Electrical Breakdown in Polar Liquids
Total Page:16
File Type:pdf, Size:1020Kb
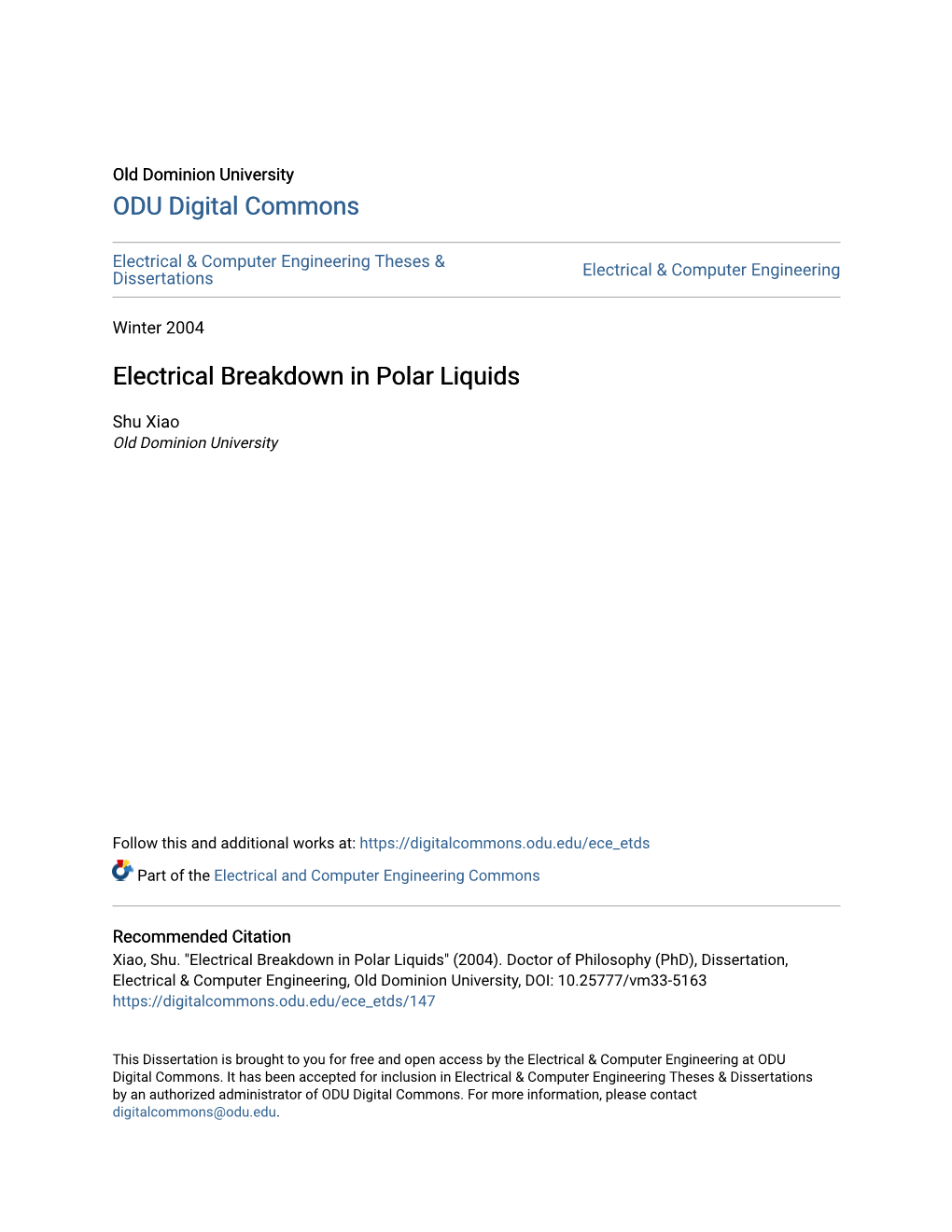
Load more
Recommended publications
-
Methodology for Analysis of Electrical Breakdown in Micrometer Gaps In
Methodology for Analysis of Electrical Breakdown In Micrometer gaps in Tip-To-Plane Configuration Kemas Tofani, Jean-Pascal Cambronne, Sorin Dinculescu, Ngapuli Sinisuka, Kremena Makasheva To cite this version: Kemas Tofani, Jean-Pascal Cambronne, Sorin Dinculescu, Ngapuli Sinisuka, Kremena Makasheva. Methodology for Analysis of Electrical Breakdown In Micrometer gaps in Tip-To-Plane Configuration. 2018 IEEE 13th Nanotechnology Materials and Devices Conference (NMDC), Oct 2018, Portland, United States. pp.1-4, 10.1109/NMDC.2018.8605855. hal-02324370 HAL Id: hal-02324370 https://hal.archives-ouvertes.fr/hal-02324370 Submitted on 1 Nov 2019 HAL is a multi-disciplinary open access L’archive ouverte pluridisciplinaire HAL, est archive for the deposit and dissemination of sci- destinée au dépôt et à la diffusion de documents entific research documents, whether they are pub- scientifiques de niveau recherche, publiés ou non, lished or not. The documents may come from émanant des établissements d’enseignement et de teaching and research institutions in France or recherche français ou étrangers, des laboratoires abroad, or from public or private research centers. publics ou privés. Methodology for analysis of electrical breakdown in micrometer gaps in tip-to-plane configuration Kemas M Tofani LAPLACE, Université de Toulouse, Jean-Pascal Cambronne Sorin Dinculescu CNRS LAPLACE, Université de Toulouse, LAPLACE, Université de Toulouse, Toulouse, France CNRS CNRS Bandung Institute of Technology Toulouse, France Toulouse, France Bandung, Indonesia [email protected] [email protected] PT. PLN Jakarta, Indonesia Kremena Makasheva [email protected] LAPLACE, Université de Toulouse, CNRS Ngapuli I. Sinisuka Toulouse, France Bandung Institute of Technology [email protected] Bandung, Indonesia [email protected] Abstract—Better understanding of the electrical behavior of electron emission process by ions bombardment on the miniaturized electrical devices is largely supported by the need cathode. -
The Pennsylvania State University
The Pennsylvania State University The Graduate School Department of Materials Science and Engineering TEMPERATURE DEPENDENCE OF DIELECTRIC BREAKDOWN IN POLYMERS A Thesis in Materials Science and Engineering by Cheolhong Min © 2008 Cheolhong Min Submitted in Partial Fulfillment of the Requirements for the Degree of Master of Science August 2008 ii The thesis of Cheolhong Min was reviewed and approved* by the following: Thomas R. Shrout Professor of Materials Science Thesis Co-Advisor Michael T. Lanagan Associate Professor of Engineering Science and Mechanics Thesis Co-Advisor Shujun Zhang Research Associate and Assistant Professor of Materials Science and Engineering Joan Redwing Professor of Materials Science and Engineering Chair, Intercollege Graduate Degree Program in Materials Science and Engineering *Signatures are on file in the Graduate School iii ABSTRACT Capacitors possess high-power densities and have the ability to deliver energy with short discharge times, which are in the micro-second to nano-second range. Both energy and power density are related to the dielectric materials used in the capacitor. One of the main challenges for capacitors is achieving high energy density as determined by the relative permittivity and dielectric breakdown strength of a material. Polymers are some of the most important dielectric materials for high-power capacitors because polymer films show high breakdown strength. A general trend in polymers is that the breakdown strength increases with decreasing temperature. An understanding of the temperature dependence relationships among electrical properties, polymer chemistry, and crystalline structure may lead to improved energy storage for polymer-based capacitors—this is the basis of the thesis. Various polymers including polypropylene (PP), polyimide (PI), polymethyl methacrylate (PMMA), poly(vinylidene fluoride-trifluoroethylene- chlorotrifluoroethylene) terpolymer (p(VDF-TrFE-CTFE)) were investigated in this study. -
