission. ABSTRACT ELECTRICAL BREAKDOWN IN POLAR LIQUIDS Shu Xiao Old Dominion University, 2004 Director: Dr. Karl H. Schoenbach Hydrodynamic processes following the electrical breakdown in polar liquids, mainly water and propylene carbonate, are studied with electrical pulse- probe systems and optical diagnostics including shadowgraphy and Schlieren techniques. The dielectric strength of water in a repetitively pulsed power system is found to be 750 kV/cm and 650 kV/cm for pulses of 200 nanosecond and 8 microsecond duration, respectively.