Liquid Dielectrics, Their Classification, Properties, and Breakdown Strength
CHAPTER 6 LIQUID DIELECTRICS, THEIR CLASSIFICATION, PROPERTIES, AND BREAKDOWN STRENGTH From the point of view of molecular arrangement, a liquid can be described as “ highly compressed gas ” in which the molecules are very closely arranged. This is known as kinetic model of the liquid structure. A liquid is characterized by free movement of the constituent molecules among themselves but without the tendency to separate. However, the movement of charged particles, their microscopic streams, and interface conditions with other materials cause a distortion in the otherwise undisturbed molecular structure of the liquids. The well known terminology describ- ing the breakdown mechanisms in gaseous dielectrics — such as impact ionization, mean free path, electron drift, and so on — are, therefore, also applicable for liquid dielectrics. Liquid dielectrics are accordingly classifi ed in between the two states of matter; that is, gaseous and solid insulating materials. Wide range of application of liquid dielectircs in power apparatus also characterizes this intermediate position of liquid dielectrics. Insulating oils are used in power and instrument transformers, power cables, circuit breakers, power capacitors, and so on. Liquid dielectrics perform a number of functions simultaneously, namely: • insulation between the parts carrying voltage and the grounded container, as in transformers • impregnation of insulation provided in thin layers of paper or other materials, as in transformers, cables and capacitors, where oils or impregnating com- pounds are used • cooling action by convection in transformers and oil fi lled cables through circulation • fi lling up of the voids to form an electrically stronger integral part of a com- posite dielectric • arc extinction in circuit breakers High Voltage and Electrical Insulation Engineering, First Edition. -
“Contribution to Liquid Lens Technology”
“CONTRIBUTION TO LIQUID LENS TECHNOLOGY” Thesis submitted in partial fulfillment of the requirement for the PhD Degree issued by the Universitat Politècnica de Catalunya, in its Electronic Engineering Program Nom del doctorand Maziar Ahmadi Zeidabadi Directors: Prof. Dr. Luis Castañer Prof. Dra. Sandra Bermejo data de lectura de la tesi Mayo 2016 2 3 4 Contents Contents .............................................................................................................................. 5 1 Summary ................................................................................................................... 21 1.1 Introduction........................................................................................................ 23 1.2 Thesis challenges and outlines .......................................................................... 25 2 Liquid lens (Fundamentals and theory) ................................................................... 27 2.1 Liquid lens devices overview ............................................................................ 29 2.2 Basic principles of capillarity and wetting ........................................................ 30 2.3 Hydrophobic surfaces ........................................................................................ 32 2.3.1 Wenzel model ............................................................................................. 33 2.3.2 Cassie-Baxter model................................................................................... 34 2.4 Electrical -
Download Technical Paper
TECHNICAL PAPER Thermal and Electrical Breakdown Versus Reliability of Ta2O5 under Both – Bipolar Biasing Conditions P. Vašina, T. Zedníček, Z. Sita AVX Czech Republic, s.r.o., Dvorakova 328, 563 01 Lanskroun, Czech Republic J. Sikula and J. Pavelka CNRL TU Brno, Technicka 8, 602 00 Brno, Czech Republic Abstract: Our investigation of breakdown is mainly oriented to find a basic parameters describing the phenomena as well as its impact on reliability and quality of the final product that is “GOOD” tantalum capacitor. Basically, breakdown can be produced by a number of successive processes: thermal breakdown because of increasing conductance by Joule heating, avalanche and field emission break, an electromechanical collapse due to the attractive forces between electrodes electrochemical deterioration, dendrite formation and so on. Breakdown causes destruction in the insulator and across the electrodes mainly by melting and evaporation, sometimes followed by ignition. An identification of breakdown nature can be achieved from VA characteristics. Therefore, we have investigated the operating parameters both in the normal mode, Ta is a positive electrode, as well as in the reverse mode with Ta as a negative one. In the reverse mode we have reported that the thermal breakdown is initiated by an increase of the electrical conductance by Joule heating. Consequently followed in a feedback cycle consisting of temperature - conductivity - current - Joule heat - temperature. In normal mode an electrical breakdown can be stimulated by an increase of the electrical conductance in a channel by an electrical pulse and stored charge leads to the sample destruction. Both of these breakdowns have got a stochastic behaviour and could be hardly localized in advance. -
Capacitive Power Transfer Through Rotational and Sliding Bearings
CAPACITIVE POWER TRANSFER THROUGH ROTATIONAL AND SLIDING BEARINGS by Skyler S. Hagen A thesis submitted in partial fulfillment of the requirements for the degree of: Master of Science (Electrical Engineering) at the UNIVERSITY OF WISCONSIN – MADISON 2016 i Abstract Throughout the history of electrification, applications have existed for the transmission of electrical energy from stationary sources to moving loads. Electrical equipment which is expected to move along tracks, or in cyclical, pivoting, or rotational patterns of motion often requires externally-supplied electrical power to operate. Various techniques have been used with success in the past such as brushes with sliding contacts [1], cable connections (when practical), and various inductive and capacitive contactless power transfer strategies [2],[3],[4],[5]; however, each has its own limitations in longevity and/or complexity. Applications for power transfer to moving loads proliferate in the automotive and traction industries, as well as automation and manufacturing. Both of these categories have strict requirements on reliability. Failure in operation can be hazardous to human life and property in the case of transportation and heavy equipment traction. In the case of manufacturing, the reliability requirement is justified by the large opportunity cost incurred by machine down time. The following is a proposition for a technology which is well suited for many key modern applications. Using the nanofarad-scale capacitance already present in a variety of rotational and linear journal bearings, along with a simple soft-switching high frequency power converter circuit, power levels in the 102-103 watt range have successfully been transferred capacitively from stationary power sources to moving loads. -
Preparation of Monodisperse Microbubbles in a Capillary Embedded T-Junction Device and the Influence of Process Control Parameters on Bubble Size and Stability
Preparation of monodisperse microbubbles in a capillary embedded T-Junction device and the influence of process control parameters on bubble size and stability A thesis submitted in partial fulfilment of the requirements for the degree of Doctor of Philosophy By Maryam Parhizkar Department of Mechanical Engineering University College London Torrington Place, London WC1E 7JE U.K March, 2014 Declaration I, Maryam Parhizkar, confirm that the work presented in this thesis is my own. Where information has been derived from other sources, I confirm that this has been indicated in the thesis. ………………………………….. Maryam Parhizkar 1 Abstract The main goal for this work was to produce microbubbles for a wide range of applications with sizes ranging between 10 to 300 µm in a capillary embedded T- junction device. Initially the bubble formation process was characterized and the factors that affected the bubble size; in particular the parameters that reduce it were determined. In this work, a polydimethylsiloxane (PDMS) block (100 x 100 x 10 mm3) was used, in which the T-shaped junction was created by embedded capillaries of fixed outer diameter. The effect of the inner diameter was investigated by varying all the inlet and outlet capillaries’ inner diameter at different stages. In addition, the effect of changes in the continuous phase viscosity and flow rate (Ql) as well as the gas pressure (Pg) on the resulting bubble size was studied. Aqueous glycerol solutions were chosen for the liquid phase, as they are widely used in experimental studies of flow phenomena and provide a simple method of varying properties through dilution. -
Electrical Breakdown in Vacuum 1
ELECTRICAL B RE AKDOWN IN VACUUM G.P. BEUKEMA Stellingen behorende bij het prdefschrift ELECTRICAL BREAKDOWN IN VACUUM 1. De door Coolen en Van Schaik opgemeten profielen van de D2~absorptielijn van z3Na in neon worden bepaald door een combinatie van de overgangswaar- schijnlijkheden tussen de niveaus en van het laservermogen. Zij hadden een uitspraak kunnen doen over de invloed van beide effekten als zij de profielen niet alleen bij verschillende laservermogens hadden opgemeten, maar ook bij verschillende dichtheden van het neongas. F.C.M. Coolen en N. van Schaik, Physica 93 C, (1978) 261 - 6. 2. De uitspraak, gedaan in "Structure of Physics" door G.R. Noakes, dat inter- ferentie van fotonen bij de proef van Young plaatsvindt nadat deze de twee spleten gepasseerd zijn, of dat een bepaald foton geen wisselwerking heeft met elk van de spleten, is onjuist. • G.R. Noakes, Structure of Physics, Mac Millan (1977), blz. 468 en 502. 3. Voor het waarnemen van het ontstaan en de groei van interne disrupties in Tokamak plasma's verdienen cyclotron-stralingsmetingen de voorkeur boven röntgen-metingen. 4. De door Knudson en Nimrod voorgestelde exacte vergelijking voor de bereke- ning van titratiecurven voor twee-basische zouten is niet exact. G.E. Knudson en D. Nimrod, J. Chem. Educ. _54_ (1977) 351. 5. Plasma's kunnen de 5 aggregatietoestand van de materie genoemd worden, niet de 4 , zoals te doen gebruikelijk is. 6. De term "desorption cross section", zoals ingevoerd door Taglauer et al. kan aanleiding geven tot misverstand. E. Taglauer, U. Beitat, G. Marin en W. Heiland, J. -
9705: Measuring Electrical Breakdown of a Dielectric-Filled
ZYVEX APPLICATION NOTE 9705 Measuring Electrical Breakdown of a Dielectric-Filled Trench Used for Electrical Isolation of Semiconductor Devices By Rishi Gupta and Phil Foster, Zyvex Corporation Introduction Semiconductor devices employ insulating dielectric materials contribute to breakdown include occluded particles, surface for electrical isolation between active elements and layers that and material contamination, and water vapor. Each can are susceptible to electrical breakdown. The breakdown voltage influence breakdown; actions must be taken to eliminate is the level at which the insulating dielectric begins to allow their contribution to breakdown voltage measurements. charge flow. Unlike conducting materials, this charge flow Humidity, for example, reduces the resistance of most tends to be non-linear. That means that below a threshold dielectrics, thus increasing the return current (the current voltage no charge will flow, and at or above that voltage a that opposes a charge build-up).3 Contamination can rush of charge will flow. This rush is termed “avalanche contribute to leakage currents and charge mobility across breakdown,” which is a runaway process resulting in a current isolation areas. Occluded particles such as alkalis or halides spike. Once the charge begins to flow, the dielectric material can act to increase the breakdown strength.2 properties become unpredictable. To properly characterize a given film, breakdown voltages must be repeated over different The S100 Nanomanipulation System (Figure 1) can function samples. as a nano- and microprobe and is an ideal tool for dielectric breakdown voltage measurements. When operated inside a Several mechanisms give rise to electron avalanche, one of scanning electron microscope (SEM), the vacuum environ- which is by impact ionization.1 Impact ionization occurs ment minimizes moisture. -
The Prevention of Electrical Breakdown and Electrostatic Voltage Problems in the Space Shuttle and Its Paylaods
1980022937 THE PREVENTION OF ELECTRICAL BREAKDOWN AND ELECTROSTATIC VOLTAGE PROBLEMS IN THE SPACE SHUTTLE AND ITS PAYLAODS PAR; I - THEORY AND PHENOMENA PART II - DESIGN GUIDES AND OPERATIONAL CONSIDERATIONS ABSTRACT A two volume manual was prepared that will hopefully prevent workers on the Space Shuttle from having the same sort of problems with electrical dlscharg_ phenomena that otheres in the space program have had. The manual contains an introduction to the theory of Y corona discharge and electrostatic phenome-,a. The theory is mainly qualitative so that workers in the field should not have to go outside this manual for an understanding of the relevant phenomena. Some of the problems that may occur vith the Space Shuttle in regards to electrical discharge are discussed in the final sections. (NA3A-T_I-8||37) l'llEi'z_gVZNIlUN 0_. NSd-31_43 EL,':CT_iCAL BEEAKDOWN A.r_DE_EC'[_OSrATIC VOLTAGE i_ROBLB15 xN TdE 5_ACI_ 5:IUTTLE ANO IF:_ PA/LOADS. PAEI' I: THEuhY AND PtlENOdENA O[_cla_ Final l{eport (NASA) 110 t) HC AOO/_F A01 G J/16 30997 ? 1980022937-002 THE PREVENTION OF ELECTRICAL BREAKDOWN AND ELECTROSTATIC VOLTAGE PROBLEMS IN THE SPACE SHUTTLE AND ITS PAYLOADS SYNOPSIS PART I - THEORY AND PHENOMENA 1.0 Introduction. Throughout the aerospace program high potentials at low gas pressures have caused myriad problems. Many of our scientific satellites have been disabled partially or completely due to electrical breakdown. The genesis of this problem, however, did not occur within the space program. In fact, electrical breakdown of high voltage supplies was a problem in high altitude aircraft during World War II. -
Electrical Breakdown from Macro to Micro/Nano Scales: a Tutorial and a Review of the State of The
Plasma Res. Express 2 (2020) 013001 https://doi.org/10.1088/2516-1067/ab6c84 TUTORIAL Electrical breakdown from macro to micro/nano scales: a tutorial RECEIVED 31 October 2019 and a review of the state of the art REVISED 23 December 2019 1,2 2 1,2 3 ACCEPTED FOR PUBLICATION Yangyang Fu , Peng Zhang , John P Verboncoeur and Xinxin Wang 16 January 2020 1 Department of Computational Mathematics, Science and Engineering, Michigan State University, East Lansing, Michigan 48824, United PUBLISHED States of America 7 February 2020 2 Department of Electrical and Computer Engineering, Michigan State University, East Lansing, Michigan 48824, United States of America 3 Department of Electrical Engineering, Tsinghua University, Beijing 10084, People’s Republic of China E-mail: [email protected] Keywords: electrical breakdown, Paschen’s law, secondary electron emission, thermionic emission, field emission, microdischarge, Townsend theory Abstract Fundamental processes for electric breakdown, i.e., electrode emission and bulk ionization, as well as the resultant Paschen’s law, are reviewed under various conditions. The effect of the ramping rate of applied voltage on breakdown is first introduced for macroscopic gaps, followed by showing the significant impact of the electric field nonuniformity due to gap geometry. The classical Paschen’s law assumes uniform electric field; a more general breakdown scaling law is illustrated for both DC and RF fields in geometrically similar gaps, based on the Townsend similarity theory. For a submillimeter gap, effects of electrode surface morphology with local field enhancement and electric shielding on the breakdown curve are discussed, including the most recent efforts. Breakdown characteristics and scaling laws in microgaps with both metallic and non-metallic (e.g., semiconductor) materials are detailed. -
Studies on Breakdown Voltages of Liquid Dielectrics
ISSN (Online) 2278-1021 IJARCCE ISSN (Print) 2319-5940 International Journal of Advanced Research in Computer and Communication Engineering ISO 3297:2007 Certified Vol. 7, Issue 4, April 2018 Studies on Breakdown Voltages of Liquid Dielectrics S Vasudevamurthy1, Girisha2, Shubham Shah3, Varun kumar B L4 , Uday N5 1 Associated Professor, Electrical and Electronics Engineering, Dr.AIT, Bengaluru, India 2,3,4,5 B.E in Electrical and Electronics Engineering, Dr AIT, Bengaluru, India Abstract: The objective of proposed work is to study the dielectric behavior of the natural ester based oil and it is compared with the transformer oil to find their suitability for use as liquid dielectric. Mineral oil contains a lot of toxic inhibitors to improve their properties. Due to this it is necessary to find a new source and that will be substitute for the mineral oil. For use as insulating liquids in power transformers, Natural ester based oils are gaining worldwide attention as biodegradable alternatives and competitors to the mineral based oils. Keywords: Liquid insulation, breakdown voltage, moisture content. INTRODUCTION Transformer plays a vital role in the field of transmission and distribution of electrical power. It is used to transforms electrical energy from one circuit to another circuit without change in frequency. Power transformers are used in transmission network of higher voltages for step-up and step-down .PT generally rated above 200MVA.A distribution transformer provides the final voltages transformation in the electrical power distribution system. it is used to stepping down the voltages as per the power requirement level of the customer. Transformer encounters lightning and other switching surges, hence it requires proper insulation.